金屬基水中拒油表面及其加工方法與流程
2023-05-27 10:45:22 2
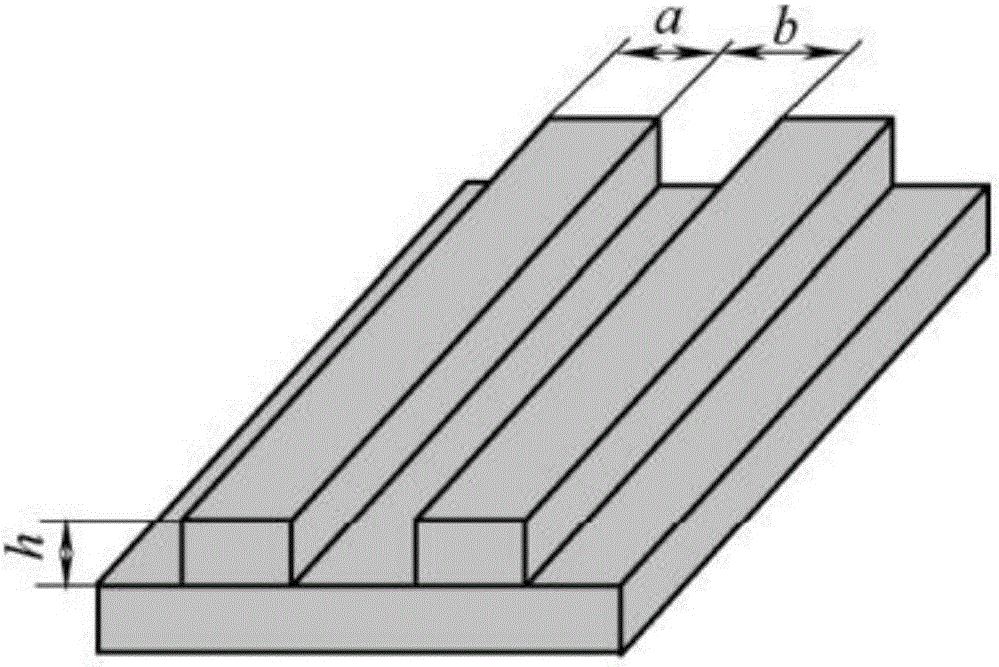
本發明涉及一種金屬基水中拒油表面及其加工方法,屬於界面材料改性技術領域。
背景技術:
水中拒油表面的設計是功能材料研究的主要方向。水中拒油表面是指在油/水/固三相體系中,油滴在固體表面的靜態接觸角大於150°,且具有極低的粘附性。一般來說水中拒油表面應該是在油/水/固三相體系中,油滴在固體表面既具有較大的靜態接觸角又具有較小的滾動角。自然界中存在著生物水中拒油表面,例如荷葉下表面、魚鱗和貝殼表面等。通過模仿他們的表面形態,人造的水中拒油表面在自清潔、防汙染、油/水分離和油滴操縱等方面存在巨大的應用價值。利用水中拒油表面的物理和化學特性來吸收水分子形成水化層,減少接觸有機液體,從而實現水中拒油功能。然而,大部分的水中拒油表面通常是以柔軟的材料(聚合物或膠體材料)作為基底,在較小機械作用下也會產生材料變形或表面損壞,失去水中拒油性能。
目前,已報導的製備水中拒油表面方法有很多,包括等離子體刻蝕,溶膠-凝膠法,電聚合,光聚合,模板法,層層自組裝,化學氣相沉積和飛秒雷射加工等,但這些方法在製備過程中表現出成本高、工藝複雜、不能批量生產、製備周期長及製備面積小等缺點,使得水中拒油表面的大規模工業生產和應用受到了極大的限制。
技術實現要素:
為了解決現有技術中存在的問題,本發明提供一種金屬基水中拒油表面及其加工方法。
本發明提供的金屬基水中拒油表面,以金屬材料為基底,表面加工有微結構。
進一步的,所述金屬材料為鋁合金、黃銅、鈦合金或不鏽鋼。
進一步的,所述微結構為溝槽陣列結構或方柱陣列結構,溝槽陣列結構凸起寬度a為50-200μm,微結構間距b為100-200μm,方柱長度c和寬度c分別為25μm-150μm,微結構高度h為50μm以上。
進一步的,所述金屬基水中拒油表面在水下油的接觸角為153-163°。
進一步的,所述金屬基水中拒油表面拒油種類為二氯乙烷、三氯甲烷、煤油、大豆油以及重油。
本發明還提供上述金屬基水中拒油表面的加工方法,包括如下步驟:
步驟一、開啟微銑削加工工具機的穩壓電源,待工具機顯示屏顯示各軸位置情況,調節速率將各軸歸零,調出工具機熱機程序,進行工具機熱機;
步驟二、工具機熱機後,將待加工金屬件裝卡到微銑削加工工具機的加工平臺上,利用測頭測出待加工金屬件的坐標點;
步驟三、用網線將電腦與微銑削加工工具機相連,將待加工金屬件表面微結構的程序從電腦中導入工具機,從工具機程序庫中調出所述程序使工具機開始加工,工具機根據程序在待加工金屬件表面加工微結構,同時開啟冷卻液,待加工結束後,卸下金屬件;
步驟四、將卸下的金屬件超聲清洗,得到金屬基水中拒油表面。
進一步的,所述步驟一的過程為:打開微銑削加工工具機電閘開關,開啟三相穩壓電源,旋轉工具機開關到ON,待工具機顯示屏顯示各軸位置情況,按下使能開關,然後同時按下Ref和綠色開關,調節速率將各軸歸零,之後調出工具機熱機程序,工具機熱機20-30分鐘。
進一步的,所述步驟二的過程為:將夾具基準面擦拭乾淨,將待加工金屬件裝夾到工具機夾具上,再利用測頭在金屬件平面上均勻取5個點測出Z值,然後算出平均值,即得到待加工金屬件坐標點。
進一步的,步驟三中,在加工微結構之前,採用直徑4-6mm銑刀對待加工金屬件表面進行平整精加工。
進一步的,步驟三中,所述工具機的加工參數為:刀具直徑為0.15-1mm,工具機轉速為5000-42000轉/分鐘,進給速度為100-1000mm/min,切削深度為20-50μm。
進一步的,步驟三中,所述冷卻液為蒸餾水或去離子水。
進一步的,步驟四中,所述的超聲清洗的過程為:將加工得到的金屬件依次放入無水乙醇和去離子水中分別進行超聲清洗10min,以去除表面殘留物。
進一步的,步驟四前,還包括,用氣槍將金屬件表面清理乾淨,卸下金屬件,打掃工具機。
與現有技術相比,本發明的有益效果為:
本發明的金屬基水中拒油表面具備優異的拒油性質,對油滴具有低粘附性,水下油的接觸角為153-163°,表現出水下超疏水性能,適用於二氯乙烷、三氯甲烷、煤油、大豆油以及重油;
本發明的金屬基水中拒油表面的加工方法使用精密微銑削設備加工水中拒油表面,一步即可以完成加工,製備工藝簡單、設備成本低、製備周期短;
本發明的金屬基水中拒油表面的加工方法可以直接在金屬材料表面加工微結構,大大降低了加工成本,並提升了加工效率;
本發明的金屬基水中拒油表面的加工方法可以方便的在金屬材料表面實現較大面積水中拒油表面的加工,可實現水中拒油表面的批量化生產。
附圖說明
圖1為溝槽陣列結構的金屬基水中拒油表面的結構示意圖;
圖2為方柱陣列結構的金屬基水中拒油表面的結構示意圖;
圖3為實施例1的鋁合金溝槽陣列結構(a=100μm,b=100μm,h=150μm)水中拒油表面的水下油接觸角。
具體實施方式
為了進一步了解本發明,下面結合具體實施方式對本發明的優選實施方案進行描述,但是應當理解,這些描述只是為進一步說明本發明的特徵和優點,而不是對本發明專利要求的限制。
本發明的金屬基水中拒油表面,以金屬材料為基底,表面加工有溝槽陣列結構或方柱陣列結構,溝槽陣列結構試樣共加工10組,如圖1所示,其中,a表示溝槽陣列結構凸起寬度,b表示微結構間距,c×c表示方柱長度×寬度,h表示微結構高度。常用的h為50μm以上,優選50-150μm,b為100-200μm,a為50-200μm,c為25μm-150μm。
上述金屬基水中拒油表面的加工方法,包括如下步驟:
步驟一、打開微銑削加工工具機的電閘開關,開啟三相穩壓電源,旋轉工具機開關到ON,待工具機顯示屏顯示各軸位置情況,按下使能開關,然後同時按下Ref和綠色開關,調節速率將各軸歸零,之後調出工具機熱機程序,工具機熱機20-30分鐘。
步驟二、工具機熱機後,將夾具基準面擦拭乾淨,將待加工金屬件裝夾到工具機夾具上,再利用測頭在金屬件平面上均勻取5個點測出Z值,然後算出平均值,即得到待加工金屬件坐標點。
步驟三、用網線將電腦與微銑削加工工具機相連,將待加工金屬件表面微結構的程序從電腦中導入工具機,從工具機程序庫中調出所述程序使工具機開始加工,工具機根據程序在待加工金屬件表面加工微結構,加工參數為:刀具直徑為0.15-1mm,工具機轉速為5000-42000轉/分鐘,進給速度為100-1000mm/min,同時開啟冷卻液,冷卻液為蒸餾水或去離子水,待加工結束後,用氣槍將金屬件表面清理乾淨,卸下金屬件,打掃工具機;
其中,待加工金屬件表面微結構的程序可以預先在電腦中編寫,根據待加工的微結構的形狀編寫程序為工具機加工中的常規過程。
步驟四、將加工得到的金屬件依次放入無水乙醇和去離子水中分別進行超聲清洗10min,以去除表面殘留物,得到金屬基水中拒油表面。該金屬基水中拒油表面在水下油的接觸角為150°以上,一般為153-163°,適用於二氯乙烷、三氯甲烷、煤油、大豆油以及重油。
以下結合實施例進一步說明本發明。下述實施例中所用的材料、試劑等,如無特殊說明,均可從商業途徑得到。
實施例1
鋁合金水中拒油表面,以鋁合金為基底,表面加工有溝槽陣列結構或方柱陣列結構。
上述鋁合金水中拒油表面的加工方法:
步驟一、打開微銑削加工工具機的電閘開關,開啟三相穩壓電源,旋轉開關到ON,待工具機顯示屏顯示各軸位置情況,按下使能開關,然後同時按下Ref和綠色開關,調節速率將各軸歸零,之後調出工具機熱機程序,工具機熱機20分鐘。
步驟二、將夾具基準面擦拭乾淨,將所加工鋁合金試樣裝夾到工具機夾具上,再利用測頭在鋁合金試樣上平面均勻取5個點測出Z值,然後算出平均值,即鋁合金試樣坐標點。
步驟三、用網線將電腦與微銑削加工工具機相連,將待加工鋁合金試樣表面微結構的程序從電腦中導入工具機,從工具機程序庫中調出所述程序使工具機開始加工,工具機根據程序在待加工鋁合金試樣表面加工微結構,加工參數為:刀具直徑為1mm,工具機轉速為10000轉/分鐘,進給速度為500mm/min,同時開啟冷卻液,冷卻液為蒸餾水,待加工結束後,用氣槍將鋁合金試樣表面清理乾淨,卸下鋁合金試樣,打掃工具機;
其中,為便於測試,加工的微結構,分為十組溝槽陣列結構,高度h均為150μm,其他結構參數如表1所示,五組方柱陣列結構,間距b均為100μm,高度h均為150μm,其他結構參數如表2所示。
步驟四、將加工得到的鋁合金試樣依次放入無水乙醇和去離子水分別進行超聲清洗10min,以去除表面殘留物,得到鋁合金水中拒油表面。
對鋁合金水中拒油表面進行油滴的靜態接觸角測量,在不同的5個位置測量了靜態接觸角,溝槽陣列結構表面接觸角結果見表1,方柱陣列結構表面接觸角結果見表2。其中,如圖3所示,溝槽陣列結構表面(a=100μm,b=100μm,h=150μm)靜態接觸角達到了158.5°。
實施例2
黃銅水中拒油表面,以黃銅為基底,表面加工有溝槽陣列結構或方柱陣列結構。
上述黃銅水中拒油表面的加工方法:
步驟一、加工前,打開微銑削加工工具機的電閘開關,開啟三相穩壓電源,旋轉工具機開關到ON。待工具機顯示屏顯示各軸位置情況,按下使能開關,然後同時按下Ref和綠色開關,調節速率將各軸歸零,之後調出工具機熱機程序,工具機熱機30分鐘。
步驟二、將夾具基準面擦拭乾淨,將所加工黃銅試樣裝夾到工具機夾具上,再利用測頭在黃銅試樣上平面均勻取5個點測出Z值,然後算出平均值,即黃銅試樣坐標點。
步驟三、用網線將電腦與微銑削加工工具機相連,將待加工黃銅試樣表面微結構的程序從電腦中導入工具機,從工具機程序庫中調出所述程序使工具機開始加工,工具機根據程序在待加工黃銅試樣表面加工微結構,加工參數為:刀具直徑為0.5mm,工具機轉速為5000轉/分鐘,進給速度為1000mm/min,切削深度為50μm,同時開啟冷卻液,冷卻液為蒸餾水,待加工結束後,用氣槍將工件表面清理乾淨,卸下黃銅試樣,打掃工具機;
其中,為便於測試,加工的微結構,分為十組溝槽陣列結構,高度h均為150μm,其他結構參數如表1所示,五組方柱陣列結構,間距b均為100μm,高度h均為150μm,其他結構參數如表2所示。
步驟四、將加工得到的黃銅試樣依次放入無水乙醇和去離子水分別進行超聲清洗10min,以去除表面殘留物,得到黃銅水中拒油表面。
對黃銅水中拒油表面進行油滴的靜態接觸角測量,在不同的5個位置測量了靜態接觸角,溝槽陣列結構表面接觸角結果見表1,方柱陣列結構表面接觸角結果見表2。
實施例3
鈦合金水中拒油表面,以鈦合金為基底,表面加工有表面加工有溝槽陣列結構或方柱陣列結構。
上述鈦合金基水中拒油表面的加工方法:
步驟一、加工前,打開微銑削加工工具機的電閘開關,開啟三相穩壓電源,旋轉工具機開關到ON。待工具機顯示屏顯示各軸位置情況,按下使能開關,然後同時按下Ref和綠色開關,調節速率將各軸歸零,之後調出工具機熱機程序,工具機熱機25分鐘。
步驟二、將夾具基準面擦拭乾淨,將所加工鈦合金試樣裝夾到工具機夾具上,再利用測頭在鈦合金試樣上平面均勻取5個點測出Z值,然後算出平均值,即鈦合金試樣坐標點。
步驟三、用網線將電腦與微銑削加工工具機相連,將待加工鈦合金試樣表面微結構的程序從電腦中導入工具機,從工具機程序庫中調出所述程序使工具機開始加工,工具機根據程序在待加工鈦合金試樣表面加工微結構,加工參數為:刀具直徑為0.15mm,工具機轉速為42000轉/分鐘,進給速度為100mm/min,同時開啟冷卻液,冷卻液為蒸餾水,待加工結束後,用氣槍將工件表面清理乾淨,卸下鈦合金試樣,打掃工具機;
其中,為便於測試,加工的微結構,分為十組溝槽陣列結構,高度h均為150μm,其他結構參數如表1所示,五組方柱陣列結構,間距b均為100μm,高度h均為150μm,其他結構參數如表2所示。
步驟四、將加工得到的鈦合金試樣依次放入無水乙醇和去離子水分別進行超聲清洗10min,以去除表面殘留物。
對鈦合金水中拒油表面進行油滴的靜態接觸角測量,在不同的5個位置測量了靜態接觸角,溝槽陣列結構表面接觸角結果見表1,方柱陣列結構表面接觸角結果見表2。
實施例4
不鏽鋼水中拒油表面,以不鏽鋼為基底,表面加工表面加工有溝槽陣列結構或方柱陣列結構。
上述不鏽鋼水中拒油表面的加工方法:
步驟一、加工前,打開微銑削加工工具機的電閘開關,開啟三相穩壓電源,旋轉工具機開關到ON。待工具機顯示屏顯示各軸位置情況,按下使能開關,然後同時按下Ref和綠色開關,調節速率將各軸歸零,之後調出工具機熱機程序,工具機熱機25分鐘。
步驟二、將夾具基準面擦拭乾淨,將所加工不鏽鋼試樣裝夾到工具機夾具上,再利用測頭在不鏽鋼試樣上平面均勻取5個點測出Z值,然後算出平均值,即不鏽鋼試樣坐標點;
步驟三、用網線將電腦與微銑削加工工具機相連,將待加工不鏽鋼試樣表面微結構的程序從電腦中導入工具機,從工具機程序庫中調出所述程序使工具機開始加工,工具機根據程序在待加工不鏽鋼試樣表面加工微結構,加工參數為:刀具直徑為0.7mm,工具機轉速為20000轉/分鐘,進給速度為600mm/min,同時開啟冷卻液,冷卻液為蒸餾水,待加工結束後,用氣槍將工件表面清理乾淨,卸下不鏽鋼試樣,打掃工具機;
其中,為便於測試,加工的微結構,分為十組溝槽陣列結構,高度h均為150μm,其他結構參數如表1所示,五組方柱陣列結構,間距b均為100μm,高度h均為150μm,其他結構參數如表2所示。
步驟四、將加工得到的不鏽鋼試樣依次放入無水乙醇和去離子水分別進行超聲清洗10min,以去除表面殘留物,得到不鏽鋼水中拒油表面。
對不鏽鋼水中拒油表面進行油滴的靜態接觸角測量,在不同的5個位置測量了靜態接觸角,溝槽陣列結構表面接觸角結果見表1,方柱陣列結構表面接觸角結果見表2。
表1實施例1-4的溝槽陣列結構拒油表面接觸角結果
從表1可以看出,本發明的溝槽陣列結構拒油表面具備優異的拒油性質,水下油的接觸角為153-163°,表現出水下超疏水性能,且在間距固定的條件下,寬度越小,水下油的接觸角越大,在寬度固定的條件下,間距越小,水下油的接觸角越大。
表2實施例1-4的方柱陣列結構拒油表面接觸角結果
從表2可以看出,本發明的方柱陣列結構拒油表面具備優異的拒油性質,水下油的接觸角為154-163°,表現出水下超疏水性能,且隨著方柱寬度的增加,水下油的接觸角先增大後減小。