催化異構化反應的方法與流程
2023-12-09 00:07:56 1
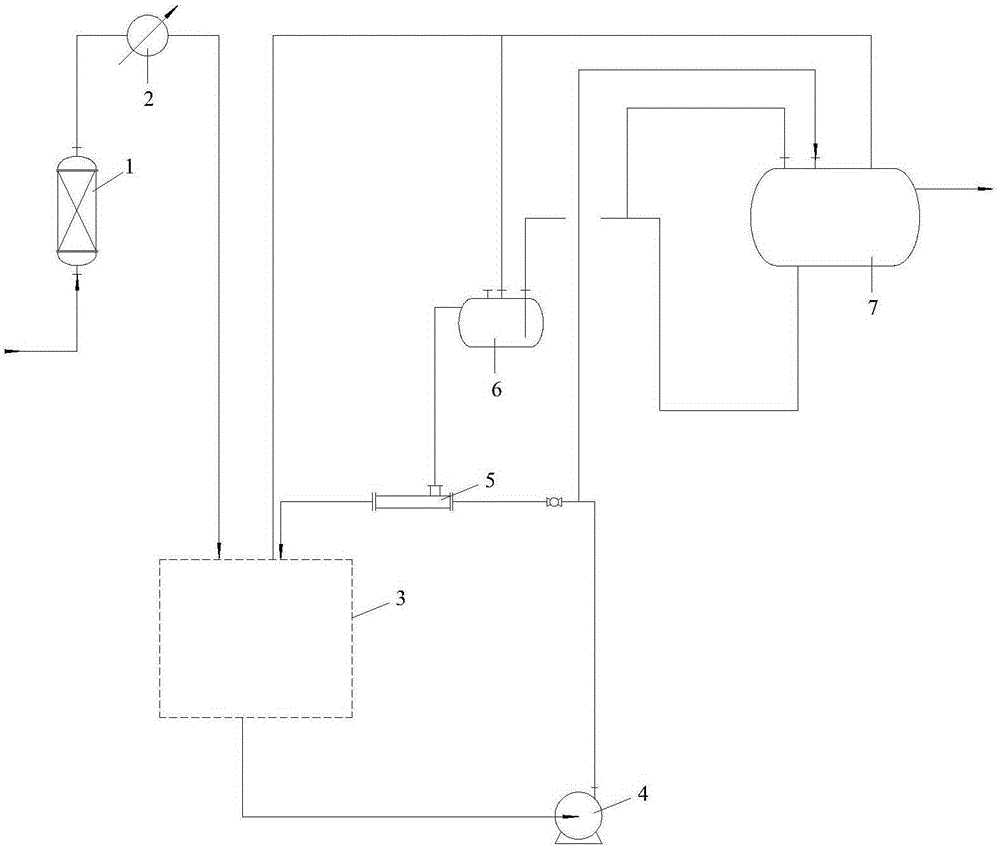
本發明涉及一種催化異構化反應的方法,可應用於相關離子液體催化異構化反應的工業連續生產中
背景技術:
石腦油裂解生產乙烯的過程中,裂解汽油經過兩段加氫和芳烴抽提後副產大量的抽餘油,目前抽餘油主要用作生產溶劑油,基本沒有進行提升附加值利用,部分返回裂解爐作為裂解原料,但是由於環烷烴含量較高,烯烴收率較低;且較高的環戊烷和甲基環戊烷也不適宜作為重整原料使用。抽餘油中C6烷烴佔40%以上,其中含有大量的包括甲基環戊烷和環己烷在內的環烷烴,因此從抽餘油中分離出C6餾分並將甲基環戊烷異構化為環己烷,然後通過精餾得到純度較高的環己烷將會極大提高抽餘油的利用價值。
離子液體是由有機陽離子和無極陰離子構成,在室溫下通常是液態的,有些種類甚至低於室溫也稱液態的鹽類。它們具有非揮發性或零蒸汽壓、寬沸程、寬電化學窗口、強的靜電場、良好的導電性,具有選擇性溶解力和可設計性等特點,其這些特殊的物性給化學研究開闢了一個全新的領域,是一種很有前景被開發利用的介質或軟功能材料。由於構成離子液體的陰、陽離子種類繁多,可通過簡單的變換不同離子來控制它的多種物理和化學性質,它不僅在電化學、有機合成、生物化學、催化、分離等方面具有獨特的作用,而且室溫離子液體作為一種環境友好的催化劑和溶劑,符合綠色化學概念,有望面臨全球環境安全問題的現代工業帶來突破性的進展。
早在20世紀80年代初期,英國BP公司和法國IFP等研究機構開始探索離子液體作為溶劑與催化劑的可能性,並在Friedel-Crafts反應、烷基化、異構化、烯烴二聚及催化加氫和Diels-Alder等反應中取得較好的結果。
技術實現要素:
本發明所要解決的技術問題是現有技術中存在的工藝流程複雜,不易操作,催化活 性低,轉化率不穩定等問題,提供了一種新的催化異構化反應的方法,該方法用於催化異構化反應時,具有工藝流程簡單,易操作,催化活性高,轉化穩定性好等優點。
為解決上述技術問題,本發明的技術方案如下:
以C6抽餘油為原料,在油劑體積比0.1~5,反應溫度50~80℃,反應壓力0.1~1.0MPa的條件下,原料與離子液體催化劑在反應器中反應得到環己烷。
上述技術方案中,優選的,反應器採用帶夾套的攪拌釜反應器,攪拌器的轉速為50~200rpm,物料在攪拌釜反應器中的停留時間控制在0.5~12h。更優選的,攪拌器的轉速為100~180rpm。若反應熱相對較大,可通過攪拌釜反應器的夾套採用冷卻介質進行撤熱。
上述技術方案中,優選的,反應後的產物經過液液分離器將反應產物和催化劑分離,下層的催化劑經過活性組分補加罐補充活性組分後返回攪拌釜反應器,上層的產物進入產品罐。
上述技術方案中,優選的,原料C6抽餘油以質量百分比計,包括以下組分:0~50%的異己烷,0~50%的正己烷,10~100%的甲基環戊烷,0~10%的環己烷,0~50ppm的水。更優選的,50~100%的甲基環戊烷,0~2%的環己烷,0~10ppm的水。
上述技術方案中,優選的,原料先經過乾燥器脫水至0~30ppm,更優選為0~10ppm。然後經預熱器加熱至25~80℃後,更優選為50~70℃,進入攪拌釜反應器,攪拌釜反應器全密閉。
上述技術方案中,優選的,物料循環反應方式為外循環,即反應後的部分物料,經過靜態混合器,與活性組分補加罐溢流的離子液體催化劑混合後返回攪拌釜反應器。
上述技術方案中,優選的,攪拌釜反應器出來的部分物料進入液液分離罐,反應產物從液液分離罐的上部溢出進入產品罐,離子液體催化劑從液液分離罐的底部溢流,進入活性組分補加罐。
上述技術方案中,優選的,液液分離罐底部溢流的離子液體催化劑需進入活性組分補加罐,活性組分補加罐設有活性組分添加口,且進料管插入液面以下,離子液體催化劑溶解活性組分後從活性組分補加罐上部溢流回反應器。
上述技術方案中,優選的,在反應過程中,離子液體催化劑中的活性組分遇水易分解,造成催化劑活性損失。
上述技術方案中,優選的,攪拌釜反應器、活性組分補加罐和液液分離罐的氣相空間相互連通,壓力平衡,離子液體催化劑通過自流的方式從液液分離罐返回攪拌釜反應 器。
離子液體催化劑在反應過程中,活性組分會逐漸減少,離子液體保持不變。且活性組分為固體,可溶解在離子液體中。若直接補加在攪拌釜反應器,會造成攪拌槳葉、泵的損壞,以及靜態混合器的堵塞。本發明設置活性組分補加罐,且頂部設有活性組分添加口,活性組分補加罐進料管插入液面以下,離子液體催化劑溶解活性組分後從活性組分補加罐上部溢流回攪拌釜反應器。為增加活性組分的溶解效果,優選為帶攪拌的活性組分補加罐。
採用本發明的技術方案,工藝流程簡單,易於實現,離子液體催化劑與反應產物容易分離可循環套用,且能及時補充活性組分保證催化劑持續的活性。在上述條件下反應,甲基環戊烷轉化率高,具有良好的經濟效益,與分離正己烷溶劑油等工藝聯合使用效果更佳,是綜合利用抽餘油副產的有效途徑。
下面通過實施例對本發明作進一步的闡述,但是這些實施例無論如何都不對本發明的範圍構成限制。
附圖說明
圖1為離子液體催化異構化反應的工藝流程簡圖。
如圖1中,用於本發明工藝的反應裝置包括:1為乾燥器,2為預熱器,3為反應器,4為循環泵,5為靜態混合器,6為活性組分補加罐,7為液液分離罐。
圖1中,包括異己烷,正己烷,甲基環戊烷、環己烷,微量水的C6抽餘油原料先經乾燥器1脫水,然後經預熱器2加熱至一定溫度,進入反應器3,發生反應得到環己烷。反應產物經循環泵4一部分循環回反應器,一部分進入液液分離罐7靜置分層,上層的反應產物作為產品採出,下層的催化劑經溢流口進入活性組分補加罐6,補加活性組分的催化劑返回反應器繼續反應。
下面通過實施例對本發明作進一步的闡述,但是這些實施例無論如何都不對本發明的範圍構成限制。
具體實施方式
【實施例1】
按圖1所示的工藝流程圖進行離子液體催化異構化反應。
將包括40%異己烷,30%正己烷,30%甲基環戊烷的原料C6抽餘油以一定的流量經 乾燥器1、預熱器2加熱至60℃後,進入攪拌釜反應器3,控制攪拌釜反應器3中的油劑體積比為3,攪拌器轉速為200rpm,反應溫度為70℃,壓力為0.15MPa,控制攪拌釜反應器3的液位,使物料在反應體系中的停留時間為2.5h。離開反應釜的物料一部分經過循環泵4循環回攪拌釜反應器3,一部分進入液液分離罐7,在液液分離罐7中,離子液體催化劑和反應產物靜置分層,上層的反應產物採出進入產品罐,控制反應產物採出量與進料量一致。下層的催化劑通過溢流口進入活性組分補加罐6,活性組分補加罐6底部裝有固體活性組分,補充了活性組分的離子液體催化劑與循環物料經過靜態混合器5混合後返回攪拌釜反應器3。
甲基環戊烷的轉化率大於60%,選擇性為大於99%。
【實施例2】
將包括90%甲基環戊烷,10%的環己烷,10ppm水的原料C6抽餘油以一定的流量經乾燥器1脫水至5ppm、預熱器2加熱至80℃後進入攪拌釜反應器3,控制攪拌釜反應器3中的油劑體積比為5,攪拌器轉速為150rpm,反應溫度為80℃,通入氮氣保持壓力為1.0MPa,控制攪拌釜反應器3的液位,使物料在反應體系中的停留時間為1.5h。離開反應釜的物料一部分經過循環泵4循環回攪拌釜反應器3,一部分進入液液分離罐7,在液液分離罐7中,離子液體催化劑和反應產物靜置分層,上層的反應產物採出進入產品罐,控制反應產物採出量與進料量一致。下層的催化劑通過溢流口進入活性組分補加罐6,活性組分補加罐6底部裝有固體活性組分,補充了活性組分的離子液體催化劑與循環物料經過靜態混合器5混合後返回攪拌釜反應器3。
甲基環戊烷的轉化率大於55%,選擇性為大於99%。
【實施例3】
將包括5%異己烷,10%正己烷,80%甲基環戊烷,5%的環己烷的原料C6抽餘油以一定的流量經乾燥器1、預熱器2加熱至50℃後進入攪拌釜反應器3,控制攪拌釜反應器3中的油劑體積比為1,攪拌器轉速為100rpm,反應溫度為60℃,通入氮氣壓力為0.3MPa,控制攪拌釜反應器3的液位,使物料在反應體系中的停留時間為5h。離開反應釜的物料一部分經過循環泵4循環回攪拌釜反應器3,一部分進入液液分離罐7,在液液分離罐7中,離子液體催化劑和反應產物靜置分層,上層的反應產物採出進入產品罐,控制反應產物採出量與進料量一致。下層的催化劑通過溢流口進入活性組分補加罐6,活性組分補 加罐6底部裝有固體活性組分,補充了活性組分的離子液體催化劑與循環物料經過靜態混合器5混合後返回攪拌釜反應器3。
甲基環戊烷的轉化率大於55%,選擇性為大於99%。
【實施例4】
將包括40%異己烷,49.9%正己烷,10%甲基環戊烷,0.1%的環己烷,50ppm水的原料C6抽餘油以一定的流量經乾燥器1脫水至30ppm、預熱器2加熱至30℃後,進入攪拌釜反應器3,控制攪拌釜反應器3中的油劑體積比為1,攪拌器轉速為50rpm,反應溫度為50℃,壓力為0.1MPa,控制攪拌釜反應器3的液位,使物料在反應體系中的停留時間為12h。離開反應釜的物料一部分經過循環泵4循環回攪拌釜反應器3,一部分進入液液分離罐7,在液液分離罐7中,離子液體催化劑和反應產物靜置分層,上層的反應產物採出進入產品罐,控制反應產物的流量為50L/h。下層的催化劑通過溢流口進入活性組分補加罐6,活性組分補加罐6底部裝有固體活性組分,補充了活性組分的離子液體催化劑與循環物料經過靜態混合器5混合後返回攪拌釜反應器3。
甲基環戊烷的轉化率大於55%,選擇性為大於99%。
【比較例1】
實施方式與實施例2相同,不同的是取消活性組分補加罐,即液液分離罐底部的催化劑溢流直接返回反應器。經過長時間的運行,甲基環戊烷的轉化率的轉化率<50%。主要是由於原料中的微量水在反應器中積累,造成催化劑活性損失。