一種金屬微孔材料及其製備方法與流程
2023-10-26 03:42:37 3
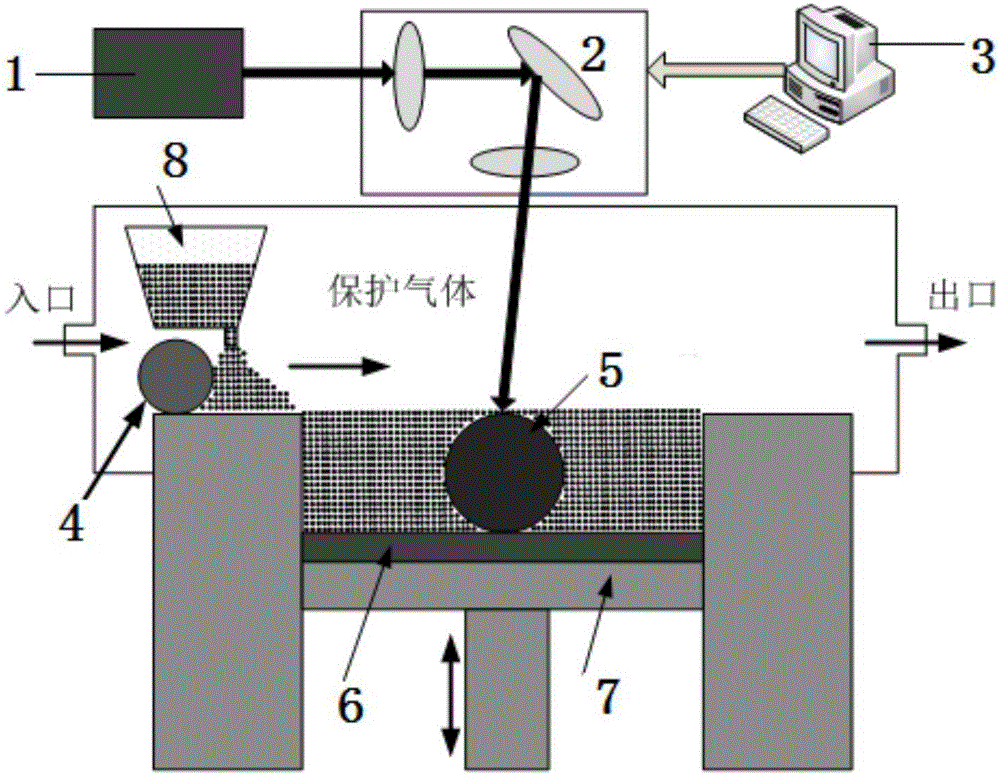
本發明涉及一種金屬微孔材料及其製備方法,屬於材料合成與加工領域。
背景技術:
近年來金屬微孔材料的開發和應用日益受到人們的關注。金屬微孔材料是20世紀80年代後期國際上迅速發展起來的,該材料是一種具有明顯空隙特徵的金屬材料,由於微孔的存在而呈現出一系列有別於金屬緻密材料的特殊功能,如:密度小、剛度大、比表面積大、吸能減震性好、消音降噪效果好、電磁屏蔽性能高,廣泛應用於冶金機械、石油化工、能源環保、國防軍工、核技術和生物製藥等工業過程中的過濾分離、流體滲透與分布控制、液態化、高效燃燒、強化傳質傳熱、阻燃防爆等。基於金屬微孔材料的廣泛應用,目前亟需研究一種新的金屬微孔材料以及其製備方法,以期該金屬微孔材料具有更加優異的性能,擴大了其應用範圍。
技術實現要素:
本發明的技術解決的問題是:提出了一種新型金屬微孔材料及其製備方法,突破了以鋁為主要研究對象的金屬微孔材料的研究現狀,獲得了高熔點的金屬微孔材料。
本發明採用的技術方案如下:
本發明提供一種金屬微孔材料的製備方法,包括以下步驟:
(1)將鈦粉末和硼粉末混合均勻,利用3D列印金屬雷射燒結技術在2800~3200℃下將混合金屬粉末列印成所需形狀的材料;
(2)將步驟(1)中具有所需形狀材料加熱至2500~2700℃,使未完全反應的硼和鈦部分或全部液化,流出所述所需形狀材料外,即得到所需形狀的金屬微孔材料。
步驟(1)中,利用3D列印技術的雷射提供2800~3200℃的溫度使所述鈦粉末和硼粉末發生反應,根據硼粉末和鈦粉末混合比例不同,所得材料含有二硼化鈦及未完全反應的硼和鈦。
所述鈦粉末的大小為15~45μm,硼粉末的大小為小於5μm。選擇此粒徑金屬粉末的原因是:一是滿足3D列印條件;二是從最後得到的金屬微孔材料的性能考慮,選擇此粒徑粉末得到的金屬微孔材料性能優異。若是選擇其他尺寸的粉末,要重新確定3d列印的工藝條件,同時材料性能也發生一些變化。經過大量實驗,本尺寸粉末為最優粉末。
進一步的,為了能夠得到金屬微孔材料,所述硼粉末和鈦粉末未按照2:1的摩爾比例混合。
進一步的,硼粉末和鈦粉末混合時採用的設備為行星球混合機(型號:Retsch PM 200),混合參數:轉速150~250rpm進行5~7h(優選的為轉速200rpm、6h),每5分鐘停留10秒。
進一步的,為了得到理想結構的金屬微孔材料,所述鈦粉和硼粉的反應溫度為3000℃。
進一步的,為了獲得性能較好的金屬微孔材料,3D列印技術的加工參數為:180~220W,雷射直徑為60~80μm;更進一步的,所述參數為:200W,雷射直徑為70μm。
本發明還提供一種上述製備方法得到的金屬微孔材料,該金屬微孔材料的組成為:TiB2的質量百分含量為55~65%,剩餘為TiB和Ti4B3或者TiB、Ti4B3與純硼和/或純鈦;孔徑大小為3~100μm,洛式硬度(HRC)為45~55,熔點為2900~3100℃。微孔率根據硼和鈦的摩爾比例可以調整,孔隙率大約為10%-60%。
本發明通過列印出來的這種材料,可以稱之為金屬。
本發明中的金屬微孔材料中的「微孔」是指具有孔徑大小為3~100μm的孔。
本發明還提供一種上述金屬微孔材料在製備汽車減振部件或汽車車身部件中的應用。由於該金屬微孔材料具有微孔結構,吸能減震性好,適合製備減震部件;由於該金屬材料的硬度和熔點較高、質量輕適合製備汽車車身部件。
上述技術方案中的一個技術方案具有如下有益效果:
(1)本發明採用鈦粉末和硼粉末兩種物質利用3D列印雷射金屬燒結技術得到所需要形狀的材料,無需其他輔料(粘結劑、成型劑)的添加。
(2)本發明採用3D列印雷射金屬燒結技術可以直接列印成零件形狀,不需要二次加工;加工零件形狀建模更容易,柔性更強;3D列印設備科提供兩種粉末化學反應所需要的能量。
(3)設置合適的3D列印加工參數,將硼粉末和鈦粉末列印成型,然後經過高溫液化即得到的金屬微孔材料,製備金屬微孔材料不需要造孔劑等添加劑,並且製備得到的材料硬度和熔點較高,孔徑大小為3~100μm。
(4)本發明的金屬微孔材料應用於汽車減振材料和替代汽車板材,降低汽車重量,實現汽車輕量化。
附圖說明
圖1是3D列印過程示意圖。
圖2是本發明金屬微孔材料的SEM圖。
圖3是本發明3個實例的xrd圖譜分析。
其中,1、電機,2、雷射鏡,3、計算機,4、鋪粉板,5、工件,6、工件支撐臺,7、平臺,8、儲存箱。
具體實施方式
本發明中所用設備均為現有技術:(1)行星球混合機,型號為Retsch PM 200;(2)3D印表機,型號為RENISHAW250。
實施例1
一種金屬微孔材料的製備方法,包括以下步驟:準備硼和鈦粉末,其中鈦粉末的大小為15-45微米,硼粉末的大小為小於5微米,將這兩種金屬粉末按照1:1的摩爾比例均勻混合,混合設備為行星球混合機,混合參數:轉速200rpm進行6小時,每5分鐘停留10秒;硼和鈦在3000℃的高溫下會發生反應,生成二硼化鈦,該反應不完全,會有殘餘的鈦,利用3D列印設備將硼和鈦的混合金屬粉末在3000℃的條件下列印成所需形狀,3D印表機的加工參數:功率200W,雷射直徑70μm;而硼的熔點為2180℃,鈦的熔點為1668℃,二硼化鈦的熔點為2980℃。將所得材料在高溫加熱器中加熱至2500~2700℃,使材料內反應不完全所殘留的鈦液化,得到新型金屬微孔材料。如圖2所示,本材料泡孔直徑約50-100微米,微孔直徑較大;孔隙率較大為31~60%左右;洛式硬度(HRC)為45~55;熔點為3000℃左右。經過試驗測得,本材料的組成為TiB2含量約60%,TiB、Ti4B3、純硼、鈦約40%,如圖3所示。該金屬微孔材料適合製備成為減震部件或製備成為汽車車身部件。
3D列印的基本過程如圖1所示,通過3D列印雷射燒結技術,為本領域技術人員常規知曉的技術,基本部件包括:電機1、雷射鏡2、計算機3、鋪粉板4、工件5、工件支撐臺6、平臺7和儲存箱8等。
實施例2
一種金屬微孔材料的製備方法,包括以下步驟:準備硼和鈦粉末,其中鈦粉末的大小為15-45微米,硼粉末的大小為小於5微米,將這兩種金屬粉末按照4:1的摩爾比例均勻混合,混合設備為行星球混合機,混合參數:轉速180rpm進行7小時,每5分鐘停留10秒;硼和鈦在3000度的高溫下會發生反應,生成二硼化鈦,該反應不完全,會有殘餘的硼,利用3D列印設備將硼和鈦的混合金屬粉末在3000℃的條件下列印成所需形狀,而硼的熔點為2180℃,鈦的熔點為1668℃,二硼化鈦的熔點為2980℃。將所得材料在高溫加熱器中加熱至2500~2700℃,使材料內反應不完全所殘留的硼液化,得到新型金屬微孔材料。本材料泡孔直徑約3-20微米,微孔直徑較小,孔隙率較小為10~30%左右;洛式硬度(HRC)為45~55;熔點為3000℃左右。經過試驗測得,本材料的組成為TiB2含量約60%,TiB、Ti4B3、純硼、鈦約40%,如圖3所示。該金屬微孔材料適合製備成為減震部件或製備成為汽車車身部件。
實施例3
一種金屬微孔材料的製備方法,包括以下步驟:準備硼和鈦粉末,其中鈦粉末的大小為15-45微米,硼粉末的大小為小於5微米,將這兩種金屬粉末按照3:1的摩爾比例均勻混合,混合設備為行星球混合機,混合參數:轉速220rpm進行6.5小時,每5分鐘停留10秒;硼和鈦在3000度的高溫下會發生反應,生成二硼化鈦,該反應不完全,會有殘餘的硼,利用3D列印設備將硼和鈦的混合金屬粉末在3000℃的條件下列印成所需形狀,而硼的熔點為2180℃,鈦的熔點為1668℃,二硼化鈦的熔點為2980℃。將所得材料在高溫加熱器中加熱至2500~2700℃,使材料內反應不完全所殘留的硼液化,得到新型金屬微孔材料。本材料泡孔直徑約20~70微米,微孔直徑較小,洛式硬度(HRC)為45~55;熔點為3000℃左右。經過試驗測得,本材料的組成為TiB2含量約60%,TiB、Ti4B3、純硼、鈦約40%,如圖3所示。該金屬微孔材料適合製備成為減震部件或製備成為汽車車身部件。
上述實施例為本發明較佳的實施方式,但本發明的實施方式並不受上述實施例的限制,其他的任何未背離本發明的精神實質與原理下所作的改變、修飾、替代、組合、簡化,均應為等效的置換方式,都包含在本發明的保護範圍之內。