一種固相反應製備尖晶石型鐵氧體材料前驅體的方法與流程
2023-11-01 00:19:12 1
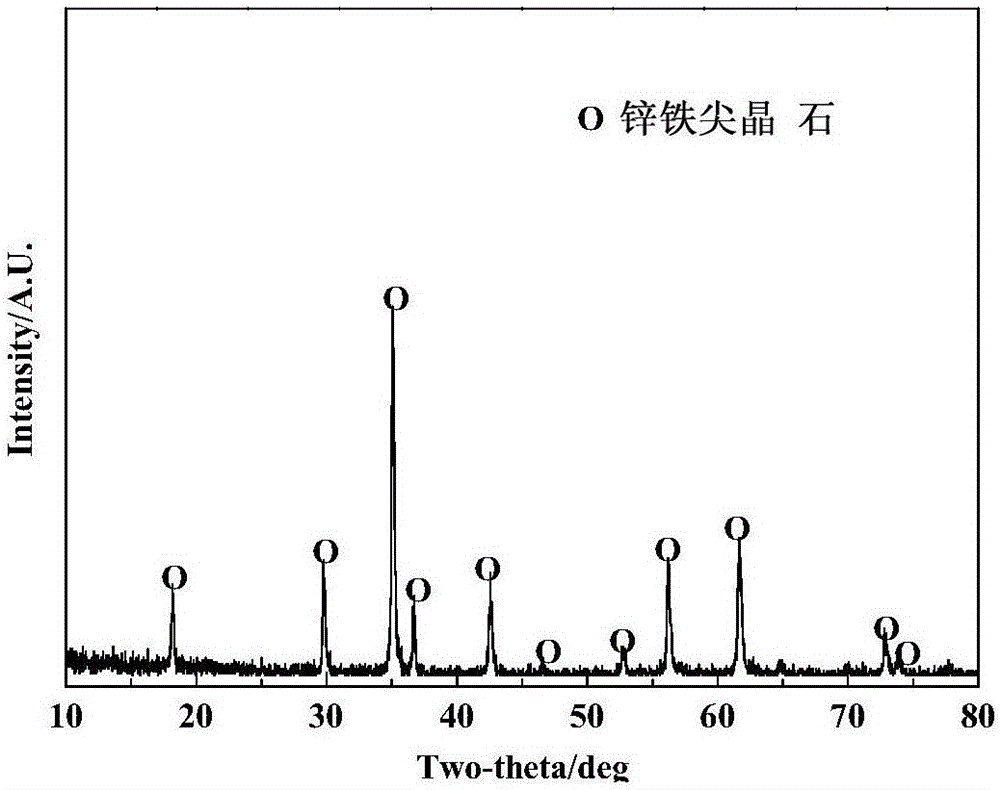
本發明涉及一種尖晶石鐵氧體材料前驅體的製備方法,特別涉及一種固相反應製備尖晶石型鐵氧體材料前驅體的方法,屬於尖晶石型鐵氧體材料的製備領域。
背景技術:
鐵氧體,主要是指鐵和其他一種或者多種金屬元素的複合氧化物,根據晶體結構的不同,主要分為尖晶石型、石榴石型、磁鉛石型(六角型)、鈣鈦礦型、鈦鐵礦型、氯化鈉型、金紅石型七種。其中尖晶石型鐵氧體性質穩定、磁性能優良、製備工藝相對簡單,是發現最早、應用最多的一類鐵氧體,常作為軟磁性材料,製備變壓器電芯、濾波器磁芯、以及磁性記錄元件等;此外尖晶石型鐵氧體還可作為吸波材料,用於製備電磁輻射人體防護、通訊降噪、信息安全保密、以及軍事武器隱身材料等領域。
尖晶石鐵氧體(MFe2O4)中的M主要是指原子半徑與Fe2+接近的二價金屬離子(鎳,錳,鋅,鎂,鋇,鍶等)。在尖晶石鐵氧體的晶體結構中,氧離子按立方緊密堆積排列,二價陽離子充填於八分之一的四面體空隙中,三價鐵離子充填於二分之一的八面體空隙中。
目前製備尖晶石型鐵氧體材料的主要方法包括高溫固相反應法和溼化學合成法。
溼化學合成法包括共沉澱法、溶液凝膠法、水熱合成法等。其主要原理是在可溶性的金屬鹽在溶液體系下,按照目標組要求分配置成均勻的溶液,然後通過改變溶液pH等條件,將複合金屬鹽的羥基前驅體轉化為沉澱等,最後將沉澱洗滌、烘乾、焙燒,即可獲得目標產物。溼化學合成法可以獲得性質穩定、粒度均勻的鐵氧體產品,但是,工藝流程複雜、產率低等缺陷導致此類方法並不能廣泛應用於實際的工業生產中。
燒結法是目前工業生產鐵氧體材料的最主要方法,首先通過配料,精確控制各種金屬氧化物的含量以及比例,再經過球磨、混勻、乾燥,以及一段或者多段燒結過程,保證原料中離子擴散的固相反應過程,由於原料活性差,固相反應速率低,因此,在生產中一般燒結溫度在1000℃-1500℃的範圍,需要焙燒時間長。在實際生產中,為降低燒結時間和溫度,常添加少量助熔劑,這一方面會引入雜質,另一方面導致局部熔融產生燒結液相,不利於後續的加工處理。燒結法的優點是工藝簡單,便於規模化生產,但由於原料固相氧化物活性不高,且需要長時間球磨以保證均勻性,導致燒結法製備產品質量不穩定。助熔劑主要包括CaO、SiO2、Nb2O5、V2O5、Bi2O3、MoO3、TiO2、CuO等中的一種或者幾種組合,用量一般為摩爾比例的1%以下,用量和比例必須嚴格控制,否則會嚴重影響鐵氧體產品性能指標。
因此,開發一種低溫、高效、環保的製備尖晶石型鐵氧體的工藝方法,可以大大緩解我國鐵氧體材料產能不足、仍需大量進口的現狀。
技術實現要素:
針對現有的高溫氧化焙燒製備尖晶石材料技術存在的不足,本發明的目的是在於提供一種焙燒溫度低、時間短的製備高純度尖晶石型鐵氧體材料前驅體的方法。
為了實現上述技術目的,本發明提供了一種固相反應製備尖晶石型鐵氧體材料前驅體的方法,該方法是將鐵氧化物粉末和鐵粉與摻雜金屬氧化物粉末混合球磨後,造塊、乾燥,所得乾燥塊料置於含CO和CO2混合氣氛中,在800~1200℃溫度下進行焙燒,即得尖晶石型鐵氧體材料前驅體。
本發明的技術方案主要是針對傳統的高溫固相反應法製備尖晶石鐵氧體材料的改進。傳統的高溫固相反應法主要是利用高溫過程中,金屬氧化物和鐵氧化物之間的固相反應,而溫度是控制元素擴散的最主要原因,因此,在生產中需要通過提高焙燒溫度來提高反應速率,或者添加少量助熔劑等提高離子遷移速度,但是過高的焙燒溫度和助熔劑的使用會導致少量液相產生,局部熔融不利於後續對產品的加工,也會降低產品性能。本發明的技術方案關鍵在於採用了含CO的氣氛結合金屬鐵粉使用,在兩者的共同活化作用下,使鐵氧化物處於活化狀態,不但有利於加快反應速率,也有利於摻雜的金屬氧化物更容易進入磁鐵礦尖晶石的晶格中,取代二價的鐵離子;同時,使二價鐵離子遷移速度加快,對合成過程有利。通過以上協同作用,可以實現降低焙燒溫度、減少助熔劑的使用,提高了合成效率和產品純度。
優選的方案,所述摻雜金屬氧化物粉末摩爾量為鐵氧化物粉末和鐵粉中鐵總摩爾量的10~50%。
優選的方案,鐵粉摩爾量為鐵氧化物粉末摩爾量的15%以內。
較優選的方案,鐵氧化物粉末包括三氧化二鐵粉末和/或四氧化三鐵粉末。
較優選的方案,摻雜金屬氧化物粉末包括氧化鎳、氧化錳、氧化鋅、氧化鎂、氧化鋇、氧化鍶中的至少一種粉末。
優選的方案,含CO和CO2混合氣氛包括以下體積百分比組分:CO 1~15.5%;CO2 40~84.5%;N2≤50%(0~50%)。
優選的方案,所述焙燒的時間為1~3h。
優選的方案,通過球磨粉碎至混合物料的粒度100%小於-0.045mm。
優選的方案,焙燒產物在保護氣氛下進行冷卻至室溫。所述的保護氣氛一般指氮氣或惰性氣體及它們的組合。如N2和/或Ar。
相對現有技術,本發明的技術方案帶來的有益技術效果:
1)本發明的技術方案最大的優點在於大大降低了固相反應製備尖晶石型鐵氧體材料前驅體的溫度,縮短了反應時間,使反應條件溫和化,達到節能、降低成本的目的。而現有技術中燒結溫度高達1500℃以內的範圍,且焙燒時間長,為降低燒結時間和溫度,往往添加少量助熔劑,助溶劑一方面會引入雜質,另一方面導致局部熔融產生燒結液相,不利於後續的加工處理。而本發明技術方案中,整過合成過程中溫度控制在1200℃以下,合成時間縮短至60~180min,且不需要添加其它含雜質成分的添加劑,大大提高了生產效率,有利於工業化生產。
2)本發明的技術方案製備的尖晶石型鐵氧體材料前驅體純度高,晶體結構均勻穩定,可以直接用於製備鐵氧體產品。克服了傳統固相方法合成的尖晶石型鐵氧體材料前驅體存在均勻性差、晶體結構不均勻等問題。
附圖說明
【圖1】是實施例1的產品XRD圖譜。
【圖2】是對比實施例1的產品XRD圖譜。
具體實施方式
以下實施例旨在進一步說明本發明內容,而不是限制本發明權利要求的保護範圍。
實施例1
將三氧化二鐵、金屬鐵粉、氧化鋅進行配料,其中金屬鐵粉佔含鐵原料的比例為15mol%,氧化鋅佔含鐵原料的比例為50mol%,將原料混合均勻後進行球磨至至粒度100%小於-0.045mm。然後添加10%的水和0.3%的CMC有機粘結劑進行造塊,將團塊乾燥後置於15.5%CO-84.5%CO2組成的混合氣體中,在1000℃焙燒1.5小時,將樣品冷卻後取出,即可獲得鋅鐵尖晶石鐵氧體材料前驅體,產品經XRD定量分析可知,尖晶石含量為98.7%。該條件下獲得的尖晶石鐵氧體XRD分析見圖1所示,圖譜中沒有游離的ZnO的衍射峰,說明基本與鐵氧化物反應完全,進入尖晶石的晶格中。
對比實施例1
將三氧化二鐵、金屬鐵粉、氧化鋅進行配料,其中金屬鐵粉佔含鐵原料的比例為15mol%,氧化鋅佔含鐵原料的比例為50mol%,將原料混合均勻後進行球磨至粒度100%小於-0.045mm。然後添加10%的水和0.3%的CMC有機粘結劑進行造塊,將團塊乾燥後置於惰性氣氛中,在1000℃焙燒1.5小時,將樣品冷卻後取出,即可獲得鋅鐵尖晶石鐵氧體材料前驅體,產品經XRD定量分析可知,尖晶石含量為78.7%。該條件下獲得的尖晶石鐵氧體XRD分析見圖1所示,圖譜中有大量游離的ZnO的衍射峰,說明樣品未反應完全。
實施例2
將四氧化三鐵、金屬鐵粉、氧化錳進行配料,其中金屬鐵粉佔含鐵原料的比例為10mol%,氧化錳佔含鐵原料的比例為20mol%,將原料混合均勻後進行球磨至粒度100%小於-0.045mm。然後添加9.5%的水和0.2%的CMC有機粘結劑進行造塊,將團塊乾燥後置於1.0%CO-80%CO2-19%N2組成的混合氣體中,在1200℃焙燒1小時,將樣品冷卻後取出,即可獲得錳鐵尖晶石鐵氧體材料前驅體,產品經XRD定量分析可知,尖晶石含量為99.7%。
實施例3
將三氧化二鐵、金屬鐵粉、氧化鋅、氧化錳進行配料,其中氧化錳佔含鐵原料的比例為10mol%,氧化鋅佔含鐵原料比例為15mol%,將原料混合均勻後進行球磨至粒度100%小於-0.045mm。然後添加9.5%的水和0.2%的CMC有機粘結劑進行造塊,將團塊乾燥後置於10.5%CO-74.5%CO2-15%N2組成的混合氣體中,在1100℃焙燒2小時,將樣品冷卻後取出,即可獲得錳鋅鐵尖晶石鐵氧體材料前驅體,產品經XRD定量分析可知,尖晶石含量為98.6%。
實施例4
將四氧化三鐵、三氧化二鐵、金屬鐵粉、氧化錳進行配料,其中四氧化三鐵、三氧化二鐵、金屬鐵粉佔含鐵原料的比例分別為40mol%、50mol%、10mol%,其中氧化錳佔含鐵原料的比例為10mol%,將原料混合均勻後進行球磨至粒度100%小於-0.045mm。然後添加9.7%的水和0.4%的CMC有機粘結劑進行造塊,將團塊乾燥後置於10%CO-40%CO2-50%N2組成的混合氣體中,在800℃焙燒3小時,將樣品冷卻後取出,即可獲得錳鐵尖晶石鐵氧體材料前驅體,產品經XRD定量分析可知,尖晶石含量為98.1%。
實施例5
將四氧化三鐵、三氧化二鐵、金屬鐵粉、氧化鎂進行配料,其中四氧化三鐵、三氧化二鐵、金屬鐵粉佔含鐵原料的比例分別為20mol%、70mol%、10mol,其中氧化鎂佔含鐵原料的比例為10mol%,氧化鎂佔含鐵原料比例為10mol%,將原料混合均勻後進行球磨至粒度100%小於-0.045mm。然後添加9.7%的水和0.4%的CMC有機粘結劑進行造塊,將團塊乾燥後置於10%CO-70%CO2-20%N2組成的混合氣體中,在900℃焙燒3小時,將樣品冷卻後取出,即可獲得鎂鐵尖晶石鐵氧體材料前驅體,產品經XRD定量分析可知,尖晶石含量為99.0%。
實施例6
將四氧化三鐵、三氧化二鐵、金屬鐵粉、氧化鎳進行配料,其中四氧化三鐵、三氧化二鐵、金屬鐵粉佔含鐵原料的比例分別為80mol%、15mol%、5mol%,其中氧化鎳佔含鐵原料的比例為20mol%,將原料混合均勻後進行球磨至粒度100%小於-0.045mm。然後添加9.7%的水和0.4%的CMC有機粘結劑進行造塊,將團塊乾燥後置於12%CO-58%CO2-30%N2組成的混合氣體中,在1050℃焙燒2.2小時,將樣品冷卻後取出,即可獲得鎳鐵尖晶石鐵氧體材料前驅體,產品經XRD定量分析可知,尖晶石含量為98.6%。
實施例7
將四氧化三鐵、金屬鐵粉、氧化鋇進行配料,其中四氧化三鐵、金屬鐵粉佔含鐵原料的比例分別為85mol%、15mol%,其中氧化鋇佔含鐵原料的比例為28mol%,將原料混合均勻後進行球磨至粒度100%小於-0.045mm。然後添加9.7%的水和0.4%的CMC有機粘結劑進行造塊,將團塊乾燥後置於3.5%CO-46.5%CO2-50%N2組成的混合氣體中,在1150℃焙燒1.5小時,將樣品冷卻後取出,即可獲得鋇鐵尖晶石鐵氧體材料前驅體,產品經XRD定量分析可知,尖晶石含量為98.8%。
實施例8
將四氧化三鐵、金屬鐵粉、氧化鋇、氧化鍶進行配料,其中四氧化三鐵、金屬鐵粉佔含鐵原料的比例分別為90mol%、10mol%,其中氧化鋇佔含鐵原料的比例為18mol%,氧化鍶佔含鐵原料的比例為8mol%,將原料混合均勻後進行球磨至粒度100%小於-0.045mm。然後添加9.7%的水和0.4%的CMC有機粘結劑進行造塊,將團塊乾燥後置於5.5%CO-74.5%CO2-20%N2組成的混合氣體中,在1100℃焙燒1.7小時,將樣品冷卻後取出,即可獲得鋇鐵尖晶石鐵氧體材料前驅體,產品經XRD定量分析可知,尖晶石含量為98.6%。