用於電弧增材製造熔敷道尺寸無滯後實時檢測裝置及實時檢測方法與流程
2023-05-28 11:00:36 1
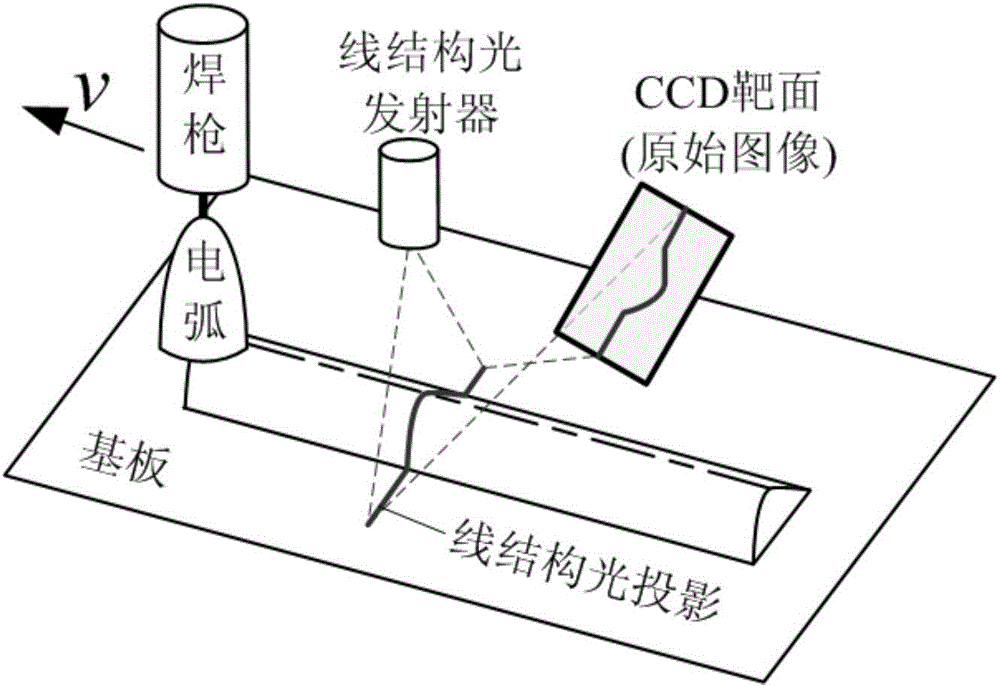
本發明屬於智能化增材製造領域。
背景技術:
在電弧增材製造中,如何無滯後地實時檢測熔敷道的寬度和高度信息是個關鍵問題。
熔敷道尺寸屬於幾何信息,適合使用視覺傳感器進行非接觸檢測。現有的視覺檢測方法包括線結構光主動式視覺檢測和CCD被動視覺檢測兩種,它們都存在一定的局限性。
線結構光傳感器是一種常用的主動視覺傳感器,可同時檢測熔敷道的寬度和高度信息。但是,為了防止電弧弧光對線結構光視覺傳感產生幹擾,需在傳感器與焊槍之間加設擋板,遮擋弧光,並且,傳感位置離焊槍有一定的距離(大約35mm),導致檢測信息的滯後問題,如圖1所示。另外,隨著熔敷道溫度升高,物體發射能力逐漸增強,當幹擾光光強與結構光信號光強水平相當時,則幹擾光會被傳感器響應,嚴重影響檢測過程,因此,線結構光傳感器不適用於熔敷道高溫區域的檢測,只能檢測熔池後方已凝固的成形金屬。
CCD被動視覺傳感方法可以直接對熔池高溫熔敷金屬及其附近區域取像觀察,經過適當的圖像處理,即可得到實時的無滯後的熔敷道尺寸信息,然而,這種傳感方式所得到的圖像無法記錄深度信息,所得到的熔敷道尺寸信息有限。
因此,迫切需要提出一種結合線結構光主動視覺和CCD被動視覺優點的新的電弧增材製造熔敷道尺寸檢測方法,實現熔敷道寬度和高度無滯後檢測。
技術實現要素:
本發明目的是為了解決現有技術無法實現熔敷道寬度和高度無滯後檢測的問題,提供了一種用於電弧增材製造熔敷道尺寸無滯後實時檢測裝置及實時檢測方法。
本發明所述用於電弧增材製造熔敷道尺寸無滯後實時檢測裝置,該裝置包括分區減光元件、線結構光發生器、濾光片、CCD攝像機和鏡頭;鏡頭安裝在CCD攝像機的成像靶面的前端,鏡頭內部的前端安裝有濾光片,線結構光發生器發射的雷射條紋投射至熔池後方,且雷射條紋與熔池之間存在距離,焊槍垂直設置在熔池的正上方,焊槍產生的電弧位於熔池的上端;CCD攝像機的成像靶面與鏡頭之間安裝有分區減光元件。
本發明所述用於電弧增材製造熔敷道尺寸無滯後實時檢測裝置的實時檢測方法,該實時檢測方法能夠實現一幅CCD視覺圖像同時看清高溫熔敷金屬和雷射條紋,實現電弧增材製造熔敷道尺寸的無滯後實時檢測,具體方法為:分區減光元件控制熔池的進光量低於雷射條紋的進光量,使分區減光後熔敷金屬光譜輻射強度與雷射條紋光強水平相同。
本發明的優點:本發明提出了CCD視覺傳感器分區減光的方法,實現了一幅CCD視覺圖像同時看清高溫熔敷金屬以及線結構光條紋,主動、被動視覺相結合的視覺傳感系統,實現了電弧增材製造熔敷道尺寸的無滯後視覺傳感,解決了現有的電弧增材製造熔敷道寬度和高度同時檢測的視覺傳感器的滯後問題。該檢測裝置包括分區減光片、CCD攝像機、一個線結構光發射器以及鏡頭和濾光片等。分區減光的方法,使減光片的不同區域具有不同的光線透過率,從而控制熔池區域的進光量低於結構光條紋區域的進光量,使分區減光之後熔敷金屬光譜輻射強度與線結構光光強水平相當,在CCD寬容度範圍之內,即可將二者同時看清。
附圖說明
圖1是現有技術線結構光傳感器安裝位置與成像原理示意圖;
圖2是本發明所述用於電弧增材製造熔敷道尺寸無滯後實時檢測裝置的結構示意圖;
圖3是分區減光片B在透鏡一倍焦距之外時的光路圖;
圖4是採用本發明所述無滯後實時檢測裝置獲得的單道熔敷過程圖;
圖5是採用本發明所述無滯後實時檢測裝置獲得的多道搭接熔敷過程圖。
具體實施方式
具體實施方式一:下面結合圖2說明本實施方式,本實施方式所述用於電弧增材製造熔敷道尺寸無滯後實時檢測裝置,該裝置包括分區減光元件100、線結構光發生器101、濾光片102、CCD攝像機108和鏡頭109;
鏡頭109安裝在CCD攝像機108的成像靶面107的前端,鏡頭109內部的前端安裝有濾光片102,線結構光發生器101發射的雷射條紋103投射至熔池104後方,且雷射條紋103與熔池104之間存在距離,焊槍106垂直設置在熔池104的正上方,焊槍106產生的電弧105位於熔池104的上端;
CCD攝像機108的成像靶面107與鏡頭109之間安裝有分區減光元件100。
本實施方式中,分區減光元件100能夠控制熔池104的進光量低於雷射條紋103的進光量,使分區減光後熔敷金屬光譜輻射強度與雷射條紋103光強水平相當,在CCD攝像機108寬容度範圍之內,將二者同時看清。
具體實施方式二:下面結合圖2說明本實施方式,本實施方式對實施方式一作進一步說明,分區減光元件100採用不同大小、不同光線透過率的減光片組成。
本實施方式中,分區減光元件100的不同區域具有不同的光線透過率,因此,焊槍106產生的電弧105、熔池104和線結構光發生器101投射到熔敷道上的雷射條紋103都能在CCD攝像機108的成像靶面107上清晰地成像。
具體實施方式三:下面結合圖2說明本實施方式,本實施方式所述用於電弧增材製造熔敷道尺寸無滯後實時檢測裝置的實時檢測方法,該實時檢測方法能夠實現一幅CCD視覺圖像同時看清高溫熔敷金屬和雷射條紋103,實現電弧增材製造熔敷道尺寸的無滯後實時檢測,具體方法為:分區減光元件100控制熔池104的進光量低於雷射條紋103的進光量,使分區減光後熔敷金屬光譜輻射強度與雷射條紋103光強水平相同。
本發明中,在電弧增材製造中,四種光源按照平均亮度遞減排序,依次為:電弧弧光、熔敷金屬光譜輻射、線結構光、環境光源。為了在保證獲得足夠成形尺寸信息的前提下實現無滯後視覺傳感,需要CCD同時看清高溫熔敷金屬以及線結構光條紋,並濾除電弧弧光。濾除電弧弧光之後,熔敷金屬光譜輻射強度仍然明顯高於線結構光光強,而CCD寬容度有限,具體表現為:當高溫熔敷金屬輪廓清晰時,線結構光條紋因光強不足而無法成像,對應區域一片漆黑。在此基礎上調整減光片透過率以及光圈參數來增大進光量,則熔敷金屬區域呈現過度曝光,其邊界模糊,無法準確體現成形尺寸。所以,常規的減光方法無法滿足同時看清高溫熔敷金屬以及線結構光條紋的需求。本發明採用了分區減光的方法,使減光片的不同區域具有不同的光線透過率,從而控制熔池區域的進光量低於結構光條紋區域的進光量,使分區減光之後熔敷金屬光譜輻射強度與線結構光光強水平相當,在CCD寬容度範圍之內,即可將二者同時看清。
本發明也適用於電弧焊接的焊道尺寸無滯後實時檢測。
如圖3所示,當分區減光片B逐漸遠離透鏡L,移動到透鏡一倍焦距F以外之後,從物體表面任意一位置出發的光線只能經過減光片的局部區域,如果該區域光線透過率高,則像點明亮;如果該區域光線透過率低,則像點暗淡,達到了分區減光的效果。同時,分區減光片會在CCD靶面的成實像B′,如果減光片B位於景深之內,則B′為清晰像,如果減光片B位於景深之外,則B′為模糊像。無論是清晰像還是模糊像,其各個區域的明暗程度都取決於減光片對應部分的光線透過率。B′與被測物體的像I相疊加,使分區減光的效果再度增強。
本發明能夠實現一幅CCD視覺圖像同時看清高溫熔敷金屬以及線結構光條紋,如圖4和圖5所示。在所採集的圖像中,結構光條紋位於圖像下三分之一區域內,減光片在對應的1/3區域具有高透過率,其餘2/3區域具有低透過率,高溫熔池在此區域清晰成像。可以看出,採用該傳感系統,能夠清晰地獲得熔敷道的熔池寬度以及線結構光條紋形貌,因此這種視覺傳感方法結合了主動視覺傳感與被動視覺傳感的優勢,在保證獲得足夠成形尺寸信息的同時,實現了無滯後檢測,適用於電弧增材製造和電弧焊接的熔敷道尺寸實時測量。