一種適用於深水油田的高壓開啟氣舉閥的製作方法
2023-10-05 15:53:39
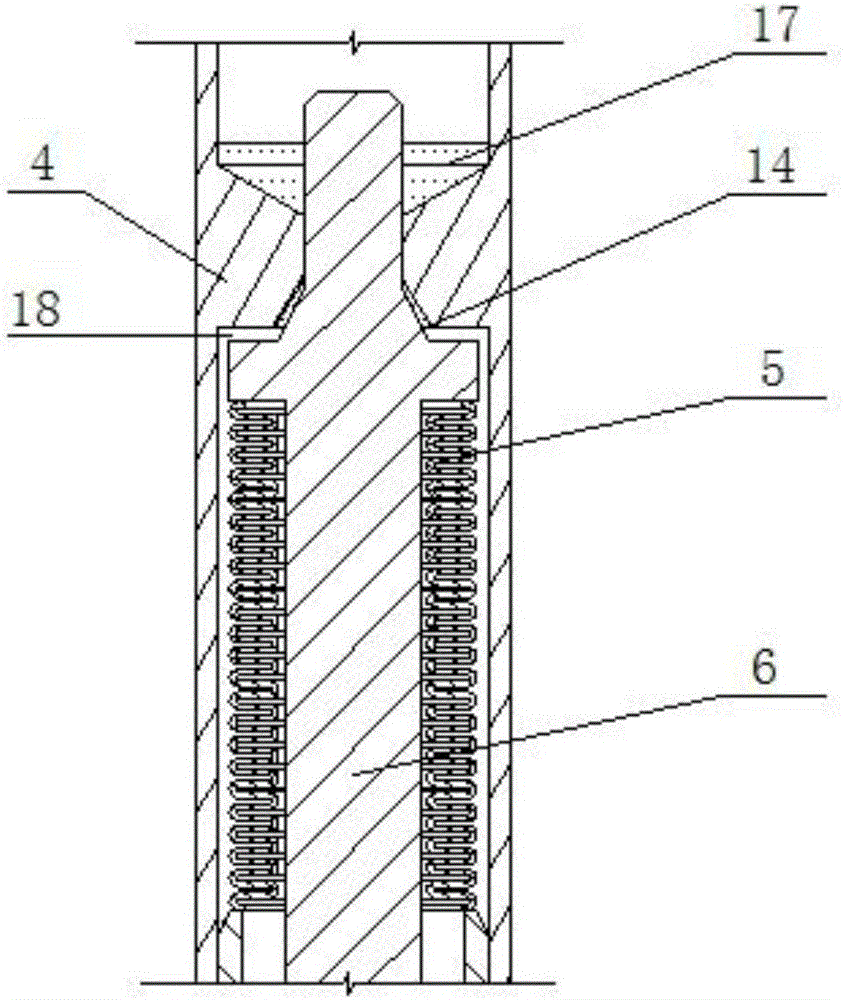
本發明涉及海上深水油田人工舉升工藝技術,特別涉及一種用於深水油田氣舉的高壓波紋管式氣舉閥。
背景技術:
傳統的氣舉技術在淺水油田開發中得到廣泛應用,氣舉系統最大注入開啟壓力不超過15MPa,注氣量在每天十萬方以下,而常規所謂高壓氣舉閥,如已有專利一種可投撈高壓氣舉閥,專利號201320162934.6裡所指高壓氣舉閥為氣舉閥整體耐壓能力高,不是指閥開啟工作壓力高,僅適用於陸上井和油藏深度較淺、生產壓力較低的近海陸架井。另外傳統非流線型氣舉閥閥座正常注氣時會造成較高的壓力損失,在大排量注氣的情況下可能會造成油套環空的不穩定,導致較大的流量變動,甚至出現間噴,無法保證注氣的可靠性。隨著深水油氣田開發向著水更深、離岸更遠、環境更複雜的方向發展,油田開發不僅要保證井筒內人工舉升,在某些環境下,還要確保流體在海底長回接管線中的順利流動,可輸送的距離儘可能遠。當採用氣舉輔助生產時,如在水深300m以上因其操作工作壓力較大,氣舉注氣壓力要達到15MPa以上,注氣量達每天幾十萬方甚至幾百萬方,需要保持水下井口處維持較高的井口壓力滿足遠輸要求。因此傳統的氣舉技術不能適應深水開發的要求。作業者面臨所安裝系統要能夠滿足深水作業環境對高可靠性能和注氣持續穩定的要求。
技術實現要素:
本發明的目的是克服現有技術中的不足,提供一種適用於深水油田的高壓開啟氣舉閥,本發明氣舉閥可用於深水注氣採液,有效提升氣舉閥打開壓力,大幅提高注入深度,以增加油井產量,同時該氣舉閥具有流線閥座,氣體通過效率更高,更穩定,滿足海上深水作業環境對高性能和持續穩定性的要求。
本發明所採用的技術方案是:一種適用於深水油田的高壓開啟氣舉閥,包括由上至下依次連接的打撈頭、氮氣室上接頭、氮氣室殼體、閥杆導向筒、閥流體入口、閥座護套和單向溢流閥;所述氮氣室殼體內設置有高壓波紋管,所述高壓波紋管與所述氮氣室殼體之間形成環形腔室;所述高壓波紋管內和所述閥杆導向筒內穿設有閥杆,所述閥杆的上端部設置有圓柱凸臺,所述高壓波紋管的上端面與所述閥杆的圓柱凸臺的下端面相連接,所述高壓波紋管的下端面與所述閥杆導向筒內的上部相連接;所述閥杆的下端連接有位於所述閥流體入口內的閥球,所述閥座護套內設置有與所述閥球相配合的閥座。
所述腔室內填充有使所述高壓波紋管受壓處於壓縮狀態的氮氣。
所述腔室內填充有幫助緩衝高壓波紋管內外衝擊的矽油。
所述閥座的內孔採用流線型流道。
本發明的有益效果是:
1.本發明氣舉閥具有較高的打開壓力可使注氣深度增加;
2.本發明中,高壓波紋管內部增加閥杆支撐可減少高壓波紋管變形,提高耐壓強度;
3.本發明中,高壓波紋管與氮氣室殼體之間形成的環空腔室填充有氮氣,預填充的氮氣使高壓波紋管外部受壓處於壓縮狀態,氣舉閥開啟壓力作用於高壓波紋管內部,由於作用於高壓波紋管內外面積存在差異從而使開啟壓力被提高,使氣舉閥打開壓力為預充氮壓力的2~2.5倍,在較低預充氮氣壓力下,實現了高壓開啟氣舉閥;
4.本發明中,高壓波紋管與氮氣室殼體之間形成的環空腔室內充滿矽油,當閥杆到上限位過程中,矽油幫助緩衝高壓波紋管內外衝擊,使高壓波紋管得到了有效的保護;
5.本發明中,閥座採用流線型流道,相同注氣壓力、注氣量情況下本發明氣舉閥過閥壓差明顯減小,注氣更穩定可靠。
附圖說明
圖1:本發明氣舉閥結構示意圖;
圖2:本發明初始狀態下氮氣室殼體與閥杆位置示意圖;
圖3:本發明初始狀態下閥球和閥座位置示意圖;
圖4:本發明氣舉閥完全關閉狀態下閥球和閥座位置示意圖;
圖5:本發明氣舉閥完全打開狀態下閥球和閥座位置示意圖;
圖6:本發明氣舉閥完全打開狀態下氮氣室殼體與閥杆位置示意圖。
附圖標註:1、打撈頭;2、氮氣室上接頭;3、高壓單流閥;4、氮氣室殼體;5、高壓波紋管;6、閥杆;7、閥杆導向筒;8、上密封組合;9、閥球;10、閥座;11、閥座護套;12、下密封組合;13、單向溢流閥;14、金屬密封;15、閥流體入口;16、流線型流道;17、矽油;18、預留間隙;19、預留間隙;20、腔室。
具體實施方式
下面結合附圖對本發明作進一步的描述。
如附圖1至圖6所示,一種適用於深水油田的高壓開啟氣舉閥,包括由上至下通過螺紋依次連接的打撈頭1、氮氣室上接頭2、氮氣室殼體4、閥杆導向筒7、閥流體入口15、閥座護套11和單向溢流閥13。其中,所述打撈頭1用於下入本發明氣舉閥,當本發明氣舉閥下井時,可通過鋼絲作業連接所述打撈頭1將本發明氣舉閥投入到預先下井的偏心工作筒裡;所述單向溢流閥13用於防止油管壓力大於注氣壓力時井液倒流到油套環空。
所述氮氣室上接頭2內設置有高壓單流閥3。
所述氮氣室殼體4內設置有高壓波紋管5,所述高壓波紋管5和所述氮氣室殼體4之間形成環空腔室20,所述腔室20內填充有矽油17和氮氣。當閥杆6到上限位過程中,矽油17幫助緩衝高壓波紋管5內外衝擊,使高壓波紋管5得到了有效的保護;預填充的氮氣使高壓波紋管5外部受壓處於壓縮狀態,氣舉閥開啟壓力作用於高壓波紋管5內部,由於作用於高壓波紋管5內外面積存在差異從而使開啟壓力被提高,使氣舉閥打開壓力為預充氮壓力的2~2.5倍,在較低預充氮氣壓力下,實現了高壓開啟氣舉閥。
所述高壓波紋管5內和所述閥杆導向筒7內穿設有閥杆6,所述閥杆6的上端部設置有圓柱凸臺,其圓柱凸臺的上端面與閥杆6本體之間設計有錐形面;所述高壓波紋管5的上端面與所述閥杆6的圓柱凸臺的下端面焊接連接,所述高壓波紋管5的下端面與所述閥杆導向筒7內的上部焊接連接。
所述閥杆6的下端通過螺紋連接有位於所述閥流體入口15內的閥球9,其中,所述閥流體入口15的中間壁上周向開設有若干個等直徑通孔,流體通過通孔後能進入本發明氣舉閥內部。所述閥座護套11內設置有與所述閥球9相配合的閥座10;所述閥球9和所述閥座10的圓弧面之間設置有預留間隙19;所述閥座10的內孔採用流線型流道16,相比非流線型閥座10不僅能減少大排量注氣時壓力損失,還能增大注氣時穩定區間的範圍,實現大排量,連續穩定注入。
本發明中,所述氮氣室殼體4的中部設置有與所述閥杆6的圓柱凸臺及其錐形面相配合的圓柱凸臺。所述氮氣室殼體4的圓柱凸臺和所述閥杆6的圓柱凸臺之間設置有預留間隙18,並且,所述氮氣室殼體4的圓柱凸臺的內部、位於與所述閥杆6的錐形面的相接觸處,設置有金屬密封14。
本發明中,所述閥杆導向筒7的外表面上和所述閥座護套11的外表面上分別設置有上密封組合8和下密封組合12,所述上密封組合8和下密封組合12可與偏心工作筒配合實現油套環空與油管內部的密封,以防止油套環空氣體提前進入油管。
本發明氣舉閥初始狀態如圖1所示,高壓波紋管5處於自然狀態,閥杆6的圓柱凸臺與氮氣室殼體4內圓柱凸臺之間有預留間隙18(如圖2所示),閥球9和閥座10之間有預留間隙19(如圖3所示)。在對氣舉閥氮氣室衝入高壓氮氣之前,預先在氮氣室內加入一定量的矽油17,使高壓波紋管5與氮氣室殼體4之間的環空腔室20充滿矽油17。氣舉閥下井到工作筒前通過地面試驗臺在氮氣室殼體4內充如一定壓力的氮氣,氮氣壓力逐漸增大時,作用到高壓波紋管5的外部壓力也增加,產生的作用力首先對高壓波紋管5進行壓縮,連同閥杆6,閥球9向下移動,當閥球9與閥座10接觸後閥杆6沒有行程可走,剩餘的力促使閥球9緊貼閥座10,關閉氣舉閥閥座10與流體入口通道。此時,球閥與閥座10位置如圖4所示。
氣舉閥工作時,油套環空注氣壓力逐漸升高,氣體經過閥流體入口15的若干個直徑均布圓孔進入氣舉閥內並作用與高壓波紋管5內部,由於閥球9和閥座10緊貼,氣體作用在高壓波紋管5內部的面積會小於高壓氮氣作用在高壓波紋管5外部的面積,由於力的平衡原理,要使閥球9離開閥座10注氣壓力要大於氮氣室充氮壓力,這樣就對氣舉閥的打開壓力進行了一定的放大,高壓波紋管5內外作用面積的比決定了壓力的放大倍數。注氣壓力達到一定值後,壓力迫使高壓波紋管5伸長,高壓波紋管5帶動閥杆6,閥杆6帶動閥球9離開閥座10向上移動,當閥杆6圓柱凸臺面與氮氣室殼體4內圓柱凸臺接觸,高壓波紋管5伸長量到最大值,此時,氣舉閥完全打開,油套環空與油管內溝通,閥球9與閥座10位置如圖5所示。高壓波紋管5伸長到上限位時,在高壓波紋管5和氮氣室殼體4之間形成了一個密閉的環空腔室20,腔室20內充滿矽油17,注氣壓力進一步升高或氣壓不穩定時,作用在高壓波紋管5內部的力會發生變化,但是由於高壓波紋管5外部被矽油17包圍且這些矽油17都在一個密閉的腔室20中,由於液體壓縮性差,矽油17產生在高壓波紋管5外的壓力會隨著高壓波紋管5內部壓力增加而快速增加,這樣使高壓波紋管5內外受力均衡高壓波紋管5得到了有效的保護。閥杆6到上限位如圖6所示。
油套環空注入氣體通過打開的閥球9進入閥座10,閥座10採用流線流線型結構,油套環空壓力經閥座10後產生一個壓力降,同等氣量下該閥座10產生的壓力損失較小,閥座10後壓力較大,這樣就能進行更深點的注氣。同時,氣體經過閥座10速度達到臨界流速後,下遊的壓力變化對注氣不會產生影響,所以,壓力損失小的閥座10下遊穩定區域更大,使上遊注氣更穩定可靠。