一種用於汽車起動機定子機殼自動衝壓線的液壓衝床的製作方法
2023-08-02 00:54:41
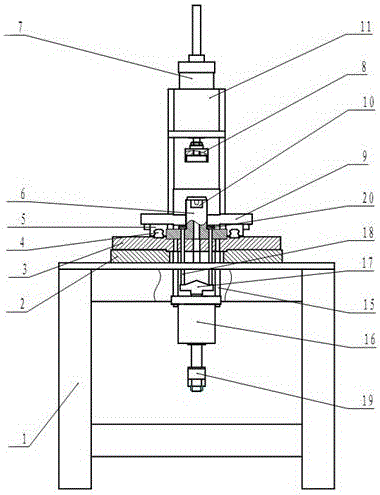
本實用新型屬於汽車起動機定子技術領域,特別涉及一種用於汽車起動機定子機殼自動衝壓線的液壓衝床。
背景技術:
汽車起動機定子機殼上設有包括上端面矩形凹槽、下端面矩形凹槽、導線引出孔和排水閥安裝孔的凹槽或孔,需要分別進行衝壓。現有技術中,要用到4臺衝壓機和4人分4道工序衝壓,加工效率低,加工精度較差,存在尺寸誤差,影響產品質量。
技術實現要素:
本實用新型所要解決的問題是,克服現有技術的不足之處,提供可以在一條生產線上連續完成4道衝壓工序,從而提高加工效率和加工精度的用於汽車起動機定子機殼自動衝壓線的液壓衝床。
本實用新型採用的技術方案包括機架,在機架上面安裝工作檯,工作檯上面安裝模具固定板,在模具固定板上安裝左右2個相互平行的直線導軌和凹模固定座,在左右2個相互平行的直線導軌上安裝直線導軌滑塊,直線導軌滑塊上安裝模具架,在凹模固定座上安裝衝壓凹模,在工作檯上面固定安裝支架,在支架上安裝機殼定位氣缸,在機殼定位氣缸的下端活塞杆上安裝定位壓頭,在模具固定板上安裝液壓油缸,在液壓油缸的前端安裝活塞杆上安裝衝頭轉接座,在衝頭轉接座前端安裝衝壓凸模,在模具固定板上還安裝氣缸固定杆,在氣缸固定杆上安裝退料氣缸,在退料氣缸的上活塞杆上安裝退料杆轉接座和退料杆,在退料氣缸的下活塞杆上安裝退料行程調節螺絲,在退料杆頂端凹模固定座上安裝退料推板。
在所述機架的前端焊接有機械手安裝座並用加強筋板支撐。
所述機座包括立柱、下橫梁、上橫梁和工作檯固定板,在工作檯固定板上面安裝工作檯。
與現有技術相比,本實用新型的有益效果是,在一條自動衝壓線上安裝4臺液壓衝床,可連續完成4道衝壓工序,分別衝壓出上端面矩形凹槽、下端面矩形凹槽、導線引出孔和排水閥安裝孔,在第一次4道工序完成後,衝壓線每動作一次即同步衝壓出4個殼體的上端面矩形凹槽、下端面矩形凹槽、導線引出孔和排水閥安裝孔,每小時可出成品460件,從而提高了加工效率和加工精度,由4人4臺設備變為1人1條衝壓線,大幅度降低人力資源和勞動強度,同時也由於節省了加工設備,可節約用電,降低生產成本,提高產品質量。
附圖說明
圖1是本實用新型的主視圖;
圖2是圖1的左視圖。
圖中:
1.機架,
1-1.立柱,1-2.下橫梁,
1-3.上橫梁,1-4.工作檯固定板,
2.工作檯,3.模具固定板,
4.直線導軌,5.直線導軌滑塊,
6.凹模固定座,7.機殼定位氣缸,
8.定位壓頭,9.模具架,
10.衝壓凹模,11.支架,
12.液壓油缸,13.衝頭轉接座,
14.衝壓凸模, 15.氣缸固定杆,
16.退料氣缸,17.退料杆轉接座,
18.退料杆,19.退料行程調節螺絲,
20.退料推板, 21.機械手安裝座,
22.機械手,23.定子機殼。
具體實施方式
如附圖所示,本實用新型包括機架1,所述機架1包括立柱1-1、下橫梁1-2、上橫梁1-3和工作檯固定板1-4,在工作檯固定板1-4上面安裝工作檯2,工作檯2上面安裝模具固定板3,在模具固定板3上安裝左右2個相互平行的直線導軌4和凹模固定座6,在左右2個相互平行的直線導軌4上安裝直線導軌滑塊5,直線導軌滑塊5上安裝模具架9,在凹模固定座6上安裝衝壓凹模10,在工作檯2上面通過螺釘固定安裝支架11,在支架11上安裝機殼定位氣缸7,在機殼定位氣缸7的下端活塞杆上安裝定位壓頭8,在模具固定板3上安裝液壓油缸12,在液壓油缸12的前端活塞杆上安裝衝頭轉接座13,在衝頭轉接座13前端安裝衝壓凸模14,在模具固定板3上還安裝氣缸固定杆15,在缸固定杆15上安裝退料氣缸16,在退料氣缸16的上活塞杆上安裝退料杆轉接座17和退料杆18,在退料氣缸16的下活塞杆上安裝.退料行程調節螺絲19,在退料杆18頂端凹模固定座6上安裝退料推板20,在機架1的前端焊接有機械手安裝座21並用加強筋板支撐。
使用時,在衝壓線上安裝4臺液壓衝床,在每道工序的液壓衝床上安裝不同加工部位的衝壓凹模10和衝壓凸模14,在每一臺液壓衝床的機械手安裝座21上安裝機械手22,由機械手22將汽車起動機的定子機殼23夾持放置在衝壓凹模10上,機殼定位氣缸7的活塞杆下行,通過定位壓頭8將汽車起動機的定子機殼23 定位壓緊在退料推板20上,液壓油缸12推動衝頭轉接座13前進,安裝在衝頭轉接座13的衝壓凸模14壓入汽車起動機的定子機殼23上衝壓成型,一道工序衝壓成型後,液壓油缸12後退,退料氣缸16帶動退料杆18上升,退料杆18推動退料推板20上升,將汽車起動機的定子機殼23頂出凹模固定座6,完成一個汽車起動機的定子機殼23一個部位的加工,然後進行下一個部位的加工,在第一次4道工序完成後,衝壓線每動作一次即同步衝壓出4個定子機殼23的上端面矩形凹槽、下端面矩形凹槽、導線引出孔和排水閥安裝孔,每小時可出成品460件,提高了加工效率和產品的加工精度。