一種筒式進排氣裝置及內燃機缸蓋的製作方法
2023-07-20 22:42:06 1
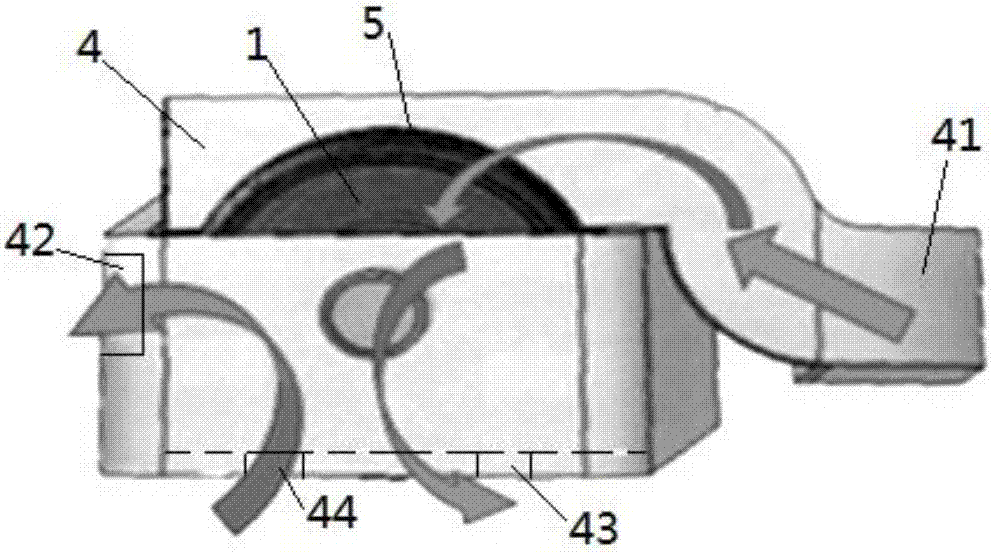
本發明屬於機械設備技術領域,尤其涉及一種筒式進排氣裝置及內燃機缸蓋。
背景技術:
內燃機包括缸蓋和缸體,缸蓋、缸體和活塞形成密閉的氣缸,活塞可在缸體內往復運動,活塞帶動曲軸旋轉,為外部設備提供動力。內燃機的工作過程包括進氣、壓縮、做功和排氣四個行程。
進氣行程時,活塞在上止點,進氣門開啟,排氣門關閉,氣體經進氣門進入氣缸。壓縮行程時氣缸內氣體受到壓縮,壓力增高,溫度上升。做功行程時,在壓縮上止點前噴油或點火使混合氣燃燒產生高溫、高壓推動活塞下行並做功。排氣行程時活塞推擠氣缸內廢氣經排氣門排出。
實際上,進氣門在上止點前即開啟,以保證活塞下行時進氣門有較大的開度。這樣可在進氣過程開始時減小流動阻力減少吸氣所消耗的功同時也可充入較多的新鮮充量。當活塞在進氣行程中運行到下止點時由於氣流慣性新鮮充量仍可繼續充入氣缸,故使進氣門在下止點後延遲關閉。排氣門也在下止點前提前開啟,即在膨脹做功行程後部分即開始排氣。這是為了利用氣缸內較高的燃氣壓力,使廢氣自動流出氣缸從而使活塞從下止點向上止點運動時氣缸內氣體壓力低些,以減少活塞將廢氣排擠出氣缸所消耗的功,但這樣也減少了做功的行程。
目前,內燃機的配氣系統包括安裝在缸蓋上的進氣門、排氣門、彈簧和凸輪軸等部件。進氣門和排氣門由彈簧支撐,凸輪軸的旋轉控制進氣門和排氣門的開閉。凸輪軸的旋轉由內燃機的曲軸帶動,凸輪軸的旋轉軸為實心,帶動凸輪旋轉時,由於其結構複雜、質量大、摩擦阻力等因素,使得其消耗的能量很大。由於氣門不斷的開閉,對彈簧的性能也有很高的要求。
技術實現要素:
為了解決上述問題,本發明期望提出一種筒式進排氣裝置及內燃機缸蓋,捨棄凸輪軸、彈簧等進排氣元件,利用外筒和內筒的配合,實現內燃機進排氣的控制,減輕進排氣裝置的重量,提高內燃機的效率和性能。
本發明首先提供一種筒式進排氣裝置,包括外筒、內筒和驅動軸;
所述外筒為一端開口的筒狀,所述外筒上設有外筒進氣孔組和外筒排氣孔組;
所述內筒為筒狀,可旋轉的安裝在所述外筒的空腔內,所述內筒上設有內筒進氣孔組和內筒排氣孔組;
所述內筒進氣孔組的掃掠面與所述外筒進氣孔組有重疊,所述內筒排氣孔組的掃掠面與所述外筒排氣孔組有重疊;
所述驅動軸連接所述內筒,驅動所述內筒旋轉。
其次,本發明提供一種內燃機缸蓋,用於內燃機的進排氣,包括蓋體和筒式進排氣裝置;
所述蓋體上設有空腔,還設有與所述蓋體的空腔連通的進氣孔和排氣孔,底部設有與所述蓋體的空腔連通的進缸氣孔和出缸氣孔;
所述筒式進排氣裝置為上述的筒式進排氣裝置,所述外筒可旋轉的安裝在所述蓋體的空腔內;
所述外筒進氣孔組與所述蓋體的進氣孔連通,所述外筒進氣孔組的掃掠面與所述進缸氣孔重合;所述出缸氣孔與所述外筒排氣孔組的掃掠面重合,所述外筒排氣孔組與所述蓋體的排氣孔連通。
本發明中,「掃掠面」是指氣孔旋轉時是掃過的環形面。「有重疊」是指可以完全重疊,也可以部分重疊,如所述內筒進氣孔組的掃掠面與所述外筒進氣孔組有重疊,意思為當內筒進氣孔組旋轉到外筒進氣孔組所在的角度時,內筒進氣孔組與外筒進氣孔組連通,但二者可以僅部分面積重合,使得進氣面積截面可調。所述外筒進氣孔組的掃掠面與所述進缸氣孔重合,是指當外筒進氣孔組位於所述進缸氣孔的角度時,二者可完全連通,當外筒進氣孔旋轉一定預定角度後,進缸氣孔被外筒關閉。
作為本發明優選的方案,所述外筒進氣孔組包括外筒進氣流入孔和外筒進氣流出孔,所述外筒排氣孔組包括外筒排氣流入孔和外筒排氣流出孔,所述內筒進氣孔組包括內筒進氣流入孔和內筒進氣流出孔,所述內筒排氣孔組包括內筒排氣流入孔和內筒排氣流出孔;
所述外筒進氣流入孔與所述蓋體的進氣孔連通,所述內筒進氣流入孔的掃掠面與所述外筒進氣流入孔有重疊,所述內筒進氣流出孔的掃掠面與所述外筒進氣流出孔有重疊,所述外筒進氣流出孔的掃掠面與所述進缸氣孔重合;
所述外筒排氣流入孔的掃掠面與所述出缸氣孔重合,所述內筒排氣流入孔的掃掠面與所述外筒排氣流入孔有重疊,所述內筒排氣流出孔的掃掠面與所述外筒排氣流出孔有重疊,所述外筒排氣流出孔與所述缸蓋的排氣孔連通。
對於多缸的內燃機,所述外筒上設有多組外筒進氣孔組和外筒排氣孔組,所述內筒上設有多組內筒進氣孔組和內筒排氣孔組。每個內燃機的氣缸均配置相應的外筒進氣孔組、外筒排氣孔組、內筒進氣孔組、內筒排氣孔組,使得各個氣缸之間的進排氣可分開工作,不受其他氣缸的影響。
進一步的,所述內筒的一端開口,所述內筒的開口端的內壁上設有內齒輪;所述驅動軸的一端設有外齒輪,所述內筒的內齒輪與所述驅動軸的外齒輪嚙合,驅動軸可帶動內筒旋轉,以配合各個氣缸的進排氣需求。內筒與驅動軸之間也可以採用其他連結方式,如鍵連接,齒輪連接可以使內筒的受力更均勻。
更進一步的,所述內筒的開口端設有油腔隔盤,所述油腔隔盤與所述內筒的內壁及所述驅動軸形成密閉的油腔,所述驅動軸上設有與所述油腔連通的液壓油孔;在所述內筒的封閉端與所述外筒的封閉端之間設有波形彈簧。波形彈簧和液壓油的配合使得內筒可沿軸線移動,向油腔內注油時,液壓油推動內筒向封閉端移動,壓縮波形彈簧;當油腔排油時,內筒在波形彈簧的推動下向開口端移動。內筒在外筒內軸向移動,可改變外筒上孔組與內筒上孔組的重疊面積,從而改變氣缸的進排氣截面積,調整氣缸的進排氣量。
作為本發明優選的方案,所述外筒的封閉端的外側設有驅動齒輪或其他相應的驅動機構,所述驅動齒輪帶動所述外筒旋轉。通過旋轉所述外筒,從而調整進排氣的相位和時間。
對於較大型的內燃機,蓋體可分開製作,所述蓋體包括上蓋和下蓋,所述上蓋設有半圓形槽,所述下蓋設有半圓形槽,所述上蓋和下蓋固定連接,所述上蓋的半圓形槽與所述下蓋的半圓形槽構成所述蓋體的空腔。
進一步的,所述蓋體上的進缸氣孔與出缸氣孔對角布置。進缸氣孔與出缸氣孔對角布置,可使得缸內更容易形成渦流和滾流。
對於較大型的內燃機,進氣部分和排氣部分可分開設置,其方案為:
所述蓋體的空腔包括進氣空腔和排氣空腔,所述進氣孔和進缸氣孔與所述進氣空腔連通,所述出缸氣孔和排氣孔與所述排氣空腔連通;
所述外筒包括進氣外筒和排氣外筒;所述進氣外筒安裝在所述進氣空腔內,所述進氣外筒上設有所述外筒進氣孔組;所述排氣外筒安裝在所述排氣空腔內,所述排氣外筒上設有所述外筒排氣孔組;
所述內筒包括進氣內筒和排氣內筒;所述進氣內筒安裝在所述進氣外筒的空腔內,所述進氣內筒上設有所述內筒進氣孔組;所述排氣內筒安裝在所述排氣外筒的空腔內,所述排氣內筒上設有所述內筒排氣孔組;
所述驅動軸包括進氣驅動軸和排氣驅動軸,所述進氣驅動軸與所述進氣內筒連接,所述排氣驅動軸與所述排氣內筒連接。
對於多缸的內燃機,所述進氣內筒內設有進氣隔離板件,所述進氣隔離板件位於相鄰的所述內筒進氣孔組之間;所述排氣內筒內設有排氣隔離板件,所述排氣隔離板件位於相鄰的所述內筒排氣孔組之間。進氣隔離板件和排氣隔離板件用於分隔各個氣缸進排氣,避免相互幹擾。
優選的,所述進氣隔離板件延伸出側壁,其側壁上設有渦片,所述進氣隔離板件的側壁上設有與所述內筒進氣孔組配合的開口。
本發明提供的筒式進排氣裝置及內燃機缸蓋,利用外筒及內筒各個氣孔組的配合,替代了傳統的氣門,極大的簡化了內燃機進排氣裝置的結構,減輕了其重量,降低其消耗的能量;利用液壓控制,改變進氣截面積,實現氣缸進排氣量的控制;通過旋轉外筒,控制進排氣提前角,改變進排的相位,從而提高內燃機的效率。
附圖說明
圖1是本發明實施例的筒式進排氣裝置結構示意圖。
圖2是本發明實施例的一種內燃機缸蓋的結構圖。
圖3是本發明實施例的內燃機缸蓋應用於多缸內燃機的示意圖。
圖4是本發明實施例的內筒旋轉及軸向移動的結構圖。
圖5是本發明實施例的驅動軸的爆炸圖。
圖6是本發明實施例的液壓油孔的示意圖。
圖7是本發明實施例的進排氣截面積改變的示意圖。
圖8是本發明實施例的分離式蓋體的結構圖。
圖9是本發明實施例的另一種筒式進排氣裝置結構示意圖。
圖10是本發明實施例的進氣外筒的示意圖。
圖11是本發明實施例的驅動齒輪示意圖。
圖12是本發明實施例的外筒旋轉的示意圖。
圖13是本發明實施例的進缸氣孔和出缸氣孔布置圖。
圖14是本發明實施例的隔離板件示意圖。
圖15是本發明實施例的帶渦片的隔離板件。
具體實施方式
以下結合附圖和實施例,對本發明的具體實施方式進行更加詳細的說明,以便能夠更好地理解本發明的方案及其各個方面的優點。然而,以下描述的具體實施方式和實施例僅是說明的目的,而不是對本發明的限制。
本發明中所述的「連接」,除非另有明確的規定或限定,應作廣義理解,可以是直接相連,也可以是通過中間媒介相連。
本發明通過筒式進排氣裝置和蓋體的配合,實現內燃機進排氣的控制。其中,進排氣孔可設置在同一組外筒和內筒上;也可根據實際需求,將進氣部分和排氣部分分離,進氣孔組和排氣孔組分別設置在不同的外筒和內筒上。
實施例1
如圖1所示,本實施例提供一種筒式進排氣裝置,包括外筒1、內筒2和驅動軸3。外筒1為一端開口的筒狀,外筒1上設有外筒進氣孔組11和外筒排氣孔組12。內筒2為筒狀,可旋轉的安裝在外筒1的空腔內,內筒2可由外筒1的開口端裝入外筒1,內筒2上設有內筒進氣孔組21和內筒排氣孔組22。驅動軸3連接內筒3,驅動內筒3旋轉。此種結構可顯著減少整個內燃機的尺寸和重量。
內筒進氣孔組21的掃掠面與外筒進氣孔組11有重疊,內筒排氣孔組22的掃掠面與外筒排氣孔組12有重疊。當內筒進氣孔組21旋轉至外筒進氣孔組11所在的角度時,外筒進氣孔組11與內筒進氣孔組21連通。當內筒排氣孔組22旋轉至外筒排氣孔組12所在的角度時,外筒排氣孔組12與內筒排氣孔組22連通。
更具體的,外筒進氣孔組11包括外筒進氣流入孔111和外筒進氣流出孔112,外筒排氣孔組12包括外筒排氣流入孔121和外筒排氣流出孔122,內筒進氣孔組21包括內筒進氣流入孔211和內筒進氣流出孔212,內筒排氣孔組22包括內筒排氣流入孔221和內筒排氣流出孔222。
內筒進氣流入孔211的掃掠面與外筒進氣流入孔111有重疊,內筒進氣流出孔212的掃掠面與外筒進氣流出孔112有重疊,內筒排氣流入孔221的掃掠面與外筒排氣流入孔121有重疊,內筒排氣流出孔222的掃掠面與外筒排氣流出孔122有重疊。
如圖2所示,安裝有上述筒式進排氣裝置的內燃機缸蓋。蓋體4可以是整體式的,也可以是分體式的。蓋體4上設有空腔5,蓋體4的側壁上設有與蓋體的空腔5連通的進氣孔41和排氣孔42,蓋體的底部設有與蓋體的空腔5連通的進缸氣孔43和出缸氣孔44。進氣孔41和排氣孔42與外部連通,用於氣體的進入和排出內燃機。進缸氣孔43和出缸氣孔44為缸蓋與氣缸內腔的連通孔。需要說明的是,進氣孔41和排氣孔42也可以設置在蓋體4的頂部,其具體位置,根據實際需求確定。
筒式進排氣裝置的外筒1可旋轉的安裝在蓋體的空腔5內。外筒進氣孔組11與蓋體的進氣孔41連通,外筒進氣孔組11的掃掠面與進缸氣孔43重合;出缸氣孔44與外筒排氣孔組22的掃掠面重合,外筒排氣孔組22與蓋體的排氣孔42連通。
具體的,外筒進氣流入孔111與蓋體的進氣孔41連通,外筒進氣流出孔112的掃掠面與進缸氣孔43重合;外筒排氣流入孔121的掃掠面與出缸氣孔44重合,外筒排氣流出孔122與缸蓋的排氣孔42連通。
在外筒進氣流入孔111所在的外筒圓周上設置多個平行排列的外筒進氣流入孔111,使得無論外筒旋轉至哪個角度外筒進氣流入孔111均與蓋體的進氣孔41連通。在外筒排氣流出孔122所在的外筒圓周上設置多個平行排列的外筒排氣流出孔122,使得無論外筒旋轉至哪個角度,外筒排氣流出孔122均與缸蓋的排氣孔42連通。
當內燃機需要進氣時,內筒進氣孔組21旋轉至外筒進氣孔組11所在的角度,外筒進氣孔組11與內筒進氣孔組21連通。外部氣體依次通過蓋體的進氣孔41、外筒進氣流入孔111、內筒進氣流入孔211進入內筒的內腔。然後氣體依次通過內筒進氣流出孔212、外筒進氣流出孔112、進缸氣孔43由內筒2的內腔進入氣缸。當內燃機不需要進氣時,內筒進氣孔組21旋轉過外筒進氣孔組11所在的角度即可。
當內燃機需要排氣時,內筒排氣孔組22旋轉至外筒排氣孔組12所在的角度,外筒排氣孔組12與內筒排氣孔組22連通。缸內的氣體依次通過出缸氣孔44、外筒排氣流入孔121、內筒排氣流入孔221進入內筒2的內腔。然後氣體依次通過內筒排氣流出孔222、外筒排氣流出孔122、蓋體的排氣孔42排出內燃機。當內燃機不需要排氣時,使內筒排氣孔組22旋轉過外筒排氣孔組12所在的角度即可。
如圖3所示,對於多缸的內燃機,外筒上設有多組外筒進氣孔組和外筒排氣孔組,內筒上設有多組內筒進氣孔組和內筒排氣孔組。以四缸內燃機為例,第一缸c1、第二缸c2、第三缸c3、第四缸c4均設有相應的進排氣孔,滿足各個氣缸單獨工作的需要。多缸的內燃機,需各個氣缸依照設定的順序依次工作,即不同的氣缸進排氣開啟的時間點不同,各個氣缸對應的內筒氣孔可設置在內筒壁的圓周的不同角度上,如依照氣缸的點火順序,對應的進排氣孔組相差90°,滿足內燃機工作的需求。
如圖4和圖5所示,一種內筒2與驅動軸3的連接方式為:內筒2的一端開口,內筒的開口端的內壁上設有內齒輪23;驅動軸3的一端設有外齒輪31,內筒的內齒輪23與驅動軸的外齒輪31嚙合,使得驅動軸3可帶動內筒2旋轉,以配合氣缸的進排氣需求。圖5為驅動軸的爆炸圖,外齒輪31通過鍵與驅動軸的轉軸連接。
在圖4中,內筒的開口端設有油腔隔盤24,油腔隔盤24與內筒2的內壁及驅動軸3形成密閉的油腔7。如圖5和圖6所示,驅動軸上設有與油腔7連通的液壓油孔32。在內筒的封閉端與外筒的封閉端之間設有波形彈簧6。波形彈簧6和油腔7中的液壓油配合,使得內筒2可沿軸線在外筒1內移動。油腔7的進油量及排油量由於液壓油孔32連接的液壓閥控制,內燃機電子控制單元(ecu)根據內燃機運行方式及各傳感器的信號調節液壓閥的開啟和關閉。為了加強油腔7的密封,在驅動軸3對應油腔的外徑上,可設置密封槽,用於安裝o型密封圈。
當向油腔7內注油時,液壓油的壓力大于波形彈簧6的彈力,內筒2向封閉端移動;當油腔7排油時,液壓油的壓力小于波形彈簧6的彈力,內筒2向開口端移動。內筒2在外筒1內軸向移動,可改變外筒上孔組與內筒上孔組的重疊面積,從而改變氣缸的進排氣截面積,調整氣缸的進排氣量。如圖7所示,外筒1與內筒2之間的陰影部分為外筒上孔組與內筒上孔組連通的面積,即是氣缸的進排氣截面積,由圖7a到圖7b,當內筒2軸向移動時,氣缸的進排氣截面積改變。一般來說,當內燃機高速工作時,進排氣量需增大,此時增大進排氣截面積即可。外筒進氣流出孔112的寬度應大於或等於內筒進氣流出孔212的寬度,以便調節進氣截面。
另一種實施方案為,內筒固定,外筒相對內筒軸向移動,來改變進排氣截面積。
附圖中,向下的箭頭代表氣缸的進氣流,向上的箭頭代表氣缸的排氣流。
實施例2
對於較大型的內燃機,如柴油機,為了便於製造和安裝,如圖8所示,可將蓋體4可分開製作,將蓋體分為上蓋45和下蓋46,組裝時,上蓋45和下蓋46通過螺栓固定連接。內燃機的進氣部分和排氣部分也可分開設置,在上蓋45上設有進氣的半圓形槽511和排氣的半圓形槽521,在下蓋46上設有進氣的半圓形槽512和排氣的半圓形槽522。上蓋45和下蓋46組合後,半圓形槽511和半圓形槽512即形成進氣空腔51,半圓形槽512和半圓形槽522即形成排氣空腔52。進氣孔41和進缸氣孔(未示出)與進氣空腔51連通,出缸氣孔(未示出)和排氣孔42與排氣空腔52連通。
由於內燃機的進氣部分和排氣部分分離,外筒1和內筒2的進排氣功能也要進行分離。如圖9所示,外筒包括進氣外筒13和排氣外筒14,內筒包括進氣內筒25和排氣內筒26,驅動軸包括進氣驅動軸33和排氣驅動軸34。進氣外筒13、進氣內筒25和進氣驅動軸33構成進氣部分,進氣外筒13安裝在進氣空腔51內,進氣內筒25安裝在進氣外筒13的空腔內,進氣驅動軸33與進氣內筒25連接。排氣外筒14、排氣內筒26和排氣驅動軸34構成排氣部分,排氣外筒14安裝在排氣空腔52內,排氣內筒26安裝在排氣外筒14的空腔內,排氣驅動軸34與排氣內筒26連接。
進氣外筒13上設有外筒進氣孔組11,排氣外筒14上設有外筒排氣孔組12,進氣內筒25上設有內筒進氣孔組21,排氣內筒26上設有內筒排氣孔組22。如圖10所示,以進氣外筒13為例,進氣外筒13上設置外筒進氣流入孔111和外筒進氣流出孔112。為了便於進氣,外筒進氣流入孔111設置多個,外筒進氣流出孔112的截面積大於外筒進氣流入孔111的截面積。排氣外筒14、進氣內筒25和排氣內筒26上氣孔的設置與進氣外筒13類似。
本實施例依然是將外筒進氣孔組11和外筒排氣孔組12設置在外筒1上,由於外筒1包括進氣外筒13和排氣外筒14,故將外筒進氣孔組11設在進氣外筒13上,外筒排氣孔組12設在排氣外筒14上。同理,內筒進氣孔組21和內筒排氣孔組22依然設在內筒2上。
外筒進氣孔組11與蓋體的進氣孔41連通,外筒進氣孔組11的掃掠面與進缸氣孔43重合;出缸氣孔44與外筒排氣孔組12的掃掠面重合,外筒排氣孔組12與蓋體的排氣孔42連通。
優選的,在外筒的封閉端的外側設有驅動齒輪,驅動齒輪帶動外筒旋轉。外筒的驅動也採用其他結構,如電磁驅動或真空驅動等,本發明對此不作限制。本實施例中,如圖11所示,在進氣外筒13的封閉端設置進氣驅動齒輪131,通過進氣驅動齒輪131帶動進氣外筒13正向順時針旋轉。在排氣外筒14的封閉端設置排氣驅動齒輪141,排氣驅動齒輪141帶動排氣外筒14正向順時針旋轉。
通過旋轉進氣外筒13,從而改變氣缸進排氣的提前角,調整進排氣的相位和時間。進排氣的相位和時間是指內燃機進排氣開啟和關閉時所對應的活塞和曲軸所在的位置。
以氣缸的進氣為例,如圖12所示,圖12a中內燃機低速工作,此時,將外筒進氣流出孔112旋轉至與進缸氣孔43完全重合,內筒進氣流出孔212旋轉至進氣開啟點時,其與外筒進氣流出孔112開始連通,氣缸即可進氣,內筒進氣流出孔212旋轉至與外筒進氣流出孔112不連通,即停止進氣。外筒進氣流出孔112的寬度一般小於進缸氣孔43的寬度,以便調節進氣相位。
圖12b中,內燃機中高速工作時,旋轉進氣外筒13,使得外筒進氣流出孔112旋轉過一定的角度,內筒進氣流出孔212旋轉至與外筒進氣流出孔112連通開啟的角度也隨之改變,氣缸進氣的開啟/關閉時間均延後,即改變了氣缸的進氣提前角,調整進氣的相位和時間,使得氣缸的壓縮行程時間變短。同樣的道理,旋轉排氣外筒14,可改變外筒排氣流入孔121與內筒排氣流入孔221連通開啟的角度,從而改變氣缸的排氣提前角,使得氣缸的做功行程時間加長。這樣的設計,可以提高內燃機的效率,大大提高內燃機的性能,減少汙染。
圖12c中,將進氣外筒13旋轉至外筒進氣流出孔112與進缸氣孔43完全不連通,同樣也可以將排氣外筒14旋轉至出缸氣孔44完全不連通,等於關閉了內燃機的進排氣,實現了閉缸。對於多缸的內燃機,可以將所有進缸氣孔和出缸氣孔關閉,實現全部閉缸,用於閉缸制動。還可以將進氣外筒13上的外筒進氣流出孔112設計在進氣外筒圓周的不同角度,以及排氣外筒14上的外筒排氣流入孔121設計在排氣外筒圓周的不同角度,使得部分氣缸的進排氣關閉,其餘氣缸正常工作,用於內燃機閉缸節油。
本實施例的內燃機工作流程是,當內燃機需要進氣時,內筒進氣孔組21旋轉至外筒進氣孔組11所在的角度,外筒進氣孔組11與內筒進氣孔組21連通。外部氣體依次通過蓋體的進氣孔41、外筒進氣流入孔111、內筒進氣流入孔211進入內筒的內腔。然後氣體依次通過內筒進氣流出孔212、外筒進氣流出孔112、進缸氣孔43由內筒2的內腔進入氣缸。當內燃機不需要進氣時,內筒進氣孔組21旋轉過外筒進氣孔組11所在的角度即可。
當內燃機需要排氣時,內筒排氣孔組22旋轉至外筒排氣孔組12所在的角度,外筒排氣孔組12與內筒排氣孔組22連通。缸內的氣體依次通過出缸氣孔44、外筒排氣流入孔121、內筒排氣流入孔221進入內筒2的內腔。然後氣體依次通過內筒排氣流出孔222、外筒排氣流出孔122、蓋體的排氣孔42排出內燃機。當內燃機不需要排氣時,使內筒排氣孔組22旋轉過外筒排氣孔組12所在的角度即可。
與實施例1相同,通過液壓油與波形彈簧的配合,使得進氣內筒25和排氣內筒26軸向移動,調節外筒孔組與內筒孔組的重疊面積,從而改變氣缸的進排氣截面積,調整氣缸的進排氣量。在內燃機高速運行時,外筒氣孔與內筒氣孔的連通截面積最大,即進排氣量最大。
通過旋轉進氣外筒13和排氣外筒14,改變氣缸進排氣的提前角,提高內燃機的效率。根據需要使得部分或全部氣缸關閉,實現內燃機的閉缸制動和節油。
本發明的進缸氣孔43和出缸氣孔44,可按傳統的內燃機,分別布置在相應氣缸的兩側。為了進一步提高內燃機的效率,如圖13所示,蓋體上的進缸氣孔43與出缸氣孔44對角布置。進缸氣孔43與出缸氣孔44對角布置,可使得缸內更容易形成渦流和滾流,渦流和滾流使得氣缸內的燃料和空氣混合更均勻,有利於提高燃料利用率和內燃機的性能。
在有多組進排氣孔組的內筒上,安裝隔離板件,隔離板件8為衝壓件,結構如圖14所示,隔離板件8設置在內筒2的內腔,將各個氣孔組隔離。圖9中所示,在進氣內筒25內設有進氣隔離板件81,進氣隔離板件81位於相鄰的內筒進氣孔組21之間;排氣內筒26內設有排氣隔離板件82,排氣隔離板件82位於相鄰的內筒排氣孔組22之間,可避免進排氣幹擾,減少噪音。同時,對於大型的內燃機,其氣缸內的工作壓力很大,這就需要外筒壁承受很大的壓力,在內筒設置隔離板件8,起到近似加強筋的作用,對外筒和內筒提供支撐,可提高進排氣裝置的抗擠壓能力。
如圖15所示,一種優選的方案為,在隔離板件8上設置渦片,以進一步提高內燃機的效率。以進氣隔離板件81為例,進氣隔離板件的側壁向外延伸出一部分,使得側壁可以覆蓋內筒進氣流出孔212,在側壁的圓周上設置渦片811,在進氣隔離板81的側壁上設有與內筒進氣流出孔212組配合的開口812,使得氣體可以流通。內筒旋轉時,進氣隔離板件81部分的氣體,從渦片中心進入低壓區域渦片中部,通過旋轉渦片的加壓推動,進一步獲得能力而增大進氣速度和進氣量。排氣隔離板件82的設計也可與進氣隔離板件81相同,排氣隔離板件82上設有與內筒排氣孔組配合的開口,廢氣排出時,因離心作用力而進一步推動排氣氣流速度,加快廢氣的排出。
需要說明的是,實施例2缸蓋的部分結構,如進缸氣孔與出缸氣孔對角布置、氣缸進排氣提前角的控制、內筒內設置隔離板件、外筒由驅動齒輪驅動等也同樣適用於實施1的缸蓋。
為了加強內筒與外筒之間、外筒與蓋體空腔之間的密封,可在外筒與內筒的外壁上,各個氣孔組之間設置密封槽,在密封槽內安裝密封件,保證各個部分之間的密封。本發明實施例的缸蓋的潤滑冷卻功能的設計按照本領域的常規設計即可。
在缸蓋的底部可以根據需要,設置火花塞和噴油嘴。缸蓋上各個部件的運行,可由內燃機的控制單元,根據內燃機的工作情況,進行調節。內燃機的曲軸通過皮帶或鏈條連接驅動軸,帶動內筒旋轉,依照曲軸的轉角控制氣缸的進排氣,完成內燃機的工作。
本發明中,內筒進氣流出孔和內筒排氣流入孔的邊沿的形狀可根據流體力學設計,使其有助於進排氣時氣體的渦流和滾流的形成,而利於燃氣混合和平穩燃燒。如在進氣時,在進氣末尾階段,因氣體流通的截面變小,而進一步推動進氣的流速等。
本發明的內燃機的進排氣控制為:外筒和內筒的相位傳感器的反饋信號進入內燃機的電子控制單元(ecu)之後,電子控制單元輸出控制信號來管理進氣/排氣的開度和相應位相。
依據來自內燃機冷卻液溫度傳感器,進氣喉管位置傳感器,機油油壓傳感器,空氣流量傳感器,曲軸位置傳感器以及外筒、內筒和各個相關傳統發動機傳感器進入電控單元之後,電子控制單元(ecu)按照標定數據相應控制進排氣筒件(外筒和內筒)的開啟時間和位相來保持相應的內燃機的動力輸出,使得燃料消耗和排放為最佳。
需要說明的是,以上參照附圖所描述的各個實施例僅用以說明本發明而非限制本發明的範圍,本領域的普通技術人員應當理解,在不脫離本發明的精神和範圍的前提下對本發明進行的修改或者等同替換,均應涵蓋在本發明的範圍之內。此外,除上下文另有所指外,以單數形式出現的詞包括複數形式,反之亦然。另外,除非特別說明,那麼任何實施例的全部或一部分可結合任何其它實施例的全部或一部分來使用。