一種磁赤混合型鐵礦弱磁尾礦的分級濃縮分級分選方法及裝置與流程
2023-07-24 03:41:06 2
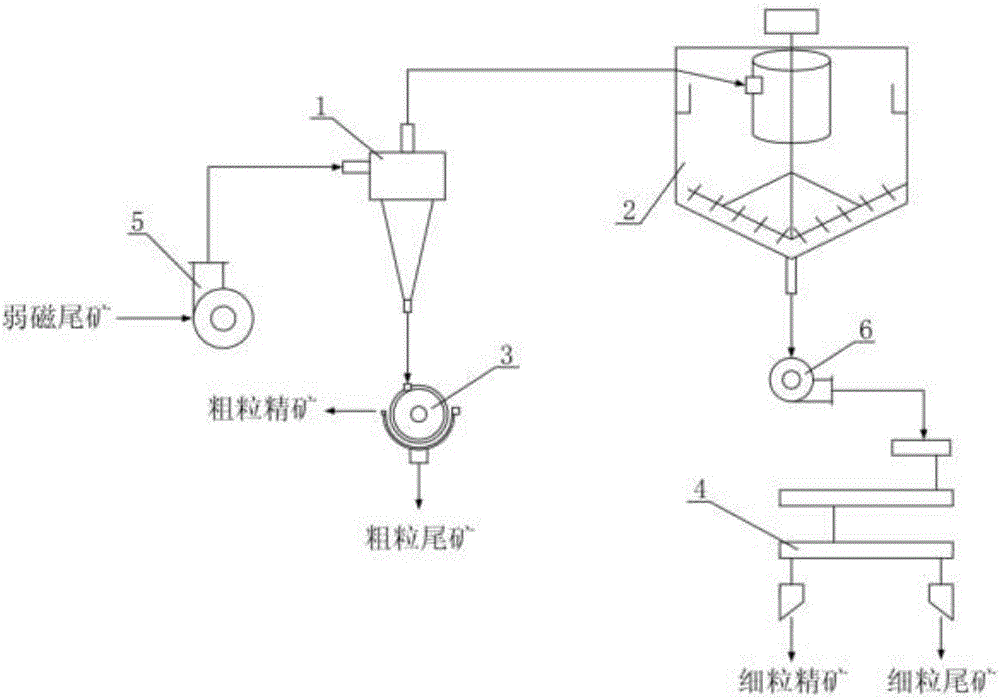
本發明屬於礦物加工技術領域,尤其涉及一種磁赤混合型鐵礦弱磁尾礦的分級濃縮分級分選方法及裝置。
背景技術:
我國磁赤混合型鐵礦山的選礦廠,需要對磨礦分級溢流或弱(中)磁選後的尾礦進行強磁選,以回收其中的弱磁性鐵礦物。然而,強磁選對給礦濃度有要求。但一般磨礦分級溢流或弱(中)磁選後的尾礦濃度較低(質量濃度<20%),達不到強磁選對尾礦的濃度要求。若在低濃度下進行強磁選,則微細粒鐵礦的回收率低,設備臺時幹礦處理量低,需要增加設備的臺數。
目前,國內一般是將磨礦分級溢流或弱磁尾礦全部輸送到選廠外的大型濃密機進行濃縮處理。待濃縮後的底流濃度達到30%-50%後再經泵輸送到選廠進行強磁選。這種工藝存在以下幾個問題:(1)所用濃密機設備選型大,設備佔地面積大、設備投資大;(2)礦漿來回輸送要消耗能源,增加了選廠運營成本;(3)粗細寬粒級別鐵礦一起入強磁選,不利於微細粒鐵礦的回收,尤其是對-20μm粒級的鐵礦物回收效果比較差,會降低鐵的回收率,影響礦山經濟效益。
技術實現要素:
本發明所要解決的技術問題是,克服以上背景技術中提到的不足和缺陷,提供一種鐵的回收率高、濃密機設備選型小、設備投資少的適用於磁赤混合型鐵礦弱磁尾礦的分級濃縮分級分選方法及裝置。
為解決上述技術問題,本發明提出的技術方案為:
一種磁赤混合型鐵礦弱磁尾礦的分級濃縮分級分選方法,包括以下步驟:
S1、採用旋流器對弱磁尾礦進行預選分級濃縮,得到旋流器溢流和沉砂;
S2、將步驟S1所得旋流器溢流送入濃密機中進行濃縮,得到濃密機底流;
S3、將步驟S1所得沉砂經強磁選機分選後得到粗粒精礦和粗粒尾礦;
S4、將步驟S2所得濃密機底流採用適合細粒鐵礦的強磁選機進行分選,得到細粒精礦和細粒尾礦。
磁赤混合型鐵礦的弱磁尾礦分選難度較大,在強磁選時對給礦濃度要求高。現有的濃縮方法將全部尾礦輸送到大型濃密機中進行濃縮,設備選型大,佔地面積大、設備投資大、運營成本高並且微細粒鐵礦的回收率低。本發明通過採用旋流器進行預先分級濃縮,粗粒(重)礦物直接由旋流器沉砂濃縮出,細粒(輕)礦物由濃密機底流濃縮出,從而大幅度減少了濃密機濃縮的礦量,濃密機設備選型小,設備投資少;採用常規強磁選機對旋流器沉砂進行分選,採用適合細粒鐵礦物回收的高效強磁機對濃密機底流進行分選,提高了微細粒級鐵礦物的回收率。
作為對上述技術方案的進一步改進:
優選的,所述步驟S1中,所述旋流器的溢流細度控制在-400目佔90%至-800目佔90%,以減少沉砂中粒度小於20μm的細粒鐵礦。
優選的,所述步驟S2中,所述濃密機底流的質量百分比濃度為30%-50%。
優選的,所述步驟S1中,旋流器對弱磁尾礦進行預選分級濃縮操作中,控制沉砂產率為50%-80%,沉砂質量濃度50%-60%,大幅度降低濃密機處理的礦量。
優選的,所述步驟S3中,強磁選機對沉砂進行分選操作中,控制入選質量濃度為25%-40%,強磁選機的磁場強度為0.8T-1.8T,以提高強磁選機的回收率,得到粗粒精礦和粗粒尾礦。
優選的,所述步驟S4中,採用適合細粒鐵礦的強磁選機對濃密機底流進行分選操作中,控制分選質量濃度為20%-40%,強磁選機的磁場強度為1.2T-1.8T,以提高強磁選機的回收率,得到細粒精礦和細粒尾礦,同時可以滿足後續工藝對礦物解離度要求。
作為一個總的技術構思,本發明另一方面提供了一種上述磁赤混合型鐵礦弱磁尾礦的分級濃縮分級分選方法所用的分選裝置,該分選裝置包括旋流器、濃密機、第一強磁選機和第二強磁選機,所述旋流器的溢流口與所述濃密機的入料口連通,所述旋流器的沉砂出口連通至所述第一強磁選機,所述濃密機的底流出口連通至所述第二強磁選機。
上述的分選裝置,優選的,所述第一強磁選機為常規強磁選機,所述第二強磁選機為適合細粒鐵礦的高效強磁選機。
上述的分選裝置,優選的,所述旋流器的入料口連接一入料管道,所述入料管道上安裝有一第一渣漿泵,所述濃密機的底流出口通過一管道與所述第二強磁選機連通,濃密機與第二強磁選機連通的管道上安裝有一第二渣漿泵。
與現有技術相比,本發明的優點在於:
(1)本發明針對磁赤混合型鐵礦採用旋流器預先分級濃縮,旋流器溢流再經濃密機進行濃縮,根據選礦工藝要求控制旋流器的溢流量(細度),使濃密機沉降面積減少50%以上,設備投資、佔地面積和基建費用都大幅度減少,礦漿輸送的能耗也減少,均減少近2/3。
(2)分別對旋流器沉砂和濃密機底流進行強磁分選,對濃密機濃縮底流採用針對微細粒鐵礦的強磁選機進行分選,提高了微細粒鐵礦的回收率。
(3)可根據選礦工藝要求控制旋流器溢流細度,使旋流器溢流經濃密機濃縮底流再強磁選的精礦不需要再磨,減少了次生礦泥對後續選別作業的影響。
(4)本發明方法步驟簡單,在新廠設計時根據工藝流程設計旋流器預先濃縮(分級)、旋流器溢流再採用濃密機濃縮即可;對現有工藝技術進行改造時只需增加旋流器預先濃縮作業,並針對旋流器沉砂和濃密機底流採用不同強磁機分選即可,在生產實踐中對細粒鐵礦高效回收具有重要意義。
(5)採用本發明的旋流器分級濃縮工藝,可以減少進入濃密機濃縮的礦量,徹底解決濃密機跑礦的問題。
附圖說明
為了更清楚地說明本發明實施例或現有技術中的技術方案,下面將對實施例或現有技術描述中所需要使用的附圖作簡單地介紹,顯而易見地,下面描述中的附圖是本發明的一些實施例,對於本領域普通技術人員來講,在不付出創造性勞動的前提下,還可以根據這些附圖獲得其他的附圖。
圖1為本發明磁赤混合型鐵礦弱磁尾礦的分級濃縮分級分選裝置的結構示意圖。
圖例說明:
1、旋流器;2、濃密機;3、第一強磁選機;4、第二強磁選機;5、第一渣漿泵;6、第二渣漿泵。
具體實施方式
為了便於理解本發明,下文將結合說明書附圖和較佳的實施例對本發明作更全面、細緻地描述,但本發明的保護範圍並不限於以下具體的實施例。
需要特別說明的是,當某一元件被描述為「固定於、固接於、連接於或連通於」另一元件上時,它可以是直接固定、固接、連接或連通在另一元件上,也可以是通過其他中間連接件間接固定、固接、連接或連通在另一元件上。
除非另有定義,下文中所使用的所有專業術語與本領域技術人員通常理解的含義相同。本文中所使用的專業術語只是為了描述具體實施例的目的,並不是旨在限制本發明的保護範圍。
除非另有特別說明,本發明中用到的各種原材料、試劑、儀器和設備等均可通過市場購買得到或者可通過現有方法製備得到。
實施例
一種本發明磁赤混合型鐵礦弱磁尾礦的分級濃縮分級分選方法及裝置的實施例,如圖1所示,該分選裝置包括旋流器1、濃密機2、第一強磁選機3和第二強磁選機4。其中旋流器1的溢流口與濃密機2的入料口連通,旋流器1的沉砂出口連通至第一強磁選機3,濃密機2的底流出口連通至第二強磁選機4。其中第一強磁選機3為常規強磁選機,而第二強磁選機4為適合細粒鐵礦的高效強磁選機。在旋流器1的入料口連接一入料管道,該入料管道上安裝有一第一渣漿泵5。在濃密機2的底流出口通過一管道與第二強磁選機4連通,濃密機2與第二強磁選機4連通的管道上安裝有一第二渣漿泵6。
該分級濃縮分級分選方法包括以下步驟:
(1)某磁赤混合型鐵礦,弱磁選尾礦濃度低於20%,而強磁選機分選要求給礦濃度35%±5%,按以前的思路全部弱磁尾礦都進入濃密機濃縮,現採用旋流器預先分級濃縮得到產率70%左右、質量濃度50%-60%的旋流器沉砂;旋流器的溢流細度控制在-600目佔90%,旋流器溢流產率為30%左右,質量百分比濃度為8%左右,粒度P95 20μm。
(2)旋流器沉砂(產率70%左右)直接在選廠內採用常規強磁選機進行分選,常規強磁選機的磁場強度為1.0T,得到粗粒精礦和粗粒尾礦。此部分粒度相對較粗,常規強磁選機都能取得較好的分選指標。
(3)旋流器溢流(產率30%左右)自流入濃密機進行濃縮,濃密機底流質量百分比濃度達到30%-35%再經泵輸送回選廠,採用適合微細粒鐵礦分選的高效強磁選機進行分選,高效強磁選機的磁場強度為1.6T,得到細粒精礦和細粒尾礦。鐵的作業回收率增加12個百分點左右。
(4)根據選礦工藝要求,控制旋流器溢流細度為P95 20μm,旋流器沉砂經強磁選後需要進一步細磨至95%-0.045mm(P8030μm),而旋流器溢流再經濃密機濃縮後底流強磁選得到的細粒精礦解離度達到要求,可以直接進入後續反浮選作業,減少了全部礦量入磨時產生的過磨和能耗浪費。
以上所述僅為本發明的優選實施例而已,並不用於限制本發明,對於本領域的技術人員來說,本發明可以有各種更改和變化。凡在本發明的精神和原則之內,所作的任何修改、等同替換、改進等,均應包含在本發明的保護範圍之內。