全自動內螺紋檢測裝置的製作方法
2023-04-30 17:16:31
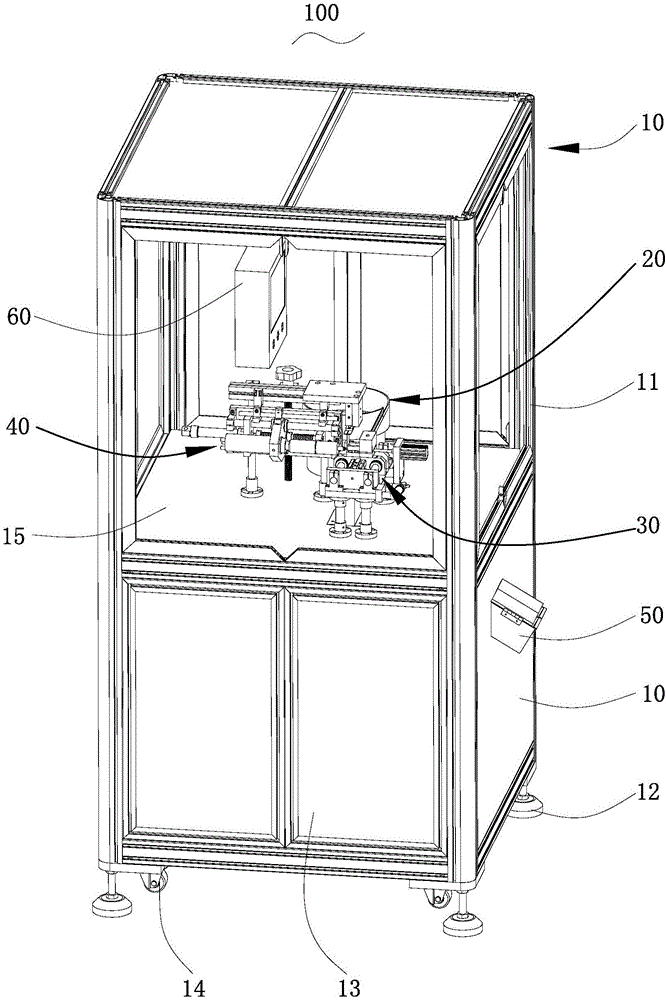
本發明涉及一種檢測設備,尤其涉及一種全自動內螺紋檢測裝置。
背景技術:
在機械加工領域,螺紋連接是固定連接的重要方式之一,對於一個零件需要螺紋連接時,在裝配之前需要對螺紋孔進行檢測,例如檢測螺紋孔是否有漏攻、內部是否有異物堵塞情況,或者在組裝時螺絲擰不進螺絲孔或者擰不到位等現象。
現有的檢測方法是採用手工或者電動螺絲刀將螺絲逐個擰入螺紋孔內,再逐個將螺絲擰出,檢測零件上的螺紋孔是否加工得符合要求。採用這種方法,需要大量的人力操作,工作量大,檢測效率較低,且檢測效果得不到有效地保證,同時在檢測過程中,螺紋孔的深度是無法有效檢測的。
技術實現要素:
為此,本發明的目的在於提供一種全自動內螺紋檢測裝置,以解決目前的螺紋檢測自動化程度低、需耗費大量人力,且檢測效率低的問題。
為實現上述目的,本發明主要採用以下技術方案為:
一種全自動內螺紋檢測裝置,用於檢測加工件上的內螺紋,包括機架及裝設於機架上的送料裝置、夾緊裝置、檢測裝置、分料裝置、控制面板,所述送料裝置將加工件送至夾緊裝置內進行固定,所述控制面板設定檢測裝置檢測時的扭力、行程位移、適配時間的標準範圍值,所述檢測裝置對固定好的加工件進行檢測,所述檢測裝置包括測量裝置、緩衝裝置及感應裝置,所述測量裝置所述緩衝裝置上,所述感應裝置檢測測量裝置的行程位移,所述測量裝置包括測量杆及氣動馬達,所述測量杆的端部設置有與加工件上的內螺紋相匹配的外螺紋,所述氣動馬達驅動測量杆旋轉,所述緩衝裝置驅動所述測量裝置向前移動,並適配於所述夾緊裝置上加工件的螺紋孔內;當檢測到的行程位移、實際扭力及適配時間中的任意一項值超出設定範圍,則判定該被檢測產品為不合格產品;所述分料裝置包括次品導槽及良品導槽,檢測完成後,所述分料裝置根據檢測結果將檢測後的加工件導入至對應的次品導槽或良品導槽內。
進一步地,所述送料裝置包括震動盤、導料槽、送料槽及推料裝置,所述導料槽連接于震動盤上,導料槽上設置有一落料孔,所述落料孔對應所述送料槽設置,所述震動盤將加工件震出至導料槽內,並自落料孔落入送料槽內。
進一步地,所述夾緊裝置包括一夾緊治具,所述夾緊治具由第一固定塊及第二固定塊組合而成,第一固定塊及第二固定塊的組合位置形成一貫穿夾緊治具的臺階孔,所述臺階孔包括連接孔及定位孔,所述連接孔連接於送料槽,所述定位孔與加工件的外徑大小相匹配,所述連接孔的外徑小於加工件的外徑。
進一步地,所述夾緊裝置還包括一滑動裝置,所述滑動裝置裝設於所述第二固定塊上,滑動裝置帶動第二固定塊與第一固定塊組合或打開。
進一步地,還包括一限位裝置,所述限位裝置包括若干調節杆及檔板,所述檔板裝設於所述調節杆上,所述調節杆帶動檔板上下移動,以打開或抵擋於所述定位孔的端部。
進一步地,所述感應裝置包括兩感應器、兩感應件及一感應軸,兩所述感應器沿測量裝置延伸方向分布並位於感應件上方,所述兩感應件分別裝設於感應軸的兩端,所述感應軸裝設於所述測量裝置上,所述測量裝置帶動所述感應件前後移動,所述感應器感應對應的感應件的位置。
進一步地,所述緩衝裝置包括緩衝氣缸、推進緩衝彈簧、緩衝軸及後退緩衝彈簧,所述測量裝置通過一活動板裝設於所述緩衝軸上,所述推進緩衝彈簧穿設於活動板前側的緩衝軸上,所述後退緩衝彈簧設置於活動板後側的緩衝軸上。
進一步地,所述推料裝置包括送料氣缸及連接於送料氣缸上的送料杆,所述送料杆設於所述送料槽內,並位於所述落料孔對應位置的後側,所述送料氣缸驅動送料杆推動加工件前向前移動。
進一步地,所述分料裝置包括下料槽、次品導槽、良品導槽及切換裝置,所述次品導槽及良品導槽並排裝設於所述下料槽的下方,所述切換裝置設置於所述下料槽內。
進一步地,所述切換裝置包括分料板及分料氣缸,所述分料板設置於下料槽內,所述分料氣缸驅動分料板在連通次品導槽或良品導槽間進行切換。
綜上所述,本發明的有益效果在於:整個檢測過程均為全自動化檢測,且檢測精準,同時,檢測後的次品與合格品可自動分檢,大大減少了人工工時,節約了大量人工成本,提高了產品分檢的良品率,實用性強,具有較強的推廣應用性。
附圖說明
圖1為本發明全自動內螺紋檢測裝置的結構示意圖,其中前側及右側的機架門未示。
圖2為圖1中送料裝置、檢測裝置、緩衝裝置、限位裝置、夾緊裝置的裝配結構示意圖。
圖3為圖2中送料裝置的結構示意圖。
圖4為圖2中支撐架的結構示意圖。
圖5為圖2中夾緊裝置的結構示意圖。
圖6為圖2安裝架、限位裝置、檢測裝置的結構示意圖。
圖7為圖1中分料裝置的結構示意圖。
具體實施方式
為了使本發明的目的、技術方案及優點更加清楚明白,以下結合附圖及實施例,對本發明進行進一步詳細說明。
如圖1至圖7所示,本發明提供的一種全自動內螺紋檢測裝置100,用於檢測加工件200上的內螺紋是否符合要求。所述加工件200呈圓柱形設置,該加工件200的一端設置有一凹槽,所述凹槽的底部設置有貫穿至加工件另一端的螺紋孔,所述螺紋孔內設置有內螺紋。
所述全自動內螺紋檢測裝置100包括機架10及裝設於機架10上的送料裝置20、夾緊裝置30、檢測裝置40、分料裝置50、控制面板60,所述送料裝置20將加工件200送至夾緊裝置30內進行固定,所述檢測裝置40對固定好的加工件200進行檢測,所述控制面板60設定檢測裝置40檢測時的扭力、行程、時間等各項參數,檢測裝置40將檢測到數據與設定參數比對,從而檢測出合格及不合格產品,所述分料裝置50將檢測後的合格及不合格產品分開導出裝袋或裝箱。
所述機架10包括支撐框架11、若干支撐腳12、若干機架門13及若干萬向輪14,四支撐腳12及若干萬向輪14均設置於所述支撐框架11的底端,以在檢測裝置定位或移動時進行切換使用。若干機架門13裝設於所述支撐框架11的四周,並與所述支撐框架11形成一封閉空間,以用於保護該機架10內的其它裝置,同時還可起到防塵的作用。所述機架10上還設置有一工作檯15,所述工作檯15固定於所述支撐框架11的中部。所述送料裝置20、夾緊裝置30、檢測裝置40、控制面板60均設置於工作檯15上,所述分料裝置50設置於所述夾緊裝置30下方。
所述送料裝置20包括震動盤21、導料槽22、送料槽23及推料裝置,所述導料槽22包括一連接端及一自由端,所述連接端的端部連接於所述震動盤21,所述自由端延伸至所述送料槽23的正上方,所述導料槽22與送料槽23呈T字形交叉設置。所述自由端的底部設置有一落料孔24,所述落料孔24正對所述導料槽22設置,加工件200自所述落料孔24落入所述導料槽22內。所述推料裝置包括送料氣缸25及連接於送料氣缸25上的送料杆26,所述送料杆26設於所述送料槽23內,並位於所述落料孔24對應位置的後側,所述送料氣缸25驅動送料杆26向前移動,以用於推動所述加工件200向前移動。
所述送料槽23對應於導料槽22的正上方設置有一氣罩27,所述氣罩27上設置有用於噴氣的氣嘴,由於本實施例中的加工件整體重量分布不均,因此,加工件自導料槽落至送料槽時可能會因重量不均而擺放位置傾斜,所述氣嘴噴出氣體可將其位置矯正。
所述工作檯上還設置有一支撐架70,所述支撐架70包括若干支撐光軸71及設置於支撐光軸71上的支撐臺72,所述送料槽23、夾緊裝置30均安裝於所述支撐臺72上。所述支撐架上設置有一下料孔73,所述支撐臺72底面裝設於一擋塊,所述擋塊設置於所述下料孔73的前側,以避免加工件200下料過程中自下料孔73前側掉出。
所述夾緊裝置30對應於所述導料槽22設置,所述推料裝置將加工件200推動至所述夾緊裝置30內進行定位。所述夾緊裝置30包括夾緊治具31及滑動裝置32,所述夾緊治具31上設置有一臺階孔,所述臺階孔包括相連通的連接孔33及定位孔34,所述連接孔33連接於所述送料槽23,所述定位孔34設置於遠離送料槽23的一端,所述連接孔33與所述送料槽23相對接位置設置有一導向部331。所述定位孔34與加工件200的外徑大小相匹配,所述連接孔36的外徑小於加工件200的外徑。所述夾緊治具31由第一固定塊35及第二固定塊36組合而成,所述第一固定塊35及第二固定塊36的對應位置設置有半圓形臺階孔,第一固定塊35及第二固定塊36上的半圓形臺階孔組合形成所述臺階孔。
所述滑動裝置32包括第一定位塊321、第二定位塊322、滑動塊323、夾緊氣缸37、軸套38及滑動軸39,所述第一定位塊321、第二定位塊322均固定於所述支撐臺72上,所述滑動軸39依次穿過第一定位塊321、滑動塊39及第二定位塊322,所述軸套38裝設於所述第二定位塊322一側的的滑動軸39上,並貼合於所述滑動塊323設置,以對所述滑動塊323進行限位。所述夾緊氣缸37裝設於所述滑動塊323上,所述夾緊氣缸37驅動所述滑動塊323沿所述滑動軸39向前後移動。所述第一固定塊35及所述送料槽23均固定於所述第一定位塊321上,所述第二固定塊322固定於所述滑動塊323上。
所述全自動內螺紋檢測裝置還包括一安裝架80及限位裝置90,所述安裝架80包括兩升降軸81、一升降絲杆82、一滑軌83、調節板84及固定於調節板84上的兩相對設置的卡塊85,兩相對設置的卡塊85上設置有連接杆86,所述滑軌83及調節板84均裝設於兩升降軸81及升降絲杆82上,從而,滑軌83及調節板84均可進行上下位置調節,所述滑軌83設置於調節板84的上方。所述檢測裝置40裝設於所述調節板84上,所述限位裝置90裝設於所述滑軌83上,所述限位裝置90可沿所述滑軌進行位置調節,所述限位裝置90包括安裝塊91、調節塊92、若干調節杆93及檔板94,所述安裝塊91裝設於所述滑軌83上,所述調位塊92固定於所述安裝塊91上,所述調位塊92內設置有安裝孔,所述調節杆93一端裝設於所述安裝孔內,另一端延伸出調位塊92並連接於所述檔板94上,所述檔板94呈豎直設置。所述調節杆93可帶動檔板94進行上下位置調節。
所述檢測裝置40包括第一活動板41、第二活動板42、測量裝置43、緩衝裝置44及感應裝置45,所述第一活動板41及第二活動板42裝設於所述連接杆86上,所述測量裝置43裝設於所述第二活動板42上,所述測量裝置43包括測量杆431及氣動馬達432,所述測量杆431的端部設置有與所述加工件200上的內螺紋相匹配的外螺紋,所述氣動馬達432驅動所述測量杆431度旋轉。所述緩衝裝置依次穿過第一活動板41、第二活動板42,並固定於所述調節板84上,所述緩衝裝置44帶動所述測量裝置43向前移動,所述緩衝裝置44包括緩衝氣缸441、推進緩衝彈簧442、緩衝軸443及後退緩衝彈簧444,所述推進緩衝彈簧442穿設於第二活動板42前側的緩衝軸上443,所述後退緩衝彈簧444設置於第二活動板42後側的緩衝軸上443,所述緩衝氣缸441驅動所述緩衝軸443向前運行。
所述感應裝置45包括兩感應器451、兩感應件452及一感應軸453,兩所述感應器451裝設於所述滑軌43上,並沿測量裝置43延伸方向分布,所述兩感應件452分別裝設於感應軸453的兩端,所述感應軸453裝設於所述第二活動板42上,所述測量裝置43帶動所述感應件452前後移動,所述感應器451感應對應的感應件452的位置。當前側感應器451感應到對應的前側的感應件452時,則該被檢測件合格,相應地,當該感應件未達到前側感應器451的感應範圍或超出其感應範圍,則該被檢測件為不合格產品。
所述分料裝置50包括下料槽51、次品導槽52、良品導槽53及切換裝置,所述下料槽51設置於所述工作檯15上,所述次品導槽52及良品導槽53並排裝設於工作檯15底部上,並正對所述下料槽51設置。所述切換裝置包括一分料板54、分料軸55及分料氣缸56,所述分料氣缸56固設於所述支撐臺72上,所述分料軸55連接於所述分料氣缸56上,所述分料板54固定於所述分料軸55上,所述分料軸55架設於所述下料槽51的兩相對設置的槽壁上,所述分料板54設置於下料槽51內,並將下料槽51分隔成兩分別對應次品導槽52及良品導槽53的通道。所述次品導槽52及良品導槽53的的下端均延伸出所述機架10,次品導槽52及良品導槽53的下端出料口上方設置有蓋板57,所述蓋板57與出料口間設有一插槽,該插槽57處插設有插板58,所述插板58用於打開或關閉所述出料口。
送料時,所述震動盤21將加工件200震出至所述導料槽22內,並自導料槽22自由端的落料孔24落入至所述送料槽23內,所述送料氣缸25驅動所述送料杆26推動加工件200向前移動至所述夾緊治具31的導向部331處,所述滑動裝置32帶動所述第二固定塊36向遠離第一固定塊35方向移動,使得所述連接孔33的孔徑變大,從而所述送料杆36能將加工件200推送至所述定位孔34內。而在此之前,所述限位裝置90將所述檔板94向下移動至完全遮擋位所述定位孔34的孔口,從而,當送料杆36將加工件200推至定位孔34內時,可避免加工件200自定位孔34的孔口落出。所述滑動裝置32推動所述第二固定塊36組合至第一固定塊35上,由於所述連接孔33的孔徑小於所述加工件200的外徑,從而,所述連接孔33可對加工件200進行限位,避免加工件200後退,導致檢測不準確。所述送料杆36後退至所述落料孔24對應的送料槽23的後側,新的檢測加工件自落料孔23落入,再重複前述操作。
檢測時,所述氣動馬達432驅動所述測量杆360旋轉,所述緩衝氣缸441推動所述測量杆431向前移動至夾緊治具31上的加工件內進行適配檢測,所述感應裝置45感應測量裝置43的行程位移,當該感應件未達到前側感應器451的感應範圍或超出其感應範圍,則該被檢測件為不合格產品。同時,所述控制面板將測量裝置的實際扭力、適配時間與設定標準範圍進行比對,實際扭力、適配時間及行程位移中有任意一項或同時幾項不符合標準,均判定為不合格產品。其中,實際扭力值為測量杆螺接至所述內螺紋孔內的扭力,所述適配時間為測量杆進入內螺紋孔至退出內螺紋孔的時間,所述行程位移為測量杆進入內螺紋孔後的整個前進的行程距離。檢測完成後,所述滑動裝置32帶動所述第二固定塊36向遠離第一固定塊35方向移動,所述加工件自第一固定塊35與第二固定塊36間的間隙落入至所述下料槽51內。所述分料裝置50根據檢測結構對產品進行分類,當檢測到的產品為合格產品時,所述分料氣缸56驅動所述分料軸55帶動分料板54下端朝向良品導槽53方向旋轉,從而將加工件導向所述良品導槽53內。相應地,當檢測產品為不合格產品時,所述分料板54下端朝向次品導槽52方向旋轉,將加工件導向次品導槽52內。
綜上所述,本發明的有益效果在於:整個檢測過程均為全自動化檢測,大大提高了檢測效率,減少了人力操作的工作量,且檢測精準,可避免漏檢及檢測不精確的問題,同時,檢測後的次品與合格品可自動進行分檢,自動化程度高,實用性強,具有較強的推廣應用性。
以上所述僅為本發明的較佳的一個實施例而已,並不用以限制本發明,凡在本發明的精神和原則之內所作的任何修改、等同替換和改進等,均應包含在本發明的保護範圍之內。