輕質牆板智能生產線系統的製作方法
2023-05-05 07:59:11
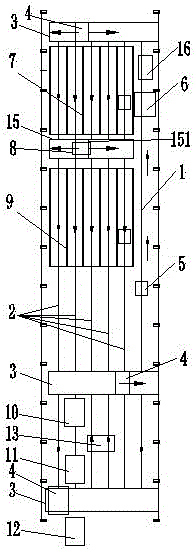
本發明涉及一種生產線,尤其是一種輕質牆板智能生產線系統。
背景技術:
輕質牆板是《國標GB/T23451-2009》建築用輕質隔牆條板的簡稱,是指採用輕質材料,兩側面設有榫頭榫槽及接縫槽,面密度不大於標準規定值(90kg/㎡:90板、110 kg/㎡:120板),用於工業與民用建築非承重內隔牆的預製條板。
當下,發泡輕質牆板的生產方式大多都是半機械化加人工方式,其生產出的產品質量不穩定,幾何精度相對較差,生產效率也較低。
技術實現要素:
本發明的目的在於提供一種產品質量穩定,幾何精度高,生產效率高的輕質牆板智能生產線系統。
為了達到上述目的,本發明的技術方案是:一種輕質牆板智能生產線系統,包括原材料計量混合系統和自動模車流水系統,自動模車流水系統包括擺渡軌道、平行布置的布料軌道和一條以上的製備軌道,擺渡軌道垂直於布料軌道和製備軌道,擺渡軌道上設有擺渡小車,所述布料軌道、製備軌道和擺渡軌道構成可供動力模車循環的軌道路線,所述該軌道路線上根據牆板製作工藝分別設置有自動布料裝置、預養窯、母槽成型裝置、終養窯、抽穿芯裝置、推板裝置、翻板裝置和噴油裝置,原材料計量混合系統與自動布料裝置連接。
所述原材料計量混合系統包括粉體計量輸送系統、液體配製輸送系統、纖維計量輸送系統和自動混合系統,粉體計量輸送系統包括多個粉倉、螺旋輸送機、稱重壓送罐和氣力輸送管道,所述多個粉倉下部均裝有螺旋輸送機,螺旋輸送機與對應的稱重壓送罐連接,液體配製輸送系統包括小料計量投放裝置、配製罐和恆溫儲存罐,小料計量投放裝置與配製罐連接,配製罐與恆溫儲存罐連接,所述自動混合系統包括粉體中間倉、液體中間倉、纖維中間倉、混合機、混泡機和高壓發泡機,稱重壓送罐通過氣力輸送管道與粉體中間倉連接,恆溫儲存罐與液體中間倉連接,纖維計量輸送系統與纖維中間倉連接,且所述粉體中間倉、液體中間倉和纖維中間倉均與混合機連接,混合機和高壓發泡機與混泡機連接,混泡機與自動模車流水系統的自動布料裝置連接。
所述預養窯和終養窯之間設有垂直於製備軌道的過渡軌道,所述過渡軌道上設有母槽成型擺渡小車,母槽成型裝置安裝在母槽成型擺渡小車上。
所述自動布料裝置設在布料軌道上。
所述布料軌道上還設有驅泡捋纖維裝置。
所述製備軌道設有平行布置的五條,且預養窯和終養窯均覆蓋五條製備軌道,所述擺渡軌道設有平行布置的三條,且其中兩條位於製備軌道兩端,另一條位於製備軌道中部。
所述抽穿芯裝置和推板裝置設在其中一條製備軌道上,噴油裝置設在另外的製備軌道上。
所述噴油裝置覆蓋兩條製備軌道。
所述翻板裝置與推板裝置配合使用,且分別位於擺渡軌道的兩側。
所述預養窯和終養窯採用蒸汽作為熱源。
採用上述結構後,由於本發明的布料軌道、製備軌道和擺渡軌道構成可供動力模車循環的軌道路線,所述該軌道路線上根據牆板製作工藝分別設置有自動布料裝置、預養窯、母槽成型裝置、終養窯、抽穿芯裝置、推板裝置、翻板裝置和噴油裝置。因此在生產中,原材料計量混合系統與自動布料裝置連接,為其提供配製好的發泡料漿。動力模車在軌道路線上運行至各工位,通過各種設備完成制板工序,再通過推板裝置將板材推出,脫離動力模車,翻板裝置將板材翻轉,使母槽朝下放置,將空動力模車再次進行生產循環。本生產線生產的輕質牆板不僅產品質量穩定而且幾何精度高,生產效率高。
附圖說明
圖1是本發明中的原材料計量混合系統示意圖;
圖2是本發明中的自動模車流水系統示意圖。
具體實施方式
以下結合附圖給出的實施例對本發明作進一步詳細的說明。
參見圖1所示,一種輕質牆板智能生產線系統,所述的粉體原材料儲存在粉體計量輸送系統110的多個粉倉111內,液體原材料儲存在液體原料池內。生產配料時,電子計量系統PLC先後發出指令,粉體原材料通過螺旋輸送機112向稱重壓送罐113送料,達設定重量,自動停止送料。而後,PLC程序控制兩個稱重壓送罐113將粉體原料壓送至自動混合系統140中的粉體中間倉141。液體原材料通過離心泵向配製罐122送料,達設定重量,自動停止送料。而後,在PLC程序控制下,各添加劑小料通過自動稱量,分別按設定重量加入該液體原料,完成配製後,自動落入恆溫儲存罐123保溫存放,在自動混合系統140需要時,由離心泵將恆溫儲存罐123的液體輸送至液體中間倉142,液體中間倉142附稱重裝置,當液體達到設定重量,則信號反饋至PLC,PLC控制離心泵停止工作。
PLC控制各原材料按順序落入混合機144,按程序設定要求混合完成後,落入混泡機145,此時高壓發泡機146程控啟動,向料漿中注入微氣泡同時開始混泡,混泡完成後料漿自動落入自動布料裝置6,等待動力模車5入位。
參見圖2所示,自動模車流水系統200包括平行布置的布料軌道1和五條製備軌道2,垂直於布料軌道1和五條製備軌道2的三條擺渡軌道3,其中兩條擺渡軌道3位於布料軌道1和製備軌道2的兩端,另一條擺渡軌道3位於布料軌道1和製備軌道2的中部,擺渡軌道3均上設有擺渡小車4,所述布料軌道1、五條製備軌道2和三條擺渡軌道3構成可供動力模車5循環的軌道路線,預養窯7和終養窯9均覆蓋五條製備軌道2。所述預養窯7和終養窯9之間設有過渡軌道15,過渡軌道15上設有母槽成型小車151,所述自動布料裝置6設在布料軌道1上,所述布料軌道1上還設有驅泡捋纖維裝置16,所述母槽成型裝置8安裝在母槽成型小車151上,所述抽穿芯裝置10和推板裝置11設在其中一條製備軌道2上,噴油裝置13設在另外的製備軌道2上,且所述噴油裝置13覆蓋兩條製備軌道2,可以同時對兩輛動力模車5進行噴脫模油作業。所述翻板裝置12與推板裝置11分別位於擺渡軌道3的兩側。
本發明的每個動力模車5上均配備單獨的驅動電機,當動力模車5行進至某工位時,工位傳感器將動力模車5的位置信號反饋給PLC,PLC發出停車信號,動力模車5按指令準確停在設定位置,之後該工位設備開始工作,該工位工序完成後,工位設備將信號反饋給PLC,PLC控制動力模車5行向下一工位,該過程稱為「模車單工位流程」。
本發明制板時,首先動力模車5按照「模車單工位流程」,由自動布料裝置6完成布料作業,之後進入驅泡捋纖維裝置16。驅泡捋纖維裝置16可以去除料漿中的大氣泡,且此過程亦能使料漿中亂向分布的纖維在制品表面大致形成同一方向的規則分布,從而提高了製品的抗折指標等物理性能(可以參考ZL201420657004.2)。
然後動力模車5駛向位於圖2所示上部的擺渡軌道3的擺渡小車4上,擺渡小車4將動力模車5擺渡至某一製備軌道2,而後動力模車5自動行至預養窯7的空模位,此時,PLC通過傳感器感應到動力模車5入模位即開始初養計時。
初養時間滿時,PLC程序控制動力模車5進入過渡軌道15上的母槽成型小車151,即母槽成型工位,按「模車單工位流程」由母槽成型裝置8完成了母槽的製作,動力模車5在PLC控制下駛入終養窯9的空模位,此時,PLC通過傳感器感應到動力模車5入模位即開始終養計時。
終養時間滿時,PLC程序控制動力模車5行至位於製備軌道2中部的擺渡軌道3的擺渡小車4上,擺渡小車4將動力模車5擺渡至抽穿芯裝置10所在的其中一條製備軌道2上,按「模車單工位流程」,由抽穿芯裝置10完成抽芯工序。
當PLC感知抽芯工序完成時,即程序控制擺渡小車4將動力模車5擺渡至可通向推板裝置11的製備軌道2,而後動力模車5行進至位於圖2下方的擺渡軌道3的擺渡小車4上,擺渡小車4將動力模車5擺渡至推板工位,按「模車單工位流程」,由推板裝置11將牆板連底模一同推離動力模車5,使得牆板進入翻板裝置12。經過 「一次翻板」及「二次翻板」後,將母槽翻轉到下端,方便放置牆板,然後牆板由叉車轉運離生產線,而後底模通過該機構返回動力模車5。
擺渡小車4在PLC控制下,將動力模車5擺渡至可通向噴油裝置13的製備軌道2,而後動力模車5根據「模車單工位流程」,進入自動噴油工位,噴油裝置13的噴塗房的進門在PLC控制下自動關閉,隨後噴塗系統自動開始工作,噴塗完成後,噴塗房的出門在PLC控制下自動打開,動力模車5行至位於製備軌道2中部的擺渡軌道3的擺渡小車4上,擺渡小車4將動力模車5擺渡至抽穿芯裝置10所在的其中一條製備軌道2上,按「模車單工位流程」,由抽穿芯裝置10自動吐出前一輛動力模車5抽出的芯管,完成了穿芯工序。擺渡小車4將動力模車5擺渡至布料軌道1,此時生產單循環完成,動力模車5重新駛向自動布料裝置6。
本發明的預養窯7和終養窯9採用清潔的蒸汽作為熱源,通過散熱暖氣片調節溫度。當氣溫傳感器探測到養護窯的室溫偏離設定溫度時,該傳感信號即時傳至PLC,控制系統隨即自動發出指令,調節該蒸汽管路中可無極調節的電磁閥,使管道中的蒸汽流量變小或變大,從而達到自動調節溫度的目的。
以上所述的僅是本發明的優選實施方式,應當指出,對於本領域的普通技術人員來說,在不脫離本發明創造構思的前提下,還可以做出若干變形和改進,這些都屬於本發明的保護範圍。