無內胎鋼圈旋壓輪幅結構的製作方法
2023-04-25 19:29:41 1
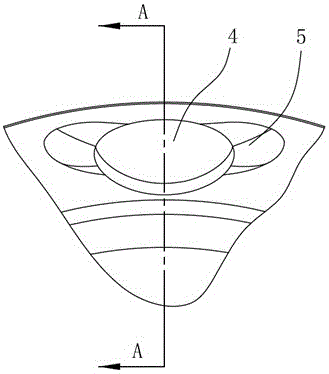
本實用新型涉及車輪部件,尤其是一種無內胎鋼圈旋壓輪幅結構。
背景技術:
輪輻是保護車輛車輪的輪圈、輻條的裝置。輪輻通常採用旋壓工藝成形,在輕量化產品需求的大環境下,需要將旋壓段減薄,以使成品的重量變輕,但是輪輻減薄後風孔位置容易產生開裂、變形等疲勞破壞。
技術實現要素:
本實用新型的目的在於提供一種無內胎鋼圈旋壓輪幅結構,以提高其疲勞壽命。為實現上述目的,本實用新型採用以下技術方案:
無內胎鋼圈旋壓輪幅結構,其為旋壓成形的圓形罩板,罩板中部為大於車輪轉動軸的中心孔,中心孔四周設有螺栓孔,罩板的邊緣為與輪圈相配合的環形輪板,環形輪板上設有若干風孔,所述的風孔上設置凸緣或沉臺,所述的凸緣或沉臺的數量小於或等於風孔的數量。
進一步地,所述的凸緣或沉臺通過壓型成形,壓型方向與輪幅的旋壓方向相反。
優選地,所述的風孔處每間隔一個風孔設置一個凸緣。
優選地,所述的風孔處每間隔一個風孔設置一個沉臺。
由於採用了上述的結構,本實用新型具有如下有益效果:本實用新型在產品風孔附近較薄弱處二次加工設置凸緣或沉臺,優化了整個輪輻的受力,避免過早開裂,變形等疲勞破壞產生,該結構可以提高20%左右的疲勞壽命,輕量化狀態下,可以滿足預期要求。
附圖說明
圖1是本實用新型實施例一的結構示意圖。
圖2為圖1風孔處的局部示意圖。
圖3為圖2的A-A剖面示意圖。
圖4為圖3的k處斷面示意圖。
圖5是本實用新型實施例二的結構示意圖。
圖6為圖5風孔處的局部示意圖。
圖7為圖6的B-B剖面示意圖。
圖8為圖7的s處斷面示意圖。
主要組件符號說明:
1: 中心孔,2:螺栓孔,3:環形輪板,4:風孔,5:凸緣,6:沉臺 。
具體實施方式
為了使本領域的技術人員更好地理解本實用新型的技術方案,下面結合附圖和具體實施例對本實用新型作進一步詳細的描述。
實施例一
如圖1所示,本實施例公開了一種無內胎鋼圈旋壓輪幅結構,其為旋壓成形的圓形罩板,罩板中部為大於車輪轉動軸的中心孔1,中心孔1四周設有螺栓孔2,罩板的邊緣為與輪圈相配合的環形輪板3,環形輪板3上設有若干風孔4,風孔4上設置有凸緣5,凸緣5數量不限於和風孔4數量相同,本實施例中每間隔一個風孔4設置一個凸緣5。如圖2、圖3所示,凸緣5通過壓型成形設置在風孔4上,壓型方向與輪幅的旋壓方向相反。如圖4所示,通過壓型工藝成型的凸緣5呈稜形,凸緣5的尺寸b>a。
實施例二
如圖5所示,本實施例公開了一種無內胎鋼圈旋壓輪幅結構,其為旋壓成形的圓形罩板,罩板中部為大於車輪轉動軸的中心孔1,中心孔1四周設有螺栓孔2,罩板的邊緣為與輪圈相配合的環形輪板3,環形輪板3上設有若干風孔4,風孔4上設置有沉臺6,沉臺6數量不限於和風孔4數量相同,本實施例中每間隔一個風孔4設置一個沉臺6。如圖6、圖7所示,沉臺6通過壓型成形設置在風孔4上,壓型方向與輪幅的旋壓方向相反。如圖8所示,通過壓型工藝成型的沉臺6的尺寸0≤c<0.5,|b|<0.5。
綜上,本實用新型通過在產品風口附近較薄弱處二次加工,通過成型工藝設置與旋壓方向相反的沉臺6或凸緣5,優化了整個輪幅的受力。使風孔4最易開裂位置局部加強,提高產品的疲勞壽命,適宜推廣應用。
以上所述,僅為本實用新型較佳的具體實施方式,但本實用新型的保護範圍並不局限於此,任何熟悉本技術領域的技術人員在本實用新型揭露的技術範圍內,可輕易想到的變化或替換,都應涵蓋在本實用新型的保護範圍之內。