一種高吸音型超輕高強GMT複合板材的製作方法
2023-05-31 17:57:46
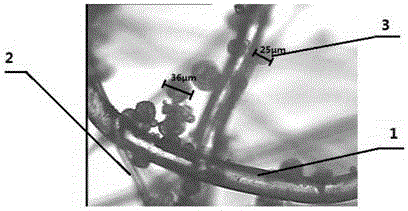
本發明屬於汽車內外飾用熱塑性複合材料技術領域,具體地說,是涉及一種用於製備汽車內外飾件的高吸音型超輕高強GMT複合板材。
背景技術:
輕質玻璃纖維氈增強熱塑性複合板材,簡稱輕質GMT(Glass fiber Mat reinforced Thermoplastics),是由連續玻璃纖維氈和熱塑性樹脂複合而成的一種新型複合材料,因其具有輕質環保、吸音隔熱、高強韌性、優良的抗化學腐蝕性和環境適應性等特點,而成為當今汽車內外飾材料中最為活躍的開發品種,已廣泛應用於各類汽車內外飾件(汽車車底屏蔽防護裝置、承重板、車頂內襯、車門裝飾、行李架、車頂模塑件、發動機蓋以及車後行李箱蓋、齒輪箱蓋)。然而,在全球提倡綠色、低碳、環保、健康主題下的今天,無論是愈發成熟與理性的傳統汽車行業或是新興的新能源汽車領域,人們對汽車的需求已從原先的代步工具逐漸升級為舒適的移動空間,消費者在購買汽車時,除注重汽車動力性、經濟性的同時,也更加注重其駕乘舒適性。即越來越關注汽車內外飾材料的健康性(VOC性能)與NVH等問題,訴求高性能與高舒適的統一,因此,如何進一步提高汽車內飾材料的綜合性能,使產品具有超輕量化(≤0.3kg/m3)、低VOC及NVH性能(吸音性能,提高駕乘者舒適性),是汽車內外飾材料行業今後3~5年必須面對和研究的熱點。然而,目前國內輕質GMT板材主要採用幹法梳理工藝,主要存下以下缺點:
製備過程相對複雜,玻纖損傷較大,而且取向明顯,板材力學性能呈各向異性;
熱熔纖維和玻璃纖主要是以點連接的方式結合,因而樹脂使用量較大,成本相對較高,進一步超輕化難以實現;
滲入空氣量不足,製品設計自由度及NVH性能遠落後於國外進口產品。
這些問題都將成為制約輕質GMT板材發展與廣泛應用的瓶頸。如何進一步提 高輕質GMT複合板材的綜合性能,使產品具有合理的性價比已成為研究的熱點,同時也是產業化的基礎。
目前,國際上寄希望通過改良現有工藝和開發新工藝來打破制約輕質GMT板材發展與廣泛應用的瓶頸。AZDEL公司主要使用溼法工藝,QPC公司使用幹法工藝。但近年來,相關設備廠家競相研發新的幹法設備,如義大利Cormatex公司,其最新研發的Lap Form Air氣流鋪網機,能夠通過氣流加壓成網,完全改變纖維成網方式——將所有纖維原料製成均勻的立體結構纖維網,這將使板材結構發生根本改變,立體結構的纖維網結合使板材的機械性能提高明顯,從而使其在保證汽車安全性和強度特性的前提下,減少自身材料用量,實現減輕車身重量的目的;法國Fibroline公司研發的Impregnation設備是通過靜電的方式將樹脂粉末浸入纖維基氈,使樹脂粉末對玻纖的浸潤更加均勻,不但減少了樹脂的用量,降低了成本,並且所得板材孔隙率高,片材中存有大量空氣,提高了聲傳播的粘滯阻力,在講究安靜舒適的高級轎車中,這種良好的吸聲特性更值得重視。這些新設備的研發將為輕質GMT的製備提供新的工藝方法,也將克服現有產品的不足。
然而,國內受設備技術研發水平的限制,主要採用改良現有工藝的辦法,比如在梳理過程中,通過調整工藝設備參數,輕度打擊玻纖,降低玻纖的損傷,從而改善板材的力學性能;在單纖網的鋪疊過程中,通過改變鋪網的方式,使玻纖的取向發生改變,從而降低板材縱橫向力學性能的差異;在基氈表面進行適當的表面處理,從而改變板材的熱性能等。但上述改善方式均未從根本上改變纖網的內部結構形態,玻璃纖維間仍然以點連接的方式結合,氈網厚度方向取向纖維含量偏少,層層單纖網之間僅靠針刺固結,二次成型過程中部件高膨化區域上下層單纖維網結合不足,仍需靠增加樹脂用量保證板材力學性能,然隨樹脂用量增加,板材膨化比減小,滲入空氣含量不足,製品超輕化難以實現,板材設計自由度及NVH性能也嚴重受限。
技術實現要素:
為解決上述問題,本發明公開了一種高吸音型超輕高強GMT複合板材,在複合板材內部氈網中引入了微球發泡劑,微球發泡劑的引入使增強纖維間的連接方 式更加多樣化,除傳統的點連接外,微球發泡劑作為連接橋梁將其周邊的增強纖維束縛在一起,微球發泡劑之間又彼此相連接,這些多樣化的連接方式使複合板材內部氈網結構發生了根本改變,產品機械性能提高明顯,從而使其在保證汽車安全性和強度特性的前提下,減少自身材料用量,實現超輕化的目的。另外所製備板材在二次成型過程中,在增強纖維內應力和微球發泡劑的雙重作用下,厚度膨鬆擴展至原來的5-10倍,相比傳統輕質GMT材料提高了2-4倍(相同面密度下),以便生產廠家可以根據產品性能要求通過調節膨化後的壓縮比來模製更多厚度變化、更高孔隙率的汽車內外飾部件,控制製品的體積密度0.05g/cm3-0.5g/cm3,進而獲得不同的強度、剛度及聲阻特性,這使得製品設計的自由度及NVH性能得以顯著提高。
本發明是通過以下技術方案實現的:
本發明公開了一種用於製備汽車內外飾件的高吸音型超輕高強GMT複合板材,所述複合板材由作為粘結基體的30wt-70wt%熱塑性合成纖維,作為增強材料的29wt-67wt%增強纖維和1wt-3wt%微球發泡劑組成,並通過熱壓製成汽車內外飾用超輕高強GMT複合板材,微球發泡劑之間彼此相連,所述的微球發泡劑與其周邊的增強纖維相互束縛連接。複合板材因微球發泡劑的引入使增強纖維間的連接方式更加多樣化,除傳統的點連接外,微球發泡劑作為連接橋梁將其周邊的增強纖維束縛在一起,微球發泡劑之間又彼此相連接,這些多樣化的連接方式使複合板材內部氈網結構發生了根本改變,產品機械性能提高明顯,從而使其在保證汽車安全性和強度特性的前提下,減少自身材料用量,實現超輕化的目的;另外所製備複合板材在二次成型過程中,在增強纖維內應力和微球發泡劑的雙重作用下,厚度可膨鬆擴展至原來的5-10倍,相比傳統輕質GMT材料提高了2-4倍(相同面密度下),以便生產廠家可以根據產品性能要求通過調節膨化後的壓縮比來模製更多厚度變化、更高孔隙率的汽車內外飾部件,控制製品的體積密度0.05g/cm3-0.5g/cm3,進而獲得不同的強度、剛度及聲阻特性,這使得製品設計的自由度及NVH性能得以顯著提高。
作為進一步地改進,本發明所述的複合板材面密度為500-2000g/m2,微球發泡劑用於改變增強纖維間格點連接方式調整板材膨化比。
作為進一步地改進,本發明所述複合板材中的微球發泡劑包括聚合物殼體和 其包裹的發泡劑,聚合物殼體為由丙烯酸酯類聚合物構成的單層或雙層結構,發泡劑為乙烷、丙烷、丙烯、異丁烷、丁烯、異丁烯、正戊烷、異戊烷、石油醚中的一種或幾種的混合物。
作為進一步地改進,本發明所述微球發泡劑的粒徑約為15~40μm,發泡起始溫度約為160-210℃,最大發泡體積倍率約為5~10倍,發泡後的尺寸為75~400μm。
作為進一步地改進,本發明所述熱塑性合成纖維選自聚丙烯纖維PP、聚乙烯纖維PE、聚酯纖維PET、ES纖維、尼龍纖維PA中的一種或幾種。
作為進一步地改進,本發明所述增強纖維選自玻璃纖維、碳纖維、玄武巖纖維或植物纖維中的一種或幾種。
作為進一步地改進,本發明所述複合板材還包括粘合在其表面的上表層和/或下表層,上表層和/或下表層選自聚丙烯膠膜、聚乙烯膠膜、EVA膠膜、EAA膠膜、聚酯薄膜、熱熔膠粉、無紡布或耐候、增強複合膜中的一種。
本發明的技術效果及優點在於:
(1)本發明在現有輕質GMT複合板材氈網內部引入微球發泡劑,通過改變增強纖維間格點設計的支撐方法來調整板材的膨化比,使所製備板材在二次成型過程中,在增強纖維內應力和微球發泡劑的雙重作用下,厚度膨鬆擴展至原來的5-10倍,相比傳統輕質GMT材料提高了2-4倍(相同面密度下),以便生產廠家可以根據產品性能要求通過調節膨化後的壓縮比來模製更多厚度變化、更高孔隙率的汽車內外飾部件,控制製品的體積密度0.05g/cm3-0.5g/cm3之間,進而獲得不同的強度、剛度及聲阻特性,這使得製品設計的自由度及NVH性能得以顯著提高。
(2)另外微球發泡劑的引入使板材內部增強纖維間連接的方式更加多樣化,除傳統的點連接外,微球發泡劑作為連接橋梁將其周邊的增強纖維束縛在一起,微球發泡劑之間又彼此相連接,這些多樣化的連接使複合板材內部氈網結構發生了根本改變,產品機械性能提高明顯,從而使其在保證汽車安全性和強度特性的前提下,減少自身材料用量,實現超輕化的目的。
附圖說明
圖1為本發明用於製備汽車內外飾件的高吸音型超輕高強GMT複合板材內部氈網結構圖;
圖2為本發明超輕高強GMT複合板材與傳統輕質GMT複合板材所製備的汽車內外飾件的內部氈網結構對比圖;
圖3為本發明超輕高強GMT複合板材所製備的汽車底護部件與傳統輕質GMT複合板材所製備的汽車底護部件吸聲性能測試對比圖;
圖4為本發明超輕高強GMT複合板材所製備的汽車頂棚部件與傳統輕質GMT複合板材所製備的汽車頂棚部件吸聲性能測試對比圖;
圖5為本發明超輕高強GMT複合板材所製備的汽車行李箱擱物板與傳統輕質GMT複合板材所製備的汽車行李箱擱物板吸聲性能測試對比圖。
圖中,1是熱塑性合成纖維,2是增強纖維,3是微球發泡劑。
具體實施方式
以下結合附圖對本發明的實施例進行詳細說明,但如下實施例以及附圖僅是用以理解本發明,而不能限制本發明的應用範圍,本發明可以由權利要求限定和覆蓋的多種不同方式實施。
實施例1
一種用於製備汽車底護板的高吸音型超輕高強GMT複合板材,由作為粘結基體的59wt%熱塑性聚丙烯纖維,作為增強材料的40wt%玻璃纖維和具有改變玻璃纖維間格點連接方式調整板材膨化比功效的1wt%微球發泡劑3組成,如圖1所示,並通過熱壓製成汽車底護板用超輕高強GMT複合板材,複合板材的面密度為1000g/m2。
將所得超輕高強GMT複合板材通過如下工藝製備汽車底護板:
(1)將複合板材放入烘箱中,加熱至180-210℃,使板材在玻璃纖維內應力和微球發泡劑3的雙重作用下,厚度膨鬆擴展至原來的5.7倍;
(2)上表面覆蓋疏水拒油功能的無紡布,下表面覆蓋耐候、增強複合膜;
(3)根據底護板產品性能要求,調節膨化後的壓縮比,模製成抗衝區厚度為3.5mm體密度為0.29g/cm3,吸音區厚度為9mm體密度為0.11g/cm3的汽車底護板產品。
對比例1
一種用於製備汽車底護板的傳統輕質GMT複合板材,由作為粘結基體的60wt%熱塑性聚丙烯纖維和作為增強材料的40wt%玻璃纖維組成,並通過熱壓製成汽車底護板用傳統輕質GMT複合板材,複合板材的面密度為1000g/m2。
將所得傳統輕質GMT複合板材通過如下工藝製備汽車底護板:
(1)將複合板材放入烘箱中,加熱至180-210℃,板材僅在玻璃纖維內應力的作用下,厚度膨鬆擴展至原來的2.3倍;
(2)上表面覆蓋疏水拒油功能的無紡布,下表面覆蓋耐候、增強複合膜;
(3)根據底護產品性能要求,調節膨化後的壓縮比,模製成抗衝區厚度為3.5mm體密度為0.29g/cm3,吸音區厚度為8mm體密度為0.13g/cm3的汽車底護板產品。
對比例2
一種用於製備汽車底護板的傳統輕質GMT複合板材,由作為粘結基體的60wt%熱塑性聚丙烯纖維和作為增強材料的40wt%玻璃纖維組成,並通過熱壓製成汽車底護板用傳統輕質GMT複合板材,複合板材的面密度為1400g/m2。。
將所得傳統輕質GMT複合板材通過如下工藝製備汽車底護板:
(1)將複合板材放入烘箱中,加熱至180-210℃,板材僅在玻璃纖維內應力的作用下,厚度膨鬆擴展至原來的2.5倍;
(2)上表面覆蓋疏水拒油功能的無紡布,下表面覆蓋耐候、增強複合膜;
(3)根據底護產品性能要求,調節膨化後的壓縮比,模製成抗衝區厚度為3.5mm體密度為0.40g/cm3,吸音區厚度為9mm體密度為0.16g/cm3的汽車底護板產品。
下表1中顯示了利用本發明所述超輕高強GMT複合板和傳統輕質GMT複合板模製的底護板的性能對比。
表1
實施例1在現有輕質GMT複合板材氈網內部引入微球發泡劑3,微球發泡劑3的引入使玻璃纖維間的連接方式更加多樣化,除傳統的點連接外,微球發泡劑3作為連接橋梁將其周邊的玻璃纖維束縛在一起,微球發泡劑3之間又彼此相連接,如圖2所示,這些多樣化的連接方式使複合板材內部氈網結構發生了根本改變,因而所製備的底護產品在同等密度下相比對比例1機械性能提高明顯,與傳統高密度GMT複合板對比例2機械性能相當,從而使其在保證汽車安全性和強度特性的前提下,減少自身材料用量,實現超輕化的目的。另外所製備的超輕高強GMT板材在二次成型底護產品過程中,在玻璃纖維內應力和微球發泡劑3的雙重作用下,厚度膨鬆擴展至原來的5.7倍,相比對比例1提高了2倍以上,以此複合板材模製的底護產品相比對比例2雖在機械性能上相當,但是所得產品中板材孔隙率高,產品中存有大量滲入空氣,提高了聲傳播的粘滯阻力,因而製品NVH性能提高明顯,如圖3所示。
實施例2
一種用於製備汽車頂棚部件的高吸音型超輕高強GMT複合板材,由作為粘結基體的45wt%熱塑性ES纖維,作為增強材料的52wt%植物纖維和具有改變增強纖維2間格點連接方式調整板材膨化比功效的3wt%微球發泡劑3組成,並通過熱壓製成汽車頂棚用超輕高強GMT複合板材,複合板材的面密度為600g/m2。
將所得超輕高強GMT複合板材通過如下工藝製備汽車頂棚部件:
1)、將複合板材放入烘箱中,加熱至180-210℃,使板材在植物纖維內應力和微球發泡劑3的雙重作用下,厚度膨鬆擴展至原來的8倍;
2)、上表面覆蓋熱軋無紡布,下表面覆蓋表面裝飾用的泡棉針織面料;
3)、根據頂棚產品性能要求,通過調節膨化後的壓縮比,模製成大面厚度為5mm體密度為0.12g/cm3的汽車頂棚產品。對比例3
一種用於製備汽車頂棚部件的傳統輕質GMT複合板材,由作為粘結基體的48wt%熱塑性ES纖維和作為增強材料的52wt%植物纖維組成,並通過熱壓製成汽車頂棚用傳統輕質GMT複合板材,複合板材的面密度為600g/m2。
將所得傳統輕質GMT複合板材通過如下工藝製備汽車棚部件:
(1)將複合板材放入烘箱中,加熱至180-210℃,板材僅在植物纖維內應力的作用下,厚度膨鬆擴展至原來的2.2倍;
(2)上表面覆蓋熱軋無紡布,下表面覆蓋表面裝飾用的泡棉針織面料;
(3)根據頂棚產品性能要求,調節膨化後的壓縮比,模製成大面厚度為5mm體密度為0.12g/cm3的汽車頂棚產品。
對比例4
一種用於製備汽車頂棚部件的傳統輕質GMT複合板材,由作為粘結基體的48wt%熱塑性ES纖維和作為增強材料的52wt%植物纖維組成,並通過熱壓製成汽車頂棚用傳統輕質GMT複合板材,複合板材的面密度為800g/m2。
將所得傳統輕質GMT複合板材通過如下工藝製備汽車棚部件:
(1)將複合板材放入烘箱中,加熱至180-210℃,板材僅在植物纖維內應力的作用下,厚度膨鬆擴展至原來的2.5倍;
(2)上表面覆蓋熱軋無紡布,下表面覆蓋表面裝飾用的泡棉針織面料;
(3)根據頂棚產品性能要求,調節膨化後的壓縮比,模製成大面厚度為5mm 體密度為0.16g/cm3的汽車頂棚產品。
下表2中顯示了利用本發明所述超輕高強GMT複合板和傳統輕質GMT複合板模製的汽車頂棚部件的性能對比。
表2
實施例2在現有輕質GMT複合板材氈網內部引入微球發泡劑3,微球發泡劑3的引入使增強纖維2間的連接方式更加多樣化,除傳統的點連接外,微球發泡劑3作為連接橋梁將其周邊的植物纖維束縛在一起,微球發泡劑3之間又彼此相連接,這些多樣化的連接方式使複合板材內部氈網結構發生了根本改變,因而所製備的頂棚產品在同等密度下相比對比例3機械性能提高明顯,與傳統高密度GMT複合板對比例4機械性能相當,從而使其在保證汽車安全性和強度特性的前 提下,減少自身材料用量,實現超輕化的目的。另外所製備的超輕高強GMT板材在二次成型頂棚產品過程中,在植物纖維內應力和微球發泡劑3的雙重作用下,厚度膨鬆擴展至原來的8倍,相比對比例3提高了近4倍,以此複合板材模製的頂棚產品相比對比例4雖在機械性能上相當,但是所得產品中板材孔隙率高,產品中存有大量滲入空氣,提高了聲傳播的粘滯阻力,因而製品NVH性能提高明顯,如圖4所示。
實施例3
一種用於製備汽車行李架擱物板的高吸音型超輕高強GMT複合板材,由作為粘結基體的33wt%熱塑性聚乙烯纖維20wt%聚酯纖維,作為增強材料的45wt%玄武巖纖維和具有改變增強纖維2間格點連接方式調整板材膨化比功效的2wt%微球發泡劑3組成,並通過熱壓製成汽車行李箱擱物板用超輕高強GMT複合板材,複合板材面密度為1600g/m2。
將所得超輕高強GMT複合板材通過如下工藝製備汽車行李箱擱物板:
(1)將複合板材放入烘箱中,加熱至180-210℃,使板材在玄武巖纖維內應力和微球發泡劑3的雙重作用下,厚度膨鬆擴展至原來的6倍;
(2)上表面覆蓋熱軋無紡布,下表面覆蓋表面裝飾用的針織面料;
(3)根據汽車行李架擱物板性能要求,通過調節膨化後的壓縮比,模製成大面厚度為5mm體密度為0.32g/cm3的汽車行李架擱物板。
對比例5
一種用於製備汽車行李架擱物板的傳統輕質GMT複合板材,由作為粘結基體的33wt%熱塑性聚乙烯纖維22wt%聚酯纖維和作為增強材料的45wt%玄武巖纖維組成,並通過熱壓製成汽車行李架擱物板用傳統輕質GMT複合板材,複合板材面密度為1600g/m2。
將所得傳統輕質GMT複合板材通過如下工藝製備汽車行李架擱物板:
(1)將複合板材放入烘箱中,加熱至180-210℃,板材僅在玻璃纖維內應力的作用下,厚度膨鬆擴展至原來的3倍;
(2)上表面覆蓋熱軋無紡布,下表面覆蓋表面裝飾用的針織面料;
(3)根據汽車行李架擱物板的性能要求,調節膨化後的壓縮比,模製成大面厚度為5mm體密度為0.32g/cm3的汽車行李架擱物板。
對比例6
一種用於製備汽車行李架擱物板的傳統輕質GMT複合板材,由作為粘結基體的33wt%熱塑性聚乙烯纖維22wt%聚酯纖維和作為增強材料的45wt%玄武巖纖維組成,並通過熱壓製成汽車行李架擱物板用傳統輕質GMT複合板材,複合板材面密度為2000g/m2。
將所得傳統輕質GMT複合板材通過如下工藝製備汽車行李架擱物板:
(1)將複合板材放入烘箱中,加熱至180-210℃,板材僅在玄武巖纖維內應力的作用下,厚度膨鬆擴展至原來的3.1倍;
(2)上表面覆蓋熱軋無紡布,下表面覆蓋表面裝飾用的針織面料;
(3)根據汽車行李架擱物板的性能要求,調節膨化後的壓縮比,模製成大面厚度為5mm體密度為0.40g/cm3的汽車行李架擱物板。
下表3中顯示了利用本發明所述超輕高強GMT複合板和傳統輕質GMT複合板模製的汽車行李箱擱物板的性能對比。
表3
實施例3在現有輕質GMT複合板材氈網內部引入微球發泡劑3,微球發泡劑3的引入使增強纖維2間的連接方式更加多樣化,除傳統的點連接外,微球發泡劑3作為連接橋梁將其周邊的玄武巖纖維束縛在一起,微球發泡劑3之間又彼此相連接,這些多樣化的連接方式使複合板材內部氈網結構發生了根本改變,因而所製備的汽車行李架擱物板產品在同等密度下相比對比例5機械性能提高明顯,與傳統高密度GMT複合板對比例6機械性能相當,從而使其在保證汽車安全性和強度特性的前提下,減少自身材料用量,實現超輕化的目的。另外所製備的超輕高強GMT板材在二次成型汽車行李架擱物板產品過程中,在玄武巖纖維內應力和微球發泡劑3的雙重作用下,厚度膨鬆擴展至原來的6倍,相比對比例5提高了近2倍,以此複合板材模製的汽車行李架擱物板相比對比例6雖在機械性能上相當,但是所得產品中板材孔隙率高,產品中存有大量滲入空氣,提高了聲傳播的粘滯阻力,因而製品NVH性能提高明顯。
以上列舉的僅是本發明的一些具體實施例,顯然,本發明不限於以上實施例,還可以有許多變形,本領域的普通技術人員能從本發明公開的內容直接導出或聯想到的所有變形,均應認為是本發明的保護範圍。