一種液壓缸差動迴路閥及液壓缸開式/閉式差動迴路的製作方法
2023-05-28 16:09:46 2
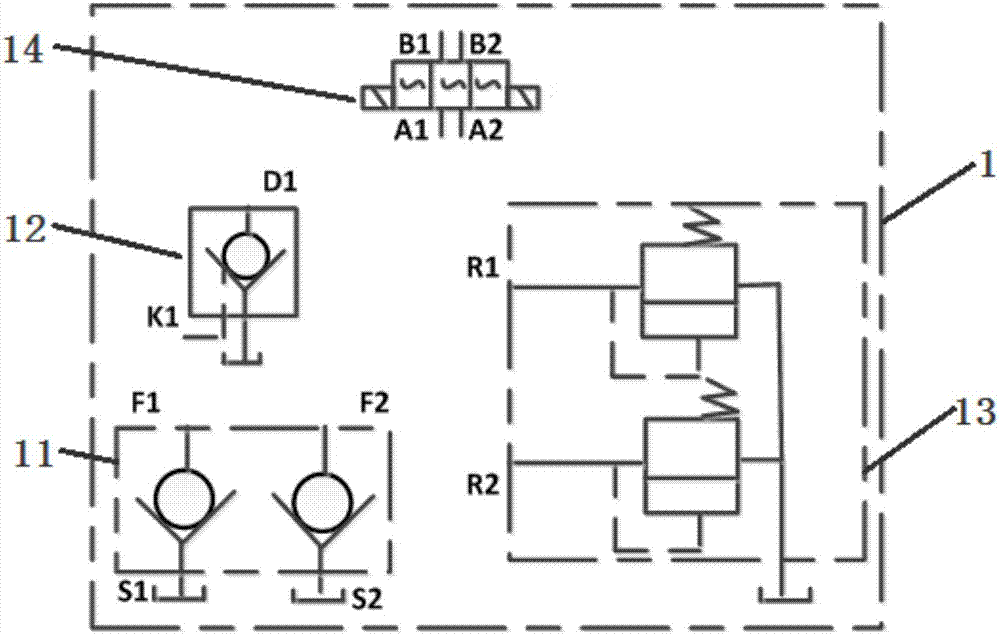
本實用新型涉及液壓缸差動系統領域,尤其涉及一種液壓缸差動迴路閥,還涉及一種包括所述液壓缸差動迴路閥的液壓缸開式差動迴路和液壓缸閉式差動迴路。
背景技術:
差動液壓缸在各種機械設備上應用極其廣泛,尤以雙作用單活塞杆式液壓缸的應用甚多。液壓缸開式差動迴路中,通常採用PO形三位四通換向閥、三通換向閥等實現差動控制;液壓缸閉式差動迴路中,通常採用單向閥作為補油閥,採用溢流閥或者液控單向閥漏出多餘流量,採用溢流閥限制油缸有杆腔和無杆腔的最高壓力。目前在開式和閉式差動缸迴路中還沒有差動迴路閥,主要是在迴路中通過串接換向閥、溢流閥或者液控單向閥等實現。現有液壓缸差動迴路具有如下缺點:
(1)開式和閉式液壓缸差動迴路採用液壓閥不通用,系統複雜,成本較高;
(2)多個零部件分開單獨組裝,效率低下;
(3)現有迴路為非模塊化設計,不利於系統功擴展。
技術實現要素:
為解決現有技術中的問題,本實用新型提供一種液壓缸差動迴路閥,還提供一種包括所述液壓缸差動迴路閥的液壓缸開式差動迴路和液壓缸閉式差動迴路。
本實用新型液壓缸差動迴路閥包括補油模塊:設置在泵吸油口,用於防止液壓泵吸空;流量漏出模塊:用於將液壓缸多餘的流量流回油箱;安全模塊:用於限制液壓缸有杆腔和無杆腔的最高壓力;換向模塊:用於實現油缸方向的轉變。
本實用新型作進一步改進,所述補油模塊為補油閥、單向閥或電磁流量閥。
本實用新型作進一步改進,所述流量漏出模塊為與油箱連接的液控單向閥、電磁流量閥或手動閥。
本實用新型作進一步改進,所述安全模塊為溢流閥。
本實用新型作進一步改進,所述換向模塊包括換向閥、梭閥,所述換向閥包括三位四通換向閥、兩位三通換向閥等等。
本實用新型還提供一種包括所述液壓缸差動迴路閥的液壓缸開式差動迴路,包括液壓泵、液壓缸,所述液壓缸通過所述液壓缸差動迴路閥的換向模塊與所述液壓泵相連,所述安全模塊連接在所述液壓泵和所述換向模塊之間的油路上。
本實用新型作進一步改進,所述換向模塊為三位四通換向閥,所述三位四通換向閥包括同側的B1口、B2口及A1口、A2口,所述三位四通換向閥B1口和B2口分別與液壓缸的無杆腔和無杆腔相接,所述三位四通換向閥A1口與液壓泵相連,所述三位四通換向閥A2口連油箱;所述安全模塊為與油箱連接的安全閥,所述安全閥的一端連接在所述液壓泵和三位四通換向閥A1口之間。
本實用新型還提供一種包括所述液壓缸差動迴路閥的液壓缸閉式差動迴路,包括閉式液壓泵、液壓缸,所述安全模塊包括兩個並列設置的安全單元,所述流量漏出模塊的一端、其中一個安全單元並接在所述閉式液壓泵其中一個口和液壓缸的無杆腔之間,所述流量漏出模塊的的另一端、另外一個安全單元和補油模塊並接在所述閉式液壓泵另一個口和液壓缸的有杆腔之間。
本實用新型作進一步改進,所述安全模塊為並接的安全閥,所述補油模塊為輸入端S1連接油箱,輸出端F1連接閉式液壓泵和液壓缸的有杆腔之間的單向閥。
本實用新型作進一步改進,所述閉式液壓泵包括S1口和S2口,所述流量漏出模塊為包括一個連接油箱的輸入端,兩個輸出端D1口和K1口的單向閥,所述單向閥的D1口連接在閉式液壓泵S1口和液壓缸無杆腔之間,所述單向閥的K1口連接在閉式液壓泵S2口和液壓缸有杆腔之間。
與現有技術相比,本實用新型的有益效果是:本實用新型液壓缸差動迴路閥既可以應用在液壓缸開式差動迴路中,也可以應用在液壓缸閉式差動迴路中;模塊化設計,根據系統設計需要,可方便地選取功能模塊並將各個功能模塊拼接,系統簡單,成本降低,並且應用組裝效率大大提高;本實用新型液壓缸差動迴路閥擴展性能較強,可以在閥塊上增加功能模塊,從而具備新增功能擴展能力。
附圖說明
圖1為本實用新型液壓缸差動迴路閥一實施例結構示意圖;
圖2為流量漏出模塊另一實施例結構示意圖;
圖3為補油模塊另一實施例結構示意圖;
圖4為液壓缸開式差動迴路結構示意圖;
圖5為液壓缸閉式差動迴路結構示意圖。
具體實施方式
下面結合附圖和實施例對本實用新型做進一步詳細說明。
如圖1所示,本實用新型液壓缸差動迴路閥1模塊化設計,包括補油模塊11、流量漏出模塊12、安全模塊13和換向模塊14。其中,在液壓缸閉式差動迴路(簡稱閉式系統)中,為了防止閉式液壓泵4吸空現象,常在泵吸油口接入補油模塊11。目前實現補油功能的補油模塊11既可以通過專用補油閥實現,也可以通過單向閥實現,本例為兩個連接油箱的單向閥並列組成,其中一個單向閥包括接口F1和連接油箱的接口S1,另一個單向閥包括接口F2和連接油箱的接口S2,此外,本例的補油模塊11還可以通過電磁流量閥來實現,如圖2所示。
本例的流量漏出模塊12的作用是用於將液壓缸多餘的流量流回油箱,本例的流量漏出模塊12為與油箱連接的液控單向閥,本例的液控單向閥包括一個連接油箱的輸入端,兩個輸出端D1口和K1口。此外,還可以用電磁流量閥或者手動閥等替換原來的液控單向閥,如圖3所示。
本例的安全模塊13用於限制液壓缸有杆腔和無杆腔的最高壓力,本例的安全模塊13主要通過溢流閥實現。本例由兩個單獨的連接油箱溢流閥組成,兩個溢流閥的接口分別為R1和R2。
本例的換向模塊14用於實現油缸方向的轉變。在液壓缸開式差動迴路(簡稱:開式系統)中,常採用換向閥來實現油缸方向的轉變,在閉式系統中因為泵是雙向的,一般不需採用換向閥來進行換向。換向模塊14主要由換向閥或梭閥等等組成,所述換向閥包括三位四通換向閥、兩位三通閥等。本例的換向模塊14為三位四通換向閥,所述三位四通換向閥包括設置在同側的B1口、B2口及設置在另一側的A1口、A2口。
如圖4所示,將液壓缸差動迴路閥1應用在開式系統中時,本實用新型液壓缸開式差動迴路包括液壓缸差動迴路閥1、液壓泵3和液壓缸2,液壓泵3高壓口與安全模塊13的R2口、換向模塊14的A1口並聯,換向模塊14的A2口連油箱,液壓缸2的進油口和出油口分別與換向模塊14的B1、B2口連接,本實用新型液壓缸差動迴路閥1的其餘油口用堵頭堵住。本例的液壓缸為單出杆液壓缸。
如圖5所示,將液壓缸差動迴路閥1應用在閉式系統中時,本實用新型液壓缸閉式差動迴路包括液壓缸差動迴路閥1、閉式液壓泵4和液壓缸2,所述閉式液壓泵包括S1口和S2口,其中,閉式液壓泵4的S2口與補油模塊11的F1口、流量漏出模塊12的K1口、安全模塊13的R2口、液壓缸2的有杆腔油口並接,閉式液壓泵4的S1口與流量漏出模塊12的D1口、安全模塊13的R1口、液壓缸2的無杆腔油口並接。
流量漏出模塊12的工作原理為:當閉式液壓泵4的S2口為高壓口,S1口為低壓口時,液壓缸2的有杆腔進油,無杆腔出油,由於無杆腔的有效作用面積Aw大於有杆腔面積Ay,此時液壓缸2的無杆腔多餘流量會從液控單向閥的D1口流回油箱;相反,則從液控單向閥的K1口流回油箱。
本實用新型液壓缸差動迴路閥既可用於開式迴路,也可用於閉式迴路。該閥採用模塊化設計方案,根據系統設計需要,可方便地選取功能模塊並將各個功能模塊拼接,系統簡單,組裝效率大大提高,成本降低。此外,該閥擴展性能較強,可以在閥塊上增加功能模塊,從而具備新增功能擴展能力。
以上所述之具體實施方式為本實用新型的較佳實施方式,並非以此限定本實用新型的具體實施範圍,本實用新型的範圍包括並不限於本具體實施方式,凡依照本實用新型所作的等效變化均在本實用新型的保護範圍內。