一種鈦及鈦合金真空自耗電極的擠壓裝置及製備方法與流程
2023-06-02 00:53:36 3
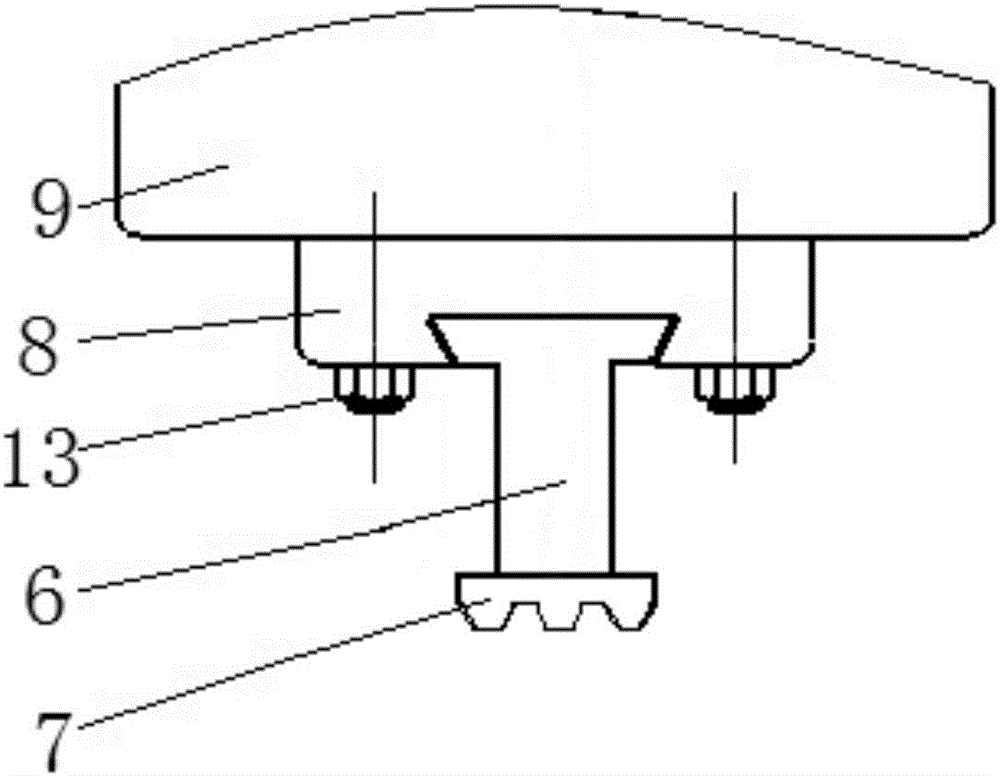
本發明屬於鈦及鈦合金產品生產加工技術領域,具體涉及一種鈦及鈦合金真空自耗電極的擠壓裝置,本發明還涉及一種鈦及鈦合金真空自耗電極的製備方法。
背景技術:
鈦及鈦合金具有低密度、高比強、耐腐蝕、耐高溫、無磁性、生物相容等優異的綜合性能,廣泛應用於航空、航天、艦船、兵器、石油、化工、醫療等領域。
鈦及鈦合金真空熔煉時,需要採用自耗電極。現有的鈦及鈦合金自耗電極的製備方法是用電極壓機將海綿鈦或鈦合金壓製成截面為扇形、半圓形、圓形或多邊形電極塊,然後通過頂出裝置將壓好的電極塊頂出脫模,再通過拼接和氬弧焊或真空等離子焊將壓好的電極塊組焊在一起,製備成所需長度的鈦及鈦合金自耗電極。這種製備方法生產效率低、成本高,壓製出的電極塊密度低,約3.0~3.3g/cm3;在電極塊組焊的過程中,容易受到有害金屬和氣體汙染,造成最終產品出現高、低密度夾雜,降低了產品的純度和品質。
技術實現要素:
本發明的目的是提供一種鈦及鈦合金真空自耗電極的擠壓裝置,解決了現有鈦及鈦合金真空自耗電極在製備過程中,焊接工序導致的電極被汙染,電極產品出現高、低密度夾雜,電極密度低以及高成本低效率的問題。
本發明的另一個目的是提供一種鈦及鈦合金真空自耗電極的製備方法。
本發明一種鈦及鈦合金真空自耗電極的擠壓裝置所採用的技術方案是,包括設置有通孔的工作檯,工作檯一側連接有出料導筒,工作檯另一側依次連接有擠壓筒和上料導筒,上料導筒內設置有擠壓杆,擠壓杆一端連接擠壓墊片,擠壓杆的另一端依次連接模座和滑塊,擠壓筒內壁套接有內套,內套內壁套接有擠壓模具;擠壓模具包括模具a和模具b,模具b靠近工作檯且其呈中空柱狀,模具a靠近上料導筒且其呈錐形。
本發明的特徵在於,
擠壓墊片位於靠近上料導筒一端,且擠壓墊片呈圓餅狀或一端分布有凸起的圓餅狀。
模座和滑塊通過螺栓相固接。
圓餅狀擠壓墊片的外徑與上料導筒的內徑相配合;一端分布有凸起的圓餅狀擠壓墊片的外徑與模具b的內徑相配合。
本發明的另一個技術方案,一種鈦及鈦合金真空自耗電極的製備方法,包括以下步驟:
步驟1,清理模具a和模具b,在模具b內壁放置與其相配合的塞子;
步驟2,稱取原料100-150kg,且將其緩慢倒入經步驟1清理的模具a中;
步驟3,將一端分布有凸起的圓餅狀擠壓墊片連接在擠壓杆上,在滑塊和模座的作用下,擠壓墊片與步驟2中的原料相接觸;
步驟4,擠壓墊片和擠壓杆繼續擠壓原料,當將原料完全擠壓至模具b時停止,在滑塊和模座的作用下,擠壓墊片與步驟2中的原料相分離;
步驟5,重複步驟2-步驟4擠壓原料若干次;
步驟6,將步驟3中的擠壓墊片換成圓餅狀擠壓墊片,步驟1中的塞子放置於模具b內繼續擠壓,依次通過通孔和出料導筒得到所需電極。
本發明的特徵還在於,
步驟2中的原料為海綿鈦或者鈦合金。
步驟6中通孔和出料導筒的內徑相同,且均不小於模具b的內徑。
通孔和出料導筒的內徑均為450-650mm。
本發明的有益效果是:本發明一種鈦及鈦合金真空自耗電極的擠壓裝置通過採用滑塊依次帶動擠壓杆、擠壓墊片的運動,在擠壓過程,連續在模具a中添加海綿鈦及其鈦合金原料,同時使用一端分布有凸起的圓餅狀擠壓墊片,實現鈦及鈦合金真空自耗電極的半連續擠壓,克服了傳統焊接工序導致的電極被汙染,電極產品出現高、低密度夾雜,密度降低的問題,擠壓出密度為3.5~3.8g/cm3,提高生產效率,節省生產成本,降低工人勞動強度,有很好的實用價值。
附圖說明
圖1是本發明一種鈦及鈦合金真空自耗電極的擠壓裝置的結構示意圖;
圖2是本發明一種鈦及鈦合金真空自耗電極的擠壓裝置中擠壓墊片的主視圖;
圖3是本發明一種鈦及鈦合金真空自耗電極的擠壓裝置中另一種擠壓墊片的主視圖。
圖中,1.通孔,2.工作檯,3.出料導筒,4.擠壓筒,5.上料導筒,6.擠壓杆,7.擠壓墊片,8.模座,9.滑塊,10.內套,11.模具a,12.模具b,13.螺栓。
具體實施方式
下面結合附圖和具體實施方式對本發明進行詳細說明。
本發明一種鈦及鈦合金真空自耗電極的擠壓裝置,如圖1所示,包括設置有通孔1的工作檯2,工作檯2一側連接有出料導筒3,工作檯2另一側依次連接有擠壓筒4和上料導筒5,上料導筒5內設置有擠壓杆6,擠壓杆6一端連接擠壓墊片7,擠壓杆6的另一端依次連接模座8和滑塊9,擠壓筒4內壁套接有內套10,內套10內壁套接有擠壓模具;擠壓模具包括模具a11和模具b12,模具b12靠近工作檯2且其呈中空柱狀,模具a11靠近上料導筒5且其呈錐形,其中擠壓墊片7位於靠近上料導筒5一端,且擠壓墊片7呈圓餅狀或一端分布有凸起的圓餅狀;模座8和滑塊9通過螺栓13相固接。
圓餅狀擠壓墊片7的外徑與上料導筒5的內徑相配合;一端分布有凸起的圓餅狀擠壓墊片7的外徑與模具b12的內徑相配合。
一種鈦及鈦合金真空自耗電極的製備方法,其特徵在於,包括以下步驟:
步驟1,清理模具a11和模具b12,在模具b12內壁放置與其相配合的塞子;
步驟2,稱取原料100-150kg,且將其緩慢倒入經步驟1清理的模具a11中,其中原料為海綿鈦或者鈦合金;
步驟3,如圖2所示,將分布有凸起的圓餅狀擠壓墊片7連接在擠壓杆6上,在滑塊9和模座8的作用下,擠壓墊片7與步驟2中的原料相接觸,分布有凸起的圓餅狀擠壓墊片7在擠壓電極時由於增大了連續兩次加料擠壓電極之間的接觸面積,使其能彼此咬合,增加了電極強度;
步驟4,擠壓墊片7和擠壓杆6繼續擠壓原料,當將原料完全擠壓至模具b12時停止,在滑塊9和模座8的作用下,擠壓墊片7與步驟2中的原料相分離;
步驟5,重複步驟2-步驟4擠壓原料若干次,直至達到所需的電極長度;
步驟6,如圖3所示,將步驟3中的擠壓墊片7換成圓餅狀擠壓墊片7,步驟1中塞子放置於模具b12內繼續擠壓,依次通過通孔1和出料導筒3得到所需電極,圓餅狀擠壓墊片7保證了電極末端在擠壓過程中能夠平整,方便自耗電極產品的使用。
步驟6中通孔1和出料導筒3的內徑相同,且均不小於模具b12的內徑;通孔1和出料導筒3的內徑均為450-650mm。
實施例1
原材料選用1級粒度為0.83~25.4mm的海綿鈦,通孔1和出料導筒3的內徑均為650mm。
清理模具a11和模具b12,在模具b12內壁放置與其相配合的塞子;將準確秤量後的150kg海綿鈦緩慢倒入處理後的模具a11中,使用分布有凸起的圓餅狀擠壓墊片7,在滑塊9和模座8的作用下,將海綿鈦擠壓推動至模具b12中;反覆裝料並擠壓共40次,最後一次擠壓採用圓餅狀擠壓墊片7使其形成平坦的電極末端,最後將塞子置於模具b12內壁,擠壓出自耗電極的最後部分,自耗電極的半連續擠壓操作結束。
所製備出的鈦自耗電極規格為Φ650mm×4900mm,密度為3.6g/cm3。後續選擇真空自耗熔煉工藝熔煉出一次Φ820mm鑄錠,二次Φ920鑄錠;鑄錠通過整錠探傷,上中下部橫截面五點化學成分分析,最終確定鑄錠為符合標準要求、達到配比計算要求,成分均勻的無偏析優質鑄錠。
實施例2
原材料選用0級粒度為3.0~12.7mm的海綿鈦、粒度為1~6mm的AlV55中間合金、Φ8~13mm鋁含量大於99.8%的鋁豆;通孔1和出料導筒3的內徑均為450mm。。
清理模具a11和模具b12,在模具b12內壁放置與其相配合的塞子;將按配比準確秤量後共100kg鈦合金原料緩慢倒入處理後的模具a11中,使用一端分布有凸起的圓餅狀擠壓墊片7,在滑塊9和模座8的作用下,將海綿鈦擠壓推動至模具b12中;反覆裝料並擠壓共33次,最後一次擠壓採用圓餅狀擠壓墊片7使其形成平坦的電極末端,最後將塞子置於模具b12內壁,擠壓出自耗電極的最後部分,自耗電極的半連續擠壓操作結束。
所製備出的自耗電極規格為Φ450mm×5600,電極密度為3.6g/cm3。後續選擇真空自耗熔煉工藝熔煉出一次Φ560mm鑄錠,二次Φ640鑄錠,三次720mm鑄錠;對鑄錠進行低倍及高倍組織分析,未發現鋁及釩元素偏析的現象;鑄錠通過整錠探傷,上中下部橫截面五點化學成分分析,最終確定鑄錠為符合標準要求、達到配比計算要求,成分均勻的無偏析優質鑄錠。
實施例3
原材料選用1級粒度為0.83~25.4mm的海綿鈦,通孔1和出料導筒3的內徑均為550mm。
清理模具a11和模具b12後,在模具b12內壁放置與其相配合的塞子;將準確秤量後的120kg海綿鈦緩慢倒入處理後的模具a11中,使用一端分布有凸起的圓餅狀擠壓墊片7,在滑塊9和模座8的作用下,將海綿鈦擠壓推動至模具b12中;反覆裝料並擠壓共35次,最後一次擠壓採用圓餅狀擠壓墊片7使其形成平坦的電極末端,最後將塞子置於模具b12內壁,擠壓出自耗電極的最後部分,自耗電極的半連續擠壓操作結束。
所製備出的鈦自耗電極規格為Φ550mm×5050mm,密度為3.5g/cm3。後續選擇真空自耗熔煉工藝熔煉出一次Φ650mm鑄錠,二次Φ750鑄錠;鑄錠通過整錠探傷,上中下部橫截面五點化學成分分析,最終確定鑄錠為符合標準要求、達到配比計算要求,成分均勻的無偏析優質鑄錠。
本發明通過採用滑塊9依次帶動擠壓杆6、擠壓墊片7的運動,在擠壓過程,連續在模具a11中添加海綿鈦及其鈦合金原料,同時使用一端分布有凸起的圓餅狀擠壓墊片7,實現鈦及鈦合金真空自耗電極的半連續擠壓,克服了傳統焊接工序導致的電極被汙染,電極產品出現高、低密度夾雜,密度降低的問題,擠壓出密度為3.5~3.8g/cm3,提高生產效率,節省生產成本,降低工人勞動強度,有很好的實用價值。