一種不鏽鋼過濾膜管的製備方法與流程
2023-12-04 15:38:36 3
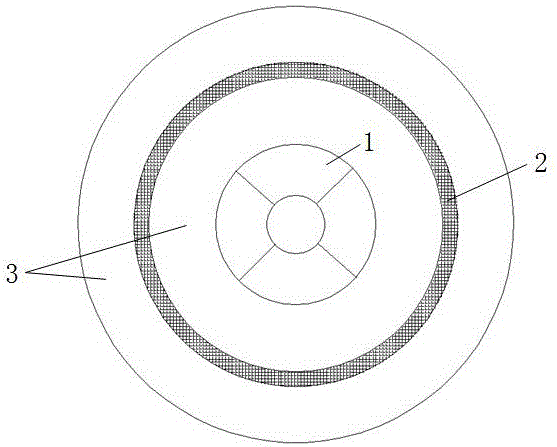
本發明屬於金屬過濾膜管制造領域,具體涉及一種不鏽鋼過濾膜管的製備方法。
背景技術:
金屬過濾膜作為一種新型的分離膜在水處理領域逐漸得到重視。與現有技術中常用的有機過濾膜以及無機過濾膜相比,金屬過濾膜具備良好的化學穩定性、耐熱性、耐酸鹼性,使用壽命比起現有技術中的常用過濾膜種類更長久,而且容易拆換和檢修、便於維護和清洗,同時,金屬過濾膜再生條件好、耐壓性能好、不易破裂、抗震性能好而且易於回收,製備過程對環境無汙染。
金屬過濾膜目前在石油化工、能源、環保、食品和製藥等領域中應用較為廣泛,其滲透性好、孔隙和孔徑可控,具有有機過濾膜和無機過濾膜無法取代的優異性能。隨著現代工業的快速發展,對過濾膜性能的要求越來越高,針對高通量、高精度的要求,金屬過濾膜越來越傾向於被製成過濾膜管進行使用。許多研究者針對金屬過濾膜管的製備進行了開發,從孔徑分布上金屬過濾膜管分為對稱金屬過濾膜管和非對稱金屬過濾膜管。
金屬過濾膜管的製備過程具備以下難點:
1、對於梯度金屬多孔過濾膜管,在保證透過性能的前提下往往在膜管基體表面塗刷一層無機膜來實現對過濾精度的控制,或者通過離心沉積法來製備,上述製備方法都存在金屬膜管基體與塗刷層結合力不佳、結合強度差的缺點,是實際使用的過程中,塗刷層易脫落,導致產品壽命短。
2、對於非對稱金屬過濾膜管,可採用將不同粒度的金屬粉末一層一層分別填充然後燒結的方法,但是這種方法裝料成形的工序複雜、工藝步驟繁複,難以大規模工業化生產。
技術實現要素:
針對目前金屬過濾膜管的製備過程中的缺點,本發明提供了一種新型的金屬過濾膜管的製備方法,通過應用本發明中的製備方法,可以工業化製備出一種非均勻膜孔的不鏽鋼過濾膜管。
本發明所要解決的技術問題通過以下步驟予以實現:
一種不鏽鋼過濾膜管的製備方法,包括以下步驟:
A、將混合不鏽鋼粉末與樹脂粉末混合均勻,其中混合不鏽鋼粉末為將粒徑範圍為5-15μm、25-35μm、40-65μm的三種不鏽鋼粉末進行混合,三種不鏽鋼粉末的質量比為1:(1.1-1.25):1;樹脂粉末的粒徑範圍為10-40μm;
B、在成型模具中置入不鏽鋼纖維氈,固定好芯棒;
C、將步驟A中的混合不鏽鋼粉末裝料成形,利用冷等靜壓機將該過濾管半成品壓製成型,然後脫模得到不鏽鋼過濾管生胚;
D、將步驟C中得到的不鏽鋼過濾管生胚在真空爐中進行燒結,升溫速率為35-55℃/min,燒結溫度為1200-1450℃,在低於燒結溫度150-200℃溫度下保溫0.5-1小時,冷卻後得到所需不鏽鋼過濾膜管。
金屬粉末顆粒的選擇是製備金屬過濾膜的重要環節,製備常規的金屬多濾膜時,一般需要根據要求選擇一定顆粒尺寸分布的粉末進行均勻混合,在燒結時各個部分的燒結收縮率基本相同,製成的產品不易發生燒結變形和表面炸裂,但是很難獲得高的過濾精度和高的透過性能。本發明中涉及的技術方法關鍵在於:通過選擇粒度相差較大的三個粒度分布範圍內的不鏽鋼粉末進行混合裝料,嚴格控制三種不同粒度粉末的質量比,同時通過選擇相匹配粒徑範圍的樹脂粉末及樹脂類型,製備出一種非均勻膜孔的不鏽鋼過濾膜管。在裝料過程中置入不鏽鋼纖維氈,一方面可以起到固定和協助成形的作用,另一方面,在步驟D中進行燒結的過程中,不鏽鋼纖維氈可減少不鏽鋼混合粉末在燒結過程中的流動性,進而防止該不鏽鋼過濾膜管在燒結過程中出現開裂、起皮等問題。
進一步優選,步驟A中混合不鏽鋼粉末為將粒徑範圍為8-10μm、28-30μm、46-48μm的三種不鏽鋼粉末進行混合。三種不鏽鋼粉末粒徑差別較大,尤其是8-10μm與46-48μm範圍的兩種。三種粉末混合後,在燒結的過程中,樹脂被燒損,燒結完成後形成無序的多孔結構。由於三種不鏽鋼粉末並非為連續粒度分布的粉末,而且有粒徑範圍差異比較大的顆粒存在,所以燒結形成的不鏽鋼多孔結構與傳統方法製成的均勻金屬過濾膜不同,其無序度高、厚度可根據需求進行調節,可根據過濾組件的設計進行不鏽鋼過濾膜管的製備。
對步驟A中樹脂粉末的粒徑進行優選,步驟A中樹脂粉末的粒徑範圍為20-30μm。
對步驟A中樹脂粉末的類型進行優選,步驟A中樹脂粉末為熱塑性樹脂粉末。進一步優選,步驟A中樹脂粉末為聚苯醚與聚苯硫醚的混合物,兩者的質量比為1:2-2:1。進一步優選,步驟A中樹脂粉末為聚苯醚與聚醯胺的混合物,兩者的質量比為1:1.5-1:2.5。
在本發明的製備不鏽鋼過濾膜管的工藝方法中,對樹脂粉末的要求首先需要與不鏽鋼粉末具備良好的結合性能,另外,還需要能夠佔據一定的空間,在燒結後能夠留下大量不規則的孔隙。本發明的發明人在實踐中發現,聚苯醚與聚苯硫醚混合物、聚苯醚與聚醯胺的混合物是與不鏽鋼粉末結合力好且能夠形成結構獨特的孔隙的樹脂粉末的選擇,與不鏽鋼粉末混合進行燒結後,所製備得到的不鏽鋼過濾膜管過濾性能好、通量大。
進一步對步驟C中的壓制壓力進行優選,步驟C中壓制的壓力為28-35MPa。
進一步對步驟D中的參數進行優選,步驟D中升溫速率為48℃/min,步驟D中保溫溫度為低於燒結溫度180℃。
本發明具有如下有益效果:
1、本發明在製備不鏽鋼過濾膜管的過程中利用不同粒徑分布範圍的三種不鏽鋼混合粉末與特定樹脂粉末進行燒結,提供了一種新型的金屬過濾膜管的製備方法,製備出了一種過濾性能好、通量大的不鏽鋼過濾膜管。
2、本發明中的不鏽鋼過濾膜管的製備方法簡單易行,適合工業化大量生產。
3、本發明中的不鏽鋼過濾膜管的製備方法中,置入了不鏽鋼纖維氈,可有效防止不鏽鋼過濾膜管在燒結過程中出現開裂、起皮等問題。
附圖說明
附圖1為本發明中不鏽鋼過濾膜管的示意圖。
具體實施方式
下面結合附圖與實施例對本發明的內容進行進一步的描述。
本發明中的實施例按照下述步驟進行製備不鏽鋼過濾膜管:
步驟1:將混合不鏽鋼粉末與樹脂粉末混合均勻;
步驟2:在成型模具中置入不鏽鋼纖維氈,固定好芯棒,選用的不鏽鋼纖維氈為市售產品,過濾精度為25μm;
步驟3:將步驟1中的混合不鏽鋼粉末裝料成形,利用冷等靜壓機將該過濾管半成品壓製成型,然後脫模得到不鏽鋼過濾管生胚;
步驟4:將步驟3中得到的不鏽鋼過濾管生胚在真空爐中進行燒結,保溫、冷卻後得到所需不鏽鋼過濾膜管,其中保溫溫度為低於燒結溫度180℃,保溫時間為1小時。
製備的不鏽鋼過濾膜管如附圖1所示,芯棒1位於中部,標號2所示為不鏽鋼纖維氈,標號3所示為不鏽鋼粉末與樹脂粉末的填充區域。本實施例中的不鏽鋼過濾膜管的製備過程中使用的設備及輔料等於現有技術中不鏽鋼過濾膜管制備過程中相類似,因不涉及到本發明中的創新點,故在此不多加贅述。
步驟1-4中混和不鏽鋼粉末的粒徑、質量比、樹脂粉末的選擇及粒徑、燒結過程的升溫速率如下表所示。
採用的對比例為市售的某品牌不鏽鋼過濾膜管,將上述實施例製得的不鏽鋼過濾膜管與對比例一同進行過濾測試。測試方法為將試驗用去離子水中加入等粒徑的<5μm的示蹤微粒子,本次測試中採用的示蹤微粒子材質為聚甲基丙烯酸甲酯材料,粒子直徑為5±0.5μm,粒子的體積質量為1.19g/cm3,在UV紫外螢光激發下粒子呈青色,該示蹤粒子在去離子水中的個數為1.0×1011個/L。
將上述實施例中製得的不鏽鋼過濾膜管與對比例中過濾膜管以同樣的連接方式製成由10根膜管組成的膜組件,然後進行過濾測試,記錄濾速及去除率如下。
從測試結果可以看出,本實施例中製成的不鏽鋼過濾膜管濾速比市售膜管高,對示蹤粒子的去除效率比市售膜管高,其中實施例9-11最佳。
最後需要說明的是,以上實施例僅用以說明本發明實施例的技術方案而非對其進行限制,儘管參照較佳實施例對本發明實施例進行了詳細的說明,本領域的普通技術人員應當理解依然可以對本發明實施例的技術方案進行修改或者等同替換,而這些修改或者等同替換亦不能使修改後的技術方案脫離本發明實施例技術方案的範圍。