具有光催化性的氫氧化苯甲酸銅‑SiO2複合材料的製備方法與流程
2023-04-23 07:09:53 2
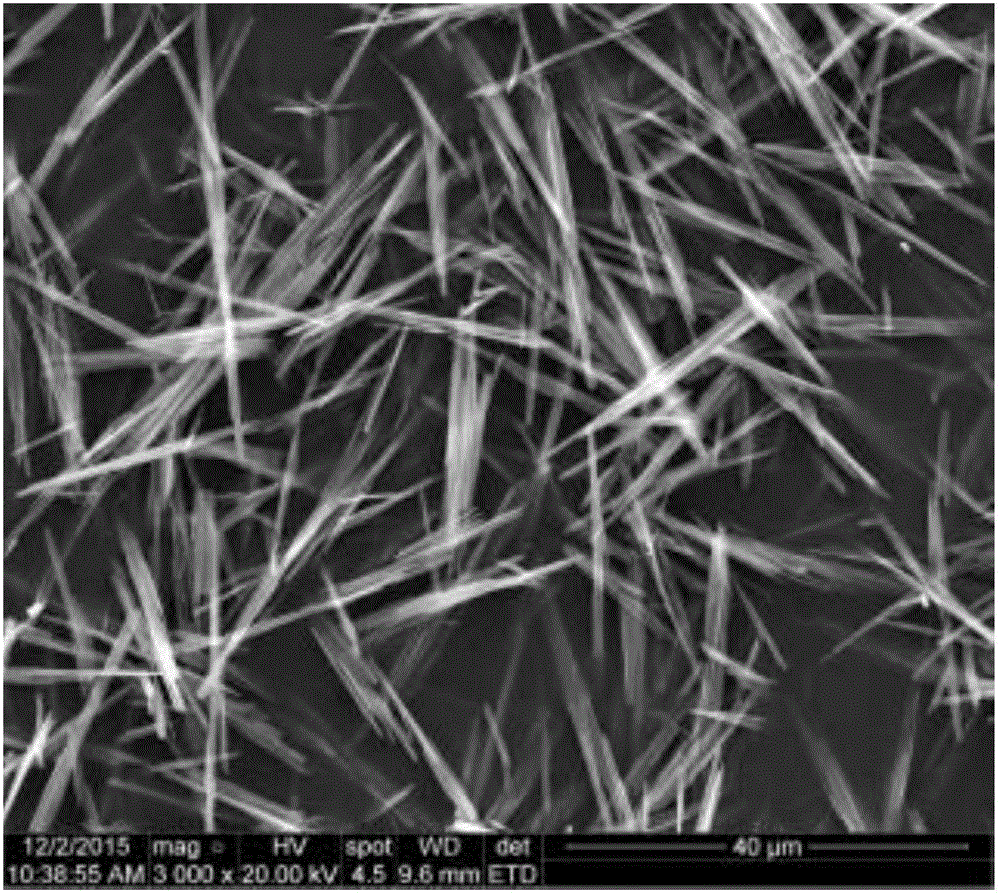
本發明屬於光催化材料製備技術領域,具體涉及一種具有光催化性的氫氧化苯甲酸銅-SiO2複合材料的製備方法。
背景技術:
近些年來我國經濟高速發展,工業、建築、紡織等行業發展勢頭迅猛,大量工業廢棄物排放導致環境汙染問題愈加嚴重。因此對各類環境汙染物的有效處理已經成為一項迫在眉睫的任務。其中造紙、印染等行業所排放的大量有色廢水具有毒性大、成分複雜、難生物降解等特點,關於這類廢水的處理一直受到研究人員的廣泛關注。目前傳統處理工藝主要有活性炭吸附法、生物降解法、加藥吸附法。但上述幾種方法存在處理成本高、降解不徹底、存在二次汙染等方面缺陷,難以大規模推廣或處理效果不佳。
光催化技術具有綠色環保、乾淨節能等特點,是學術界非常活躍的研究領域之一,在環境保護、新型功能材料開發、太陽能利用等方面具有廣闊的應用前景。但以TiO2為代表的光催化材料容易發生光腐蝕現象,穩定性不高;且能帶間隙寬,內部載流子符合率高等缺陷使得光催化性能不佳,大大限制了進一步的應用與發展。因此對已有材料的改性、修飾和開發新型光催化材料成為當前研究的熱點問題。
技術實現要素:
本發明的目的是提供一種具有光催化性的氫氧化苯甲酸銅-SiO2複合材料的製備方法,解決現有光催化材料能量利用率低以及對染料廢水光催化降解效果差的問題。
本發明所採用的技術方案為,一種具有光催化性的氫氧化苯甲酸銅-SiO2複合材料的製備方法,具體按照以下步驟實施:
步驟1,製備層狀氫氧化苯甲酸銅;
步驟2,製備二氧化矽微球;
步驟3,將步驟1所得的層狀氫氧化苯甲酸銅與步驟2所得的二氧化矽微球置於水中,在120~160℃條件下進行水熱合成反應24~36h後,將所得產物經抽濾、用去離子水、無水乙醇洗滌、在恆溫乾燥箱乾燥24h,即得層狀氫氧化苯甲酸銅-SiO2複合材料(LDH-Cu@SiO2)。
本發明的特徵還在於,
步驟1中,層狀氫氧化苯甲酸銅的製備過程為:
步驟1.1:向硝酸銅溶液中滴加濃氨水,不斷攪拌,待生成淡藍色沉澱後,在常溫下繼續攪拌0.5~1h,待溶液徹底沉澱後陳化6~8h,進行抽濾,並用去離子水對沉澱物進行多次洗滌,隨後在常溫下乾燥24~32h,得氫氧化銅;
步驟1.2:將氫氧化銅、苯甲酸置於去離子水中,在90~100℃條件下進行充分攪拌下回流反應18~24h,待反應結束後,產物經過抽濾、洗滌、常溫乾燥24~32h,即得層狀氫氧化苯甲酸銅(LDH-Cu)。
步驟1.1中,硝酸銅溶液的濃度為0.32mol/L,濃氨水與硝酸銅溶液的用量比為1:18~25。
步驟1.2中,氫氧化銅與苯甲酸的用量比為1~1.5:1。
步驟2中,二氧化矽微球的製備過程為:
步驟2.1:在常溫下,將去離子水、氨水和無水乙醇混合,配製得A溶液;將乙醇與正矽酸乙酯混合,配製得B溶液;
步驟2.2:攪拌同時將B溶液滴加到A溶液中,密封反應24h,經高速離心分離,經洗滌、乾燥後,即得二氧化矽。
A溶液中氨水與去離子水的用量比為1:1~1.2,無水乙醇與去離子水的用量比為1:1.5~2;B溶液中乙醇與正矽酸乙酯的用量比為4~5:1。
步驟2.2中,A溶液與B溶液的用量比為1~1.5:1。
步驟3中,層狀氫氧化苯甲酸銅與二氧化矽微球的用量比為1~2:1。
本發明的有益效果是,通過自組裝法製備了核-殼結構的LDH-Cu@SiO2複合材料,纖維狀的LDH-Cu均勻地包裹在SiO2微球上,整體形貌完整。與常規層狀納米化合物相比,在反應體系中分散性更好,光催化活性更好;LDH-Cu@SiO2複合材料中的LDH-Cu能夠藉助離子交換、靜電作用等多種方式協同降解染料廢水中有機物質,提高染料廢水的降解效率。該製備方法簡單有效,不需要特殊設備,為更多不同功能材料的複合提供了一種簡單可行的方法。
附圖說明
圖1為本發明實施例所得層狀氫氧化苯甲酸銅的SEM圖;
圖2為本發明方法所得層狀氫氧化苯甲酸銅-二氧化矽的SEM圖;
圖3為本發明實施例3所得層狀氫氧化苯甲酸銅-二氧化矽的SEM圖;
圖4為本發明具有光催化性的氫氧化苯甲酸銅-SiO2複合材料的製備方法所得層狀氫氧化苯甲酸銅-二氧化矽對甲基橙的降解效果圖;
圖5為本發明具有光催化性的氫氧化苯甲酸銅-SiO2複合材料的製備方法所得層狀氫氧化苯甲酸銅-二氧化矽對羅丹明的降解效果圖;
圖6為本發明具有光催化性的氫氧化苯甲酸銅-SiO2複合材料的製備方法所得層狀氫氧化苯甲酸銅-二氧化矽的降解原理圖。
具體實施方式
下面結合附圖和具體實施方式對本發明進行詳細說明。
本發明一種具有光催化性的氫氧化苯甲酸銅-SiO2複合材料的製備方法,先採用沉澱法製備氫氧化銅,以氫氧化銅、苯甲酸為主要原料製備層狀氫氧化苯甲酸銅,再使其與二氧化矽微球進行水熱合成反應,即得組裝產物-氫氧化苯甲酸銅-二氧化矽。具體按照以下步驟實施:
步驟1,向硝酸銅溶液中滴加濃氨水,不斷攪拌,待生成淡藍色沉澱後,在常溫下繼續攪拌0.5~1h,待溶液徹底沉澱後陳化6~8h,進行抽濾,並用去離子水對沉澱物進行多次洗滌,隨後在常溫下乾燥24~32h,得氫氧化銅;其中,硝酸銅溶液的濃度為0.32mol/L,濃氨水與硝酸銅溶液的用量比為1:18~25。
步驟2,將氫氧化銅、苯甲酸置於去離子水中,在90~100℃條件下進行充分攪拌下回流反應18~24h,待反應結束後,產物經過抽濾、洗滌、常溫乾燥24~32h,即得層狀氫氧化苯甲酸銅(LDH-Cu)。其中,氫氧化銅與苯甲酸的用量比為1~1.5:1。
步驟3,在常溫下,將去離子水、氨水和無水乙醇混合,配製得A溶液;將乙醇與正矽酸乙酯混合,配製得B溶液;攪拌同時將B溶液滴加到A溶液中(A溶液與B溶液的用量比為1~1.5:1),密封反應24h,經高速離心分離,經洗滌、乾燥後,即得二氧化矽。其中,A溶液中氨水與去離子水的用量比為1:1~1.2,無水乙醇與去離子水的用量比為1:1.5~2。B溶液中乙醇與正矽酸乙酯的用量比為4~5:1。
步驟4,將步驟2所得的層狀氫氧化苯甲酸銅與步驟3所得的二氧化矽微球置於水中(層狀氫氧化苯甲酸銅與二氧化矽微球的用量比為1~2:1),隨後將其置於襯有聚四氟乙烯的不鏽鋼反應釜中,放入到均相反應器中在120~160℃條件下進行水熱合成反應24~36h後,將所得產物經抽濾、用去離子水、無水乙醇洗滌、在恆溫乾燥箱乾燥24h,即得層狀氫氧化苯甲酸銅-二氧化矽複合材料(LDH-Cu@SiO2)。
實施例1
步驟1,稱取3.0g的硝酸銅溶於50mL水中,得硝酸銅溶液,向硝酸銅溶液中滴加2.5mL濃氨水,不斷攪拌,待生成淡藍色沉澱後,在常溫下繼續攪拌0.5h,待溶液徹底沉澱後陳化6h,進行抽濾,並用去離子水對沉澱物進行多次洗滌,隨後在常溫下乾燥24h,得氫氧化銅;
步驟2,將0.7140g氫氧化銅、0.7170g苯甲酸置於20mL去離子水中,在95℃條件下進行充分攪拌下回流反應24h,待反應結束後,產物經過抽濾、洗滌、常溫乾燥24h,即得層狀氫氧化苯甲酸銅(LDH-Cu)。
步驟3,在常溫下,將31.5mL去離子水、30mL氨水和20mL無水乙醇混合,配製得A溶液;將50mL乙醇與11mL正矽酸乙酯混合,配製得B溶液;攪拌同時將B溶液滴加到A溶液中,密封反應24h,經高速離心分離,經洗滌、乾燥後,即得二氧化矽。
步驟4,取0.1g層狀氫氧化苯甲酸銅與0.1g二氧化矽微球置於20mL水中,隨後將其置於襯有聚四氟乙烯的不鏽鋼反應釜中,放入到均相反應器中在140℃條件下進行水熱合成反應30h後,將所得產物經抽濾、用去離子水、無水乙醇洗滌、在恆溫乾燥箱乾燥24h,即得層狀氫氧化苯甲酸銅-二氧化矽複合材料(LDH-Cu@SiO2)。
實施例2
步驟1,稱取3.0g的硝酸銅溶於50mL水中,得硝酸銅溶液,向硝酸銅溶液中滴加3mL濃氨水,不斷攪拌,待生成淡藍色沉澱後,在常溫下繼續攪拌1h,待溶液徹底沉澱後陳化8h,進行抽濾,並用去離子水對沉澱物進行多次洗滌,隨後在常溫下乾燥32h,得氫氧化銅;
步驟2,將1.5g氫氧化銅、1g苯甲酸置於45mL去離子水中,在90℃條件下進行充分攪拌下回流反應18h,待反應結束後,產物經過抽濾、洗滌、常溫乾燥32h,即得層狀氫氧化苯甲酸銅(LDH-Cu)。
步驟3,在常溫下,將30mL去離子水、30mL氨水和20mL無水乙醇混合,配製得A溶液;將50mL乙醇與10mL正矽酸乙酯混合,配製得B溶液;攪拌同時將B溶液滴加到A溶液中,密封反應24h,經高速離心分離,經洗滌、乾燥後,即得二氧化矽。
步驟4,取0.2g層狀氫氧化苯甲酸銅與0.1g二氧化矽微球置於20mL水中,隨後將其置於襯有聚四氟乙烯的不鏽鋼反應釜中,放入到均相反應器中在120℃條件下進行水熱合成反應24h後,將所得產物經抽濾、用去離子水、無水乙醇洗滌、在恆溫乾燥箱乾燥24h,即得層狀氫氧化苯甲酸銅-二氧化矽複合材料(LDH-Cu@SiO2)。
實施例3
步驟1,稱取3.0g的硝酸銅溶於50mL水中,得硝酸銅溶液,向硝酸銅溶液中滴加2mL濃氨水,不斷攪拌,待生成淡藍色沉澱後,在常溫下繼續攪拌45min,待溶液徹底沉澱後陳化7h,進行抽濾,並用去離子水對沉澱物進行多次洗滌,隨後在常溫下乾燥28h,得氫氧化銅;
步驟2,將1.2g氫氧化銅、1g苯甲酸置於36mL去離子水中,在100℃條件下進行充分攪拌下回流反應20h,待反應結束後,產物經過抽濾、洗滌、常溫乾燥28h,即得層狀氫氧化苯甲酸銅(LDH-Cu)。
步驟3,在常溫下,將36mL去離子水、30mL氨水和24mL無水乙醇混合,配製得A溶液;將40mL乙醇與10mL正矽酸乙酯混合,配製得B溶液;攪拌同時將B溶液滴加到A溶液中,密封反應24h,經高速離心分離,經洗滌、乾燥後,即得二氧化矽。
步驟4,取0.15g層狀氫氧化苯甲酸銅與0.1g二氧化矽微球置於20mL水中,隨後將其置於襯有聚四氟乙烯的不鏽鋼反應釜中,放入到均相反應器中在160℃條件下進行水熱合成反應32h後,將所得產物經抽濾、用去離子水、無水乙醇洗滌、在恆溫乾燥箱乾燥24h,即得層狀氫氧化苯甲酸銅-二氧化矽複合材料(LDH-Cu@SiO2)。
圖1為本發明實施例步驟2所得LDH-Cu的SEM圖,由圖可以看出,合成的層狀化合物具有纖維狀的形貌特徵,可以清楚觀察到這種由於納米單元層重疊形成特殊結構。圖2和圖3為利用本發明方法不同水熱反應時間所得產物的SEM圖,其中,圖2是在160℃24h的情況下反應生成的,圖3是在160℃反應36h的情況下生成的。反應24h時雖然大多數層狀氫氧化苯甲酸銅都包裹在二氧化矽微球上,但其基本形貌仍然呈現球狀,僅有少量的類似蜂窩狀的結構生成。而反應36h時看出層狀氫氧化苯甲酸銅與二氧化矽組裝生成的LDH-Cu@SiO2呈現出均勻的蜂窩狀結構,具有較大比表面積,且組裝結構完整。後續光催化實驗選取這種結構複合材料進行。
將所製備的LDH-Cu@SiO2複合材料進行光催化實驗,以測試其光催化活性:
a:對甲基橙催化降解
取50mL濃度為10mg/L的甲基橙溶液放入100mL燒杯中,加入0.05g LDH-Cu@SiO2材料(具有實施例3的蜂窩狀結構),開啟磁力攪拌保證反應過程中材料分散均勻,在避光黑暗的條件下反應1h,中間每次間隔20min取少量溶液經過高速離心、過濾後在463nm處測定吸光度值,隨後開啟紫外燈照射繼續反應,每次間隔20min取樣按照上述方法測定吸光度值,直到連續測出的吸光度值趨於穩定時停止。將測得的實時數據按照公式η=﹝(A1-A2)/A2﹞*100%計算催化降解率。
b:對羅丹明B催化降解
過程與a相同,僅在554nm處測定吸光度值。
測試結果如圖4和5所示,其中圖4為甲基橙降解效果,圖5為羅丹明B降解效果。在剛開始的1h內,體系處於暗反應條件下,對照組(1)TiO2對有機染料基本無降解,原因在於光催化反應條件不具備。但隨後在紫外光照射條件下,第1組降解效率迅速增加,最終降解率超過95%。而對照組(2)LDH-Cu則在體系處於暗反應條件下就表現出一定處理能力,這與層狀化合物具備離子交換能力有關,部分染料分子在特定體系pH值下以負離子形式進入LDH-Cu化合物層間,藉助靜電作用力吸附在材料上。所以在剛開始的1h內,甲基橙溶液濃度逐漸下降,但光催化活性不高,最終降解效率為70%左右。第(3)組LDH-Cu@SiO2結果表明,當形成核-殼複合結構之後,該材料不但在暗反應條件下能夠直接吸附染料分子,而且在紫外光照射下,光催化活性較好,最終降解效率接近100%。在同等條件下,該催化劑不但適用範圍廣,而且吸附作用和光催化降解的協同作用也使得其降解效率比單純TiO2光催化劑要好。圖4實驗結果表明對羅丹明B的處理也呈現類似的結果。
圖6為LDH-Cu@SiO2降解染料原理過程示意圖,形成複合結構後,一方面以氫鍵形式與SiO2直接連接的LDH-Cu能夠將染料分子吸附至層間,同時在紫外光照射條件下,與SiO2直接結合的染料分子通過光催化氧化的形式被降解。且形成LDH-Cu@SiO2後材料比表面積、溶液中分散性能均有一定程度提高,最終有助於提升光催化降解效率。
對於光化學反應而言,反應介質對反應速率、產物純度等方面有重要影響,均相溶液和非均相介質中的差別很大。層狀雙氫氧化物材料(Layered double hydroxide,LDH)可以作為主體材料,將具有光活性的物質固定,並提供有序可控的二維層狀空間,從而改變主客體的光學、電學性質並用於光催化領域。納米SiO2微球具有表面光滑、粒徑統一、分散性良好的優點,並且兼具納米粒子比表面積大、量子尺寸效應特點。通過自組裝形成LDH@SiO2核-殼結構的納米複合材料,不但有利於增加催化劑的分散性,改變反應介質來提高光催化活性;並且特殊的核-殼結構降低了分離過程中材料的損失,部分待降解物也能被LDH類物質直接吸附,從而以協同作用的方式共同提高染料廢水的降解效率,在實用化新型光催化劑研製方面是一項突破。