一種脫銅電解淨化工藝的製作方法
2023-11-08 07:13:13 2
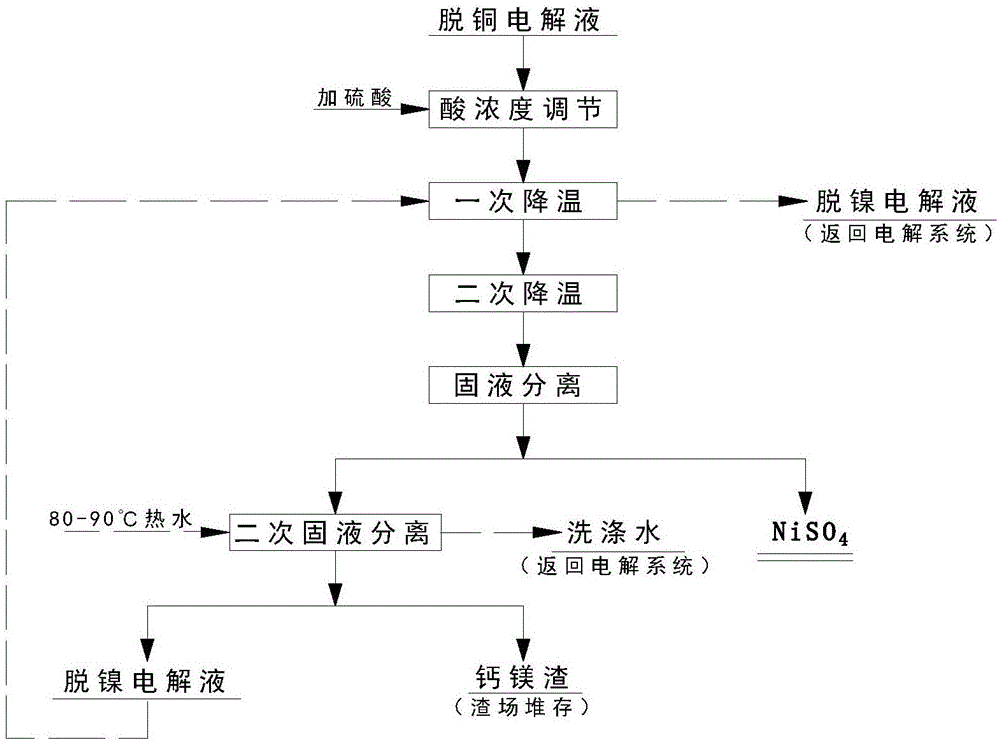
本發明涉及銅冶煉電解液除雜工藝技術領域。
背景技術:
銅電解過程中,砷、銻、鉍、鎳、鈣、鎂等雜質隨著陽極銅一起電化學溶解進入電解液。當累積到一定程度時,就需要對電解液進行淨化,否則會影響陰極銅產品質量。目前國內普遍採用的工藝是電解液真空蒸髮結晶,生產硫酸銅帶走部分鈣、鎂;硫酸銅過濾後液採用誘導法電積脫銅、砷、銻、鉍等雜質,脫銅後液進行冷凍結晶脫除鎳,脫鎳後液返回電解系統。該方法的缺點是:1)電解液中的鈣、鎂等雜質不斷富集形成難溶性化合物,附著於電解槽管壁、槽壁等部位,長期會導致管道堵塞,流量難以達到生產需求,清理過程困難。2)脫銅後液經過-20~-15℃的冷凍結晶8~10h,結晶後液含鎳仍有15~20g/l,鎳的直收率僅為50~62%左右,存在生產成本高,作業效率低等缺陷。3)脫鎳後液由於溫度在-10至-13℃,返回電解系統時,需要通過板式換熱器升溫,而脫銅電解液冷凍時需要通過冷凍機進行降溫,升溫和降溫都需要消耗能量,造成能源浪費。4)常規硫酸鎳生產液體運輸都需要通過泵來實現,存在能源消耗高現象。
技術實現要素:
本發明的目的在於解決現有技術的不足,提供一種銅電解液深度淨化工藝,以降低生產成本,節能降耗,增加電解淨化過程中有價金屬鎳的直收率,提高作業效率;同時深度脫除電解系統中的鈣、鎂等雜質,避免生產過程中各類輸液管道堵塞,槽壁結垢,進一步優化電解液淨化過程。
本發明的目的通過如下技術方案實現:
一種銅電解液深度淨化工藝,工藝步驟如下:
1)添加硫酸::向含H2SO4200~350g/l、Ni18~30g/l、Cu0.5~5g/l、As0.1~0.5g/l、Sb 0.01~0.5g/l、Bi0.15~0.5g/l、Ca0.1~0.3g/l、Mg0.1~0.3g/l的脫銅電解液中加入50%以上濃度的硫酸;
2)一次降溫:使用-10至-13℃的脫鎳電解液對貯存在罐內的脫銅電解液進行一次降溫,使脫銅電解液的溫度從45~55℃降到20~30℃;
3)二次降溫:把20~30℃的脫銅電解液放入二次降溫槽,經過8~10h再降溫過程,使溫度降低35~45℃,使脫銅電解液中的鎳以NiSO4晶體形態冷凝析出;
4)一次脫雜:把二次降溫槽內的低溫脫銅電解液放入固液分離設備進行固液分離回收硫酸鎳,得到硫酸鎳產品,分離後液為含鎳6~8g/l的脫鎳電解液;
5)二次脫雜:脫鎳後電解液經過板框壓濾機進行二次脫雜,將液體中含有鈣、鎂雜質過濾出來,形成深度淨化的電解液,減少電解系統中管壁、槽壁的附著物;
6)高溫洗滌:向二次脫雜裝置中通入60~90℃的熱水,洗滌二次脫雜板框壓濾機中含有的銅、鎳等有價金屬,洗滌後液返回電解系統;
7)卸載板框:經過洗滌的板框壓濾機通過壓縮風吹乾後,打開板框卸載鈣鎂渣,達到了鈣鎂雜質的開路。
2、根據權利要求1所述,硫酸加入速度以0.1~1.0t/h,並同時均勻攪拌,控制攪拌速度在30~100r/min,最終使脫銅電解液中硫酸濃度達到380~420g/l。
3、根據權利要求1所述,脫銅電解液從一次降溫到二次降溫,再到一次脫雜,最後到二次脫雜,整個過程是通過液位差自流完成液體輸送。
4、根據權利要求1所述,使用-10至-14℃的脫鎳電解液對貯存在罐內的脫銅電解液進行一次降溫,使脫銅電解液的溫度從45~55℃降到20~30℃。
5、根據權利要求1所述,控制二次脫雜後的脫鎳電解液溫度在-10至-14℃,脫鎳電解液自流進入板框壓濾機,所述板框壓濾機使用的濾布為200~400目,當進液壓力達15~20kPa後達到滿載狀態停止進液。
6、根據權利要求1所述,高溫洗滌是板框壓濾機滿載後通入熱水,通入熱水的時間為5~10分鐘,水壓為0.6~0.8MPa,含銅、鎳的洗滌水與淨化後的電解液混合,返回電解系統。滿載板框壓濾機用0.1~0.3Mpa壓縮風吹0.5~3小時吹乾鈣鎂渣,卸載板框,鈣鎂渣作為棄渣在渣場堆存。
本發明通過在脫銅電解液中加入H2SO4,使脫銅電解液中H2SO4含量在380~420g/l,降低有價金屬鎳在脫銅電解液中的飽和度,提高鎳析出率的同時增加了直收率;脫銅電解液經過一次降溫和二次降溫,使脫銅電解液中的鎳以NiSO4晶體形態冷凝析出,通過固液分離設備產出硫酸鎳晶體和脫鎳後液,脫鎳後液在通過板框壓濾機進行二次脫雜,有效脫除液體中的鈣、鎂等雜質,減少了電解系統中槽壁、管壁的附著物。用熱水對板框渣進行清洗,綜合回收板框渣中銅、鎳等有價金屬。另外還利用了脫鎳後液需要升溫和脫銅電解液需要降溫的因素進行了熱交換,有效節約了能源。在整個工藝流程中,脫銅電解液從一次降溫到二次降溫,再到一次脫雜,最後到二次脫雜,整個過程是通過液位差自流完成液體輸送,有效減少了通過泵體輸液所需的能量。本工藝明具有工藝簡單、淨化效果好,節能降耗明顯,得到的硫酸鎳產品可直接出售。雜質鈣、鎂通過簡單的工藝即得到脫除,保證了主工藝陰極銅的產品質量,特別適合於銅電解淨化工業生產應用。
附圖說明
圖1為本發明的工藝流程圖;
圖2為設備連接圖。
具體實施方式
如圖1、圖2所示,本發明的銅電解液深度淨化工藝步驟如下:
1)通過向含H2SO4200~350g/l、Ni18~30g/l、Cu0.5~5g/l、As0.1~0.5g/l、Sb 0.01~0.5g/l、Bi0.15~0.5g/l、Ca0.1~0.3g/l、Mg0.1~0.3g/l的脫銅電解液中以0.1~1.0t/h的速度加入50%以上濃度的硫酸,控制攪拌速度在30~100r/min,攪拌均勻後使脫銅電解液中硫酸濃度達到380~420g/l。
2)利用步驟5)得到的脫鎳電解液對脫銅電解液進行一次降溫,使脫銅電解液的溫度從45~55℃降到20~30℃;同時脫鎳電解液的溫度升高10~25℃。
3)步驟2)的脫銅電解液自流至二次降溫槽,經過8~10h再降溫過程,使溫度降低35~45℃,脫銅電解液中的鎳以NiSO4晶體形態冷凝析出;
4)步驟3)中的脫銅電解液自流至固液分離設備進行固液分離,完成了一次脫雜過程,得到了硫酸鎳晶體和分離後液,分離後液為含鎳6~8g/l的脫鎳電解液;
5)控制步驟4)的脫鎳電解液溫度在-10至-14℃,自流進入板框,板框壓濾機使用的濾布為200~400目,當板框壓力達到15~20Kpa,停止進液;二次脫雜後的脫鎳電解液進入一次降溫槽對脫銅電解液進行一次降溫。
6)板框壓濾機滿載後通入熱水,通入熱水時間為5~10分鐘,水壓0.6-0.8Mpa,將板框渣中的銅、鎳等有價金屬進行回收。含銅、鎳的洗滌水與完成一次降溫過程的脫鎳電解液混合,返回電解系統。
滿載板框壓濾機用0.1~0.3Mpa壓縮風吹0.5~3小時吹乾鈣鎂渣,卸載板框,鈣鎂渣作為棄渣堆存在渣場。降低電解槽中管壁、槽壁的附著,達到了深度淨化的目的。
驗證例:採用本發明方法,使用脫銅電解液,溫度為50℃,其主要成分為:H2SO4340g/l、Cu1.35g/l、Sb 0.01g/l、Ni30g/l、Bi0.15g/l、As0.40g/l、Ca0.19g/l、Mg0.18g/l等,將其泵至一次降溫槽,加入98%濃度的硫酸同時不斷攪拌,攪拌機轉速為40r/min,使脫銅電解液含H2SO4達到400g/l;將二次脫雜後的脫鎳電解液通過一次降溫槽內的蛇形冷卻管冷卻脫銅電解液至25℃;然後自流至二次降溫槽,在不斷攪拌的條件下,打開冷凍機組的冷凍介質鹽水對二次降溫槽進行降溫,經過10h後,二次降溫槽內脫銅電解液降溫至-15℃;打開二次降溫槽放液閥門,二次降溫槽內的固液混合體自流至三足離心機,得到了含Ni20%的硫酸鎳晶體和進入儲槽的脫鎳電解液,脫鎳電解液主要成分為:H2SO4400g/l、Cu1.15g/l、Sb 0.01g/l、Ni7g/l、Bi0.10g/l、As0.40g/l、Ca0.17g/l、Mg0.16g/l等,通過三足離心機後脫鎳電解液溫度在-13℃,脫鎳電解液自流至板框壓濾機,板框壓濾機使用濾布為300目,經過板框壓濾機過濾後,由泵運輸至一次降溫槽進行一次冷卻,冷卻後脫鎳電解液溫度為12℃,返回電解系統;當板框壓濾機壓力達到20Kpa時,停止進液,然後對板框壓濾機通入80℃熱水進行洗滌,水壓為0.6Mpa,時間8分鐘,洗滌水主要含Cu1g/l、Ni2g/l,返回電解系統,板框壓濾機用0.2Mpa的壓縮風吹風1小時後卸載板框,得到了鈣鎂渣堆存於渣場,主含量為Cu0.0001%、Sb 0.001%、Ni0.02%、Bi0.05%、As0.03%、Ca6.04%、Mg5.20%。