雙軌滑移式模板支撐體系及成套施工方法與流程
2023-12-04 11:12:42
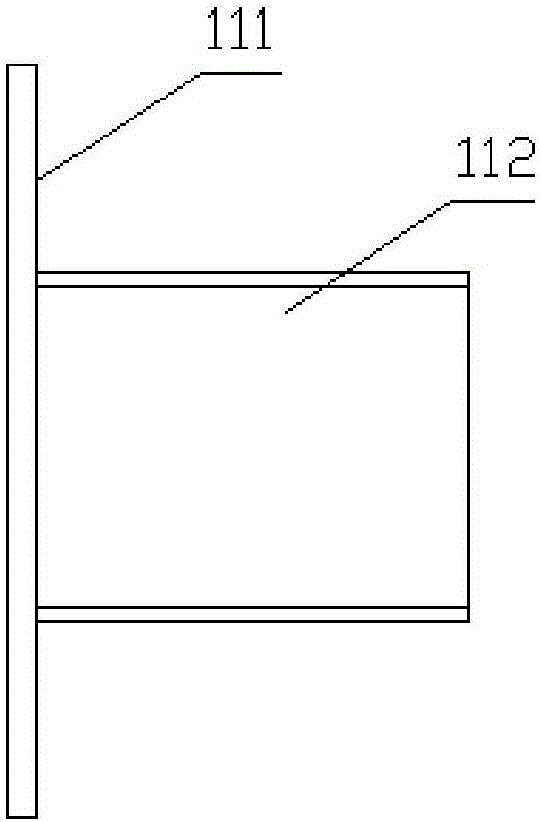
本發明涉及建築施工技術,具體涉及適用於層高大於6米的鋼筋混凝土排架結構廠房的混凝土梁板結構施工技術。
背景技術:
單層面積大、層高高(大於6米)的廠房排架結構梁板混凝土施工時,傳統支模方法是採用滿搭鋼管腳手架,層高越高,採用傳統方法的成本及工期就越難控制,一方面是因為鋼管扣件的周轉速度比普通3米的層高慢,另一方面,為保證高支模施工安全及質量,實際施工時必須縮小立杆間距(通常為800左右),這不僅需要大量的周轉材料,而且在拆模時現場轉運的工作量也大大增加。
技術實現要素:
本發明所要解決的技術問題就是提供一種雙軌滑移式模板支撐體系,解決傳統施工方法成本耗費大,工期拖延時間長,場內二次搬運工作量大的問題。
為解決上述技術問題,本發明採用如下技術方案:雙軌滑移式模板支撐體系,包括與鋼筋混凝土獨立柱固定的平臺支座及用於支撐支模體系的鋼平臺構件,所述平臺支座上設有軌道,所述鋼平臺構件設有與軌道配合的定向輪,所述鋼平臺構件的下方設有支撐鋼平臺構件並將鋼平臺構件的荷載傳遞至地面的傳力構件,所述平臺支座上設有在拆除傳力構件後牽引鋼平臺構件沿軌道移動的平臺牽引裝置。
優選的,所述平臺支座包括牛腿以及安裝在牛腿上的型鋼軌道梁,所述型鋼軌道梁的上部焊接槽鋼軌道。
優選的,所述鋼筋混凝土獨立柱在鋼平臺構件的設計標高處預埋有螺栓孔,且對應螺栓孔設置有與牛腿固定的預埋件。
優選的,所述傳力構件包括立柱、調節短柱、底座,所述立柱通過螺栓與鋼平臺構件連接,所述底座設於立柱下方且立柱與底座間設有調節短柱。
優選的,所述鋼平臺構件連接成整體的主梁、次梁、檁條,所述定向輪焊接在主梁的下部。
優選的,所述平臺牽引裝置包括與平臺支座可拆卸連接的可拆卸支座、設於可拆卸支座上的電動葫蘆以及由電動葫蘆牽引帶動鋼平臺構件沿軌道平移的牽引鋼絲。
優選的,所述鋼平臺構件與平臺支座之間可拆卸固定有將鋼平臺構件與平臺支座固定的隅撐。
本發明還提供了一種雙軌滑移式模板支撐體系成套施工方法,包括如下步驟:
(1)預留預埋:在鋼筋混凝土獨立柱施工時,在鋼平臺構件的設計標高處預埋螺栓孔,待混凝土達到設計強度後安裝預埋件;
(2)製作並安裝平臺支座,使平臺支座與預埋件固定;
(3)製作並安裝型鋼軌道梁;
(4)安裝鋼平臺構件;
(5)安裝傳力構件;
(6)鋪安全網、平臺加密、鋪腳手板;
(7)預堆載試驗;
(8)平臺上部支模體系搭設;
(9)混凝土澆築;
(10)混凝土強度達到設計要求後拆除鋼平臺構件上部的支模體系;
(11)安裝牽引裝置;
(12)牽引裝置牽引鋼平臺構件滑移至下一軌道區間後固定鋼平臺構件;
(13)再次移動平臺、循環操作;
(14)拆卸、移除整個雙軌滑移式模板支撐體系。
進一步的,所述步驟(12)包括如下步驟:①將鋼平臺構件下部用千斤頂抬起,移除傳力構件中的調節短柱,然後下降千斤頂,使鋼平臺構件重新就位在型鋼軌道梁上;②啟動平臺牽引裝置,將鋼平臺構件向下一區域移動;③每移動1米即中止操作,鋼平臺構件恢復穩定後繼續操作,以免由於慣性難於控制、致使平臺移出既定區域;④通過固定裝置或與周邊建築拉結固定鋼平臺構件。
本發明採用的技術方案,通過在鋼筋混凝土獨立柱上懸空設置的鋼平臺構件節省鋼平臺構件下部腳手架搭拆及搬運工時及成本,進一步的,鋼平臺構件設有定向輪與平臺支座上軌道配合,因此,通過牽引裝置牽引,可以實現鋼平臺構件的整體移動,實現了流水施工,保證施工進度。
附圖說明
下面結合附圖和具體實施方式對本發明作進一步描述:
圖1為平臺牽引裝置牽引鋼平臺構件沿軌道平移的結構示意圖;
圖2為單體支座的主視圖;
圖3為單體支座的側面視圖;
圖4為複合支座的結構示意圖;
圖5為鋼平臺構件與平臺支座的固定結構示意圖。
具體實施方式
如圖1至圖5所示,雙軌滑移式模板支撐體系,包括與鋼筋混凝土獨立柱1固定的平臺支座及用於支撐支模體系的鋼平臺構件3,所述鋼平臺構件包括連接成整體的主梁31、次梁、檁條、定向輪32,所述定向輪焊接在主梁的下部。所述平臺支座上設有軌道,所述定向輪32與軌道配合,所述鋼平臺構件的下方設有支撐鋼平臺構件並將鋼平臺構件的荷載傳遞至地面的傳力構件,所述平臺支座上設有在拆除傳力構件後牽引鋼平臺構件沿軌道移動的平臺牽引裝置2。
上述鋼平臺構件的製作方式為:
①根據圖紙,確定主梁尺寸、高度即主梁間、主次梁間連接方式(螺栓連接或焊接),並將主梁連接成整體;本案例中採用螺栓連接;
②確定次梁尺寸,下料並將次梁與主梁連接成整體;
③確定檁條間距,將檁條固定在主次梁間;
④固定定向輪。定向輪包括擋輪支架、輪子、實心圓軸三個部分組成,本案例中採用的材料分別是擋輪支架厚50mm圓鋼,輪子直徑200mm、厚50mm圓鋼,實心圓軸50mm圓鋼。固定方法:將擋輪支架與主梁下部焊接連接(滿焊),注意焊接間距必須大於輪子厚度,焊接前需試組裝在主梁底部繪定位線。焊接完成後,再將輪軸、輪子與擋輪支架組合。
⑤平臺整體拼裝完成,準備吊裝。
其中,如圖1所示,所述平臺支座包括牛腿11以及安裝在牛腿上的型鋼軌道梁12,所述型鋼軌道梁的上部焊接槽鋼軌道13。所述鋼筋混凝土獨立柱1在鋼平臺構件的設計標高處預埋有螺栓孔,且對應螺栓孔設置有與牛腿固定的預埋件。
如圖2和圖3所示,所述牛腿包括固定鋼板111、與固定鋼板垂直的工字鋼112,固定鋼板上設有固定孔與預埋件通過螺栓固定,工字鋼112用於支撐型鋼軌道梁12。
所述傳力構件包括立柱、調節短柱、底座,所述立柱通過螺栓與鋼平臺構件連接,所述底座設於立柱下方且立柱與底座間設有調節短柱。
①立柱由型鋼製成、與上部螺栓連接;立柱一般設置在平臺主節點下方,其數量依主節點數量而定。本案例採用立柱的規格材料為直徑194mm壁厚為5mm的截面為圓形的鋼管,立柱根數為每個平臺下方12根立柱。
②調節短柱由與立柱等直徑的鋼管制成,有不同規格,用來填補立柱與下部底座之間的空間,將立柱的力軸心傳遞至下部底座。本案例採用與立柱相同規格的鋼管,上部與立柱焊接連接,下部墊鋼板固定在底座上。
③底座可由鋼板或混凝土預製塊製作。本案例採用混凝土預製塊,下料的尺寸為(1000×1000×300)mm。
所述平臺牽引裝置2包括與平臺支座可拆卸連接的可拆卸支座21、設於可拆卸支座上的電動葫蘆22以及由電動葫蘆牽引帶動鋼平臺構件沿軌道平移的牽引鋼絲23。平臺牽引裝置的作用是用水平力牽引鋼平臺構件,使其移動到下一有軌區域內,實現循環施工的目的。牽引裝置兩側軌道上同時設置,同時工作。製作方式為:
①將可拆卸支座21(牽引支點)固定在獨立柱部位的型鋼軌道梁端處,採用螺栓連接。
②可拆卸支座21套掛牽引鋼絲,與鋼平臺構件連接。工作時,兩側同時施加相同的水平牽引力,拉動鋼平臺構件。
如圖5所示,所述鋼平臺構件與平臺支座之間可拆卸固定有將鋼平臺構件與平臺支座固定的隅撐33。
本成套施工方法的施工流程為:預留預埋、製作平臺→製作並安裝支座→製作並安裝軌道梁→安裝鋼平臺構件→安裝傳力系統→鋪安全網、平臺加密、鋪腳手板等→預堆載試驗→平臺上部支模體系搭設→混凝土澆築→(強度達到設計要求後)拆除平臺上部支模體系→安裝牽引設備→鋼平臺構件滑移至下一軌道區間、固定平臺→設置平臺維護結構至再次移動平臺、循環操作→拆卸、移除鋼平臺構件→整理構件、分類儲存、處理或再利用。具體技術要點如下:
(1)預留預埋:在鋼筋混凝土獨立柱施工時,在鋼平臺構件設計標高處、獨立柱內部預埋螺栓孔,本案例預埋8個M48螺栓孔,待混凝土達到設計強度後安裝預埋件,此預埋件可拆卸重複使用。(螺栓規格通過荷載計算確定)
(2)製作並安裝平臺支座,支座有兩種,一種是用於架設活動平臺的單體支座,另外一種是架設固定平臺的複合支座:
①單體支座:將型鋼通過螺栓錨入、固定在獨立柱上形成牛腿;本案例採用H300×450×5×10規格型鋼。
②複合支座:如圖4所示,在單體支座的基礎上,再增加一段型鋼短柱113,短柱與牛腿焊接連接。
(3)製作並安裝軌道梁:設置型鋼軌道梁,將梁安裝在平臺支座上。在安裝之前,在軌道梁上部焊接上口尺寸與定向輪尺寸相當的槽鋼軌道。軌道梁通過吊裝、與軌道支架螺栓連接。
(4)安裝鋼平臺構件:將製作好的鋼平臺構件,用兩臺吊車同步、沿軌道梁方向傾斜起吊,再通過調整吊車起升高度正位,固定在平臺支架上。
(5)安裝傳力構件:先將底座吊至平臺主節點下方,再將傳力系統中的立柱通過螺栓與鋼平臺構件連接,最後安裝調節短柱。
(6)鋪安全網、平臺加密、鋪腳手板等:①在平臺四角拉結安全網,確保後續施工安全;②採用鋼管、扣件將檁條的間距加密,主要是通過直角扣件卡在主梁及次梁上;③在加密後的平臺上部鋪設腳手板。
(7)預堆載試驗:平臺及傳力構件安裝完成後必須進行預堆載試驗,以確保後續施工安全。按預堆載方案實施。
(8)平臺上部支模體系搭設:腳手架的材料選擇在平臺方案確定時就一確定。本案例採用鋼管扣件腳手架搭設方式,按間距(1000×1000)mm搭設,相鄰跨拉接成整體。
(9)混凝土澆築:為避免平臺單側受力失穩,混凝土布料從中間向兩側進行。本案例中採用汽車泵施工。
(10)(強度達到設計要求後)拆除平臺上部支模體系:拆除連接部分,從上至下,後搭設的部分先拆除;在平臺邊緣設置溜槽,將拆除後的鋼管扣件通過溜槽傳至地面。
(11)安裝牽引設備:本案例中平臺一次移動距離為12m,所以在前方軌道端部安裝牽引設備。
(12)鋼平臺構件滑移至下一軌道區間、固定平臺:①將平臺下部用千斤頂抬起,移除傳力系統中的調節短柱,然後下降千斤頂,使平臺重新就位在軌道梁上;②啟動牽引系統,將平臺緩緩向下一區域移動;③每移動1米即中止操作,平臺恢復穩定後繼續操作,以免由於慣性難於控制、致使平臺移出既定區域。④通過專門設置的固定裝置或與周邊建築拉結固定平臺。固定裝置可由型鋼製作、通過螺栓或點焊與軌道連接。由於本案例中平臺重量較大,整體依靠自重及與周邊結構拉結即可起到平臺固定作用,因此未單獨設置固定裝置。
(13)設置平臺維護結構至再次移動平臺、循環操作:①固定平臺後,重新檢查平臺安全網、加密鋼管、腳手板等設施,確保達到後續施工條件;②再次搭設模板支撐體系、澆築混凝土;③循環移動平臺、固定平臺操作。
(14)拆卸、移除鋼平臺構件:所有區域主體梁板施工完成後,拆除支模架。拆卸平臺:①先移除下部傳力調節短柱、傳力立柱等;②拆除加密鋼管,通過溜槽輸送至地面;③兩端備用兩臺汽車吊,將鋼絲繩捆綁在平臺上,在平臺1/3、2/3處分別、分開布置4個起吊點;④用小型千斤頂從一側將平臺緩緩頂出,平臺伸出1/3後調整起吊鋼絲繩長度,使吊車處於受力狀態;⑤繼續頂出平臺至2/3處,調整另一吊車鋼絲繩長度,使其處於受力狀態;⑥繼續頂出平臺至其脫離主體結構。
(15)整理構件、分類儲存、處理或再利用:由於鋼平臺構件幾乎全部採用螺栓連接,逐一拆卸,將構件清理後分類存儲,用過的平臺可全部回收再利用。
本發明的有益效果體現在:
(1)節省了材料成本。由於軌道具有一定的空間高度,省去了該標高以下的鋼管扣件用量。通過製作鋼胎架、設置導軌,節省了長期、高額的鋼管扣件租賃費用,減省了人工費;而其替換增加的鋼胎架、導軌等為定型化設施,數量有限,增加的成本有限。
(2)部分替換了人工作業,降低了人工消耗。在軌道標高以下的支模架搭設、拆除、搬運等人工作業,被替換成空間支撐、設備牽引定向滑移作業,技術上改良了純人工作業的傳統工藝,大大降低了人工消耗,同時也改觀了人工操作效率低的狀態。
(3)降低了施工成本。其全套設備乃至穿柱拉結的螺栓,均可重複利用,一次投入、多次收益,其成本效益不容小覷,且符合綠色施工的理念。
(4)提高了施工效率,不僅如此,還為穿插施工提供了作業面,加快了施工進度。
(5)非常適合在同類型、超高、多跨的現澆鋼筋混凝土廠房項目中應用。