一種大型火箭發動機及支架整體翻轉夾具的製作方法
2023-06-08 02:36:37 4
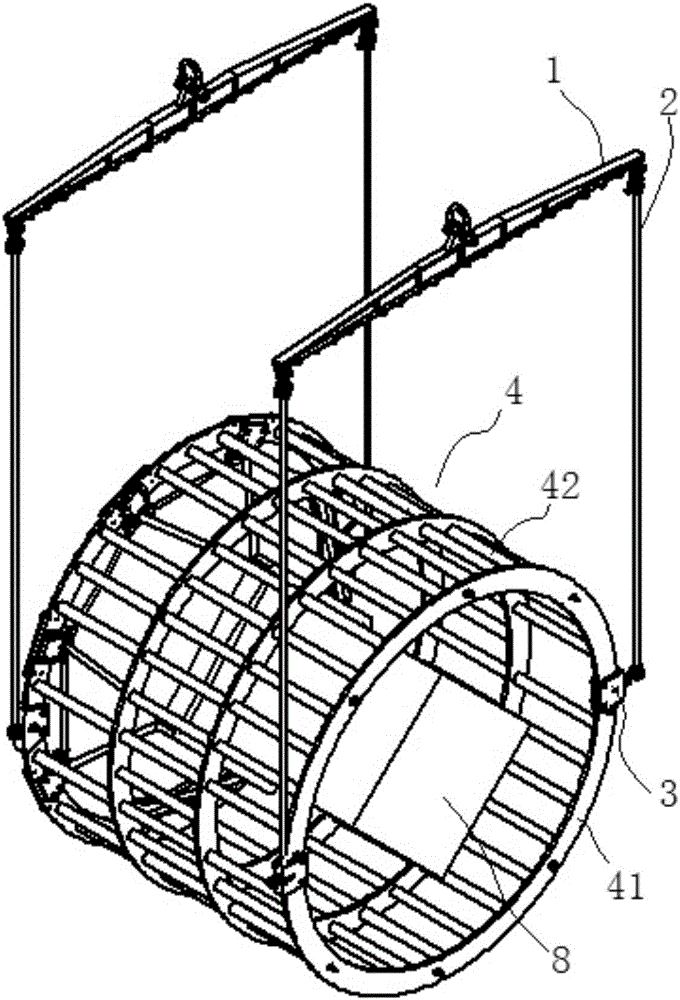
本發明屬於大型太空飛行器力學環境試驗技術領域,具體涉及一種大型火箭發動機及支架整體翻轉夾具。
背景技術:
火箭發動機進行力學環境試驗考核時,由于振動設備推力不足等因素一般僅採用質量及尺寸均相對較小的單機作為試驗件。隨著大推力振動臺的發展及振動試驗技術的成熟,力學環境試驗考核的邊界更加真實,某大型火箭多機並聯發動機及支架需整體進行力學環境試驗考核。試驗過程中,發動機及支架需要採用與箭體安裝方向相反的倒扣形式與振動臺夾具連接,需要將發動機及支架從正常狀態翻轉至倒扣狀態。由於發動機及支架整體尺寸達到3500mm×3500mm×3000mm,質量約3000kg,沒有適用的翻轉夾具和方法實現產品的翻轉。
對於該類型火箭發動機一般根據使用工況設計專用夾具,但在發動機進行振動試驗前,使用工況均為發動機從豎直狀態轉成水平狀態或從水平狀態轉至豎直狀態,而振動試驗過程中,發動機從豎直狀態需轉至倒扣狀態,且需保證倒扣狀態下發動機支架安裝面與振動夾具能安裝。
目前,為保證發動機翻轉過程中的可靠性及通用性,大型火箭發動機翻轉夾具一般採用電機翻轉,成本相對較高,對於本發明中火箭發動機翻轉夾具,工況特殊,使用頻率低,考慮設計一套滿足大型火箭發動機安裝接口要求,可實現發動機180度翻轉,具備安全係數大、成本低特點的翻轉夾具是非常必要的。
技術實現要素:
本發明的目的在於解決上述的技術問題而提供一種大型火箭發動機及支架整體翻轉夾具。
為實現上述目的,本發明採用如下技術方案:
一種大型火箭發動機及支架整體翻轉夾具,包括:
發動機連接主框,所述發動機連接主框的主體為圓筒狀結構,包括多個同軸心間隔設置的環形板以及多個將所述環形板連接起來的軸向均勻間隔設置的連接杆,所述發動機連接主框的兩端分別通過分別通過可拆裝的卡具連接兩根吊繩,每兩所述吊繩可拆裝的連接一個吊梁,所述發動機主框的機架安裝面上布設有多個機架安裝面墊塊,所述機架安裝墊塊的內側與外側分別可拆裝地安裝有機架安裝面連接法蘭、機架安裝面反側連接法蘭。
所述卡具通過螺栓與所述環形端板相連接,且每個環形端板上的卡具為180°對稱安裝。
所述機架安裝面連接法蘭、機架安裝面反側連接法蘭分別與所述機架安裝面側的所述發動機連接主框的環形端板及安裝面墊塊通過螺栓相連接。
所述吊梁採用工字梁焊接結構,吊梁跨度超過發動機連接主框以及卡具外部包絡尺寸;所述吊梁的上端中心設有與吊車連接的圓孔,在所述吊梁與吊車自然懸掛下,所述吊梁呈水平狀態;所述吊梁下端均布用於滿足不同尺寸產品吊裝要求的多個吊孔。
所述吊繩採用鋼絲繩,兩端壓制鋼絲繩套並套有雞心環,所述吊繩一端的所述雞心環通過卸扣與所述吊梁連接而另一端的所述雞心環直接與所述卡具連接。
所述發動機連接主框採用鋼結構焊接而成。
本發明實現了大尺寸大質量火箭發動機及支架的整體單臂翻轉,且翻轉過程平穩可控,保證了發動機的安全性,具備操作性強、成本低的優點。
附圖說明
圖1是本發明的大型火箭發動機及支架整體翻轉夾具翻轉過程的立體結構示意圖;
圖2是本發明的圖1的局部結構圖;
圖3是本發明的圖1翻轉前的結構示意圖;
圖4是本發明的圖3翻轉完成後的結構示意圖。
圖中:1.吊梁,2.吊繩,3.卡具,4.發動機連接主框,5.機架安裝面墊塊,6.機架安裝面連接法蘭,7機架安裝面反側連接法蘭,8.發動機及其機架。
具體實施方式
下面,結合實例對本發明的實質性特點和優勢作進一步的說明,但本發明並不局限於所列的實施例。
參見圖1-4所示,一種大型火箭發動機及支架整體翻轉夾具,包括:
發動機連接主框4,所述發動機連接主框的主體為圓筒狀結構,包括多個同軸心間隔設置的環形板41以及多個將所述環形板連接起來的軸向均勻間隔設置的連接杆42,所述發動機連接主框的兩端分別通過可拆裝的卡具3連接兩根吊繩2,每兩所述吊繩2可拆裝的連接一個吊梁1,所述發動機連接主框4的機架安裝面上布設有多個機架安裝面墊塊5,所述機架安裝墊塊5的內側與外側分別可拆裝地安裝有機架安裝面連接法蘭6、機架安裝面反側連接法蘭7。
所述的機架安裝面墊塊5、機架安裝面連接法蘭6與機架安裝面反側連接法蘭7,主要用於發動機及支架8與發動機連接主框4之間的連接與拆除;吊梁1、吊繩2與卡具3用於實現發動機及支架8與發動機連接主框4的整體翻轉。
其中,所述吊繩為四根,所述機架安裝面墊塊5、機架安裝面連接法蘭6與機架安裝面反側連接法蘭7分別為8個,所述吊梁為2件,所述卡具3為4件。
其中,所述卡具通過螺栓與所述環形端板可拆裝式相連接,且每個環形端板上的卡具為180°對稱安裝。
具體的,在進行使用時,所述機架安裝面連接法蘭、機架安裝面反側連接法蘭分別與機架安裝面側的所述發動機連接主框的環形端板及安裝面墊塊通過螺栓相連接。
具體實現上,所述吊梁採用工字梁焊接結構,所述吊梁的跨度超過發動機連接主框以及卡具外部包絡尺寸;所述吊梁的上端中心設有與用於吊車連接的圓孔,在所述吊梁與吊車自然懸掛下,所述吊梁呈水平狀態;所述吊梁下端均布用於滿足不同尺寸產品吊裝要求的多個吊孔。
所述吊梁在安裝吊車在翻轉狀態下承受發動機、發動機連接主框、機架安裝面墊塊、機架安裝面連接法蘭、機架安裝面反側連接法蘭等質量負載。
具體實現上,所述吊繩採用鋼絲繩,兩端壓制鋼絲繩套並套有雞心環,,所述吊繩一端的所述雞心環通過卸扣與所述吊梁連接而另一端的所述雞心環直接與所述卡具連接,並採用措施防止雞心環滑落。
所述吊繩能滿足承受載荷2.5倍安全係數要求,長度不小於2倍發動機連接主框的高度;翻轉狀態時,吊繩處於豎直狀態。
所述發動機連接主框4的內部安裝尺寸應超過發動機外部包絡尺寸,高度應滿足發動機豎直狀態下不與地面接觸;且發動機連接主框應能承受翻轉狀態下最大載荷。
具體實現上,所述發動機連接主框4採用鋼結構焊接而成,所述機架安裝面墊塊5、機架安裝面連接法蘭6、機架安裝面反側連接法蘭7及卡具3並採用鋼板加工而成
本發明中,所述發動機連接主框4主要承力結構件,連接有機架安裝面墊塊5、機架安裝面連接法蘭6、機架安裝面反側連接法蘭7的環形端板為發動機支架對接面,表面平面度要求高,平面誤差度小於0.1mm。
本實施例使用翻轉夾具進行翻轉作業的步驟如下:
第一步:將各個機架安裝面反側連接法蘭7分別通過螺釘固連在發動機連接主框4上,然後用吊具將發動機整機吊至機架安裝面反側連接法蘭7上側,通過螺釘將發動機及機架8與機架安裝面反側連接法蘭7、機架安裝面墊塊5固連,斷開發動機機架與吊具的連接,如圖3所示;
第二步:將各個機架安裝面連接法蘭6分別通過螺釘固連在發動機連接主框4上,通過擰緊螺釘將機架安裝面連接法蘭6與機架安裝面墊塊5連接;將卡具3分別通過螺釘固連在發動機連接主框4上,卡具3分別通過吊繩2連接雙鉤吊車前後吊車的吊梁1;
第三步:通過控制前後吊車上下距離,實現發動機整機及機架與發動機連接主框整體翻轉,翻轉過程示意圖如圖1所示。待發動機整體翻轉180°後(如圖4所示),拆除由卡具3、吊繩2及吊梁1組成的發動機翻轉吊具;
第四步:拆除機架安裝面連接法蘭6,將發動機及機架8與發動機連接主框4整體吊運至振動夾具處,拆除機架安裝面反側連接法蘭7,吊離發動機連接主框4。
本發明實現了大尺寸大質量火箭發動機及支架的整體單臂翻轉,且翻轉過程平穩可控,保證了發動機的安全性,具備操作性強、成本低的優點。
以上所述僅是本發明的優選實施方式,應當指出,對於本技術領域的普通技術人員來說,在不脫離本發明原理的前提下,還可以做出若干改進和潤飾,這些改進和潤飾也應視為本發明的保護範圍。