分料器、分料噴射組件、氣化爐及合成氣生產方法與系統與流程
2023-04-30 19:46:51 2
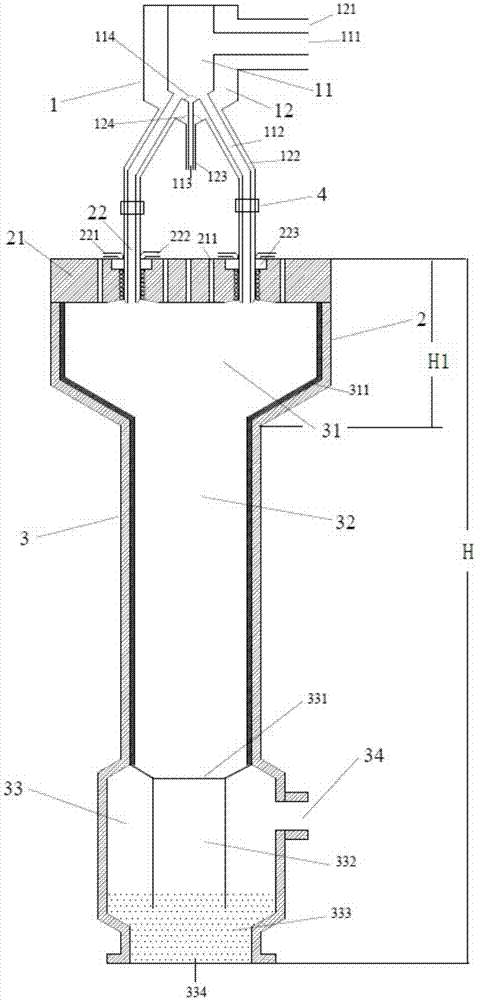
本發明涉及含碳燃料的氣化領域,特別地,涉及一種多噴嘴氣化爐裝置及其氣化工藝。
背景技術:
含碳燃料的氣化原理是將含碳燃料如煤炭等在破碎、乾燥後被輸送並通過噴嘴噴入高溫的氣化爐中,而後產生燃燒反應以生產合成氣。進一步地,還可往氣化爐中通入更多的水蒸氣以產生水煤氣反應,增加合成氣的產出。
本領域研究人員孜孜追求改進輸送裝置、分料機構、氣化爐裝置及其關聯部件、工藝流程等,防止輸料堵塞、分料不均、氣化反應不充分等,以提高碳轉化率低、降低設備與工藝成本、設備經久耐用。例如,在專利文獻CN1903998B中公開了一種氣化器注射器,其包括兩級泥流分離器和整合了冷卻系統的注射器面板。第一級分離器將主泥流分離成多個二級泥流,每個二級泥流又通過第二級分離器將單個二級泥流分離成多個三級泥流,三級泥流則通過泥流注射管以高壓泥流形式注入氣化爐的氣化室中。氣化劑則在高壓下以環形形狀的噴霧狀通過整合在注射器面板上的多個環狀衝擊孔衝擊在每一個高壓泥流上。
然而,這種採用圓錐體作為分離器將一級泥流分成多個二級泥流的氣化器注射器存在以下幾個方面的問題:
1)、物料在從上而下的輸送過程中,因物料自身重力及管道輸送「邊壁效應」的影響,物料通常難以理想性地從輸送管道中心通過,而是從管道一側集中通過,如此則圓錐體的分離器會喪失分料功能,使得物料僅從二級泥流的其中一個或幾個中流過,導致分料極不均勻;
2)、多個二級泥流通道之間存在許多死角,當物料濃度較高時非常容易導致堵塞通道;
3)、設置多個三級泥流通道固然能強化氣固之間的混合效果,但在煤氣化過程中,相對於C和氣化劑的燃燒反應,C與H2O、C與CO2的氣化反應程度最終決定了碳轉化率的高低,當反應後期H2O和CO2濃度達到平衡時,這兩個反應進行的程度主要由反應時間的長短來決定。圓柱體氣化室既不能提高氣化室H2O和CO2的濃度,也不能延長反應時間,因此嚴重影響碳轉化率的高低。
此外,專利文獻CN101892086A也公開了一種用於水煤漿氣化的水煤漿氣化爐,包括燃燒室和激冷室,其中燃燒室為類橢球狀的寬徑燃燒室殼體,至少有兩個水煤漿與氧氣三流道工藝噴嘴室對稱設置在燃燒室殼體的寬徑處且稍向下傾斜,至少有兩個水煤漿與氧氣三流道噴嘴稍向下傾斜且可拆卸地安裝於每一水煤漿與氧氣三流道工藝噴嘴室內,並且噴嘴開口朝向燃燒室內部,耐火磚襯於燃燒室殼體內,至少兩個氧氣噴嘴室,位於每一水煤漿與氧氣三流道工藝噴嘴室下方的圓周處並向上傾斜,至少兩個氧氣噴嘴向上傾斜且可拆卸地安裝於每一氧氣噴嘴室內,並且噴嘴開口朝向燃燒室內部。
這種類橢球狀寬徑的燃燒室存在的主要問題是對燃燒室的加工及安裝要求非常高,氣化強度受限,反應停留時間太長,氣化產率低,且氣化後的飛灰很容易腐蝕頂部,耐火磚很容易被侵蝕及脫落。
技術實現要素:
針對現有技術中的上述缺陷或不足,本發明提供了一種分料器、分料噴射組件和安裝有該分料噴射組件的氣化爐及合成氣生產方法與系統,以有效解決多個噴嘴存在的物料分配不均勻及堵料、碳轉化率低、氣化強度低、飛灰過濾成本高等問題。
為實現上述目的,根據本發明的第一方面,提供了一種分料器,該分料器包括外主管和內主管,外主管內的外主管料腔與內主管內的內主管料腔為彼此獨立且隔離的閉合腔室,內主管包括分別連通內主管料腔的內進料管和多個內分料管,外主管包括均連通外主管料腔的外進料管和多個外分料管,其中每個內分料管均伸入對應的外分料管內向外延伸以形成分料套管單元。
優選地,多個外分料管在外主管的底壁上呈環形等間隔排布並從底壁伸出,多個內分料管在內主管的底壁上也呈環形等間隔排布,每個內分料管從內主管的底壁同軸延伸至對應的外分料管內,從而形成環形排布的多個分料套管單元。
優選地,內分料管和外分料管的個數相同且不少於3個,更優選為3~24個。
優選地,外主管的底端和內主管的底部均為具有下頂點的圓錐體或半球體。
優選地,分料器還可相應包括內反吹管和/或外反吹管,外反吹管在外主管的底部的低點位置連通外主管料腔,連通內主管料腔的內反吹管從內主管的底部的低點位置延伸至外反吹管內並向外伸出。
優選地,分料器還包括內主管氣體分布器和/或外主管氣體分布器,內主管氣體分布器設置在內主管料腔的低點位置處以分散內反吹管的反吹進氣,外主管氣體分布器設置在外主管料腔的低點位置處以分散外反吹管的反吹進氣。
優選地,內主管和外主管的上埠封閉,外進料管從外主管的圓管壁沿切向伸出以能夠向外主管料腔中通入進料旋流;內進料管從內主管的圓管壁沿切向延伸至外進料管內並向外伸出,以能夠向內主管料腔中通入進料旋流。
優選地,在構成套管結構的內分料管和外分料管、構成套管結構的內反吹管和外反吹管以及構成套管結構的內進料管和外進料管中,套管結構中的內套管的伸出端與外套管的伸出端齊平或伸出於外套管的伸出端外。
根據本發明的第二方面,還提供了一種分料噴射組件,該分料噴射組件包括噴嘴布置面板、多個噴嘴單元和上述的分料器,噴嘴單元為套管結構並與對應的分料套管單元對接,多個噴嘴單元相互間隔且貫穿設置在噴嘴布置面板上。
優選地,噴嘴布置面板上設有貫通的螺紋安裝孔,噴嘴單元通過外管壁上設置的連接螺紋螺接於螺紋安裝孔。
優選地,多個噴嘴單元在噴嘴布置面板上呈環形等間隔布置。
優選地,該分料噴射組件還包括噴嘴冷卻系統,該噴嘴冷卻系統包括用於流入或流出冷卻介質的多個可拆裝三通管和在噴嘴布置面板中圍繞每個噴嘴單元設置的冷卻管單元,任意相鄰的兩個噴嘴單元的冷卻管單元之間通過可拆裝三通管相連。
優選地,噴嘴布置面板上還貫穿設置有多個水蒸氣入口,該多個水蒸氣入口環繞多個噴嘴單元排布。
根據本發明的第三方面,還提供了一種氣化爐,該氣化爐包括爐體和上述的分料噴射組件,該分料噴射組件的噴嘴布置面板安裝在爐體的頂部。
優選地,爐體包括由上至下的具有氣化室的氣化段、具有緩衝腔的緩衝段和具有激冷室的激冷段,氣化室通過緩衝腔與激冷室連通,噴嘴布置面板水平安裝在氣化段的頂蓋上,使得能夠通過噴嘴單元豎直向下地朝向氣化室噴入氣化原料和氣化劑。
優選地,氣化段的底端形成為縮口結構,該縮口結構傾斜向下地連接至緩衝段。
優選地,氣化室和緩衝腔均為圓筒形腔室,氣化室的高度不超過爐體的總高度的1/3,優選為1/6~1/3,緩衝腔的高度不超過爐體的總高度的1/3,且氣化室的內徑與緩衝腔的內徑之比不小於2,優選為2~10。
優選地,氣化室的內壁和緩衝腔的內壁上連續布置有水冷壁。
優選地,激冷室的周壁上形成有合成氣出口,激冷室的底部形成為渣池,激冷室的內徑與緩衝腔的內徑之比為1.2~1.5。
優選地,激冷室頂部與緩衝腔的連接處安裝有激冷環,該激冷環連接有伸入渣池的下降管。
優選地,氣化爐的反應溫度為1300℃~3000℃,優選為1500℃~2800℃,更優選為1900℃~2500℃。
根據本發明的第四方面,還提供了一種煤氣化生產合成氣的方法,方法包括:
氣化步驟:向氣化爐內輸入氣化原料和氣化劑,在氣化條件下,使氣化原料在氣化爐內發生氣化反應並產生粗合成氣和氣化殘渣;和
合成氣過濾步驟:對氣化殘渣進行乾燥處理,以形成多孔顆粒材料;使粗合成氣和多孔顆粒材料接觸以過濾粗合成氣中的飛灰。
優選地,氣化步驟還包括在氣化爐內對氣化殘渣和粗合成氣進行激冷,並將激冷後的氣化殘渣和粗合成氣排出氣化爐。
在粗合成氣和多孔顆粒材料接觸以過濾飛灰時,控制多孔顆粒材料的溫度為105~200℃,粒徑為0.1~15mm。
優選地,對氣化殘渣進行乾燥處理後,控制多孔顆粒材料的含水體積不大於多孔顆粒材料的總體積的50%,優選為0~30%。
優選地,在合成氣過濾步驟中,將乾燥後的多孔顆粒材料加入到移動床中,使粗合成氣在移動床中通過多孔顆粒材料而進行過濾。
優選地,該方法還包括:
合成淨化濾步驟:洗滌過濾後的粗合成氣以進一步除去飛灰。
優選地,在根據本發明的上述氣化爐中進行氣化反應。
根據本發明的第五方面,還提供了一種煤氣化生產合成氣的系統,該系統包括:
氣化原料破碎、乾燥和運輸系統,用於生產和輸送幹煤粉或水煤漿;
氣化爐,與氣化原料破碎、乾燥和運輸系統連通,在氣化爐中,幹煤粉或水煤漿在氣化劑的存在下發生氣化反應,生成粗合成氣和氣化殘渣;
排渣系統,與氣化爐相連通,用於將氣化殘渣排出氣化爐;
乾燥單元,與排渣系統相連通,至少部分的氣化殘渣在乾燥單元中被乾燥而形成為多孔顆粒材料;以及
過濾除灰系統,與乾燥單元和氣化爐相連通,在過濾除灰系統中,粗合成氣和多孔顆粒材料接觸以過濾粗合成氣中的飛灰。
優選地,過濾除灰系統包括移動床,粗合成氣在移動床中與多孔顆粒材料接觸以過濾飛灰。
優選地,氣化爐為根據本發明上述的氣化爐。
根據上述技術方案,在本發明的分料器中形成了內外兩路相互獨立的輸送通道,氣化原料和氣化劑能夠以流化態在內外輸送通道中通過,並通過多個分料套管單元進行分料。其中,可通過連接料腔底部的反吹管的反吹進氣,使得料腔內始終維持流化態,底部不產生沉積,以防止堵塞並使得分料高效、均勻。在氣化爐的頂部,通過環狀布置的多個頂置噴嘴及對接的均勻分料的分配器,可使得各噴嘴的噴料均勻,扁圓柱型氣化室及其底部縮口設計可增加反應時間,縮短停留時間,能有效提高碳轉化率和降低氣化爐投資成本。在氣化工藝中,通過氣化爐內激冷並乾燥後的氣化殘渣以吸附過濾同質的粗合成氣中的飛灰,可減少過濾成本,降低氣化設備總投資成本。
本發明的其他特徵和優點將在隨後的具體實施方式部分予以詳細說明。
附圖說明
附圖是用來提供對本發明的進一步理解,並且構成說明書的一部分,與下面的具體實施方式一起用於解釋本發明,但並不構成對本發明的限制。在附圖中:
圖1為相同試驗條件下單噴嘴與多噴嘴的爐體橫截面徑向均值速度分布對比圖;
圖2為根據本發明的優選實施方式的氣化爐的結構示意圖;
圖3為根據本發明的優選實施方式的分料器的結構原理圖;
圖4為圖3中的分料器的斷面圖,其中圖示了沿切向進料以形成旋流;
圖5為根據本發明的優選實施方式的噴嘴布置面板的俯視圖;
圖6為根據本發明的優選實施方式的氣化爐的氣化工藝的原理圖。
附圖標記說明
1 分料器 2 噴嘴裝置
3 爐體 4 連接短管
5 氣化原料破碎、乾燥和運輸系統 6 排渣系統
7 移動床 8 文丘裡洗滌設備
11 內主管 12 外主管
21 噴嘴布置面板 22 噴嘴單元
31 氣化室 32 緩衝腔
33 激冷室 34 合成氣出口
111 內主管 112 內分料管
113 內反吹管 114 內主管氣體分布器
121 外進料管 122 外分料管
123 外反吹管 124 外主管氣體分布器
211 水蒸氣入口 221 冷卻介質入口
222 冷卻介質出口 223 噴嘴單元固定面板
224 可拆裝三通管 311 水冷壁
331 激冷環 332 下降管
333 渣池 334 排渣口
H1 氣化室的高度 H 爐體的總高度
具體實施方式
以下結合附圖對本發明的具體實施方式進行詳細說明。應當理解的是,此處所描述的具體實施方式僅用於說明和解釋本發明,並不用於限制本發明。
在本發明中,在未作相反說明的情況下,使用的方位詞如「上、下、頂、底」通常是針對附圖所示的方向而言的或者是針對豎直、垂直或重力方向上而言的各部件相互位置關係描述用詞;「豎直方向」指的是圖示的紙面上下方向;「內、外」通常指的是相對於腔室而言的腔室內外或相對於圓心而言的徑向內外。
另外,本申請的申請人於2015年11月14日提交了中國專利申請No.201510740660.8,其作為參考而整體納入本申請中。
參見圖3,本發明首先提供了一種新型分料器,該分料器1包括外主管12和內主管11,外主管12內的外主管料腔與內主管11內的內主管料腔為彼此獨立且相互隔離的閉合腔室,內主管11包括分別連通內主管料腔的內進料管111和多個內分料管112,外主管12包括均連通外主管料腔的外進料管121和多個外分料管122,其中每個內分料管112均伸入對應的外分料管122內向外延伸以形成分料套管單元。
在此分料器中,通過外主管12和內主管11形成了內外兩路輸送通道,從而使得例如氣化原料和氣化劑等得以獨立輸送並通過多個分料套管單元進行獨立的均勻分料,互不影響。這種套管式分料器的結構新穎、緊湊,可根據輸送物料的形態、重量等對外主管12、內主管11及其進料管和分料管的管徑大小進行匹配設計,使之輸送物料在料腔內始終保持流化態,儘量不在輸送通道中產生任何物料沉積或堵塞等。
具體地,多個外分料管122在外主管12的底壁上優選地呈環形等間隔排布並從底壁伸出,多個內分料管112在內主管11的底壁上也相應地呈環形等間隔排布,每個內分料管112從內主管11的底壁同軸延伸至對應的外分料管122內。如圖3所示,其中的內分料管112和外分料管122的個數優選為相同,特別優選為分別是3~24個(根據工藝需要確定),從而形成環形排布的多個分料套管單元,使得結構對稱性強,分料均勻。在裝配時,底壁上可設置環形排布的多個分料孔,將各個分料管插接在相應分料孔上即可實現分料管的安裝。
其中,如圖4所示,外進料管121優選地從外主管12的圓管壁沿切向伸出以能夠向外主管料腔中通入進料旋流;內進料管111從內主管11的圓管壁沿切向延伸至外進料管121內並向外伸出,以能夠向內主管料腔中通入進料旋流。無論氣化原料或氣化劑均以流體形態輸送,沿切向進入料腔後,將沿料腔內壁環繞,形成進料旋流,從而充分流動,使得停留時間長,便於分料均勻。
料流在料腔中會由於自身重力而下落,因此底壁優選為傾斜向下,以便於料流進入各分料孔進行分料。在本實施方式中,外主管12的底壁(或底部)和內主管11的底壁(或底部)均優選為漏鬥形狀,即具有下頂點的圓錐壁(或圓錐體)形式。這樣,下沉至料腔底部的料流沿圓錐壁可方便地流入分料孔中。
然而帶有固體顆粒的料流可能在圓錐壁的下頂點(即低點位置)產生沉積。因此在本發明中,若內、外主管中輸送的物料存在固體顆粒,則分料器1還可相應地包括套管結構的內反吹管113和/或外反吹管123,外反吹管123在外主管12的底壁的低點位置連通外主管料腔,連通述內主管料腔的內反吹管113從內主管11的底壁的低點位置延伸至外反吹管123內並向外伸出。通過反吹管的反吹進氣,可向上揚起沉積的料流,使料腔內流體始終處於流化狀態,防止堵塞並保障物料分配均勻。當然本領域技術人員能夠理解的是,若內主管或外主管中只是輸送氣化劑,即不存在堵塞的情況,則無需設置相應的反吹管。
更優選地,分料器1還可包括內主管氣體分布器114和/或外主管氣體分布器124,內主管氣體分布器114設置在內主管料腔的低點位置處以分散內反吹管113的反吹進氣,外主管氣體分布器124設置在外主管料腔的低點位置處以分散外反吹管113的反吹進氣。這種氣體分布器可以是簡單結構的頂部圓弧面上具有各個氣孔的容腔殼體,通過設置氣體分布器可使得反吹管的進氣分散更均勻,且不會對料腔內的流場產生過大攪動。
參見圖3和圖4,內分料管112和外分料管122、內反吹管113和外反吹管123以及內進料管111和外進料管121均為構成套管結構的三組套管。在各組套管結構中,內套管的伸出端(即外端)與外套管的伸出端齊平或伸出於外套管的伸出端外,以便於內套管的外端與連接管的對接操作,並且內套管的進出料可不受外套管的影響。
在以上套管式分料管的基礎上,本發明還提供了一種分料噴射組件,該分料噴射組件包括噴嘴裝置2和上述的分料器1。噴嘴裝置2包括噴嘴布置面板21和安裝於其上的多個噴嘴單元22,噴嘴單元22同樣為套管結構,可通過連接短管4等與對應的分料套管單元對接,多個噴嘴單元22相互間隔且貫穿設置在噴嘴布置面板21上。這樣,從多個分料套管單元出來的分料料流通過相應的噴嘴單元22可豎直噴入氣化爐內。
同樣的,在多個分料套管單元呈環形布置時,與其對接的多個噴嘴單元22在噴嘴布置面板21上也呈環形等間隔布置。噴嘴單元22在噴嘴布置面板21上優選地呈豎直插入狀。其中,噴嘴單元22可通過各種合適方式安裝在噴嘴布置面板21上。在本實施方式中優選地採用螺接方式,即噴嘴布置面板21上設有貫通的螺紋安裝孔,噴嘴單元22通過外管壁上設置的連接螺紋螺接於螺紋安裝孔。這種螺接方式不僅方便拆卸、更換,還便於例如下述的冷卻管的布置與維護等。
為控制噴嘴單元22的溫度,延長使用壽命,分料噴射組件還可包括噴嘴冷卻系統。如圖5所示,該噴嘴冷卻系統包括用於流入或流出冷卻介質的多個可拆裝三通管224和在噴嘴布置面板21中圍繞每個噴嘴單元22設置的冷卻管單元,任意相鄰的兩個噴嘴單元22的冷卻管單元之間通過可拆裝三通管224相連。可拆裝三通管224的兩個埠分別連接相鄰的兩個冷卻管單元,另一個埠可作為冷卻介質入口221或冷卻介質出口222。優選地,冷卻介質入口221和冷卻介質出口222沿周向間隔排布,以使得各冷卻單元的冷卻介質流動均勻、合理。其中,冷卻管單元可鑲嵌在噴嘴布置面板21內並盤繞噴嘴單元22外,在噴嘴布置面板21的頂部通過噴嘴單元固定面板223固定,只對外留出冷卻介質入口221和冷卻介質出口222。
此外,噴嘴布置面板21上還可貫穿設置有多個水蒸氣入口211,該多個水蒸氣入口211環繞多個噴嘴單元22排布。水蒸氣入口211用於向氣化爐內噴入水蒸氣,以便實現水煤氣反應。在噴嘴布置面板21上設置的水蒸氣入口211的個數根據面板尺寸和工藝需要設定,例如優選為3-72個。
此外,本發明還提供了如圖2所示的氣化爐,該氣化爐包括爐體3和上述的分料噴射組件,該分料噴射組件的噴嘴布置面板21安裝在爐體3的頂部。
此處採用了頂置多噴嘴結構,這是由於氣化冷模實驗表明:頂置單噴嘴單噴嘴射流距離較長,而頂置多噴嘴射流距離相對較短;從分散效果來看,多噴嘴分散效果明顯好於單噴嘴。圖1展示了相同實驗條件下單噴嘴和多噴嘴橫截面徑向均值速度分布對比,從圖1中可以看出,單噴嘴在爐體內中心射流速度達近70m/s,且沿徑向位置的速度分布呈急劇下降趨勢,而頂置多噴嘴的速度分布表現較為平緩。根據高速攝像機也可追蹤拍攝相同條件下單噴嘴和多噴嘴的流場圖(未示出),可顯示單噴嘴時爐壁上顆粒濃度較大且高濃度面積較大,而多噴嘴僅在噴嘴附近顆粒濃度稍高,但遠不如單噴嘴濃度高,且多噴嘴高濃度面積遠小於單噴嘴,並且頂置多噴嘴會在氣化爐內的中心兩側形成兩個反向的漩渦,且漩渦尺度較小。由此說明,頂置多噴嘴存在向爐體兩側的小尺度返混,但爐體中心基本無返混。
因此,頂置多噴嘴具有噴射距離短、分散效果好及其在爐內流場呈現兩側返混的現象。試驗結果也證實對於頂置多噴嘴所需要的氣化空間相比單噴嘴小很多,可減少氣化室的佔用空間。當然,本發明也不限於採用上述的頂置噴嘴結構,也可以採用例如管殼式同軸射流結構的頂置噴嘴等;而所述的分料器也不限於採用上述的單級和單套管結構,也可以是多級分級和多套管分料結構等
本發明不僅採用了上述具有套管式分料管且頂置多噴嘴的分料噴射組件,還對爐體結構進行了優化設計。如圖2所示,爐體3包括由上至下的具有氣化室31的氣化段、具有緩衝腔32的緩衝段和具有激冷室33的激冷段,氣化室31通過緩衝腔32與激冷室33連通,噴嘴布置面板21水平安裝在氣化段的頂蓋上,使得能夠通過噴嘴單元22和水蒸氣入口211豎直向下地朝向氣化室31噴入氣化原料、氣化劑和水蒸氣,以便於產生氣化反應。本領域技術人員知曉的是,通過水蒸汽入口211通入更多的水蒸氣以增進水煤氣反應,可有效增加碳轉化率。燃燒反應和水煤氣反應均在氣化室31內完成,反應產物包括粗合成氣和氣化殘渣,通過緩衝腔32到達激冷室33,最後分別從其中的合成氣出口34和排渣口334排出。當然,本領域技術人員能夠理解的是,為防消耗後的水蒸汽補充不足,可通過此處的水蒸汽入口211補充,但並不限於此,水蒸汽也可以和氧氣一塊通過外管輸送到氣化爐中。
其中,緩衝段的設計目的是一方面考慮到氣化溫度過高,若在緩衝段內設置水冷壁有利於通過其中的合成氣降溫;其次,緩衝段與氣化室連通能適當增加氣化反應時間。
特別地,氣化段的底端形成為縮口結構,該縮口結構傾斜向下地連接至緩衝段。氣化室的這種縮口設計減少了氣化室空間,既能提高氣化反應溫度,也能使CO2、H2O及部分未反應的殘碳等物質觸碰底壁後回流至氣化室31繼續反應,可有效提高二次反應物CO2和H2O的濃度和反應停留時間,由此提高碳轉化率。通過本發明的氣化爐,碳轉化率可達99%以上,合成氣組成達90%以上,比氧耗約290Nm3/1000Nm3(CO+H2)。
由於氣化室的頂置多噴嘴具有氣固混合效果好、火焰短、溫度高等特點,因此相比現有氣化爐的氣化室而言,氣化室31的高度可以縮短,氣化室31的寬度可更寬,以更好地布置多個噴嘴,而縮口結構的設計有利於反應氣和未反應完全的氣化原料回流(返混)至高溫火焰處,以發生C與CO2的二次反應,提高碳轉化率。緩衝腔32的徑向尺寸縮短設計可縮短氣體停留時間,降低爐體尺寸和投資成本。
在本實施方式中,如圖2所示,氣化室31和緩衝腔32均優選為圓筒形腔室,氣化室31的高度H1不超過爐體3的總高度H的1/3,優選為1/6~1/3,且氣化室31的內徑與緩衝腔32的內徑之比不小於2,根據實際應用優選為2~10。這樣形成的倒「工」字形爐體設計降低了氣化爐的爐體體積和投資成本。頂置平行多噴嘴布置和倒「工」字形爐體設計還強化了氣固之間的混合。另外,氣化室31的內壁和緩衝腔32的內壁上還連續布置有水冷壁311,以防護爐體內壁。
特別地,激冷室33頂部與緩衝腔32的連接處還安裝有激冷環331,該激冷環331連接有朝向渣池333延伸的下降管332。激冷環331的設置有利於激冷後的合成氣的後續處理(如除塵、脫硫淨化等)。經過緩衝腔32到達激冷室33的反應產物中,粗合成氣經激冷環331激冷後速度下降、溫度降低,從下降管332進入渣池333水中以便除去更多的飛灰,最後從激冷室33的周壁上形成的合成氣出口34排出,去往合成氣處理單元。產生的熔渣(即氣化殘渣)在水冷壁311上可形成熔渣層以保護水冷壁311,多餘的熔渣通常沿水冷壁311掉入激冷室33的底部的渣池333中,並從排渣口334排出。
使用本發明上述氣化爐,其氣化工藝的原理如圖6所示,該工藝包括氣化反應步驟,該氣化反應步驟包括通過分料器的外進料管121輸入氣化原料和氣化劑中的一者,通過內進料管111輸入氣化原料和氣化劑中的另一者,並且可通過噴嘴布置面板21上的水蒸氣入口211補充水蒸氣,使氣化原料在氣化爐內於氣化條件下發生氣化反應,產生粗合成氣和氣化殘渣以向外排出。
其中,氣化室31內的氣化反應溫度優選為保持在1300℃~3000℃之間,更優選為1500℃~2800℃之間,甚至1900℃~2500℃之間,以順利完成燃燒反應和水煤氣變換反應(CO+H2O→CO2+H2,C+H2O→CO+H2)。相較於現有技術的氣化爐,本發明中的氣化爐的氣化溫度可提高到2800℃以上,只要水冷壁和激冷換熱足夠即可保障對後續工藝參數,如合成氣出口溫度、氣化殘渣溫度等影響甚小;氣化溫度提高後,結合頂置多噴嘴的氣固混合效果,氣化反應更快,氣化室的停留時間可少於0.5s甚至更短,緩衝段的停留時間同樣少於0.5s甚至更短。
特別地,氣化工藝還可包括合成氣過濾步驟,包括:
在氣化反應步驟中產生的氣化殘渣進行乾燥處理,以形成多孔顆粒材料;使粗合成氣和多孔顆粒材料接觸以過濾粗合成氣中的飛灰;
將乾燥後溫度為105~200℃,粒徑為0.1~15mm的多孔顆粒材料作為過濾介質,使激冷後300℃左右的粗合成氣通過乾燥後的多孔顆粒材料以過濾其中的飛灰。
其中,採用氣化殘渣作為過濾介質去除合成氣中的飛灰,能很大程度上降低氣化工藝的投資成本。由於氣化殘渣和飛灰的物質成分基本相似,且被激冷後的氣化殘渣的孔隙度較高,因此飛灰極易吸附與氣化殘渣上,除灰效果較好。其中,乾燥後的氣化殘渣的含水體積應不大於總體積的50%,優選為0~30%,以具有對飛灰較好吸附效果。
具體地,乾燥後的氣化殘渣可加入移動床7中,粗合成氣在移動床7中通過乾燥後的氣化殘渣(即多孔顆粒材料)進行過濾。而後,氣化工藝還包括將過濾後200℃左右的粗合成氣通過文丘裡洗滌設備8進行洗滌的合成氣淨化步驟,從而得到淨化後的合成氣。
參見圖6可知,採用上述方法的煤氣化生產合成氣的系統包括:
氣化原料破碎、乾燥和運輸系統5,用於生產和輸送幹煤粉或水煤漿;
氣化爐,與氣化原料破碎、乾燥和運輸系統5連通,在氣化爐中,幹煤粉或水煤漿在氣化劑的存在下發生氣化反應,生成粗合成氣和氣化殘渣;
排渣系統,與氣化爐相連通,用於將氣化殘渣排出氣化爐;
乾燥單元,與排渣系統相連通,至少部分的氣化殘渣在乾燥單元中被乾燥而形成為多孔顆粒材料;以及
過濾除灰系統,與乾燥單元和氣化爐相連通,在過濾除灰系統中,粗合成氣和多孔顆粒材料接觸以過濾粗合成氣中的飛灰。
其中優選地在移動床7中高效地過濾粗合成氣。
其中,總的工藝過程是:氣化原料經過氣化原料破碎、乾燥和運輸系統5進入氣化爐的爐體3後,在溫度為1500~2500℃的氣化室31內發生氣化反應,部分氣化殘渣從爐體底部的排渣系統6排出,另一部分氣化殘渣經乾燥後溫度約為100℃,進入移動床除灰系統,氣化後的粗合成氣經過移動床除灰系統除灰後,再經文丘裡洗滌設備8和合成氣淨化後成為乾淨的合成氣產品。
與現有技術相比,本發明所提供的氣化爐及其氣化工藝至少具有以下有益的技術效果:
a)、套管式分料器可將氣化劑和氣化原料分離成多個通道,其進料口採用切線旋流進料,且其底部設置有分布式反吹孔以使物料始終保持流化狀態,這樣既能保障物料分配的均勻性,也能防止管道堵塞;
b)、每個通道形成的噴嘴都獨立存在,其噴嘴上下均採用內外螺紋方式連接,噴嘴冷卻水入口和出口均採用可拆卸三通連接,每個噴嘴安裝和拆卸方便,操作簡單;
c)、頂置平行多噴嘴布置和類似倒「工」字形的爐體設計強化了氣固之間的混合,且爐體氣化室的縮口設計減少了氣化室空間,既能提高氣化反應溫度,也能能使CO2、H2O及部分未反應的殘碳等物質回流至氣化室繼續反應,在一定程度上提高了反應停留時間和反應物濃度,從而提高碳轉化率。此外,倒「工」字形爐體設計降低了氣化爐爐體體積和其投資成本。
d)、採用氣化殘渣作為過濾介質除去合成氣中的飛灰,很大程度上降低了氣化工藝的投資成本。由於氣化殘渣和飛灰的物質成分基本相似,且激冷過的殘渣孔隙度較高,因此飛灰極易吸附與氣化殘渣上,除灰效果較好。
以上結合附圖詳細描述了本發明的優選實施方式,但是,本發明並不限於上述實施方式中的具體細節,在本發明的技術構思範圍內,可以對本發明的技術方案進行各種簡單變型,例如套管式分料器中的外主管或內主管的底壁形狀並不限於具有下頂點的圓錐形,也可以是壁面傾斜向下的半球體等;分料套管單元與噴嘴單元之間的連接方式也不限於圖示的套管對接方式,還可以採用旁通方式連接;爐體的頂部也不限於是圓筒形,還可以是半球形等;這些簡單變型均落入本發明的保護範圍內。
上述具體實施方式中所描述的各個具體技術特徵,在不矛盾的情況下,可以通過任何合適的方式進行組合,為了避免不必要的重複,本發明對各種可能的組合方式不再另行說明。
此外,本發明的各種不同的實施方式之間也可以進行任意組合,只要其不違背本發明的思想,其同樣應當視為本發明所公開的內容。