一種二氯亞碸氯化反應尾氣的處理方法與流程
2023-12-05 20:06:11 3
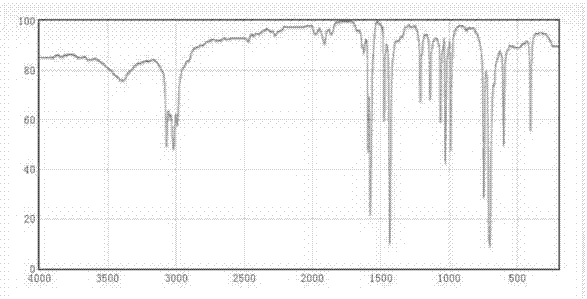
本發明涉及一種二氯亞碸氯化反應尾氣的處理方法。
背景技術:
二氯亞碸作為一種基礎化工原料,廣泛應用於氯化反應中,如將醇羥基氯化為氯代烷烴或將羧酸氯化為醯氯等,具有氯化完全,副反應少等優點,得到的副產物均為揮發性氣體,故所得的醯氯產品易於純化。在生產中使用二氯亞碸的最大問題是其反應尾氣的處理,每摩爾正常參與氯化反應的二氯亞碸會產生一摩爾氯化氫及一摩爾二氧化硫,每摩爾與水反應的二氯亞碸會產生二摩爾氯化氫和一摩爾二氧化硫。
不管是正常參與氯化反應還是反應結束後被水分解,都會產生大量的氯化氫及二氧化硫氣體;如果不加以處理,必然會造成嚴重的環境汙染。
目前常用的處理方法是分級吸收,先用水將大部分混合氣體吸收,得到鹽酸和二氧化硫或亞硫酸的混合物;然後再將前面沒有被吸收的氣體用鹼水吸收,得到含鹼、氯化鹽和亞硫酸鹽的混合廢鹼液,這樣處理得到的混合廢鹼液只能作為廢水進行處理,處理成本高;且第一級吸收得到的混合酸也無法應用,一般情況下也只能用鹼中和後作為廢水處理。在環保要求日益提高的社會環境下,上述傳統的尾氣處理方法由於消耗大量鹼而使成本高,且由於最終產生大量含雜離子的廢水而使環保壓力大。還有一種方法是通過分級吸收控制水的用量得到濃鹽酸,再用鹼水處理尾氣中的二氧化硫得到較純的鹼液,該方法雖然實現了部分副產物的回收利用,降低了處理成本、減輕了環保壓力,但是尾氣中的二氧化硫依然沒有得到較好的處理。
現有的脫硫技術中,以石灰、石灰石為基礎的鈣法,以氧化鎂為基礎的鎂法,以碳酸鈉、氫氧化鈉為基礎的鈉法應用較為廣泛。該些方法雖然能使廢氣達到排放標準,但存在設備投資大、運行維護費用高的問題,並且吸收劑無法實現循環利用,造成大量的資源浪費,而且得到的副產物附加值低,不易銷售,易造成二次汙染的問題。。基於上述不足之處,本發明人就此提出改良,設計出一種二氯亞碸氯化反應尾氣的處理方法。
技術實現要素:
本發明要解決的技術問題是克服現有的缺陷,提供一種二氯亞碸氯化反應尾氣的處理方法,可以有效解決背景技術中的問題,既得到工業上可使用的氯化氫醇溶液,又提供高效、可循環使用的二氧化硫吸收劑。
為了解決上述技術問題,本發明提供了如下的技術方案:
一種二氯亞碸氯化反應尾氣的處理方法,其特徵在於:包括以下步驟:
第一步,通過控制醇的用量,用醇對尾氣中的氯化氫進行二級吸收,得到工業上可用的氯化氫醇溶液,然後加熱蒸出二氧化硫;
第二步,對加熱蒸出的二氧化硫尾氣與吡啶吸收劑接觸,得到符合二氧化硫濃度排放標準的氣體和二氧化硫吡啶鹽。
第三步,對結合有二氧化硫的吡啶鹽進行解吸,將氣態二氧化硫從吸收劑中解吸出來,得到高純度二氧化硫氣體的同時對吸收劑再生,再生後的吡啶溶液可以直接再次投入使用。
對本發明做進一步優選,所述第一步中加熱處理,溫度範圍為80℃-120℃,時間範圍一般為1到5小時。
對本發明做進一步優選,所述第二步中,尾氣中每含64.0克二氧化硫,使用的吡啶量為150到220克。
對本發明做進一步優選,所述第二步中,尾氣中每含64.0克二氧化硫,使用的吡啶量為176到200克。
對本發明做進一步優選,用吡啶吸收劑吸收時所用的溫度為0℃到30℃之間。
對本發明做進一步優選,用吡啶吸收劑吸收時所用的溫度為15℃到25℃之間。
對本發明做進一步優選,解吸過程可以利用加熱方法進行,溫度控制在80-120℃,使鹽分解,解析出SO2氣體。
對本發明做進一步優選,解吸過程的溫度控制為90-110℃。
與現有技術相比本發明所達到的有益效果是:
本發明處理效率高,尾氣吸收完全,另外得到的副產品氯化氫醇溶液中所含的二氧化硫含量很低,可直接作為工業品使用;其中SO2吸收劑投資低,使用過程中運行成本低,處理效率高,尾氣吸收完全,能耗低,可循環使用,無二次汙染。
附圖說明
附圖用來提供對本發明的進一步理解,並且構成說明書的一部分,與本發明的實施例一起用於解釋本發明,並不構成對本發明的限制。
圖1為本發明的工藝流程圖。
圖2為吡啶二氧化硫鹽紅外示意圖。
圖3為吡啶紅外示意圖。
圖4為二氧化硫紅外示意圖。
具體實施方式
以下結合附圖對本發明的優選實施例進行說明,應當理解,此處所描述的優選實施例僅用於說明和解釋本發明,並不用於限定本發明。
醇中二氧化硫的含量用直接碘量法測定(參見GB/T11198.12-1989);尾氣中二氧化硫的含量按照國家環境保護總局標準HJ/T56-2000用碘量法測定。
以下實施例中吸收方式都是磁力攪拌鼓泡吸收,所述的工藝流程見圖1。
實驗中所用的儀器:NEXUS型FT-IR紅外光譜儀。
本發明涉及一種二氯亞碸氯化反應尾氣的處理方法,其特徵在於:包括以下步驟:
第一步,通過控制醇的用量,用醇對尾氣中的氯化氫進行二級吸收,得到工業上可用的氯化氫醇溶液,然後加熱蒸出二氧化硫;該加熱處理溫度範圍為80℃-120℃,時間範圍一般為1到5小時。主要是因為尾氣包含等摩爾的氯化氫和二氧化硫,二者在醇中的溶解度差異很大,通過加熱可以選擇性脫除二氧化硫。
第二步,對加熱蒸出的二氧化硫尾氣與吡啶吸收劑接觸,得到符合二氧化硫濃度排放標準的氣體和二氧化硫吡啶鹽,若是尾氣中每含64.0克二氧化硫,使用的吡啶量為150到220克,室溫下最佳的吡啶使用量為176-200克。若是太少的吡啶達不到吸收效果;而太多的吡啶又會使吸收效率降低,故此能得到最佳的效果。用吡啶吸收劑吸收時所用的溫度為0℃到30℃之間,用吡啶吸收劑吸收時所用的溫度為15℃到25℃之間。溫度高將使吸收效率降低,溫度太低使其在工業上運用時難以達到製冷要求。所述的吸收裝置可以是吸收塔(包括填料塔和篩板塔等),也可以是簡單的攪拌吸收釜或吸收槽等裝置,只要能達到吸收效果即可,並無特殊限制,工業上考慮吸收效率,以由耐腐蝕材料填充的吸收塔為好。
第三步,對結合有二氧化硫的吡啶鹽進行解吸,將氣態二氧化硫從吸收劑中解吸出來,得到高純度二氧化硫氣體的同時對吸收劑再生,再生後的吡啶溶液可以直接再次投入使用,其中解吸過程可以利用加熱方法進行,溫度控制在80-120℃,解吸過程的最佳溫度控制為90-110℃,使鹽分解,解析出SO2氣體。
實施例1
一摩爾氯化亞碸與醇羥基反應後產生的尾氣,經過甲醇溶液的二級吸收,將第一級吸收液於60℃加熱1.5小時脫除二氧化硫,收集的二氧化硫通入150克吡啶於10℃吸收後排放,廢氣按國家環境保護總局標準HJ/T56-2000的方法檢測,二氧化硫含量為5mg/m3(達到環保總局排放要求),吸收液冷卻後可以觀察到淺黃色晶體,經紅外檢測(譜圖見圖2),其紅外吸收明顯不同於吡啶。此晶體為二氧化硫與吡啶絡合的鹽;該晶體於60℃加熱後分解,重新變為吡啶。吡啶吸收液整體於90℃加熱解吸1小時,得到的吡啶吸收劑可循環使用,釋放出的二氧化硫去進一步深加工。
其中分析儀器及條件:NEXUS型FT-IR紅外光譜儀,KBr壓片。
由圖得出分析可知:二氧化硫的特徵吸收峰(游離二氧化硫為1300-1350)處已很不明顯。紅外對比與譜圖庫中吡啶鹽的相似度較高,說明吡啶已成鹽。
實施例2
與實施例1不同的是:一摩爾氯化亞碸與醇羥基反應後產生的尾氣,經過乙醇溶液的二級吸收,將第一級吸收液於70℃加熱3.5小時脫除二氧化硫,收集的二氧化硫通入180克吡啶於30℃吸收後排放,廢氣按國家環境保護總局標準HJ/T56-2000的方法檢測,二氧化硫含量為7mg/m3(達到環保總局排放要求)。吡啶吸收液於110℃加熱解吸1小時,得到的吡啶吸收劑可循環使用,釋放出的二氧化硫去進一步深加工。
實施例3
與實施例1不同的是:一摩爾氯化亞碸與醇羥基反應後產生的尾氣,經過正丁醇溶液的二級吸收,將第一級吸收液於115℃加熱1小時脫除二氧化硫,收集的二氧化硫通入180克吡啶20℃吸收後排放,廢氣按國家環境保護總局標準HJ/T56-2000的方法檢測,二氧化硫含量為4mg/m3(達到環保總局排放要求),得到二氧化硫的吡啶吸收液。吡啶吸收液於110℃加熱解吸1小時,得到的吡啶吸收劑可循環使用,釋放出的二氧化硫去進一步深加工。
實施例4
與實施例1不同的是:一摩爾氯化亞碸與醇羥基反應後產生的尾氣,經過正戊醇溶液的二級吸收,將第一級吸收液於130℃加熱5小時脫除二氧化硫,收集的二氧化硫通入180克吡啶0℃吸收後排放,廢氣按國家環境保護總局標準HJ/T56-2000的方法檢測,二氧化硫含量為2mg/m3(達到環保總局排放要求),得到二氧化硫的吡啶鹽吸收液。吡啶吸收液於100℃加熱解吸3小時,得到的吡啶吸收劑可循環使用,釋放出的二氧化硫去進一步深加工。
實施例5
與實施例1不同的是:一摩爾氯化亞碸與醇羥基反應後產生的尾氣,經過正丁醇溶液的二級吸收,將第一級吸收液於110℃加熱4小時脫除二氧化硫,收集的二氧化硫通入210克吡啶30℃吸收後排放,廢氣按國家環境保護總局標準HJ/T56-2000的方法檢測,二氧化硫含量為3mg/m3(達到環保總局排放要求),得到二氧化硫的吡啶鹽吸收液。吡啶吸收液於100℃加熱解吸2小時,得到的吡啶吸收劑可循環使用,釋放出的二氧化硫去進一步深加工。
實施例6
與實施例1不同的是:一摩爾氯化亞碸與醇羥基反應後產生的尾氣,經過乙醇溶液的二級吸收,將第一級吸收液於65℃加熱5小時脫除二氧化硫,收集的二氧化硫通入180克吡啶15℃吸收後排放,廢氣按國家環境保護總局標準HJ/T56-2000的方法檢測,二氧化硫含量為3mg/m3(達到環保總局排放要求),得到二氧化硫的吡啶鹽吸收液。吡啶吸收液於90℃加熱解吸3小時,得到的吡啶吸收劑可循環使用,釋放出的二氧化硫去進一步深加工。
最後應說明的是:以上所述僅為本發明的優選實施例而已,並不用於限制本發明,儘管參照前述實施例對本發明進行了詳細的說明,對於本領域的技術人員來說,其依然可以對前述各實施例所記載的技術方案進行修改,或者對其中部分技術特徵進行等同替換。凡在本發明的精神和原則之內,所作的任何修改、等同替換、改進等,均應包含在本發明的保護範圍之內。