一種運車架的製作方法
2023-05-06 16:59:52 2
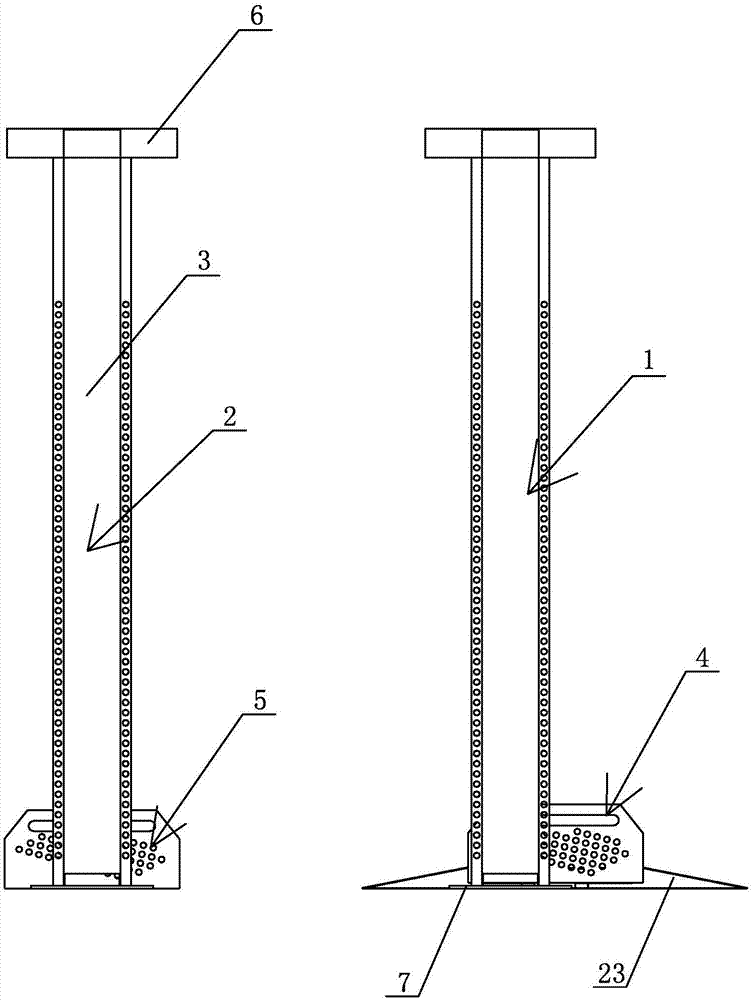
本發明涉及一種車輛運輸裝置,尤其涉及一種運車架。
背景技術:
車輛生產完成之後,一般是利用大貨車將車輛運輸至預定地點,這樣採用大貨車同時運輸多輛汽車,既能夠降低運輸成本,同時新車也不會出現公裡數,防止出現不必要的麻煩及糾紛。
在現有技術中,對車輛進行運輸時,一般為專車專用,也就是同一種汽車,必須採用同一種類型的貨車才能運輸,局限性強;如果採用廂式貨車運輸,運輸車的內部結構複雜、專業、難以拆解,這樣的局限性也特別強,導致運輸車只能對車輛進行運輸,難以運輸其他物品,成本高;而框架式的運輸車輛,易對車輛造成劃傷,而且清潔度低,在車輛成交前,還需要專門的打理,非常的不方便。採用海運的貨櫃,則沒有專用的固定裝置,需要人工進行固定,其固定的穩定性差,容易造成車輛的磨損及損壞。
技術實現要素:
本發明目的是提供一種運車架,通過使用該結構,提高了車輛運輸的穩定性及牢固性,提高了車輛的運輸範圍,減小了車輛運輸的局限性。
為達到上述目的,本發明採用的技術方案是:一種運車架,包括前輪固定機構及後輪固定機構,所述前輪固定機構設置於所述後輪固定機構的正前方,所述前輪固定機構包括兩根立柱及設置於兩根立柱之間的前輪固定架,所述後輪固定機構包括兩根立柱及設置於兩根立柱之間的後輪固定架;所述前輪固定架的兩端螺接安裝於兩根所述立柱的中部,所述後輪固定架的兩端螺接安裝於兩根所述立柱的中部,所述前輪固定架與立柱底部之間的高度為第一間距,所述後輪固定架與立柱底部之間的高度為第二間距,所述第一間距大於所述第二間距,所述前輪固定架與後輪固定架之間構成的平面與水平面之間呈3°~30°的夾角。
上述技術方案中,所述立柱頂部設有一中空定位塊,底部設有定位板,所述立柱頂部通過所述中空定位塊經棘輪拉緊器與貨櫃頂部連接,所述立柱底部通過螺栓經定位板與貨櫃底部連接。
上述技術方案中,所述中空定位塊的底部設有複數塊吊裝板,每塊所述吊裝板上設有一吊裝孔;所述立柱的底部兩側分別設有一吊環,所述吊環設置於所述定位板的正上方。
上述技術方案中,所述立柱為中部開槽結構,所述立柱中部設有條形通槽,所述立柱的兩側分別設有複數個通孔,所述通孔由上至下均布於所述立柱上。
上述技術方案中,所述前輪固定架及後輪固定架的兩端均分別固定有一安裝板,所述安裝板上設有複數個連接孔,所述安裝板經螺栓穿過所述連接孔及通孔與所述立柱相連;每塊所述安裝板上設有一通槽,所述通槽垂直於所述前輪固定架或後輪固定架設置;每塊所述安裝板的外側分別設有一開口朝外的u型定位板,所述通槽內設有一鉚釘,所述鉚釘滑動設置於所述通槽內,所述鉚釘的一端設置於所述安裝板的內側,另一端設置於所述安裝板的外側,且所述鉚釘的外側與所述u型定位板的中部相連,所述u型定位板滑動設置於所述條形通槽內;所述安裝板內側面的兩端分別設有一吊環。
上述技術方案中,所前輪固定架為中空結構,包括兩根相互間隔設置的連接板,兩根所述連接板相互間隔設置,兩根連接板的兩端分別與所述安裝板相連;還設有兩根加強筋,兩根所述加強筋分別間隔設置於兩根連接板的中部,所述加強筋的兩端分別與兩根所述連接板的中部相連。
上述技術方案中,所述連接板的截面呈等腰梯形結構。
上述技術方案中,所述後輪固定架包括相互間隔設置的支撐板及支撐杆,所述支撐板與支撐杆相互平行設置,所述支撐杆設置於所述支撐板的前側,所述支撐板與支撐杆的兩端分別與兩塊所述安裝板的內側相連;所述支撐板與支撐杆之間還設有兩塊限位板,兩塊所述限位板相互間隔設置,兩塊所述限位板的的兩端分別與所述支撐板及支撐杆的中部相連。
上述技術方案中,所述支撐杆的底部與所述支撐板的底部齊平設置。
上述技術方案中,所述前輪固定架的下方還設有兩塊爬坡架,兩塊爬坡架設置於前輪固定架兩端安裝板的內側,且所述爬坡架靠近對應側安裝板設置;所述爬坡架包括前、後爬坡板及中部支撐板,所述中部支撐板設置於所述前、後爬坡板之間,所述前爬坡板的頂面向前傾斜向下設置,所述後爬坡板的頂面向後傾斜向下設置,所述中部支撐板設置於兩根連接板之間。
由於上述技術方案運用,本發明與現有技術相比具有下列優點:
1.本發明中通過設置前輪固定機構及後輪固定機構,其中,利用前輪固定機構中的前輪固定架對汽車的兩個前輪進支撐固定,利用後輪固定機構中的後輪固定架對汽車的後輪進行支撐固定,同時,前輪固定架及後輪固定架都能夠安裝與立柱的中部,這樣通過設置前輪固定機構及後輪固定機構,前輪固定架及後輪固定架能夠將一輛汽車抬起,然後前輪固定架及後輪固定架的下方還能夠放置一輛汽車,這樣運車架不僅能夠同時同時對兩輛車進行支撐固定,同時固定的牢固性及穩定性好,能夠有效防止車輛直接的磨損,同時便於拆卸,適用於不同型號的汽車固定,適用範圍廣,能夠降低運輸成本;
2.本發明中前輪固定機構與後輪固定機構的距離能夠隨意調節,這樣能夠適應不同型號的車輛,便於對不同的車輛進行運輸,能夠降低運輸成本,而且運輸成本低廉;
3.本發明中前輪固定架及後輪固定架的兩端都是安裝與立柱上,這樣前輪固定機構與後輪固定機構中的立柱結構都是一樣,這樣可以根據不同寬度的車輛,更換不同長度的前輪、後輪固定架,便於適應不同的車輛運輸固定,適用範圍廣;
4.本發明中立柱利用螺栓與運輸設備固定,這樣在使用時,可以根據時間的情況,對立柱的位置進行調節,當車輛運輸完成之後,可以將前輪固定機構及後輪固定機構拆卸,進行其他貨物的運輸,這樣能夠儘可能的降低運輸成本,提高運輸設備的利用率,減少能耗,降低成本。
附圖說明
圖1是本發明實施例一中的結構示意圖(前、後輪固定架與立柱未組裝狀態);
圖2是圖1的俯視圖;
圖3是圖1的立體結構示意圖;
圖4是圖3的局部放大圖ⅰ;
圖5是圖3的局部放大圖ⅱ;
圖6是圖3的局部放大圖ⅲ;
圖7是圖3的局部放大圖ⅳ。
其中:1、前輪固定機構;2、後輪固定機構;3、立柱;4、前輪固定架;5、後輪固定架;6、中空定位塊;7、定位板;8、吊裝板;9、吊裝孔;10、吊環;11、通孔;12、安裝板;13、u型定位板;14、條形通槽;15、通槽;16、連接孔;17、連接板;18、加強筋;19、支撐板;20、支撐杆;21、限位板;22、鉚釘;23、爬坡架;24、前爬坡板;25、後爬坡板;26、中部支撐板。
具體實施方式
下面結合附圖及實施例對本發明作進一步描述:
實施例一:參見圖1~7所示,一種運車架,包括前輪固定機構1及後輪固定機構2,所述前輪固定機構1設置於所述後輪固定機構2的正前方,所述前輪固定機構1包括兩根立柱3及設置於兩根立柱3之間的前輪固定架4,所述後輪固定機構2包括兩根立柱3及設置於兩根立柱3之間的後輪固定架5;所述前輪固定架4的兩端螺接安裝於兩根所述立柱3的中部,所述後輪固定架5的兩端螺接安裝於兩根所述立柱3的中部,所述前輪固定架4與立柱3底部之間的高度為第一間距,所述後輪固定架5與立柱3底部之間的高度為第二間距,所述第一間距大於所述第二間距,所述前輪固定架4與後輪固定架5之間構成的平面與水平面之間呈3°~30°的夾角。
在本實施了中,在使用時,可以將運車架安裝與箱式運輸車內,也可以直接放置於框架式運輸車內,也可以安裝與貨櫃內。以貨櫃為例,在對車輛進行運輸時,可以先對需要運輸的車輛進行尺寸的測量,然後根據需要運輸的車輛長度及寬度,先選用對應長度的前輪固定架及後輪固定架,其中,前輪、後輪固定架的長度,必定要大於車輛的寬度,這樣能夠適用於一定寬度的車輛,如果需要運輸的車輛寬度大於這個數值,則可以選用長度更長規格的前輪、後輪固定架。然後根據待運輸車輛長度,對前輪固定機構及後輪固定機構中的立柱進行安裝。可以將立柱安裝與貨櫃的底部,然後立柱的側壁及頂部可以與貨櫃的側壁及頂部進行固定。如果採用框架式的運輸車,可以將立柱底部安裝與車輛底部,側部與框架固定。立柱安裝完成之後,將前輪固定架放置於前輪固定機構的兩根立柱之間,將後輪固定架放置於後輪固定機構的兩根立柱之間,然後將車輛的前輪拉動於前輪固定架上,將車輛的後輪拉動於後輪固定架上,此時,前輪固定架對車輛的前輪進行了初步定位及固定,後輪固定架對車輛的後輪進行了初步的定位及固定。然後利用提升機構,將前輪固定架及後輪固定架進行提升,當前輪固定架與後輪固定架離立柱底部之間有10釐米~20釐米時,操作人員採用綁紮帶對車輛的前輪及後輪進行固定,其中前輪利用綁紮帶固定於前輪固定架上,後輪利用綁紮帶固定於後輪固定架上。
車輛的前輪及後輪固定完成之後,提升機構繼續將前輪、後輪固定架提升,在這個過程中,車輛的前輪的高度要高於後輪的高度,當前輪、後輪固定架下方的位置,能夠容納一輛汽車的高度時,停止提升,操作人員再利用螺栓,將前輪固定架及後輪固定架的兩端分別固定於對應側的立柱上,完成一輛汽車的固定,然後再放入下一輛汽車,將下一輛汽車放置於前輪、後輪固定架的下方,再利用綁紮帶對將輛汽車的輪胎固定於立柱上,完成車輛的固定。再本實施了中,一組運車架能夠固定兩輛汽車,而且不會存在相互幹擾的問題,同時對車輛固定的牢固性強,運輸設備再運輸過程中,運車架上的車輛也不會移動,穩定性好。
在本實施了中,通過將前輪固定架與後輪固定架之間構成的平面與水平面之間呈3°~30°的夾角,這樣可以使設置在運車架上面的汽車傾斜設置,這樣運輸設備在剎車或啟動過程中,所產生的慣性,也不會對車輛造成任何影響,保證運車的穩定性。同時,小型車輛一般為三廂車或者兩廂車,車頭處一般會低於車身,這樣運車架下方的車輛,其車頭能夠直接放置於上方車輛的正下方,這樣還能夠減小運車架的整體高度,提高運輸設備運輸時的穩定性。
參見圖1~7所示,所述立柱3頂部設有一中空定位塊6,底部設有定位板7,所述立柱3頂部通過所述中空定位塊6經棘輪拉緊器與貨櫃頂部連接,所述立柱3底部通過螺栓經定位板與貨櫃底部連接。所述中空定位塊6的底部設有複數塊吊裝板8,每塊所述吊裝板8上設有一吊裝孔9;所述立柱3的底部兩側分別設有一吊環10,所述吊環10設置於所述定位板7的正上方。
在本實施了中,如果運輸設備為中空結構,則可以採用外置的吊裝設備對前輪、後輪固定架進行吊裝提升,如果為箱式的封閉式結構,則需要採用吊輪及鏈條進行提升,而通過吊裝孔、吊裝板及吊環的設置,這樣便於吊輪及鏈條的安裝,便於對前、後輪固定架進行提升,便於適應不同的場合,適用範圍廣。然後立柱的頂部利用棘輪拉緊器與貨櫃的頂部進行拉緊固定,底部通過螺栓穿過定位板與貨櫃底部固定,完成立柱的安裝固定。
參見圖1~7所示,所述立柱3為中部開槽結構,所述立柱3中部設有條形通槽14,所述立柱3的兩側分別設有複數個通孔11,所述通孔11由上至下均布於所述立柱3上。
所述前輪固定架4及後輪固定架5的兩端均分別固定有一安裝板12,所述安裝板12上設有複數個連接孔16,所述安裝板16經螺栓穿過所述連接孔16及通孔11與所述立柱3相連;每塊所述安裝板12上設有一通槽15,所述通槽垂直於所述前輪固定架4或後輪固定架5設置;每塊所述安裝板12的外側分別設有一開口朝外的u型定位板13,所述通槽15內設有一鉚釘22,所述鉚釘22滑動設置於所述通槽15內,所述鉚釘22的一端設置於所述安裝板的內側,另一端設置於所述安裝板的外側,且所述鉚釘的外側與所述u型定位板的中部相連,所述u型定位板滑動設置於所述條形通槽14內;所述安裝板12內側面的兩端分別設有一吊環10。通過吊環的設置,便於對前、後輪固定架進行提升安裝。
通過在立柱上設置通孔,這樣便於前、後輪固定架與立柱的安裝固定,同時,通孔由上至下均布於立柱上,這樣前、後輪固定架能夠固定在立柱的任何一個位置,這樣便於適應不同的場合,適用範圍廣。
同時,在本實施了中,通過在安裝板的外側設置u型定位板,u型定位板能夠滑動設置於立柱的條形通槽內,在利用提升機構帶動前、後輪固定架上升或者下降的過程中,能夠利用立柱及u型定位板對前、後輪固定架進行限位,這樣能夠防止前、後輪固定架前、後、左、右的晃動,也就是防止車輛在提升過程中晃動,能夠保證車輛提升過程的穩定性。車輛提升完成之後,再利用螺栓對安裝板與立柱進行鎖緊固定,也就是對汽車的位置進行固定。
參見圖1~7所示,所前輪固定架4為中空結構,包括兩根相互間隔設置的連接板17,兩根所述連接板17相互間隔設置,兩根連接板17的兩端分別與所述安裝板12相連;兩根連接板17之間還設有兩根加強筋18,兩根所述加強筋分別間隔設置於兩根連接板的中部,所述加強筋的兩端分別與兩根所述連接板的中部相連。所述連接板的截面呈等腰梯形結構。
通過設置將兩根連接板相互間隔設置,這樣能夠形成一定的空腔,這樣能夠用於對車輛的後輪進行卡位、限位。同時,連接板的截面呈等腰梯形結構,這樣在實際使用時,連接板兩側均為傾斜面,這樣車輛在開上前輪固定架或者拉上前輪固定架上時,更加省力,也更加方便,同時,前輪固定架的內部會形成喇叭狀的開口結構,這樣在對車輛進行卡位時,能夠增大後輪固定架與車輪的接觸面積,減小對車輪的壓力,減小車輪的損傷。
參見圖1~7所示,所述後輪固定架5包括相互間隔設置的支撐板19及支撐杆20,所述支撐板19與支撐杆20相互平行設置,所述支撐杆20設置於所述支撐板19的前側,所述支撐板19與支撐杆20的兩端分別與兩塊所述安裝板12的內側相連;所述支撐板19與支撐杆20之間還設有兩塊限位板21,兩塊所述限位板21相互間隔設置,兩塊所述限位板的的兩端分別與所述支撐板及支撐杆的中部相連。所述支撐杆的底部與所述支撐板的底部齊平設置。
在本實施例中,由於支撐杆的底部會支撐板的底部齊平設置,這樣在車輛的後輪開到後輪固定架上時,不用費力,非常的方便,同時將其提升之後,也能夠利用支撐杆、支撐板及限位板之間構成的u型槽,能夠對後輪進行限位。
所述前輪固定架4的下方還設有兩塊爬坡架23,兩塊爬坡架23設置於前輪固定架4兩端安裝板12的內側,且所述爬坡架23靠近對應側安裝板12設置;所述爬坡架23包括前爬坡板24、後爬坡板25及中部支撐板26,所述中部支撐板設置於所述前、後爬坡板之間,所述前爬坡板的頂面向前傾斜向下設置,所述後爬坡板的頂面向後傾斜向下設置,所述中部支撐板設置於兩根連接板之間,也就是中部支撐板設置於空腔內。
通過設置爬坡架,這樣便於汽車的前輪通過前輪固定架,開到後輪固定架上,也便於汽車的後輪爬到後輪固定架上。
在本實施了中,前輪固定機構上可以設置至少一組前輪固定架,後輪固定機構上可以設置至少一組後輪固定架,根據實際要求,例如海運中的大型貨櫃,其高度高,則立柱的長度也可以更長,例如一根立柱的長度為8~10米,而一輛汽車的高度為1.5米左右,則前、後輪固定機構中可以分別設置4~6組的前、後輪固定架,這樣一組運車架可以固定4~6輛汽車,進一步提高運輸量,降低運輸成本。前、後輪固定架的數量,主要根據實際情況,以及立柱的長度,由操作人員隨意調節或者選取即可。