水溶結合鹼溶從電解槽廢陰極炭塊中提取碳的方法與流程
2023-10-11 04:07:34 2
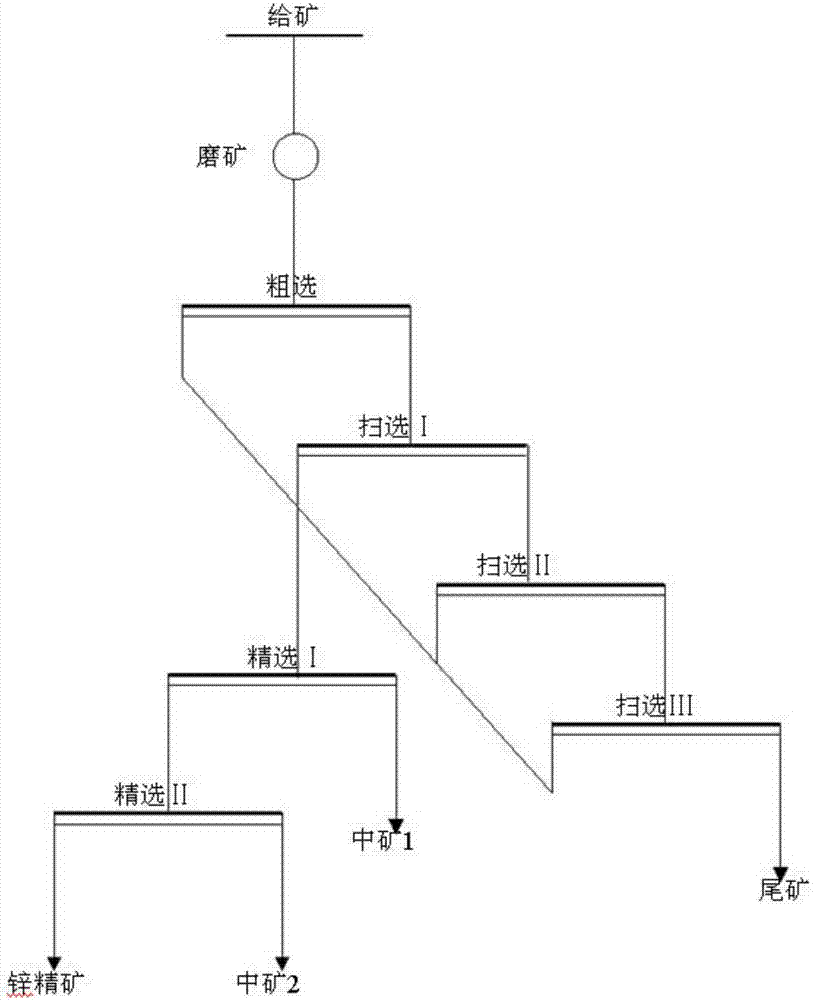
本發明涉及電解槽廢陰極炭塊綜合利用技術領域,具體涉及一種水溶結合鹼溶從電解槽廢陰極炭塊中提取碳的方法。
背景技術:
鋁電解槽一般在使用4到5年後需進行大修,我國多數企業平均槽壽命在1500天左右,大修時清除大量的廢陰極炭塊。現有技術中,對鋁電解槽廢陰極炭塊的處理方法主要是在廢陰極炭塊中加入石灰使之與其中的電解質發生反應,得到氟化鈣、氟化鈉和氟化鋁,使氟得到固化以重新利用,回收的炭重新用於製造陰極材料,但處理費用太高。或者利用水泥窯爐內部反應溫度高,炭塊在流程中停留時間長等條件,使廢陰極炭塊中的有害物質在高溫環境中進行分解置換,並最終固化在水泥熟料中,同時廢陰極炭塊中的碳作為燃料降低了煤的消耗。但是,採用該方法的缺點也非常明顯氟對耐火磚有損害,並且氟容易隨煙氣排放入空氣造成大氣汙染;廢陰極炭塊中鈉的含量極高,會對水泥後期強度有影響。
中國專利文獻公開號為105586607a、名稱為一種廢陰極炭塊的利用方法的專利申請文件提供了這樣一種廢陰極炭塊利用的技術方案,其利用過程是將鋁電解槽大修停槽刨除的廢陰極炭塊,進行粗碎、細碎、篩分、分選,得到廢陰極炭塊中炭質顆粒和電解質顆粒,其中的炭質顆粒用於鋁用陰極炭塊生產原料,電解質顆粒返回鋁電解生產過程。
中國專利文獻公開號為101798691a,名稱為一種回收鋁電解槽廢陰極的方法的專利申請文件提供了這樣的技術方案,包括如下步驟:1)清理廢陰極碳塊表面粘連的耐火材料、保溫材料;2)將廢陰極碳塊破碎成1~6mm的顆粒;3)採用上述破碎後的廢陰極碳塊顆粒通過焦粒焙燒啟動法對大修後的電解槽進行預焙;4)回收預焙後的殘留顆粒;5)分離殘留顆粒中的灰分;6)將回收的殘留顆粒作為氟化鹽返鋁電解槽使用。
中國專利文獻公開號為101440500,名稱為電解鋁大修槽產生的廢陰極碳塊的處置方法提供了這樣的技術方案:它是將電解槽大修產生廢渣中分選出來的廢陰極碳塊用機械破碎成粉料後,加入氧化鋁廠燒結法系統中進行配料,然後與生料漿一起進入燒成車間迴轉窯中進行熟料燒結。
然而經研究表明,廢陰極碳塊廢渣碳元素含量較高,可以達到66.07%,其它元素中以氟、鈉、鋁含量較高,是該廢渣的主要雜質,其中的氰根含量達到8.7ppm,已超出國家排放標準。因此,對廢陰極碳塊廢渣的回收利用在於碳的回收。然而以上公開的現有技術,均沒有對廢陰極中碳的回收提出理想的技術方案。
技術實現要素:
本發明提供了一種水溶結合鹼溶從電解槽廢陰極炭塊中提取碳的方法,以解決電解槽廢陰極炭塊的綜合利用問題。
本發明提供了如下技術方案:
一種水溶結合鹼溶從電解槽廢陰極炭塊中提取碳的方法,該方法是先進行磨礦,然後進行水溶出,對水溶條件下得到的水溶渣用naoh進行鹼浸出。
其中,磨礦時磨礦細度為-200目,捕收劑採用柴油,起泡劑採用2#油,抑制劑採用水玻璃。所述水溶出工藝條件為:液固比2-4:1、溫度18-25℃、時間50-80min。所述鹼浸出工藝條件為:液固比3-5:1、溫度40-60℃、時間50-70min、naoh用量160-185g/l。
優選的,還可以再對鹼浸出後的渣相取樣用鹽酸或硫酸進行酸浸出,最後進行碳含量的檢測。
這裡採用鹽酸和硫酸浸出分別提供兩種提取碳的方案:
第一種方案,先採用水溶,水溶出最佳工藝條件:液固比3:1、溫度20℃、時間60min;水溶後進行鹼溶,鹼浸出最佳工藝條件:液固比4:1、溫度50℃、時間60min、naoh用量175g/l;然後採用鹽酸進行酸溶,鹽酸酸浸出最佳工藝條件:hcl(濃度37%):h2o=3:1、液固比=3:1、溫度80℃、時間60min;溶出後檢測碳含量可達到89.9%。
第二種方案,先採用水溶,水溶出最佳工藝條件:液固比3:1、溫度20℃、時間60min;水溶後進行鹼溶,鹼浸出最佳工藝條件:液固比4:1、溫度50℃、時間60min、naoh用175g/l;然後採用硫進行酸溶,硫酸浸出最佳工藝條件:h2so4(濃度98%):h2o=3:1、液固比=3:1、溫度80℃、時間60min;溶出後檢測碳含量可達到90%。
本發明達到的有益效果:通過本發明的技術方案,可以將電解槽廢陰極炭塊中的碳含量,從65%左右,提升至90%左右,從而實現對電解槽廢陰極炭塊中碳的回收利用。
附圖說明
圖1是廢陰極炭塊xrd譜圖;
圖2是本發明的選礦法提取碳工藝流程圖;
圖3是水溶後產物xrd物相圖;
圖4是硫酸溶出後產物的物相組成示意圖;
圖5是鹽酸溶出後固體物相及相對含量示意圖。
具體實施方式
下面結合附圖和實施例對本發明作進一步的詳細說明。本發明及以下實施例中有關數量份數、百分比、數量比例等,若無特殊說明,均指質量單位。
首先,本發明的採用xrd技術確定廢陰極炭塊中各元素的存在形態,對該廢渣進行了xrd分析,其譜圖如圖1所示。從原樣的xrd譜圖可以得出,該樣中主要汗有碳、氟化鈉、六氟鋁酸鈉、共晶鋁鈉氧化物、共晶鐵鈉氰化物以及氟化鈣。
經過對廢渣各物相含量分析可知,在廢陰極炭塊中,naf的含量約佔12%,c的含量約佔66%,na4fe(cn)6的含量約佔2%,naal11o17的含量約佔3%,al2na6f12的含量約佔16%,caf2的含量約佔16%。
本發明通過以下實施例的實驗,實現從上述廢陰極炭塊中提取碳。
實施例1:電解槽廢陰極炭塊可磨性
邦德功指數測定:根據要求,試驗首先測定原礦-200目(0.074mm)邦德功指數。磨礦循環負荷按250%,預計篩下產品質量為237g。試驗結果列於表1。
表1原礦-200目(0.074mm)邦德功指數測定試驗結果
說明:表中gbp即為每轉淨產生-0.074mm產品質量,下同。
試驗進行一組後,發現相對於與以往試驗,本次磨礦gbp值明顯偏小,計算的第二次磨機轉速需1396轉,遠大於一般礦石的正常水平。分析認為,由於原礦難磨,且原礦細粒產品在磨礦當中會起到阻磨的作用,對幹磨幹擾巨大,導致在磨礦進行到一定程度後剩餘粗粒產品難以進一步被磨細。鑑於上述結果,試驗考慮將目的產品粒度調整為-100目(0.15mm),再進行邦德功指數測定,試驗結果列於表2。
表2原礦-100目(0.15mm)邦德功指數測定試驗結果
由表2試驗結果可見,當調整目的磨礦細度後,試驗gbp值任然遠小於正常值,並且隨磨礦轉數的增加急劇降低。當試驗進行到第三組時,計算磨機轉數為6838轉,根據以往試驗經驗,其遠大於正常值。分析試驗結果,試驗認為該礦在幹磨過程當中,隨磨礦時間的延長,可能存在磨礦效率急劇降低的情況,為此試驗進行了驗證試驗,試驗以磨礦轉數為變量,以-200目產品產量為判據,試驗結果列於表3。
表3磨礦驗證試驗結果
由表3結果可以看出,在同樣的條件下,磨機轉數從100轉增加到300轉,-200目產品量僅增加了0.2g,在試驗系統誤差內可以忽略不計,即從100轉至300轉之間,磨機磨礦效率為零。
實施例2:選礦法提取碳
試驗對鋁電解廢陰極炭塊原礦進行了浮選初步探索試驗,考察原礦的可選性能。對原礦的多元素分析表明,原礦含c固(固定碳)為67.83%,原礦水溶性鹽含量較高,經試驗測定其含量為9.60%。
為探索該礦的可選性能,試驗進行了初步的浮選捕收劑及起泡劑條件試驗、抑制劑及調整劑條件試驗及磨礦細度條件試驗,工藝流程如圖2所示。
1)捕收劑及起泡劑條件試驗
石墨浮選常用捕收劑為煤油、柴油等,常用起泡劑為2#油、4#油等。本實施例的條件試驗在磨礦細度在-200目90%左右進行,捕收劑及起泡劑主要採用石墨浮選常規藥劑(其中98#油為浮選起泡劑,其起泡性能強於2#油,並且具有一定捕收性能)。
2)抑制劑及調整劑條件試驗
石墨浮選常用抑制劑及調整劑有石灰、碳酸鈉、水玻璃等,本次試驗原礦含有一定量的黃鐵礦,添加石灰有助於提高對黃鐵礦的抑制效果。本次抑制劑及調整劑條件試驗採用石墨浮選常用藥劑,其它試驗條件為:磨礦細度-200目90%、捕收劑選用柴油、起泡劑選用2#油。
試驗原礦呈鹼性,在不添加任何藥劑的情況下,礦漿ph可達到9~10,試驗表明在此條件下原礦中的黃鐵礦對石墨浮選影響較小,添加石灰後浮選泡沫粘度提高,導致精選困難;適量添加水玻璃有助於改善礦漿分散性能,並對脈石有一定的抑制效果,有利於提高浮選效率。
3)磨礦細度條件試驗
本次原礦為無定型石墨礦,該類型礦石石墨與脈石礦物嵌布關係複雜,浮選困難,因此選擇適宜的磨礦細度保證磨礦單體解離度,對該礦的浮選影響較大。為此試驗進行了一組磨礦細度條件試驗,其它試驗條件為:抑制劑選用水玻璃、捕收劑選用柴油、起泡劑選用2#油。
試驗結果說明,在較粗的磨礦細度下原礦浮選分選效果較差,在磨礦細度達到-200目100%後,浮選效果有所改善。
4)結論
本實施例採用的鋁電解槽廢陰極炭塊原礦為無定型石墨,原礦品位較高但可選性較差。對原礦的浮選探索試驗表明,對原礦進行浮選,可以在一定程度上提高精礦品位。但在常規的磨礦細度及藥劑制度下,獲得的選別指標相對不太理想。
實施例3:酸溶出工藝提取碳
1)水溶出實驗結果
在試驗中,主要考察液固比、溫度、時間、顆粒粒徑等參數對電解槽廢陰極炭塊中的si、f、al和c元素的溶出率。水溶後產物xrd物相圖如圖3所示,水溶後產物xrd物相表如下表5所示。
表5水溶後產物xrd物相表
本發明發現,在溶出過程中,各因素對氟化鈉的溶出率影響較大,工藝段主要溶出物為氟化鈉。在溶出過程中,各因素對碳、六氟鋁酸鈉、共晶鋁鈉氧化物、共晶鐵鈉氰化物以及氟化鈣的溶出率影響較小,在工藝段中基本不溶出。
2)硫酸溶出實驗結果
在探索初步實驗的基礎上已完成剩餘酸溶出的單因素實驗,主要完成了酸的用量、液固比、溶出溫度、溶出時間、對渣中各元素的溶出效果的影響;硫酸溶出後產物的物相組成如圖4所示。
本發明發現在硫酸溶出過程中,各因素對水溶出後渣中的六氟鋁酸鈉的溶出率影響較大,工藝段主要溶出物為六氟鋁酸鈉。
在溶出過程中,各因素對碳、共晶鋁鈉氧化物、共晶鐵鈉氰化物以及氟化鈣氟化鈉的溶出率影響較小,在工藝段中基本不溶出。
3)鹽酸溶出實驗結果
本實施例鹽酸溶出實驗採用如下工藝條件:使用濃度為30%hcl溶出,固液比1:3,溫度80℃,時間1h。
實施結果:試樣減重為17.3%,碳含量為90.4%。
同時,本實施例對鹽酸溶出的固體產物進行了物相鑑定,結果如圖5和下表6:
表6鹽酸溶出後固體物相表
本發明發現在鹽酸溶出過程中,各因素對水溶出後渣中的六氟鋁酸鈉的溶出率影響較大,工藝段主要溶出物為六氟鋁酸鈉。其次,鹽酸溶出能溶出部分氟化鈣。
在溶出過程中,各因素對碳、共晶鋁鈉氧化物、共晶鐵鈉氰化物以及氟化鈉的溶出率影響較小,在工藝段中基本不溶出。
4)硫酸溶出正交實驗結果
如下表7所示:
表7硫酸溶出正交實驗結果表
從正交實驗結果看,實驗重複性較好,在最佳條件下,經水洗和硫酸溶出後,碳的含量可以有原樣的66%提高到89.62%。
實施例4:鹼溶出工藝提取碳
本發明採用鹼溶出工藝提取碳,是基於發現電解槽廢陰極炭塊中具有含量較高的電解質na3alf6,通過鹼浸出能使其溶解到浸出液中,達到其脫離固體混合物,使混合物的成分變少,達到碳比例提高的目的。
本實施例探索了液固比分別為3:1、4:1、5:1、6:1時,各元素的溶出質量,以及電解槽廢陰極炭塊中碳的含量。實驗操作在naoh用量為175g/l,浸出時間為60min,浸出溫度為50℃的條件下進行,取水溶最佳條件溶出渣樣10g,控制液固比分別為3:1、4:1、5:1及6:1,然後進行溶出實驗。溶出結束後對al、si、fe、f、c等元素的溶出質量,以及電解槽廢陰極炭塊中碳的含量進行測量分析。
我們可以分別找出各元素的最佳溶出液固比。即f元素的最佳溶出固液比為4:1;在實驗固液比變化範圍內,si元素的最佳溶出固液比越大越好;al元素的最佳溶出液固比為5:1;fe元素的最佳溶出液固比為5:1。
而鹼浸出後的渣相中的各元素的含量,經檢測分析後,具體結果如下列各表:
表8液固比為3∶1時渣相中各元素的含量及溶出率
表9液固比為4∶1時渣相中各元素的含量及溶出率
表10液固比為5∶1時渣相中各元素的含量及溶出率
表11液固比為6∶1時渣相中各元素的含量及溶出率
表8到表11表明了渣相中各元素的存留含量,由此可以看出鹼浸出的浸出效果。因渣相中si、fe元素的含量整體相對較低,故可以得出結論,鹼溶液可以較好除去渣相中的si、fe元素,從而提高電解槽廢陰極炭塊中碳的含量。同時,對比各表中的數據,可以準確得到各元素的最佳液固比。
本實施例的實驗還發現,鹼浸礦樣的減重率隨液固比的增大呈現先增大,於液固比4∶1後趨於平緩的趨勢。另外,碳含量隨液固比的增大呈現先降低後增大再降低的趨勢,在液固比變化範圍內出現最佳值,液固比為5∶1時,碳含量達到最大,為83.44%。而且不同液固比下,碳含量的變化不大,變化範圍在1.4%內,故液固比對碳含量的影響不大。
本實施例以最佳水溶條件下的溶出渣樣為樣品進行不同溫度下的鹼浸出實驗。取水溶最佳條件溶出渣樣10g,在液固比為4:1、浸出時間為1h、naoh濃度為300g/l的實驗條件下,考查不同浸出溫度(25℃、30℃、40℃、50℃及100℃)下電解槽廢陰極炭塊中碳的含量。
實驗結束後,對鹼浸出液中各元素的含量進行了檢測與的分析,本實施例發現,在實驗溫度範圍內,si、al、fe元素的濃度均隨著溫度的增加呈現先降低後增加的趨勢(al元素的溶出濃度在增加後又有所降低),且均是在室溫條件下,即溫度為25℃時具有較高浸出濃度,故si、al、fe元素的最佳溶出溫度為25℃。其中,f元素的溶出濃度隨溫度增加呈現先降低後增加而後降低的變化趨勢,在溫度為50℃時達到最佳溶出溫度。
在實驗分析中同樣對鹼浸出後的渣相中的各元素的含量進行了檢測與分析,具體結果如下列各表:
表12溫度為25℃時渣相中各元素的含量及溶出率
表13溫度為30℃時渣相中各元素的含量及溶出率
表14溫度為40℃時渣相中各元素的含量及溶出率
表15溫度為50℃時渣相中各元素的含量及溶出率
表16溫度為100℃時渣相中各元素的含量及溶出率
從表12到表16可知,各溫度條件下鹼浸出的浸出效果以及渣相中各元素的含量。同時可以在同一溫度下比較各個元素的含量,得出在此溫度下何種元素更易從礦樣中除去。如從表中可知25℃、40℃與100℃時,fe元素更易浸出。
最後,對實驗結果進行總體分析,發現在實驗條件下,實驗樣品的減重率隨溫度的增加雖存在局部的波動,但整體呈現不斷增加的趨勢,及溫度越高,試樣中的可溶性雜質越易溶於鹼性浸出液中。出現這種現象的主要原因是高溫有利於提高反應速率常數,促進反應的進行。同時,隨著浸出溫度的不斷增加,鹼浸礦樣中碳的含量總體呈現增加的趨勢,這主要是由於礦樣中的可溶性雜質去除後,礦樣總體質量下降,分母變小,從而碳含量提高。
本實施例針對最佳水溶條件下的溶出渣樣進行了浸出時間的探索試驗。試驗操作是在naoh用量為175g/l、液固比為4∶1、溫度為50℃的條件下進行,取水溶最佳條件溶出渣樣10g,考查不同浸出時間(45min、60min及90min)下電解槽廢陰極炭塊中碳的含量。試驗結束後,將浸出液與渣相過濾分離,記錄濾液體積和烘乾後的濾餅質量,然後進行分析。
本實施例發現浸出液中的f、si、al元素的濃度在不同浸出時間下具有相同的變化趨勢,均是隨著溫度的增加呈現現增加後降低的趨勢,即在浸出時間為60min時具有最大溶出濃度;另外,浸出液中fe元素的濃度與f、si、al濃度變化趨勢正好相反,隨著浸出時間的增加,fe元素的浸出濃度先降低後增加,在60min時達到最低,在實驗範圍內,fe元素最佳浸出時間為40min。
在實驗分析中同樣對鹼浸出後的渣相中的各元素的含量進行了檢測與分析,具體結果如下列各表:
表17時間為45min時渣相中各元素的含量及溶出率
表18時間為60min時渣相中各元素的含量及溶出率
表19時間為90min時渣相中各元素的含量及溶出率
從表17到表19可知,各浸出時間條件下鹼浸出的浸出效果和渣相中各元素的含量。同時可以在同一浸出時間下比較各個元素的含量,得出在此溫度下何種元素更易從礦樣中除去。如從表中可知,在浸出時間為60min和90min時,相同浸出時間下,fe元素最易浸出,而f元素最難浸出;在浸出時間為45min時,si元素較易浸出,而f元素不易浸出。
本實施例還發現,隨著浸出時間的增加,鹼浸礦樣的減重率總體呈現增大趨勢,在實驗給定的浸出時間範圍內,浸出時間越長,鹼浸礦樣的減重率越大,即可溶性雜質的去除越徹底,出現這種顯現的原因可能是由於反應時間的延長,使得反應更加充分的進行。另外,本發明還發現,鹼浸礦樣中的碳含量隨著浸出時間的增大同樣呈現整體增大的趨勢,即時間越長,碳含量越高。
本實施例還探索了鹼用量為100g/l、125g/l、150g/l、175g/l和300g/l時,可溶性雜質的去除情況和電解槽廢陰極炭塊中碳的含量。取水溶最佳條件溶出渣樣10g,在液固比為4:1、浸出時間為60min、浸出溫度為50℃的實驗條件下,考查不同鹼用量對電解槽廢陰極炭塊中碳的含量的影響。
試驗結束後,將浸出液與渣相過濾分離,記錄濾液體積和烘乾後的濾餅質量,然後進行分析。
本實施例發現,在實驗鹼用量範圍內,溶出液中f離子的濃度隨鹼用量的增加呈現先降低後增加再降低的趨勢,在鹼用量為100g/l時具有最大溶出濃度;溶出液中si離子的濃度隨鹼用量的增加呈現先降低後增加再降低再增加的折線趨勢,在鹼用量為300g/l時達到最大溶出濃度;溶出液中al離子的濃度隨鹼用量的增加呈現先降低後增加的趨勢,即在鹼用量為300g/l時達到最大溶出濃度;另外,溶出液中fe離子的濃度隨鹼用量的增加呈現先增後降再增的趨勢,鹼用量為300g/l時達到最大溶出濃度。
在實驗分析中同樣對鹼浸出後的渣相中的各元素的含量進行了檢測與分析,具體結果如下列各表:
表20鹼用量為100g/l時渣相中各元素的含量及溶出率
表21鹼用量為125g/l時渣相中各元素的含量及溶出率
表22鹼用量為150g/l時渣相中各元素的含量及溶出率
表23鹼用量為175g/l時渣相中各元素的含量及溶出率
表24鹼用量為300g/l時渣相中各元素的含量及溶出率
從表20到表24可知,不同鹼用量條件下鹼浸出的浸出渣相中各元素的含量。同時可以在同一鹼用量下比較各個元素的含量,得出在此鹼用量下何種元素更易從礦樣中除去。如從表中可知鹼用量除去300g/l時,即在低鹼用量下fe元素更易浸出。300g/l下al溶出率為100%,此數據不可信,可能是由於實驗誤差造成。
最後,對實驗結果進行總體分析,發現隨著鹼用量的增加,實驗樣品鹼浸礦樣的減重率先降低後增加,在實驗給定的鹼用量範圍內,鹼用量越大,鹼浸礦樣的減重率越大,即可溶性雜質的去除越徹底。本實施例還發現鹼浸礦樣中的碳含量隨著鹼用量的增大呈現先降低後增大的趨勢,即鹼用量越大,碳含量越高。
本實施例在進行單因素實驗研究後,為更加準確的了解最佳溶出條件組合,又進行了三因素三變量的正交實驗。具體的實驗條件與實驗數據如表25所示:
表25正交實驗條件及實驗數據表
從表25中顯示的實驗數據可知,b9實驗條件下,即液固比為4∶1,溫度為100℃,鹼用量為12ml時,電解槽廢陰極炭塊中碳的含量最大,可達到88.8865%。
實施例5:補充實驗
本實施例在實驗後期又進行了補充實驗,及對最佳水溶條件下得到的水溶渣取樣進行最佳鹼浸出條件下鹼浸出,而後再對鹼浸出後的渣相取樣分別用鹽酸和硫酸在最佳酸浸條件下進行酸浸出,最後進行碳含量的檢測。具體實驗數據如下表:
表26水溶鹼溶後不同酸溶條件下各元素的溶出質量(g)
表26為兩組實驗條件下各元素的溶出質量,與此同時還對碳含量進行了測量與分析,結果如下:
1)水溶(條件:液固比3∶1、溫度20℃、時間60min)→鹼溶(條件:液固比4∶1、溫度50℃、時間60min、naoh用175g/l)→酸溶(條件:hcl(濃度37%):h2o=3∶1、液固比=3:1、溫度80℃、時間60min)→碳含量為89.9%。
2)水溶(條件:液固比3:1、溫度20℃、時間60min)→鹼溶(條件:液固比4:1、溫度50℃、時間60min、naoh用量175g/l)→酸溶(條件:h2so4(濃度98%):h2o=3:1、液固比=3:1、溫度80℃、時間60min)→碳含量為90%。
當然,以上只是本發明的具體應用範例,本發明還有其他的實施方式,凡採用等同替換或等效變換形成的技術方案,均落在本發明所要求的保護範圍之內。