一種金屬型重力鑄造方法以及鑄造模具與流程
2023-09-14 20:09:05 4
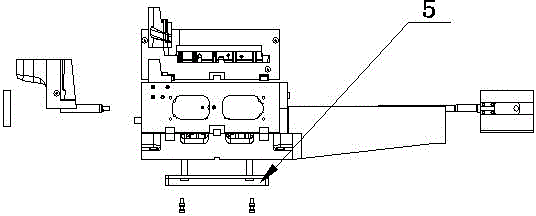
本發明屬於鑄造領域,具體是指一種金屬型重力鑄造方法以及鑄造模具。
背景技術:
隨著汽車產業的發展,汽車發動機缸蓋罩對於降低發動機噪聲和成本質量的要求越來越高,開發低成本高質量及具有降噪效果的汽車發動機缸蓋罩已成為國內外製造行業關注的熱點,汽車發動機整體鋁合金集成缸蓋罩零部件的核心製造實現國產化已迫在眉睫。目前該產品存在技術難點,由於鑄件壁厚較薄,形態結構複雜,砂芯數量多,前後端模為動模抽芯,砂芯定位有一定的高難度,缸蓋罩易產生疏鬆、冷隔、錯位、滲透現象。
技術實現要素:
本發明的目的在於:克服現有技術上述缺陷,提供一種金屬型重力鑄造方法以及鑄造模具。
本發明通過下述技術方案實現:
一種金屬型重力鑄造模具,包括金屬鑄型本體、左側模、右側模、前端模、後端模和底模,所述金屬鑄型本體的型腔內放置有氣道砂芯和油道砂芯,所述金屬型重力鑄造模具設有尺寸定位點,通過尺寸定位點將氣道砂芯以及油道砂芯在型腔內準確定位,所述尺寸定位點的型態通過數控加工中心加工成型。
作為一種優選的方式,所述尺寸定位點設計與底模上。
作為一種優選的方式,所述尺寸定位點的型態可以為方形、T型、橢圓或者喇叭型。
作為一種優選的方式,所述金屬型重力鑄造模具設有排氣抽風系統,所述前端模和後端模的抽芯軸均採用H13鋼製成,所述左側模、右側模和底模均設有水冷卻裝置,所述底模設有頂芯板。
作為一種優選的方式,所述金屬型重力鑄造模具採用中注式澆注系統,所述中注式澆注系統包括外澆口、橫澆道和內澆道。
作為一種優選的方式,所述金屬型重力鑄造模具澆道的頂端設有過濾網。
作為一種優選的方式,所述過濾網為矽酸鋁纖維編織網。
作為一種優選的方式,所述過濾網的網孔口徑為2.0mmx2.0mm。
本發明包括以下工藝過程:
(一)制芯:製作砂芯,砂芯包括油道砂芯、氣道砂芯和冒口砂芯;
(二)預熱:將鑄造模具預熱至220-250℃,吹淨型腔,並噴塗塗料;
(三)下芯:將油道砂芯和氣道砂芯放入型腔內,並通過尺寸定位點進行固定;
(四)前端模和後端模合型:首先將左側模和右側模合型,合型完成後再打開左側模和右側模,然後將前端模和後端模合型;
(五)組裝冒口砂芯:將冒口砂芯組裝至金屬型重力鑄造模具上,然後吹淨型腔,再將左側模和右側模合型,合型完成後等待澆注;
(六)澆註:將金屬液通過澆包在外澆口處進行澆注,保持外澆口處於充滿狀態,不可中斷流速,直到冒口砂芯充滿為止;
(七)凝固取件:等待金屬液完全凝固後,通過頂芯板取出鑄件。
本發明與現有技術相比,具有以下優點及有益效果:
(1)本發明砂芯與金屬鑄型通過尺寸定位點相互扣緊,鋁水充型時金屬鑄型遇高溫與砂芯相吻合,避免了砂芯偏移,振動、錯動導致的內壁尺寸超差質量現象,有利於形成結構複雜的鑄件,保證產品內部的質量;
(2)本發明無需人工監控,通過機械半自動化的運行即可完成鑄件鑄造模具制殼,降低了鑄件生產過程中的人力成本,有利於企業自身收益的增長;
(3)本發明操作簡單,工作人員經過簡單培訓後即可獨立操作,且裝置的可靠性好,實用性強,基本上不會發生故障。
附圖說明
圖1為本發明的俯視圖。
圖2為本發明的側視圖。
其中:1—右側模,2—外澆口,3—左側模,4—後端模,5—頂芯板。
具體實施方式
下面結合實施例對本發明作進一步地詳細說明,但本發明的實施方式不限於此。
參見圖1、圖2,一種金屬型重力鑄造模具,包括金屬鑄型本體、左側模3、右側模1、前端模、後端模4和底模,所述金屬鑄型本體的型腔內放置有氣道砂芯和油道砂芯,所述金屬型重力鑄造模具設有尺寸定位點,通過尺寸定位點將氣道砂芯以及油道砂芯在型腔內準確定位,所述尺寸定位點的型態通過數控加工中心加工成型。
本發明的尺寸定位點採用CAE仿真模擬動態分析技術進行設計,並通過數控加工中心加工成型。尺寸定位點的型態可以為方形、T型、橢圓或者喇叭型。通過此種設置,可使砂芯與金屬鑄型通過尺寸定位點相互扣緊,砂芯包括氣道砂芯和油道砂芯,鋁水充型時金屬鑄型遇高溫與砂芯相吻合,避免了砂芯偏移,鬆動、錯動導致的內壁尺寸超差質量現象,有利於形成結構複雜的鑄件,保證產品內部的質量。
作為一種優選的方式,所述尺寸定位點設計與底模上,通過此種設置,可保障產品的尺寸精度。
作為一種優選的方式,所述金屬型重力鑄造模具設有排氣抽風系統,所述前端模和後端模4的抽芯軸均採用H13鋼製成,所述左側模3、右側模1和底模均設有水冷卻裝置,所述底模設有頂芯板5。通過排氣抽風系統,可將鑄造過程中砂芯產生的氣體以及油煙排出。抽芯軸採用H13剛製成,其強度和耐磨性能要比普通鋼要高30%以上,H13鋼經過特殊的熱處理工藝,材料經久耐用,可使用15萬-20萬次。通過水冷卻系統裝置,可進行控制自動調節閥水冷卻,以保證在指定的控制下模具溫度在260℃±20℃。
作為一種優選的方式,所述金屬型重力鑄造模具採用中注式澆注系統,所述中注式澆注系統包括外澆口2、橫澆道和內澆道。中注式澆注系統綜合了底注式或頂注式的系統的優點,改善了補縮條件,充型平穩;又有利於排氣,能方便的實現自下而上的順序凝固;可使冒口充分補縮鑄件,減少產品夾渣、氣孔、疏鬆等缺陷,以確保鑄件的質量。此外,中注式澆注系統結構簡單緊湊,有利於提高鑄型面積的利用率及方便造型從鑄件上清除掉。
作為一種優選的方式,所述金屬型重力鑄造模具澆道的頂端設有過濾網。過濾網優選為矽酸鋁纖維編織網。作為優選,過濾網的網孔口徑為2.0mmx2.0mm。通過此種設置,可以使外澆口2處於充滿狀態,避免外來氣體捲入,同時減少冷隔、夾渣等缺陷的現象。
本發明的具體工藝過程如下:
(一)制芯:製作砂芯,砂芯包括油道砂芯、氣道砂芯和冒口砂芯;
(二)預熱:將鑄造模具預熱至220-250℃,吹淨型腔,並噴塗塗料;
(三)下芯:將油道砂芯和氣道砂芯放入型腔內,並通過尺寸定位點進行固定;
(四)前端模和後端模4合型:首先將左側模3和右側模1合型,合型完成後再打開左側模3和右側模1,然後將前端模和後端模4合型;
(五)組裝冒口砂芯:將冒口砂芯組裝至金屬型重力鑄造模具上,然後吹淨型腔,再將左側模3和右側模1合型,合型完成後等待澆注;
(六)澆註:將金屬液通過澆包在外澆口2處進行澆注,保持外澆口2處於充滿狀態,不可中斷流速,直到冒口砂芯充滿為止;
(七)凝固取件:等待金屬液完全凝固後,通過頂芯板5取出鑄件。
本發明改變了國內外採用的消失模及砂型鑄造工藝,原工藝班產量(8小時/班 40件),生產效率底,質量成本高,採用本發明工藝後班產量(8小時/班 60件),生產效率得到了成倍提升,而且穩定了產品質量,降低了生產成本,可實現機械半自動化。
以上所述,僅是本發明的較佳實施例,並非對本發明做任何形式上的限制,凡是依據本發明的技術實質對以上實施例所作的任何簡單修改、等同變化,均落入本發明的保護範圍。