一種摻氟氧化亞銅薄膜及其製備方法與流程
2023-04-28 19:05:11 5
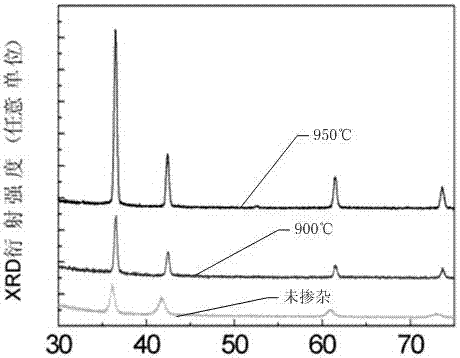
本發明涉及光電功能材料領域,尤其涉及一種摻氟氧化亞銅薄膜及其製備方法。
背景技術:
能源和環保是人類面臨的兩大問題,作為新能源的重要組成部分,用之不竭、潔淨環保的太陽能備受矚目。但目前的單晶矽、非晶矽、碲化鎘以及銅銦鎵硒太陽能電池有著各自的缺陷,所以仍需研發環境友好及低成本的太陽能電池材料,氧化亞銅是很好的候選材料。這是因為,氧化亞銅有眾多優點:直接帶隙的p 型半導體,禁帶寬度約為2.1 eV,在可見光範圍內有很高的吸收係數,較大的少子擴散長度,且理論計算表明氧化亞銅太陽能電池的轉換效率能達到20%,它無毒性、儲量豐富、在300 ℃以下比較穩定。氧化亞銅的眾多優點使其在新型太陽能電池上有重要應用,例如,氧化亞銅可與其它n型半導體材料形成異質結太陽能電池,可用作基於銅銦鎵硒的多晶疊層太陽能電池的頂層結,氧化亞銅也可用於中間帶太陽能電池,因為中間帶太陽能電池所要求的最佳禁帶寬度(1.9eV)與氧化亞銅的禁帶寬度非常接近。
然而,實驗表明用氧化亞銅薄膜製成的太陽能電池其轉換效率並不高,這是因為未摻雜的氧化亞銅薄膜由於電阻率高,無法獲得高的光電轉換效率,而材料的載流子遷移率是影響電池光電轉換效率的關鍵因素之一;進一步,現有技術製備氧化亞銅薄膜的方法存在可控性差、成本較高的問題。因此,如何解決氧化亞銅薄膜製備工藝中存在的技術問題,實現高載流子遷移率、低電阻的氧化亞銅薄膜的製備,是實現氧化亞銅薄膜大規模使用的關鍵所在。
由此可見,現有技術還有待於改進和發展。
技術實現要素:
鑑於上述現有技術的不足,本發明的目的在於提供一種摻氟氧化亞銅薄膜及其製備方法,旨在解決現有的氧化亞銅薄膜載流子遷移率低、電阻率高的問題。
本發明的技術方案如下:
一種摻氟氧化亞銅薄膜的製備方法,其中,包括步驟:
A、將銅靶安裝在磁控濺射設備的靶位上,通入高純氧氣和高純氬氣進行反應性共濺射,生成氧化亞銅薄膜;
B、將所述氧化亞銅薄膜放入管式爐中,採用熱擴散方法將CuF2粉末摻雜到所述氧化亞銅薄膜中,從而生成摻氟氧化亞銅薄膜。
較佳地,所述的摻氟氧化亞銅薄膜的製備方法,其中,所述步驟B具體包括:
B1、先將所述氧化亞銅薄膜放置在不鏽鋼支架上,然後將所述不鏽鋼支架放入管式爐中;
B2、將CuF2粉末放置在所述不鏽鋼支架前面7~9mm處,採用熱擴散方法將所述CuF2粉末摻雜到所述氧化亞銅薄膜中,從而生成摻氟氧化亞銅薄膜。
較佳地,所述的摻氟氧化亞銅薄膜的製備方法,其中,步驟A中,所述反應性共濺射過程在氧氣流為1sccm、氬氣流為12sccm條件下進行。
較佳地,所述的摻氟氧化亞銅薄膜的製備方法,其中,步驟A中,所述反應性共濺射氣壓為1.5~2.5Pa,反應性共濺射電壓為300~400V,反應性共濺射時間為50~70min。
較佳地,所述的摻氟氧化亞銅薄膜的製備方法,其中,步驟A中,所述反應性共濺射氣壓為2Pa,反應性共濺射電壓為350V,反應性共濺射時間為60min。
較佳地,所述的摻氟氧化亞銅薄膜的製備方法,其中,步驟B中,所述熱擴散過程在氬氣流為100sccm的條件下進行。
較佳地,所述的摻氟氧化亞銅薄膜的製備方法,其中,步驟B中,所述管式爐內的氣壓為350~450Pa。
較佳地,所述的摻氟氧化亞銅薄膜的製備方法,其中,步驟B中,所述熱擴散溫度為900~1200℃,熱擴散時間為25~35min。
一種摻氟氧化亞銅薄膜,其中,採用如上所述的製備方法製成。
有益效果:本發明先通過反應共濺射沉積技術製備氧化亞銅薄膜,然後再通過簡單管式爐裝置採用熱擴散方法將氟元素摻雜到所述氧化亞銅薄膜中,從而生成載流子遷移率高、電阻率低的摻氟氧化亞銅薄膜,可有效提高摻氟氧化亞銅薄膜製成的太陽能電池光電轉換效率。本發明製備摻氟氧化亞銅薄膜的方法,其可控性強、工藝簡單、製作成本低,並且生成的薄膜具有很好的附著性和重複性,可滿足大規模生產需要。
附圖說明
圖1為本發明摻氟氧化亞銅薄膜製備方法較佳實施例流程圖。
圖2為本發明測得的未摻雜和實施例1及實施例2製備的摻氟氧化亞銅薄膜的X射線衍射圖譜對比圖。
具體實施方式
本發明提供一種摻氟氧化亞銅薄膜及其製備方法,為使本發明的目的、技術方案及效果更加清楚、明確,以下對本發明進一步詳細說明。應當理解,此處所描述的具體實施例僅僅用以解釋本發明,並不用於限定本發明。
本發明所提供的一種摻氟氧化亞銅薄膜的製備方法,如圖1所示,其包括步驟:
S10、將銅靶安裝在磁控濺射設備的靶位上,通入高純氧氣和高純氬氣進行反應性共濺射,生成氧化亞銅薄膜;
S20、將所述氧化亞銅薄膜放入管式爐中,採用熱擴散方法將CuF2粉末摻雜到所述氧化亞銅薄膜中,從而生成摻氟氧化亞銅薄膜。
進一步,所述步驟S20具體包括:
S21、先將所述氧化亞銅薄膜放置在不鏽鋼支架上,然後將所述不鏽鋼支架放入管式爐中;
S22、將CuF2粉末放置在所述不鏽鋼支架前面7~9mm處,採用熱擴散方法將所述CuF2粉末摻雜到所述氧化亞銅薄膜中,從而生成摻氟氧化亞銅薄膜。
本發明先採用反應共濺射沉積技術製備氧化亞銅薄膜,然後再通過簡單管式爐裝置採用熱擴散方法將氟元素摻雜到所述氧化亞銅薄膜中,從而生成載流子遷移率高、電阻率低的摻氟氧化亞銅薄膜。該方法可控性強、工藝簡單、並且生成的薄膜具有很好的附著性和重複性,可滿足大規模生產需要。
具體來說,本發明採用石英做襯底,在濺射前先用有機溶液對基片進行超聲清洗,設置本底真空為6×10-4Pa,襯底溫度為400℃,接著進行反應性共濺射,所述反應性共濺射過程是在氧氣流為1sccm、氬氣流為12sccm條件下進行的,所述氧氣為質量百分比大於99.99%的高純氧氣,所述氬氣為質量百分比大於99.999%的高純氬氣。
進一步,本發明所述反應性共濺射氣壓為1.5~2.5Pa,反應性共濺射電壓為300~400V,反應性共濺射時間為50~70min;優選地,所述反應性共濺射氣壓為2Pa,反應性共濺射電壓為350V,反應性共濺射時間為60min,在此條件下可使氧化亞銅薄膜均勻生長,並且具有較佳的附著性和重複性。
另外,在反應性共濺射過程完成後,將製備好的氧化亞銅薄膜放入特製的不鏽鋼支架上,隨後放入管式爐中,所述管式爐為真空管式燒結爐,然後將一定量的提供氟元素的 CuF2粉末放在所述不鏽鋼支架前8mm處,最後進行熱擴散過程。在熱擴散過程中要避免CuF2粉末長時間暴露於空氣中,防止其接觸水蒸氣變藍。
具體地,所述熱擴散過程是在氬氣流量為100sccm的條件下進行的,進一步,本發明所述熱擴散溫度為900~1200℃,熱擴散時間為25~35min,所述管式爐內的氣壓為350~450Pa;優選地,所述熱擴散溫度為950℃,熱擴散時間為30min,所述管式爐內的氣壓為400Pa,在此條件下,所述氟元素能均勻地摻雜到所述氧化亞銅薄膜上,從而生成載流子遷移率高、電阻率低的摻氟氧化亞銅薄膜。
進一步,在生成摻氟氧化亞銅薄膜後,本發明還對其進行了XRD及霍爾測試。
一種摻氟氧化亞銅薄膜,其中,採用如上所述的製備方法製成。
基於上述方法,本發明還提供一種摻氟氧化亞銅薄膜,其採用如上所述的製備方法製成,所述摻氟氧化亞銅薄膜可用於製備太陽能電池。
下面通過具體實施例對本發明進行詳細說明。
實施例1
首先,將純度為99.999 %的Cu靶材固定在靶材架上;以石英做襯底,在清洗襯底時採用丙酮、酒精和去離子水依次對襯底進行超聲波清洗;濺射系統本底真空抽至6.0×10-4Pa,通入流量為1sccm的高純氧氣和流量為12 sccm的高純氬氣,保持工作壓強為2 Pa。沉積薄膜前先對Cu靶預濺射10min,以除去靶表面的氧化物和雜質。進行薄膜濺射沉積時,襯底溫度為400℃,銅靶上的濺射電壓為350V,濺射時間為1小時。鍍膜結束後,關閉濺射源和進氣閥,等待襯底溫度降至室溫時,依次關閉真空泵和電源以及其它的開關,取出樣品。然後把濺射製備的氧化亞銅薄膜放入自製的不鏽鋼支架上,連同支架一起放入真空管式燒結爐的石英管中,在距離不鏽鋼支架前方8 mm處放置盛放CuF2粉末的石英舟。實驗中,熱擴散的反應溫度為950℃,壓強為410Pa,CuF2的質量為102.1mg,氬氣流量為100 sccm,實驗時間為30 min。擴散結束後,在溫控程序控制下降溫到一定值,然後進行自然降溫。待通過自然降溫至室溫後關閉各個氣體閥門、機械泵及真空計,通入氣體使石英管內外壓強保持一致,打開法蘭,取出樣品。
圖2為測得的未摻雜和摻氟氧化亞銅薄膜的X射線衍射(XRD)圖譜。從圖2可以看出,所製備的薄膜具有單一的氧化亞銅結構,而且高溫擴散摻氟沒有改變薄膜的結構,且薄膜的結晶性能變好。
表1為測得的未摻雜和摻氟氧化亞銅薄膜的霍爾效應測試結果。
從表 1可以看出,摻氟使氧化亞銅薄膜的載流子遷移率明顯增加,電阻率減小,載流子濃度增大。進一步比較發現,擴散摻氟溫度越高,載流子濃度越大,電阻率越小,但載流子遷移率變小。這是因為雜質濃度增加時,雜質散射中心數量也增加,遷移率變小。
實施例2
與實施例1不同之處在於擴散的工藝參數上,熱擴散的反應溫度為900℃,壓強為400Pa,CuF2的質量為100.2mg,氬氣流量仍為100 sccm,實驗時間仍為30 min。圖2也給出了實施例2所得氧化亞銅薄膜的X射線衍射圖譜。從圖2可以看出,實施例1所得薄膜的結晶度比實施例2所得薄膜的結晶度更好。表1也給出了實施例2所測得的氧化亞銅薄膜的霍爾效應測試結果。從表1可以看出,實施例1所得薄膜的載流子遷移率比實施例2的低,電阻率也比實施例2的低。
實施例3
與實施例1不同之處在於,反應性共濺射過程中,濺射氣壓為1.5Pa、濺射電壓為300V、濺射時間為50分鐘;熱擴散過程中,管式爐內的氣壓為350Pa、熱擴散溫度為900℃,熱擴散時間為25min;通過實施例3所製得的薄膜,其結晶度比實施例2所得薄膜的結晶度更差,其載流子遷移率也比實施例2的低。
實施例4
與實施例1不同之處在於,反應性共濺射過程中,濺射齊腰為2.5Pa、濺射電壓為400V、建設時間為70min;熱擴散過程中,管式爐內的氣壓為450Pa、熱擴散溫度為1200℃,熱擴散時間為35min。通過實施例3所製得的薄膜,其結晶度比實施例3所得薄膜的結晶度更差,其載流子遷移率也比實施例3的低。
綜上所述,本發明先通過反應共濺射沉積技術製備氧化亞銅薄膜,然後再通過簡單管式爐裝置採用熱擴散方法將氟元素摻雜到所述氧化亞銅薄膜中,從而生成載流子遷移率高、電阻率低的摻氟氧化亞銅薄膜,可有效提高摻氟氧化亞銅薄膜製成的太陽能電池光電轉換效率。本發明製備摻氟氧化亞銅薄膜的方法,其可控性強、工藝簡單、製作成本低,並且生成的薄膜具有很好的附著性和重複性,可滿足大規模生產需要。
應當理解的是,本發明的應用不限於上述的舉例,對本領域普通技術人員來說,可以根據上述說明加以改進或變換,所有這些改進和變換都應屬於本發明所附權利要求的保護範圍。