汽車用保險槓、保險槓的製造方法以及保險槓的車身安裝結構與流程
2023-10-08 15:06:19 2
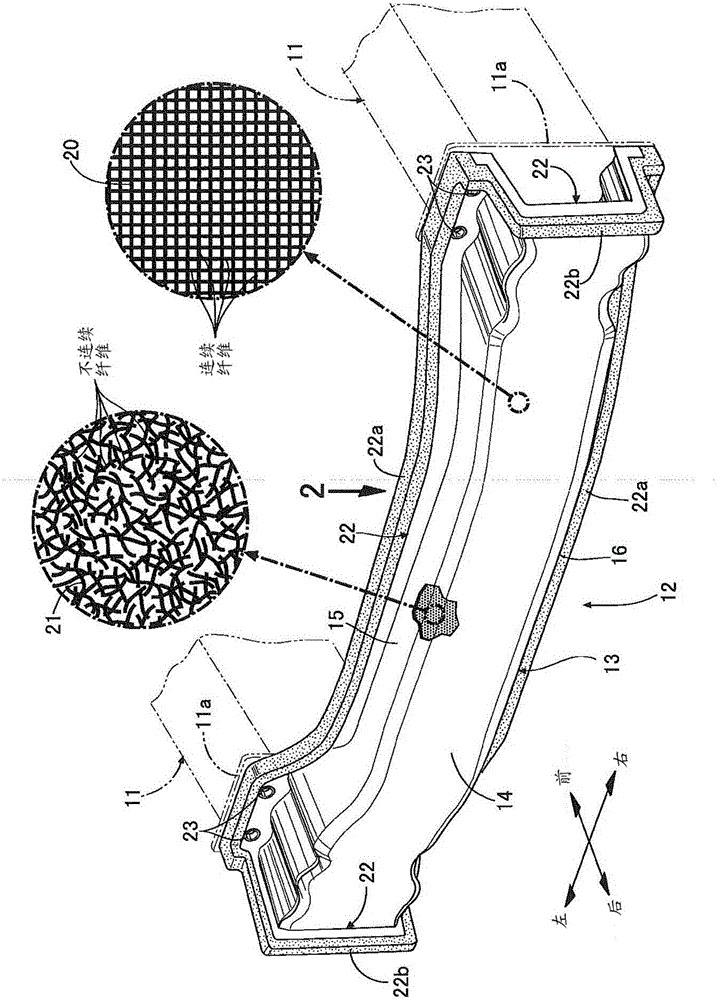
本發明涉及一種汽車用保險槓、保險槓的製造方法以及保險槓的車身安裝結構。沿著車寬方向配置的纖維增強樹脂制的保險槓具有:保險槓主體,其具有向前後方向的內側開放的日文片假名「コ」字形的剖面;凸緣部,其從所述保險槓主體的端部邊緣開始延伸。所述保險槓主體和所述凸緣部包括連續纖維增強樹脂層。
背景技術:
在下述專利文件1中,公開有一種具有樹脂層和連續纖維增強樹脂層的2層結構的保險槓的製造方法,其將不包含纖維的熱可塑性樹脂和包含連續纖維的熱可塑性樹脂重疊,再由壓力加工模具進行壓力加工成型。
現有技術文獻
專利文獻
【專利文獻1】日本發明專利公報特表2000-515828號
技術實現要素:
但是,所述現有技術的製造方法中,連續纖維增強樹脂層中包含的連續纖維的切斷端部會從產品端部邊緣伸出形成毛刺,這種毛刺可能接觸到工作人員的手而降低作業效率,並降低產品的美觀性。因此,有必要在產品壓力加工成型後,對於連續纖維伸出而形成毛刺的產品的端部邊緣進行修整加工,將其光滑地切斷,但是由此產生了由於增加加工工時而導致成本上升的問題。
本發明是鑑於所述問題而做出的,其目的在於,不必進行修整加工,也可以防止連續纖維由包含連續纖維增強樹脂層的保險槓的端部邊緣伸出而產生毛刺。
本發明的第1技術方案為,一種汽車用保險槓,沿著車寬方向配置的纖維增強樹脂制的保險槓具有:保險槓主體,其具有向前後方向的內側開放的日文片假名「コ」字形的剖面;凸緣部,其從所述保險槓主體的端部邊緣開始延伸,
所述保險槓主體和所述凸緣部包括連續纖維增強樹脂層,
該汽車用保險槓的特徵在於,
在所述保險槓的所述凸緣部,位於上側與下側的的端部邊緣連接有熱可塑性樹脂制的第1凸緣頂端部,第1凸緣頂端部向上下方向外側延伸並向前後方向外側彎折,形成L字形剖面。
本發明的第2技術方案為,根據第1技術方案所述的汽車用保險槓,其特徵在於,
所述保險槓主體以及所述凸緣部是在所述連續纖維增強樹脂層上層積了不連續纖維增強樹脂層的2層構造,而所述凸緣部的所述不連續纖維增強樹脂層比所述保險槓主體的所述不連續纖維增強樹脂層厚。
本發明的第3技術方案為,根據第1技術方案或第2技術方案所述的汽車用保險槓,其特徵在於,
在所述保險槓主體和所述凸緣部的分界處,所述連續纖維增強樹脂層平滑地彎曲。
本發明的第4技術方案為,根據第1技術方案~第3技術方案中任意一項所述的汽車用保險槓,其特徵在於,
在所述保險槓的位於車寬方向兩側的所述凸緣部的端部邊緣上連接有熱可塑性樹脂制的第2凸緣頂端部,第2凸緣頂端部向上下方向外側或向前後方向外側延伸,形成I字形剖面。
本發明的第5技術方案為,根據第1技術方案~第4技術方案中任意一項所述的汽車用保險槓,其特徵在於,
在所述保險槓主體的前後方向外表面上設有熱可塑性樹脂制的蜂窩結構體。
本發明的第6技術方案為,一種汽車用保險槓的製造方法,是第1技術方案~第5技術方案中任意一項所述的保險槓的製造方法,其特徵在於,
該汽車用保險槓的製造方法具有:
第1工序,使用壓力加工成型模具,對預浸漬片(pre preg)進行熱壓力加工加工,成型所述保險槓主體和所述凸緣部;
第2工序,向所述壓力加工成型模具內的、形成於對著所述凸緣部的端部邊緣的位置的空間注入熱可塑性樹脂,成型所述第1凸緣頂端部。
本發明的第7技術方案為,根據第6技術方案所述的汽車用保險槓的製造方法,其特徵在於,
該汽車用保險槓的製造方法還具有:
第3工序,其在所述第2工序之後,在所述凸緣部上形成安裝孔;
第4工序,通過壓入或嵌緊,將軸環固定於所述安裝孔。
本發明的第8技術方案為,根據第6技術方案或第7技術方案所述的汽車用保險槓的製造方法,其特徵在於,
在所述第1工序中,所述預浸漬片由層積的不連續纖維預浸漬片和連續纖維預浸漬片構成,所述壓力加工成型模具的陰模和陽模的成型面的間隔,在所述保險槓主體和所述凸緣部的分界處比其他的部分大。
本發明的第9技術方案為,一種保險槓的車身安裝結構,是將第1技術方案~第5技術方案中任意一項所述的保險槓固定於車身框架部件的保險槓的車身安裝結構,其特徵在於,
在設置於所述保險槓的所述凸緣部的所述安裝孔上,嵌合在前後方向內端一體具有凸緣的帶凸緣軸環,將一體具有凸緣的帶凸緣螺栓從前後方向外側貫穿所述帶凸緣軸環緊固於所述車身框架部件時,在所述帶凸緣螺栓的所述凸緣和所述保險槓的所述凸緣部的前後方向外表面之間配置了彈性材料。
另外,實施方式的安裝板11a與本發明的車身框架部件相對應,實施方式的後保險槓12與本發明的保險槓相對應,實施方式的連續纖維預浸漬片20ˊ以及不連續纖維預浸漬片21ˊ與本發明的預浸漬片相對應,實施方式的帶凸緣軸環23與本發明的軸環相對應。
根據第1技術方案,沿著車寬方向配置的纖維增強樹脂制的保險槓具有:保險槓主體,其具有向前後方向的內側開放的日文字母「コ」字形的剖面;凸緣部,其從保險槓主體的端部邊緣開始延伸。保險槓主體和凸緣部包括連續纖維增強樹脂層。在保險槓上下的凸緣部的端部邊緣,連接有向上下方向外側延伸並向前後方向外側彎折,具有L字形剖面的熱可塑性樹脂制的第1凸緣頂端部,因此即使連續纖維增強樹脂層的連續纖維或鑄型樹脂從凸緣部的端部邊緣伸出而形成毛刺,也可以用第1凸緣頂端部覆蓋,因此不需要進行去除毛刺的修整加工,也可以提高產品品質。另外,即使在向壓力加工成型模具內部設置預浸漬片時發生錯位,由於第1凸緣頂端部形成L字形的剖面,因此預浸漬片的端部邊緣無法到達L字形剖面的頂端,確保了成型第1凸緣頂端部的空間,可以更加切實地防止毛刺露出。
根據第2技術方案,由於保險槓主體以及凸緣部是在連續纖維增強樹脂層上層積了不連續纖維增強樹脂層而成的2層構造,而凸緣部的不連續纖維增強樹脂層要比保險槓主體的不連續纖維增強樹脂層厚,因此可以由成型性優異的不連續纖維增強樹脂層容易地加厚凸緣部,由較厚的凸緣部提高保險槓的安裝強度。
根據第3技術方案,在保險槓主體以及凸緣部的分界部,連續纖維增強樹脂層平滑地彎折,因此在使用壓力加工成型模具成型保險槓時,可以防止連續纖維增強樹脂層在所述分界部急劇地彎折而導致連續纖維破損斷裂。
根據第4技術方案,在保險槓的車寬方向兩側的凸緣部的端部邊緣上,連接有向上下方向外側或向前後方向外側延伸的、具有I字形剖面的熱可塑性樹脂制的第2凸緣頂端部,因此可以由第1凸緣頂端部以及第2凸緣頂端部整周覆蓋保險槓的凸緣部的端部邊緣,防止露出毛刺。
根據第5技術方案,由於在保險槓主體的前後方向外表面上設置有熱可塑性樹脂制的蜂窩結構體,因此,在發生碰撞時,可以通過壓壞蜂窩結構體,增加對碰撞能量的吸收。
根據第6技術方案,由於具有使用壓力加工成型模具對預浸漬片進行熱壓力加工加工,成型保險槓主體和凸緣部的第1工序,以及向壓力加工成型模具內的、形成於對著凸緣部的端部邊緣的位置的空間注入熱可塑性樹脂,成型第1凸緣頂端部的第2工序,因此,可以利用成型保險槓主體以及凸緣部的壓力加工成型模具,成型第1凸緣頂端部,從而節省設備費用和加工工時。
根據第7技術方案,在第2工序之後,具有在凸緣部上形成安裝孔的第3工序,以及通過壓入或嵌緊,將軸環固定於安裝孔的第4工序,因此,可以使用套管增強凸緣部的安裝孔,提高保險槓對車身的安裝強度。
根據第8技術方案,在第1工序中,預浸漬片由層積的不連續纖維預浸漬片和連續纖維預浸漬片構成,壓力加工成型模具的陰模和陽模的成型面的間隔,在保險槓主體和凸緣部的分界處比其他的部分大,因此,在所述分界處的不連續纖維增強樹脂層的厚度比別的部分大,由較厚的不連續纖維增強樹脂層提高所述分界處的連續纖維增強樹脂層的變形自由度,因此可以防止連續纖維增強樹脂層急劇地彎折而導致連續纖維破損斷裂。
根據第9技術方案,在設置於保險槓的凸緣部的安裝孔上,嵌合在前後方向內端一體具有凸緣的軸環,將一體具有凸緣的帶凸緣螺栓從前後方向外側貫穿帶凸緣軸環緊固於車身框架部件時,即使由於帶凸緣螺栓抵接於帶凸緣軸環,無法進一步進行緊固,僅憑帶凸緣螺栓的緊固力無法牢固地固定保險槓的凸緣部,因為在帶凸緣螺栓的凸緣和保險槓的凸緣部的前後方向的外表面之間配置了彈性材料,所以能夠通過彈性材料防止保險槓的凸緣部發生鬆動,牢固地固定保險槓。
附圖說明
圖1是後保險槓的立體圖。(第1實施方式)
圖2是圖1的2的方向的向視圖。(第1實施方式)
圖3是圖2的3的部分的放大圖。(第1實施方式)
圖4是圖3的4-4線的剖面圖。(第1實施方式)
圖5是圖3的5-5線的剖面圖。(第1實施方式)
圖6是圖4的6的部分的放大圖。(第1實施方式)
圖7是保險槓的成型工序的說明圖。(第1實施方式)
圖8是後保險槓的立體圖。(第2實施方式)
符號說明
11a:安裝板(車身框架部件);12:後保險槓(保險槓);13:保險槓主體;20:連續纖維增強樹脂層;20ˊ:連續纖維預浸漬片(預浸漬片);21:不連續纖維增強樹脂層;21ˊ:不連續纖維預浸漬片(預浸漬片);22:凸緣部;22a:第1凸緣頂端部;22b:第2凸緣頂端部;22c:安裝孔;23:帶凸緣軸環(軸環);23b:凸緣;24:帶凸緣螺栓;24a:凸緣;27:彈性材料;28:蜂窩結構體;41:壓力加工成型模具;42:陰模;43:陽模;44:空間。
本發明的具體實施方式
第1實施方式
下面,根據圖1~圖7,對本發明的第1實施方式進行說明。另外,本說明書中所說的前後方向、左右方向(車寬方向)以及上下方向,均以就坐於駕駛席的乘員為標準定義。
如圖1~圖5所示,在汽車的車身後部的前後方向上所配置的左右一對的後側架11、11的後端上,安裝有沿著車寬方向延伸的纖維增強樹脂制的後保險槓12。構成後保險槓12的主體的保險槓主體13,具有沿上下方向延伸的底壁14、從底壁14的上端向前方延伸的上壁15、從底壁14的下端向前方延伸的下壁16,形成向前方開放的剖面呈日文片假名「コ」的形狀。
保險槓主體13由小剖面面積部17和兩個大剖面面積部18、18以及兩個剖面面積變化部19、19構成,其中:小剖面面積部17位於車寬方向中央,具有比較小的基本不變的剖面;兩個大剖面面積部18、18位於車寬方向兩端,具有比較大的基本不變的剖面;左右一對的兩個剖面面積變化部19、19將小剖面面積部17的車寬方向的外端連接於兩個大剖面面積部18、18的車寬方向的內端,兩個剖面面積變化部19、19的剖面面積,從小剖面面積部17開始朝向兩個大剖面面積部18、18漸漸增加。
另外,小剖面面積部17由直線部17a和左右一對的彎曲部17b、17b構成,其中:直線部17a位於車寬方向中央呈直線狀延伸;左右一對的彎曲部17b、17b從直線部17a的車寬方向外端,朝向兩個剖面面積變化部19、19的車寬方向內端並向前方彎曲。彎曲部17b、17b的車寬方向內端附近最為朝向後方突出,該位置在發生來自後面的碰撞時成為承受碰撞負荷F、F的碰撞負荷承受部P、P。
保險槓主體13的外表面,即底壁14的後表面、上壁15的上表面以及下壁16的下表面,由通過尼龍等熱可塑性樹脂使連續的玻璃纖維結合而成的連續纖維增強樹脂層20構成。保險槓主體13的內表面,即底壁14的前表面、上壁15的下表面以及下壁16的上表面,由通過尼龍等熱可塑性樹脂使不連續的玻璃纖維結合而成的不連續纖維增強樹脂層21構成。連續纖維增強樹脂層20的連續纖維朝向車寬方向和與其垂直的上下方向以及前後方向。
另外,在保險槓主體13的外周緣,整周突出設置有凸緣部22,該凸緣部22也是由從保險槓主體13連續而來的連續纖維增強樹脂層20以及不連續纖維增強樹脂層21構成的2層結構。
如圖4~圖6所示,在從保險槓主體13的上壁部15和下壁部16分別向上方和下方延伸的凸緣部22的外周緣,連接有由不含玻璃纖維的尼龍等熱可塑性樹脂構成的第1凸緣頂端部22a。上側的第1凸緣頂端部22a從上側的凸緣部22的上端向上方延伸後向後方彎折而形成L字形的剖面,同樣,下側的第1凸緣頂端部22a從下側的凸緣部22的下端向下方延伸後向後方彎折而形成L字形的剖面。另外,在從保險槓主體13的車寬方向的外端的底壁14、上壁15、下壁16分別向後方、上方和下方延伸的凸緣部22的外周緣,連接有由不含玻璃纖維的尼龍等熱可塑性樹脂構成的第2凸緣頂端部22b。第2凸緣頂端部22b具有I字形的剖面,由凸緣部22保持原樣延長形成。這些第1凸緣頂端部22a和第2凸緣頂端部22b在附圖上以陰影方式表示。
連續纖維增強樹脂層20的厚度基本不變,通過調整層積其上的不連續纖維增強樹脂層21的厚度,可以將凸緣部22的厚度設定得比保險槓主體13的厚度大。在保險槓主體13和凸緣部22的分界部,不連續纖維增強樹脂層21的厚度最大。第1凸緣頂端部22a和第2凸緣頂端部22b的厚度與凸緣部22的厚度相同。
如圖7(A)所示,壓力加工成型保險槓主體13以及凸緣部22的壓力加工成型模具41,由陰模42和陽模43構成,其中,陰模42具有成型連續纖維增強樹脂層20的凹狀空腔42a,陽模43具有成型不連續纖維增強樹脂層21的凸狀型芯43a。首先,在將壓力加工成型模具41開模的狀態下,將連續纖維預浸漬片20ˊ和不連續纖維預浸漬片21ˊ以預先加熱後的狀態配置於陰模42的空腔42a和陽模43的型芯43a之間。
接著,如圖7(B)所示,通過將壓力加工成型模具41閉模而將保險槓主體13以及凸緣部22壓力加工成型。此時,在對應凸緣部22上連續的第1凸緣頂端部22a和第2凸緣頂端部22b的部分,留有不存在玻璃纖維和樹脂的空間44。接著,如圖7(C)所示,通過向所述空間44注入融化的熱可塑性樹脂,形成第1凸緣頂端部22a和第2凸緣頂端部22b。這樣,利用成型保險槓主體13以及凸緣部22的壓力加工成型模具41,成型第1凸緣頂端部22a和第2凸緣頂端部22b,因此可以節省設備費用和加工工時。
將這樣成型的後保險槓12從壓力加工成型模具41取出後,如圖7(D)所示,在凸緣部22上加工安裝孔22c。然後如圖6(E)所示,通過壓入或嵌緊,將帶凸緣軸環23固定於凸緣部22的安裝孔22c,完成後保險槓12的加工。
如圖6所示,在形成於後保險槓12的車寬方向兩端部的上下凸緣部22的各3個安裝孔22c上,嵌合有帶凸緣軸環23。帶凸緣軸環23具有從主體部23a的前端開始向徑向外側突出的凸緣23b,主體部23a嵌合於凸緣部22的安裝孔22c,凸緣23b與凸緣部22的前表面相抵接。在閉塞後車身側架11的後端的安裝板11a的前表面上,焊接有焊接螺母25。在後板26被夾持於安裝板11a的後表面和帶凸緣軸環23的凸緣23b的前表面之間的狀態下,帶凸緣螺栓24從後方貫穿帶凸緣軸環23、後板26和安裝板11a,旋合於焊接螺母25,由此,將後保險槓12固定於左右的安裝板11a、11a。此時,在帶凸緣螺栓24的凸緣24a和後保險槓12的凸緣部22的後表面之間,配置有由橡膠等構成的環狀的彈性材料27。
而如果帶凸緣軸環23的主體部23a的後端從後保險槓12的凸緣部22的後表面突出的話,則帶凸緣螺栓24的緊固力無法直接作用於後保險槓12的凸緣部22,後保險槓12的凸緣部22僅由與帶凸緣軸環23之間的摩擦力來保持,易於發生振動和噪音。但是,由於在帶凸緣軸環23的主體部23a的後端突出部的周圍配置了彈性材料27,帶凸緣螺栓24的緊固力通過被壓縮的彈性材料27作用於後保險槓12的凸緣部22的後表面,可以將後保險槓12牢固地固定並防止發生振動和噪音。
接著,對具有上述結構的本發明的實施方式的作用進行說明。
在本車的後保險槓受到其他車輛的前保險槓輕微碰撞等情況下,若採用只是單純向後方彎曲的現有技術的後保險槓,由於碰撞負荷集中施加於其保險槓的車寬方向中央的一點,因此會產生有較大的彎曲力矩作用於後保險槓的車寬方向中央部的問題。
與此相對,若採用圖2所示的本實施方式的後保險槓12,由於具有最為向後方突出的左右一對的碰撞負荷承受部P、P,因此碰撞負荷F、F集中施加至左右一對的碰撞負荷承受部P、P。其結果,通過降低作用於後保險槓12的車寬方向中央部的彎曲力矩的最大值,可以提高後保險槓12抵抗彎曲變形的強度。
並且,由於保險槓主體13具有位於車寬方向中央的小剖面面積部17,與小剖面面積部17的車寬方向外側連續的剖面面積漸漸增加的一對剖面面積變化部19、19,以及與剖面面積變化部19、19的車寬方向外側連續的一對大剖面面積部18、18,因此在有碰撞負荷F、F施加於一對碰撞負荷承受部P、P時,通過由剖面面積變化部19、19和大剖面面積部18、18支承彎曲力矩,既能減少保險槓主體13的厚度來實現輕量化,又能提高強度。
另外,由於保險槓主體13以及凸緣部22是包括連續纖維增強樹脂層20和不連續纖維增強樹脂層21的至少2層的層積體,其中,連續纖維增強樹脂層20是將連續的玻璃纖維朝向車寬方向及與其垂直的方向配置並以熱可塑性樹脂結合而成,不連續纖維增強樹脂層21是將不連續的玻璃纖維在隨機方向上配置並以熱可塑性樹脂結合而成,因此可以通過在保險槓主體13上合併使用高價的連續纖維增強樹脂層20和廉價的不連續纖維增強樹脂層21,與保險槓主體13全部由高價的連續纖維增強樹脂層20構成的情況相比,不僅可以降低成本,而且可通過高強度的連續纖維增強樹脂層20來確保後保險槓12的必要強度。
但是,由於後保險槓12的保險槓主體13以及凸緣部22是包括連續纖維增強樹脂層20以及不連續纖維增強樹脂層21的2層構造,其凸緣部22的端部邊緣由連續纖維預浸漬片20′以及不連續纖維預浸漬片21′的切斷面構成,因而連續纖維增強樹脂層20以及不連續纖維增強樹脂層21的被切斷的玻璃纖維的頂端和鑄型樹脂的一部分會從凸緣部22的端部邊緣伸出而形成毛刺。特別是若連續纖維增強樹脂層20所含有的連續的玻璃纖維層的銳利的頂端伸出而形成毛刺的話,該毛刺會接觸到工作人員的手,從而會降低工作效率,並有降低產品美觀性的可能。在現有技術中,有必要進行切斷修整加工,以確保凸緣部22的端部邊緣的光滑。
但根據本實施方式,用第1凸緣頂端部22a和2凸緣頂端部22b覆蓋了後保險槓12的外周的凸緣部22的伸出毛刺的端部邊緣,因此不需要進行去除毛刺的修整加工,也可以防止毛刺伸出,提高產品的品質。
另外,在向壓力加工成型模具41的內部設置連續纖維預浸漬片20ˊ和不連續纖維預浸漬片21ˊ的時候,如果發生錯位,將連續纖維預浸漬片20ˊ和不連續纖維預浸漬片21ˊ的端部邊緣突入到壓力加工成型模具41的空間44(參考圖7(C))的裡面的話,用來成型第1凸緣頂端部22a或第2凸緣頂端部22b的合成樹脂就無法充分注入到空間44的裡面,可能出現第1凸緣頂端部22a或第2凸緣頂端部22b不能完全覆蓋毛刺的情況。但在本實施方式中,特別是由於第1凸緣頂端部22a形成L字形的剖面,因此連續纖維預浸漬片20ˊ和不連續纖維預浸漬片21ˊ的端部邊緣無法到達L字形剖面的頂端,因而可以由第1凸緣頂端部22a完全覆蓋毛刺防止其露出。
另外,由於後保險槓12是將連續纖維增強樹脂層20以及不連續纖維增強樹脂層21層積而成的2層構造,而凸緣部22的不連續纖維增強樹脂層21要比保險槓主體13的不連續纖維增強樹脂層21厚,因此可以由成型性優異的不連續纖維增強樹脂層21容易地加厚凸緣部22,由較厚的凸緣部22提高後保險槓12的安裝強度。
另外,在保險槓主體13以及凸緣部22的分界部,不連續纖維增強樹脂層21的厚度達到最大,因此通過提高在分界部的連續纖維增強樹脂層20的位置的自由度,能夠使連續纖維增強樹脂層20平滑地彎折,而非急劇地彎折。據此,在使用壓力加工成型模具41成型後保險槓12時,可以防止連續纖維增強樹脂層20在所述分界部急劇地彎折而導致連續的玻璃纖維破損斷裂。
接著,根據圖8對本發明的第2實施方式進行說明。
第2實施方式的後保險槓12,在其保險槓主體13的車寬方向中央部以及車寬方向的兩端部具有蜂窩結構體28。蜂窩結構體28為熱可塑性合成樹脂製成,與第1凸緣頂端部22a和第2凸緣頂端部22b同時注塑成型。
根據本實施方式,被從後方或斜後方輕微碰撞時,通過壓壞蜂窩結構體28,可以有效吸收碰撞能量。
以上,對本發明的實施方式進行了說明,但是只要不脫離本發明主旨的範圍,也可以進行各種設計變更。
例如,在實施方式中,對後保險槓12進行了說明,但是本發明對前保險槓也同樣適用。在後保險槓12的情況下,前後方向的外側對應後方,在前保險槓的情況下,前後方向的外側對應前方。