一種基於封閉循環式燒結冷卻機的雙工質餘熱發電系統的製作方法
2023-04-24 04:14:31
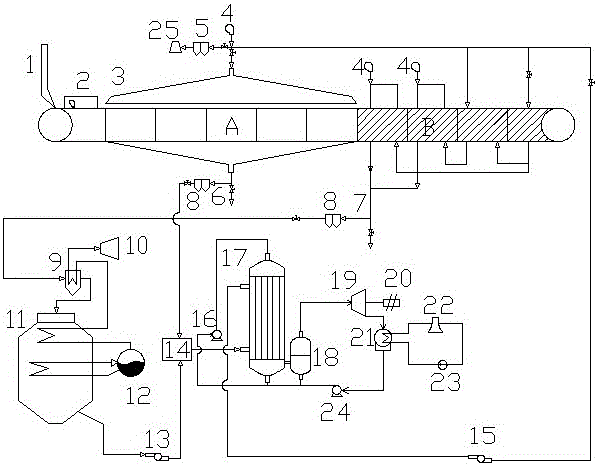
本發明屬於餘熱發電技術領域,尤其涉及一種基於封閉循環式燒結冷卻機的雙工質餘熱發電系統。
背景技術:
鋼鐵工業是我國能源消耗最大的產業部門之一,燒結生產一般佔噸鋼能耗的10~20%,僅次於煉鐵。燒結節能在鋼鐵企業節能中佔有十分重要的地位。熱燒結礦顯熱和燒結煙氣顯熱佔燒結過程熱耗的50%以上,有效利用這部分餘熱是燒結節能的重要方面。我國鋼產量已躍居世界第一,具備年產鋼5億噸生產能力,需要燒結礦8.5億噸,據初步統計,全國共建有100m2以上的燒結機總面積大於6萬m2,燒結礦年用量超過7億噸。
目前,冷卻燒結礦的低溫廢氣直接排掉,廢氣中的熱量全部浪費,年價值損失超過百億元,同時造成粉塵汙染和熱汙染。因此,中國鋼鐵企業廢氣熱量的回收利用是節能降耗,降低成本,減少汙染,提高效率的重要問題。可見,我國燒結冷卻機廢氣量巨大,利用技術非常落後,但目前燒結冷卻機廢氣利用存在著燒結冷卻機外排低溫廢氣、難於回收的技術難題。
技術實現要素:
本發明的目的在於提供一種基於封閉循環式燒結冷卻機的雙工質餘熱發電系統,其在不影響燒結礦冷卻效果的前提下,實現了熱量梯級耦合、高效、可靠回收利用燒結機廢熱氣餘熱發電的目標,可有效提高燒結餘熱回收效率。
為解決上述技術問題,本發明採用如下技術方案:一種基於封閉循環式燒結冷卻機的雙工質餘熱發電系統,包括燒結機入口低溫段A和燒結冷卻高溫段B,它還包括一級餘熱利用系統、混合系統、二級餘熱利用系統,一級餘熱利用系統包括餘熱鍋爐以及與餘熱鍋爐外接配設的汽輪機,餘熱鍋爐的氣道進口與燒結冷卻高溫段B的廢熱氣排氣口通過高溫風道連接;
混合系統包括混合器,混合器的第一分支輸入口與燒結機入口低溫段A的廢熱氣排氣口通過第一低溫風道連接,混合器的第二分支輸入口與餘熱鍋爐的氣道出口通過第二低溫風道連接,混合器的主輸出口與二級餘熱利用系統連接;
二級餘熱利用系統包括基於降膜蒸發器的有機朗肯循環系統,混合器的主輸出口與降膜蒸發器的加熱氣進口通過混合管連接,降膜蒸發器的加熱氣排口通過回氣風道與燒結機入口低溫段A的進氣口和燒結冷卻高溫段B的進氣口連接。
基於降膜蒸發器的有機朗肯循環系統包括降膜蒸發器、分離器、螺杆膨脹機、發電機、凝汽器、冷卻塔、循環水泵、凝結泵、熱泵,其中,降膜蒸發器的載熱工質氣體排口、分離器、螺杆膨脹機、凝汽器、凝結泵、熱泵和降膜蒸發器的載熱工質液體進口通過連接管路依次連接構成循環迴路,螺杆膨脹機與發電機傳動連接,凝汽器旁接冷卻塔和循環水泵構成用於冷卻凝汽器的循環水系統;所述分離器的液體出口接入所述凝結泵之後的循環迴路。
燒結冷卻高溫段B上設置有連續換熱風道,連續換熱風道的出口和進口分別為燒結冷卻高溫段B的廢熱氣排氣口和進氣口。
連續換熱風道包括在燒結冷卻高溫段B內排列設置的多個隔板,隔板將燒結冷卻高溫段B分隔為多個獨立冷卻腔,每個獨立冷卻腔上分別設置有獨立進氣口和獨立出氣口;獨立冷卻腔間設置支氣管路將不同獨立冷卻腔的獨立進氣口和/或獨立出氣口連接形成多次穿過燒結冷卻高溫段B的換熱路線。
回氣風道的尾部上設置煙氣脫硫淨化集成系統和煙囪。
高溫風道和第一低溫風道上分別設置除塵器,第二低溫風道上設置引風機,回氣風道上設置循環風機;
燒結機入口低溫段A的進氣口處和燒結冷卻高溫段B的進氣口處分別設置鼓風機。
循環風機採用調速風機,鼓風機為可控式鼓風機。
高溫風道和第一低溫風道上分別設置切換閥門。
降膜蒸發器內加設的載熱工質為低沸點有機質。
餘熱鍋爐為呈立式布置的雙壓餘熱鍋爐,雙壓餘熱鍋爐內設置有用於發電的主蒸汽裝置,主蒸汽裝置設有雙壓汽包和過熱器。
本發明的有益效果:
本發明利用廢熱氣及降膜蒸發器內加設的低沸點有機質形成雙工質,實現了高效、可靠、最大限度回收利用燒結機廢熱氣餘熱的目標,並能確保不影響燒結機工藝系統正常生產。
本發明實現了熱量梯級耦合、高效、可靠回收利用燒結機廢熱氣餘熱發電的目標,可有效提高燒結餘熱回收效率。
本發明提高了循環入口廢氣的溫度和鍋爐入口的溫度,可有效提高回收效率和蒸汽發電效率,充分體現了「溫度對口、梯級利用、高效轉化」的原則,在不影響燒結礦冷卻機工藝生產的前提下能最大限度的利用燒結礦廢熱氣餘熱,同時有利於環境保護和穩定燒結餘熱回收。
本發明解決了燒結冷卻機外排低溫廢氣、難於回收的技術難題,可減少外排廢氣總量50%,提高低質熱能回收率達80%以上,可大幅降低漏風、現場噪音,減少冷卻風機數量和耗電。
燒結冷卻高溫段B上設置有連續換熱風道,連續換熱風道的出口和進口分別為燒結冷卻高溫段B的廢熱氣排氣口和進氣口,連續換熱風道包括在燒結冷卻高溫段B內排列設置的多個隔板,隔板將燒結冷卻高溫段B分隔為多個獨立冷卻腔,每個獨立冷卻腔上分別設置有獨立進氣口和獨立出氣口;獨立冷卻腔間設置支氣管路將不同獨立冷卻腔的獨立進氣口和\或獨立出氣口連接形成多次穿過燒結冷卻高溫段B的換熱路線,上述連續換熱風道的設置方式使通過燒結冷卻高溫段的冷卻廢氣形成全封閉式強制多次循環,以提高廢氣入口溫度和鍋爐入口溫度。
餘熱鍋爐採用雙壓餘熱鍋爐,熱廢氣在餘熱鍋爐中換熱,餘熱鍋爐產生的蒸汽推動配設的汽輪機做功。所述餘熱鍋爐為呈立式布置的雙壓餘熱鍋爐,雙壓餘熱鍋爐內設置有用於發電的主蒸汽裝置,主蒸汽裝置設有雙壓汽包和過熱器,餘熱鍋爐同過熱器配套使用,可充分利用高溫段熱氣的熱能,通過熱能的多極梯度利用取得最高熱效率。
本發明採用調速循環風機控制循環冷卻風量,並設置鼓風機以及循環風機出口的煙氣脫硫淨化集成系統和煙囪,可靈活控制燒結機的冷卻效果。切換閥門的設置,在餘熱利用系統故障時,可同燒結機原有系統隔離,從而確保無論熱能回收系統是否運行,均不影響燒結礦主體工藝的生產。
本發明可以通過控制循環風機轉速及風門調節,控制燒結礦冷卻機的的廢熱氣道即煙罩與隔板密封處的廢氣壓力,從而減少廢熱氣的外洩。
附圖說明
圖1是本發明中實施例一的系統原理圖;
圖2是本發明中實施例二的系統原理圖;
圖3是本發明中實施例三的系統原理圖;
圖4是本發明中實施例四的系統原理圖。
具體實施方式
實施例一:
圖1主要顯示出本發明中一級餘熱利用系統、混合系統、二級餘熱利用系統、連續換熱風道及基於降膜蒸發器的有機朗肯循環系統的系統結構關係,其它非主體部分的功能設置不在本技術說明之列。
圖1中箭頭方向表示管道內的介質流向。
如圖1所示,本發明的一種基於封閉循環式燒結冷卻機的雙工質餘熱發電系統,包括燒結機入口低溫段A和燒結冷卻高溫段B,它還包括一級餘熱利用系統、混合系統、二級餘熱利用系統,一級餘熱利用系統包括餘熱鍋爐11以及與餘熱鍋爐11外接配設的汽輪機10,餘熱鍋爐11的氣道進口與與燒結冷卻高溫段B的廢熱氣排氣口通過高溫風道7連接;
混合系統包括混合器14,混合器14的第一分支輸入口與燒結機入口低溫段A的廢熱氣排氣口通過第一低溫風道6連接,混合器14的第二分支輸入口與餘熱鍋爐11的氣道出口通過第二低溫風道連接,混合器的14主輸出口與二級餘熱利用系統連接;
二級餘熱利用系統包括基於降膜蒸發器17的有機朗肯循環系統,混合器14的主輸出口與降膜蒸發器17的加熱氣進口通過混合管連接,降膜蒸發器17的加熱氣排口通過回氣風道與燒結機入口低溫段A的進氣口和燒結冷卻高溫段B的進氣口連接。降膜蒸發器17的加熱氣排口位於加熱氣進口的上方。
基於降膜蒸發器的有機朗肯循環系統包括降膜蒸發器17、分離器18、螺杆膨脹機19、發電機20、凝汽器21、冷卻塔22、循環水泵23、凝結泵24、熱泵16,其中,降膜蒸發器17的出料口、分離器18、螺杆膨脹機19、凝汽器21、凝結泵24、 熱泵16和降膜蒸發器17的進料口通過連接管路依次連接構成循環迴路,螺杆膨脹機19與發電機20傳動連接,凝汽器21旁接冷卻塔22和循環水泵23構成用於冷卻凝汽器的循環水系統。所述分離器18的液體出口接入所述凝結泵24之後的循環迴路。
低溫餘熱發電的載熱工質採用低沸點有機質,有機工質經過凝結泵24加壓後到達降膜蒸發器17進口,經預熱後在降膜蒸發器17中與低溫熱源充分換熱,換熱後的載熱工質液體被汽化成載熱工質氣體。之後載熱工質氣體進入分離器18進行氣液分離,被分離的飽和液體工質重新經過工質循環泵進行循環,飽和氣態工質進入螺杆膨脹機19中膨脹做功,驅動發電機20發電,螺杆膨脹機19尾部乏汽在凝汽器21內經冷卻塔22、循環水泵23組成的循環水系統冷卻後變為冷凝水,冷凝水再經凝結水泵24加壓和熱泵16加熱後進入降膜蒸發器17進行下一個循環。降膜蒸發器17內較少部分的載熱工質液體未被汽化而從降膜蒸發器17底部出口接入所述凝結泵24之後的循環迴路。
燒結冷卻高溫段B上設置有連續換熱風道,連續換熱風道的出口和進口分別為燒結冷卻高溫段B的廢熱氣排氣口和進氣口。
連續換熱風道包括在燒結冷卻高溫段B內排列設置的多個隔板,隔板將燒結冷卻高溫段B分隔為多個獨立冷卻腔,每個獨立冷卻腔上分別設置有獨立進氣口和獨立出氣口;獨立冷卻腔間設置支氣管路將不同獨立冷卻腔的獨立進氣口和或獨立出氣口連接形成多次穿過燒結冷卻高溫段B的換熱路線。
上述連續換熱風道的設置方式使通過燒結冷卻高溫段的冷卻廢氣形成全封閉式強制多次循環,以提高廢氣入口溫度和鍋爐入口溫度。
所述回氣風道的尾部上設置煙氣脫硫淨化集成系統5和煙囪25。
所述高溫風道和第一低溫風道上分別設置除塵器8,第二低溫風道上設置引風機13,回氣風道上設置循環風機15。
燒結機入口低溫段A的進氣口處和燒結冷卻高溫段B的進氣口處分別設置鼓風機4。所述循環風機15採用調速風機,鼓風機4為可控式鼓風機。本發明採用調速循環風機15控制循環冷卻風量,並設置鼓風機4以及循環風機15出口的煙氣脫硫淨化集成系統5和煙囪25,可靈活控制燒結機的冷卻效果。
本發明還可以通過控制循環風機15轉速及風門調節(鼓風機4及循環風機15的風門),控制燒結礦冷卻機的的廢熱氣道即煙罩與隔板密封處的廢氣壓力,從而減少廢熱氣的外洩。
所述高溫風道和第一低溫風道上分別設置切換閥門,在餘熱利用系統故障時,可同燒結機原有系統隔離,從而確保無論熱能回收系統是否運行,均不影響燒結礦主體工藝的生產。
所述降膜蒸發器17內加設的低沸點有機質為烷烴、氟代烷烴等低沸點有機物。為了充分利用不同工質的不同優點,採用混合工質如異丁烷和異戊烷也是正在發展的有前途的一種選擇。
所述餘熱鍋爐11為呈立式布置的雙壓餘熱鍋爐,所述餘熱鍋爐11為呈立式布置的雙壓餘熱鍋爐,雙壓餘熱鍋爐內設置有用於發電的主蒸汽裝置,主蒸汽裝置設有雙壓汽包(低壓汽包和中壓汽包12)、過熱器9和回熱器,主蒸汽裝置採用補氣式雙壓循環。
熱廢氣在餘熱鍋爐11中依次流經過熱器9、中壓蒸發器、中壓省煤器和低壓蒸發器,溫度降至130±20℃。經給水預熱器進入餘熱鍋爐的補水溫度在80±10℃,與冷凝水經凝結水泵送入除氧器,除氧後部分進入低壓汽包,汽液分離後,低壓蒸汽作為補汽式進入汽輪機,液體水進入低壓蒸汽作為補汽進入汽輪機10,液體水進入低壓蒸發器進行加熱;另一部分除氧水經中壓省煤器進入中壓汽包12,氣液分離後,飽和蒸汽經過熱器9加熱成為中壓過熱蒸汽進入汽輪機10做功,分離水進入中壓蒸發器進行吸熱汽化。餘熱鍋爐同過熱器配套使用,可充分利用高溫段熱氣的熱能,通過熱能的多極梯度利用取得最高熱效率。餘熱鍋爐11中設置的過熱器9、中壓蒸發器、中壓省煤器、低壓汽包、中壓汽包12和低壓蒸發器為雙壓餘熱鍋爐的常規配置,其與汽輪機10的配合也為本領域的常規技術,本實施例及附圖中不再詳述。
本實施例中,燒結機3由布料裝置1、點火爐2以及燒結機低溫段A組成,燒結冷卻高溫段B及燒結機3的各段均由風道、廢熱氣道即煙罩等組成。鼓風機4通過風道接入燒結礦冷卻高溫段B,鼓風機4通過風道接入燒結機入口低溫段A。
本發明的工作流程如下:高溫風道收集燒結冷卻高溫段約500±50℃廢熱氣,低溫風道收集燒結機低溫段約150±20℃廢熱氣,高溫風道廢熱氣經過蒸汽過熱器加熱後一起送入雙壓餘熱鍋爐入口。雙壓餘熱鍋爐出口溫度降低至150±20℃左右的廢氣在混合器14中同低溫風道的廢熱氣混合後進入降膜蒸發器17,在降膜蒸發器17中進行蒸發換熱,完成強化換熱後的低溫廢氣通過調速循環風機15送入燒結礦冷卻高溫段B、燒結機的低溫段A的進口風道,完成廢熱氣系統的循環使用。調速的循環風機15和循環風機15出口設置煙氣脫硫淨化集成系統5和煙囪25,可靈活調節循環風量以及循環廢氣的溫度,減少燒結礦冷卻機的的廢熱氣道與隔板密封處的廢氣洩露,並控制燒結礦冷卻效果。
本發明利用廢熱氣及降膜蒸發器內加設的低沸點有機質形成雙工質,實現了高效、可靠、最大限度回收利用燒結機廢熱氣餘熱的目標,並能確保不影響燒結機工藝系統正常生產。
本發明優點在於實現了熱量梯級耦合、高效、可靠回收利用燒結機廢熱氣餘熱發電的目標,可有效提高燒結餘熱回收效率。
本發明提高了循環入口廢氣的溫度和鍋爐入口的溫度,可有效提高回收效率和蒸汽發電效率,充分體現了「溫度對口、梯級利用、高效轉化」的原則,在不影響燒結礦冷卻機工藝生產的前提下能最大限度的利用燒結礦廢熱氣餘熱,同時有利於環境保護和穩定燒結餘熱回收。
本發明解決了燒結冷卻機外排低溫廢氣、難於回收的技術難題,可減少外排廢氣總量50%,提高低質熱能回收率達80%以上,可大幅降低漏風、現場噪音,減少冷卻風機數量和耗電。
餘熱鍋爐採用雙壓餘熱鍋爐,熱廢氣在餘熱鍋爐中換熱,餘熱鍋爐產生的蒸汽推動配設的汽輪機做功。餘熱鍋爐中配設過熱器,餘熱鍋爐同過熱器配套使用,可充分利用高溫段熱氣的熱能,通過熱能的多極梯度利用取得最高熱效率。
實施例二:
圖2主要顯示出本發明的系統結構關係,其它非主體部分的功能設置不在本技術說明之列。圖2箭頭方向表示管道內的介質流向。
如圖2所示,燒結機3由布料裝置1、點火爐2以及燒結機低溫段A組成,燒結冷卻高溫段B及燒結機3的各段均由風道、廢熱氣道即煙罩等組成。鼓風機4通過風道接入燒結礦冷卻高溫段B,鼓風機4通過風道接入燒結機入口低溫段A。
基於封閉循環式燒結冷卻機的雙工質餘熱發電系統由燒結冷卻高溫段B、燒結機入口低溫段A、第一低溫風道6、高溫風道7、降塵器8、過熱器9、餘熱鍋爐11、中壓汽包12、混合器14、循環風機15、鼓風機4、煙氣脫硫淨化集成系統5和煙囪25等構成。
高溫風道入口連接燒結冷卻高溫段B,低溫風道入口連接燒結機入口低溫段A。
高溫風道出口連接到除塵器8的風道入口,除塵器8的風道入口的風道出口接入蒸汽過熱器9的風道入口,蒸汽過熱器9的風道入口的風道出口連接至中壓飽和蒸汽餘熱鍋爐11的風道入口,中壓飽和蒸汽餘熱鍋爐11的風道出口通過管道接至混合器14的風道入口,低溫風道出口連接到除塵器8的風道入口,除塵器8的風道入口的風道出口通過管道接至混合器14的另一個風道入口,混合器14的風道出口連接至降膜蒸發器17,在降膜蒸發器17中進行蒸發換熱,完成強化換熱後的低溫廢氣,進入循環風機15加壓,然後依次進入燒結機出口低溫段A、燒結機冷卻高溫段B,實現廢氣循環。
基於降膜蒸發器的有機朗肯循環(ORC)系統包括降膜蒸發器17、分離器18、螺杆膨脹機19、發電機20、凝汽器21、冷卻塔22、循環水泵23、工質循環泵24,低溫餘熱發電的載熱工質採用低沸點有機質,有機工質經過凝結泵24加壓後到達降膜蒸發器17進口,經預熱後在降膜蒸發器17中與低溫熱源充分換熱,之後進入分離器18進行氣液分離,被分離的飽和液體工質重新經過工質循環泵進行循環,飽和氣態工質進入螺杆膨脹機19中膨脹做功,驅動發電機20發電,螺杆膨脹機19尾部乏汽在凝汽器21內經冷卻塔22、循環水泵23組成的循環水系統冷卻後變為冷凝水,冷凝水再經凝結水泵加壓後進入降膜蒸發器17進行下一個循環。
餘熱鍋爐11的中壓飽和蒸汽輸出口接入蒸汽過熱器9的中壓飽和蒸汽入口,蒸汽過熱器9中壓蒸汽出口外接,可用於補汽式汽輪機10用於發電。
循環風機15採用調速風機,循環風機15的出口風道分別接燒結機3低溫段11、燒結礦冷卻高溫段B的風道入口。燒結機冷卻高溫段B和燒結機入口低溫段A的進風道分別設置鼓風機4,循環風機15的出口風道尾部上設置煙氣脫硫淨化集成系統5和煙囪25。
為了最大限度獲取燒結礦冷卻機的廢熱氣,提高熱能利用量,燒結礦冷卻高溫段B的冷卻廢氣採用全封閉閉式強制多次循環。
本實施例中,燒結機3由布料裝置1、點火爐2以及燒結機低溫段A組成,燒結冷卻高溫段B及燒結機3的各段均由風道、廢熱氣道即煙罩等組成。鼓風機4通過風道接入燒結礦冷卻高溫段B,鼓風機4通過風道接入燒結機入口低溫段A。
高溫風道收集燒結冷卻高溫段約500±50℃廢熱氣,低溫風道收集燒結機低溫段約150±20℃廢熱氣,高溫風道廢熱氣經過蒸汽過熱器加熱後一起送入雙壓餘熱鍋爐入口。雙壓餘熱鍋爐出口溫度降低至150±20℃左右的廢氣在混合器14中同低溫風道的廢熱氣混合後進入降膜蒸發器17,在降膜蒸發器17中進行蒸發換熱,完成強化換熱後的低溫廢氣通過調速循環風機15送入燒結礦冷卻高溫段B、燒結機的低溫段A的進口風道,完成廢熱氣系統的循環使用。調速的循環風機15和循環風機15出口設置煙氣脫硫淨化集成系統5和煙囪25,可靈活調節循環風量以及循環廢氣的溫度,減少燒結礦冷卻機的的廢熱氣道與隔板密封處的廢氣洩露,並控制燒結礦冷卻效果。
本發明優點在於實現了熱量梯級耦合、高效、可靠回收利用燒結機廢熱氣餘熱發電的目標,可有效提高燒結餘熱回收效率。
本實施例與實施例一的不同之處主要在於:燒結礦冷卻高溫段B的冷卻廢氣的換熱路線布置方式不同。
實施例三:
圖3主要顯示出本發明的系統結構關係,其它非主體部分的功能設置不在本技術說明之列。圖3中箭頭方向表示管道內的介質流向。
如圖3所示,一種基於封閉循環式燒結冷卻機的雙工質餘熱發電系統,包括燒結機入口低溫段A、燒結冷卻高溫段B、第一低溫風道6、高溫風道7、除塵器8、過熱器9、雙壓餘熱鍋爐11、中壓汽包12、混合器14、基於降膜蒸發器17的有機朗肯循環(ORC)系統、循環風機15、鼓風機4、煙氣脫硫淨化集成系統5和煙囪25,全封閉循環式燒結餘熱發電系統是先進的燒結廢氣餘熱回收系統,提高循環入口廢氣的溫度和鍋爐入口的溫度可有效提高回收效率和蒸汽發電效率,充分體現了「溫度對口、梯級利用、高效轉化」的原則,在不影響燒結礦冷卻機工藝生產的前提下能最大限度的利用燒結礦廢熱氣餘熱,同時有利於環境保護和穩定燒結餘熱回收等特點。通過燒結冷卻高溫段B的冷卻廢氣採用全封閉閉式強制多次循環,以提高廢氣入口溫度和鍋爐入口溫度,從高溫段多次循環過後的熱廢氣經過高溫風道7進入除塵器8,經除塵後進入過熱器9,再進入雙壓餘熱鍋爐11進行換熱,換熱後的低溫煙氣進入引風機13加壓,然後進入混合器14;來自燒結機入口低溫段A的低溫廢氣經過第一低溫風道6進入除塵器8除塵後,然後也進入混合器14;經混合器14混合後進入降膜蒸發器17進行蒸發換熱,完成強化換熱後的低溫廢氣,進入循環風機15加壓,然後依次進入燒結機出口低溫段A、燒結機冷卻高溫段B,實現廢氣循環。燒結機冷卻高溫段B和燒結機入口低溫段A的進風道分別設置鼓風機4,循環風機15的出口風道尾部上設置煙氣脫硫淨化集成系統5和煙囪25。
基於降膜蒸發器的有機朗肯循環(ORC)系統包括降膜蒸發器17、分離器18、螺杆膨脹機19、發電機20、凝汽器21、冷卻塔22、循環水泵23、工質循環泵24、熱泵16,低溫餘熱發電的載熱工質採用低沸點有機質,有機工質經過凝結泵24加壓後到達降膜蒸發器17進口,經預熱後在降膜蒸發器17中與低溫熱源充分換熱,之後進入分離器18進行氣液分離,被分離的飽和液體工質重新經過工質循環泵進行循環,飽和氣態工質進入螺杆膨脹機19中膨脹做功,驅動發電機20發電,螺杆膨脹機19尾部乏汽在凝汽器21內經冷卻塔22、循環水泵23組成的循環水系統冷卻後變為冷凝水,冷凝水再經凝結水泵24加壓和熱泵16加熱後進入降膜蒸發器17進行下一個循環。
由於採用了以上方案,本發明實現了高效、可靠、最大限度回收利用燒結機廢熱氣餘熱的目標,並能確保不影響燒結機工藝系統正常生產。
通過燒結冷卻高溫段的冷卻廢氣採用全封閉閉式強制多次循環,以提高廢氣入口溫度和鍋爐入口溫度。
餘熱鍋爐採用雙壓餘熱鍋爐,熱廢氣在餘熱鍋爐11中依次流經中壓過熱器9、中壓蒸發器、中壓省煤器、和低壓蒸發器,溫度降至130±20℃。經給水預熱器進入餘熱鍋爐的補水溫度在80±10℃,與冷凝水經凝結水泵送入除氧器,除氧後部分進入低壓汽包,汽液分離後,低壓蒸汽作為補汽式進入汽輪機10,液體水進入低壓蒸汽作為補汽進入汽輪機10,液體水進入低壓蒸發器進行加熱;另一部分除氧水經中壓省煤器進入中壓汽包12,氣液分離後,飽和蒸汽經中壓過熱器9加熱成為中壓過熱蒸汽進入汽輪機10做功,分離水進入中壓蒸發器進行吸熱汽化。餘熱鍋爐11同過熱器9配套使用,可充分利用高溫段熱氣的熱能,通過熱能的多極梯度利用取得最高熱效率。餘熱鍋爐11中設置的過熱器9、中壓蒸發器、中壓省煤器、低壓汽包、中壓汽包12和低壓蒸發器為雙壓餘熱鍋爐的常規配置,其與汽輪機10的配合也為本領域的常規技術,本實施例及附圖中不再詳述。
本發明採用調速循環風機15控制循環冷卻風量,並設置鼓風機4以及循環風機15出口的煙氣脫硫淨化集成系統5和煙囪25,可靈活控制燒結機的冷卻效果。高溫風道、低溫風道同燒結機廢氣煙囪之間均設有切換閥門,在餘熱利用系統故障時,可同燒結機原有系統隔離,從而確保無論熱能回收系統是否運行,均不影響燒結礦主體工藝的生產。
本發明通過控制循環風機15轉速及風門調節(鼓風機4及循環風機15的風門),控制燒結礦冷卻機的的廢熱氣道即煙罩與隔板密封處的廢氣壓力,從而減少廢熱氣的外洩。
本實施例中,燒結機3由布料裝置1、點火爐2以及燒結機低溫段A組成,燒結冷卻高溫段B及燒結機3的各段均由風道、廢熱氣道即煙罩等組成。鼓風機4通過風道接入燒結礦冷卻高溫段B,鼓風機4通過風道接入燒結機入口低溫段A。
本發明實現了熱量梯級耦合、高效、可靠回收利用燒結機廢熱氣餘熱發電的目標,可有效提高燒結餘熱回收效率。
本實施例與實施例一及實施例二的不同之處主要在於:燒結礦冷卻高溫段B的冷卻廢氣的換熱路線布置方式不同。
實施例四:
圖4主要顯示出本發明的系統結構關係,其它非主體部分的功能設置不在本技術說明之列。圖4中箭頭方向表示管道內的介質流向。
如圖4所示,一種基於封閉循環式燒結冷卻機的雙工質餘熱發電系統,包括燒結機入口低溫段A、燒結冷卻高溫段B、除塵器8、過熱器9、中壓餘熱鍋爐11、中壓汽包12、混合器14、基於降膜蒸發器17的有機朗肯循環(ORC)系統、循環風機15、鼓風機4、煙氣脫硫淨化集成系統5、煙囪25,燒結冷卻高溫段B的冷卻氣採用全封閉閉式強制多次循環,以提高廢氣入口溫度和鍋爐入口溫度,從高溫段多次循環過後的冷卻氣依次通過除塵器8,過熱器9,餘熱鍋爐11,引風機13,混合器14;來自燒結機入口低溫段A的低溫廢氣經過除塵器8除塵後,進入混合器14;經混合器14混合後依次通過降膜蒸發器17,循環風機15,最終依次回到燒結機冷卻高溫段B和燒結機入口低溫段A,實現熱廢氣循環。燒結機冷卻高溫段B和燒結機入口低溫段A分別設置鼓風機4,循環風機15的出口風道尾部上設置煙氣脫硫淨化集成系統5、煙囪25。
基於降膜蒸發器的有機朗肯循環(ORC)系統包括降膜蒸發器17、分離器18、螺杆膨脹機19、發電機20、凝汽器21、冷卻塔22、循環水泵23、凝結泵24、熱泵16,低溫餘熱發電的載熱工質採用低沸點有機質,有機工質經過凝結泵24加壓後到達降膜蒸發器17進口,經預熱後在降膜蒸發器17中與低溫熱源充分換熱,之後進入分離器18進行氣液分離,被分離的飽和液體工質重新經過工質循環泵進行循環,飽和氣態工質進入螺杆膨脹機19中膨脹做功,驅動發電機20發電,螺杆膨脹機19尾部乏汽在凝汽器21內經冷卻塔22、循環水泵23組成的循環水系統冷卻後變為冷凝水,冷凝水再經凝結水泵24加壓和熱泵16加熱後進入降膜蒸發器17進行下一個循環。
所述的循環風機15採用調速風機,鼓風機4為可控式鼓風機,鼓風機4與循環風機15的混合風溫通過風量配比調節可靈活控制燒結機的冷卻效果。
所述的燒結冷卻高溫段的冷卻氣採用全封閉閉式強制多次循環。
本發明在不影響燒結礦冷卻效果的前提下,提高循環入口廢氣的溫度和鍋爐入口的溫度並有效提高回收效率和蒸汽發電效率,最大限度的利用廢熱氣餘熱品質。
所述的餘熱鍋爐11為雙壓餘熱鍋爐呈立式布置,設置有用於發電的主蒸汽裝置,主蒸汽裝置設有雙壓汽包、過熱器9和回熱器,主蒸汽採用補氣式雙壓循環。
所述的低沸點有機工質為烷烴、氟代烷烴等低沸點有機物。為了充分利用不同工質的不同優點,採用混合工質(如異丁烷和異戊烷)也是正在發展的有前途的一種選擇。
本實施例中,燒結機3由布料裝置1、點火爐2以及燒結機低溫段A組成,燒結冷卻高溫段B及燒結機3的各段均由風道、廢熱氣道即煙罩等組成。鼓風機4通過風道接入燒結礦冷卻高溫段B,鼓風機4通過風道接入燒結機入口低溫段A。
本發明應用於餘熱發電技術領域,本發明充分體現了「溫度對口、梯級利用、高效轉化」的原則,實現了熱量梯級耦合、高效、可靠回收利用燒結機廢熱氣餘熱發電的目標,可有效提可有效提高燒結餘熱回收效率,保護環境。
本實施例與實施例一、實施例二及實施例三的不同之處主要在於:燒結礦冷卻高溫段B的冷卻廢氣的換熱路線布置方式不同。
以上實施例僅用以說明而非限制本發明的技術方案,儘管參照上述實施例對本發明進行了詳細說明,本領域的普通技術人員應當理解:依然可以對本發明進行修改或者等同替換,而不脫離本發明的精神和範圍的任何修改或局部替換,其均應涵蓋在本發明的權利要求範圍當中。