一種豎爐生產直接還原鐵的系統及其方法與流程
2023-07-28 20:33:41 3
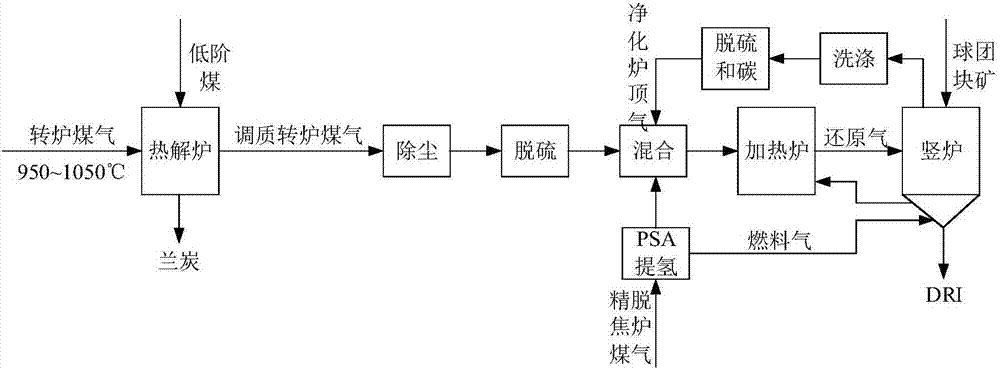
本發明總地涉及生產直接還原鐵領域,具體涉及一種豎爐生產直接還原鐵的系統及其方法。
背景技術:
目前,冶金工業中直接還原鐵的生產工藝主要有煤基法和氣基豎爐法兩種。通過氣基豎爐生產的直接還原鐵是代替廢鋼並優於廢鋼的煉鋼原料,是稀釋廢鋼中的錯雜元素、發展電爐煉鋼必不可少的純淨鐵原料。由於氣基豎爐生產技術汙染小、能耗低,被認為是鋼鐵工業發展中最有可能替代高爐的冶金技術。而我國「缺油、少氣、富煤」的資源結構,限制了國外通用的以天然氣為還原氣源的豎爐直接還原技術在國內的推廣應用。因此,開發推廣以煤制氣為氣源的氣基豎爐直接還原技術在國內具有廣闊的發展空間。
氣基豎爐直接還原技術對入爐的還原氣體成分的要求較為嚴格,例如,midrex工藝要求還原氣中(co+h2)>90%,h2/co≈1.6,而hylⅲ工藝要求還原氣中(co+h2)>90%,h2/co≈3.6。還原氣體為富氫氣體具有以下優勢:(1)在高於815℃的溫度下,氫氣還原速度是co的5-6倍;(2)co還原過程中,球團易產生膨脹、碎裂等現象,而用氫還原時這些現象幾乎不會出現;(3)在升降溫過程中,能夠有效地避免嚴重析碳的發生。
但是,現有的煤制氣技術產生的氣體中h2/co大部分都小於1.5。只有魯奇移動床加壓氣化技術產生的氣體中h2/co為1.6,但是有效氣體成分(co+h2)只有65%左右。為了滿足氣基豎爐直接還原工藝對還原氣組成成分的要求,煤制氣技術必須增加煤氣轉換裝置,通過水煤氣反應,增加還原氣體中h2的含量,而此方法將直接導致生產工序的增加和能耗的提高。
綜上所述,開發出一種能夠提高還原氣體中h2/co比值和有效氣體成分(co+h2)含量的技術,成為煤制氣—氣基豎爐直接還原技術工業化應用的關鍵所在。
轉爐煉鋼在吹煉期間產生大量煤氣,其溫度達1400-1600℃,煤氣中co含量達到60-85%,其發熱值達7mj/m3以上。由於煤氣溫度和co含量高,出爐口後遇到空氣就立即燃燒。近年來國內外對煤氣處理主要包括:(1)將煤氣隨意燃燒後經降溫、除塵後放散,其不足為汙染環境且浪費大量資源;(2)煤氣回收利用。煤氣回收利用存在的主要問題在於:轉爐煙氣中的物理顯熱在汽化冷卻的過程中全部被浪費,由於轉爐的煙氣量很大,因此,此種浪費是驚人的;同時氧和煤氣反應不充分時,存在剩餘的氧和剩餘的煤氣共存的情形,存在安全隱患。汽化冷卻不僅浪費了轉爐煙氣的大量顯熱,而且還要消耗大量的水,可回收的煤氣量少,即噸鋼回收煤氣只有70m3,單位發熱值只有5mj/m3左右。
技術實現要素:
本發明的目的在於提供一種豎爐生產直接還原鐵的系統及其方法。該系統及其方法充分利用轉爐煤氣熱解低階煤,獲取熱解氣,也能夠利用轉爐煤氣顯熱,節約能源。熱解氣經轉爐煤氣稀釋後,甲烷含量明顯降低,省卻煤制氣重整流程,節省設備投資,降低生產成本。
本發明提供了一種豎爐生產直接還原鐵的系統,其中,所述系統包括製備豎爐還原氣的子系統和氣基豎爐,所述製備豎爐還原氣的子系統包括轉爐、熱解爐、除塵器、脫硫塔、氣體混合器和加熱爐。所述轉爐包括轉爐煤氣出口;所述熱解爐包括第一氣體入口、低階煤入口和第二氣體出口;所述除塵器包括第二氣體入口和第三氣體出口,所述脫硫塔包括第三氣體入口和第四氣體出口;所述氣體混合器包括第四氣體入口、氫氣入口和還原氣出口;所述加熱爐包括所述還原氣入口、加熱爐燃料氣入口和熱還原氣出口;所述氣基豎爐包括熱還原氣入口、礦料入口和設置在豎爐頂部的豎爐爐頂氣出口。所述轉爐的轉爐煤氣出口連接所述熱解爐的第一氣體入口,所述熱解爐的第二氣體出口連接所述除塵器的第二氣體入口,所述除塵器的第三氣體出口連接所述脫硫塔的第三氣體入口,所述脫硫塔的第四氣體出口連接所述氣體混合器的第四氣體入口,所述氣體混合器的還原氣出口連接所述加熱爐的還原氣入口,所述加熱爐的熱還原氣出口連接所述氣基豎爐的熱還原氣入口。
優選地,根據上述的豎爐生產直接還原鐵的系統,其中,所述製備豎爐還原氣的子系統還包括提氫裝置,所述提氫裝置包括精脫焦爐煤氣入口、氫氣出口和第五氣體出口,所述氫氣出口連接所述氣體混合器的氫氣入口。
更優選地,根據上述的豎爐生產直接還原鐵的系統,其中,所述氣基豎爐還包括第五氣體入口和加熱後第五氣體出口,所述第五氣體入口連接所述提氫裝置的第五氣體出口,所述加熱後第五氣體出口與所述加熱爐燃料氣入口連接。
再優選地,根據上述的豎爐生產直接還原鐵的系統,其中,所述系統還包括豎爐爐頂氣淨化循環系統,其包括所述氣基豎爐的豎爐爐頂氣出口、設置在所述氣體混合器的豎爐爐頂氣入口、以及依次設置在所述豎爐爐頂氣出口和所述豎爐爐頂氣入口之間的洗滌塔和脫硫脫碳裝置。具體地,所述洗滌塔用於對氣基豎爐爐頂氣洗滌得到洗滌後尾氣;所述脫硫脫碳裝置用於脫除所述洗滌後尾氣中的co和硫得到淨化的爐頂氣;所述淨化的爐頂氣進入所述氣體混合器,成為所述還原氣的一部分。
本發明還提供了一種通過上述的豎爐生產直接還原鐵的系統生產直接還原鐵的方法,其中,所述方法包括:
(1)低階煤熱解:從第一氣體入口和低階煤入口,分別向熱解爐中通入轉爐煤氣和低階煤,使所述低階煤熱解,並得到調質轉爐煤氣,其中,所述轉爐煤氣的溫度為800~1100℃;
(2)除塵和脫硫:所述調質轉爐煤氣經由第二氣體入口通入除塵器中進行除塵處理,得到除塵後的調質轉爐煤氣,並從第三氣體出口排出,所述除塵後的調質轉爐煤氣經由第三氣體入口通入脫硫塔中進行脫硫處理,得到除塵脫硫後的調質轉爐煤氣,並從第四氣體出口排出;
(3)調氫:將所述除塵脫硫後的調質轉爐煤氣和氫氣分別經由第四氣體入口和氫氣入口通入氣體混合器進行混合,得到還原氣;
(4)加熱:使所述還原氣在加熱爐中被加熱至900-1000℃,得到熱還原氣;
(5)直接還原:使所述熱還原氣在氣基豎爐中與鐵礦料接觸,將所述鐵礦料還原,得到直接還原鐵,並將爐頂氣經豎爐爐頂氣出口排出。其中,步驟(1)中的轉爐煤氣的主要成分為co62~68%、co216~24%、n210~18%,低階煤可以為低階煤團或低階煤顆粒,所述低階煤球團的粒徑為4~12mm,所述低階煤顆粒的粒徑為3~8mm。
優選地,根據上述的生產直接還原鐵的方法,其中,步驟(3)中所述還原氣中h2/co的摩爾比為1.5-5.0。
優選地,根據上述的生產直接還原鐵的方法,其中,所述方法還包括焦爐煤氣氫氣分離步驟:在提氫裝置中,使焦爐煤氣經變壓吸附法分離,得到氫氣和第五氣體,所得到的氫氣通入所述氣體混合器中,用於步驟(3)中,與除塵脫硫後的調質轉爐煤氣混合。其中,氫氣的純度大於99體積%。其中,所述焦爐煤氣為經除塵、脫硫、脫碳處理後的焦爐煤氣。
優選地,根據上述的生產直接還原鐵的方法,步驟(2)中得到的所述調質轉爐煤氣中含有(co+h2)的體積百分比為65-80%、co210-20%,ch40.1-0.5%,n29-16%。
優選地,根據上述的生產直接還原鐵的方法,其中,所述方法還包括如下步驟:將所述提氫裝置得到的第五氣體送入所述氣基豎爐中,對所述直接還原鐵進行冷卻,得到加熱後的第五氣體,並將所述加熱後的第五氣體,用作步驟(4)中所述加熱爐的燃料氣。具體地,所述第五氣體從所述氣基豎爐冷卻段底部進入所述氣基豎爐後,與直接還原鐵充分接觸換熱後,再進入所述加熱爐作燃料氣。
優選地,根據上述的生產直接還原鐵的方法,其中,所述方法還包括豎爐爐頂氣循環步驟:採用豎爐爐頂氣循環系統,使從所述豎爐爐頂氣出口排出的爐頂氣,依次經洗滌塔洗滌以及脫硫脫碳裝置的脫硫脫碳處理後,得到淨化後的爐頂氣,使所述淨化後的爐頂氣用作還原氣,通入所述氣體混合器中,與步驟(3)得到的還原氣混合。
本發明的有益效果體現在如下幾方面:
(1)轉爐煤氣作為低階煤熱解的熱源,避免了轉爐煤氣顯熱損失,獲得熱解煤氣的同時降低了轉爐煤氣中的co2含量;節省了熱解爐加熱元件及熱源的投資,節能環保;
(2)將焦爐煤氣分離為高純氫氣和燃料氣,利用焦爐煤氣的同時,避免了焦爐煤氣中ch4對後續還原過程的不利影響,又有效利用了其中的氫氣來提高所需還原氣的h2/co,h2/co可在1.5-5.0之間調節。焦爐煤氣分離出的燃料氣先作氣基豎爐冷卻段的冷卻氣,吸熱後用作加熱爐的燃料氣,使直接還原鐵(dri)顯熱得到有效利用,節約能源;
(3)本發明提供的豎爐生產直接還原鐵的系統及其方法採用轉爐煉鋼、低階煤熱解與直接還原工藝設備進行耦合,既可經濟有效地利用轉爐煤氣,又可降低熱解設備、氣基直接還原設備投資,降低直接還原鐵生產成本。
附圖說明
圖1為一種豎爐生產直接還原鐵的系統結構圖;以及
圖2為一種合成豎爐還原氣生產直接還原鐵的工藝流程圖;
附圖標記說明:
11、熱解爐;12、除塵器;13、脫硫塔;14、氣體混合器;15、加熱爐;16、提氫裝置;21、氣基豎爐;31、爐頂氣出口;32、洗滌塔;33、脫碳塔;34、第二脫硫塔;35、爐頂氣入口。
具體實施方式
以下結合附圖和實施例,對本發明的具體實施方式進行更加詳細的說明,以便能夠更好地理解本發明的方案以及其各個方面的優點。然而,以下描述的具體實施方式和實施例僅是說明的目的,而不是對本發明的限制。
如圖1所示,本發明提供了一種豎爐生產直接還原鐵的系統,其中,所述系統包括製備豎爐還原氣的子系統和氣基豎爐21,所述製備豎爐還原氣的子系統包括轉爐、熱解爐11、除塵器12、脫硫塔13、氣體混合器14和加熱爐15。所述轉爐包括轉爐煤氣出口;所述熱解爐11包括第一氣體入口、低階煤入口和第二氣體出口;所述除塵器12包括第二氣體入口和第三氣體出口,所述脫硫塔13包括第三氣體入口和第四氣體出口;所述氣體混合器14包括第四氣體入口、氫氣入口和還原氣出口;所述加熱爐15包括所述還原氣入口和熱還原氣出口;所述氣基豎爐21包括熱還原氣入口、礦料入口和設置在豎爐頂部的豎爐爐頂氣出口。所述轉爐的轉爐煤氣出口連接所述熱解爐的第一氣體入口,所述熱解爐11的第二氣體出口連接所述除塵器12的第二氣體入口,所述除塵器12的第三氣體出口連接所述脫硫塔13的第三氣體入口,所述脫硫塔13的除塵脫硫調質轉爐煤氣出口連接所述氣體混合器14的第四氣體入口,所述氣體混合器14的還原氣出口連接所述加熱爐15的還原氣入口,所述加熱爐15的熱還原氣出口連接所述氣基豎爐21的熱還原氣入口。
在一種實施方案中,所述熱解爐11的第一氣體入口設置在所述熱解爐11的底部,低階煤入口設置在所述熱解爐11的頂部或側壁的上部,這樣,使得轉爐煤氣從所述熱解爐11的底部通入,所述熱解爐11內上升的轉爐煤氣與下行的低階煤球團或顆粒進行充分換熱,將低階煤球團或顆粒加熱到700-1000℃,優選的是800-950℃,促使低階煤發生熱解反應。所述熱解爐11的第二氣體出口設置在所述熱解爐11的中上部,使得調質轉爐煤氣從所述熱解爐11的中上部經煤氣管道排出。所述熱解爐11還具有固體產物出口,用於排出熱解的固體產物例如蘭炭。該熱解爐是用於對轉爐煤氣進行初步淨化,同時利用轉爐煤氣顯熱熱解低階煤產生熱解氣,達到調質轉爐煤氣的目的,並促使轉爐煤氣中的co2發生布多爾反應,進一步降低co2含量。在一種實施方案中,所述製備豎爐還原氣的子系統還包括提氫裝置16,所述提氫裝置16包括精脫焦爐煤氣入口、氫氣出口和第五氣體出口,所述氫氣出口連接所述氣體混合器14的氫氣入口。提氫裝置16為psa變壓吸附提氫裝置,其用於對精脫焦爐煤氣分離氫氣和燃料氣。
在一種實施方案中,氣體混合器14用於將淨化後的調質轉爐煤氣、氫氣和淨化後的爐頂氣混合,所得混合氣作為冷還原氣進入所述加熱爐15加熱。
所述加熱爐15用於將還原氣加熱至900-1000℃,為豎爐還原反應提供熱源。
在一種實施方案中,所述氣基豎爐21還包括第五氣體入口和加熱後第五氣體出口,所述第五氣體入口用於接收所述提氫裝置分離得到的第五氣體,所述加熱後第五氣體出口用於向所述氣體混合器傳輸加熱後的第五氣體。所述氣基豎爐21還包括還原鐵出口,該氣基豎爐21是用於利用還原氣及球團礦生產直接還原鐵,並產生爐頂氣。氣基豎爐21還包括第五氣體入口設置在所述氣基豎爐21冷卻段底部。
在一種實施方案中,所述系統還包括爐頂氣淨化循環系統,其包括設置在所述氣基豎爐頂部的爐頂氣出口31、設置在所述氣體混合器的爐頂氣入口35、以及依次設置在所述爐頂氣出口和所述爐頂氣入口之間的洗滌塔32、脫碳塔33和第二脫硫塔34,用於淨化所述氣基豎爐的爐頂氣。具體地,所述洗滌塔32用於對氣基豎爐爐頂氣洗滌得到洗滌後尾氣;所述脫碳塔33用於脫除所述洗滌後尾氣中的co2,得到脫碳尾氣;所述第二脫硫塔34主要用於脫除所述脫碳後尾氣中的硫得到脫硫尾氣;所述脫硫尾氣可以用作所述氣基豎爐21的還原氣,進入所述氣體混合器14,與第一脫硫塔13輸出的還原氣混合,一起送入氣基豎爐21。
如圖2所示,本發明還提供了一種通過上述的豎爐生產直接還原鐵的系統生產直接還原鐵的方法,其中,所述方法包括:
(1)低階煤熱解:從第一氣體入口和低階煤入口,分別向熱解爐中通入轉爐煤氣和低階煤,使所述低階煤熱解,得到調質轉爐煤氣,其從第二氣體出口排出,其中,所述轉爐煤氣的溫度為800-1100℃。
具體地,未經處理的轉爐煤氣經降溫裝置降溫至800-1100℃,優選為850-1050℃,直接從熱解爐的底部通入,熱解爐內上升的轉爐煤氣與下行的低階煤球團或低階煤顆粒進行充分換熱,將低階煤球團或低階煤顆粒加熱到700-1000℃,優選為800-950℃,促使低階煤發生熱解反應。同時轉爐煤氣中的co2部分發生布多爾反應(co2+c—2co),轉化為co。最終,轉爐煤氣與生成的熱解氣形成調質轉爐煤氣,並從熱解爐的中上部經煤氣管道排出。其中,轉爐煤氣的主要成分為co62-68%,co216-24%,n210-18%,低階煤可以為低階煤球團和/或低階煤顆粒,低階煤球團的粒徑為4-12mm,低階煤顆粒的粒徑為3-8mm。轉爐煤氣作為低階煤熱解的熱源,避免了轉爐煤氣顯熱損失,獲得熱解煤氣的同時降低了轉爐煤氣中的co2含量。
(2)除塵和脫硫:所述調質轉爐煤氣經由第二氣體入口通入除塵器中進行除塵處理,得到除塵後的調質轉爐煤氣,並從第三氣體出口排出,所述除塵後的調質轉爐煤氣經由第三氣體入口通入脫硫塔中進行脫硫處理,得到除塵脫硫後的調質轉爐煤氣,並從第四氣體出口排出。具體地,所述除塵器為旋風除塵器,除塵脫硫後的調質轉爐煤氣的含硫量在15ppm以下。
(3)調氫:將所述除塵脫硫後的調質轉爐煤氣和氫氣分別經由第四氣體入口和氫氣入口通入氣體混合器進行混合,得到還原氣。
(5)加熱:使所述還原氣在加熱爐中被加熱至900-1000℃,得到熱還原氣。
(6)直接還原:使所述熱還原氣在氣基豎爐中與鐵礦料接觸,將所述鐵礦料還原,得到直接還原鐵,並將爐頂氣經豎爐爐頂氣出口排出。
在一種實施方案中,其中,步驟(3)中所述還原氣中h2/co的摩爾比為1.5-5.0。
在一種實施方案中,其中,所述方法還包括焦爐煤氣氫氣分離步驟:在提氫裝置中,使焦爐煤氣經變壓吸附法分離,得到氫氣和第五氣體,所得到的氫氣通入所述氣體混合器中,用於步驟(3)中,與除塵脫硫後的調質轉爐煤氣混合。其中,氫氣的純度大於99體積%。將焦爐煤氣分離為高純氫氣和第五氣體(燃料氣),利用焦爐煤氣的同時,避免了焦爐煤氣中ch4對後續還原過程的不利影響,又有效利用了其中的氫氣來提高所需還原氣的h2/co。其中,所述焦爐煤氣為經除塵、脫硫、脫碳處理後的焦爐煤氣。
在一種實施方案中,其中,調質轉爐煤氣的(co+h2)為65-80%,優選為70-75%,而調質轉爐煤氣中co210-20%,ch40.1-0.5%,n29-16%。
在一種實施方案中,其中,所述方法還包括如下步驟:將所述提氫裝置得到的第五氣體送入所述氣基豎爐中,對所述直接還原鐵進行冷卻,得到加熱後的第五氣體,並將所述加熱後的第五氣體,用作步驟(4)中所述加熱爐的燃料氣。具體地,所述第五氣體從所述氣基豎爐冷卻段底部進入所述氣基豎爐後,與直接還原鐵充分接觸換熱後,再進入所述加熱爐作燃料氣。焦爐煤氣分離出的燃料氣先作氣基豎爐冷卻段的冷卻氣,吸熱後用作加熱爐的燃料氣,使直接還原鐵(dri)顯熱得到有效利用,節約能源。
在一種實施方案中,其中,步所述方法還包括豎爐爐頂氣循環步驟:採用豎爐爐頂氣循環系統,使從所述豎爐爐頂氣出口排出的爐頂氣,依次經洗滌塔洗滌以及脫硫脫碳裝置的脫硫脫碳處理後,得到淨化後的爐頂氣,使所述淨化後的爐頂氣用作還原氣,通入所述氣體混合器中,與步驟(3)得到的還原氣混合。
實施例1
本實施例1利用圖1所示系統並採用圖2所示的一種合成豎爐還原氣生產直接還原鐵的工藝流程實施,具體如下:
轉爐煤氣25000nm3/h,入熱解爐溫度1050℃,其中含co約65%、co2約20%、n2約15%。轉爐煤氣從熱解爐的底部通入,熱解爐內上升的轉爐煤氣與下行的低階煤球團或顆粒進行充分換熱,將低階煤球團或顆粒加熱到950℃,促使低階煤發生熱解反應,轉爐煤氣與生成的熱解氣形成調質轉爐煤氣,並從熱解爐的中上部經煤氣管道排出。其中,低階煤球團的粒徑為4-12mm,低階煤熱解量為1t/h,所得調質轉爐煤氣26060nm3/h,主要成分為h2約0.81%,co約67.27%,co2約17.15%,n2約14.42%,ch4約0.24%。
調質轉爐煤氣經旋風除塵器除塵、脫硫處理後,加入氫氣27712nm3/h,混合加熱成為熱還原氣。熱還原氣的流量為53772nm3/h,溫度為1000℃,主要成分為h2約51.93%,co約32.60%,co2約8.31%,n2約6.99%,ch4約0.09%,其中(co+h2)≈84.53%,h2/co≈1.6。
所述氫氣為焦爐煤氣經除塵、脫硫、脫碳處理後,由psa降壓吸附法分離得到,其中氫氣的純度大於99體積%。
使用該熱還原氣53772nm3/h,進入豎爐還原段參與還原反應,可生產直接還原鐵28.3t/h,產生豎爐爐頂氣約53770nm3/h,其中co2含量較高,約19.82%,可經脫硫脫碳後循環使用。爐頂氣經除塵脫硫淨化後約39029nm3/h,是一氧化碳和氫氣為主的合成氣。淨化爐頂氣含水和二氧化碳很低,作為還原氣與調質轉爐煤氣和氫氣混合,加熱後作為還原氣一部分進氣基豎爐用於生產直接還原鐵。
精脫焦爐煤氣由psa降壓吸附法分離出的解析氣作為燃料氣從豎爐冷卻段底部進入豎爐與直接還原鐵充分接觸換熱後,進入加熱爐作燃料。
實施例2
本實施例2利用圖1所示系統並採用圖2所示的一種合成豎爐還原氣生產直接還原鐵的工藝流程實施,具體如下:
轉爐煤氣30000nm3/h,入熱解爐溫度950℃,其中含co約75%、co2約15%、n2約10%。轉爐煤氣從熱解爐的底部通入,熱解爐內上升的轉爐煤氣與下行的低階煤球團或顆粒進行充分換熱,將低階煤球團或顆粒加熱到900℃,促使低階煤發生熱解反應,轉爐煤氣與生成的熱解氣形成調質轉爐煤氣,並從熱解爐的中上部經煤氣管道排出。其中,低階煤球團的粒徑為4-12mm,低階煤熱解量為1t/h,所得調質轉爐煤氣31060nm3/h,成分為h2約0.68%,co約76.57%,co2約12.78%,n2約9.68%,ch4約0.20%。
調質轉爐煤氣經旋風除塵器除塵、脫硫處理後,加入氫氣37712nm3/h,混合加熱成為熱還原氣。熱還原氣的流量為68772nm3/h,溫度為900℃,主要成分為h2約55.14%,co約34.58%,co2約5.77%,n2約4.37%,ch4約0.09%,其中(co+h2)≈89.72%,h2/co≈1.6。
所述氫氣為焦爐煤氣經除塵、脫硫、脫碳處理後,由psa降壓吸附法分離得到,其中氫氣的純度大於99.6體積%。
使用該熱還原氣68772nm3/h,進入豎爐還原段參與還原反應,可生產直接還原鐵36.2t/h,產生豎爐爐頂氣約68770nm3/h,其中co2含量較高,約17.98%,可經脫硫脫碳後循環使用。爐頂氣經除塵脫硫淨化後約50648nm3/h,一氧化碳和氫氣為主的合成氣。淨化爐頂氣含水和二氧化碳很低,作為還原氣與調質轉爐煤氣和氫氣混合,加熱後作為還原氣一部分進氣基豎爐用於生產直接還原鐵。
精脫焦爐煤氣由psa降壓吸附法分離出的解析氣作為燃料氣從豎爐冷卻段底部進入豎爐與直接還原鐵充分接觸換熱後,進入加熱爐作燃料。
最後應說明的是:顯然,上述實施例僅僅是為清楚地說明本發明所作的舉例,而並非對實施方式的限定。對於所屬領域的普通技術人員來說,在上述說明的基礎上還可以做出其它不同形式的變化或變動。這裡無需也無法對所有的實施方式予以窮舉。而由此所引申出的顯而易見的變化或變動仍處於本發明的保護範圍之中。