一種半導體雷射器陣列封裝結構的製作方法
2023-09-20 18:01:30 1
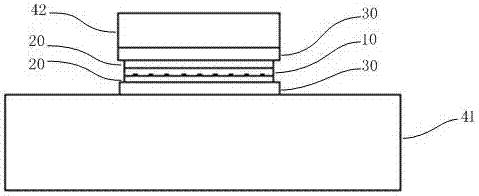
本申請屬於雷射技術領域,具體地說,涉及一種半導體雷射器陣列封裝結構。
背景技術:
半導體雷射器具有電光轉化效率高、波段範圍廣、壽命長、體積小、重量輕等優點,在軍事、航空、生物醫療、空間雷射通信等領域具有廣泛應用。隨著實際工程應用需求的發展,對半導體雷射器輸出功率水平要求越來越高,目前實現高功率的半導體雷射器通常採用兩種方式:一是採用光學透鏡器件將多個半導體雷射器晶片發生的光進行準直聚焦耦合到光纖輸出,受限於雷射晶片數量增多對光斑大小的影響,採用該方式可以實現百瓦級的雷射輸出,但對於更高功率的雷射輸出就變得尤為困難;另一種方法是對半導體雷射陣列結構的晶片進行光束整形聚焦,半導體雷射陣列晶片通常有19-25個發光單元構成,單個陣列晶片可實現50-75w的雷射輸出,半導體雷射陣列的垂直疊陣的應用使輸出功率達幾百上千瓦。半導體雷射器陣列結構的研究促進了半導體雷射器的應用。
在半導體雷射器陣列中電光轉化效率一般小於50%,在應用中將有50%的電功率將轉化成熱的形式耗散,該部分熱量的存在將導致雷射輸出功率的降低、輸出光譜的展寬。同時雷射陣列晶片和熱沉材料的熱膨脹係數的不匹配性將導致雷射陣列晶片發生形變,使輸出光發生彎曲形成smile效應,熱應力過大將導致陣列晶片與熱沉間的焊接層的開裂,甚至陣列晶片的斷裂等問題,嚴重影響半導體雷射器的可靠性及壽命。
技術實現要素:
有鑑於此,本申請所要解決的技術問題是提供了一種半導體雷射器陣列封裝結構,通過在雷射器晶片上下分別焊接焊片、過渡熱沉及散熱熱沉,保證半導體雷射器陣列的高效散熱的同時降低陣列晶片的熱形變。
為了解決上述技術問題,本申請公開了一種半導體雷射器陣列封裝結構,其包括雷射器陣列晶片;分別焊接於雷射器陣列晶片兩側的焊片;焊接於兩側焊片的過渡熱沉;支撐一側過渡熱沉的第一散熱熱沉;以及覆蓋另一側過渡熱沉的第二散熱熱沉;其中,第一散熱熱沉與第二散熱熱沉遠離雷射器陣列晶片的一端通過絕緣層相互連接。
根據本發明的一實施方式,其中上述雷射器陣列晶片兩側蒸鍍有ti-pt-au金屬層,ti-pt-au金屬層包括ti粘附層,pt阻擋層及au浸潤層。
根據本發明的一實施方式,其中上述焊片由3μm厚的預成型ausn合金焊片製成。
根據本發明的一實施方式,其中上述過渡熱沉由熱膨脹係數匹配的cuw製成,熱膨脹係數為6.5×10-6mm/℃。
根據本發明的一實施方式,其中上述過渡熱沉與第一散熱熱沉及第二散熱熱沉之間採用焊接熔點溫度低於ausn焊片溫度的焊料焊接。
根據本發明的一實施方式,其中上述第一散熱熱沉與第二散熱熱沉之間設置的絕緣層為ain電絕緣層。
根據本發明的一實施方式,其中上述雷射器陣列晶片正極面向第一散熱熱沉,負極面向第二散熱熱沉。
與現有技術相比,本申請可以獲得包括以下技術效果:
1)本發明提供的半導體雷射器陣列封裝結構,採用三明治結構將雷射器陣列晶片焊接在過渡熱沉、散熱熱沉之間,採用上下兩層過渡熱沉對半導體雷射器晶片的熱膨脹性進行匹配,降低了雷射陣列晶片工作時的熱應力,同時防止雷射陣列晶片在熱應力作用下產生發光面的彎曲變形。
2)上下兩塊散熱熱沉對雷射陣列晶片上下面進行散熱,提高雷射器熱容量的同時提高散熱能力,有效降低工作時雷射器陣列晶片上的結溫。
3)方便實用,效率較高。
當然,實施本申請的任一產品必不一定需要同時達到以上所述的所有技術效果。
附圖說明
此處所說明的附圖用來提供對本申請的進一步理解,構成本申請的一部分,本申請的示意性實施例及其說明用於解釋本申請,並不構成對本申請的不當限定。在附圖中:
圖1是本發明一實施方式的半導體雷射器陣列封裝結構立體圖;
圖2是本發明一實施方式的半導體雷射器陣列封裝結構側視圖。
附圖標記
雷射陣列晶片10,焊片20,過渡熱沉30,第一散熱熱沉41,第二散熱熱沉42,絕緣層50。
具體實施方式
以下將配合附圖及實施例來詳細說明本申請的實施方式,藉此對本申請如何應用技術手段來解決技術問題並達成技術功效的實現過程能充分理解並據以實施。
請一併參考圖1與圖2,圖1是本發明一實施方式的半導體雷射器陣列封裝結構立體圖;圖2是本發明一實施方式的半導體雷射器陣列封裝結構側視圖。如圖所示,一種半導體雷射器陣列封裝結構包括雷射器陣列晶片10;分別焊接於雷射器陣列晶片10兩側的焊片20;焊接於兩側焊片20的過渡熱沉30;支撐一側過渡熱沉30的第一散熱熱沉41;以及覆蓋另一側過渡熱沉30的第二散熱熱沉42;其中,第一散熱熱沉41與第二散熱熱沉42遠離雷射器陣列晶片10的一端通過絕緣層50相互連接。在本發明一實施方式中,焊片20藉以連接過渡熱沉30與雷射器陣列晶片10,提高雷射器陣列晶片10的焊接強度。第一散熱熱沉41與第二散熱熱沉42保證散熱,防止雷射器陣列晶片10的形變,提高穩定性。
雷射器陣列晶片10上下兩面採用真空蒸鍍方式鍍上厚度為微米量級的ti-pt-au金屬層,ti-pt-au金屬層包括ti粘附層,pt阻擋層及au浸潤層。膜層中ti膜層作為粘附層,利於其他金屬膜層蒸鍍時的粘附,pt膜層作為阻擋層可以防止在晶片焊接時焊料融化時對晶片發光面的汙染,au膜層作為浸潤層提高膜層的穩定性。蒸鍍完的雷射器陣列晶片10採用正極面朝下的方式焊接在過渡熱沉30,即雷射器陣列晶片10正極面向第一散熱熱沉41,負極面向第二散熱熱沉42,實現工作需求,有利於雷射器陣列晶片10產生的熱量的耗散,提高使用過程中的穩定性。
在本發明一實施方式中,焊片20採用3μm厚的預成型ausn合金焊片,具有較高的熱導率和高強度,不易發生電遷移或熱遷移,且在溫度循環時不會發生疲勞斷裂,可以提高雷射陣列晶片10的焊接強度。
值得一提的是,本發明的過渡熱沉30由熱膨脹係數匹配的cuw製成,熱膨脹係數為6.5×10-6mm/℃,雷射器陣列晶片10為gaas材料熱膨脹係數為5.9×10-6mm/℃。多次試驗,保證過渡熱沉30及雷射器陣列晶片10隨溫度變化產生的長度變化足夠穩定,保證使用過程中的數據準確性。同時,在雷射器陣列晶片10上下兩面上各設置有cuw材料的過渡熱沉30,保證熱的作用下雷射器陣列晶片10的形變一致,避免發光面的彎曲,降低smile效應(大功率半導體雷射器列陣在工作時,從雷射器到熱沉溫度梯度很大,由於lda襯底材料與熱沉材料線性熱膨脹係數不匹配,從而導致熱應力的產生。熱應力引起lda中各個發光單元在垂直於p-n結方向發生位移,再加上垂直於p-n結方向發光尺寸只有約1μm;所以較小的位移對發光產生較大影響,使列陣中各個發光單元不在一條直線上,從而導致lda整體發光彎曲,這種現象被稱為smile效應或稱各發射腔的近場非線性效應),提高雷射器輸出功率的穩定性。
此外,過渡熱沉30與第一散熱熱沉41及第二散熱熱沉42之間採用焊接熔點溫度低於ausn焊片溫度的焊料焊接。在焊接時不會影響雷射陣列晶片10的焊接質量,過渡熱沉30上下兩面設置的第一散熱熱沉41及第二散熱熱沉42有效增大雷射器的熱容量,有利於雷射器陣列晶片10的散熱。第一散熱熱沉41和第二散熱熱沉42分別作為雷射器陣列晶片10的正、負供電電極,兩個散熱熱沉接觸部分,設置有電絕緣層50,選取aln材料作為電絕緣層50,其熱膨脹係數4.5×10-6mm/℃,和雷射器陣列晶片10相差不大,保證在熱的作用下熱形變的匹配性,提高整個雷射器的熱穩定性。
上述說明示出並描述了本申請的若干優選實施例,但如前所述,應當理解本申請並非局限於本文所披露的形式,不應看作是對其他實施例的排除,而可用於各種其他組合、修改和環境,並能夠在本文所述申請構想範圍內,通過上述教導或相關領域的技術或知識進行改動。而本領域人員所進行的改動和變化不脫離本申請的精神和範圍,則都應在本申請所附權利要求的保護範圍內。