晶圓匣的製作方法
2023-05-11 03:01:27 2
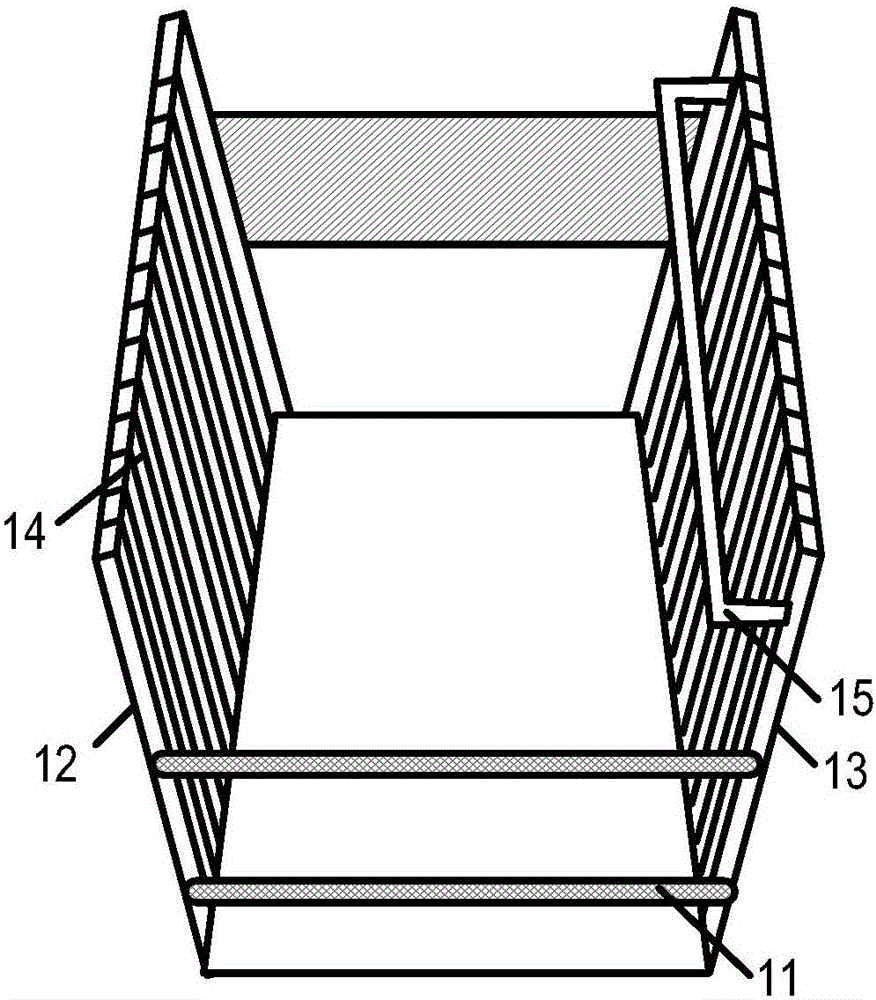
本發明涉及半導體製造領域,尤其涉及一種晶圓匣。
背景技術:
隨著半導體產業的飛速發展,對晶圓的需求越來越旺盛。一般來說,晶圓匣是在晶圓的製造工序中,於晶圓的切割、烘烤等工藝流程中用來盛放、運送晶圓的裝置。圖1是現有技術中的晶圓匣結構示意圖。如圖1所示,現有技術中的晶圓匣一般包括第一側壁12、第二側壁13和連接杆11,所述第一側壁12和第二側壁13分別連接於所述連接杆11相對的兩側,所述第一側壁12與第二側壁13上橫向層疊設置有多條滑槽14,所述第一側壁12與第二側壁13的滑槽兩兩對應並用於承載晶圓,當一晶圓被放置於晶圓匣中時,所述晶圓被插入第一側壁12與第二側壁13上兩兩對應的滑槽中,所述兩兩對應的滑槽是指使得所述晶圓在同一平面內的滑槽。在所述晶圓匣的第一側壁12和/或第二側壁13上沿豎直方向還設置有鋼條15,所述鋼條15可以沿第一側壁12或第二側壁13轉動,當將所述晶圓置於晶圓匣的滑槽之後,翻轉鋼條15至晶圓匣內部,由於每一滑槽14沿橫向延伸,而鋼條15沿豎直方向,因而翻轉鋼條15可以防止晶圓滑落。然而,由於鋼條15易於轉動,在運送或盛裝晶圓的過程中,容易造成鋼條15損壞或意外旋動,或是工作人員忘記翻轉鋼條至晶圓匣內部,或是提取晶圓匣時不注意方向性等,這些都容易導致晶圓在晶圓匣中錯位滑動,甚至從晶圓匣中掉落出來,從而導致晶圓損壞,嚴重影響後續工序的進行,使得生產成本大幅度升高,生產效率大大降低。
技術實現要素:
本發明提供一種晶圓匣,用以防止晶圓從晶圓匣中滑落,提高生產效率,降低生產成本。
為了解決上述問題,本發明提供了一種晶圓匣,包括兩相對設置的側壁,兩側壁相對的內側面分別對應設置有多條晶圓槽;其特徵在於,至少一所述側壁的邊緣處沿豎直方向設置有一開口,所述開口內設置有沿豎直方向滑動的限位件,所述限位件上設置有多個凸塊,所述凸塊的數量與所述晶圓槽數量相等,且相鄰凸塊之間的距離與相鄰晶圓槽之間的距離相等;當所述晶圓匣處於裝卸晶圓的第一狀態時,所述限位件上相鄰凸塊之間的間隙與晶圓槽對應;當所述晶圓匣處於運輸晶圓的第二狀態時,所述限位件上的凸塊與所述晶圓槽對應。
優選的,所述限位件包括第一基板以及位於第一基板上的第二基板,所述凸塊位於所述第二基板上,所述第一基板的兩端各設置有一缺口,兩固定件分別在兩個缺口處與所述第二基板連接,所述固定件將所述限位件固定於一所述側壁上。
優選的,所述固定件呈矩形,且兩端各具有一通孔,所述固定件在兩通孔之間的部位與所述第二基板連接,在所述通孔內設置螺絲連接所述固定件與一所述側壁。
優選的,所述缺口的寬度大於所述固定件的寬度。
優選的,所述固定件與所述第二基板通過焊接的方式連接。
優選的,相鄰所述凸塊之間的間隙距離不小於所述晶圓的厚度。
優選的,所述限位件和所述固定件採用金屬或有機高分子材料構成。
優選的,當所述晶圓匣處於所述第一狀態時,所述限位件的一側與所述開口的邊緣卡合固定。
本發明在傳統晶圓匣的基礎上增加了限位件,限位件上設置有一側壁上的晶圓槽數量相等的凸塊,由於相鄰凸塊之間的距離與晶圓匣上相鄰晶圓槽之間的距離相等,晶圓匣處於運輸晶圓的狀態時,所述限位件由於重力作用自然下滑,使得限位件上的每一凸塊位置恰好與晶圓槽的位置對應,從而卡合晶圓,故不需要進行鋼條的翻轉,就能有效的防止晶圓從晶圓匣中滑落,提高了生產效率,降低了生產成本。
附圖說明
圖1是現有技術中的晶圓匣結構示意圖;
圖2是本發明具體實施方式的晶圓匣結構示意圖;
圖3是本發明具體實施方式的限位件結構示意圖;
圖4是本發明具體實施方式的固定件結構示意圖;
圖5A是本發明具體實施方式的限位件部位內側結構示意圖;
圖5B是本發明具體實施方式的限位件部位外側結構示意圖。
具體實施方式
下面結合附圖和具體實施方式對本發明的技術方案作詳細說明。
本發明提供一種晶圓匣,圖2是本發明具體實施方式的晶圓匣結構示意圖。如圖2所示,所述的晶圓匣包括相對設置的第一側壁22和第二側壁23,以及用於連接所述第一側壁22和所述第二側壁23的連接件21。為了便於工作人員移動晶圓匣,一般還在所述晶圓匣上所述連接件21的相對側設置有把手。在所述第一側壁22與所述第二側壁23之間形成一容置空間,用於容納晶圓。所述第一側壁22與第二側壁23的材料可以為金屬材料,也可以為有機高分子材料,本領域技術人員可以根據實際需要進行選擇。本發明對所述連接件21的形狀並不作限定,可以為連接板或連接杆,只需要將第一側壁22與第二側壁23連接為一體即可。所述連接件的數量可以根據實際需要進行設定,可以僅在第一側壁22和第二側壁23的一側設置,也可以在第一側壁22和第二側壁23的兩側同時設置。
所述第一側壁22和所述第二側壁23相對的內側面分別設置有多條晶圓槽24,所述第一側壁22與所述第二側壁23上的晶圓槽24兩兩對應並用於承載晶圓。所述兩兩對應是指,將晶圓置於兩側壁上的晶圓槽24後,所述晶圓在同一平面內。晶圓槽24數量和深度的設置屬於本領域技術人員所熟知的技術手段,在此不再贅述。
為了防止晶圓滑落,如圖2所示,本發明在所述第一側壁22和/或所述第二側壁23的邊緣處沿垂直於晶圓槽24的方向設置有一開口,用於防止晶圓滑落的限位件26安裝於所述開口內。
圖3是本發明限位件26的結構示意圖。如圖3所示,所述的限位件26呈矩形結構,其上表面設置有多個凸塊37,相鄰所述凸塊37之間的距離與第一側壁22或第二側壁23上相鄰晶圓槽24之間的距離相等。相鄰所述凸塊37之間的距離優選為0.4cm。為了便於承載晶圓,相鄰所述凸塊37之間的間隙距離不小於所述晶圓的厚度。所述凸塊37的高度可以根據實際需要進行設定,優選為0.8cm。當所述晶圓匣處於裝卸晶圓的第一狀態時,所述限位件26上相鄰凸塊37之間的間隙與所述晶圓槽24的位置對應;當所述晶圓匣處於運輸晶圓的第二狀態時,所述限位件26上的凸塊37與所述晶圓槽的位置對應。因而,在使用本發明提供的晶圓匣時,當將裝載晶圓的晶圓匣立起從而運輸晶圓的過程中,所述限位件26因重力作用自動下滑,所述限位件26上的凸塊恰好對應於晶圓槽的位置,從而有效的卡合住晶圓,防止晶圓的滑落。
圖4是本發明具體實施方式的固定件結構示意圖,圖5A是本發明具體實施方式的限位件部位內側結構示意圖,圖5B是本發明具體實施方式的限位件部位外側結構示意圖。較佳的,為了便於將所述限位件26固定於所述第一側壁22或第二側壁23上,如圖4所示,所述限位件26可以包括第一基板381以及位於所述第一基板381上的第二基板382,所述凸塊37位於所述第二基板382上,在所述第一基板381上設置有缺口39,所述缺口39位於第一基板381的兩端部,兩個固定件40分別在兩個缺口39處與第二基板382連接,所述連接方式優選為焊接。所述固定件40呈矩形結構,其兩端分別設有一通孔,通過在所述通孔401內設置螺絲來連接所述固定件40與第一側壁22或第二側壁23。即所述固定件40在其中部與第二基板連接,在其兩端分別與第一側壁22或第二側壁23螺接。其中,為了便於固定,所述固定件40的寬度小於所述缺口39的寬度。所述限位件26與所述固定件40的材料可以根據實際需要進行選擇,可以為金屬或有機高分子材料,優選為鋼材。
優選的,還可以在限位件26的一側設置卡合部件,當所述晶圓匣處於裝卸晶圓的第一狀態時,所述限位件26一側的卡合部件與所述開口的邊緣卡合固定,便於裝載晶圓。
本發明在傳統晶圓匣的基礎上增加了限位件,限位件上設置有一側壁上的晶圓槽數量相等的凸塊,由於相鄰凸塊之間的距離與晶圓匣上相鄰晶圓槽之間的距離相等,晶圓匣處於運輸晶圓的狀態時,所述限位件由於重力作用自然下滑,使得限位件上的每一凸塊位置恰好與晶圓槽的位置對應,從而卡合晶圓,故不需要進行鋼條的翻轉,就能有效的防止晶圓從晶圓匣中滑落,提高了生產效率,降低了生產成本。
以上所述僅是本發明的優選實施方式,應當指出,對於本技術領域的普通技術人員,在不脫離本發明原理的前提下,還可以做出若干改進和潤飾,這些改進和潤飾也應視為本發明的保護範圍。