一種堆取料機俯仰液壓系統、閉環控制系統及控制方法與流程
2023-11-09 17:54:12 2
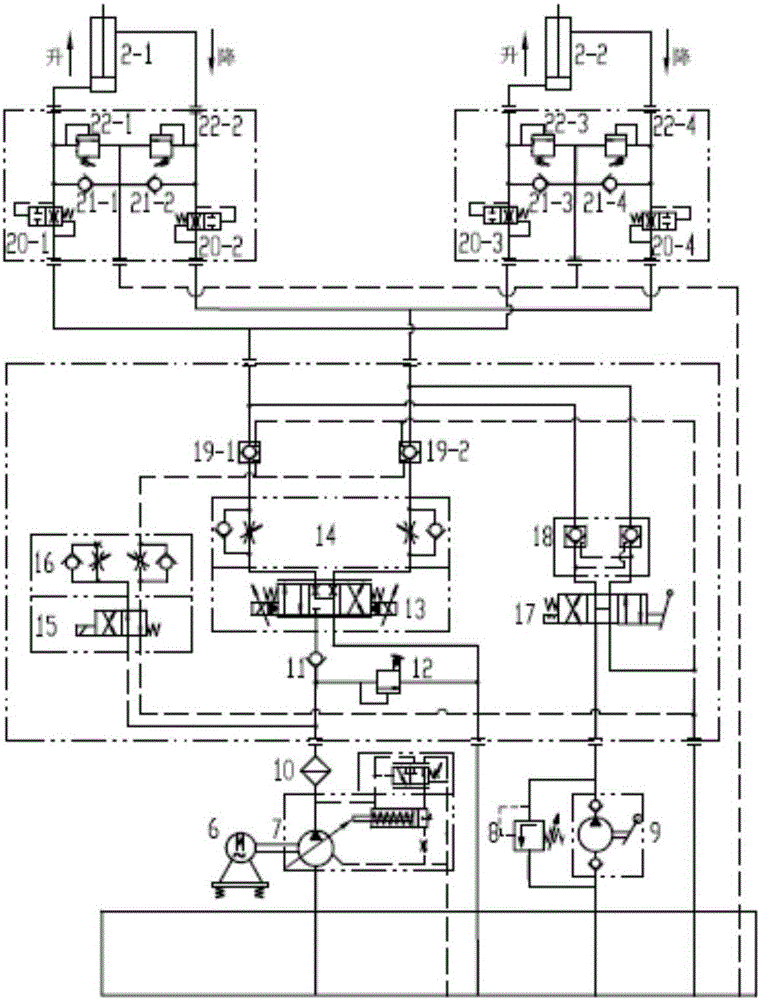
本發明涉及鬥輪堆取料機械設備領域,具體的說是涉及一種堆取料機俯仰液壓系統、閉環控制系統及控制方法。
背景技術:
堆取料機是一種利用鬥輪連續取料,再利用設備自身的帶式輸送機連續堆料的有軌式裝卸機械。其主要由鬥輪機構、迴轉機構、俯仰機構、大車行走機構、尾車、帶式輸送機和上部鋼結構等部件組成;其中堆取料機的俯仰機構包括機械和液壓兩種型式,液壓式俯仰機構因其具有結構小巧,配置靈活,工作可靠,組裝方便等優點被廣泛應用。
俯仰機構與主機聯結示意圖如圖1所示,包括懸臂機構1、液壓缸2、俯仰鉸點3、支撐鉸座4以及轉盤5。在液壓缸2牽引下,懸臂1繞俯仰鉸點3轉動,實現鬥輪高度的調整,使鬥輪在不同高度的料堆上進行堆料和取料作業。同時俯仰機構還需要支撐取料鬥輪、懸臂機構及配重裝置的重量。液壓缸2所受負載力隨著懸臂1位置改變而變化,導致液壓系統壓力和流量不斷變化。當懸臂1處於最下端接地位置,即液壓缸2與水平面夾角為θ1時,液壓缸2所受負載為正且負載最大,此時無杆腔壓力最大;隨著懸臂1的上升,液壓缸2出現負負載,受拉應力,液壓缸2最上端位置與水平面夾角為θ2。
另,現有的堆取料機俯仰液壓系統原理圖見圖2所示,異步電機6驅動恆壓變量泵7作為動力源;恆壓變量泵7的輸出壓力隨外負載變化而變化,實際運行時泵輸出壓力一直小於泵上調壓閥調定壓力值,斜盤位於最大擺角處,泵的排量最大,此時恆壓變量泵7相當於定量泵;通過調節比例換向閥13和單向節流閥14閥口開度控制液壓缸2的流量;但是此俯仰液壓系統屬於節流控制系統,存在節流和溢流損失,效率低,系統溫升高。
現階段,大部分作業面靠人工操作進行懸臂高度的調整,然而操作工人靠視力觀察很難準確判斷懸臂移動的垂直高度是否達到指定位置,從而影響了堆取料的作業效率。堆取料機懸臂俯仰過程中,液壓缸2的運動速度一般要求控制在0.7m/min左右,同時要求嚴格控制懸臂1移動的垂直高度,即液壓缸2的垂直位移。俯仰機構所受載荷不斷變化引起液壓系統壓力、流量及活塞速度不斷改變,而液壓系統控制方式為開環控制,決定了此液壓系統不能實現對液壓缸2速度及懸臂1垂直位移的精確控制。
現場調試時,需精準調節比例換向閥13和單向節流閥14的開口度。懸臂1上升過程中帶動液壓缸2的活塞伸出,若比例換向閥13閥口開度較大,則活塞伸出速度也會較快。但是現有的恆壓變量泵結構複雜,變量機構慣性大,響應速度較慢。此時恆壓變量泵7已經無法提供活塞運動速度所需的流量,使得泵出口出現真空,不能提供液控單向閥19的反向開啟壓力,造成短時間內活塞停頓,液壓缸出現「爬行」現象。懸臂1下降時帶動液壓缸2活塞縮回,在外負載作用下液壓缸無杆腔產生較大背壓,如果比例換向閥13和單向節流閥14的閥口開度較小,無杆腔油液不能快速流回油箱,會使無杆腔背壓進一步增大,對系統可靠性和安全性形成威脅。
為此,有必要研究一種新穎的堆取料機俯仰液壓系統及其控制方法,以能夠有效減少系統能量損失,實現對液壓缸速度和懸臂垂直位移的精確控制。
技術實現要素:
鑑於已有技術存在的缺陷,本發明的目的是要提供一種堆取料機俯仰液壓系統,該系統能夠解決現有堆取料機俯仰液壓系統能源利用率低,無法實現精確調節液壓系統流量的問題,通過控制俯仰液壓缸的速度和懸臂垂直位移達到設計要求,以保證堆取料機能夠高效、穩定、可靠地運行。
為了實現上述目的,本發明的技術方案:
一種堆取料機俯仰液壓系統,其特徵在於,包括:
控制堆取料機懸臂俯仰機構進行動作的主迴路、為液控單向閥提供反向開啟壓力的液控單向閥控制迴路以及在系統斷電或發生故障狀態下為系統提供動力的手動控制迴路;其中,所述主迴路包括與取料機懸臂俯仰機構連接的液壓缸,與所述液壓缸連接、用以控制液壓缸的升降動作的第一電磁換向閥,與所述第一電磁換向閥連接、用以避免油液回流的第一單向閥,與所述第一單向閥連接、用以為主迴路提供過壓保護的第一溢流閥,與所述第一單向閥連接、用以過濾油液中雜質的過濾器,與所述過濾器連接的定量泵,與所述定量泵連接、用以帶動定量泵為系統提供動力的變頻電機,兩個分別與所述第一電磁換向閥連接、用以防止由內洩引起的液壓缸下滑的液控單向閥,兩個分別與各所述液控單向閥一一對應連接、用以防止活塞杆出現伸縮動作的防爆閥以及用以實現在一定條件下使得液壓缸的無杆腔中的液壓油一部分洩回油箱,一部分進入有杆腔對有杆腔進行補油的兩組雙溢流制動閥,所述雙溢流制動閥包括第二單向閥以及第二溢流閥,所述一定條件是指在液壓缸的活塞杆承受一定載荷而迅速下降時,液壓缸的無杆腔承受一定的壓力,同時其有杆腔形成真空的狀態;所述液控單向閥控制迴路包括由電機帶動、用以作為動力源的定量泵,與所述定量泵連接、用以避免油液回流的第三單向閥,與所述第三單向閥連接、用以為本液控單向閥控制迴路提供過壓保護的第三溢流閥以及與所述液控單向閥連接,用以控制各液控單向閥反向啟閉的第二電磁換向閥;所述手動控制迴路包括用以實現人工操作的手動泵,與所述手動泵連接、用以為手動控制迴路提供過壓保護的第四溢流閥,用以控制液壓缸進行升降動作的手動換向閥以及用以防止由內洩引起的液壓缸下滑的液壓鎖。
本發明的另一目的是要提供一種能夠對上述堆取料機俯仰液壓系統進行閉環控制的堆取料機俯仰液壓系統閉環控制系統,其特徵在於,包括:
用以檢測液壓缸的速度信號的速度傳感器;
用以檢測液壓缸的角位移信號的角位移傳感器;
兩個分別與所述速度傳感器、角位移傳感器連接、用以實現將模擬信號轉換成數位訊號的A/D轉換模塊;
與所述A/D轉換模塊連接、用以將所輸入數位訊號通過內置PID進行邏輯運算並向變頻器輸出數字控制信號的PLC可編程控制器;同時PLC可編程控制器28用以給定第一電磁換向閥及第二電磁換向閥數位訊號以控制第一電磁換向閥或第二電磁換向閥換向,從而實現懸臂的升降動作;
與所述PLC可編程控制器連接、用以將數位訊號轉換成模擬信號的D/A轉換模塊;
與所述D/A轉換模塊連接、用以根據PLC可編程控制器所輸出的模擬信號,改變所述變頻電機的工作電源頻率方式來控制變頻電機的轉速的變頻器23;
以及用於檢測變頻電機的轉速信號的旋轉編碼器。
本發明的另一目的是要提供一種能夠對上述堆取料機俯仰液壓系統進行閉環控制的堆取料機俯仰液壓系統閉環控制方法,其特徵在於,包括如下步驟:
步驟1、通過PLC可編程控制器輸出數字控制信號,該數字控制信號經D/A轉換模塊轉換成對應的模擬信號後輸入給變頻器,通過變頻器控制變頻電機的轉速,以實現對定量泵轉速的控制;同時PLC可編程控制器給定第一電磁換向閥及第二電磁換向閥數位訊號以控制第一電磁換向閥或第二電磁換向閥換向,從而實現懸臂的升降動作;
步驟2、通過速度傳感器將檢測到的液壓缸的速度信號經A/D轉換模塊轉換成數位訊號,通過角位移傳感器將檢測到的液壓缸的角位移信號經A/D轉換模塊轉換成數位訊號並通過旋轉編碼器檢測變頻電機的轉速信號,上述三種信號反饋至PLC可編程控制器,PLC可編程控制器經預設的PID邏輯運算後輸出相應的控制信號,以實現對液壓缸的速度和懸臂機構垂直位置的閉環控制。
與現有技術相比,本發明的有益效果:
1、本發明極大程度地減少了能源消耗,提高了系統工作效率;其利用變頻器控制變頻電機轉速驅動定量泵,使泵的輸出流量適應系統要求,最大限度地減少了溢流損失;並採用電磁換向閥減少了節流損失,降低了油液發熱量;
2、由於現有的變量泵斜盤的擺角只能限制在一定的範圍內使得調速範圍受限,因此本發明採用變頻電機帶動定量泵使得系統調速範圍增大以克服上述缺陷;
3、本發明採用電磁換向閥,省去了對傳動介質要求較高的比例換向閥,對傳動介質及過濾精度的要求有所降低。
4、本發明避免了電機和液壓泵的高速連續運轉,從而有效地降低系統噪聲和機件磨損,提高液壓系統的使用壽命和可靠性;
5、本發明省去了帶有複雜變量機構的變量泵,提高了系統響應速度,結構更合理;
6、本發明經過變頻器內置PID邏輯計算,具有更好的控制特性,實現了對液壓缸速度和懸臂垂直位移地精確閉環控制。
附圖說明
圖1為現有俯仰機構與主機聯結示意圖;
圖2為現有的堆取料機俯仰液壓系統原理圖;
圖3為所述堆取料機俯仰液壓系統原理圖;
圖4為所述閉環控制系統控制原理框圖。
圖中:1、懸臂機構;2、液壓缸;3、俯仰鉸點;4、支撐鉸座;5、轉盤;6、異步電機;7、恆壓變量泵;8、第四溢流閥;9、手動泵;10、過濾器;11、第一單向閥;12、第一溢流閥;13、比例換向閥;14、單向節流閥;15、電磁換向閥;16、單向節流閥;17、手動換向閥;18、液壓鎖;19、液控單向閥;20、防爆閥;21、第二單向閥;22、第二溢流閥;23、變頻器VFD;24、變頻電機;25、定量泵;26、旋轉編碼器PG;27、D/A轉換模塊;28、PLC可編程控制器;29、定量泵;30、電機;31、第三單向閥;32、第三溢流閥;33、第二電磁換向閥;34、第一電磁換向閥;35、A/D轉換模塊;36、速度傳感器;37、角位移傳感器。
具體實施方式
為使本發明的目的、技術方案和優點更加清楚,下面將結合本發明實施例中的附圖,對本發明的技術方案進行清楚、完整地描述,顯然,所描述的實施例是本發明一部分實施例,而不是全部的實施例。基於本發明中的實施例,本領域普通技術人員在沒有做出創造性勞動前提下所獲得的所有其他實施例,都屬於本發明保護的範圍。
隨著大型機械設備機械化、自動化技術的不斷發展,堆取料機的少人甚至無人化是一種未來發展趨勢,而堆取料裝備的機械化和自動化是實現這一趨勢的必要條件。針對上述背景,本發明提出了一種堆取料機俯仰液壓系統,其是對現有堆取料機俯仰液壓系統的改進。具體的,現有堆取料機俯仰液壓系統控制方式為開環控制,其動力源一般採用異步電機帶動恆壓變量泵,通過調節比例換向閥和單向節流閥閥口開度調節進入液壓缸的流量,進而控制液壓缸的伸縮速度;並靠操作工人視力判斷進行懸臂高度的調整。同時現有鬥輪堆取料機俯仰液壓系統還存在能源利用率低,液壓缸速度和懸臂高度控制精度一般的問題,無法達到堆取料機俯仰液壓系統對液壓缸速度和懸臂垂直位移的控制要求,從而影響了堆取料機的工作效率及可靠性。
本發明提出的一種堆取料機俯仰液壓系統其採用變頻器控制變頻電機的轉速來驅動定量泵,使泵的輸出流量滿足系統要求,同時採用電磁換向閥實現液壓缸伸縮動作的控制,該系統屬於一種直驅式容積控制電液系統。與現有堆取料機俯仰液壓系統相比,定量泵比變量泵的可靠性更高,泵轉速控制系統節能效果更好,這種新型液壓系統具有變頻電機控制靈活、功耗低、效率高、噪聲低、結構簡單等優勢;而且變頻電機帶動定量泵,系統調速範圍增大;將比例換向閥換成電磁換向閥,降低了對傳動介質及過濾精度的要求;電機工作方式由連續工作改為間歇工作,有效地降低系統噪聲和機件磨損,提高元件使用壽命。
本發明所述堆取料機俯仰液壓系統如圖3所示,由主迴路、液控單向閥控制迴路、手動控制迴路組成;
主迴路用以控制堆取料機懸臂俯仰機構進行動作,其包括變頻電機24、定量泵25、過濾器10、第一單向閥11、第一溢流閥12、第一電磁換向閥34、液控單向閥19、防爆閥20、第二單向閥21、第二溢流閥22以及液壓缸2;其由變頻電機24帶動定量泵25為系統提供動力,過濾器10用於過濾油液中的雜質,第一單向閥11用於避免油液回流,第一溢流閥12為主迴路提供過壓保護,第一電磁換向閥34用於控制液壓缸的升降動作,液控單向閥19(包括液控單向閥19-1、液控單向閥19-2)用於防止由內洩引起的液壓缸下滑,當系統壓力過高導致管路破裂時,防爆閥20起保護作用,防止活塞杆出現伸縮動作,第二單向閥21和第二溢流閥22組成雙溢流制動閥(所述雙溢流制動閥包括第二單向閥21以及第二溢流閥22),在液壓缸活塞杆承受較大載荷而迅速下降時,無杆腔承受較大壓力,有杆腔形成真空,此時無杆腔中的液壓油一部分洩回油箱,一部分經相應的第二單向閥進入有杆腔對有杆腔進行補油。
液控單向閥控制迴路用以為液控單向閥19-1、19-2提供反向開啟壓力,其由定量泵29、電機30、第三單向閥31、第三溢流閥32、第二電磁換向閥33組成;其中電機30帶動定量泵29作為動力源,第三單向閥31用於避免油液回流,第三溢流閥32為液控單向閥迴路提供過壓保護,第二電磁換向閥33用於控制液控單向閥19-1和19-2的反向啟閉,之所以設計液控單向閥控制迴路,是為了避免出現因外負載變化引起的液壓系統無法提供液控單向閥19-1、19-2反向開啟壓力的問題,而造成短時間內活塞停頓,液壓缸「爬行」的現象。
手動控制迴路用以在系統斷電或發生故障狀態下為系統提供動力;其包括第四溢流閥8、手動泵9、手動換向閥17及液壓鎖18,其中第四溢流閥8為手動控制迴路提供過壓保護,手動換向閥17用於控制液壓缸升降動作,液壓鎖18用於防止由內洩引起的液壓缸下滑。
上述液壓系統的工作過程為:當懸臂機構1進行上升動作時,電磁鐵YH1、YH4同時得電;主迴路中變頻電機24帶動定量泵25轉動,為系統提供動力,液壓油依次經過過濾器10、第一單向閥11、第一電磁換向閥34左位、液控單向閥19-1,以及兩個防爆閥20-1、20-3,分別進入液壓缸2-1、2-2的無杆腔,壓力油推動液壓缸2-1、2-2的活塞向上運動,實現懸臂的上升,液壓缸2-1、2-2有杆腔油液分別經過兩個防爆閥20-2、20-4,液控單向閥19-2以及第一電磁換向閥34左位流回油箱;液控單向閥控制迴路為液控單向閥19-2提供反向開啟壓力,電機30帶動定量泵29作為液控單向閥控制迴路動力源,油液依次經過單第三向閥31、第二電磁換向閥33右位,流入液控單向閥19-2的控制油口,使液控單向閥19-2反向開啟。
當懸臂機構1進行下降動作時,電磁鐵YH2、YH3同時得電;主迴路中變頻電機24帶動定量泵25轉動,為系統提供動力;液壓油依次經過過濾器10、第一單向閥11、第一電磁換向閥34右位、液控單向閥19-2、以及兩個防爆閥20-2、20-4,分別進入液壓缸2-1、2-2的有杆腔,在懸臂和活塞自重作用以及壓力油推動作用下,液壓缸2-1、2-2的活塞向下運動,實現懸臂的下降;液壓缸2-1、2-2的無杆腔油液分別經過兩個防爆閥20-1、20-3,液控單向閥19-1、第一電磁換向閥34右位流回油箱;液控單向閥控制迴路為液控單向閥19-1提供反向開啟壓力,電機30帶動定量泵29作為液控單向閥控制迴路動力源,油液依次經過第三單向閥31、第二電磁換向閥33左位,流入液控單向閥19-1的控制油口,使液控單向閥19-1反向開啟。
在系統斷電或發生故障等緊急狀況時,操作工人手動實現手動泵9、手動換向閥17動作;當懸臂進行上升動作時,液壓油從手動泵9依次流入手動換向閥17右位、液壓鎖18,以及兩個防爆閥20-1、20-3,分別進入液壓缸2-1、2-2的無杆腔,壓力油推動液壓缸2-1、2-2的活塞向上運動,實現懸臂的上升;液壓缸2-1、2-2有杆腔油液分別經過兩個防爆閥20-2、20-4,液壓鎖18、手動換向閥17右位流回油箱;當懸臂進行下降動作時,液壓油從手動泵9依次流入手動換向閥17左位、液壓鎖18,以及兩個防爆閥20-2、20-4,分別進入液壓缸2-1、2-2的有杆腔,在懸臂和活塞自重作用以及壓力油推動作用下,液壓缸2-1、2-2的活塞向下運動,實現懸臂的下降;液壓缸2-1、2-2無杆腔油液分別經過兩個防爆閥20-1、20-3,液壓鎖18、手動換向閥17左位流回油箱。
上述過程所對應的液壓傳動基本公式:
液壓缸在懸臂上升過程中的速度為:
液壓缸在懸臂下降過程中的速度為:
式中q—液壓缸輸入的流量(m3/s);
D—活塞直徑(m);
d—活塞杆直徑(m)。
對於俯仰液壓缸,要求升降過程中勻速運動,則根據上述公式,俯仰液壓缸的活塞面積D和活塞杆的面積d均為常數,可通過調節液壓缸的輸入流量q使得v1=v2。因此通過改變泵的轉速便可改變液壓缸的輸入流量,實現液壓缸速度的控制。
例如如圖1,液壓缸與水平面的夾角為θ,則液壓缸的垂直位移為:H=v·sinθ·t式中v—液壓缸運動速度(m/s);t—液壓缸運動時間(s)。
其在運動過程中,懸臂和液壓缸的垂直位移相等;懸臂升降時,液壓缸與水平面的夾角θ不斷變化,角位移傳感器37實時檢測液壓缸與水平面的夾角信號,通過調節液壓缸的運動時間t即可實現液壓缸垂直位移的控制,從而實現懸臂垂直位移的精確控制。
本發明的另一目的是要提供一種能夠對上述堆取料機俯仰液壓系統進行閉環控制的堆取料機俯仰液壓系統閉環控制系統,其特徵在於,包括:
用以檢測液壓缸的速度信號的速度傳感器36;
用以檢測液壓缸的角位移信號的角位移傳感器37;
兩個分別與所述速度傳感器、角位移傳感器連接、用以實現將模擬信號轉換成數位訊號的A/D轉換模塊35-1、35-2;
與所述A/D轉換模塊連接、用以將所輸入數位訊號通過內置PID進行邏輯運算並向變頻器輸出數字控制信號的PLC可編程控制器28;同時PLC可編程控制器28用以給定第一電磁換向閥及第二電磁換向閥數位訊號以控制第一電磁換向閥或第二電磁換向閥換向,從而實現懸臂的升降動作;
與所述PLC可編程控制器連接、用以將數位訊號轉換成模擬信號的D/A轉換模塊27;
與所述D/A轉換模塊連接、用以根據PLC可編程控制器所輸出的模擬信號,改變所述變頻電機24的工作電源頻率方式來控制變頻電機的轉速的變頻器23;
以及用於檢測變頻電機的轉速信號的旋轉編碼器26。
具體的堆取料機俯仰液壓系統閉環控制系統控制框圖如圖4所示。PLC可編程控制器28輸出數字控制信號,經D/A轉換模塊27轉換成數位訊號後輸入給變頻器23;變頻器23控制變頻電機24的轉速,從而實現對定量泵25轉速的控制;同時PLC可編程控制器28給定第二電磁換向閥33、第一電磁換向閥34對應的數位訊號,控制換向閥換向,實現懸臂的升降動作;速度傳感器36將檢測到的液壓缸2速度信號經A/D轉換模塊35-1轉換成數位訊號,角位移傳感器37將檢測到的液壓缸2的角位移信號經A/D轉換模塊35-2轉換成數位訊號,以及旋轉編碼器26將檢測到的變頻電機24轉速信號同時反饋給PLC可編程控制器28,隨後經過PID邏輯運算後輸出控制信號,最終實現液壓缸2速度和懸臂1垂直位置的閉環控制。
本發明的另一目的是要提供一種能夠對上述堆取料機俯仰液壓系統進行閉環控制的堆取料機俯仰液壓系統閉環控制方法,其特徵在於,包括如下步驟:
步驟1、通過PLC可編程控制器輸出數字控制信號,該數字控制信號經D/A轉換模塊轉換成對應的模擬信號後輸入給變頻器,通過變頻器控制變頻電機的轉速,以實現對定量泵轉速的控制;同時PLC可編程控制器給定第一電磁換向閥及第二電磁換向閥數位訊號以控制第一電磁換向閥或第二電磁換向閥換向,從而實現懸臂的升降動作;
步驟2、通過速度傳感器將檢測到的液壓缸的速度信號經A/D轉換模塊轉換成數位訊號,通過角位移傳感器將檢測到的液壓缸的角位移信號經A/D轉換模塊轉換成數位訊號並通過旋轉編碼器檢測變頻電機的轉速信號,上述三種信號反饋至PLC可編程控制器,PLC可編程控制器經預設的PID邏輯運算後輸出相應的控制信號,以實現對液壓缸的速度和懸臂機構垂直位置的閉環控制。
本設計提出的控制方法,通過實時監測液壓缸速度、液壓缸角位移以及變頻電機轉速的信號,反饋給PLC可編程控制器並通過內置PID邏輯運算,給定變頻器輸入信號控制變頻電機的轉速,最終實現對液壓缸速度和懸臂垂直位移的閉環控制。綜上所述,本發明具有控制方法簡單,能夠保證堆取料機能夠高效、穩定、可靠地運行等優點。
以上所述,僅為本發明較佳的具體實施方式,但本發明的保護範圍並不局限於此,任何熟悉本技術領域的技術人員在本發明揭露的技術範圍內,根據本發明的技術方案及其發明構思加以等同替換或改變,都應涵蓋在本發明的保護範圍之內。