一種氨氧化反應器及腈類化合物製備方法與流程
2024-03-27 02:26:05 1
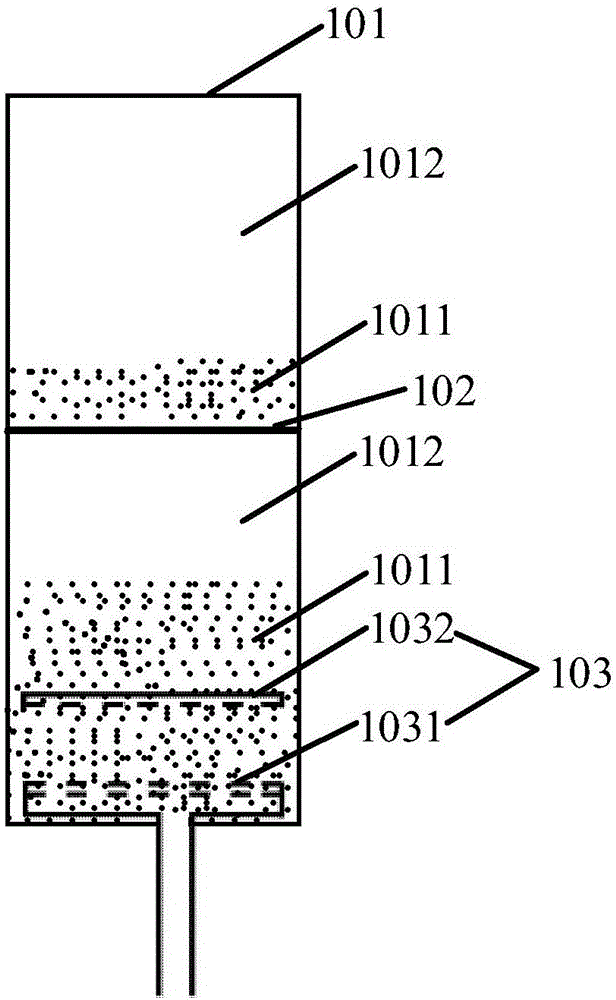
本發明涉及化工設備和工藝技術領域,特別涉及一種氨氧化反應器及腈類化合物製備方法。
背景技術:
腈類化合物如丙烯腈、間苯二腈、氯苯甲腈等,是重要的醫藥、農藥、染料中間體。其合成方法主要包括:亞硝醯氯氰化法和氨氧化法。其中,亞硝醯氯氰化法由於原料與溶劑價格較貴,不具有經濟優勢。大多數化工企業均採用氨氧化法製備腈,其基本原理是將烴類或滷代烴原料氣、氨氣和空氣為反應原料通入反應器,並利用反應器中的催化劑(以過渡金屬元素為主要活性成分)催化反應原料進行氨氧化反應。
目前,在反應器中進行催化氨氧化反應過程中,催化劑基本均勻分布在反應器的反應腔內形成流化床。由於腈類產物需要經過較長的流化床,同時反應腔內催化劑固體的強烈混合,常常使部分腈類產物被催化劑固體吸附,而被催化劑固體吸附的部分腈類產物會跟隨催化劑固體沉降。
因此,現有的這種反應器在進行催化氨氧化反應過程中,產物返混比較嚴重。
技術實現要素:
本發明實施例提供了一種氨氧化反應器及腈類化合物製備方法,能夠有效地降低產物返混。
一種氨氧化反應器,包括:流化床反應器、設置於所述流化床反應器內的二段分布板以及兩個氣體分布器,其中,
所述二段分布板,用於將所述流化床反應器切分成上、下兩段反應空間;
每一段所述反應空間,包括:一個催化劑密相區以及所述催化劑密相區對應的催化劑稀相區;
第一氣體分布器,設置於所述流化床反應器底部;
第二氣體分布器,設置於下段反應空間中的所述催化劑密相區內,其中,所述第二氣體分布器出氣孔向下;
分別通過所述第一氣體分布器和所述第二氣體分布器將第一溫度範圍的原料氣與氨氣的混合氣體以及第二溫度範圍的空氣注入到所述流化床反應器,在每一段所述反應空間中的所述催化劑密相區,進行催化氨氧化反應;
每一段所述反應空間中的催化劑稀相區,用於抑制反應後的產物氣體返混到對應的所述催化劑密相區。
可選地,下段反應空間中的所述催化劑密相區與對應的所述催化劑稀相區高度比為0.5~10;
上段反應空間中的所述催化劑密相區與對應的所述催化劑稀相區高度比為0.01~1。
可選地,所述氨氧化反應器,進一步包括:設置於所述流化床反應器頂部的擴大段和氣固分離器,其中,
所述擴大段,用於當攜帶有催化劑顆粒的產物氣體進入時,沉降部分所述催化劑顆粒到所述流化床反應器;
所述氣固分離器,優選旋風分離器,用於對所述擴大段沉降後的產物氣體進一步通過氣固分離方式沉降所述產物氣體攜帶的催化劑顆粒,並將沉降後的所述催化劑顆粒返回到所述催化劑密相區。
可選地,所述氣固分離器,包括:旋風筒體、設置於所述旋風筒體側壁上的氣體入口、設置於所述旋風筒體頂部的升氣管以及設置於所述旋風筒體底部的料腿和料腿底部的翼閥,其中,
經過所述擴大段沉降後的產物氣體通過所述氣體入口進入所述旋風筒體;
經過所述旋風筒體分離後的產物氣體通過所述升氣管進入外部的產物分離精製裝置;
經過所述旋風筒體分離後的催化劑顆粒沉降入所述料腿;
所述料腿插入上段反應空間中的催化劑密相區或催化劑稀相區,其中,所述料腿上的翼閥位於上段反應空間中的催化劑密相區或催化劑稀相區;
當所述料腿內沉降的所述催化劑顆粒高度達到高度閾值時,所述翼閥開啟,所述料腿內沉降的所述催化劑顆粒進入到所述上段反應空間中的催化劑密相區。
可選地,所述氨氧化反應器,進一步包括:
設置於下段反應空間中的第一換熱器,用於為所述下段反應空間中的催化劑密相區加熱;以及
設置於上段反應空間中的第二換熱器,用於為所述上段反應空間中的催化劑密相區加熱。
可選地,所述第一換熱器,包括:普通盤管換熱器或者虹吸式換熱器;
所述第二換熱器,包括:普通盤管換熱器或者虹吸式換熱器。
可選地,所述氨氧化反應器,進一步包括:
設置於所述流化床反應器內的催化劑溢流裝置,所述催化劑溢流裝置的催化劑入口端設置於上段反應空間中的催化劑稀相區,與所述二段分布板的距離為所述流化床反應器直徑的0.2~3倍;
所述催化劑溢流裝置的催化劑出口端設置於下段反應空間中的催化劑密相區,與所述流化床反應器底部的距離為所述流化床反應器直徑的0.05~0.7倍。
可選地,所述氨氧化反應器,進一步包括:
設置於所述流化床反應器外側壁的催化劑溢流裝置,所述催化劑溢流裝置的催化劑入口端與所述外側壁的第一連接位置位於上段反應空間中的催化劑稀相區,所述第一連接位置與所述二段分布板的距離為所述流化床反應器直徑的0.2~3倍;
所述催化劑溢流裝置的催化劑出口端與所述外側壁的第二連接位置位於下反應空間中的催化劑密相區,所述第二連接位置與所述流化床反應器底部的距離為所述流化床反應器直徑的0.05~0.7倍。
可選地,所述第一氣體分布器與所述第二氣體分布器之間的距離為所述流化床反應器直徑的0.1~0.5倍。
可選地,所述流化床反應器與外部的氣體壓縮機相連,進一步用於接收所述外部的氣體壓縮機鼓氣,使內部包含的所述原料氣、所述氨氣、所述空氣以及所述產物氣體在所述流化床反應器內的表觀線速度達到0.1~0.9m/s。
可選地,所述混合氣體與所述空氣的流量比為1~10。
可選地,所述混合氣體中所述原料氣與所述氨氣的摩爾比不小於1。
可選地,上述氨氧化反應器進一步包括:設置於所述流化床反應器的側壁上的催化劑入口,其中,所述催化劑入口在所述側壁上的位置與下段反應空間中的催化劑密相區相對應。
可選地,所述第一氣體分布器,包括:板式氣體分布器和管式氣體分布器中的任意一種。
可選地,所述第二氣體分布器,包括:管式氣體分布器。
可選地,所述二段分布板,包括:多孔板式或者浮伐式。
可選地,所述設置於所述流化床反應器外側壁的催化劑溢流裝置,進一步包括:設置於所述催化劑溢流裝置上部的防倒竄擴大室,所述防倒竄擴大室,用於防止下段反應空間中的催化劑倒竄。
可選地,所述催化劑溢流裝置的催化劑出口設置有防止氣體倒竄的倒椎體結構或翼閥結構。
可選地,所述氨氧化反應器可進一步包括:設置於所述上反應空間中的催化劑密相區內的空氣輸入管路,用於為所述上反應空間中的催化劑密相區輸入空氣。通過對每一個催化劑密相區通入不同含量的空氣可調節不同密相區的氧含量,尤其是在上反應空間中的催化劑密相區提供過量的氧氣氛圍,不僅可以提高反應器整體的轉化率,也可對消除反應過程中的少量積碳。
一種腈類化合物製備方法,將催化劑裝入流化床反應器,所述催化劑集中分布於每一個催化劑密相區,還包括:
分別通過第一氣體分布器和第二氣體分布器將第一溫度範圍的原料氣與氨氣的混合氣體以及第二溫度範圍的空氣注入到所述流化床反應器;
通過每一個所述催化劑密相區,進行催化氨氧化反應;
通過每一個所述催化劑稀相區抑制反應後的產物氣體返混到對應的所述催化劑密相區。
可選地,在所述分別通過第一氣體分布器和第二氣體分布器將第一溫度範圍的原料氣與氨氣的混合氣體以及第二溫度範圍的空氣注入到所述流化床反應器之前,進一步包括:
分別向第一換熱器和第二換熱器通入加熱介質,控制所述流化床反應器升溫至200~500℃,其中,所述加熱介質包括:惰性氣體、空氣及水中的任意一種。
可選地,在所述分別通過第一氣體分布器和第二氣體分布器將第一溫度範圍的原料氣與氨氣的混合氣體以及第二溫度範圍的空氣注入到所述流化床反應器之前,進一步包括:直接向所述流化床反應器內充入熱的惰性氣體,控制所述流化床反應器升溫至200~500℃。
可選地,在所述分別通過第一氣體分布器和第二氣體分布器將第一溫度範圍的原料氣與氨氣的混合氣體以及第二溫度範圍的空氣注入到所述流化床反應器之後,進一步包括:
分別向第一換熱器和第二換熱器通入冷卻水,控制所述流化床反應器溫度在200~500℃之間。
可選地,所述催化劑,包括:粒徑為25~300μm的金屬負載型催化劑;
可選地,所述第一溫度範圍包括100~300℃。
可選地,所述第二溫度範圍包括100~300℃。
所述原料氣,包括:烴類或者滷代烴類中的任意一種。
本發明實施例提供了一種氨氧化反應器及腈類化合物製備方法,該氨氧化反應器,包括:流化床反應器、設置於所述流化床反應器內的二段分布板以及兩個氣體分布器,其中,所述二段分布板,用於將所述流化床反應器切分成上、下兩段反應空間;每一段所述反應空間,包括:一個催化劑密相區以及所述催化劑密相區對應的催化劑稀相區;第一氣體分布器,設置於所述流化床反應器底部;第二氣體分布器,設置於下段反應空間中的所述催化劑密相區內,其中,所述第二氣體分布器出氣孔向下;分別通過所述第一氣體分布器和所述第二氣體分布器將第一溫度範圍的原料氣與氨氣的混合氣體以及第二溫度範圍的空氣注入到所述流化床反應器,在每一段所述反應空間中的所述催化劑密相區,進行催化氨氧化反應;每一段所述反應空間中的催化劑稀相區,用於抑制反應後的產物氣體返混到對應的所述催化劑密相區。由於二段分布板將流化床反應器劃分為兩個催化劑密相區和兩個催化劑稀相區,其中,催化劑稀相區中的催化劑含量稀疏,同時,催化劑密相區與催化劑稀相區相鄰存在。那麼,在催化劑密相區生成的產物氣體進入催化劑稀相區,由於催化劑稀相區中的催化劑含量稀疏,催化劑固體顆粒對產物氣體的阻力大大降低,從而能夠有效地降低產物返混。
附圖說明
為了更清楚地說明本發明實施例或現有技術中的技術方案,下面將對實施例或現有技術描述中所需要使用的附圖作簡單地介紹,顯而易見地,下面描述中的附圖是本發明的一些實施例,對於本領域普通技術人員來講,在不付出創造性勞動的前提下,還可以根據這些附圖獲得其他的附圖。
圖1是本發明一個實施例提供的一種氨氧化反應器的結構示意圖;
圖2是本發明另一個實施例提供的一種氨氧化反應器的結構示意圖;
圖3是本發明一個實施例提供的一種氣固分離器的結構示意圖;
圖4是本發明一個實施例提供的普通盤管換熱器的結構示意圖;
圖5是本發明一個實施例提供的虹吸式換熱器的結構示意圖;
圖6是本發明一個實施例提供的一種換熱器分布方式的結構示意圖;
圖7是本發明另一個實施例提供的一種氨氧化反應器的結構示意圖;
圖8是本發明另一個實施例提供的一種氨氧化反應器的結構示意圖;
圖9是本發明一個實施例提供的板式氣體分布器的結構示意圖;
圖10是本發明一個實施例提供的管式氣體分布器的結構示意圖;
圖11是本發明一個實施例提供的浮筏式氣體分布器的結構示意圖;
圖12是本發明一個實施例提供的二段分布板的結構示意圖。
具體實施方式
為使本發明實施例的目的、技術方案和優點更加清楚,下面將結合本發明實施例中的附圖,對本發明實施例中的技術方案進行清楚、完整地描述,顯然,所描述的實施例是本發明一部分實施例,而不是全部的實施例,基於本發明中的實施例,本領域普通技術人員在沒有做出創造性勞動的前提下所獲得的所有其他實施例,都屬於本發明保護的範圍。
本發明實施例提供的氨氧化反應器及腈類化合物製備方法能夠有效地克服或減少常規工藝的缺點及安全隱患,同時能夠有效地降低成本。
返混一般是由於催化劑固體顆粒物阻礙產物氣體上升,使產物氣體繼續在催化劑作用下發生過度反應,例如:在氨氧化反應過程中,腈類產物一旦發生返混將會生成二氧化碳等,造成腈類產物收率降低。
如圖1所示,本發明實施例提供一種氨氧化反應器,包括:流化床反應器101、設置於所述流化床反應器內的二段分布板102以及兩個氣體分布器103,其中,
所述二段分布板102,用於將所述流化床反應器切分成上、下兩段反應空間;
每一段所述反應空間,包括:一個催化劑密相區1011以及所述催化劑密相區對應的催化劑稀相區1012;
第一氣體分布器1031,設置於所述流化床反應器101底部;
第二氣體分布器1032,設置於下段反應空間中的所述催化劑密相區1011內,其中,所述第二氣體分布器1032出氣孔向下;
分別通過所述第一氣體分布器1031和所述第二氣體分布器1032將第一溫度範圍的原料氣與氨氣的混合氣體以及第二溫度範圍的空氣注入到所述流化床反應器101,在每一段所述反應空間中的所述催化劑密相區1011,進行催化氨氧化反應;
每一段所述反應空間中的催化劑稀相區1012,用於抑制反應後的產物氣體返混到對應的所述催化劑密相區1011。
在圖1所示的實施例中,由於二段分布板將流化床反應器劃分為兩個催化劑密相區和兩個催化劑稀相區,其中,催化劑稀相區中的催化劑含量稀疏,同時,催化劑密相區與催化劑稀相區相鄰存在。那麼,在催化劑密相區生成的產物氣體進入催化劑稀相區,由於催化劑稀相區中的催化劑含量稀疏,催化劑固體顆粒對產物氣體的阻力大大降低,從而能夠有效地降低產物返混。
在本發明另一實施例中,為了能夠儘可能的避免產物返混,下段反應空間中的所述催化劑密相區與對應的所述催化劑稀相區高度比為0.5~10;上段反應空間中的所述催化劑密相區與對應的所述催化劑稀相區高度比為0.01~1。由於原料氣、氨氣以及空氣在受到外部氣體壓縮機鼓氣作用下,均是從下向上運動,即原料氣、氨氣以及空氣順序經過下段反應空間中的催化劑密相區、下段反應空間中的催化劑稀相區、上段反應空間中的催化劑密相區、上段反應空間中的催化劑稀相區。其中,下段反應空間中的催化劑密相區為主要反應區,即大部分原料氣、氨氣以及空氣在下反應空間中的催化劑密相區完成反應;而上段反應空間中的催化劑密相區為補償反應區,即剩餘一小部分未參與反應的原料氣、氨氣以及空氣在該上反應空間中的催化劑密相區進行反應。在下段反應空間中的所述催化劑密相區與對應的所述催化劑稀相區高度比為0.5~10時,不僅能夠保證大部分原料氣、氨氣以及空氣在下段反應空間中的催化劑密相區完成反應,而且能夠有效地降低產物氣體返混回下反應空間中的催化劑密相區。另外,上段反應空間中的所述催化劑密相區與對應的所述催化劑稀相區高度比為0.01~1,不僅能夠避免產物氣體在上反應空間中的所述催化劑密相區進行二次反應,而且能夠儘可能使未反應的小部分原料氣、氨氣以及空氣完成反應。
如圖2所示,在本發明另一實施例中,上述氨氧化反應器,進一步包括:設置於所述流化床反應器頂部的擴大段104和氣固分離器105,其中,
所述擴大段104,用於當攜帶有催化劑顆粒的產物氣體進入時,沉降部分所述催化劑顆粒到所述流化床反應器101;從圖中可以看出擴大段104的寬度明顯大於流化床反應器,攜帶有催化劑顆粒物的產物氣體進入到擴大段後,速率會降低,由於速率的降低會使部分催化劑顆粒物沉降回流化床反應器。
所述氣固分離器105,用於對所述擴大段104沉降後的產物氣體進一步通過氣固分離方式沉降所述產物氣體攜帶的催化劑顆粒,並將沉降後的所述催化劑顆粒返回到所述催化劑密相區1011。
該氣固分離器可以直接使用現有技術中常用的一些氣固分離裝置,也可以利用旋風分離原理,構建出如圖3所示的氣固分離器,並將其應用於本發明實施例提供的氨氧化反應器。
如圖3所示,該氣固分離器105,包括:旋風筒體1051、設置於所述旋風筒體側壁上的氣體入口1052、設置於所述旋風筒體頂部的升氣管1053以及設置於所述旋風筒體底部的料腿1054,其中,
經過所述擴大段104沉降後的產物氣體通過所述氣體入口1052進入所述旋風筒體1051;產物氣體沿著旋風筒體內壁進行螺旋式運動,此時由於產物氣體本身向上的作用力,使得產物氣體在旋風筒體內進行螺旋向上運動,而催化劑固體顆粒與分離室內壁碰撞產生向下的阻力,向下的阻力與催化劑固體顆粒重力,使得催化劑固體顆粒螺旋向下運動,從而實現產物氣體與催化劑固體顆粒的分離。
經過所述旋風筒體1051分離後的產物氣體通過所述升氣管1053進入外部的產物分離精製裝置;
經過所述旋風筒體1051分離後的催化劑顆粒沉降入所述料腿1054;
所述料腿插入上段反應空間中的催化劑密相區或催化劑稀相區,其中,所述料腿1054上的翼閥1055位於上段反應空間中的催化劑密相區或催化劑稀相區;
當所述料腿1054內沉降的所述催化劑顆粒高度達到高度閾值時,所述翼閥1055開啟,所述料腿1054內沉降的所述催化劑顆粒進入到所述上段反應空間中的催化劑密相區。
另外,為了進一步防止催化劑固體顆粒隨產物氣體進入外部的產物收集裝置,還可以在升氣管設置濾網,以進一步阻攔催化劑固體顆粒。
從圖3中可以看出,料腿1054的上端寬度大於下端寬度,這樣方便催化劑顆粒物螺旋向下沉降,同時,使產物氣體進行螺旋向上運動。
另外,為了防止流化床反應器內的氣體(原料氣、氨氣、空氣以及產物氣體)通過第一閥門和第二閥門反竄入料腿,影響氣固分離,第一閥門可以設置為倒錐體結構或者翼閥結構,第二閥門可以設置為翼閥結構。
在本發明另一實施例中,上述氨氧化反應器,進一步包括:
設置於下段反應空間中的第一換熱器,用於為所述下段反應空間中的催化劑密相區加熱/散熱;以及
設置於上段反應空間中的第二換熱器,用於為所述上段反應空間中的催化劑密相區加熱/散熱。
其中,所述第一換熱器,包括:普通盤管換熱器或者虹吸式換熱器;所述第二換熱器,包括:普通盤管換熱器或者虹吸式換熱器。
該普通盤管換熱器可以為圖4A和圖4B所示,其中,圖4A所示的普通盤管換熱器的介質入口和介質出口位於同一側,而圖4B所示的普通盤管換熱器的介質入口和介質出口分布於兩側,另外,介質入口位於普通盤管換熱器的下端,介質出口則位於換熱器的上端。
上述虹吸式換熱器如圖5所示,包括:氣囊501、回形換熱管502,其中,回形換熱管502部分插入催化劑密相區,氣囊中的液態介質進入到回形換熱管502中的內部直形管路5021,當液態介質到達催化劑密相區時,由於催化劑密相區氣溫很高,使得液態介質氣化進入到回形換熱管502中的外部U型管路5022,氣化後的介質返回到氣囊501冷凝成液態,繼續進入到內部直形管路5021中,實現為催化劑密相區散熱。
下段反應空間中的第一換熱器主要為下段反應空間中的催化劑密相區加熱/散熱,其中,加熱的過程是在通入原料氣、氨氣以及空氣之前,為流化床反應器預熱,以保證氨氧化反應的進行;散熱過程主要是在氨氧化反應過程中會放熱,那麼為了避免氨氧化反應放熱引起的流化床反應器溫度升高,則需要通過換熱器散熱。
相應地,上段反應空間中的第二換熱器則主要為上段反應空間中的催化劑密相區加熱/散熱。
例如:將第一換熱器設置為普通盤管換熱器106,第二換熱器設置為虹吸式放熱器107,其與流化床反應器101中下段反應空間中的催化劑密相區1011以及上段反應空間中的催化劑密相區1011對應關係如圖6所示。普通盤管換熱器106主要為下段反應空間中的催化劑密相區加熱/散熱;虹吸式放熱器107主要為上段反應空間中的催化劑密相區加熱/散熱。
另外,還可以將第一換熱器和第二換熱器同時設置為普通盤管換熱器或者同時設置為虹吸式換熱器;也可以將第一換熱器設置為虹吸式換熱器,第二換熱器設置為普通盤管換熱器。
通過分別在上段反應空間中的催化劑密相區以及下段反應空間中的催化劑密相區布置換熱器,可使上段反應空間中的催化劑密相區以及下段反應空間中的催化劑密相區可分別對應不同的反應溫度,例如:上段反應空間中的催化劑密相區溫度可高於下段反應空間中的催化劑密相區溫度,有利於未反應的原料氣充分反應。
如圖7所示,上述氨氧化反應器,進一步包括:
設置於所述流化床反應器內的催化劑溢流裝置108,所述催化劑溢流裝置108的催化劑入口端設置於上段反應空間中的催化劑稀相區,與所述二段分布板的距離為所述流化床反應器直徑的0.2~3倍;
所述催化劑溢流裝置108的催化劑出口端設置於下段反應空間中的催化劑密相區,與所述流化床反應器底部的距離為所述流化床反應器直徑的0.05~0.7倍;通過該催化劑溢流裝置可以避免上段反應空間中的催化劑密相區高度過高,以進一步抑制產物氣體返混。
如圖8所示,上述氨氧化反應器,進一步包括:
設置於所述流化床反應器外側壁的催化劑溢流裝置109,所述催化劑溢流裝置109的催化劑入口端與所述外側壁的第一連接位置位於上段反應空間中的催化劑稀相區,所述第一連接位置與所述二段分布板的距離為所述流化床反應器直徑的0.2~3倍;
所述催化劑溢流裝置109的催化劑出口端與所述外側壁的第二連接位置位於下段反應空間中的催化劑密相區,所述第二連接位置與所述流化床反應器底部的距離為所述流化床反應器直徑的0.05~0.7倍。
另外,為了防止催化劑倒竄,在催化劑溢流裝置109上部還設置了防倒竄擴大室。對於設置於所述流化床反應器外側壁的催化劑溢流裝置來說,方便工作人員檢修,而不會影響反應器的運行。該防倒竄擴大室還可用於為流化床反應器添加催化劑。
另外,可以在流化床反應器的側壁設置催化劑入口以為流化床反應器補充催化劑,使保證氨氧化反應器連續運行,氨氧化反應持續發生。另外,還可以在流化床反應器底部設置催化劑出口,通過該催化劑出口將一些失效的催化劑或者結塊的催化劑導出,從而保證流化床反應器中催化劑的活性,以保證目標產物一直具有較高的收率。
在本發明另一實施例中,所述第一氣體分布器1031與所述第二氣體分布器1032之間的距離為所述流化床反應器直徑的0.1~0.5倍。通過將兩個氣體分布器之間的距離設置為流化床反應器直徑的0.1~0.5倍,一方面能夠保證原料氣、氨氣以及空氣中的氧氣能夠在下段反應空間中的催化劑密相區混合均勻,另一方面使大部分原料氣、氨氣以及空氣中的氧氣在下段反應空間中的催化劑密相區內發生氨氧化反應,而剩餘小部分的原料氣、氨氣以及空氣中的氧氣在上段反應空間中的催化劑密相區內發生氨氧化反應,以保證原料的轉化率和產物的收率。另外,由於空氣中的氧氣與氨氣直接接觸容易發生爆炸,本發明通過兩個氣體分布器分別向流化床反應器輸入空氣和氨氣,保證氣體通入時的安全性,同時,對氣體溫度控制靈活,可使分布器的熱點溫度比現有技術降低10~20℃。同時,使兩個催化劑密相區以不同的溫度進行反應,實現了對溫度的靈活控制,從而保證產物的收率,避免局部溫度過高以及催化劑燒結,並能夠減少其他副反應。當兩個換熱器溫度不同時,可副產不同等級的蒸汽,增加了蒸汽用途和靈活性。例如:蒸汽可為原料氣和氨氣的混合氣體以及空氣進行預先加熱等。
在本發明又一實施例中,所述流化床反應器與外部的氣體壓縮機相連,進一步用於接收所述外部的氣體壓縮機鼓氣,使內部包含的所述原料氣、所述氨氣、所述空氣以及所述產物氣體在所述流化床反應器內的表觀線速度達到0.1~0.9m/s。通過使表觀線速度達到0.1~0.9m/s不僅保證催化劑密相區和催化劑稀相區的形成,而且保證催化劑在催化劑密相區一直處於懸浮狀態,同時還可以使原料氣、氨氣及空氣能夠儘可能與催化劑接觸,參與氨氧化反應。
在本發明另一實施例中,所述混合氣體與所述空氣的流量比為1~10,該流量比在能夠滿足氨氧化反應的同時,能夠儘可能的避免原料的浪費。
在本發明又一實施例中,所述混合氣體中所述原料氣與所述氨氣的摩爾比不小於1,該原料氣與氨氣的摩爾比主要是為了保證氨氧化的發生。
另外,上述第一氣體分布器可以為板式,也可以為管式還可以為浮筏式,而第二氣體分布器則主要為管式,其中,板式氣體分布器如圖9所示,從圖中可以看出,氣流可以穿過管路以及板中的孔洞進入到流化床反應器內。管式氣體分布器如圖10所示,氣體通過回形管路上的孔洞進入到流化床反應器內。浮筏式氣體分布器如圖11所示,與板式氣體分布器相比,其表面不平整為一個一個的突起,該結構可以承受比較大的壓力,當流化床反應器承載比較多的催化劑或反應原料氣時,該浮筏式能夠支撐起比較多的催化劑或反應原料氣。
另外,上述的二段分布板的結構主要如圖12所示,在分布板上排列著一些非直行孔道,該非直行孔道一方面能夠阻擋下段反應空間中的催化劑大量的進入到上段反應空間,另一方面可以阻擋上段反應空間中的催化劑大量的進入到下段反應空間,而能夠使氣體自由的穿行。同時,該非直行孔道可以擠壓破碎氣泡。由於大量氣泡的存在會造成與催化劑接觸面積降低以及氣泡被催化劑吸附形成返混,通過二段分布板的非直行孔道擠壓破碎能夠有效地提高氣體與催化劑接觸面積以及避免氣泡引起的返混,從而能夠大大的提高產物收率以及原料的轉化率。
另外,上述氨氧化反應器可進一步包括:設置於上反應空間中的催化劑密相區內的空氣輸入管路,用於為上反應空間中的催化劑密相區輸入空氣。通過對每一個催化劑密相區通入不同含量的空氣可調節不同密相區的氧含量,尤其是在上反應空間中的催化劑密相區提供過量的氧氣氛圍,不僅可以提高反應器整體的轉化率,也可對消除反應過程中的少量積碳。
通過圖1、圖2、圖6、圖7及圖8結合的氨氧化反應器包含有:流化床反應器、設置於流化床反應器內部的二段分布板、二段分布板將流化床反應器劃分為上下兩段反應空間,每一段反應空間具有催化劑密相區和催化劑稀相區,並在下段反應空間中的催化劑密相區設置兩個氣體分布器(該兩個氣體分布器上下排列,且處於上部的氣體分布器排氣孔向下),並分別在兩個催化劑密相區設置換熱器,並設置一個催化劑溢流裝置(內部或外部),通過中試實驗進行氨氧化反應。中試實驗結果表明,在通過上述具有二段分布板的氨氧化反應器進行氨氧化反應,使原料轉化率達到97%以上,產物選擇性達到90%以上,目標產物收率達到87%以上。而現有技術在進行氨氧化反應時,其原料轉化率一般為85%,產物選擇性僅70%,目標產物收率僅為59%。因此,本發明實施例提供的氨氧化反應器能夠明顯的提高轉化率、產物選擇性以及產物收率。
本發明一個實施例提供一種腈類化合物製備方法,該腈類化合物製備方法可以包括如下步驟:
步驟A:將催化劑裝入流化床反應器,所述催化劑集中分布於每一個催化劑密相區;
步驟B:分別通過第一氣體分布器和第二氣體分布器將第一溫度範圍的原料氣與氨氣的混合氣體以及第二溫度範圍的空氣注入到所述流化床反應器;
步驟C:通過每一個所述催化劑密相區,進行催化氨氧化反應;
步驟D:通過每一個所述催化劑稀相區抑制反應後的產物氣體返混到對應的所述催化劑密相區。
另外,為了能夠保證氨氧化反應的發生,在步驟A之後,在步驟B之前,還可以預先為流化床反應器加熱,以使原料氣、氨氣以及空氣進入到流化床反應器之後即達到氨氧化反應溫度,進行氨氧化反應,該預先為流化床反應器加熱具有下述兩種實現方式:
方式一:分別向第一換熱器和第二換熱器通入加熱介質,控制所述流化床反應器升溫至200~500℃,其中,所述加熱介質包括:惰性氣體、空氣及水中的任意一種;該種加熱方式是藉助換熱器進行加熱。
方式二:
直接向所述流化床反應器內充入熱的惰性氣體,控制所述流化床反應器升溫至200~500℃;由於惰性氣體比較穩定,其既不會參與氨氧化反應,也不會對氨氧化反應有任何的抑制作用,因此,通過充入熱的惰性氣體可以保證流化床反應器溫度比較均勻。
為了進一步保證氨氧化反應生成的產物為目標產物,同時避免目標產物進行二次的氨氧化反應,在上述步驟B之後還需要分別向第一換熱器和第二換熱器通入冷卻水,控制所述流化床反應器溫度在200~500℃之間。即只有流化床反應器的溫度保持在200~500℃時,才能保證氨氧化反應的發生,同時能夠避免二次氨氧化,從而保證原料的轉化率以及產物的收率。
為了更加直觀的表明上述實施例提供的氨氧化反應器進行氨氧化反應的過程,下面分別以在15wt/a氨氧化反應器中進行丙烯氣相氨氧化製備丙烯腈、在1000t/a氨氧化反應器中進行間二甲苯氣相氨氧化製備間苯二腈以及1200t/a氨氧化反應器中進行對氯甲苯氣相氨氧化製備對氯苯甲腈為例,展開說明。
(1)在15wt/a氨氧化反應器中,進行丙烯氣相氨氧化製備丙烯腈的過程及實驗結果:
空氣由風機鼓入氨氧化反應器底部,經過下部的板式多孔分布器向上運動,氨氣與丙烯經過上部的管式分布器,進入氨氧化反應器的下段反應空間中的催化劑密相區。三種物料(空氣、氨氣與丙烯)在下段反應空間中的催化劑密相區充分混合,與催化劑接觸,進行氨氧化反應。其中,丙烯與氨的摩爾比為1:4-8,丙烯與氧的摩爾比為1:5-9,通過換熱器控制下段反應空間中的催化劑密相區反應溫度在435℃,通過換熱器控制上段反應空間中的催化劑密相區溫度為450℃;下段反應空間中的催化劑密相區中氣體實際氣速為0.45m/s。對反應結果進行計算得到,丙烯轉化率為97%,選擇性為95%,丙烯腈的收率為92%。
(2)在1000t/a氨氧化反應器中,進行間二甲苯氣相氨氧化製備間苯二腈的過程及實驗結果:
空氣由風機鼓入氨氧化反應器底部,經過下部的板式多孔分布器向上運動,氨與間二甲苯經過上部的管式分布器,進入氨氧化反應器的下段反應空間中的催化劑密相區。三種物料(空氣、氨與間二甲苯)在下段反應空間中的催化劑密相區充分混合,與催化劑接觸,進行氨氧化反應。間二甲苯與氨的摩爾比為1:4-8,間二甲苯與氧的摩爾比為1:5-9,通過換熱器控制下段反應空間中的催化劑密相區反應溫度在400℃,通過換熱器控制上段反應空間中的催化劑密相區反應溫度為440℃;下段反應空間中的催化劑密相區中氣體實際氣速為0.45m/s。對反應結果進行計算得到,間二甲苯轉化率為99.5%,選擇性為97%,間苯二腈的收率為97%。
(3)在1200t/a氨氧化反應器中,進行對氯甲苯氣相氨氧化製備對氯苯甲腈的過程及實驗結果:
空氣由風機鼓入氨氧化反應器底部,經過下部的板式多孔分布器向上運動,氨與對氯甲苯經過上部的管式分布器,進入氨氧化反應器的下段反應空間中的催化劑密相區。三種物料(空氣、氨與對氯甲苯)在下段反應空間中的催化劑密相區充分混合,與催化劑接觸,進行氨氧化反應。對氯甲苯與氨的摩爾比為1:4-8,對氯甲苯與氧的摩爾比為1:5-9,通過換熱器控制下段反應空間中的催化劑密相區反應溫度在415℃,通過換熱器控制上段反應空間中的催化劑密相區反應溫度為440℃;下段反應空間中的催化劑密相區中氣體實際氣速為0.3m/s。對反應結果進行計算得到,對氯甲苯轉化率為99%,選擇性為95%,氯苯甲腈的收率為92%。另外,與一個現有的技術的全混釜相比,催化劑總體裝量不變的情況下,本發明實施例提供的氨氧化反應器處理能力更大,可實現對氯甲苯的深度轉化。
根據上述方案,本發明的各實施例,至少具有如下有益效果:
1.本發明實施例提供的氨氧化反應器,通過二段分布板將流化床反應器劃分為兩個催化劑密相區和兩個催化劑稀相區,其中,催化劑稀相區中的催化劑含量稀疏,同時,催化劑密相區與催化劑稀相區相鄰存在。那麼,在催化劑密相區生成的產物氣體能夠快速的進入催化劑稀相區,由於催化劑稀相區中的催化劑含量稀疏,催化劑固體顆粒對產物氣體的阻力大大降低,從而能夠有效地降低產物返混。
2.由於本發明實施例通過兩個催化劑密相區進行氨氧化反應,即兩段式反應,通過實驗結果表明,本發明實施例這種氨氧化反應器不僅能夠有效地提高原料的轉化率,而且能夠大大的提高產物選擇性及產物收率。
3.通過設置催化劑溢流裝置使流化床反應器中催化劑密相區與催化劑稀相區的高度基本保持不變,從而保證氨氧化反應過程中產物收率。
4.本發明實施例通過為催化劑密相區設置換熱器,能夠保證流化床反應器內溫度調節的靈活性,使氨氧化過程能夠在特定的溫度下進行,避免溫度過高造成催化劑燒結失活,同時,也避免了溫度過低造成的轉化不徹底。
5.本發明實施例通過為兩個催化劑密相區分別設置換熱器,使兩個催化劑密相區以不同的溫度進行反應,實現了對溫度的靈活控制,從而保證產物的收率,同時能夠避免局部溫度過高以及催化劑燒結,並能夠減少其他副反應。
6.一般來說,氣體進入反應器中會形成大量的氣泡,而氣泡內部會包裹一些催化劑,另外,只有氣泡表面能夠與催化劑接觸,一定程度上會降低產物收率,而通過本發明實施例提供的氨氧化反應器中的二段分布板能夠破碎氣泡增加氣體與催化劑的接觸,從而提高產物收率。
7.通過中試實驗發現,通過本發明實施例提供的具有二段分布板的氨氧化反應器進行氨氧化反應,能夠使原料轉化率達到97%以上,產物選擇性達到90%以上,目標產物收率達到87%以上。而現有技術在進行氨氧化反應時,其原料轉化率一般為85%,產物選擇性僅70%,目標產物收率僅為59%。因此,與現有技術相比,本發明實施例提供的氨氧化反應器能夠明顯的提高轉化率、產物選擇性以及產物收率。
8.通過兩個分布器分別向流化床反應器輸入空氣和氨氣,保證氣體通入時的安全性,同時,對氣體溫度控制靈活,可使分布器的熱點溫度比現有技術降低10~20℃。
9.通過對每一個催化劑密相區通入不同含量的空氣可調節不同密相區的氧含量,尤其是在上反應空間中的催化劑密相區提供過量的氧氣氛圍,不僅可以提高反應器整體的轉化率,也可對消除反應過程中的少量積碳。
需要說明的是,在本文中,諸如第一和第二之類的關係術語僅僅用來將一個實體或者操作與另一個實體或操作區分開來,而不一定要求或者暗示這些實體或操作之間存在任何這種實際的關係或者順序。而且,術語「包括」、「包含」或者其任何其他變體意在涵蓋非排他性的包含,從而使得包括一系列要素的過程、方法、物品或者設備不僅包括那些要素,而且還包括沒有明確列出的其他要素,或者是還包括為這種過程、方法、物品或者設備所固有的要素。在沒有更多限制的情況下,由語句「包括一個······」限定的要素,並不排除在包括所述要素的過程、方法、物品或者設備中還存在另外的相同因素。
最後需要說明的是:以上所述僅為本發明的較佳實施例,僅用於說明本發明的技術方案,並非用於限定本發明的保護範圍。凡在本發明的精神和原則之內所做的任何修改、等同替換、改進等,均包含在本發明的保護範圍內。