一種汽車排氣管消音器的有限元建模方法與流程
2023-09-18 10:33:55 2
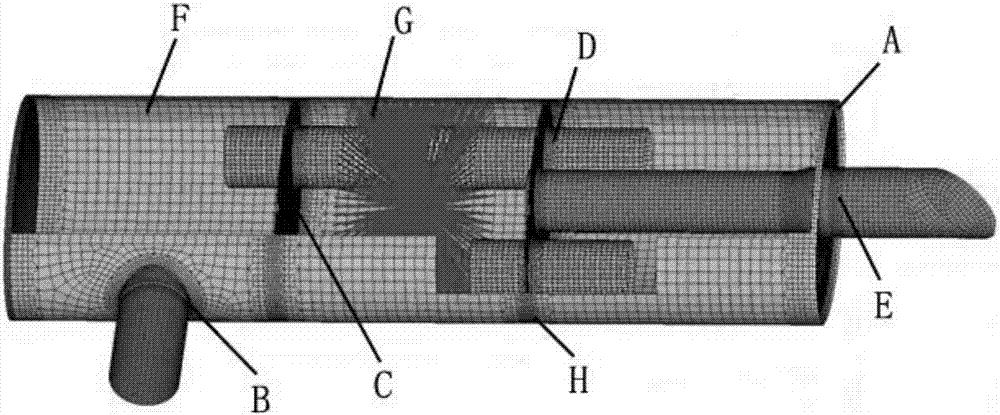
本發明屬於計算機輔助工程的技術領域,具體涉及一種汽車排氣管消音器的有限元建模方法。
背景技術:
汽車排氣管消音器主要由薄板材製造而成,用於降低車輛噪聲。在機械振動、氣流衝擊和熱作用下,為實現其聲學特性要求和空氣動力學要求,消音器必須有著良好的結構設計(含材料),滿足一定的強度、剛度和動力學(模態、響應譜分析等)要求。傳統的消音器結構設計主要採用設計人員的經驗和大量實驗相結合的方法,時間長、成本高。隨著計算機硬體的不斷發展以及軟體應用的日益成熟,可以採用計算機模擬仿真的方法來研究排氣管消音器的結構設計,或進行優化組合,以達到縮短設計周期、減少不必要的人力物力消耗的目的,實現消音器設計的現代化、精確化。
有限元方法是目前應用最成熟、最廣泛的一種數值計算方法,它利用數學近似的方法對真實物理系統(幾何和載荷工況)進行模擬。有限元求解問題的基本過程主要包括:前處理(建立有限元模型,簡稱建模)、有限元求解、計算結果的後處理三部分。其中,建模主要有幾何清理、網格劃分、屬性設置、加載及求解設置等內容。有限元模型的質量直接影響到求解時間及求解結果的準確性。
現有文獻中,針對消音器有限元結構分析模型的建立方法的研究少之又少。其中,《單腔擴張式消聲器的模態分析及結構改進》(文獻一)僅簡單提及了使用ansys三維實體單元solid45來建立模型;《hyperworks在消聲器模態計算上的應用》(文獻二)公開的建模方法如下:全部採用shell單元,定義厚度,對薄板進行網格劃分;用節點重合代替焊接;內管的圓孔用方孔代替。相對於文獻一中的方法,文獻二中的方法採用了shell單元來進行網格劃分,比利用六面體劃分網格獲得的網格數目少很多,而且網格質量更好,一定程度上提高了計算效率。
但是,上述兩種方法中:(1)都沒有公開具體的實施步驟與方法;(2)都沒有考慮焊縫,但是,忽略焊縫將不能分析焊縫自身及周邊的應力,且引起較大的質量誤差與質量分布誤差,不能真實地反應出消音器在振動、氣流衝擊與熱作用下的靜力學與動力學性能;(3)對於翻邊的處理,雖然文獻二中略有提及,但是其開始忽略、最後補劃的方法,將破壞已有的網格模型,增加了建模難度;(4)模型因忽略細小特徵與焊縫,必然導致總質量的差異,對計算結果的精度影響大,兩種方法都沒有考慮質量的校正。因此,需要一種建模精確、網格數量更少、網格質量更高的且容易實施的消音器的建模技術,以進行消音器的強度、剛度和模態的仿真分析。
技術實現要素:
本發明克服現有技術存在的不足,所要解決的技術問題為:提供一種建模精確、網格數量更少、網格質量更高且容易實施的汽車排氣管消音器的有限元建模方法。
為了解決上述技術問題,本發明採用的技術方案為:一種汽車排氣管消音器的有限元建模方法,所述汽車排氣管消音器包括:筒體、端蓋、內管、進氣管、隔板和出氣管,所述進氣管與所述筒體、所述出氣管與所述端蓋、所述內管與所述隔板、所述出氣管與所述隔板均通過焊接聯接,所述筒體本身、所述筒體與所述端蓋均通過翻邊聯接。
所述的有限元建模方法包括:對筒體的翻邊部分進行有限元建模,得到筒體翻邊的網格;對筒體與端蓋處的翻邊部分進行有限元建模,得到筒體與端蓋處翻邊的網格;對進氣管進行有限元建模,得到進氣管的網格;對內管進行有限元建模,得到內管的網格;對隔板進行有限元建模,得到隔板的網格;對出氣管進行有限元建模,得到出氣管的網格;對端蓋進行有限元建模,得到端蓋的網格;對進氣管與筒體焊接處進行有限元建模,得到進氣管與筒體焊接處的網格;對出氣管與端蓋焊接處進行有限元建模,得到出氣管與端蓋焊接處的網格;對內管與隔板焊接處進行有限元建模,得到內管與隔板焊接處的網格;對筒體與隔板焊接處進行有限元建模,得到筒體與隔板焊接處的網格;對筒體進行有限元建模,得到筒體的網格;以及為上述網格創建材料和屬性,並將所創建的材料和屬性分別賦給相應的網格;增加質量點,建立剛性單元,對汽車排氣管消音器整體進行質量校正。
優選地,所述對進氣管與筒體焊接處進行有限元建模,具體包括:建立整圈四面體單元、六面體單元,並與進氣管、筒體接觸處的面網格節點重合;所述對出氣管與端蓋焊接處進行有限元建模,具體包括:建立整圈四面體單元、六面體單元,並與出氣管、端蓋接觸處的面網格節點重合;所述對內管與隔板焊接處進行有限元建模,具體包括:沿圓周建立整圈的四面體單元、六面體單元,單元節點與內管、隔板接觸處的面網格節點重合;所述對筒體與隔板焊接處進行有限元建模,具體包括:沿筒體圓周建立離散的四面體單元,表示點焊,單元節點與筒體、隔板接觸處的面網格節點重合。
優選地,所述對筒體的翻邊部分進行有限元建模,具體包括:抽取翻邊兩部分的中面,刪除翻邊處摺疊部分面,用平面光滑填充缺口,代替此處翻邊,劃分填充面的網格;所述對筒體與端蓋處的翻邊部分進行有限元建模,具體包括:抽取端蓋的中面,刪除翻邊處摺疊部分面,軸向拉伸筒體中面,代替此處翻邊,劃分拉伸面的網格。
優選地,所述對進氣管進行有限元建模,具體包括:抽取進氣管的中面,在焊接處進行切割,劃分焊接處的面網格;繼續切割,劃分過渡網格;最後劃分餘下部分網格;所述對內管進行有限元建模,具體包括:抽取內管的中面,在與隔板的焊接處進行切割,劃分焊接處內管的面網格;劃分餘下部分網格;均勻刪除單個網格形成內管上的小孔;所述對出氣管進行有限元建模,具體包括:抽取出氣管的中面,在焊接處進行切割,劃分焊接處的面網格;繼續切割,劃分過渡網格;最後劃分餘下部分網格;所述對隔板進行有限元建模,具體包括:抽取隔板的中面,在焊接處進行切割,劃分焊接處的面網格;最後劃分餘下部分網格;所述對端蓋進行有限元建模,具體包括:抽取端蓋的中面,劃分面網格;在與翻邊接觸處節點對應重合;所述對筒體進行有限元建模,具體包括:劃分焊接處的面網格;劃分翻邊處的面網格,劃分過渡網格;最後劃分餘下部分網格。
優選地,所述增加質量點,建立剛性單元,對汽車排氣管消音器整體進行質量校正,具體包括:測量現有網格模型的質量,與實際幾何模型質量相比,增加質量點並賦於缺少的質量,並與筒體部分節點建立一維剛性單元。
優選地,所述為上述網格創建材料和屬性,具體包括:指定各部分的厚度、材料與單元類型。
本發明與現有技術相比具有以下有益效果:
1、本發明在建模初期即考慮翻邊,而不是如現有技術中一樣開始時忽略、最後發現質量問題、再增加翻邊,避免了對已有模型的修改與破壞,降低了建模難度,節省了建模時間;
而且,本發明準確建立了焊縫單元,可分析焊縫自身及周邊的應力,使得消音器的質量分布與真實情況逼近,避免較大的質量差異,可真實地反應出消音器的力學性能;
此外,本發明在建模的最後進行質量校正,確保所建有限元模型與實際幾何質量相等,避免了質量和剛度對計算結果的影響。
2、本發明全部採用四邊形的面網格與四面體、六面體的體網格,無三角形網格,網格質量大幅提高;
而且,本發明在絕大多數面均採用了網格過渡技術,而僅在細小特徵與關注部位採用小尺寸網格,從而大幅減少網格數量,提高了後繼的計算速度。
附圖說明
下面結合附圖對本發明做進一步詳細的說明;
圖1為本發明實施例提供的一種現有的汽車排氣管消音器的幾何模型;
圖2為根據本發明實施例提供的一種汽車排氣管消音器的有限元建模方法建立的有限元模型;
圖3為圖2中a的放大圖;
圖4為圖2中b的放大圖;
圖5為圖2中c的放大圖;
圖6為圖2中d的放大圖;
圖7為圖2中e的放大圖;
圖中:101為筒體,102為端蓋,103為內管,104為進氣管,105為隔板,106為出氣管。
具體實施方式
為使本發明實施例的目的、技術方案和優點更加清楚,下面將結合本發明實施例中的附圖,對本發明實施例中的技術方案進行清楚、完整地描述,顯然,所描述的實施例是本發明的一部分實施例,而不是全部的實施例;基於本發明中的實施例,本領域普通技術人員在沒有作出創造性勞動前提下所獲得的所有其他實施例,都屬於本發明保護的範圍。
一種汽車排氣管消音器的有限元建模方法,所述汽車排氣管消音器的幾何模型如圖1所示,可包括:筒體101、端蓋102、內管103、進氣管104、隔板105和出氣管106,所述進氣管104與所述筒體101、所述出氣管106與所述端蓋102、所述內管103與所述隔板105、所述出氣管106與所述隔板105均通過焊接聯接,所述筒體101本身、所述筒體101與所述端蓋102均通過翻邊聯接。
所述的有限元建模方法包括:
對筒體101的翻邊部分進行有限元建模,得到筒體101翻邊的網格。
對筒體101與端蓋102處的翻邊部分進行有限元建模,得到筒體101與端蓋102處翻邊的網格。
對進氣管104進行有限元建模,得到進氣管104的網格。
對內管103進行有限元建模,得到內管103的網格。
對隔板105進行有限元建模,得到隔板105的網格。
對出氣管106進行有限元建模,得到出氣管106的網格。
對端蓋102進行有限元建模,得到端蓋102的網格。
對進氣管104與筒體101焊接處進行有限元建模,得到進氣管104與筒體101焊接處的網格。
對出氣管106與端蓋102焊接處進行有限元建模,得到出氣管106與端蓋102焊接處的網格。
對內管103與隔板105焊接處進行有限元建模,得到內管103與隔板105焊接處的網格。
對筒體101與隔板105焊接處進行有限元建模,得到筒體101與隔板105焊接處的網格。
對筒體101進行有限元建模,得到筒體101的網格。
以及:
為上述網格創建材料和屬性,並將所創建的材料和屬性分別賦給相應的網格。
增加質量點,建立剛性單元,對汽車排氣管消音器整體進行質量校正。
具體地,所述對進氣管104與筒體101焊接處進行有限元建模,具體可包括:建立整圈四面體單元、六面體單元,並與進氣管104、筒體101接觸處的面網格節點重合。
所述對出氣管106與端蓋102焊接處進行有限元建模,具體可包括:建立整圈四面體單元、六面體單元,並與出氣管106、端蓋102接觸處的面網格節點重合。
所述對內管103與隔板105焊接處進行有限元建模,具體可包括:沿圓周建立整圈的四面體單元、六面體單元,單元節點與內管103、隔板105接觸處的面網格節點重合。
所述對筒體101與隔板105焊接處進行有限元建模,具體可包括:沿筒體101圓周建立離散的四面體單元,表示點焊,單元節點與筒體101、隔板105接觸處的面網格節點重合。
具體地,所述對筒體101的翻邊部分進行有限元建模,具體可包括:抽取翻邊兩部分的中面,刪除翻邊處摺疊部分面,用平面光滑填充缺口,代替此處翻邊,劃分填充面的網格。
所述對筒體101與端蓋102處的翻邊部分進行有限元建模,具體包括:抽取端蓋102的中面,刪除翻邊處摺疊部分面,軸向拉伸筒體101中面,代替此處翻邊,劃分拉伸面的網格。
具體地,所述對進氣管104進行有限元建模,具體可包括:抽取進氣管104的中面,在焊接處進行切割,劃分焊接處的面網格;繼續切割,劃分過渡網格;最後劃分餘下部分網格。
所述對內管103進行有限元建模,具體可包括:抽取內管103的中面,在與隔板105的焊接處進行切割,劃分焊接處內管103的面網格;劃分餘下部分網格;均勻刪除單個網格形成內管上的小孔。
所述對出氣管106進行有限元建模,具體可包括:抽取出氣管106的中面,在焊接處進行切割,劃分焊接處的面網格;繼續切割,劃分過渡網格;最後劃分餘下部分網格。
所述對隔板105進行有限元建模,具體可包括:抽取隔板105的中面,在焊接處進行切割,劃分焊接處的面網格;最後劃分餘下部分網格。
所述對端蓋102進行有限元建模,具體可包括:抽取端蓋102的中面,劃分面網格;在與翻邊接觸處節點對應重合。
所述對筒體101進行有限元建模,具體可包括:劃分焊接處的面網格;劃分翻邊處的面網格,劃分過渡網格;最後劃分餘下部分網格。
具體地,所述增加質量點,建立剛性單元,對汽車排氣管消音器整體進行質量校正,具體可包括:測量現有網格模型的質量,與實際幾何模型質量相比,增加質量點並賦於缺少的質量,並與筒體101部分節點建立一維剛性單元。
具體地,所述為上述網格創建材料和屬性,具體可包括:指定各部分的厚度、材料與單元類型。
下面以圖1中所示的幾何模型為例,對本發明中的方法做更加仔細的說明:設所有板材厚度均為2mm,材料相同是q235;焊縫材料用不鏽鋼304;消音器總質量8kg。具體建模方法如下:
第一步:筒體翻邊建模包括:
創建新的組件,命名為筒體翻邊,用以存放筒體翻邊的網格;
抽取翻邊兩部分的中面,刪除翻邊處摺疊部分面,用平面光滑填充以代替翻邊;
劃分填充面的網格;
翻邊的材料與屬性定義:根據設計狀態為筒體翻邊創建材料和屬性,並將所創建的材料和屬性賦給筒體翻邊。本實施例中的筒體材料是q235,厚度是2mm,故翻邊厚度設為4×2=8mm。根據這些信息為筒體創建材料和屬性,並賦給本步驟創建的筒體翻邊,單元類型為二維單元。
第二步:筒體與端蓋處翻邊建模包括:
創建新的組件,命名為筒體端蓋翻邊,用以存放筒體端蓋翻邊的網格;
刪除筒體與端蓋翻邊處的摺疊部分面,分別軸向拉伸筒體中面,長度為實際長度,代替兩端翻邊;
劃分拉伸面的網格;
翻邊的材料與屬性定義:根據設計狀態為筒體與端蓋翻邊創建材料和屬性,並將所創建的材料和屬性賦給筒體與端蓋翻邊。本實施例中的筒體與端蓋的材料都是q235,翻邊厚度設為4×2=8mm。根據這些信息為筒體創建材料和屬性,並賦給本步驟創建的筒體與端蓋翻邊,單元類型為二維單元。
第三步:進氣管建模包括:
創建新的組件,命名為進氣管,用以存放進氣管的網格;
抽取進氣管的中面,在焊接處、網格過渡處分別進行切割;
劃分焊接處的面網格、過渡網格、餘下部分網格;
進氣管的材料與屬性定義:根據設計狀態為進氣管創建材料和屬性,並將所創建的材料和屬性賦給進氣管。本實施例中進氣管材料是q235,厚度是2mm。根據這些信息為進氣管創建材料和屬性,並賦給本步驟創建的進氣管,單元類型為二維單元。
第四步:內管建模包括:
創建新的組件,命名為內管,用以存放內管的網格;
抽取內管的中面,在與隔板的焊接處進行切割;
劃分焊接處內管的面網格;
劃分餘下部分網格;均勻刪除單個網格形成內管上的小孔;
內管的材料與屬性定義:根據設計狀態為內管創建材料和屬性,並將所創建的材料和屬性賦給內管。本實施例中內管材料是q235,厚度是2mm。根據這些信息為內管創建材料和屬性,並賦給本步驟創建的內管,單元類型為二維單元。
第五步:出氣管建模包括:
創建新的組件,命名為出氣管,用以存放出氣管的網格
抽取出氣管的中面,在焊接處進行切割,劃分焊接處的面網格;
繼續切割,劃分過渡網格;
最後劃分餘下部分網格;
出氣管的材料與屬性定義:根據設計狀態為出氣管創建材料和屬性,並將所創建的材料和屬性賦給出氣管。本實施例中出氣管材料是q235,厚度是2mm。根據這些信息為出氣管創建材料和屬性,並賦給本步驟創建的出氣管,單元類型為二維單元。
第六步:隔板建模包括:
創建新的組件,命名為隔板,用以存放隔板的網格
抽取隔板的中面,在焊接處進行切割,
劃分焊接處的面網格;
最後劃分餘下部分網格;
隔板的材料與屬性定義:根據設計狀態為隔板創建材料和屬性,並將所創建的材料和屬性賦給隔板。本實施例中隔板材料是q235,厚度是2mm。根據這些信息為隔板創建材料和屬性,並賦給本步驟創建的隔板,單元類型為二維單元。
第七步:對端蓋建模包括:
創建新的組件,命名為端蓋,用以存放端蓋的網格
抽取端蓋的中面,劃分面網格;在與翻邊接觸處節點對應重合;
端蓋的材料與屬性定義:根據設計狀態為端蓋創建材料和屬性,並將所創建的材料和屬性賦給端蓋。本案例中端蓋材料是q235,厚度是2mm。根據這些信息為端蓋創建材料和屬性,並賦給本步驟創建的端蓋,單元類型為二維單元。
第八步:進氣管與筒體焊接處建模包括:
創建新的組件,命名為焊縫,用以存放所有焊縫的網格;
沿進氣管圓周建立連續完整的四面體、六面體焊縫單元,單元尺寸2.5mm;
使四面體、六面體單元節點與進氣管、筒體接觸處的面網格節點重合。
第九步:出氣管與端蓋焊接處建模包括:
沿出氣管圓周建立連續完整的四面體、六面體焊縫單元,單元尺寸2.5mm;
使四面體、六面體單元節點與出氣管、端蓋接觸處的面網格節點重合。
第十步:內管與隔板焊接處建模包括:
沿內管圓周建立連續完整的四面體、六面體焊縫單元,單元尺寸2.5mm;
使四面體、六面體單元節點與內管、隔板接觸處的面網格節點重合。
第十一步:對筒體與隔板焊接處建模包括:
根據模型實際情況,沿圓周建立四面體焊縫單元,尺寸為2.5mm;
本實施例是圓周方向八處點焊,所以用離散的單元表示;每個焊縫用四個單元表示一處點焊10mm;
四面體單元節點與內管、隔板接觸處的面網格節點重合;
焊縫材料與屬性定義:根據設計狀態為所有焊縫創建材料和屬性,並將所創建的材料和屬性賦給所有的焊縫。本實施例中焊縫材料是不鏽鋼304。根據這些信息為焊縫創建材料和屬性,並賦給步驟八、九、十、十一所創建的焊縫,單元類型為三維單元。
第十二步:對筒體建模包括:
創建新的組件,命名為筒體,用以存放所有筒體的網格;
劃分焊接處的面網格;
劃分翻邊處的面網格;
劃分過渡網格;
最後劃分餘下部分網格;
筒體的材料與屬性定義:根據設計狀態為筒體創建材料和屬性,並將所創建的材料和屬性賦給筒體。本實施例中筒材料是q235,厚度是2mm。根據這些信息為筒體創建材料和屬性,並賦給本步驟創建的筒體,單元類型為二維單元。
第十三步:對排氣管整體質量的校正包括:
測量現有網格模型的質量為7.5kg,與實際幾何模型質量8kg相比,求得缺少質量為0.5kg;
在筒體中心位置,增加一個臨時節點作為質量點,並賦於缺少的質量0.5kg;
創建新的組件,命名為剛性單元,用以存放用於校正質量的網格;
以此臨時節點為獨立節點,中間筒體部分節點為從節點,建立一維剛性單元;
再次測量網格模型質量。
上述幾何中面的抽取與切割、網格劃分、質量點的添加、材料和屬性的定義並賦予,均可以採用現有成熟的商業化前處理軟體得以實現。
至此,消音器的有限元模型全部完成,如圖2所示,a為筒體與端蓋翻邊部分,b為進氣管與筒體焊縫部分,c為隔板與筒體焊縫部分,d為內管與隔板焊縫部分,e為出氣管與端蓋焊縫部分,f為筒體翻邊部分,g為質量校正部分,h為筒體網格過渡部分。通過邊界條件的設置、載荷的施加以及輸出的設置,經過有關有限元求解軟體的分析計算,可獲得消音器的剛度、強度、動力學性能,進而輔助排氣管設計工程師快速、準確地評估消音器的力學性能。
採用本發明的建模方式,能夠提供更精確的有限元模型,節省建模時間,提高網格質量,減少網格數量,從而提高計算求解速度,更能準確地模擬消音器的靜力學性能(剛度、強度)與動力學性能,為進一步優化改進提供更可靠的有限元分析支持。
最後應說明的是:以上各實施例僅用以說明本發明的技術方案,而非對其限制;儘管參照前述各實施例對本發明進行了詳細的說明,本領域的普通技術人員應當理解:其依然可以對前述各實施例所記載的技術方案進行修改,或者對其中部分或者全部技術特徵進行等同替換;而這些修改或者替換,並不使相應技術方案的本質脫離本發明各實施例技術方案的範圍。