反應流出物空冷器流動腐蝕洩漏檢測及風險評估控制方法與流程
2023-09-11 11:18:30 5
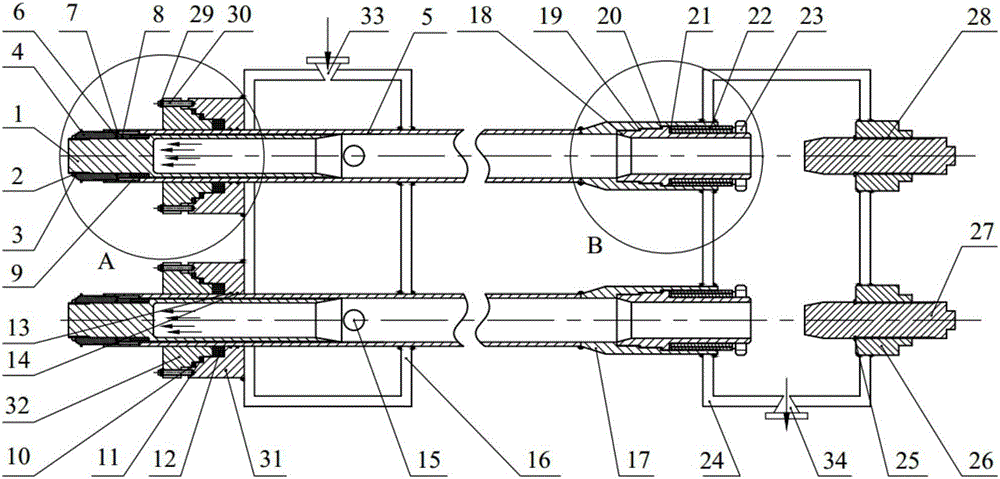
本發明涉及管道或管束類設備腐蝕洩漏的在線監測與防控,具體地說是涉及一種反應流出物空冷器流動腐蝕洩漏檢測及風險評估控制方法。
背景技術:
能源是社會、經濟發展的基礎,煉油工業是能源領域的重要支撐。煉油工業的健康、有序發展,是國家安定和社會平穩的重要基石。隨著原油資源的逐漸枯竭,我國對外國進口原油的依存度逐年增加,預計到2020年將達到70%,且以高硫、高氮、高酸、含氯的劣質原油為主。在原油劣質化、裝置大型化和運行工況苛刻化的發展過程中,我國煉油工業中許多的換熱設備,例如加氫反應流出物空冷器、加氫反應流出物換熱器等普遍出現了嚴重的流動腐蝕現象,換熱管束穿孔洩漏引發的裝置非計劃停工事故屢見不鮮。由於換熱設備管束的工藝過程複雜,涉及到流動、傳熱、相變、腐蝕等一系列問題,且處在高壓(約13MPa)、臨氫工況,服役環境極為苛刻,管束的洩漏穿孔具有明顯的局部性、突發性和風險性,頻繁的非計劃停工及著火死亡等安全事故,不僅嚴重影響企業的生產計劃、成本與效益,而且還嚴重威脅著節能、環保與安全,已成為制約行業可持續發展的重要障礙。
煉油工業中的加氫反應流出物冷換設備,特別是空冷管束,其內徑為19mm,壁厚僅為3mm,且長期處於流動、傳熱、冷卻、相變的複雜流動環境,是國際公認的流動腐蝕高風險設備。自上世紀60年代加氫工藝投用以來,空冷管束的流動腐蝕失效一直未得到有效解決。國際行業組織NACE、API等通過數十年的失效跟蹤調研,形成了國際標準API 932-A/B,主要採用材質升級、原料限定、工藝調整等傳統思路進行腐蝕防控,比較適用於歐美等發達國家的常規油種、穩定工況下的設備運行安全。但是隨著我國原油資源開採進入中後期,生產過程需添加腐蝕性注劑來維持產量;同時進口大量劣質原油,原油劣質化、多變化形成的腐蝕機理複雜性及防控難度已遠超API標準,因強腐蝕環境下的流動腐蝕臨界特性、安全運行區域、失效位置及風險程度不清楚,既缺少定量的預測方法,又缺少科學實用的流動腐蝕洩漏檢測和防控技術。一旦出現加氫空冷器管束的洩漏問題,常規的手段只能是採用停工的方式進行消缺堵漏,嚴重的則會造成火災、爆炸等事故,引起嚴重的社會負面影響。
在加氫空冷器的結構方面,目前常用的結構形式主要有2-2-2、1-1-1-1-1、3-3等結構,其中2-2-2表示2管排3管程結構、1-1-1-1-1表示單管排5管程結構、3-3表示3管排兩管程結構。鑑於各管程之間的間隙極小,若中間管程出現管束的洩漏穿孔,無法通過直觀有效的手段對洩漏的管束進行識別,常規的手段只能是先對裝置進行停工,再通過水壓試驗確定洩漏的管束位號,從而進行管束的堵管堵漏,設備停工造成的物料損失、設備檢維修費用高達200~300萬元。因此,亟需一種科學實用的反應流出物空冷器流動腐蝕洩漏檢測及風險評估控制方法,實現裝置的高效、穩定、長周期運行。
技術實現要素:
為實現煉油工業換熱管束類設備的腐蝕洩漏在線檢測防控,提高設備的連續運行周期,本發明提供一種反應流出物空冷器流動腐蝕洩漏檢測及風險評估控制方法。
本發明包括兩個方面,其一是實現流動腐蝕洩漏的在線檢測技術方法,其二是實現流動腐蝕的風險等級評定以及不停工前提下的流動腐蝕洩漏防控方法,從而降低加氫反應流出物空冷器因流動腐蝕洩漏引發的非計劃停工頻次,滿足加氫裝置的安、穩、長、滿、優可靠運行。
為了達到上述目的,本發明採用的技術方案是包括以下步驟:
1)採用兩排平行布置的管束連接入口管箱和出口管箱,即反應流出物空冷器將上下兩排規格相同的管束結構平行安裝在入口管箱和出口管箱之間,上排包括沿水平方向平行均布的m根管束結構,下排包括沿水平方向平行均布的n根管束結構,且m-n=1,上排和下排的各管束結構沿水平的排列方向交錯布置;管束結構和入口管箱之間通過管束側壁開設的通孔連通,管束結構和出口管箱之間通過管束結構端面的中心孔連通;入口管箱頂部開設有入口法蘭,出口管箱底部開設有出口法蘭;反應流出物空冷器每個管束結構中安裝有沿同一圓周周向均布的四個結構相同的壓力傳感器,將所有壓力傳感器通過耐腐蝕同軸電纜連接至計算機數據採集卡;
2)反應流出物空冷器工作時,從入口法蘭注入多相流介質,經由管束結構的側壁通孔從入口管箱進入管束結構,並從管束結構另一端面的中心孔進入出口管箱,最後從出口法蘭流出;
3)初始階段,在反應流出物空冷器無洩漏狀態時,即正常運行工況時,對每一壓力傳感器PXwi進行壓力標定,將每一壓力傳感器PXwi的初始壓力標記為反應流出物空冷器未洩漏狀態時壓力傳感器PXwi的壓力標定值
其中PXwi表示第X排第w個管束結構中位於i位置處的壓力傳感器,X=m或者n,當X=m時表示安裝在上排管束結構中的壓力傳感器,X=n時表示安裝在下排管束結構中的壓力傳感器,w表示一排中管束結構的序號,i表示同一個管束結構中的四個壓力傳感器的序號位置;
4)反應流出物空冷器運行過程中,利用計算機數據採集卡對所有壓力傳感器進行實時壓力的數據採集;
5)針對安裝於同一個管束結構上的四個壓力傳感器,採用以下公式計算獲得監測壓力值的幾何平均值:
式中:為第X排第w個管束結構中的四個壓力傳感器監測的壓力幾何平均值;式中u、d、l、r分別表示同一管束結構橫截面上的上、下、左、右四個壓力傳感器的相位號,各相位間隔90°;
6)將步驟3)、步驟4)、步驟5)所獲得的每一個壓力傳感器PXwi的壓力標定值和所在管束結構的壓力幾何平均值採用以下公式進行計算獲得壓力偏差值K:
其中,X表示上排管束或者下排管束,w表示一排中管束結構的序號;m表示上排管束的數量,n表示下排管束的數量;
若壓力偏差值K<1%則為III級風險,若壓力偏差值1%≤K<5%則為II級風險,若壓力偏差值K≥5%則為I級風險;
7)根據步驟6)計算得出的壓力偏差值K,若壓力偏差值K≥5%,則認為壓力傳感器所在的管束結構出現流動腐蝕洩漏,馬上堵住管束結構側壁開設的通孔,使得入口管箱和管束之間的連接通道關閉;同時堵住管束結構另一端面的中心孔,使得出口管箱和管束之間的連接通道關閉,以避免所在管束結構發生大腐蝕洩漏狀況,降低爆管風險;
所述的管束結構側壁開設的通孔直徑d滿足:其中D為管束結構的內徑;其目的在於保證多相流介質經兩個水平徑向通孔的流通面積之和與管束5內部流通面積相同,防止多相流介質在管束5內的流速偏大或偏小;
所述方法中,反應流出物空冷器流動腐蝕洩漏檢測的危害源包括NH4Cl、NH4HS吸溼潮解引起的垢下腐蝕洩漏,以及銨鹽溶解於水衝刷腐蝕引起的衝蝕洩漏;
所述的反應流出物空冷器具體包括入口管箱、出口管箱、管束、厚壁管、伸縮管段、壓力傳感器和螺紋壓緊件;入口管箱和出口管箱平行布置並且沿橫截面為矩形,入口管箱布置有上下兩排水平平行的管束,每根管束兩端穿過入口管箱並且管束與入口管箱兩側箱板的通孔之間過盈配合,位於入口管箱內的管束側壁開有用於介質流入到管束內的水平徑向通孔,遠離出口管箱的管束一端通過密封壓緊組件與入口管箱密封連接;靠近出口管箱的管束一端與厚壁管一端連接,厚壁管另一端經壓力傳感組件和出口管箱一側箱板的通孔連接,出口管箱另一側箱板的通孔安裝有用於洩漏時堵塞壓力傳感器組件中套管的絲堵組件;管束內設置有中心通孔,管束端部的通孔內設有用於與伸縮管段外螺紋配合連接的內螺紋。
所述密封壓緊組件包括內凹階梯型固定擋塊、外凸階梯型壓緊塊和伸縮管段;伸出入口管箱外的管束套裝有內凹階梯型固定擋塊和外凸階梯型壓緊塊,內凹階梯型固定擋塊一端面通過焊接與入口管箱側箱板聯接固定,外凸階梯型壓緊塊通過聯接螺栓和螺帽與內凹階梯型固定擋塊另一端面固定連接,與管束外壁連接的內凹階梯型固定擋塊通孔孔壁開設兩道密封槽,兩道密封槽分別嵌入第一O型密封圈和第二O型密封圈;內凹階梯型固定擋塊與外凸階梯型壓緊塊之間的連接端面為階梯型端面,階梯型端面自內向外依次安裝有第一密封圈、第二密封圈和第三密封圈,通過三個密封圈使得內凹階梯型固定擋塊與外凸階梯型壓緊塊之間構成多級高壓密封結構;伸出入口管箱外的管束端面銑有階梯孔,階梯孔大端設有內螺紋,階梯孔小端即為管束的中心通孔;伸縮管段套入管束階梯孔中,伸縮管段套入管束的一端銑有中心盲孔,伸縮管段另一端車有階梯軸肩,伸縮管段階梯軸肩處的管段向外依次套裝有彈性密封圈、滑塊擋塊和軸端擋塊,並在伸縮管段末端裝有第一旋緊螺母和第一墊片,通過第一旋緊螺母和第一墊片軸向壓緊軸端擋塊,軸端擋塊和管束的階梯孔的大端螺紋連接;滑塊擋板和軸端擋塊相聯接的端面之間嵌有第三O型密封圈;滑塊擋板和管束階梯孔大端內壁之間具有間隙,第二墊片連接在滑塊擋塊和管束階梯孔大端內壁之間並支撐在軸端擋塊端面。
所述的壓力傳感組件包括套管、壓力傳感器、螺紋壓緊件和第二旋緊螺母,在和管束連接的所述厚壁管一端的內徑和外徑分別與管束內徑和外徑相同,管束和厚壁管之間通過焊接固定,厚壁管另一端的外徑變大,厚壁管另一端伸入出口管箱並與出口管箱側箱板焊接,靠近出口管箱側箱板的厚壁管一端銑有內凹階梯型中心孔,套管一端套入厚壁管的內凹階梯型中心孔中,套管套入內凹階梯型中心孔的端部外銑有外凸型階梯結構,外凸型階梯結構和內凹階梯型中心孔之間相配合構成階梯密封結構,並依次在階梯臺階之間設置一級密封圈和二級密封圈;套管外凸型階梯結構最大端處套管和厚壁管內壁之間的環向間隙內嵌入有壓力傳感器,壓力傳感器外的套管另一端上套有螺紋壓緊件和第二旋緊螺母,螺紋壓緊件與厚壁管內凹階梯型中心孔的最大端形成螺紋配合,通過螺紋壓緊件將壓力傳感器壓緊在套管外凸型階梯結構最大端和套管另一端的臺階處,螺紋壓緊件軸向通過第二旋緊螺母鎖緊固定。
所述的絲堵組件包括外絲堵和內絲堵,與厚壁管連接側的出口管箱另一側箱板開設有與厚壁管同軸的通孔,通孔內安裝有外絲堵,外絲堵通過焊接與箱板聯接固定;外絲堵開設有內螺紋的通孔,內絲堵通過螺紋旋入外絲堵的螺紋通孔中形成螺紋聯接配合;位於出口管箱內的內絲堵側壁周向開設有環形凹槽,環形凹槽內嵌入外絲堵密封圈,外絲堵密封圈使得外絲堵和內絲堵相密封連接。
伸入入口管箱內的所述伸縮管段一端端面的中心孔為錐孔;伸入厚壁管內凹階梯型中心孔內的套管一端內部中心孔為錐孔。
每個所述的管束結構中,在厚壁管與套管之間的環向間隙內,沿周向間隔均布設置四個壓力傳感器,分別位於套管同一橫截面的上、下、左、右四個位置,各個壓力傳感器安裝的徑向半徑距離均相同。
本發明具有的有益效果是:
本發明能夠有效檢測任意單根管束橫截面上、下、左、右四個位置的壓力變化情況,基於壓力的波動進行流動腐蝕洩漏程度和風險等級的評定,並給出了出現流動腐蝕洩漏狀態時的不停工控制技術,有效降低了原油劣質化、工況苛刻化發展過程中加氫裝置冷換設備的流動腐蝕洩漏風險,防止流動腐蝕大洩漏引發的火災、爆炸等重特大安全事故的發生概率。
附圖說明
圖1是本發明的結構示意圖。
圖2是圖1中A區域的放大圖。
圖3是圖1中B區域的放大圖。
圖4是入口管箱、出口管箱和管束組成的反應流出物空冷器結構示意圖。
圖5是入口管箱的左視圖。
圖6是出口管箱的右視圖。
圖中:1、伸縮管段,2、第一旋緊螺母,3、第一墊片,4、軸端擋塊,5、管束,6、第三O形密封圈,7、第二墊片,8、滑塊擋塊,9、彈性密封圈,10、第三密封圈,11、第二密封圈,12、第一密封圈,13、第二O型密封圈,14、第一O型密封圈,15、水平徑向通孔,16、入口管箱,17、厚壁管,18、套管,19、一級密封圈,20、二級密封圈,21、壓力傳感器,22、螺紋壓緊件,23、第二旋緊螺母,24、出口管箱,25、外絲堵密封圈,26、外絲堵,27、內絲堵,28、內螺紋,29、螺帽,30、聯接螺栓,31、內凹階梯型固定擋塊,32、外凸階梯型壓緊塊,33、入口法蘭,34、出口法蘭。
具體實施方式
下面結合附圖和實施例對本發明作進一步說明。
如圖1所示,本發明實施的反應流出物空冷器具體包括入口管箱16、出口管箱24、管束5、厚壁管17、伸縮管段1、壓力傳感器21和螺紋壓緊件22;入口管箱16和出口管箱24平行布置並且沿橫截面為矩形,入口管箱16布置有上下兩排水平平行的管束5,入口管箱16長邊側面開設通孔,每根管束5兩端穿過入口管箱16並且管束5與入口管箱16兩側箱板的通孔之間過盈配合,位於入口管箱16內的管束5側壁開有用於介質流入到管束5內的水平徑向通孔15,遠離出口管箱24的管束5一端通過密封壓緊組件與入口管箱16密封連接;靠近出口管箱24的管束5一端與厚壁管17一端連接,厚壁管17另一端經壓力傳感組件和出口管箱24一側箱板的通孔連接,出口管箱24另一側箱板的通孔安裝有用於洩漏時堵塞壓力傳感器組件中套管18的絲堵組件;管束5內設置有中心通孔,管束5端部的中心通孔內設有內螺紋,內螺紋用於與伸縮管段1的外螺紋配合連接。
如圖1、圖4所示,入口管箱16頂部和出口管箱24底部分別開有用於多相流介質流入的入口法蘭33和用於多相流介質流出的出口法蘭34,多相流介質經入口管箱16頂部的入口法蘭33進入入口管箱16,接著經水平徑向通孔15進入管束5,經過管束5向出口管箱24流動後從套管18流出到出口管箱24內,最後從出口管箱24底部的出口法蘭34流出。
如圖2所示,所述密封壓緊組件包括內凹階梯型固定擋塊31、外凸階梯型壓緊塊32和伸縮管段1;伸出入口管箱16外的管束5套裝有內凹階梯型固定擋塊31和外凸階梯型壓緊塊32,內凹階梯型固定擋塊31靠近入口管箱16,內凹階梯型固定擋塊31一端面通過焊接與入口管箱16側箱板聯接固定,外凸階梯型壓緊塊32通過聯接螺栓30和螺帽29與內凹階梯型固定擋塊31另一端面固定連接,與管束5外壁連接的內凹階梯型固定擋塊31通孔孔壁開設兩道密封槽,兩道密封槽分別嵌入第一O型密封圈14和第二O型密封圈13。內凹階梯型固定擋塊31與外凸階梯型壓緊塊32之間的連接端面為階梯型端面,階梯型端面自內向外依次安裝有第一密封圈12、第二密封圈11和第三密封圈10,即第一密封圈12、第二密封圈11和第三密封圈10自內向外依次安裝在內凹階梯型固定擋塊31與外凸階梯型壓緊塊32階梯型端面的臺階間形成的間隙中,通過三個密封圈使得內凹階梯型固定擋塊31與外凸階梯型壓緊塊32之間構成多級高壓密封結構。
伸出入口管箱16外的管束5端面銑有階梯孔,階梯孔大端設有內螺紋,階梯孔小端即為管束5的中心通孔。伸縮管段1套入管束5的階梯孔中,伸縮管段1外設有外螺紋,伸縮管段1通過外螺紋旋入管束5內,伸縮管段1套入管束5的一端銑有中心盲孔,伸縮管段1另一端車有階梯軸肩,伸縮管段1階梯軸肩處的管段向外依次套裝有彈性密封圈9、滑塊擋塊8和軸端擋塊4,並在伸縮管段1末端裝有第一旋緊螺母2和第一墊片3,通過第一旋緊螺母2和第一墊片3軸向壓緊軸端擋塊4,軸端擋塊4設有外螺紋,軸端擋塊4和管束5的階梯孔的大端螺紋連接;滑塊擋板8和軸端擋塊4相聯接的端面之間嵌有第三O型密封圈6。滑塊擋板8和管束5階梯孔大端內壁之間具有間隙,第二墊片7連接在滑塊擋塊8和管束5階梯孔大端內壁之間並支撐在軸端擋塊4端面。
如圖3所示,壓力傳感組件包括套管18、壓力傳感器21、螺紋壓緊件22和第二旋緊螺母23,在和管束5連接的所述厚壁管17一端的內徑和外徑分別與管束5內徑和外徑相同,管束5和厚壁管17之間通過焊接固定,厚壁管17另一端的外徑變大,厚壁管17另一端伸入出口管箱24並與出口管箱24側箱板焊接,靠近出口管箱24側箱板的厚壁管17一端銑有內凹階梯型中心孔,套管18一端套入厚壁管17的內凹階梯型中心孔中,套管18套入內凹階梯型中心孔的端部外銑有外凸型階梯結構,外凸型階梯結構和內凹階梯型中心孔之間相配合構成階梯密封結構,並依次在階梯臺階之間設置一級密封圈19和二級密封圈20;套管18外凸型階梯結構最大端處套管18和厚壁管17內壁之間的環向間隙內嵌入有壓力傳感器21,壓力傳感器21外的套管18另一端上套有螺紋壓緊件22和第二旋緊螺母23;螺紋壓緊件22設有外螺紋,厚壁管17內凹階梯型中心孔的大端設有內螺紋,螺紋壓緊件22與厚壁管17內凹階梯型中心孔的最大端形成螺紋配合,通過螺紋壓緊件22將壓力傳感器21壓緊在套管18外凸型階梯結構最大端和套管18另一端的臺階處,螺紋壓緊件22軸向通過第二旋緊螺母23鎖緊固定。
如圖1所示,絲堵組件包括外絲堵26和內絲堵27,與厚壁管17連接側的出口管箱24另一側箱板開設有與厚壁管17同軸的通孔,通孔內安裝有外絲堵26,外絲堵26通過焊接與箱板聯接固定;外絲堵26開設有螺紋通孔,內絲堵27通過螺紋旋入外絲堵26的螺紋通孔中形成螺紋聯接配合;內絲堵27伸入出口管箱24內,位於出口管箱24內的內絲堵27側壁周向開設有環形凹槽,環形凹槽內嵌入外絲堵密封圈25,外絲堵密封圈25使得外絲堵26和內絲堵27相密封連接。
如圖1、圖3所示,伸入入口管箱16內的所述伸縮管段1一端端面的中心孔設置內倒錐角,即為錐孔,實現結構的平穩過渡,防止流體流動出現渦流效應。另外,伸入厚壁管17內凹階梯型中心孔內的套管18一端內部中心孔設置內倒錐角,即設置外凸型階梯結構的套管18一端中心孔為錐孔,保證多相流介質自管束5向套管18內部流通過程中平穩流動,防止衝刷腐蝕。
每個所述的管束結構中,在厚壁管與套管之間的環向間隙內,沿周向間隔均布設置四個壓力傳感器,分別位於套管同一橫截面的上、下、左、右四個位置,各個壓力傳感器安裝的徑向半徑距離均相同。
當管束出現洩漏狀態時,通過旋轉伸縮管段1端部的第一旋緊螺母2將伸縮管段1向管束5內旋進,使銑中心盲孔的伸縮管段末端封閉入口管箱內管束5的水平徑向通孔15,從而關閉入口管箱16內部多相流介質通向管束5的通道;類似地,亦可通過旋轉第一旋緊螺母2將伸縮管段向管束5外旋出,從而打開入口管箱內管束5的水平徑向通孔15。
當管束出現洩漏狀態時,向出口管箱24內部旋進內絲堵27,使得內絲堵27端部封閉套管18端面的中心孔,從而關閉套管18出口與出口管箱24之間的連接通道。
本發明的具體工作過程如下:
①採用兩排平行布置的管束連接入口管箱和出口管箱,即反應流出物空冷器將上、下兩排規格相同的管束結構平行安裝在入口管箱和出口管箱之間,上排包括沿水平方向平行均布的m根管束結構,下排包括沿水平方向平行均布的n根管束結構,且m-n=1;圖5為未安裝密封壓緊組件的入口管箱左視圖,圖6為未安裝外絲堵和內絲堵狀態時的出口管箱右視圖;其中,上排、下排的各管束結構沿水平的排列方向交錯布置,其結構分別如圖5和圖6所示。
其中,沿上、下兩排管束的末端,厚壁管一端與套管間的環向間隙內,沿周向均布的上、下、左、右四個位置設置結構相同的壓力傳感器,各個壓力傳感器安裝的軸向位置及徑向方位均相同。
②定義安裝在上排、下排管束的壓力傳感器位號分別為Pmw、Pnw,其中對應徑向切面的上、下、左、右四個位置的壓力傳感器分別定義為PXwi,其中i分別對應上、下、左、右四個位置的壓力傳感器,即i=u、i=d、i=l或i=r;當X=m時,表示對應安裝在上排管束中的壓力傳感器,X=n時則對應安裝在下排管束中的壓力傳感器,w為對應的管束位號,w的取值域為w∈[1,m+n]。
③將安裝在反應流出物空冷器任意一位置的PXwi的壓力傳感器通過耐腐蝕同軸電纜連接至計算機採集卡。
④反應流出物空冷器運行過程中,由油、氣、水多相流介質構成的加氫反應流出物自入口法蘭進入入口法蘭,經由入口管箱內部的水平徑向通孔從入口管箱進入管束結構,再從套管18流入到出口管箱,最終從出口管箱底部的出口法蘭流出,完成一個持續的冷卻過程;該過程中,利用計算機數據採集卡對所有壓力傳感器進行實時壓力的採集,並繪製單位時間t內的實時壓力值曲線。
⑤開工初期,保證反應流出物空冷器無洩漏狀態時,對安裝在反應流出物空冷器任意一位置的壓力傳感器PXwi進行壓力標定,標記為反應流出物空冷器未洩漏狀態時的壓力標定值
⑥對安裝於任意一根管束上沿周向布置的上、下、左、右四個位置的壓力傳感器,採用以下公式取壓力的幾何平均值,即表示為:
式中:為第X排第w個管束結構中四個壓力傳感器監測的壓力傳感器幾何平均值;式中u、d、l、r分別表示同一管束結構橫截面上的上、下、左、右四個壓力傳感器的相位號,各相位間隔90°;
⑦反應流出物空冷器運行過程中,利用計算機數據採集卡對壓力傳感器的壓力進行採集,獲取任意管束位號為w的四個壓力傳感器的壓力幾何平均值若監測獲得的壓力幾何平均值與該根管束壓力標定值的壓力偏差值K<1%,定義為Ⅲ級風險,若1%≤K<5%,定義為Ⅱ級風險,若K≥5%,定義為Ⅰ級風險;其中壓力偏差值K計算定義為:
其中,X表示上排管束或者下排管束,w表示一排中管束結構的序號;m表示上排管束的數量,n表示下排管束的數量;
⑧根據步驟⑤⑥⑦計算得出的壓力偏差值K,若滿足K≥5%,則可認為對應上排或下排的第w根管束出現腐蝕洩漏;此時,立即調整位於伸縮管段末端的旋緊螺母,使銑中心盲孔的伸縮管段末端封閉入口管箱內管束開設的水平徑向通孔,關閉入口管箱內部介質通向管束5的通道;同時,調整位於外絲堵和內絲堵之間的螺紋配合,通過旋進內絲堵外端使內絲堵內端旋入套管18內部,關閉套管出口與出口管箱之間的連接通道,避免所在管束結構,即第w根管束髮生大腐蝕洩漏狀況,降低爆管風險。並且可以保證加氫空冷管束系統不停工持續運行,待達到運行檢驗周期,即大檢修時再停工進行管束更換。
⑨按照上述步驟進行分析能夠經一部對壓力傳感器的監測數據進行單位時間t內的歷史數據查詢,適用於加氫反應流出物空冷器管束的失效原因分析、失效時的工況確認等,為其他同類裝置的優化操作、安全運行提供指導。
需特殊說明的是位於入口管箱16內的管束5開設的水平徑向通孔15,其原因在於若經入口法蘭進入入口管箱16的介質為氣液固多相流,為防止重力影響導致管束底部液固相較多,從而開設的是水平徑向通孔15,可以實現氣液固多相流介質充分進入管束5,避免堵塞。而假如進入入口管箱16的介質為氣相,那麼不考慮密度差異的工況,那麼水平徑向通孔亦可改為豎直徑向通孔。類似的,本發明實施例給出的反應流出物空冷器管束形式為雙管排結構,同樣適用於其他例如單管排、多管排或單根管束的管束結構。
上述具體實施方式用來解釋說明本發明,而不是對本發明進行限制,在本發明的精神和權利要求的保護範圍內,對本發明作出的任何修改和改變,都落入本發明的保護範圍。