油水分離裝置的製作方法
2024-04-05 03:55:05 2
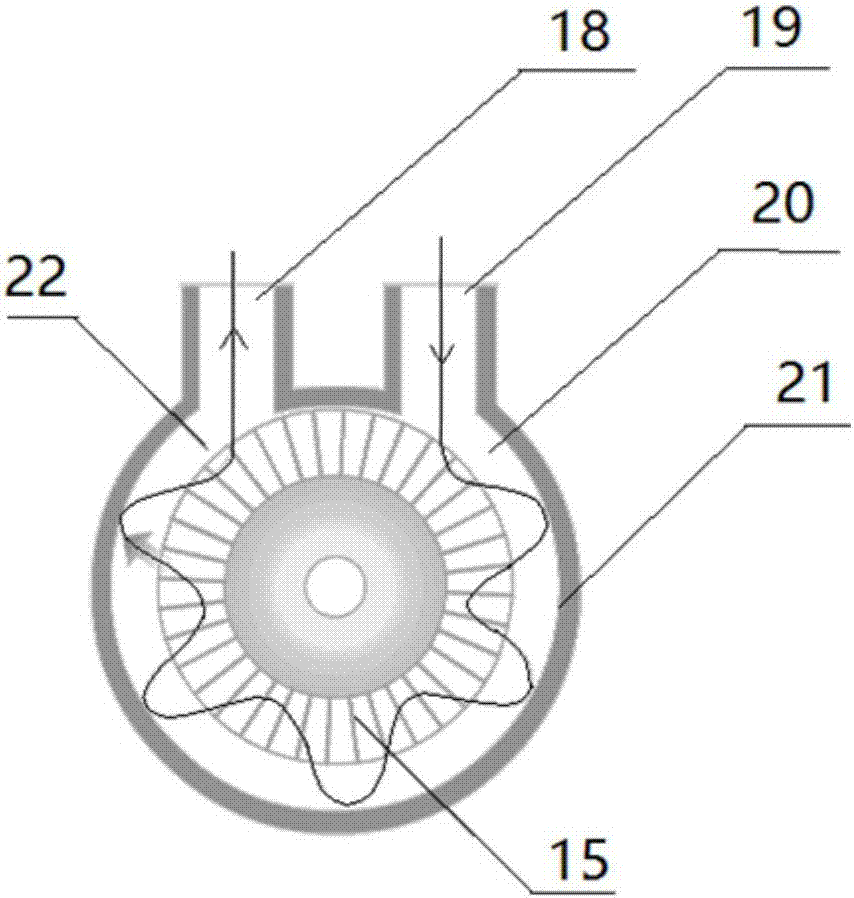
本實用新型涉及塗裝領域,特別涉及油水分離裝置。
背景技術:
在切削液、塗裝前處理領域,使用的料液中含大量的有價值物料,如切削乳化液、脫脂劑等;這些物質如果直接按照廢水處理的方式處理,由於屬於烴類,同時含大量的含油物質、金屬離子等,屬於危險廢物,不僅成本高,而且造成了極大的浪費。因此,相對綠色環保的處理方式是,採用一定的方式將料液中的油和料液進行分離,讓料液回到原槽罐,讓油作為廢液處理,這種處理方式不僅大大減少了廢物的處理量,而且大部分料液回到了原槽罐。
但是,無論是切削液還是塗裝前處理過程的清洗液,都含有乳化功能的清洗劑成分,因此,油與料液之間,包含多種形態,形態1:油與料液是雙向體系,即油是漂浮的浮油;形態2:料液與油之間是乳化體系。對於漂浮體系,相對而言是比價容易處理的,採用的方式基本是通過撇油器吸取上層的油層,然後通過粗顆粒化技術進行分離,即讓油彼此聚集成大顆粒,上浮;清液通過粗顆粒化層,然後再回到原槽體;或者直接通過溢流的方式將上層撇除,但是比利用粗顆粒化技術,浪費更多的可利用料液。
對於乳化體系,由於是以回收為目的的,因此,傳統採用化學藥劑破乳的方式,會引入新的物質,可能會對料液產生汙染問題,並不能使用。在現行的處理方式中,常用的方式是通過加熱高溫破乳,即通過將料液與油的乳化體系加熱至80-95℃,利用高溫將乳化體系打破,然後讓油上浮,通過溢流或者其他的方式分離。由於採用高溫,需要將溫度加熱至80-95℃,因此,需要消耗大量的熱量,能耗很高。
技術實現要素:
為解決上述現有技術方案中的不足,本實用新型提供了一種分離效果好、無需高溫、能耗低的油水分離裝置。
本實用新型的目的是通過以下技術方案實現的:
一種油水分離裝置,所述油水分離裝置包括容器,所述油水分離裝置進一步包括:
第一隔板、第二隔板和第三隔板,所述第一隔板和第二隔板將所述容器內部分割為第一區、第二區和第三區;所述第一隔板的底端與所述容器的底部間的距離大於零;第三隔板,所述第三隔板設置在所述第二區內的底部;
第一連通管,所述第一連通管的兩端分別連通所述第一區和第四區;
第四區,所述第四區設置在所述第二區內;
破乳裝置,所述破乳裝置的輸入端、輸出端連通所述第二隔板和第二隔板之間的第二區內;
第二連通管,所述第二連通管的進口端設置在所述第二區內,出口端設置在所述第三區內,且上下可調。
與現有技術相比,本實用新型具有的有益效果為:
1.在低溫的情況下更為高效的分離出廢油,不僅能耗低,而且分離更為徹底;
2.採用了旁路式破乳裝置,可以在現有油水分離器的基礎上改造,從而降低回收式低溫油水分離器的成本。
附圖說明
參照附圖,本實用新型的公開內容將變得更易理解。本領域技術人員容易理解的是:這些附圖僅僅用於舉例說明本實用新型的技術方案,而並非意在對本實用新型的保護範圍構成限制。圖中:
圖1是根據本實用新型實施例的油水分離裝置的結構簡圖;
圖2是根據本實用新型實施例的第一破乳裝置的結構簡圖;
圖3是根據本實用新型實施例的轉動輪的結構簡圖
圖4是根據本實用新型實施例的殼體內壁的結構簡圖
圖5是根據本實用新型實施例的第二破乳裝置的結構簡圖。
具體實施方式
圖1-5和以下說明描述了本實用新型的可選實施方式以教導本領域技術人員如何實施和再現本實用新型。為了教導本實用新型技術方案,已簡化或省略了一些常規方面。本領域技術人員應該理解源自這些實施方式的變型或替換將在本實用新型的範圍內。本領域技術人員應該理解下述特徵能夠以各種方式組合以形成本實用新型的多個變型。由此,本實用新型並不局限於下述可選實施方式,而僅由權利要求和它們的等同物限定。
實施例1:
圖1示意性地給出了本實用新型實施例的油水分離裝置的結構簡圖,如圖1所示,所述油水分離裝置包括:
容器15,所述容器具有進口1、出口14;
第一隔板81、第二隔板82和第三隔板11,所述第一隔板和第二隔板將所述容器內部分割為第一區9、第二區3和第三區4;所述第一隔板的底端與所述容器的底部間的距離大於零;第三隔板,所述第三隔板設置在所述第二區內的底部,所述第三隔板的上端位置高於所述第一隔板的底端;
第一連通管8,所述第一連通管的兩端分別連通所述第一區和第四區,其中進口設置在所述第一區內的中上層,以便第一區內的浮油通入第四區內;閥門7設置在所述第一連通管8上;
填料層5,所述填料層內設置空心球填料,用於油水快速的分離;
第四區2,所述第四區設置在所述第二區內,且圍成第四區的一個側壁與所述第一隔板81共用;所述第四區具有排油口10;
第二連通管6,所述第二連通管的進口端設置在所述第二區內,出口端設置在所述第三區內,且上下可調;
第四隔板83,所述第四隔板設置在所述容器的底部,破乳裝置的進口端和輸出端分別處於所述第四隔板的兩側,所述第四隔板的上端的位置高於所述進口端和輸出端的位置;
破乳裝置12,所述破乳裝置的輸入端、輸出端連通所述第二隔板和第二隔板之間的第二區內;
圖2-4示意性地給出了本實用新型實施例的破乳裝置的結構簡圖,如圖2-4所示,所述破乳裝置包括:
殼體20,所述殼體整體呈圓柱形,一側具有進口19、出口18;
轉動軸16,所述轉動軸穿過所述殼體;
轉動輪15,所述轉動輪設置在殼體內的轉動軸上,並具有沿徑向分布的凹槽17;所述轉動輪和所述殼體內壁21間為流體通道22,所述流體通道與所述進口、出口連通;所述殼體的在所述進口和出口之間部分的內壁到轉動輪的距離小於其它部分到轉動輪的距離;
固定部25,所述固定部設置在所述殼體的臨著所述流體通道的內壁上,與切向方向呈25-45°角,所述固定部的迎著流體的一側具有突起24。
根據上述油水分離裝置在切削液油水分離中的應用,在該應用中:
切削液進入第一區內,由於切削液中油含量高,在第一區會累計較多的油,當廢油累積到一定程度,超過第四區溢流液位時,則打開閥門7,利用第一區與第四區的液位差,第一區的廢油自動溢流至第四區,進入第四區的廢油通過排油口10排放;
切削液在第四區的下部,且在第一隔板和第三隔板之間向上流動,進入第二區中,填料層5讓油能夠快速的分離;旁路破乳裝置從第三隔板和第四隔板之間的第二區內抽取乳化液,進入到旁路處理處理器12中進行破乳,具體為:流體經過19進入到流道22中,進入被轉動輪15中的凹槽17,在轉動輪15旋轉時,凹槽中的液體被甩出,碰到內壁21,再次發生方向折轉進入到凹槽17,再次被甩出,從而獲得流速和壓力。在流體進出凹槽時,由於時序的不同,導致流體之間彼此摩擦,以及流體與凹槽之間摩擦,發生破乳;固定部25和突起24進一步強化碰撞與破乳,讓乳化體系中脫脂液和油分離;破乳後的液體送回到從第三隔板和第四隔板之間的第二區內;
第二連通管6的出口高度是可調的,用於調節第二區區廢油溢流至第四區的量;在第三區4的底部,有回收液出口14,回收液回到應用槽罐體。
實施例2:
本實用新型實施例的油水分離裝置,與實施例1不同的是:
1.圖5示意性地給出了本實用新型實施例的破乳裝置的結構簡圖,如圖5所示,所述破乳裝置包括:
第一管26,所述第一管通過彎曲連接部28與所述第二管連接,所述第一管和第二管的中心軸線間的夾角為銳角或直角;
第二管,所述第二管具有沿流體流動方向的內徑收縮段33和內徑膨脹段34;
多孔板36,所述多孔板具有通孔32,設置在所述第二管內內徑收縮段的上遊;
第三管30,所述第三管穿過所述多孔板,出口端35在所述內徑收縮段和內徑膨脹段間移動,進口端設置在所述連接部外;所述第三管與所述連接部的壁、多孔板分別通過螺紋孔29、31連接;
單向閥37,外部空氣通過該閥門進入第三管內,第二管內的流體無法通過單向閥而流至外部空間;
氣源,所述氣源連通所述進口端;
2.不再設置第四隔板,所述破乳裝置的在第二區內的輸出端的位置高於所述第二連通管的進口端的位置;
3.填料層被蜂窩斜板代替。
根據上述油水分離裝置在塗裝前處理中清洗液的油水分離中的應用,與實施例1不同的是:
在破乳中,流體進入第一管26、第二管內,經過多孔板36,進入內徑收縮段33中,由於橫截面積縮小,流速增大;當流體進入到內徑膨脹段34中後,橫截面積變大,在第三管出口段35處產生吸力,將空氣吸入到該管段,與流體進行混合;
當含油熱水或者含油脫脂液經過該第二破乳裝置時,經過多孔板36的水力作用,以及內徑收縮段和內徑膨脹段的水力作用,實現破乳,而經過空氣混合,油與空氣結合,極易上浮。
實施例3:
本實用新型實施例的油水分離裝置,與實施例1不同的是:
實施例1中的破乳裝置作為第一破乳裝置,實施例2中的破乳裝置作為第二破乳裝置,設置在所述第一破乳裝置的下遊,進一步提高破乳效果。