一種3D印表機高精度安裝結構及基於其的3D列印方法與流程
2023-10-27 06:41:52 4
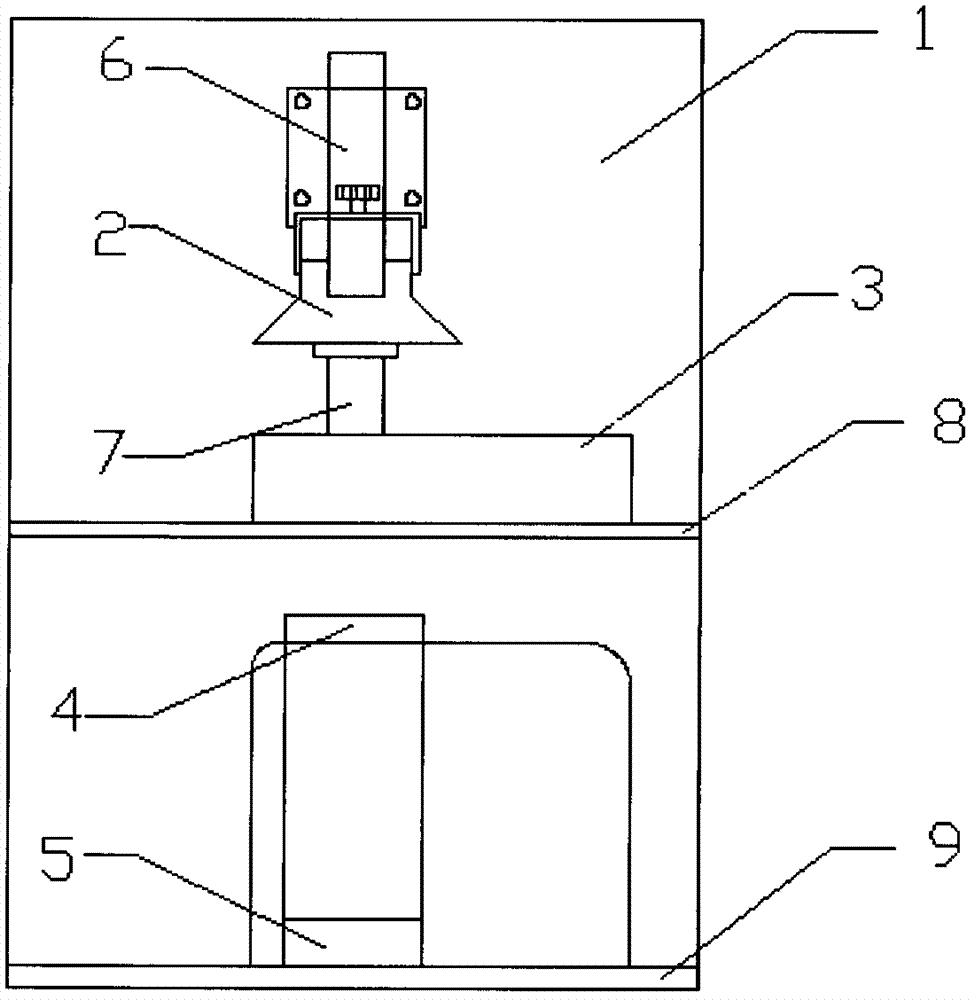
本發明涉及一種3d印表機高精度安裝結構及基於其的3d列印方法,屬於3d列印技術領域。
背景技術:
傳統光敏材料3d印表機多採用dlp投影機(高壓汞燈或led燈泡光源)改裝後作為光源,通過高壓汞燈或led(特殊波長)白光或紫外光或者雷射發生器發出的紫外光來照射光敏材料,從而使得光敏材料在光照情況下發生反應產生凝固,成型平臺在軟體控制下驅動z軸上下運動,從而實現層層疊加成型,完成3d列印動作。但傳統的dlp或者sla雷射3d列印因為光源發射鏡頭直逕往往較列印區域會更小,同時所有發光元器件都有不同程度的從而發產生光源與列印版面呈扇形角度,因為列印平面與發光元器件平面的距離不一樣,會產生中心區域與周邊區域的光照強度有所區別,中心區域相對光照度較強,邊緣區域光照度會較弱,從而導致列印出來的產品中心區域較邊緣區域的尺寸會偏厚,影響列印精度;而且現有的led、dlp投射紫外光成型的3d印表機因為投影光平面、成型材料液面及列印成型臺三個面不是絕對平形,從而導致每個列印區域的3d圖像產生畸變影響列印精度,從而使列印出來的產品精度誤差通常只能控制在0.1mm-0.2mm以上,無法滿足高精度的市場需求。
技術實現要素:
本發明的目的是:提供一種3d印表機高精度安裝結構及基於其 的3d列印方法,通過使投影光平面、成型材料液面及列印成型臺高度平行和精確控制不同光照強度區域的列印時間,以減小列印產品的精度誤差。
為實現上述目的,本發明採用以下技術方案:
本發明所述的一種3d印表機高精度安裝結構,包括安裝背板、成型平臺、樹脂料盤、光學鏡頭及dmd發光晶片,所述成型平臺、樹脂料盤、光學鏡頭及dmd發光晶片由上至下平行固定於安裝背板上,且均與所述安裝背板呈90°的垂直角度,所述成型平臺通過成型平臺掛臂固定於安裝背板上,所述安裝背板固定有絲杆運動部件,所述成型平臺掛臂與所述絲杆運動部件固定連接。
優選地,所述樹脂料盤通過料盤隔板固定於安裝背板上,且料盤隔板與所述安裝背板固定連接。
優選地,所述光學鏡頭及dmd發光晶片通過投影機固定安裝板固定於安裝背板上,且投影機固定安裝板與所述安裝背板固定連接。
優選地,安裝背板材料為鑄鐵、大理石、合金鋁板等硬質材料。
本發明中一種基於上述3d印表機高精度安裝結構的3d列印方法,其特徵在於,包括如下步驟:
(1)將所列印區域的列印時間段分為普通列印時間段與附加列印時間段;
(2)依據所述列印的材料及光照強度的情況設定普通列印時間段;
(3)將所列印區域在xy平面區域內尺寸等分成x/y等尺寸的若干方塊;
(4)通過照度計精確單獨測量步驟(3)中每個方塊的紫外光照強度誤差,結合所述列印產品的厚度來調節每個方塊的附加列印時間段。
優選地,所述步驟(2)普通列印時間段為1~20s。
優選地,所述步驟(3)中方塊數量為若干等份。
優選地,所述附加列印時間段通過參數設定在3d列印軟體中控制。
優選地,所述步驟(3)中方塊數量為48個或60個。
本發明的有益效果在於,所述高精度安裝結構能保證光學鏡頭及dmd發光晶片與樹脂料盤、成型平臺高度平行,因此光學鏡頭髮射光的平面與成型平臺在x(左右)、y(前後)平面的垂直距離最大限度的保證了同一高度尺寸,能從物理上保證其相對精度;並且通過將所列印區域裡xy平面尺寸等分成x/y等尺寸的若干方塊,可自定義成48個或60個方塊或更多方塊,通過照度計精確單獨測量每個方塊的紫外光照強度誤差,結合實際列印產品的厚度來調節每個方塊的列印時間,軟體裡增加附加調節列印時間,在附加時間參數裡可從0-100參數進行設定,光強度的區域和列印後與實際參數偏厚的區域減少附加列印時間;光強度弱的區域和列印後與實際參數偏薄的區域增加附加列印時間,從而解決led或dlp印表機光源不均勻,導致列印精度偏差的問題。
附圖說明
如圖1為本發明中一種3d印表機高精度安裝結構的主視圖;
如圖2為本發明中一種3d印表機高精度安裝結構的側視圖;
如圖3為實施例2中附加列印時間段功能控制界面的說明示意圖;
其中,1-安裝背板,2-成型平臺,3-樹脂料盤,4-光學鏡頭,5-dmd發光晶片,6-成型平臺掛臂,7-絲杆運動部件,8-料盤隔板,9-投影機固定安裝板。
具體實施方式
下面結合具體實施例對本發明進一步進行描述。
實施例1
參照附圖1及圖2所示,一種led光源或dlp投影3d印表機高精度安裝結構,包括安裝背板1、成型平臺2、樹脂料盤3、光學鏡頭4及dmd發光晶片5,所述成型平臺2、樹脂料盤3、光學鏡頭4及dmd發光晶片5由上至下平行固定於安裝背板1上,且均與所述安裝背板1呈90°的垂直角度,所述成型平臺2通過成型平臺掛臂6固定於安裝背板1上,所述安裝背板1固定有絲杆運動部件7,所述成型平臺掛臂6與所述絲杆運動部件7固定連接,所述樹脂料盤3通過料盤隔板8固定於安裝背板1上,且料盤隔板8與所述安裝背板1固定連接,所述光學鏡頭4及dmd發光晶片5通過投影機固定安裝板9固定於安裝背板1上,且投影機固定安裝板9與所述安裝背板1固定連接,安裝背板1材料為合金鋁板硬質材料。
基於上述3d印表機高精度安裝結構的3d列印方法,其特徵在於,包括如下步驟:
(1)將測試件所列印區域的列印時間段分為普通列印時間段與附加列印時間段;
(2)依據測試件的材料及光照強度的情況設定普通列印時間段為10s;
(3)將所列印區域在xy平面區域內尺寸等分成x/y等尺寸的48個方塊;
(4)通過照度計精確單獨測量步驟(3)中每個方塊的紫外光照強度誤差,結合所述列印測試件的厚度在列印軟體中設置參數1~100來調節每個方塊的附加列印時間段。
實施例2
與實施例1中不同之處在於,本實施例中一種基於3d印表機高精度安裝結構的3d列印方法中,步驟(2)中設定普通列印時間段為15s,步驟(3)中將所列印區域在xy平面區域內尺寸等分成x/y等尺寸的60個方塊。
基於上述,所述高精度安裝結構能保證光學鏡頭4及dmd發光晶片5與樹脂料盤3、成型平臺2高度平行,從而使投影光平面、成型材料液面及列印成型臺三個面平行尺寸控制在0.02-0.20mm以內,並使光學鏡頭4發射光的平面與成型平臺2在x(左右)、y(前後)平面的垂直距離最大限度的保證了同一高度尺寸,精度將能最有效保證。將普通列印時間段根據材料及光照設定,並通過調整附加時間段 的參數(0-100)來設定單獨的曝光時間,測試件厚的區域調小曝光時間,測試件偏薄的區域調大曝光時間,從而精準控制列印尺寸,達到高精度列印,並最終使產品誤差範圍在0.02-0.05mm的範圍內。
以上示意性的對本發明及其實施方式進行了描述,該描述沒有限制性,附圖中所示的也只是本發明的實施方式之一,實際的結構並不局限於此。所以,如果本領域的普通技術人員受其啟示,在不脫離本發明創造宗旨的情況下,不經創造性的設計出與該技術方案相似的結構方式及實施例,均應屬於本發明的保護範圍。