包裝袋的邊角切割成型裝置的製作方法
2023-09-27 06:06:05 1
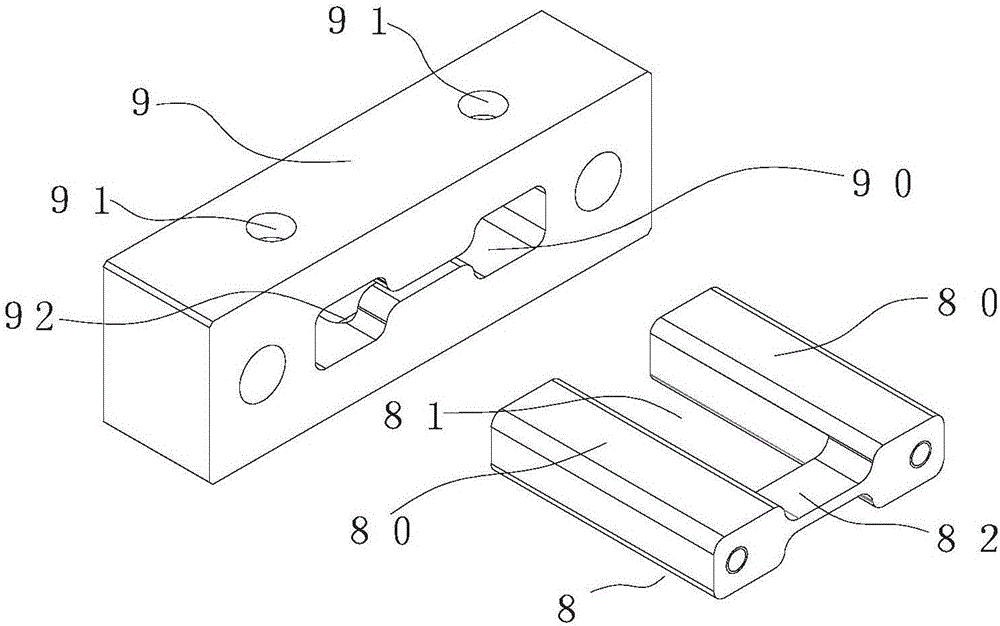
本發明涉及自動化生產過程中包裝袋的分割技術,尤其涉及包裝袋的邊角切割成型裝置。
背景技術:
隨著人們的生活水平的提高,用於包裝食品、藥品、醫療品、雜貨等各種物品的包裝袋種類也越來越多,因而各種食品或是雜貨的包裝越來越豐富多樣,很多包裝袋是正方形或長條形,此類包裝袋由於四角落形成尖細的角,不僅在外形上不夠美觀,而且對於這些採用較硬的材料製成的包裝袋,尖角很刺手,刺壞外包裝,且容易刮傷或勾住其他異物,甚至會造成危險,特別是一些涉及兒童使用的包裝。
因此,將包裝袋的四角切割成大致圓弧狀的技術被廣泛使用。
技術實現要素:
本發明提供一種導向精度高、切割性能好,設備成本低,有效避免卡帶、圓角偏切,可靠地製造規定形狀的切角,一次性完成包裝袋的切割分離、圓角剪切和易撕口的加工,集剪切、導向、自動定中、成品與廢屑分離、自動潤滑於一體;運行穩定,生產效率高,易於操作調試,便於維護保養,使用壽命長,生產使用成本底,生產效率高的包裝袋的邊角切割成型裝置。
為了實現上述發明目的,本發明採用的技術方案是:
包裝袋的邊角切割成型裝置,包括驅動單元、固定架和便於裝填後的連體包裝袋順序流線導入的導帶鬥,驅動單元安裝於固定架前側外壁,所述導帶鬥安裝於固定架上側;
所述固定架內設有對從導帶鬥導入的連體包裝袋的連接邊及上下側邊角的兩側面一體衝裁的前切刀和後切刀,所述驅動單元驅動前切刀直線移動;
所述前切刀呈倒扣「U」字形結構,前切刀兩側設有兩個同向並排排列與後切刀滑動導向配合的柱狀導軌,兩個柱狀導軌之間形成對穿過其間的待衝裁連體包裝袋進行定位的導向槽,前切刀前側端形成與兩側柱狀導軌一體連接用於對連體包裝袋衝裁處按照一定的厚度進行直線和圓角切斷的工形凸刃;
對應的後切刀上前後貫通的設有與前切刀兩側的柱狀導軌滑動導向配合及與前側工形凸刃衝切配合的工形凹嵌槽,工形凹嵌槽下側的後切刀底部鏤空有便於衝裁後的廢料排出和避免廢料擠壓的排出口;
所述固定架後側設有與工形凹嵌槽連通便於前切刀穿過工形凹嵌槽且對前切刀讓位防止碰撞的讓位槽。
優選地,所述固定架由前橫板、後橫板、左側板、右側板和刀盒蓋組成,所述前橫板、右側板、後橫板和左側板的端部依次連接固定成一體,驅動單元安裝於前橫板前側外壁,刀盒蓋安裝固定於一體連接的前橫板、右側板、後橫板和左側板上側,刀盒蓋上設有便於包裝袋導入的導料口,所述導帶鬥安裝於刀盒蓋上的導料口上;所述前切刀和後切刀安裝於刀盒蓋下側的前橫板與後橫板之間,所述後切刀安裝固定於後橫板側面。
優選地,所述前切刀前側設有便於對其固定的切刀座,切刀座與所述驅動單元之間設有便於兩者傳動連接的關節軸承。
優選地,所述驅動單元為氣缸。
優選地,所述後切刀後側與後橫板側面之間還設有便於兩者之間連接固定的墊柱,所述後切刀與墊柱之間形成的空隙便於廢料排出。
優選地,所述導向槽前側從後切刀對應的待衝裁連體包裝袋過料處到工形凸刃處對應的導向槽兩側形成向內收縮便於防止衝裁連體包裝袋卡帶及防止衝切圓角偏角的導向角α,所述導向角α的角度範圍為10°~24°;導向角在兩側的柱狀導軌內側形成兩個中心對稱且傾斜角度相同的導向面,兩個柱狀導軌內側的兩個導向面端部收斂於工形凸刃兩側處的距離與待衝裁連體包裝袋的寬度一致。
優選地,所述工形凸刃的頂端還形成左右對稱分布且向衝裁方向錐狀凸出便於剪切連體包裝袋及與廢料脫離的衝料剪切凸角β,所述衝料剪切凸角β的角度範圍為166°~176°。
優選地,所述後切刀的剪切面還形成左右對稱分布且向工形凸刃方向錐狀凸出便於剪切連體包裝袋及與廢料脫離的下料剪切凸角γ,所述下料剪切凸角γ的角度範圍為166°~176°。
優選地,所述工形凸刃上側或下側對應兩個柱狀導軌的一邊或/和兩邊內側設有向內側凸出一定距離便於在待衝裁連體包裝袋的邊緣形成易撕口的邊口衝凸刃。
優選地,所述後切刀中還設有對兩個柱狀導軌與工形凹嵌槽滑動配合處進行自潤滑供給潤滑油的儲油杯。
本發明的有益效果是:
本發明的導向採用前切刀和後切刀不完全分離的設計,前切刀的兩個柱狀導軌之間的導向槽形成便於待衝裁連體包裝袋穿過其間和進行初步的定位,進一步利用後切刀的工形凹嵌槽與前切刀兩側的兩個柱狀導軌形成滑動配合,且後切刀中還設計有儲油杯,潤滑油能自動供給前後切刀,實現自動潤滑;因此,不需要通過導柱和導套的額外導向配合,避免了因導柱、導套本身的間隙而產生的誤差,造成前切刀和後切刀分離時刀口不能完全對正而產生的撞刀、剪切不斷的問題。
包裝袋的剪切通過前切刀的工形凸刃與後切刀的工形凹嵌槽有效配合,並由氣缸提供動力,對連體包裝袋衝裁處按照一定的厚度進行直線和圓角切斷,有效地切出包裝袋的圓弧角;切刀還可以設計成能切出異形袋以及各種形式的易撕口;前切刀和後切刀中均設計有錐狀凸出便於剪切連體包裝袋及與廢料脫離的剪切凸角,剪切時前後切刀形成先由中間戳穿然後往兩邊剪切的雙剪刀形式的切削,切刀口受力均勻、減小切削受力、縮短剪切時間,使得剪切平順,切出的包裝袋切口光滑,並且增加剪切凸角後,前切刀與切削廢屑的接觸面小,廢屑與前切刀容易分離、掉落,避免廢屑與前切刀粘在一起而影響切屑效果。
連體包裝袋的自動定中,通過前切刀的導向槽兩側形成向內收縮的導向角,形成前大後小的內框,送料時,前切刀的導向槽內框停在大端,形成較大的送料空間,使連體包裝袋的送料過程順暢,避免卡袋;剪切時,前切刀的導向槽內框由大端向小端運動,小端寬度與包裝袋寬度尺寸一致,起到自動導向定中的作用,剪出料的成品圓角均勻、對稱,避免了卡袋、圓角不均勻、切偏的問題。
連體包裝袋成品與廢屑分離過程中,本發明採用成品與廢屑分別通過不同的通道輸出收集的設計,即包裝袋衝裁後的成品在後切刀前面輸出,衝裁後的廢屑從後切刀底部的排出口和後切刀與墊柱之間形成的空隙排出,避免了成品與廢屑混合輸出而產生後續的分揀工序。
本發明的切刀設計簡單,集剪切、導向、自動定中、成品與廢屑分離、自動潤滑於一體,整個裝置運行穩定,生產效率高,易於操作調試,便於維護保養,使用壽命長,大大降低了包裝袋的生產成本。
【附圖說明】
圖1是本發明實施例一的爆炸結構示意圖;
圖2是本發明實施例一中前切刀和後切刀的立體結構放大示意圖;
圖3是本發明實施例一的橫向剖視圖;
圖4是本發明實施例一的縱向剖視圖;
圖5是本發明實施例一的立體放大結構示意圖;
圖6是本發明實施例二中前切刀的主視結構示意圖;
圖7是本發明實施例二中前切刀的立體結構示意圖;
圖8是本發明實施例三中後切刀的主視結構示意圖;
圖9是圖8中的M部放大結構示意圖;
圖10是本發明實施例三中後切刀的立體結構示意圖;
圖11是本發明實施例三中後切刀與實施例二中前切刀的裝配結構示意圖;
圖12是本發明實施例四中後切刀的主視結構示意圖;
圖13是圖12中的I部放大結構示意圖;
圖14是本發明實施例四中後切刀的立體結構示意圖;
圖15是本發明實施例四中前切刀與實施例三中後切刀的裝配結構示意圖;
圖16是本發明實施例五中前切刀的主視結構示意圖;
圖17是本發明實施例五中前切刀的仰視結構示意圖;
圖18是本發明實施例五中前切刀的立體結構示意圖;
圖19是本發明實施例五中後切刀的主視結構示意圖;
圖20是本發明實施例五中後切刀的立體結構示意圖;
圖21是本發明實施例五的立體結構示意圖;
圖22是本發明實施例五的橫向剖視圖;
圖23是本發明實施例五的縱向剖視圖。
以下結合附圖對本發明的具體實施方式作進一步詳細地說明。
【具體實施方式】
實施例一
包裝袋的邊角切割成型裝置,如圖1至圖5所示,包括驅動單元1、固定架和便於裝填後的連體包裝袋X順序流線導入的導帶鬥7,固定架由前橫板2、後橫板3、左側板4、右側板5和刀盒蓋6組成,前橫板2、右側板5、後橫板3和左側板4的端部依次通過螺釘連接固定成一體,該驅動單元1為採用氣動驅動的氣缸,驅動單元1安裝於前橫板2前側外壁,刀盒蓋6安裝固定於一體連接的前橫板2、右側板5、後橫板3和左側板4上側,刀盒蓋6上設有便於包裝袋導入的導料口60,對應的導帶鬥7安裝於刀盒蓋6上的導料口60上。
繼續如圖1至圖5所示,刀盒蓋6下側的前橫板2與後橫板3之間設有對從導帶鬥7導入的連體包裝袋X的連接邊及上下側邊角的兩側面一體衝裁的前切刀8和後切刀9,前切刀8前側設有便於對其固定的切刀座10,切刀座10與驅動單元1之間設有便於兩者傳動連接的關節軸承11,驅動單元1通過關節軸承11和切刀座10驅動前切刀8直線移動;所述後切刀9安裝固定於後橫板3側面,後切刀9後側與後橫板3側面之間還設有便於兩者之間連接固定的墊柱12。
如圖2至圖4所示,前切刀8呈倒扣「U」字形結構,前切刀8兩側設有兩個同向並排排列與後切刀9內腔滑動導向配合的柱狀導軌80,兩個柱狀導軌80之間形成對穿過其間的待衝裁連體包裝袋X進行定位的導向槽81,前切刀8前側端形成與兩側柱狀導軌80一體連接用於對連體包裝袋X衝裁處按照一定的厚度進行直線和圓角切斷的工形凸刃82;對應的後切刀9上前後貫通的設有與前切刀8兩側的柱狀導軌80滑動導向配合及與前側工形凸刃82衝切配合的工形凹嵌槽90,工形凹嵌槽90下側的後切刀底部鏤空有便於衝裁後的廢料排出和避免廢料擠壓的排出口92,其中,後切刀9與墊柱12之間形成的空隙也便於廢料排出;固定架後側的後橫板3上設有與工形凹嵌槽90連通便於前切刀8穿過工形凹嵌槽90且對前切刀8讓位防止碰撞的讓位槽30。另外,在後切刀9中還設有對前切刀8的兩個柱狀導軌80與工形凹嵌槽90滑動配合處進行自潤滑供給潤滑油的儲油杯91。
該實施例的導向採用前切刀8和後切刀9不完全分離的設計,前切刀8的兩個柱狀導軌80之間的導向槽81形成便於待衝裁連體包裝袋穿過其間和進行初步的定位,進一步利用後切刀9的工形凹嵌槽90與前切刀8兩側的兩個柱狀導軌80形成滑動配合,且後切刀9中還設計有儲油杯91,潤滑油能自動供給前後切刀,實現自動潤滑;因此,該實施例不需要通過導柱和導套的額外導向配合,避免了因導柱、導套本身的間隙而差生的誤差,造成的前切刀8和後切刀9分離時刀口不能完全對正而產生的撞刀、剪切不斷的問題,有效的簡化產品的結構。
同時,包裝袋的剪切通過前切刀8的工形凸刃82與後切刀9的工形凹嵌槽90有效配合,並由氣缸提供動力,對連體包裝袋衝裁處按照一定的厚度進行直線和圓角切斷,有效地切出包裝袋的圓弧角,實現一次性完成包裝袋的切割分離、圓角剪切,可靠地製造規定形狀的切角。
而且,連體包裝袋成品與廢屑分離過程中,該實施例採用成品與廢屑分別通過不同通道輸出收集的設計,即包裝袋衝裁後的成品在後切刀9前面下側輸出,衝裁後的廢屑在前切刀8的推動下,一部分衝裁後的廢屑從後切刀底部的排出口92排出,一部分後切刀9與墊柱12之間形成的空隙排出,避免了成品與廢屑混合輸出而產生後續的分揀工序。
實施例二
如圖6和圖7所示,該實施例與實施例一的不同之處在於,前切刀8的導向槽81前側從後切刀對應的待衝裁連體包裝袋過料處到工形凸刃82處對應的導向槽81兩側形成向內收縮便於防止衝裁連體包裝袋卡帶及防止衝切圓角偏角的導向角α,該導向角α的角度為16°,導向角α在兩側的柱狀導軌80內側形成兩個中心對稱且傾斜角度相同的導向面800,相對於16°的導向角,導向面800的傾下角度為8°,兩個柱狀導軌80內側的兩個導向面800端部收斂於工形凸刃82兩側處的距離與待衝裁連體包裝袋的寬度一致。
這樣,通過前切刀8的導向槽81兩側形成向內收縮的導向角α,形成前大後小的內框,送料時,前切刀8的導向槽81內框停在大端,形成較大的送料空間,使連體包裝袋的送料過程順暢,避免卡袋;剪切時,前切刀8的導向槽81內框由大端向小端運動,小端寬度與包裝袋寬度尺寸一致,起到連體包裝袋的自動導向定中的作用,剪出料的成品圓角均勻、對稱,避免了卡袋、圓角不均勻、切偏的問題。
實施例三
如圖8至圖11所示,該實施例與實施例二的不同之處在於,後切刀9的剪切面還形成左右對稱分布且向前切刀8工形凸刃82方向錐狀凸出便於剪切連體包裝袋及與廢料脫離的下料剪切凸角β,該下料剪切凸角β的角度為174°。
採用後切刀設計有錐狀凸出便於剪切連體包裝袋及與廢料脫離的下料剪切凸角β,剪切時後切刀9形成先由中間戳穿然後往兩邊剪切的切削,切刀口受力均勻、減小切削受力、縮短剪切時間,使得剪切平順,切出的包裝袋切口光滑,並且增加剪切凸角後,前切刀與切削廢屑的接觸面小,廢屑與前切刀容易分離、掉落,避免廢屑與前切刀粘在一起而影響切屑效果。
實施例四
如圖12至圖15所示,該實施例與實施例二的不同之處在於,前切刀8的工形凸刃82的頂端面還形成左右對稱分布且向衝裁方向錐狀凸出便於剪切連體包裝袋及與廢料脫離的衝料剪切凸角γ,衝料剪切凸角γ的角度為174°。同時,該實施例中的後切刀9與實施例三中的後切刀結構一致。
這樣,前切刀8和後切刀9中均設計有錐狀凸出便於剪切連體包裝袋及與廢料脫離的剪切凸角,剪切時前後切刀形成先由中間戳穿然後往兩邊剪切的雙剪刀形式的切削,切刀口受力均勻、減小切削受力、縮短剪切時間,使得剪切平順,切出的包裝袋切口光滑,並且增加剪切凸角後,前切刀與切削廢屑的接觸面小,廢屑與前切刀容易分離、掉落,避免廢屑與前切刀粘在一起而影響切屑效果。
實施例五
如圖16至圖23所示,該實施例與以上實施例的不同之處在於,在前切刀8工形凸刃82上側對應兩個柱狀導軌80的和兩邊內側均設有向內側凸出一定距離便於在待衝裁連體包裝袋的邊緣形成易撕口的邊口衝凸刃83;對應的後切刀9的工形凹嵌槽90內形成與邊口衝凸刃83配合的凹槽。
其中,邊口衝凸刃83在連體包裝袋的邊緣衝裁處平切、三角形或異形等各種形式的易撕口;當然,易撕口根據包裝袋的需要,易撕口也可以位於連體包裝袋的一側單邊或雙側的雙邊,或者易撕口是位於連體包裝袋上側邊緣的上切易撕口或位於連體包裝袋下側邊緣的下切易撕口,在前切刀8的對應位置處設置與易撕口匹配的邊口衝凸刃。
該實施例結合了以上實施例的所有優點,一次性完成包裝袋的切割分離、圓角剪切和易撕口的加工,集剪切、導向、自動定中、成品與廢屑分離、自動潤滑於一體;實現整個裝置易於操作調試和便於維護保養,運行穩定,大大提高生產效率高和使用壽命長,有效地降低包裝袋的生產成本。
以上所述實施例只是為本發明的較佳實施例,並非以此限制本發明的實施範圍,凡依本發明之形狀、構造及原理所作的等效變化,均應涵蓋於本發明的保護範圍內。