一種多元微合金化高強高導銅合金及其製備工藝的製作方法
2023-05-15 06:57:16 2
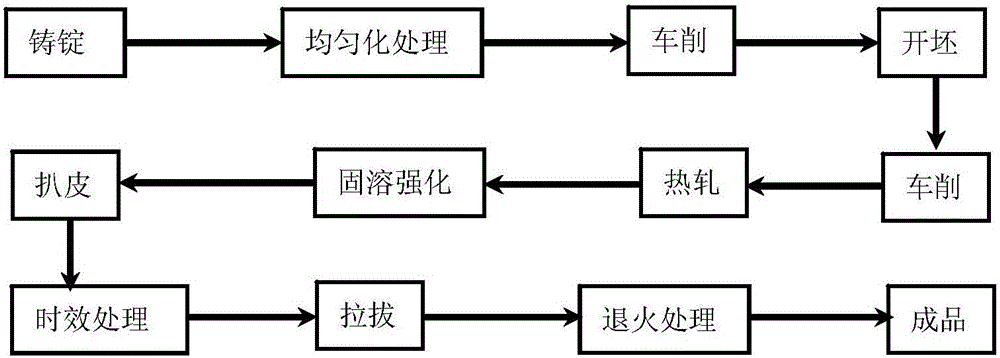
本發明涉及銅合金導體領域,尤其是一種多元微合金化高強高導銅合金及其製備工藝。
背景技術:
銅合金具有導電性能良好、高軟化溫度的特點,是電機換向器和接觸線的理想材料。今年來,隨著生產要求的增加,傳統銅合金導體的電阻率、拉斷力以及抗拉強度等性能差,不能滿足生產需求。
技術實現要素:
本發明要解決的技術問題是:克服現有技術中之不足,提供一種多元微合金化高強高導銅合金及其製備工藝。
本發明解決其技術問題所採用的技術方案是:一種多元微合金化高強高導銅合金,其組成成分為:
進一步地,多元微合金化高強高導銅合金的組成成分為:
一種多元微合金化高強高導銅合金的製備工藝,具有如下步驟:
(1)、準備配料,在熔煉爐內分別製備銅鉻合金、銅鋯合金、銅鎂合金和銅鑭合金;
(2)、造爐,石墨坩堝作為熔煉坩堝,石墨坩堝固定在熔煉爐內,進行烘爐,烘爐的時間保持在2小時以上,除去坩堝中的水蒸氣;
(3)、烘料和洗爐,將100重量份的純度為99.9%的電解銅,切割成所需要的形狀,放入熱處理爐中,溫度保持在600℃以下進行烘料,除去內部水蒸氣,烘料時間為1小時,0.60~1.10重量份銅鉻合金、0.25~0.35重量份銅鋯合金、0.05~0.12重量份銅鎂合金和0.10~0.30重量份銅鑭合金的烘料溫度均為300℃,保溫1小時,烘料結束之前,石墨坩堝內選用純銅進行熔煉,進而達到對坩堝及爐體進行洗爐,從而防止合金熔煉雜質對合金的汙染;
(4)、真空感應熔煉,將原料進行預熱處理後,先將銅鉻合金和電解銅原料放入石墨坩堝中,將銅鋯合金、銅鎂合金和銅鑭合金放入二次加料盒中,同時澆鑄模具內表面塗抹耐高溫的脫模劑後在放入熔煉爐內腔並進行預熱;關閉熔煉爐門進行抽真空,直至真空度小於10Pa,保持繼續抽真空的狀態,熔煉爐功率為15KW~110KW,讓石墨坩堝中的電解銅原料開始慢慢的軟化最後達到熔化,熔化的過程中合金內部的氣體會完全被排除;當電解銅原料完全熔化之後,打開二級抽真空模式,當真空度達到10-2Pa時,開始慢慢轉動石墨坩堝,使石墨坩堝中的爐料進行熔清;當石墨坩堝中的爐料熔清之後,保持精煉10分鐘,然後充入氬氣保護性氣體,降低熔煉爐功率,將二次加料盒內的剩餘合金原料加入,這樣以減少易揮發元素的燒損;增加功率並適當攪拌溶液,待石墨坩堝中溶液均勻後,關閉熔煉爐;
(5)、澆鑄,石墨坩堝中溶液在氬氣保護下倒入澆鑄模具進行澆鑄,澆鑄完成後待石墨坩堝與模具適當冷卻至200℃,放氣並取出銅合金鑄錠;
(6)、均勻化退火處理,將銅合金鑄錠在低於固相線的溫度1083℃下進行長時間的保溫加熱,消除澆鑄過程中由於密度不一致引起的成分偏析和冷卻速度不均勻引起的鑄錠內的殘餘應力,退火溫度為950℃,保溫2小時;
(7)、開坯,將均勻化退火處理後的銅合金鑄錠進行表面車削處理,去除由於鑄造過程引起的缺陷,銅合金在800~850℃進行鍛造開坯,將坯料鍛成50mm×50mm的方坯;
(8)、熱軋,將鍛成50mm×50mm的方坯進行表面打磨處理,去除鍛造開坯過程中產生的微裂紋,切除端部,然後在800~850℃進行熱軋,經過多道次熱軋,軋制到Φ7.5~8.5mm的銅合金杆;
(9)、固溶處理,固溶處理溫度為930℃,保溫1小時後,採用水冷法冷卻銅合金杆;
(10)、扒皮,將固溶處理後的銅合金杆通過扒皮模進行扒皮,去除表面氧化層,保證扒皮後的銅合金杆為Φ7.0~8.0mm;
(11)、冷變形,將去除氧化皮的Φ7.0~8.0mm銅合金杆進行冷變形,變形量為80%~85%,冷拉到Φ2.5~3.5mm;
(12)、時效處理,Φ2.5~3.5mm銅合金杆在常溫放入「井」式退火爐中,抽真空後充入氫氣,然後升溫至退火溫度450℃後,開始保溫2.5小時,保溫結束後隨爐冷卻,冷卻至室溫取出,氫氣作為保護氣氛可有效防止合金表面氧化,冷卻至室溫後排放保護氣氛;
(13)、拉拔,通過17模連拉連退拉絲機,將Φ2.5~3.5mm銅合金杆拉伸至直徑為0.5~0.7mm的線狀銅合金導體;
(14)、退火處理,將直徑為0.5~0.7mm的線狀銅合金導體通過直線大拉連續電加熱退火工藝技術,拉伸至直徑為0.1mm~0.2mm的線狀合金導體。
進一步地,所述步驟(1)中銅鉻合金的成分為70wt%銅,30wt%鉻;銅鋯合金的成分為70wt%銅,30wt%鋯;銅鎂合金的成分為70wt%銅,30wt%鎂;銅鑭合金的成分為70wt%銅,30wt%鑭。
本發明的有益效果是:本發明設計合理,操作簡便,經過配料、造爐烘料洗爐、熔煉、澆鑄以及強化工藝後製得的銅合金導體具有優異的電阻率、拉斷力以及抗拉強度,滿足生產需求。
附圖說明
下面結合附圖和實施例對本發明進一步說明。
圖1是本發明中熔煉工藝的工藝流程圖;
圖2是本發明中熱加工及強化工藝的工藝流程圖。
具體實施方式
現在結合圖1、圖2以及實施例對本發明作進一步的說明。
實施例1
一種多元微合金化高強高導銅合金,其特徵在於:其組成成分為:
這種多元微合金化高強高導銅合金的製備工藝,具有如下步驟:
(1)、準備配料,在熔煉爐內分別製備銅鉻合金、銅鋯合金、銅鎂合金和銅鑭合金;
(2)、造爐,石墨坩堝作為熔煉坩堝,石墨坩堝固定在熔煉爐內,進行烘爐,烘爐的時間保持在2小時以上,除去坩堝中的水蒸氣;
(3)、烘料和洗爐,將100公斤的純度為99.9%的電解銅,切割成所需要的形狀,放入熱處理爐中,溫度保持在600℃以下進行烘料,除去內部水蒸氣,烘料時間為1小時,0.80公斤銅鉻合金、0.30公斤銅鋯合金、0.067公斤銅鎂合金和0.20公斤銅鑭合金的烘料溫度均為300℃,保溫1小時,烘料結束之前,石墨坩堝內選用純銅進行熔煉,進而達到對坩堝及爐體進行洗爐,從而防止合金熔煉雜質對合金的汙染;
(4)、真空感應熔煉,將原料進行預熱處理後,先將銅鉻合金和電解銅原料放入石墨坩堝中,將銅鋯合金、銅鎂合金和銅鑭合金放入二次加料盒中,同時澆鑄模具內表面塗抹耐高溫的脫模劑後在放入熔煉爐內腔並進行預熱;關閉熔煉爐門進行抽真空,直至真空度小於10Pa,保持繼續抽真空的狀態,熔煉爐功率為15KW~110KW,讓石墨坩堝中的電解銅原料開始慢慢的軟化最後達到熔化,熔化的過程中合金內部的氣體會完全被排除;當電解銅原料完全熔化之後,打開二級抽真空模式,當真空度達到10-2Pa時,開始慢慢轉動石墨坩堝,使石墨坩堝中的爐料進行熔清;當石墨坩堝中的爐料熔清之後,保持精煉10分鐘,然後充入氬氣保護性氣體,降低熔煉爐功率,將二次加料盒內的剩餘合金原料加入,這樣以減少易揮發元素的燒損;增加功率並適當攪拌溶液,待石墨坩堝中溶液均勻後,關閉熔煉爐;
(5)、澆鑄,石墨坩堝中溶液在氬氣保護下倒入澆鑄模具進行澆鑄,澆鑄完成後待石墨坩堝與模具適當冷卻至200℃,放氣並取出銅合金鑄錠;
(6)、均勻化退火處理,將銅合金鑄錠在低於固相線的溫度1083℃下進行長時間的保溫加熱,消除澆鑄過程中由於密度不一致引起的成分偏析和冷卻速度不均勻引起的鑄錠內的殘餘應力,退火溫度為950℃,保溫2小時;
(7)、開坯,將均勻化退火處理後的銅合金鑄錠進行表面車削處理,去除由於鑄造過程引起的缺陷,銅合金在800~850℃進行鍛造開坯,將坯料鍛成50mm×50mm的方坯;
(8)、熱軋,將鍛成50mm×50mm的方坯進行表面打磨處理,去除鍛造開坯過程中產生的微裂紋,切除端部,然後在800~850℃進行熱軋,經過多道次熱軋,軋制到Φ8.0mm的銅合金杆;
(9)、固溶處理,固溶處理溫度為930℃,保溫1小時後,採用水冷法冷卻銅合金杆;
(10)、扒皮,將固溶處理後的銅合金杆通過扒皮模進行扒皮,去除表面氧化層,保證扒皮後的銅合金杆為Φ7.5mm;
(11)、冷變形,將去除氧化皮的Φ7.5mm銅合金杆進行冷變形,變形量為80%~85%,冷拉到Φ3.0mm;
(12)、時效處理,Φ3.0mm銅合金杆在常溫放入「井」式退火爐中,抽真空後充入氫氣,然後升溫至退火溫度450℃後,開始保溫2.5小時,保溫結束後隨爐冷卻,冷卻至室溫取出,氫氣作為保護氣氛可有效防止合金表面氧化,冷卻至室溫後排放保護氣氛;
(13)、拉拔,通過17模連拉連退拉絲機,將Φ3.0mm銅合金杆拉伸至直徑為0.6mm的線狀銅合金導體;
(14)、退火處理,將直徑為0.6mm的線狀銅合金導體通過直線大拉連續電加熱退火工藝技術,拉伸至直徑為0.1mm或0.2mm的線狀合金導體。
拉拔成Φ0.20~0.10mm銅合金單絲後各狀態的物理性能如表1所示。
表1Φ0.20~0.10mm單絲各狀態的物理性能
綜上所述,本發明設計合理,操作簡便,製得的銅合金導體具有優異的抗拉強度、延伸率以及導電率,滿足生產需求。
上述實施例只為說明本發明的技術構思及特點,其目的在於讓熟悉此項技術的人士能夠了解本發明的內容並加以實施,並不能以此限制本發明的保護範圍,凡根據本發明精神實質所作的等效變化或修飾,都應涵蓋在本發明的保護範圍內。