一種車身後地板的製作方法
2023-06-09 04:52:57 1
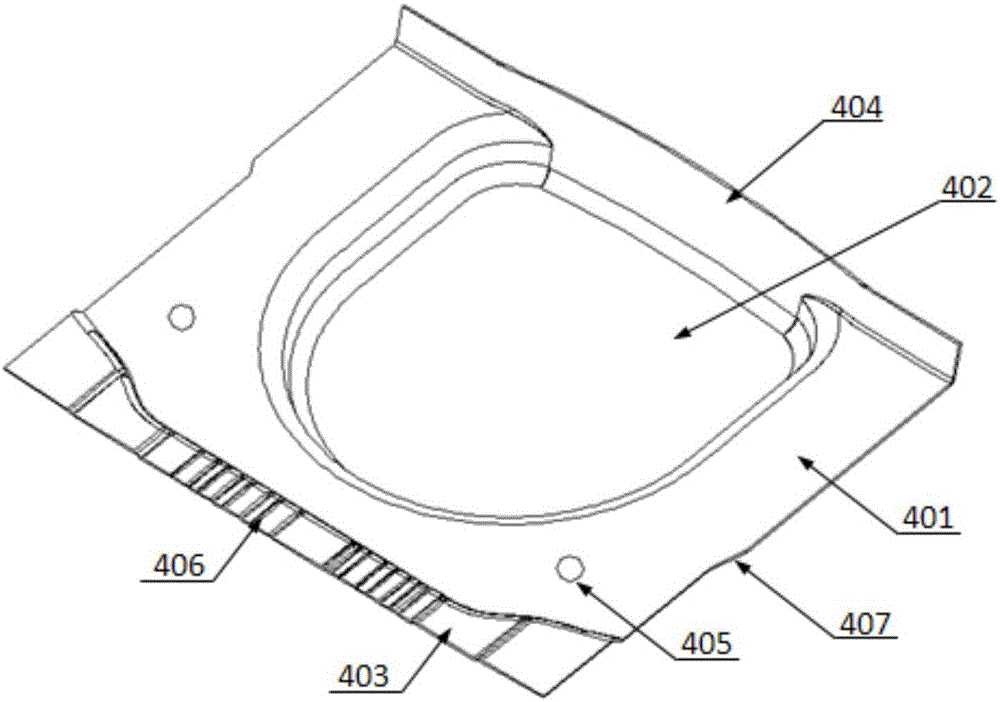
本發明涉及汽車車身結構,尤其是一種車身後地板,屬於汽車製造技術領域。
背景技術:
隨著汽車市場的競爭越來越激烈,顧客對於汽車安全性能、舒適度及輕便性的要求也越來越高。汽車車身後地板主要起著承載汽車後半部的自重、有效載荷以及備胎重量。汽車車身後地板的結構通常有後座地板及備胎存放地板兩部分,其主要工作狀況為:高模量、抗拉伸、抗彎曲、減震、吸能。
現有的車身後地板大多採用金屬材料製成,連接件較多且通過焊接連接,其存在彈性恢復不足及對行人容易造成傷害等弊端。
玻璃纖維增強熱塑性複合材料在汽車零部件中使用得越來越普遍,但在模壓或注塑過程中,玻纖會進入塑料製品的表面,使得製品表面變得很粗糙。另外,玻璃纖維增強熱塑性複合材料在遭受破壞時,易產生尖銳型斷口而造成二次傷害,以及易產生玻纖的粉碎性粉塵而對人體呼吸系統造成傷害的有害粉塵。
因而,設計一種採用新型材料製成的整體式車身後地板,對提高後地板的強度、抗衝擊韌性及最大程度地減輕車身的重量很有意義。
技術實現要素:
本發明目的在於解決現有技術中存在的上述問題,提供一種結構合理、一體化成型、高強度及高韌性的車身後地板。
為解決上述技術問題,本發明採用如下技術方案:
一種車身後地板,包括一體成型的後地板基材以及設置在後地板基材上的基準邊、備胎池、前插邊及後擋壁,
所述後地板基材採用混雜纖維複合材料,所述後地板基材包括一體成型的上表層、下表層及多層的芯層,所述芯層設置在上表層與下表層之間,
所述備胎池設置於後地板基材中部位置,所述備胎池的形狀為半圓形及方形的組合結構,所述後擋壁設置於備胎池上半圓形邊所對的側邊的頂部,所述基準邊設置於備胎池上除後擋壁所在側邊的另外三個側邊的頂邊上,所述基準邊的兩側邊設置傾斜結構,
所述前插邊設置於基準邊上靠近半圓形邊的側邊上,所述前插邊的底邊與基準邊的底邊在同一水平面上,前插邊的頂邊低於基準邊的頂邊且與基準邊組成臺階狀。
作為優選,所述基準邊上設置2至4個定位安裝孔,便於車身後地板的準確安裝。
作為優選,所述前插邊的上表面設置加強筋,所述每條加強筋的間隔為5~12mm,所述加強筋與前插邊接觸過度角曲率半徑為3~6mm,保證前插邊的高強度。
作為優選,所述備胎池與基準邊連接處為平滑的弧形結構,所述弧形結構的曲率半徑為6~10mm,保證車身後地板整體結構的強度及韌性。
作為優選,所述芯層的層數為2~6層,保證車身後地板整體結構的強度及韌性。
作為優選,所述混雜纖維複合材料的上表層及下表層的基體為熱塑性樹脂,上表層及下表層的增強相採用麻纖維或竹纖維。
作為優選,所述混雜纖維複合材料的芯層的基體為熱塑性樹脂,芯層的增強相採用連續長玻璃纖維或連續長碳纖維。
作為優選,所述熱塑性樹脂為改性聚丙烯PP或聚醯胺PA或聚對苯二甲酸丁二醇酯PBT或聚苯硫醚PPS。
作為優選,所述麻纖維及竹纖維的纖維平均長度大於6mm,彈性模量大於5000MPa,保證車身後地板整體結構的強度及韌性。
作為優選,所述連續長玻璃纖維為無鹼玻璃纖維,其抗拉強度為2800MPa,彈性模量為86000MPa,連續長碳纖維的彈性模量大於210 Gpa,抗拉強度大於3500 MPa。
作為優選,所述後地板基材通過真空輔助成型或熱壓成型。
本發明採用了上述技術方案,具有以下有益效果:
本車身後地板為一體式整體結構,且結構設置合理簡便,通過設置前插邊及定位安裝孔,便於車身後地板的準確插接安裝;另外,通過採用混雜纖維複合材料,克服了傳統金屬後地板重量重問題,進一步提高車身後地板的韌性,無脆性斷裂,能量吸收能力好,大部分材料可回收利用。
附圖說明
圖1為本發明車身後地板中後地板基材截面結構示意圖;
圖2為本發明車身後地板軸向結構示意圖;
圖3為本發明車身後地板俯視圖;
圖4為本發明車身後地板右視圖。
圖中:1-上表層,2-下表層,3-芯層,401-基準邊,402-備胎池,403-前插邊,404-後擋壁,405-定位安裝孔,406-加強筋,407-傾斜結構。
具體實施方式
為了更清楚地說明本發明實施例或現有技術中的技術方案,下面將對實施例或現有技術描述中所需要使用的附圖及技術方案作簡單地介紹,顯而易見地,下面描述中的附圖僅僅是本發明的一些實施例,對於本領域普通技術人員來講,在不付出創造性勞動的前提下,還可以根據這些附圖獲得其它的附圖。
實施方式1
如圖1至圖4所示,一種車身後地板,包括一體成型的後地板基材以及設置在後地板基材上的基準邊401、備胎池402、前插邊403及後擋壁404,所述後地板基材採用混雜纖維複合材料,所述後地板基材包括一體成型的上表層1、下表層2及多層的芯層3,所述芯層3設置在上表層1與下表層2之間,所述備胎池402設置於後地板基材中部位置,所述備胎池402的形狀為半圓形及方形的組合結構,所述後擋壁404設置於備胎池402上半圓形邊所對的側邊的頂部,所述基準邊401設置於備胎池402上除後擋壁404所在側邊的另外三個側邊的頂邊上,所述基準邊401的兩側邊設置傾斜結構,所述傾斜結構與車身側圍前柱邊緣相匹配,所述前插邊403設置於基準邊401上靠近半圓形邊的側邊上,所述前插邊403的底邊與基準邊401的底邊在同一水平面上,前插邊403的頂邊低於基準邊401的頂邊且與基準邊401組成臺階狀。
本較佳實施方式中,所述基準邊401上設置2個定位安裝孔405,所述前插邊403的上表面設置加強筋406,所述加強筋406的間隔分別為5mm、8mm、12mm,所述加強筋406與前插邊403接觸過度角曲率半徑為4mm,所述備胎池402與基準邊401連接處為平滑的弧形結構的曲率半徑為8mm,所述芯層3的層數為4層。
本較佳實施方式中,所述上表層1及下表層2的基體為改性聚丙烯PP,上表層1及下表層2的增強相採用麻纖維,麻纖維的纖維平均長度為10mm,彈性模量達到5500MPa;所述芯層3的基體為改性聚丙烯PP,芯層3的增強相採用連續長玻璃纖維,所述連續長玻璃纖維為無鹼玻璃纖維,其抗拉強度為2800MPa,彈性模量為86000MPa,連續長碳纖維的彈性模量大於210 Gpa,抗拉強度大於3500 MPa。
本較佳實施方式中,所述上表層1及下表層2的重量之和佔後地板基材重量百分比為15%~35%,所述芯層3的重量之和佔後地板基材重量百分比為30%~55%。
本較佳實施方式中,車身後地板的主要生產步驟為:先對後地板進行一體化整體設計;
然後,按照設計尺寸裁切好的各纖維預浸料在一些局部需要增強的部位進行鋪層增厚,所述後地板的邊緣與車身側圍前柱配合的邊緣處相匹配。
最後,將上述按設計鋪層好的纖維預製體進行浸膠,然後入模,再經過一體化熱壓成型,即得到麻纖維/玻璃纖維熱塑性複合材料車身後地板。
實施方式2
一種車身後地板,具有與實施方式1中相同的車身後地板結構,並且本較佳實施方式中,所述上表層1及下表層2的基體為聚醯胺PA,上表層1及下表層2的增強相採用竹纖維,所述芯層3的基體為聚醯胺PA,芯層3的增強相採用連續長碳纖維。
本較佳實施方式中,所述車身後地板的成型工藝為:將設計鋪層好的纖維預製體進行浸膠,然後入模,再經過一體化真空輔助成型(VARI),即得到竹纖維/碳纖維熱塑性複合材料的車身後地板。
以上所述,僅為本發明的具體實施方式,但本發明的保護範圍並不局限於此,任何不經過創造性勞動想到的變化或替換,都應涵蓋在本發明的保護範圍之內。因此,本發明的保護範圍應該以權利要求書所限定的保護範圍為準。