絕緣體上矽晶圓的製造方法與流程
2023-11-09 19:15:13 1
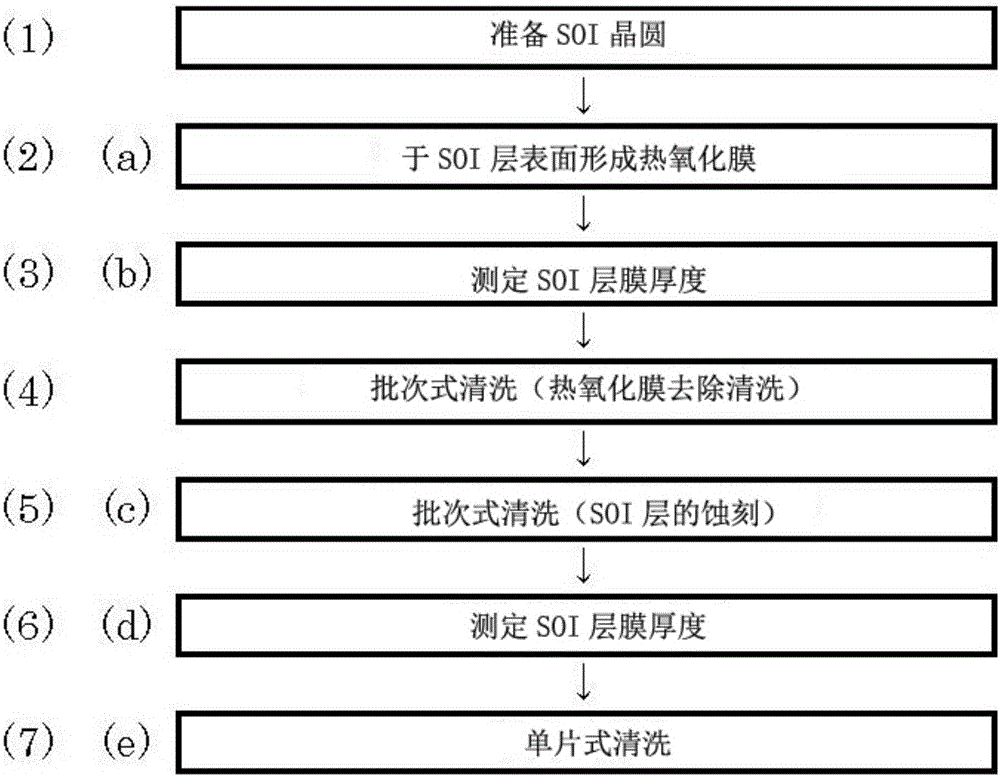
本發明涉及絕緣體上矽(Silicon-On-Insulator,以下簡稱為SOI)晶圓的製造方法,特別是被稱為FDSOI(Fully Depleted Silicon-On-Insulator:全空乏SOI),要求有極高SOI層膜厚的均一性的SOI晶圓的製造方法。
背景技術:
現有技術中,作為將SOI層薄膜化的方法之一,進行將SOI晶圓以批次式熱處理爐進行熱處理,藉由氧化SOI表面的Si而使變質成氧化膜之後,去除氧化膜的方法。
藉由此方法將SOI膜厚度(SOI層的膜厚度)高精度地薄膜化至目標值(target值),必須有正確的調控使氧化膜厚度達到目標值。然而,由於氧化過程中的大氣壓的變動會導致氧化率變化的緣故,實際上正確地調控經熱處理成長的氧化膜的厚度是件非常困難的事。因此,進行藉由氧化的薄膜化的情形下,會採取使薄膜化後的SOI膜厚度比目標值稍微較厚而進行氧化的薄膜化,之後再另外調控蝕刻時間而藉由蝕刻(etching)的薄膜化以達到目標值的方法。
作為這種兩階段薄膜化的方法,如專利文獻1所示,採取於去除氧化後的氧化膜之後測定SOI層的膜厚度,以該值為基礎,設定下個階段的蝕刻步驟的加工量的方法。
再者,於藉由「氧化」加「蝕刻」的該兩階段薄膜化處理,作為縮短上述處理的方法,提出有:於氧化後氧化膜還在附著的狀態下測定SOI層的膜厚度,基於測定的SOI的值,以氧化膜去除與蝕刻+洗淨工程以洗淨的同一批處理進行的方式(專利文獻2)。
現有技術文獻
專利文獻
【專利文獻1】日本特開2007-266059號公報。
【專利文獻2】日本特開2010-92909號公報
技術實現要素:
〔發明所欲解決的問題〕
然而,即使是藉由這些方法高精度地調控SOI層的膜厚度,依然會由于于批次式熱處理的熱處理過程中產生的氧化膜厚度的分散、蝕刻(批次式洗淨等的洗淨)所致的加工量分散(SOI層的蝕刻量的分散)而於同一批次內處理的多個SOI晶圓的膜厚度中,產生分散(SOI膜厚度的分散)。
圖5顯示,對1批次25片的SOI晶圓,進行以SC1洗淨液(氨水與過氧化氫溶液的混合水溶液)將SOI層的厚度減少14.5nm程度的批次式洗淨(蝕刻)時,該洗淨的卡匣內的插槽位置與SOI層(Si)的加工量的面內平均值的關係。批次內的加工量分散以P-V(Peak to Valley)值(最大值減去最小值)為0.61nm。
圖6顯示,將1批次100片的SOI晶圓以批次式熱處理爐熱氧化時,爐內位置與形成的氧化膜厚度(面內平均值)的關係。
圖6所示的於批次式熱處理中發生的面內平均值的膜厚度分散,如圖5所示,僅以批次式洗淨進行蝕刻的情形下無法調控、修正,特別是,於FDSOI晶圓,高精度的膜厚度均一性。例如:SOI膜厚度的分散,全點(全晶圓的全測定點)要求控制在目標值±0.5nm以內,僅以批次式洗淨無法滿足此要求。再者,因從氧化後至目標值的調整加工量(藉由蝕刻的加工量),即最終階段的膜厚度的調整加工量為多,與目標值的偏差也有變大的傾向。
另一方面,藉由單片式的洗淨機(例如日本特開2000-31071號公報的圖2的旋轉洗淨機)調整SOI膜厚度,雖以晶圓單位能修正批次內的膜厚度分散,因於藥液噴嘴部藥液的溫度變高,而比批次式洗淨機有較大的晶圓面內的加工量分散;若僅以單片式洗淨(蝕刻)進行膜厚度的調整,晶圓面內的膜厚度範圍(Range(P-V值))惡化,無法使全測定點達到±0.5nm以下;再者,與僅以批次式洗淨機相同,自氧化後至目標值的最終階段的膜厚度調整加工量有較多的情形,與目標值的偏差有變大的傾向。
圖7顯示,將多片SOI晶圓,僅以批次式洗淨機與僅以單片式洗淨機進行SC1洗淨,SC1加工量的面內平均值與面內加工量範圍(P-V值)的比較結果的示意圖。如圖7所示,相較於批次式洗淨機,單片式洗淨機的面內的加工量範圍較大;並且,單片式洗淨機的加工量範圍有隨著SC1加工量的增加而增加的傾向。
本發明的目的為鑑於上述的問題點,提供一種SOI晶圓的製造方法,能夠製造具有優越均一性的SOI層的膜厚度的SOI晶圓。
〔解決問題的技術手段〕
為達成上述的目的,本發明提供一種SOI晶圓的製造方法,將於絕緣層上形成SOI層的SOI晶圓的該SOI層減少至預定的厚度,使該SOI層的膜厚度達到目標值,該SOI晶圓的製造方法至少包含下列步驟:
(a)在氧化性氣體氛圍下進行熱處理,於該SOI層的表面形成熱氧化膜;
(b)測定該熱氧化膜形成後的SOI層的膜厚度;
(c)對該SOI層進行批次(batch)式洗淨,該批次式洗淨包括將該SOI層浸泡於對於該SOI層具蝕刻性的洗淨液,藉由因應於該步驟(b)所測定的SOI層的膜厚度來調整該SOI層的蝕刻量,而將經該批次式洗淨後的SOI層的膜厚度調整成比該目標值較厚;
(d)測定經該批次洗淨後的SOI層的膜厚度;以及
(e)對該SOI層進行單片式洗淨,該單片式洗淨包括將該SOI層浸泡於對於該SOI層具蝕刻性的洗淨液,藉由因應於該步驟(d)所測定的SOI層的膜厚度來調整該SOI層的蝕刻量,而將經該單片式洗淨後的SOI層的膜厚度調整成該目標值,
其中,於該步驟(a)之後且於該步驟(b)之前,或於該步驟(b)之後且於該步驟(c)之前,去除在該步驟(a)所形成的熱氧化膜。
此SOI晶圓的製造方法,藉由利用批次式洗淨與單片式洗淨調整SOI層的膜厚度,能夠抑制經批次式洗淨的膜厚度調整的批次內SOI膜厚分散,及經單片式洗淨的膜厚度調整的面內膜厚分散。藉此製造有優越均一性的SOI層的膜厚度的SOI晶圓。
再者,該步驟(b)的膜厚度的測定是未去除該步驟(a)所形成的熱氧化膜下進行,於該步驟(b)之後且於該步驟(c)之前,在將該步驟(a)所形成的熱氧化膜用含有HF的水溶液以批次式洗淨去除後,以不使該經去除熱氧化膜的SOI層的表面乾燥而將該SOI層浸泡於對於該SOI層具蝕刻性的洗淨液之方式進行該步驟(c)的批次式洗淨為佳。
此SOI晶圓的製造方法,即使縮短SOI層薄膜化程序也能高精度地進行SOI層的膜厚度的調控,不使SOI層的膜厚度的精度下降並能使SOI層的薄膜化程序整體的成本降低。
再者,該SOI晶圓藉由離子注入剝離法所製作為佳,該離子注入剝離法至少包括:將接合具有藉由注入離子所形成的微小氣泡層的接合晶圓與作為支持基板的基底晶圓。
如此,本發明的SOI晶圓的製造方法,能夠適合使用於將進行薄膜化的SOI晶圓藉由離子注入剝離法製作SOI晶圓的情形。
再者,該批次式洗淨及該單片式洗淨,浸泡於SC1溶液者為佳。
如此,藉由浸泡於SC1溶液中更能精確地調控SOI層的膜厚度。
再者,將該步驟(c)的批次式洗淨後的SOI層的膜厚度的批次內平均值,調控在該目標值與該目標值+0.5nm之間為佳。
此SOI晶圓的製造方法,藉由單片式洗淨使蝕刻的加工量最小化,將SOI膜厚度的面內的膜厚度分散抑制在最小限度,並於單片式洗淨調整膜厚度,故得以修正經批次式洗淨所產生的批次內的膜厚度分散。
〔對照現有技術的功效〕
本發明的SOI晶圓的製造方法,藉由單片式洗淨減低蝕刻的加工量,能將SOI膜厚度的面內的膜厚度分散抑制在最小限度,並能以單片式洗淨調整膜厚度,故能修正經批次式洗淨所產生的批次內的膜厚度的分散。再者,藉由於批次式洗淨後進行單片式洗淨,而分段調整SOI層的膜厚度,能夠比現有的方法有較少的最終階段的膜厚度調整加工量。藉此精確地調控達到目標值的膜厚度。特別是,本發明能安定地製造須有高精度的膜厚度均一性(全點在目標值±0.5nm以內)的FDSOI晶圓。
附圖說明
圖1是顯示本發明的SOI晶圓的製造方法的一實施方式的流程圖。
圖2是顯示本發明的SOI晶圓的製造方法的另一實施方式的流程圖。
圖3是顯示實施例的洗淨卡匣內的插槽位置與SOI層膜厚度值的關係的顯示圖。
圖4是顯示比較例1的洗淨卡匣內的插槽位置與SOI層膜厚度值的關係的顯示圖。
圖5是顯示進行批次式洗淨時,洗淨卡匣內插槽位置與SOI層(Si)的加工量面內平均值的關係的顯示圖。
圖6是顯示以批次式熱處理爐熱氧化一批次100片的晶圓時的爐內位置與形成的氧化膜厚度(面內平均值)的關係的顯示圖。
圖7是顯示僅以批次式洗淨機與僅以單片式洗淨機對複數片的SOI晶圓進行SC1洗淨,比較SC1加工量的面內平均值與面內的加工量範圍(P-V值)的結果的顯示圖。
具體實施方式
以下對本發明進行更詳細地說明。
如同上述,求取一種SOI晶圓的製造方法,能夠製造SOI層的膜厚度的均一性優越的SOI晶圓。
本申請的發明人為達成上述目的努力進行研究的結果,發現一種SOI晶圓的製造方法,將自熱處理形成熱氧化膜後的SOI晶圓,於批次式洗淨(例如:HF洗淨+SC1洗淨)將膜厚度調整成比目標的SOI膜厚度(目標值)稍厚(例如:目標值+0~+0.5nm以下)後,更藉由單片式洗淨的蝕刻將膜厚度調整成最終的目標值,此方法能夠解決上述的問題,而完成本發明。
以下關於本發明的實施例參考圖式進行詳細說明,而本發明則不限定於此。
圖1、2是顯示本發明的晶圓的製造方法的一實施方式的流程圖。
首先,如圖1(1)、圖2(1)所示,準備於絕緣層上形成SOI層的SOI晶圓。
在此準備的SOI晶圓可以是具有於絕緣層上形成SOI層的SOI構造的晶圓。例如,具有於單晶矽等的支持層上形成絕緣層(埋入絕緣層),於此埋入絕緣層上形成SOI層的構造的晶圓。
另外,本說明書中的SOI層為「絕緣層上的矽層(Silicon on Insulator)」之意。
雖未特別限定SOI晶圓的製作方法,例如,將準備的SOI晶圓藉由離子注入剝離法所製作成SOI晶圓者為佳。該離子注入剝離法包括:將具有藉由注入離子所形成的微小器泡層的接合晶圓與作為支持基板的基底晶圓透過絕緣膜而相接合,以及以該為小氣泡層為邊界剝離接合晶圓而於基底晶圓上形成薄膜。
再者,本發明無論是上述的離子注入剝離法(也就是Smart法)與rT-CCP法(溫式機械剝離法,也被稱為SiGen法),或是SIMOX法(Separation by Implanted Oxygen法)等的SOI晶圓的製造法皆能適用。
下一步,如圖1(2)、圖2(2)所示,以氧化性氣體氛圍下進行熱處理,於SOI層的表面形成熱氧化膜(步驟(a))。此熱氧化膜經SOI層靠近表面部分的矽氧化變質成氧化膜。作為氧化性氣體氛圍例如Pyrogenic氛圍。
下一步,如圖1(3)、圖2(4)所示,測定熱氧化膜形成後的SOI層的膜厚度(步驟(b))。雖未特別限定SOI層厚度的測定方法,較佳地可利用橢圓偏光計(ellipsometer)的測定方法而可精確測定SOI層厚度。
本發明如圖2(3)所示,於該步驟(a)之後且於該步驟(b)之前,或者,如圖1(4)所示,於該步驟(b)之後且於該步驟(c)之前,去除在該步驟(a)所形成的熱氧化膜。熱氧化膜能利用含有HF的水溶液去除。
例如,如圖2(3)所示,可於步驟(b)前進行熱氧化膜的去除洗淨。在此情形下,能於將熱氧化膜去除後的SOI晶圓乾燥之後測定SOI層的膜厚度。
再者,如圖1所示,步驟(b)中,可在未去除步驟(a)所形成的熱氧化膜下進行膜厚度的測定。藉此,可保護測定時SOI層的表面,降低傷痕與不純物汙染等的危險性,最終可提升SOI晶圓的質量及製造的產率。
再者,此時測定的SOI層的厚度不包含表面的熱氧化膜厚度。這情形下,可於步驟(b)之後且於該步驟(c)之前,將該步驟(a)所形成的熱氧化膜去除,特別如圖1(4)所示,利用含有HF的水溶液以批次式洗淨去除,可以將此熱氧化膜的去除與後述步驟(c)的SOI層的蝕刻作為連續的處理進行。
下一步,如圖1(5)及圖2(5)所示,對SOI層進行批次式洗淨(步驟(c)),批次式洗淨包括將SOI層浸泡於對於SOI層具蝕刻性的洗淨液,藉由因應於步驟(b)所測定的SOI層的膜厚度來調整SOI層的蝕刻量,而將經批次式洗淨後的SOI層的膜厚度調整成比目標值較厚。作為此調整的方法,可為調控蝕刻時間的方法、變更洗淨液的組成及溫度的條件的方法。
步驟(c)中,可將經批次式洗淨後的SOI層的膜厚度調整成比目標值較厚,例如,將步驟(c)的批次式洗淨後的SOI層的膜厚度的批次內平均值,控制於目標值與目標值+0.5nm之間為佳。藉此,可使經後續步驟的單片式洗淨所致的蝕刻的加工量最小化,將SOI膜厚度的面內膜厚度分散抑制在最小限度,並且單片式洗淨中可依每片調整膜厚度而修正批次內的膜厚度分散。再者,比現有的方法有較少的最終階段的膜厚度調整加工量,能精確地調控達目標值的膜厚度。此外,批次內平均值是同一批次內經洗淨的多個SOI晶圓的SOI層的膜厚度的平均值。
作為對於該SOI層具蝕刻性的洗淨液,例如SC1溶液(氨水及過氧化氫溶液的混和水溶液)。
以上述顯示於圖1(4)的方法去除熱氧化膜的情形下,未使該經去除熱氧化膜的SOI層的表面乾燥而將該SOI層浸泡於對於該SOI層具蝕刻性的洗淨液之方式進行該步驟(c)的批次式洗淨為佳。亦即,進行熱氧化膜去除及SOI層蝕刻以連續的處理為佳。藉此縮短全體SOI層薄膜化處理並可降低處理的成本。
下一步,如圖1(6)及圖2(6)所示,測定經該批次洗淨後的SOI層的膜厚度(步驟(d))。SOI層的膜厚度的測定方法是利用橢圓偏光計(Ellipsometer)的測定方法。
下一步,如圖1(7)及圖2(7)所示,對該SOI層進行單片式洗淨(步驟(e)),包括將SOI層浸泡於對於SOI層具蝕刻性的洗淨液。此步驟藉由因應於步驟(d)所測定的SOI層的膜厚度來調整該SOI層的蝕刻量,而將該單片式洗淨後的SOI層的膜厚度調整成目標值。此調整方法可為調控蝕刻時間的方法及改變洗淨液的組成與溫度的條件的方法。特別是為了抑制於步驟(c)生成的批次內的SOI膜厚度分散,依各SOI晶圓調控蝕刻時間為佳。
如同上述,利用SC1溶液作為洗淨液。步驟(c)的批次式洗淨及步驟(e)的單片式洗淨以包括浸泡於SC1溶液的洗淨,能夠進行更良好精確度的SOI的膜厚度的調控。另外,實施這些洗淨時雖至少將SOI層浸泡於洗淨液就足夠,但也可浸泡晶圓整體。
如此一來,藉由於進行批次式洗淨之後進行單片式洗淨,階段地調整SOI層的膜厚度,能夠減少單片式洗淨的膜厚度調整加工量。藉此能夠有良好精確度地達到目標值的膜厚度調控。
經由如同以上步驟的SOI晶圓的製造方法,藉由組合批次式洗淨與單片式洗淨,可調控且修正基於批次式熱處理中發生的氧化膜分散所產生的SOI層的面內平均值的膜厚度分散。特別是進行批次式洗淨後,藉由進行單片式洗淨,可減少經單片式洗淨的SOI層的蝕刻量。藉此,面內的加工量分散變小,改善晶圓面內的膜厚度範圍(P-V值)。本發明分別藉由批次式洗淨的膜厚度調整與單片式洗淨的膜厚度調整,抑制批次內的SOI膜厚度分散與面內的膜厚度分散,特別是能安定地製造須有極高SOI層膜厚的均一性(全點在目標值±0.5nm以內)的FDSOI晶圓。
實施例
以下藉由實施例與比較例對本發明進行更具體的說明,而本發明則不限定於此實施例。
(實施例)
準備46片藉由離子注入剝離法製作的直徑300mm的SOI晶圓(SOI膜厚度150nm),分別置入兩個批次式洗淨卡匣(卡匣-01、卡匣-02)並將實施的例子顯示於表1。
具體為,首先對上述的SOI晶圓,以950℃、2小時、Pyrogenic氛圍進行熱處理,於SOI層的表面形成熱氧化膜(步驟(a))。之後使用橢圓偏光計測定形成熱氧化膜後的SOI層的膜厚度(步驟(b))。此時,與測定SOI膜厚度同時測定表面氧化膜厚度。之後利用含有15%HF的水溶液進行批次式洗淨100秒,去除此熱氧化膜後不將SOI層的表面乾燥,而進行將SOI層浸漬於SC1溶液的批次式洗淨,將SOI層的膜厚度調整成較目標值厚(步驟(c))。此時,SC1條件(組成,液溫)為NH4OH:H2O2:H2O=1:1:5,液溫76℃。另外,考慮步驟(b)測定的SOI層的膜厚度,洗淨時間為140秒。
之後使用橢圓偏光計測定批次式洗淨步驟後的SOI層的膜厚度(步驟(d))。此時也計算批次內的SOI膜厚度的平均值。之後進行將SOI層浸漬於SC1溶液的單片式洗淨(藉由旋轉洗淨機的SC1洗淨),將SOI層的膜厚度調整成目標值(步驟(e))。SC1條件(組成,液溫)與上述條件相同。另外,考慮步驟(d)測定的SOI層的膜厚度,洗淨時間依照各個SOI晶圓分別為20~60秒。
(比較例1)
比較例1是僅以批次式洗淨機進行氧化後的氧化膜去除及膜厚度調整洗淨。於比較例1中的氧化膜去除洗淨及批次式膜厚度調整洗淨,同時將22片已熱氧化處理的晶圓做為一批次置入同一個卡匣(卡匣-01)並進行批處理。之後利用含有15%HF的水溶液進行批次式洗淨100秒,並於去除熱氧化膜後不將SOI層的表面乾燥,將SOI層浸漬於SC1溶液且進行批次式洗淨180秒。SC1條件(組成,液溫)與實施例的條件相同。
(比較例2)
再者,比較例2是僅以單片式洗淨進行氧化後的氧化膜去除及膜厚度調整洗淨。具體為,首先與實施例相同進行至步驟(b)。之後去除SiO2(熱氧化膜)。之後將SOI層浸漬於SC1溶液,依各個SOI晶圓分別以160~200秒進行單片式洗淨(藉由旋轉洗淨機的SC1洗淨)。SC1條件(組成,液溫)與實施例的條件相同。
表1顯示實施例及比較例的各步驟的條件與測定結果。另外,表1的批次內範圍顯示批次內各晶圓的面內平均膜厚度的分散(P-V值)。再者,圖3是顯示實施例的洗淨卡匣內的插槽位置與SOI層膜厚度值的關係顯示圖。圖4是顯示比較例1的洗淨卡匣內的插槽位置與SOI層膜厚度值的關係顯示圖。
表1
如表1及圖4所示,僅以批次式洗淨機做膜厚度調整的情況(比較例1)下,批次內平均值亦比實施例較差,再者因無法修正批次內的膜厚度分散,超過目標值±0.5nm的膜厚度的晶圓的比例比實施例大許多。
再者,如表1所示,僅以單片式洗淨機做膜厚度調整的情況(比較例2)下,批次內平均值亦比實施例較差,再者因面內的膜厚度的惡化,全部的晶圓皆超過目標值±0.5nm的膜厚度。
另一方面,如表1及圖3所示,組合批次式洗淨及單片式洗淨的本實施例中,能夠有良好精確度地調整各晶圓的平均值至目標值(12nm),再者亦能夠藉由單片式洗淨機而抑制面內的膜厚度分散的惡化,故近乎全數的晶圓(96%)滿足目標值±0.5nm的條件。
另外,本發明不限定於上述的實施例。上述實施例為示例,凡擁有和記載於申請專利範圍內相同的技術思想與實質上同樣的構成,產生相同的作用效果者,不論為何物皆包含在本發明的技術範圍內。