一種齒輪室蓋的製作方法
2023-08-10 07:45:21
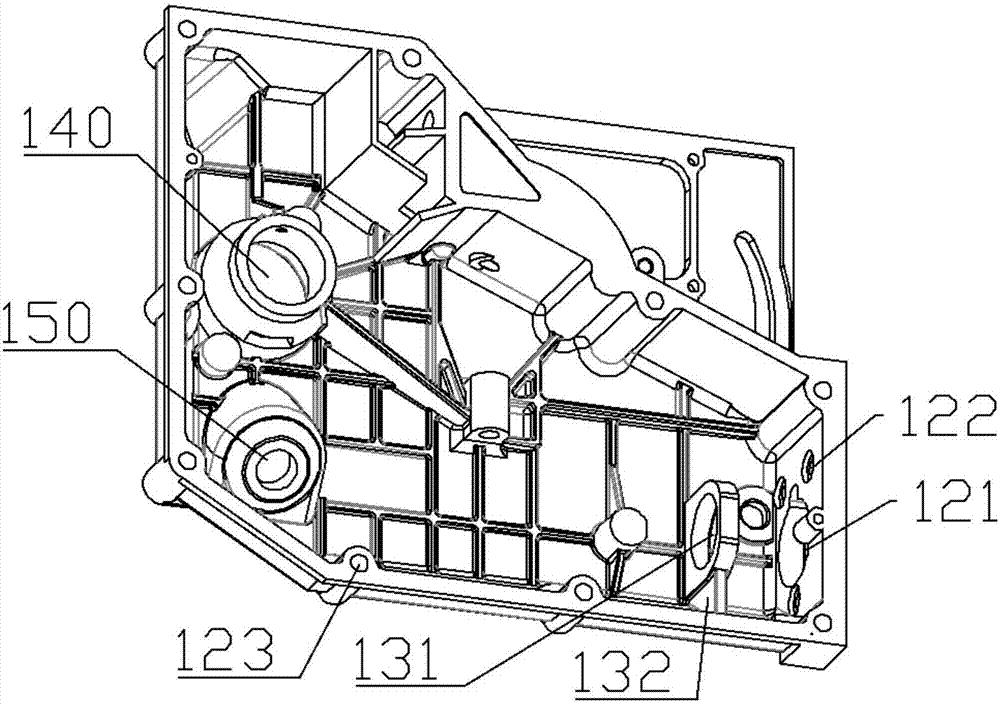
本實用新型涉及內燃機技術領域,尤指一種齒輪室蓋。
背景技術:
單缸柴油機,即按氣缸數量分類時只有一個氣缸的柴油機。是用柴油作燃料的內燃機,將燃料燃燒釋放出的熱能轉化為電能或機械能的裝置。單缸柴油機主要應用於農業機械、工程機械、汽車工業、船舶機械、電力工業等領域。
目前,單缸柴油機噴油泵一端安裝在齒輪室蓋上,另一端懸空,屬於懸臂支撐,其中,由於噴油泵安裝面與噴油泵受力點之間距離較大,故導致齒輪室蓋上的安裝孔、噴油泵安裝面及其兩者之間的連接部件所受力矩大,在噴油泵工作時的振動使得這些零部件容易受損,因而常常發生齒輪室蓋因受力過大而損壞、連接件鬆動等事件,導致齒輪室蓋可靠性較差。因此,在實際應用中,需要經常更換新的齒輪室蓋,增加了單缸柴油機的安裝成本和維護成本。
因此,本申請人致力於研究一種齒輪室蓋。
技術實現要素:
本實用新型的目的是提供一種齒輪室蓋,降低了噴油泵對齒輪室蓋安裝孔、連接齒輪室蓋和噴油泵的連接部件力的作用,進而減少了噴油泵對這些零部件的損壞,從而提高了齒輪室蓋安裝孔、連接部件的使用壽命,提高了齒輪室蓋的可靠性。
本實用新型提供的技術方案如下:
一種齒輪室蓋,用於封閉內燃機的齒輪室,並與噴油泵連接,包括:
底板,所述底板的一側朝所述齒輪室方向延展有安裝板;
所述安裝板上開有安裝孔和連接孔,所述連接孔分設於所述安裝孔的周圍,並用於連接所述噴油泵;
所述底板上設有一支撐板,所述支撐板從所述底板的表面朝所述齒輪室方向凸起,所述支撐板上設有與所述安裝孔對應的支撐孔;
所述噴油泵的滾軸一端穿過所述安裝孔和所述支撐孔,並與所述支撐孔間隙配合。
本技術方案中,通過在齒輪室蓋設置一個與安裝孔對應的支撐孔,且支撐孔與噴油泵靠近滾軸的一端間隙配合,這樣不僅使得齒輪室蓋上的安裝板與噴油泵連接,對噴油泵具有一個定位且固定支撐的作用,且齒輪室蓋上的支撐孔限制噴油泵在工作時的振動幅度範圍的同時還起到支撐噴油泵的作用,因而降低了噴油泵對齒輪室蓋安裝孔、連接齒輪室蓋和噴油泵的連接部件力的作用,進而減少了噴油泵對這些零部件的損壞,從而提高了齒輪室蓋安裝孔、連接部件的使用壽命,提高了齒輪室蓋的可靠性,降低了單缸柴油機的安裝成本和維護成本。進一步地,由於支撐孔對噴油泵的限位作用,因而減少了噴油泵與圍設其周邊的零部件的碰撞,進而降低了單缸柴油機工作時的噪音和振動,減少噪音汙染對單缸柴油機使用者的傷害;保護了了圍設噴油泵周邊的零部件。本實用新型結構簡單,設計合理,實用性強。
進一步優選地,所述支撐板與所述底板之間設有第一加強筋,所述第一加強筋分別與所述支撐板與所述底板連接。
本技術方案中,通過設置連接支撐板和底板的加強筋,可以提高支撐板與底板的連接強度,進而提高了支撐板的機械強度,由於支撐板和加強筋的傳導作用,降低了噴油泵工作振動時對支撐板力的作用,進而提高支撐板的可靠性和使用壽命。
進一步優選地,所述安裝孔的軸線與所述支撐孔的軸線在同一直線上。
本技術方案中,保證了支撐孔與安裝孔在噴油泵工作振動時在各自相對應的位置起到對噴油泵支撐和限位的作用,這樣使得噴油泵的支撐力來自相同方向的兩個力(即支撐孔對噴油泵的力和安裝孔對噴油泵的力)的支撐,提高了安裝孔和支撐孔之間的配合使用時的支撐和限位效果。
進一步優選地,所述安裝孔為一凸臺軸孔,所述凸臺軸孔由所述安裝板的表面朝所述支撐板方向凸起形成。
本技術方案中,凸臺軸孔可以提高安裝孔與噴油泵之間的力的作用面積,降低了噴油泵對安裝孔的力矩作用,進而提高了安裝孔對噴油泵之間的限位和支撐效果,減少了噴油泵在使用過程中對安裝板的損壞程度,保護了安裝板,提高了安裝板的使用壽命,提高了齒輪室蓋的可靠性。
進一步優選地,所述底板上設有動力輸出軸孔和機油尺孔,所述動力輸出軸孔和所述機油尺孔遠離所述支撐板。
進一步優選地,所述底板的表面朝所述齒輪室方向凸起有第二加強筋;所述第二加強筋連接所述支撐板、所述動力輸出軸孔和所述機油尺孔。
本技術方案中,通過加強筋將設置在齒輪室蓋上的各種孔連接起來,這樣增強了齒輪室蓋上這些孔之間的連接剛度,提高了這些孔的機械強度,從而進一步提高了齒輪室蓋的可靠性和使用壽命,降低了單缸柴油機的安裝成本和維護成本。
進一步優選地,所述第二加強筋呈十字交叉形或輻射形設置。
通過本實用新型提供的齒輪室蓋,能夠帶來以下至少一種有益效果:
1.本實用新型中,通過在齒輪室蓋設置一與安裝孔對應的支撐孔,且支撐孔與噴油泵靠近滾軸的一端間隙配合,這樣支撐孔限制了噴油泵在工作時的振動幅度範圍,降低了噴油泵對齒輪室蓋安裝孔、連接齒輪室蓋和噴油泵的連接部件力的作用,進而減少了噴油泵對這些零部件的損壞,從而提高了齒輪室蓋安裝孔、連接部件的使用壽命,提高了齒輪室蓋的可靠性,降低了單缸柴油機的安裝成本和維護成本。進一步地,由於支撐孔對噴油泵的限位作用,因而減少了噴油泵與圍設其周邊的零部件的碰撞,進而降低了單缸柴油機工作時的噪音和振動,減少噪音汙染對單缸柴油機使用者的傷害;且保護了了圍設噴油泵周邊的零部件。本實用新型結構簡單,設計合理,實用性強。
2.本實用新型中,通過加強筋將設置在齒輪室蓋上的各種部件(如支撐板、動力輸出軸孔和機油尺孔)連接起來,這樣增強了齒輪室蓋上這些部件之間的連接剛度,提高了這些部件的機械強度,從而進一步提高了齒輪室蓋的可靠性和使用壽命,降低了單缸柴油機的安裝成本和維護成本。
3.本實用新型中,通過支撐板在底板之間設置加強筋,可以提高支撐板與底板的連接強度,進而提高了支撐板的機械強度,由於支撐板和加強筋的傳導作用,降低了噴油泵對支撐板力的作用,進而提高支撐板的可靠性和使用壽命。
附圖說明
下面將以明確易懂的方式,結合附圖說明優選實施方式,對一種齒輪室蓋的上述特性、技術特徵、優點及其實現方式予以進一步說明。
圖1是本實用新型的一種實施例的結構示意圖;
圖2是圖1的主視圖結構示意圖;
圖3為本實用新型的齒輪室蓋與噴油泵連接的結構示意圖;
圖4為圖3的A-A剖面結構示意圖。
附圖標號說明:
100.齒輪室蓋,110.底板,120.安裝板,121.安裝孔,122.第一連接孔,123.第二連接孔,130.支撐板,131.支撐孔,132.第一加強筋,140.動力輸出軸孔,150.機油尺孔,160.第二加強筋,170.第一圍板,180.第二圍板,190.第三圍板,200.噴油泵,210.噴油泵滾軸外殼,220.噴油泵凸輪軸外殼,230.噴油泵安裝軸外殼,240.噴油泵連接端面。
具體實施方式
為了更清楚地說明本實用新型實施例或現有技術中的技術方案,下面將對照附圖說明本實用新型的具體實施方式。顯而易見地,下面描述中的附圖僅僅是本實用新型的一些實施例,對於本領域普通技術人員來講,在不付出創造性勞動的前提下,還可以根據這些附圖獲得其他的附圖,並獲得其他的實施方式。
為使圖面簡潔,各圖中只示意性地表示出了與本實用新型相關的部分,它們並不代表其作為產品的實際結構。另外,以使圖面簡潔便於理解,在有些圖中具有相同結構或功能的部件,僅示意性地繪示了其中的一個,或僅標出了其中的一個。在本文中,「一個」不僅表示「僅此一個」,也可以表示「多於一個」的情形。
在實施例一中,如圖1和2所示,一種齒輪室蓋,用於封閉內燃機的齒輪室(圖中未標示),並與噴油泵200連接,包括:底板110,底板110的一側朝齒輪室方向延展有安裝板120;安裝板120上開有安裝孔121和第一連接孔122,第一連接孔122分設於安裝孔121的周圍,並用於連接噴油泵200;底板110上設有一支撐板130,支撐板130從底板110的表面朝齒輪室方向凸起,支撐板130上設有與安裝孔121對應的支撐孔131;噴油泵200的滾軸一端穿過安裝孔121和支撐孔131,並與支撐孔131間隙配合。通過安裝孔121和支撐孔131的配合使用來定位和支撐噴油泵200,優選地安裝孔121與噴油泵安裝軸外殼230間隙配合,安裝板120通過第一連接孔122與噴油泵連接端面240連接,支撐孔131與噴油泵滾軸外殼210間隙配合,這樣,齒輪室蓋100上的安裝板120與噴油泵200連接,對噴油泵200具有定位、固定支撐以及對噴油泵200在工作時的振動幅度範圍限制的作用,且齒輪室蓋100上的支撐孔131進一步起到支撐和限制噴油泵200在工作時的振動幅度範圍的作用,因而降低了噴油泵200對齒輪室蓋100上的安裝孔121、連接齒輪室蓋100和噴油泵200的連接部件等(圖中未標示)力的作用,進而減少了噴油泵200對這些零部件的損壞,從而提高了齒輪室蓋100上的安裝孔121、連接部件的使用壽命,提高了齒輪室蓋100的可靠性,降低了單缸柴油機的安裝成本和維護成本。進一步地,由於支撐孔131對噴油泵200的限位作用,因而減少了噴油泵200與圍設其周邊的零部件的碰撞,進而降低了單缸柴油機工作時的噪音和振動,減少噪音汙染對單缸柴油機使用者的傷害;保護了了圍設噴油泵200周邊的零部件。本實用新型結構簡單,設計合理,實用性強。值得指出的是,安裝孔121和支撐孔131主要與噴油泵200靠近滾軸的一端的外殼間隙連接,具體的連接部位以及安裝孔121和支撐孔131的大小、位置等可根據實際情況(如噴油泵200的類型、大小尺寸等)進行設計和安裝,提高齒輪室蓋100與噴油泵200連接的適配性。
在實施例二中,如圖1和2所示,在實施例一的基礎上,安裝孔121的軸線與支撐孔131的軸線在同一直線上,這樣保證了支撐孔131與安裝孔121在噴油泵200工作振動時在各自相對應的位置起到對噴油泵200支撐和限位的作用,這樣使得噴油泵200的支撐力來自相同方向的兩個力(即支撐孔131對噴油泵200的力和安裝孔121對噴油泵200的力)的支撐,提高了安裝孔121和支撐孔131之間的配合使用時的支撐和限位效果。安裝孔121為一凸臺軸孔(圖中未標示),凸臺軸孔由安裝板120的表面朝支撐板130方向凸起形成,凸臺軸孔可以提高安裝孔121與噴油泵200之間的力的作用面積,降低了噴油泵200對安裝孔121的力矩作用,進而提高了安裝孔121對噴油泵200之間的限位和支撐效果,減少了噴油泵200在使用過程中對安裝板120的損壞程度,保護了安裝板120,提高了安裝板120的使用壽命,提高了齒輪室蓋100的可靠性。且支撐板130與底板110之間設有第一加強筋132,第一加強筋132分別與支撐板130與底板110連接,第一加強筋132提高了支撐板130與底板110的連接強度,進而提高了支撐板130的機械強度,由於支撐板130和第一加強筋132的傳導作用,降低了噴油泵200工作振動時對支撐板130的力的作用,進而提高支撐板130的可靠性和使用壽命。且齒輪室蓋100還包括了第一圍板170、第二圍板180和第三圍板190;安裝板120、第一圍板170、第三圍板190和第二圍板180依次連接並圍設於底板110的四周,且安裝板120、第一圍板170、第三圍板190和第二圍板180由所述底板110的各個周邊朝齒輪室方向延展得到,安裝板120、第一圍板170、第三圍板190和第二圍板180靠近齒輪室的端面均設有第二連接孔123,齒輪室蓋100通過第二連接孔123與齒輪室封閉連接。第一加強筋132優選為板狀的加強筋,且由支撐板130遠離底板110的端部朝底板110延展得到,優選地靠近第一圍板170的第一加強筋132延展至第一圍板170,並與第一圍板170連接,這樣增加了支撐板130在承受噴油泵200力的作用時,增加了承受力的接觸面和方向,根據力的分解作用,從而降低了支撐板130承受噴油泵200力的大小,進而保護了支撐板130,提高支撐板130的使用壽命,提高支撐板130的可靠性。當然,第一加強筋132還可以延伸至第二圍板180,甚至延伸至第三圍板190,並分別與第二圍板180和第三圍板190連接,進一步提高支撐板130的可靠性。且第一加強筋132可也由支撐孔131下方的支撐板130朝向底板110延伸得到,且呈漸擴(或直線狀)方式延展得到,且第一加強筋132可以與支撐板130一體成型,或分開設置。
在實施例三中,如圖1和2所示,在實施例一或二的基礎上,底板110上設有動力輸出軸孔140和機油尺孔150,動力輸出軸孔140和機油尺孔150遠離支撐板130。底板110的表面朝齒輪室方向凸起有第二加強筋160;第二加強筋160連接支撐板130、動力輸出軸孔140和機油尺孔150,第二加強筋160使齒輪室蓋100上的各個部件之間連接在一起,這樣增強了齒輪室蓋100上這些部件之間的連接剛度,提高了這些部件的機械強度,從而進一步提高了齒輪室蓋100的可靠性和使用壽命,降低了單缸柴油機的安裝成本和維護成本。優選地第二加強筋160呈十字交叉形或輻射形設置;且第一加強筋132與第二加強筋160相互連接;底板110、支撐板130、安裝板120、第一圍板170、第二圍板180、第三圍板190、第一加強筋132和第二加強筋160一體成型。
示例性的,如圖1-4所示,為本實用新型的齒輪室蓋與噴油泵連接的具體應用情況:
噴油泵200靠近滾軸的一端依次穿過安裝孔121和支撐孔131,其中,安裝孔121與噴油泵安裝軸外殼230間隙配合,且安裝板120還設有一間隙孔(圖中未標示),間隙孔設置在安裝孔121的旁邊,並與安裝孔121相通;設置在安裝板120上的三個第一連接孔122分設在安裝孔121的周圍,且安裝板120通過螺絲組件(或螺栓組件、插銷組件)和第一連接孔122的配合使用,與噴油泵200靠近齒輪室蓋100一側的噴油泵連接端面240連接;噴油泵凸輪軸外殼220穿過支撐孔131,而分別連接噴油泵凸輪軸外殼220和噴油泵安裝軸外殼230的噴油泵滾軸外殼210與支撐孔131間隙配合。通過第一連接孔122、安裝孔121、支撐孔131之間的配合使用,提高了齒輪室蓋100與噴油泵200之間定位的準確性和支撐以及連接的穩固性;還降低了噴油泵200對齒輪室蓋100上的安裝孔121、連接齒輪室蓋100和噴油泵200的連接部件等力的作用,進而減少了噴油泵200對這些零部件的損壞,從而提高了齒輪室蓋100上的安裝孔121、連接部件的使用壽命,提高了齒輪室蓋100的可靠性;還限制了噴油泵200在工作振動時的振幅,因而降低了噴油泵200工作時所產生的噪音汙染和振動,進而保護了單缸柴油機使用者;還減少了噴油泵200與圍設其周邊的零部件的碰撞,保護了了圍設噴油泵200周邊的零部件。
應當說明的是,上述實施例均可根據需要自由組合。以上所述僅是本實用新型的優選實施方式,應當指出,對於本技術領域的普通技術人員來說,在不脫離本實用新型原理的前提下,還可以做出若干改進和潤飾,這些改進和潤飾也應視為本實用新型的保護範圍。