管件端部錐孔自動化擴孔設備的製作方法
2023-09-18 05:32:45
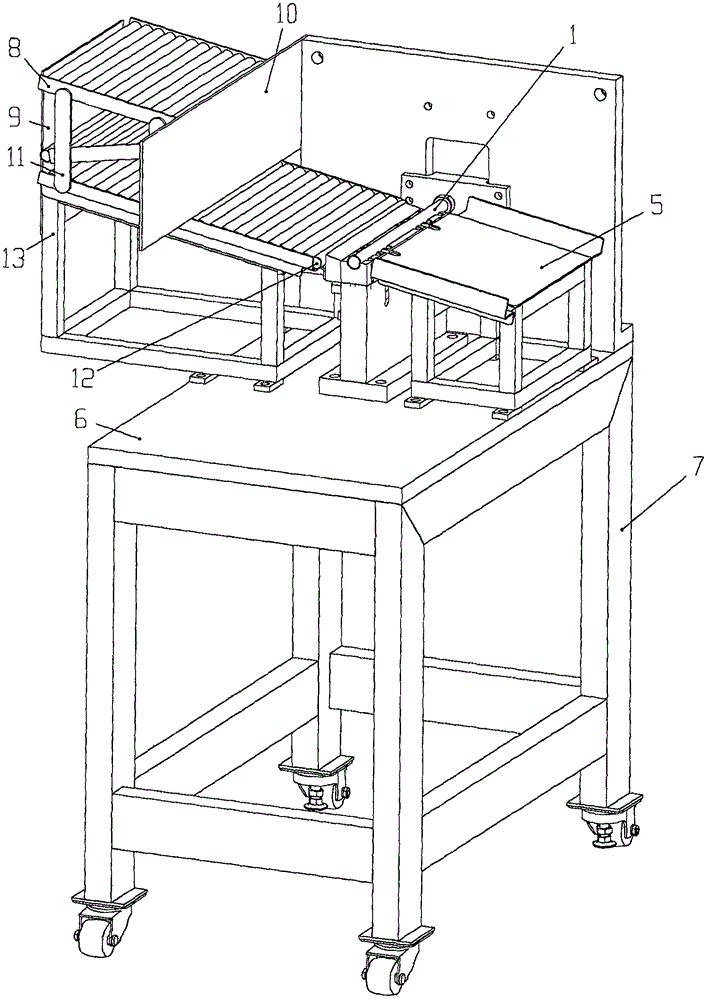
本發明涉及一種自動化設備,尤其涉及一種用於管件端部錐孔的自動化擴孔設備。
背景技術:
管件擴孔,指將管件端部直徑加以擴大,以便增加其承受荷載的區域,是用來增加管件內徑的方法。
管件擴孔的生產過程中,需要耗費大量人工對管件進行擴孔,目前這項工作基本上為人工將管件送入擴孔機中進行擴孔;生產效率低下,且工人工作強度大,並且這種依靠工人的實踐經驗來控制產品質量的方式不符合現代製造業的發展要求,難以可持續發展。
技術實現要素:
本發明的目的在於提供一種管件端部錐孔自動化擴孔設備,將一組若干個管件置於Z型排料架上,再通過上料機構驅動管件自動上料,通過工裝固定機構固定好管件,擴孔機構實現自動化擴孔並下料,從而實現管件擴孔過程全自動完成,大大提高生產效率,並保證了產品質量。
為實現上述目的,本發明本發明公開了一種管件端部錐孔自動化擴孔設備,包括:上料機構、擴孔機構、工裝固定機構、落料槽、工作檯、機架,所述工作檯固連於所述機架上,所述工作檯呈水平放置,所述上料機構固連於所述工作檯上,所述擴孔機構固連於所述工作檯,所述工裝固定機構固連於所述工作檯上,所述落料槽固連於所述工作檯上;
所述上料機構包括Z型排料架、第一擋板、第二擋板、軌道連杆、軌道支架、頂料氣缸、浮動接頭、頂塊、第一頂杆、氣缸支架,所述Z型排料架的底面從上到下依次由三個坡面構成,分別是第一坡面、第二坡面、第三坡面,三個坡面收尾相接呈「Z」字型,所述軌道連杆位於所述Z型排料架的側面,所述軌道連杆固連於所述Z型排料架,所述第一擋板位於所述Z型排料架的背面,所述第一擋板固連於所述Z型排料架,所述第一擋板與所述第二坡面下端部之間的距離為大於管件的直徑並且小於管件的直徑的兩倍,所述第二擋板位於所述Z型排料架的正面,所述第二擋板固連於所述Z型排料架,所述第二擋板與所述第一坡面下端部之間的距離為為大於管件的直徑並且小於管件的直徑的兩倍,送料口位於所述第三坡面下端部;
所述氣缸支架固連於所述工作檯上,所述頂料氣缸的氣缸體固連於所述氣缸支架上,所述頂料氣缸的活塞杆固連於所述浮動接頭,所述浮動接頭固連於所述頂塊,所述第一頂杆固連於所述頂塊,所述第一頂杆位於所述送料口的下方;
所述工裝固定機構包括鍥形塊、管件下模塊、端部抵塊、第一側擋板、側擋塊、壓緊氣缸、壓緊導柱、極限塊、上壓板、管件上模塊、第二頂杆、模塊底座,所述模塊底座固連於所述工作檯,所述管件下模塊固連於所述模塊底座,所述管件下模塊設置有與管件相匹配的型腔,所述第二頂杆固連於所述頂塊,所述第二頂杆位於所述管件下模塊的下方,所述鍥形塊較低的一端固連於所述管件下模塊,所述鍥形塊較高的一端活動連接於所述第三坡面下端部;
所述第一側擋板固連於所述工作檯上,所述側擋塊固連於所述第一側擋板,所述端部抵塊固連於所述側擋塊,所述端部抵塊活動連接於所述管件下模塊中放置的管件;
所述上壓板固連於所述第一側擋板,所述壓緊氣缸的氣缸體固連於所述上壓板,所述壓緊氣缸的活塞杆固連於所述管件上模塊,所述管件上模塊設置有與管件相匹配的型腔,所述壓緊導柱的下端部固連於所述管件上模塊,所述壓緊導柱活動連接於所述上壓板,所述壓緊導柱的上端部固連於所述極限塊,所述緊導柱與所述壓緊氣缸的活塞杆平行布置;
所述擴孔機構包括擴孔氣缸、擴孔極限塊、擴孔導柱、錐形擴孔頭、擴孔壓板、第二側擋板,所述第二側擋板固連於所述工作檯上,所述擴孔氣缸的氣缸體固連於所述第二側擋板,所述擴孔氣缸的的活塞杆活動連接於所述第二側擋板,所述擴孔氣缸的的活塞杆固連於所述擴孔壓板上,所述錐形擴孔頭固連於所述擴孔氣缸的的活塞杆,所述錐形擴孔頭的中心線與所述管件下模塊中放置的管件的中心線重合,所述擴孔導柱固連於所述擴孔壓板,所述擴孔導柱活動連接於所述第二側擋板,所述擴孔導柱固連於所述擴孔極限塊,所述擴孔導柱與所述擴孔氣缸的的活塞杆平行布置。
優選地,所述管件下模塊中放置的管件的端部接觸所述端部抵塊的平面。
優選地,所述第一擋板與所述第二坡面下端部之間的距離為管件直徑的1.1-1.2倍。
和傳統技術相比,本發明管件端部錐孔自動化擴孔設備具有以下積極作用和有益效果:
若干管件一根一根按順序排列於所述Z型排料架上,所述Z型排料架底面從上到下依次由三個坡面構成,分別是第一坡面、第二坡面、第三坡面,呈「Z」字型,所述Z型排料架上放置的管件在重力作用下有向下滑動的趨勢,為了保證需要進料時,排料架上的管件按照「Z」字型下滑,在所述Z型排料架的背面設置有所述第一擋板,所述第一擋板與所述第二坡面下端部之間的距離為大於管件的直徑並且小於管件的直徑的兩倍,在所述Z型排料架的正面設置有所述第二擋板,所述第二擋板固連於所述Z型排料架,所述第二擋板與所述第一坡面下端部之間的距離為大於管件的直徑並且小於管件的直徑的兩倍,在所述Z型排料架的第三坡面底端設置有鍥形塊,所述鍥形塊與第三坡面底端相接觸,所述第三坡面的最底端處的管件被移走時,所述Z型排料架上放置的管件能夠按照「Z」字型有序下滑一個管件位置,且「Z」字型排料可以充分利用空間。
所述送料口位於所述Z型排料架底面最低點處,所述第一頂杆位於所述送料口的下方,所述頂料氣缸的活塞杆向運動時,驅動所述浮動接頭向上運動,與所述浮動接頭固連的所述頂塊向上運動,所述第一頂杆和所述第二頂杆也向上運動。
所述第一頂杆位於所述送料口的下方,所述第二頂杆位於所述管件下模塊的下方,當所述第一頂杆和所述第二頂杆向上運動時,分別推動位於所述送料口的管件和位於所述管件下模塊中的管件均向上頂起;位於所述送料口的管件沿著所述鍥形塊向下滑動,推動所述管件下模塊中的管件沿著所述落料槽向下滑動,同時位於所述送料口的管件進入所述管件下模塊中,由此完成了管件待擴孔件的上料和完成擴孔件的下料。
完成管件帶擴孔件的上料後,所述管件下模塊中的管件的一端與所述端部抵塊相接觸,所述壓緊氣缸的驅動所述管件上模塊向下運動,同時所述壓緊導柱也同時往下運動,所述壓緊氣缸的活塞杆到達最大位置時,所述管件上模塊將所述管件下模塊中的管件壓住,所述管件上模塊設置有與管件相匹配的型腔,所述管件下模塊設置有與管件相匹配的型腔,管件位於所述管件下模塊和所述管件上模塊中的型腔中,而所述壓緊導柱上端部設置的極限塊防止碰撞等意外情況的發生,由此所述工裝固定機構完成了管件的裝夾固定。
所述擴孔氣缸的活塞杆伸出,驅動所述擴孔壓板沿著所述擴孔氣缸的活塞杆伸出方向移動,驅動所述錐形擴孔頭也沿著所述擴孔氣缸的活塞杆伸出方向移動,所述錐形擴孔頭的中心線與所述管件下模塊中放置的管件的中心線重合,因此所述錐形擴孔頭進入已完成裝夾固定的管件端部,而此時管件的另一端與所述端部抵塊的平面相接觸,保證了管件的位置被完全固定。
在所述錐形擴孔頭的張力的作用下,管件完成端部擴孔,根據擴孔錐角的需求可以選取不同的錐形擴孔頭,所述擴孔導柱與所述錐形擴孔頭平行同向運動,而所述擴孔導柱的端部設置的擴孔極限塊防止碰撞等意外情況的發生。
以一組100根管件的擴孔為例,若採用人工擴孔,每根管件的需要花費6-8秒鐘,則100根管件需要工人花費10-13分鐘一刻不停的高負荷勞動才能實現。本發明管件端部錐孔自動化擴孔設備將一組100根管件放置於所述排列架上後,可以完成自動化的上料、夾緊固定、擴孔、下料等一系列的動作,工人僅需花費10餘秒鐘時間將管件放置於所述排料架上,就可以自動完成擴孔工作,大大降低了工人的勞動強度,若一個工人同時看5-6臺設備,則生產效率可以提高5-6倍,工人工作強度降低的同時,使得產品的生產質量不依賴於工人的熟練程度,達到生產效率和產品質量的雙重提升。
通過以下的描述並結合附圖,本發明管件端部錐孔自動化擴孔設備將變得更加清晰,這些附圖用於解釋本發明的實施例。
附圖說明
圖1、2為本發明管件端部錐孔自動化擴孔設備的結構示意圖;
圖3、4為本發明管件端部錐孔自動化擴孔設備上料機構的結構示意圖;
圖5、6為本發明管件端部錐孔自動化擴孔設備工裝固定機構的結構示意圖;
圖7為本發明管件端部錐孔自動化擴孔設備擴孔機構的結構示意圖。
1管件、2上料機構、3擴孔機構、4工裝固定機構、5落料槽、6工作檯、7機架、8 Z型排料架、9第一擋板、10第二擋板、11軌道連杆、12送料口、13軌道支架、14頂料氣缸、15浮動接頭、16頂塊、17第一頂杆、18鍥形塊、19管件下模塊、20端部抵塊、21第一側擋板、22側擋塊、23壓緊氣缸、24壓緊導柱、25極限塊、26上壓板、27管件下模塊、28第二頂杆、29擴孔氣缸、30擴孔極限塊、31擴孔導柱、32錐形擴孔頭、33擴孔壓板、34氣缸支架、35模塊底座、36第二側擋板、37第一坡面、38第二坡面、39第三坡面。
具體實施方式
現在參考附圖描述本發明的實施例,附圖中類似的元件標號代表類似的元件。如上所述,本發明的目的在於提供一種管件端部錐孔自動化擴孔設備,將一組若干個管件置於Z型排料架8上,再通過上料機構2驅動管件1自動上料,通過工裝固定機構4固定好管件,擴孔機構3實現自動化擴孔並下料,從而實現管件1擴孔過程全自動完成,大大提高生產效率,並保證了產品質量。
圖1、2為本發明管件端部錐孔自動化擴孔設備的結構示意圖,圖3、4為本發明管件端部錐孔自動化擴孔設備上料機構的結構示意圖,圖5、6為本發明管件端部錐孔自動化擴孔設備工裝固定機構的結構示意圖,圖7為本發明管件端部錐孔自動化擴孔設備擴孔機構的結構示意圖。
本發明公開了一種管件端部錐孔自動化擴孔設備,包括:上料機構2、擴孔機構3、工裝固定機構4、落料槽5、工作檯6、機架7,所述工作檯6固連於所述機架7上,所述工作檯6呈水平放置,所述上料機構2固連於所述工作檯6上,所述擴孔機構3固連於所述工作檯6,所述工裝固定機構4固連於所述工作檯上,所述落料槽5固連於所述工作檯6上;
所述上料機構2包括Z型排料架8、第一擋板9、第二擋板10、軌道連杆11、軌道支架13、頂料氣缸14、浮動接頭15、頂塊16、第一頂杆17、氣缸支架34,所述Z型排料架8的底面從上到下依次由三個坡面構成,分別是第一坡面37、第二坡面38、第三坡面39,三個坡面收尾相接呈「Z」字型,所述軌道連杆11位於所述Z型排料架8的側面,所述軌道連杆11固連於所述Z型排料架8,所述第一擋板9位於所述Z型排料架8的背面,所述第一擋板9固連於所述Z型排料架8,所述第一擋板9與所述第二坡面38下端部之間的距離為大於管件1的直徑並且小於管件1的直徑的兩倍,所述第二擋板10位於所述Z型排料架8的正面,所述第二擋板10固連於所述Z型排料架8,所述第二擋板10與所述第一坡面37下端部之間的距離為為大於管件1的直徑並且小於管件1的直徑的兩倍,送料口12位於所述第三坡面39下端部;
所述氣缸支架34固連於所述工作檯6上,所述頂料氣缸14的氣缸體固連於所述氣缸支架34上,所述頂料氣缸14的活塞杆固連於所述浮動接頭15,所述浮動接頭15固連於所述頂塊16,所述第一頂杆17固連於所述頂塊16,所述第一頂杆17位於所述送料口12的下方;
所述工裝固定機構4包括鍥形塊18、管件下模塊19、端部抵塊20、第一側擋板21、側擋塊22、壓緊氣缸23、壓緊導柱24、極限塊25、上壓板26、管件上模塊27、第二頂杆28、模塊底座35,所述模塊底座35固連於所述工作檯6,所述管件下模塊19固連於所述模塊底座35,所述管件下模塊19設置有與管件1相匹配的型腔,所述第二頂杆28固連於所述頂塊16,所述第二頂杆28位於所述管件下模塊19的下方,所述鍥形塊18較低的一端固連於所述管件下模塊19,所述鍥形塊18較高的一端活動連接於所述第三坡面39下端部;
所述第一側擋板21固連於所述工作檯6上,所述側擋塊22固連於所述第一側擋板21,所述端部抵塊20固連於所述側擋塊22,所述端部抵塊20活動連接於所述管件下模塊19中放置的管件1;
所述上壓板26固連於所述第一側擋板21,所述壓緊氣缸23的氣缸體固連於所述上壓板26,所述壓緊氣缸23的活塞杆固連於所述管件上模塊27,所述管件上模塊27設置有與管件1相匹配的型腔,所述壓緊導柱24的下端部固連於所述管件上模塊27,所述壓緊導柱24活動連接於所述上壓板26,所述壓緊導柱24的上端部固連於所述極限塊25,所述緊導柱24與所述壓緊氣缸23的活塞杆平行布置;
所述擴孔機構3包括擴孔氣缸29、擴孔極限塊30、擴孔導柱31、錐形擴孔頭32、擴孔壓板33、第二側擋板36,所述第二側擋板36固連於所述工作檯6上,所述擴孔氣缸29的氣缸體固連於所述第二側擋板36,所述擴孔氣缸29的的活塞杆活動連接於所述第二側擋板36,所述擴孔氣缸29的的活塞杆固連於所述擴孔壓板33上,所述錐形擴孔頭32固連於所述擴孔氣缸29的的活塞杆,所述錐形擴孔頭32的中心線與所述管件下模塊19中放置的管件1的中心線重合,所述擴孔導柱31固連於所述擴孔壓板33,所述擴孔導柱31活動連接於所述第二側擋板36,所述擴孔導柱31固連於所述擴孔極限塊30,所述擴孔導柱31與所述擴孔氣缸29的的活塞杆平行布置。
更具體地,所述管件下模塊19中放置的管件1的端部接觸所述端部抵塊20的平面。
更具體地,所述第一擋板9與所述第二坡面38下端部之間的距離為管件1直徑的1.1-1.2倍。
見圖1至圖7,接下來詳細描述本發明管件端部錐孔自動化擴孔設備每個步驟的工作過程和工作原理:
若干管件1一根一根按順序排列於所述Z型排料架8上,所述Z型排料架8底面從上到下依次由三個坡面構成,分別是第一坡面37、第二坡面38、第三坡面39,呈「Z」字型,所述Z型排料架8上放置的管件1在重力作用下有向下滑動的趨勢,為了保證需要進料時,排料架8上的管件1按照「Z」字型下滑,在所述Z型排料架8的背面設置有所述第一擋板9,所述第一擋板9與所述第二坡面38下端部之間的距離為大於管件1的直徑並且小於管件1的直徑的兩倍,在所述Z型排料架8的正面設置有所述第二擋板10,所述第二擋板10固連於所述Z型排料架8,所述第二擋板10與所述第一坡面37下端部之間的距離為大於管件1的直徑並且小於管件1的直徑的兩倍,在所述Z型排料架8的第三坡面39底端設置有鍥形塊18,所述鍥形塊18與第三坡面39底端相接觸,所述第三坡面39的最底端處的管件1被移走時,所述Z型排料架8上放置的管件1能夠按照「Z」字型有序下滑一個管件位置,且「Z」字型排料可以充分利用空間。
所述送料口12位於所述Z型排料架8底面最低點處,所述第一頂杆17位於所述送料口12的下方,所述頂料氣缸14的活塞杆向運動時,驅動所述浮動接頭15向上運動,與所述浮動接頭15固連的所述頂塊16向上運動,所述第一頂杆17和所述第二頂杆28也向上運動。
所述第一頂杆17位於所述送料口12的下方,所述第二頂杆28位於所述管件下模塊19的下方,當所述第一頂杆17和所述第二頂杆28向上運動時,分別推動位於所述送料口12的管件1和位於所述管件下模塊19中的管件1均向上頂起;位於所述送料口12的管件1沿著所述鍥形塊18向下滑動,推動所述管件下模塊19中的管件1沿著所述落料槽5向下滑動,同時位於所述送料口12的管件1進入所述管件下模塊19中,由此完成了管件1待擴孔件的上料和完成擴孔件的下料。
完成管件1帶擴孔件的上料後,所述管件下模塊19中的管件1的一端與所述端部抵塊20相接觸,所述壓緊氣缸23的驅動所述管件上模塊27向下運動,同時所述壓緊導柱24也同時往下運動,所述壓緊氣缸23的活塞杆到達最大位置時,所述管件上模塊27將所述管件下模塊19中的管件1壓住,所述管件上模塊27設置有與管件1相匹配的型腔,所述管件下模塊19設置有與管件1相匹配的型腔,管件1位於所述管件下模塊19和所述管件上模塊27中的型腔中,而所述壓緊導柱24上端部設置的極限塊25防止碰撞等意外情況的發生,由此所述工裝固定機構4完成了管件的裝夾固定。
所述擴孔氣缸29的活塞杆伸出,驅動所述擴孔壓板33沿著所述擴孔氣缸29的活塞杆伸出方向移動,驅動所述錐形擴孔頭32也沿著所述擴孔氣缸29的活塞杆伸出方向移動,所述錐形擴孔頭32的中心線與所述管件下模塊19中放置的管件1的中心線重合,因此所述錐形擴孔頭32進入已完成裝夾固定的管件1端部,而此時管件1的另一端與所述端部抵塊20的平面相接觸,保證了管件1的位置被完全固定。
在所述錐形擴孔頭32的張力的作用下,管件1完成端部擴孔,根據擴孔錐角的需求可以選取不同的錐形擴孔頭32,所述擴孔導柱31與所述錐形擴孔頭32平行同向運動,而所述擴孔導柱31的端部設置的擴孔極限塊30防止碰撞等意外情況的發生。
以一組100根管件的擴孔為例,若採用人工擴孔,每根管件的需要花費6-8秒鐘,則100根管件需要工人花費10-13分鐘一刻不停的高負荷勞動才能實現。本發明管件端部錐孔自動化擴孔設備將一組100根管件放置於所述排列架上後,可以完成自動化的上料、夾緊固定、擴孔、下料等一系列的動作,工人僅需花費10餘秒鐘時間將管件放置於所述排料架上,就可以自動完成擴孔工作,大大降低了工人的勞動強度,若一個工人同時看5-6臺設備,則生產效率可以提高5-6倍,工人工作強度降低的同時,使得產品的生產質量不依賴於工人的熟練程度,達到生產效率和產品質量的雙重提升。
最後,應當指出,以上實施例僅是本發明較有代表性的例子。顯然,本發明不限於上述實施例,還可以有許多變形。凡是依據本發明的技術實質對以上實施例所作的任何簡單修改、等同變化與修飾,均應認為屬於本發明的保護範圍。