用於鑄造鑄件的方法與流程
2023-07-26 03:52:21 2
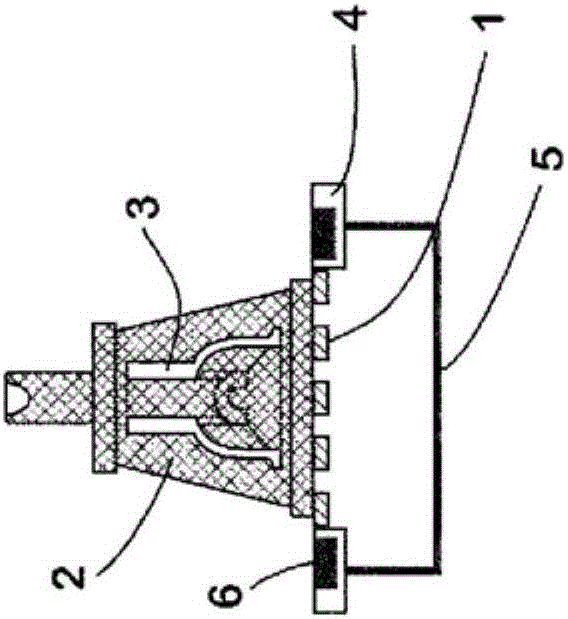
本發明涉及一種鑄造鑄件的方法,其中,將金屬熔體澆鑄到鑄模中,該鑄模圍繞形成待產生的鑄件的空腔,其中,該鑄模作為缺失模而由一個或多個鑄模部件或鑄芯組成。這些鑄模部件或鑄芯在此由模製材料成型,該模製材料由芯砂、粘合劑和可選的一種或多種用於調整模製材料的特定性能的添加劑組成。
背景技術:
在這類常規的方法中,通常首先提供形成鑄件的鑄模,該鑄模的鑄芯和鑄模部件在分開的加工過程中預製。該鑄模在此也可以作為所謂的「組合砂芯(Kernpaket)」由多個鑄芯組合成。同樣可能的是,使用例如僅由兩個分別由模製材料製成的模具半部組成的模具,在模具半部中成型有鑄件形狀的空腔,其中在此也可能存在模具芯,從而在鑄件中形成凹口、空心、通道和類似結構。
按照本發明產生的鑄件的典型的例子有氣缸體曲軸箱和氣缸蓋。更大和高負載的發動機由鑄鐵以砂型鑄造法製成。
在鐵鑄造領域中,與膨潤土、光澤碳形成劑和水混合的石英砂通常用作形成鑄模的外殼的鑄模部件的模製材料。相反,形成鑄件內側的空腔和通道的鑄芯通常由市售的芯砂形成,該芯砂與有機或無機的粘合劑、例如與合成樹脂或水玻璃混合。
與芯砂和粘合劑的類型無關,在由上述類型的模製材料成型的鑄模中基本原則在於,在粘合劑的賦形之後通過適當的熱處理或化學處理而時效硬化,從而使芯砂的顆粒粘合併且在足夠長的持續時間中確保經過各個鑄模部件和鑄芯的形狀穩定性。
在由鑄鐵澆鑄大體積的鑄件過程中,在金屬熔體的澆鑄之後負荷在鑄模上的內壓可能是非常高的。為了承受該壓力並且可靠地避免鑄模的破裂,必須使用厚壁、大體積的鑄模或者使用在鑄模外側上支承鑄模的支承結構。
這類支承結構的一個可能性為罩在鑄模上的外罩。該外罩通常按照護罩的形式而形成,該護罩在鑄模的外周面上圍繞鑄模,但是在其上側具有足夠大的開口,從而實現將熔體澆鑄到鑄模中。外罩在此這樣定尺寸,以使得在安裝之後至少在對於鑄模的支承起決定作用的區段中在外罩的內表面和鑄模的外表面之間保留存在一個填充腔。該填充腔通過能夠流動的填充物而填充,從而確保了各個表面區段在外罩上的大面積支承。為了在此實現填充腔儘可能均勻的填充、鑄模與填充材料同樣均勻的接觸以及易碎的鑄模材料的與之相應的均勻的支承,通常使用精細顆粒、能夠流動的填充材料(比如砂或鋼粒)作為填充物,這些填充材料具有較高的松密度。在填充之後額外地密封填充物。在此的目的是產生儘可能緊密的填充塊,其根據不可壓縮整體的類型確保支承力由外罩直接傳遞到鑄模上。
金屬熔體以較高的溫度澆鑄到鑄模中,從而也同樣劇烈地加熱組成鑄模的鑄模部件和鑄芯。因此,該鑄模開始釋放熱量。如果鑄模的溫度超過特定的最低溫度,則模製材料的粘合劑開始蒸發並且在進一步釋放熱量的條件下燃燒。由此使粘合劑失去其作用。通過粘合劑的分解而失去製成鑄模的鑄模部件和鑄芯的模製材料的顆粒的連接,並且使鑄模或其由模製材料組成的部件和芯分裂成單個的碎片。
實踐中已知的是,為了從各個鑄模中取出鑄件可以利用該效果。因此,例如EP 0 546 210 B2或EP 0 612 276 B2中已知用於鑄件的熱處理方法,其中,在一個連續的方法過程中使鑄模和鑄件由鑄造加熱進入熱處理爐。在通過該爐的過程中,鑄模和鑄件在一個溫度下經過足夠長的持續時間,在該溫度下調整通過熱處理所期望達到的鑄件的狀態。同時應這樣選擇熱處理的溫度,以使得模製材料的粘合劑分解。隨後自發從鑄件上脫落的、由模製材料組成的鑄模的碎片仍在熱處理爐中收集在砂床中。這些碎片在此處停留經過一定的持續時間,從而促使鑄模部件和鑄芯的碎片進一步分裂。通過鼓入熱風流經砂床而促使從鑄模上脫落的模製材料碎片進一步粉碎。足夠細碎的模製材料碎片最終運送至加工部中,在加工部中通過將模製材料碎片用於製造新的鑄模部件和鑄芯來恢復成芯砂。
在脫模和準備鑄造鑄件所需的鑄模過程中的已知的方法已經證明在大量鑄造由鋁製成的內燃機的部件中是有效的。然而其前提是相當大的結構長度的熔爐和鑄造模具和鑄模和鑄件的處理,在大體積部件或鑄模的情況下通過上述類型的外罩的額外支承被證明是複雜的。這特別適用於要由鑄鐵以中小批量製造的鑄件。
技術實現要素:
在該背景下,本發明的目的在於說明一種方法,該方法以優化的能效並且以特別經濟的方式實現了鑄件的大批量生產。
本發明通過權力要求1中給出的方法實現了該目的。
本發明的有利的設計方案在從屬權利要求中給出並且隨後將像一般發明構思一樣詳細說明。
相應地,本發明提出了一種用於鑄造鑄件的方法,其中,將金屬熔體澆鑄到鑄模中,該鑄模圍繞形成待制的鑄件的空腔。該鑄模作為缺失模而由一個或多個鑄模部件或鑄芯組成。這些鑄模部件由模製材料成型,模製材料由芯砂、粘合劑和可選的一種或多種用於調整模製材料的特定性能的添加劑組成。
按照本發明的方法在此包括以下工作步驟:
-提供所述鑄模;
-將鑄模套入外殼中以形成在外殼的至少一個內表面區段和鑄模相對應的外表面區段之間的填充腔;
-為填充腔填充能自由流動的填充物;
-將金屬熔體澆鑄到鑄模中,
-其中,鑄模伴隨著金屬熔體的澆鑄而開始散發熱量,該熱量是通過熱的金屬熔體引起的熱傳入的結果,並且
-其中,由於通過金屬熔體引起的熱傳入使模製材料的粘合劑蒸發並開始燃燒,從而使粘合劑失去其作用並使鑄模碎裂成碎片。
按照本發明,填充在填充腔中的填充物具有較低的松密度,以使得在填充腔填滿之後在此由填充物形成的填充物包能夠由氣流流通經過。
此外,在按照本發明的方法中,填充物在填充該填充腔的過程中具有最低溫度,填充物的溫度由該最低溫度開始通過過程熱而升高至700℃的臨界溫度以上,該過程熱通過鑄模散發的熱量和在粘合劑燃燒過程中釋放的熱量形成。
按照本發明的方法因此基於這樣的構思,即,在蓄熱器的意義上使用填充物並且該蓄熱器這樣調溫和形成,以使得製成鑄模的鑄模部件和鑄芯的模製材料的粘合劑在外罩中停留時間的過程中通過溫度作用而儘可能分解。
以這種方式實現了,由模製材料組成的鑄模的部件和鑄芯碎裂成碎片,以使得這些碎片從鑄件上脫落並且在移除該外罩之後該鑄件至少在其外表面的區域內儘可能沒有附著的鑄模部件或鑄芯。
在該時間點上,在鑄件內部形成通道和空腔的鑄芯也同時分裂,從而使該鑄芯的芯砂和模製材料碎片可以在外罩中自動地從鑄件中流出或者以已知的方式(例如通過機械的方法,比如晃動或者通過由適宜的液體衝洗)而從鑄件中除去。
按照本發明在鑄件和外罩之間形成的填充腔中填充的填充物是能夠流動的,從而在鑄模的外表面的區域中存在背切、空穴和類似結構時該填充物仍可以完全填充該填充腔。
在此重要的是,填充物按照本發明具有較低的松密度,以使得即使在填充腔填滿並在必要時對填充在填充腔中的填充物實施壓縮之後,仍能夠由氣流流通經過。與上述現有技術相反地,按照本發明明顯不在填充腔中產生高壓縮的填充包,該填充包雖然可以確保鑄模的理想的支承,但是應為儘可能不透氣的。確切地說,這樣選擇按照本發明使用的填充物,即,其對於氣流而言是可通過的,該氣流例如由於熱對流而調整。當鑄模通過澆鑄到其中的金屬熔體而加熱並且使鑄模部件和鑄芯的模製材料的可蒸發的粘合劑組分蒸發以及在釋放熱量的條件下開始燃燒時,產生該氣流。
當在此談及可蒸發並可燃燒的粘合劑時,總是意味著這樣的粘合劑組分,其通過供熱而變為蒸汽狀的並且能夠燃燒。這並不排除,粘合劑組成以固體或其他形式(例如作為裂紋產物)保留在鑄模中並在此以理想的方式同樣通過熱影響而分解。
填充在填充腔中的填充物的按照本發明規定的、能夠由氣流通過的可通過性在此不僅僅提供了使可從鑄模中蒸發出的粘合劑在填充物的區域中自燃並由此進一步加熱填充物的可能性,而且還允許額外地輸入促進粘合劑燃燒的氧氣。以這種方式,通過由金屬熔體引入的以及由粘合物燃燒釋放的過程熱將填充物加熱至一個溫度,該溫度足夠高,以使得與填充物接觸的、從鑄模中逸出的鑄模部件和鑄芯的粘合劑組分燃燒或者至少這樣熱分解,從而使其不再具有有害環境的作用或者能夠作為廢氣從外罩中排出並且輸送給廢氣淨化裝置。
按照本發明預調溫的填充物優選在澆鑄金屬熔體之前短的時間間隔內裝入填充腔中,從而使溫度損失最小化。
在填充腔中達到了足夠濃度的模製材料的可燃氣體之後,通過與已加熱的填充物接觸而開始燃燒。從鑄模中逸出的粘合劑的燃燒進一步進行並且一直對填充物進行進一步調溫。該過程一直持續,直到從鑄模中僅逸出非常少的粘合劑量,從而不再能在外罩中形成可燃燒的氣氛。但是,熱的填充物現仍按照蓄熱器的類型而將溫度保持在可以導致粘合劑燃燒的臨界溫度以上。鑄模相應地也至少停留在該溫度上,從而使保留在鑄模中的粘合劑殘留物熱分解。
按照本發明的方法特別適用於其鑄模部件和鑄芯由有機粘合劑連接的模製材料組成的鑄模。為此,例如可以使用市售的含溶劑的粘合劑或者通過化學反應而發揮其作用的這類粘合劑。相應的粘合劑系統目前以所謂的「冷箱法(Cold-Box-Verfahren)」使用。
在實踐中,特別是在鑄鐵熔體的加工過程中,700℃的溫度適合作為臨界溫度。在700℃以上特別是有機粘合劑可靠地燃燒。同時,在該溫度下可以使從鑄模中逸出的其他有害物質氧化或者以其他方式處理成無害的。這同樣適用於在鑄模中由於溫度引起的粘合劑分解調整的裂紋產物,該裂紋產物同樣在這樣的高溫下可靠地分解。
通過按照本發明地將已預熱到特定溫度的填充物填充到填充腔中,實現了使填充物由於輸入的過程熱而加熱到位於臨界溫度以上的溫度。實際的試驗已顯示,在填充腔的填充過程中,500℃的溫度作為填充物的最低溫度是足夠的。
伴隨著粘合劑的逸出、燃燒和分解,由模製材料成型的鑄模的部件和鑄芯碎裂成鬆散的碎片,這些碎片可以在去掉外罩之後清除並且可以運送至處理裝置或者以有利的方式已經在澆鑄金屬熔體和去掉外罩之間的停留時間過程中從外罩排出。針對該目的可以將鑄模放置在篩板上並且收集流過篩板的鑄模的碎片。以實際的方式這樣設計篩板的開口,即,鑄模的碎片和填充物共同通過所述篩板流動、收集、處理並且在處理之後相互分離。這樣的優點在於,當取下外罩時,沒有鬆散的填充物還存在於外罩中。
鑄模的外罩可以相應地通過由絕熱且足夠形狀穩定的材料構成的護罩、用作篩板的穿孔的支承板和同樣隔熱的蓋子形成,其中,該護罩以足以形成填充腔的距離圍繞鑄模,鑄模放置在支承板上,蓋子在填充鑄模之後安裝。為了實現填充腔中形成的廢氣的受控地排出,可以額外地設置廢氣開口。
在按照本發明的方法中也可以壓縮填充在填充腔內的填充物,從而在鑄模和外罩之間產生預應力,當鑄模形成作為由多個鑄模部件和鑄芯組成的組合砂芯時,通過該預應力確保鑄模可靠、位置精確的粘結。但是如上所述地,即使在這樣壓縮的填充物的情況下由於較小的松密度仍確保了氣流的流通性。
按照本發明所實現的鑄模的鑄模部件和鑄芯的破壞的效率也可以由此得以提高,即,不僅將填充物而且將鑄模本身都設計成為能夠通氣的。為此可以將目標的通道引入到鑄模中,可以使填充腔中形成的熱廢氣或者相應預熱的含氧氣體流通經過該通道。以這種方式實現了模製材料粘合劑在鑄模內部快速的蒸發、燃燒和其他熱分解。由此額外地加速了鑄模的碎裂。
有針對性地在鑄模中引入的通道另外用於加速冷卻在鑄件上或鑄件內的特定區域或者避免這類加速的冷卻,從而實現鑄件在各個區域中的特定的性能。
在根據本發明的填充材料中,在壓實之後,預應力通過彼此接觸的填充材料的顆粒傳遞。在此為了在按照本發明要求的填充物的通氣性的情況下仍避免填充物的顆粒不受控制地移位,外罩可以在其面向鑄模的內表面上設置有結構化的表面,撞擊該表面的顆粒至少局部地以形狀配合的方式支承在該表面上。
填充物應該同時具有較小的儲熱的能力,由此可以快速地加熱該填充物並且在臨界溫度以上的溫度上保持經過儘可能長的時間。
以理想的方式適用於按照本發明的目的的填充物因此將材料的較小的松密度與較小的比熱容相結合,形成填充物的單個部分由該材料製成。
在此,實際的試驗得出,填充物中的材料的松密度Sd和比熱容cp的乘積P最大為1kJ/dm3K(P=Sd×cp≤1kJ/dm3K),該填充物由該材料製成,其中,乘積P=Sd×cp最大為0.5kJ/dm3K的填充物是特別適宜的。
與是否進行壓縮無關地,顆粒或者其他顆粒狀的散積物證實適合作為填充物。在此,對於按照本發明的目的適宜的是,這類散積物具有最大為4kg/dm3的松密度Sd,特別是小於1kg/dm3或甚至小於0.5kg/dm3。
如果使用顆粒狀的、鬆散的並且能夠流動的填充物,那麼在實際的試驗中被證實為有益的是,顆粒材料具有1.5-100mm的平均直徑,其中,理想地使用其顆粒大小為1.5-40mm的填充物。
在此,由具有最大為1kJ/kgK、理想為小於0.5kJ/kgK的比熱容的材料構成的填充物表現出對於本發明而言理想的加熱和儲熱性能。
原則上所有能夠負荷熱的散積物適合作為填充物,這些散積物滿足上述說明的條件並且是充分熱穩定的。對此適合的特別是非金屬的散積物,比如由陶瓷材料製成的顆粒。這些材料可以不規則地成型、設置成球狀或者具有空腔,從而實現填充在填充腔中的填充物在較小的儲熱性能的同時具有良好的通氣性。填充物也可以由環形或者多邊形的部件組成,這些部件相互僅點狀地接觸,從而在它們之間分別保留足夠的空間以確保良好的流通性。
為了避免通過可選地經氣體入口引導進入外罩的含氧氣流導致填充物冷卻,可以使氣流在其進入填充腔之前加熱到室溫以上的溫度。在此理想的是,氣流的溫度至少處於填充物的最低溫度的水平上。為了加熱氣流例如可以使用從外罩中排出的熱廢氣。為此可以使用已知的熱交換器。如果設置有篩板,鑄模的碎片在必要時連同填充物可以從外罩通過該篩板流出,含氧的氣流也可以通過該篩板引導。這樣不僅具有大面積導入的優點而且還促使輸送的氣流通過與從外罩中流出的熱的模製材料碎片以及同樣熱的填充物接觸而加熱。
替代性或補充地還可以考慮,廢氣流的部分氣流與含氧的氣流混合併且將這樣得到的熱氣流引導回填充腔中。為此適宜的是,引導到填充腔中的含氧的氣流中10-90體積%由廢氣組成。
輸送給填充腔中的含氧的氣流例如可以是環境空氣。
由於通過熱交換而在填充腔內部引起的流通,使輸送給填充腔中的含氧的氣流通過適合的入口吸入到填充腔中。替代性地,當然可以同樣考慮,藉助鼓風機或類似物以一定的壓力將氣流帶入填充腔中。
可以根據從外罩逸出的廢氣體積流量而對引導到填充腔中的氣流進行可選地調節,從而避免產生在填充腔中存在的氣氛的過壓。為此可以為各個氣體入口配備一個根據氣流速度調節供氣的機構。適合於該目的的例如是已知的舌瓣閥門,其可以這樣安裝和負載,以使得經過該舌瓣閥門的氣流的流體壓根據平衡自動地調節流速並因此調節燃燒氣體輸入。
同樣能夠考慮的是,在廢氣出口上進行廢氣測量並且根據該測量的結果來調節含氧的氣流,從而確保粘合劑的完全燃燒並且確保其他可能從鑄模逸出的氣體在填充腔中的完全燃燒。
在按照本發明的方法中也可以由此實現有害物質排放的最小化,即,外罩配備有用於分解粘合劑的燃燒產物中所含的有害物質的催化裝置。
在按照本發明脫模之後取出的鑄件可以在鑄模碎裂之後進行熱處理,其中該鑄件按照特定冷卻曲線的標準而以已知的方式受控制地冷卻,從而產生鑄件的特定狀態。
在按照本發明的方式中,當然可以同時將多個鑄模設置在一個外罩中並且使這些鑄模平行地或者在時間上緊密地以依次相鄰的順序填充有金屬熔體。
按照本發明的方法原則上適用於各種類型的金屬鑄造材料,在這些金屬鑄造材料的加工過程中產生足夠高的過程熱。按照本發明的方法特別適用於製造由鑄鐵組成的鑄件,因為由於鑄鐵熔體的高溫能夠特別可靠地達到用於粘合劑燃燒的、按照本發明規定的溫度。特別是可以以按照本發明的方式加工GJL、GJS和GJV鑄鐵材料以及鋼鑄件。
如果在此談及按照本發明使用的鑄模由模製材料成型的鑄模部件或鑄芯組成,那麼當然包括這種可能性,即,在這類鑄模中由其他材料製成單個部件,比如冷鑄型、支承體和類似物。重要的僅在於,鑄模含有這樣一定體積的模製材料,即,在澆注熔融金屬的過程中導致粘合劑的蒸發,該粘合劑隨後在填充腔中燃燒,並且將填充物加熱到這樣的程度,即,將溫度在臨界溫度以上保持經過足夠長的時間以確保模製材料的粘合劑儘可能地完全分解。
從根據本發明設置的外罩中流出的廢氣流的清潔可以這樣實現,即,仍存在於廢氣中的可燃物質隨後在廢氣燃燒過程中後續燃燒。在此釋放的熱量又可以用於預熱引導到外罩中的含氧氣流。
如果通過多個根據本發明的鑄模以根據本發明的方式平行地依次形成鑄件,那麼可能適宜的是,鑄模與與其對應的外罩一起布置在通道或類似物中並且形成的廢氣通過共同的廢氣管道排出。
根據本發明的方法特別適用於大批量地製造內燃機的汽缸體曲軸箱和氣缸蓋。特別是在所涉及的部件特定用於商用車輛的情況下,這些部件及其製造所需的鑄模具有相對較大的體積,在這種情況下根據本發明的方法的優點特別顯著地發揮作用。
通常,根據本發明獲得的芯砂碎片在它們從外罩中排出時仍是較熱的,以使得它們可以在常規的粉碎機中粉碎而不需要額外的供熱。如果芯砂碎片以與填充物的混合物的形式存在,則在粉碎後進行分離。這是非常簡單的,因為在粉碎之後獲得的芯砂的顆粒大小遠小於填充物的顆粒大小。因此,粉碎機在此可以設計成,其促使芯砂的機械預處理。這樣的預處理可以例如包括,通過芯砂與填充物顆粒的接觸而增加砂粒的表面粗糙度並因此在隨後的鑄模部件或鑄芯的加工期間改善粘合劑在芯砂上的粘合。
在處理之後所得到的再生砂可以以已知的方式與新砂混合。
附圖說明
隨後藉助示出一個實施例的附圖進一步說明本發明。這些附圖分別示意性示出了:
圖1為示出了按照本發明的過程的流程圖;
圖2-8分別以沿縱軸的截面圖示出了在按照本發明的方法的實施過程中的不同階段的熱反應器;
圖9以對應於圖2-8的視角示出了為了取出鑄件而打開的熱反應器;
圖10示出了用於冷卻鑄件的裝置;
圖11示出了製成的鑄件;
圖12以對應於圖2-8的視角示出了熱反應器的收集容器;
圖13以橫向於其縱軸的截面圖示出了用於芯砂再生的破碎工具;
圖14以對應於圖2-8的視角示出了用於鑄造鑄件的鑄模;
圖15以對應於圖2-8的視角示出了填充有填充物的儲備容器。
具體實施方式
圖1作為實施按照本發明的方法過程中產生的循環的圖表而示出。在此由模製材料組成的鑄模部件和鑄芯開始,該模製材料由新的、目前未使用的芯砂(例如石英砂)和常規的粘合劑(例如市售的冷箱粘合劑,「Cold-Box-Binder」)混合而成。同樣地使用新的填料,例如具有1.5-25mm的平均顆粒大小的陶瓷顆粒,在第一次使用時,在能夠使用之前必須將該陶瓷顆粒加熱至要求的最低溫度,例如500℃。另外,在該循環中的初始材料可以如下所述地再次利用。
在圖2-8中示出的在按照本發明的方法的不同階段的熱反應器T具有一個篩板1,用於倒出鑄鐵熔體而準備的鑄模2放置在該篩板上。該鑄模2特定用於鑄件G的大規模製造,在該例子中該鑄件涉及一種用於商用車輛內燃機的氣缸體曲軸箱
該鑄模2以常規的方式作為組合砂芯(Kernpaket)由多個外部設置的外芯或鑄模部件和設置在內部的鑄芯組成。額外地,該鑄模2可以包含由鋼或者其他不可破壞的材料組成的組件。這些組件例如為設置在鑄模2中的冷鑄型和類似物,從而通過加速凝固分別與冷鑄型接觸的熔體而實現定向地凝固鑄件G。
鑄模2相對於周圍環境U限定了使鑄鐵熔體澆鑄到其中從而形成鑄件G的鑄模空腔3。在此,鑄鐵熔體經過澆鑄系統(Anschnittsystem)流入鑄模空腔3,該澆鑄系統在此為了清除起見沒有示出。
鑄模2的芯和鑄模部件以常規的方式以冷箱法由常規的模製材料製成,其涉及由市售的芯砂、同樣市售的有機粘合劑或可選加入的添加劑組成的混合物,添加劑例如用於使芯砂的顆粒通過粘合劑更好的潤溼。由模製材料成型鑄模2的鑄芯和鑄模部件。隨後得到的鑄芯和鑄模部件加載有反應氣體,從而通過化學反應使粘合劑硬化並由此賦予芯和鑄模部件必要的形狀剛性。
篩板1以其邊緣支承在收集容器5的環形的邊緣凸肩4上。在邊緣凸肩4的環形的支承面中嵌入密封部件6。
在將鑄模2定位在篩板1上之後,將同樣屬於熱反應器T的外罩7放置在收集容器5的環形的邊緣凸肩4上。該外罩7根據保護罩的類型而形成並且在鑄模的外周面8上罩住該鑄模2。在此,由外罩7所圍繞的空間的外周相對於鑄模2的外周具有多餘部分,從而在將外罩7安裝在篩板1上之後在鑄模2的外周面和外罩7的內周面9之間形成填充腔10。該外罩以其對應於收集容器5的邊緣位於密封部件6上,從而在此確保了填充腔10相對於周圍環境U的密封封閉。該外罩由隔熱的材料製成,該材料由多個層組成,其中,一個層確保外罩7的必要的形狀穩定性而另一個層確保了熱隔離。外罩7在其上側具有較大的開口11,通過該開口可以使鑄模2填充有鑄鐵熔體並且使填充腔10填充有填充物F(圖3)。
為了使填充腔10填滿作為顆粒狀的顆粒材料形成的並加熱到至少500℃的溫度Tmin的填充物F,將儲備容器V在該開口11上定位,隨後使熱的填充物F從該儲備容器通過分配系統12緩緩流入填充腔10(圖4)。
當填充過程結束時,在必要時密封填充在填充腔10中的填充物包。隨後將蓋子13放到開口11上,該蓋子同樣具有開口14,通過該開口可以使鑄鐵熔體填充到鑄模2中(圖5)。
隨後進行鑄鐵熔體向鑄模2中的澆鑄(圖6)。
與此同時,含氧的環境氣體可以經過外罩7的下邊緣區域中成型的氣體入口15進入填充腔10。同樣地,通過收集容器5中的通入口16進入的環境空氣穿過篩板1進入到填充腔10中(圖7)。
隨著鑄鐵熔體的澆鑄而產生的鑄造模具2的所期望的損壞和與之伴隨的鑄件G的脫模分兩個階段進行。
在第一階段中蒸發包含在粘合劑中的溶劑。從鑄模2中逸出的蒸汽狀的溶劑在填充腔中達到一個濃度,在該濃度下溶劑自動點燃並且燃燒。通過此處釋放的熱量使顆粒狀的、已經在約500℃的溫度Tmin的填充物F加熱到超過700℃的極限溫度T臨界,直到其溫度達到近900℃的最高溫度Tmax。
如果從鑄模2蒸發出的粘合劑組分的濃度對於自燃而言是不足夠的,這樣加熱的填充物具有蓄熱器的功能,通過該蓄熱器使鑄模2的溫度和填充腔10中的溫度保持在位於700℃的極限溫度T臨界以上的水平。以這種方式使從鑄模2中逸出的粘合劑組分以及其他潛在的有害物質的燃燒持續進行,直到不再從鑄模2中蒸發出粘合劑為止。可能仍持續從鑄模2中逸出的蒸汽狀的物質通過填充腔10中的高溫氧化或者以其他方式變成無害的。
同樣地,含氧的、由環境空氣形成的氣流S1,S2促使從鑄模2中逸出氣體的徹底燃燒,這些氣流通過氣體入口15和篩板1進入外罩7的填充腔10。
由於填充物F的松密度較低,以至於即使在密封之後仍能確保存在於填充腔10中的填充物包的良好的氣體通過性,因此確保了從鑄模2中逸出的氣體與提供用於燃燒的氣流S1,S2的氧氣良好的混合。同時,填充腔10中的填充物包在鑄模的外周面上支承鑄模2並因此防止了鑄鐵熔體的折斷。
從鑄模2中逸出的氣體通過填充物F的流通促使了與所輸送的氣流S1,S2的良好的混合、較長的停留時間以及良好的反應能力。鑄模2既可以通過粘合劑系統的燃燒和澆鑄到鑄模2中的金屬引入的熱量而加熱也可以通過預熱的填充物F加熱。這可能導致的結果是,幾乎完全破壞將鑄模2的鑄模部件和芯連接在一起的粘合劑系統。因此,鑄模部件和芯碎裂成碎片B或者單個的砂顆粒。
碎片B和鬆散的砂通過篩網1而落入收集容器5中並在此收集。在此,篩網1可以與鑄模2的碎裂進行無關地打開,從而使填充物F也進入收集容器5中(圖8)。
為了理想地燃燒從鑄模2中逸出的氣體並且為了使已經在外罩中的芯砂再生,填充物F的溫度和在填充腔10中流通的氣體的溫度理想地分別顯著地高於700℃。為此這樣設計熱反應器T中的條件,即,使再生過程和廢氣處理不依賴於設備可用性而獨立地進行。確定的和設定的大小為填充物F的起始溫度、通過氣體入口15和通入口16流動的含氧的氣流S1,S2以及鑄模2本身。
鑄模2的碎裂的進行與澆鑄到鑄模2中的鑄鐵熔體的凝固過程這樣相互適應,以使得在鑄模2碎裂時鑄件G已充分凝固。
在鑄模2基本上完全碎裂之後,收集容器5與其中含有的模製材料-填充物混合物通過篩板1分離並且外罩7也從篩板1上取下。現可以任意地觸及儘可能產生的鑄件G並且可以在為此預設的通道形的空腔17中受控地冷卻(圖10)。該鑄件G由於該過程而在取出過程中具有較高的溫度,其中,奧氏體轉換尚未結束而且快速的冷卻可能導致內應力並由此導致裂紋。出於這個原因,使鑄件G在冷卻通道17中對應於消除應力退火的退火曲線而緩慢地冷卻。這樣定量輸入的冷卻空氣,即,實現與產品相關的冷卻曲線(Abkühlprofil)。
收集容器5中含有的由填充物F、芯砂和碎片B組成的混合物在破碎工具18中充分混合併且摻入充足的氧化氣體,從而儘可能地後續燃燒仍存在的粘合劑殘留,該破碎工具例如為轉筒。在該過程階段中,填充物F也可以與芯砂分離並且二者輸送至單獨的冷卻。這樣的再生確保了可靠保持粘合劑系統的完全燃燒並且為了再用作芯砂而額外地通過機械摩擦提供用於粘合劑的良好的粘附的芯砂表面。
所獲的芯砂幾乎冷卻到室溫並且在再次加工成為鑄模部件或鑄芯的組分分離之後供應給新的鑄模2。
相對地,將填充物F冷卻至預設的起始溫度Tmin並且在循環中為了填充腔10的再次填充而填充到儲備容器V中。
作為氣流S1,S2導入填充腔10中的燃燒氣體的量通過可機械調整的活門或滑閥而調節,通過活門或滑閥可以調節氣體入口15或通入口16的開口截面。相應調整可以首先通過化學計量所需的用於粘合劑系統燃燒所需的空氣量而確定並隨後通過測定在此通過蓋子13的開口14形成的廢氣出口19上的CO、NOx和02而精調,該廢氣出口在蓋子13中成型並且在填充腔10中產生的廢氣通過該廢氣出口從外罩7中排出。
從圖16可以看出,通過溶劑從鑄模2的粘合劑系統的蒸發和鑄模2的其他蒸發而在澆鑄之後立即在填充腔10中達到了通過K有害物質曲線示出的高有害物質濃度,該有害物質濃度本身在室溫下自主地燃燒。臨界K臨界在圖16以虛線給出,由該臨界開始在室溫下達到能夠燃燒的有害物質濃度。但是,由於較高的500℃的最低溫度Tmin,由鑄模2進入填充腔10的氣體的燃燒在明顯更低的濃度下已經開始(參見圖16),其中,該最低溫度通過在此引入的熱的填充物F而產生。
通過在階段1中在顆粒材料內部的燃燒使顆粒材料加熱並且填充物溫度T填充物在短時間後超過700℃的臨界溫度T臨界,在該臨界溫度下有機材料以已知方式在充足的氧含量下自發氧化並因此燃燒。溫度T填充物的變化在圖16中以虛線示出。
從鑄模2中蒸發出的粘合劑的劇烈燃燒的階段(「階段1」)持續到從鑄模2進入填充腔10的有害物質濃度K有害物質基本上通過可蒸發的粘合劑形成的可燃氣體而顯著降低到室溫下不再能進行燃燒為止。
通過大於700℃的較高的填充物溫度如上所述地使氧化或燃燒在接下來的階段2中仍持續,其中,在此釋放的熱量足夠將填充物10的溫度進一步提高至最高溫度Tmax。填充物10保持在溫度上,直到鑄模2的破裂進展到不再有明顯的出氣發生為止,該鑄模2破裂成小塊並且模製材料殘留物掉落到容器5中。但是,只要在填充腔10中進行燃燒過程,在此總是依然產生足夠的熱量使填充物F在足夠長的持續時間內保持在一定範圍內,該範圍的上限為溫度Tmax而其下限為溫度T臨界。
因此,按照本發明通過選擇填充物填入填充腔10時所具有的溫度這樣確定超過700℃的臨界溫度T臨界的時間點,即,在由於較低的有害物質濃度K有害物質而在填充腔10內不再可靠地以必要的強度發生燃燒過程之前就已經達到了該臨界溫度。隨後,較高加熱的填充物F確保,仍從鑄模2蒸發出的氣體進行分解和剩餘燃燒,即使在位於溫度T臨界以下的溫度的條件下在填充腔中存在的可燃氣體的濃度也過小。
能夠證實的是,通過鑄模2中所含的可蒸發的且可燃的物質為燃燒提供足夠多的化學能,以使得填充物溫度可以達到遠高於1000℃。在這種情況下,可能使澆鑄的冷卻延長,從而可能需要較長的停留時間。這也可能通過將填充物F填入填充腔10所具有的起始溫度而確定。同樣可以通過提高作用為冷卻空氣的氣流S1,S2防止過強的溫度升高。
填充物F的選擇過程中(例如為陶瓷填充物)應注意,填充物F的單個顆粒具有較高的壓強度,從而在澆鑄過程中接受壓力並在循環中保持儘可能少的摩擦損失。另一個選擇標準為填充物F的較小的熱容與松密度的結合,從而由階段1儘可能快地獲得超過700℃的溫度升高。在相適應的燃燒氣體輸入和相對較低的溫度下,通過在散積物(Schüttgut)中的氧化避免了氮氧化物形成。
因為排出的廢氣按照本發明基本上本身在第一階段中加熱散積物,在散積物內部產生了確保較徹底燃燒的溫度特性。燃燒氣體由於在填充腔10中產生的熱對流而沿垂直方向向上並且有害物質從鑄模2中的排出由於較強的蒸汽形成而在第一階段中沿著水平方向進入填充物包中。通過在填充物F內部氣流的交叉確保了良好的混合。
在鑄模2上方的區域中,氣流於是相同取向並且在從澆鑄漏鬥上方的廢氣出口19離開之前可以在蓋子13和填充物F之間的燃燒空間中在廢氣的最熱區域中充分地後燃。
在示例計算中,基於表1中給出的針對根據本發明的方法的參數和材料值確定通過熔體的冷卻和粘合劑的燃燒所釋放的熱能Qa以及用於填充物加熱以及用於鑄模的芯砂加熱所需的熱能Qb。
由此出發,作為熔體,將灰口鑄鐵熔體澆鑄到鑄模中,該鑄模的注模部件和鑄芯以常規的冷箱法由模製材料製成,該模製材料由常規的芯砂(例如石英砂)和針對該目的同樣市面可購買到的粘合劑組成。
此外,為了簡化已經假設鑄造金屬在鑄造之後將其熱量傳遞到鑄模和填充物上並且所使用的粘合劑中潛在的化學能以燃燒能的形式完全可用於加熱填充物。
為了熔體的凝固而排散的熔體熱Hfus於是根據公式
Hfus=m熔體×hfus×1/1000MJ/kJ
計算,因此在該例子中
Hfus=170kg×96kJ/kg×1/1000MJ/kJ=16.3MJ。
在其冷卻過程中從熔體中釋放的熱能Qal於是根據公式
Qal=cp×ΔΤ×m×1/1000MJ/kJ–Hfus
計算,在該例子中
ΔΤ=(Tl-T2)=(850K-1500K)=-650K
Qal=950J/kgK×-650K×170kg×1/1000MJ/kJ–16.3MJ
Qal=-121MJ。
在相應的計算中,通過模製材料中所含的粘合劑的燃燒釋放的熱量Qa2根據公式
Qa2=hi×m粘合劑×(-1)
即,
Qa2=30MJ/kg×4kg×(-1)=-120MJ。
於是釋放的熱能的總和Qa=Qal+Qa2為-241MJ。
將鑄模的芯砂由溫度T1加熱至溫度T2所需的熱能Qbl根據公式
Qbl=cp芯砂×(T2-Tl)×m芯砂計算,
即,
Qbl=835J/kgK×(800K-20K)×255kg=166[MJ]。
同樣,將鑄模的芯砂由溫度T1加熱至溫度T2所需的熱能Qb2根據公式
Qb2=cp填充物×(T2-Tl)×m填充物計算,
即,
Qb2=754J/kgK×(800K-500K)×125kg=28[MJ]。
為了將加熱初始在20℃的室溫下鑄模的芯砂和以500℃的溫度T1填充的填充物加熱至800℃的最終溫度T2所需的熱能為Qb=Qbl+Qb2,即,總共Qb=166MJ+28MJ=194MJ。
因此,利用表1中所述的參數,由於通過熔體的熱輸入和從鑄模中逸出的粘合劑的燃燒,提供47MJ的多餘能量用於加熱填充物F,並用於補償公差和損失。
在表1所示的在灰鑄鐵熔體的澆鑄過程中可達到的能量平衡的確定表明,在使用基於常規粘合劑系統和在使用由石英砂製成的、常規模製材料的條件下,存在明顯的熱能的產能過剩。在這種考慮中,忽略所輸入的含氧的氣流S1,S2,因為它們在能量方面的影響非常小。
在表2中,針對不同的散積物給出了松密度Sd、比熱容cp和乘積P=Sd×cp,這些散積物在其溫度穩定性方面基本上適合用作填充物。可以看出,例如鋼粒,雖然具有比在此談及類型的陶瓷顆粒明顯更低的比熱容cp,但具有明顯過高的松密度,從而確保在填充腔中圍繞鑄模預設的填充物包的根據本發明規定的氣體滲透性。
附圖標記列表
1 篩板
2 鑄模
3 鑄模空腔
4 環形的邊緣凸肩
5 收集容器
6 密封部件
7 外罩(外殼)
8 鑄模2的外周面
9 外罩7的內表面
10 填充腔
11 外罩的開口
12 分配系統
13 蓋子
14 蓋子13的開口
15 氣體入口
16 通入口
17 冷卻通道
18 粉碎工具
19 廢氣出口
B 碎片
F 填充物
G 鑄件
S1,S2 含氧的氣流
T 熱反應器
U 周圍環境
V 儲備容器
表1
表2。