一種解決焊接不良的電池連接器及製作方法與流程
2024-03-31 09:33:05 1
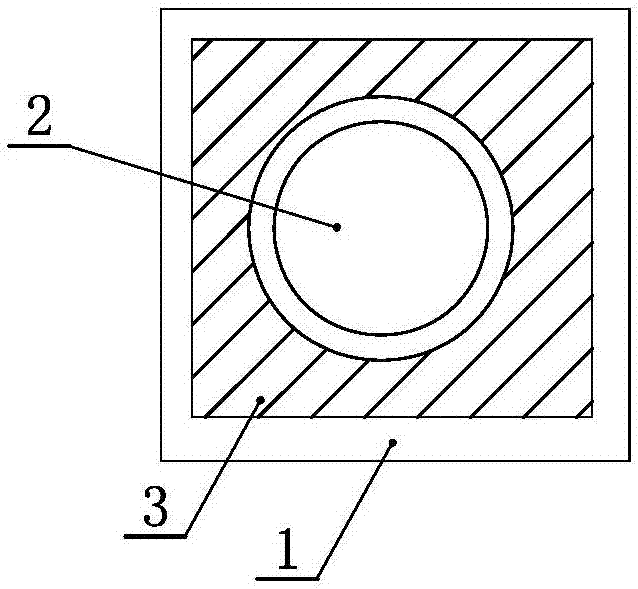
本發明涉及印刷電路板技術領域,特別涉及一種解決焊接不良的電池連接器及製作方法。
背景技術:
目前現有產品的電池連接器經常會出現焊接不良,有時不良率甚至高達30%左右。如圖1中標記a和標記b的區域為不良pin腳的位置。針對現有的電池連接器來說,為了能提高焊接效果,就必須要增加焊接的時間,然而,增加焊接時間的話,就會造成銅箔受熱時間過長,從而導致銅皮掉落,造成板卡報廢。
技術實現要素:
為克服現有技術中存在的問題,本發明提供了一種解決焊接不良的電池連接器及製作方法。
本發明解決其技術問題所採取的技術方案是:該種解決焊接不良的電池連接器,包括pcb,pcb上設有若干pin腳插孔,pin腳插在對應位置的pin腳插孔內,部分pin腳與pcb間設有銅箔,pin腳插孔外的銅箔為線條狀,線條狀的銅箔一端接觸pin腳,銅箔的其餘部分貼附固定在pcb上。
進一步地,所述線條狀的銅箔有一條。
進一步地,所述線條狀的銅箔包括若干條。
一種解決焊接不良的電池連接器的製作方法,包括以下步驟:
步驟s1:對pcb鑽通孔/盲孔,部分通孔作為pin腳插孔;
步驟s2:沉銅,對步驟s1中鑽的通孔/盲孔進行孔內沉銅以形成孔內銅箔;
步驟s3:沉銅,對步驟s1中鑽的通孔/盲孔進行孔外沉銅以形成孔外銅箔;孔外銅箔為線條狀銅箔,線條狀銅箔的一端與步驟s2中的孔內銅箔連為一體;
步驟s4:將pin腳插入經過沉銅的pin腳插孔內。
進一步地,在進行步驟s2之前對步驟s1中鑽的通孔/盲孔進行磨孔、溶脹和去玷汙處理。
進一步地,所述線條狀銅箔的寬度小於pin腳插孔直徑的二分之一。
綜上,本發明實施例的有益效果如下:
經過確認與分析,此電池連接器pcb(printedcircuitboard印刷電路板)layout(設計、布局)區域銅箔面積太大(圖2),即連接器pin腳處的銅箔面積較大,導致pin(物料本體引腳)腳在上錫的過程中,由於大部分熱量被大銅箔吸收走,從而導致pin腳不上錫,造成焊接不良。由於該發明在其他部件保持不變的條件下將銅箔面積變小,及有原來的面式銅箔改為線條式銅箔,從而實現了對焊接區域銅箔吸收熱量的降低,提升了上錫的效果,保證了焊接質量。也就是說,將所焊接區域的大銅箔面積減小,降低銅箔本身所吸收的熱量,當銅箔面積減少後,其吸收的能力也就減少,同時,連接器焊接的pin腳散熱也就慢了,從而達到滿足上錫要求的效果。
由於該發明實施例線條狀的銅箔吸收熱量較少,在進行同一上錫操作過程中減少了上錫所需時間,提高了上錫效率。
由於該發明實施例線條狀的銅箔吸收熱量較少,降低了散熱速度,給焊接提供了充分的潤展時間,因此pin腳焊接牢固,避免了焊接不良的發生。
該發明實施例適用於所有帶有該種連接器的板卡,有效的解決了電池連接器的焊接不良問題,降低了因為不良而帶來的維修成本、板卡報廢成本、人力成本等。該發明實施例的有益效果還表現在:有效的加強了良品的產出,從而增加了產能效益,帶來較大的經濟效益。
附圖說明
圖1為現有電池連接器焊接不良結構示意圖;
圖2為現有結構中pin腳位置銅箔的設計圖;
圖3為本發明中pin腳位置一條銅箔的設計圖;
圖4為本發明中pin腳位置若干條銅箔的設計圖。
圖中:
1pcb、2pin腳、3銅箔。
具體實施方式
以下結合附圖對本發明的特徵和原理進行詳細說明,所舉實施例僅用於解釋本發明,並非以此限定本發明的保護範圍。
該發明設計的解決焊接不良的電池連接器,包括pcb1,pcb1上設有若干pin腳插孔,pin腳2插在對應位置的pin腳插孔內,部分pin腳2與pcb1間設有銅箔3,pin腳插孔外的銅箔3為線條狀,線條狀的銅箔3一端接觸pin腳2,銅箔3的其餘部分貼附固定在pcb1上。
實施例一:如圖3所示,線條狀的銅箔有一條,且線條狀銅箔3的寬度小於pin腳插孔直徑的二分之一。線條狀的銅箔吸收熱量較少,降低了散熱速度,給焊接提供了充分的潤展時間,因此pin腳焊接牢固,避免了焊接不良的發生。
實施例二:如圖4所示,線條狀的銅箔包括若干條。且每條線條狀銅箔3的寬度小於pin腳插孔直徑的二分之一。線條狀的銅箔吸收熱量較少,降低了散熱速度,給焊接提供了充分的潤展時間,因此pin腳焊接牢固,避免了焊接不良的發生。
一種解決焊接不良的電池連接器的製作方法,包括以下步驟:
步驟s1:對pcb1鑽通孔/盲孔,部分通孔作為pin腳插孔。為了保證沉銅的效果,對鑽的通孔/盲孔進行磨孔、溶脹和去玷汙處理,防止通孔/盲孔內存在毛刺、氣泡和殘渣等。經過磨孔處理將孔內的毛刺去除。經過溶脹處理將氣泡去除,同時使得通孔/盲孔內壁更為緊實,減少沉銅步驟中銅的浪費。通過去玷汙處理將孔內的殘渣等雜物除去,便於沉銅步驟中銅箔3的形成。
步驟s2:沉銅,對步驟s1中鑽的通孔/盲孔進行孔內沉銅以形成孔內銅箔3。
步驟s3:沉銅,對步驟s1中鑽的通孔/盲孔進行孔外沉銅以形成孔外銅箔3。孔外銅箔3為線條狀銅箔3,線條狀銅箔3的一端與步驟s2中的孔內銅箔3連為一體。在保證銅箔3起到導電體作用的同時,為了儘可能的減少銅箔3對上錫過程中熱量的吸收,線條狀銅箔3的寬度小於pin腳插孔直徑的二分之一。
步驟s4:將pin腳2插入經過沉銅的pin腳插孔內。
本發明的創新點不僅在於解決了背景技術中提到的問題,更重要的是,本發明找到了電池連接器經常會出現焊接不良的原因。
經過確認與分析,此電池連接器pcb(printedcircuitboard印刷電路板)layout(設計、布局)區域銅箔面積太大(圖2),即連接器pin腳處的銅箔面積較大,導致pin(物料本體引腳)腳在上錫的過程中,由於大部分熱量被大銅箔吸收走,從而導致pin腳不上錫,造成焊接不良。由於該發明在其他部件保持不變的條件下將銅箔面積變小,及有原來的面式銅箔改為線條式銅箔,從而實現了對焊接區域銅箔吸收熱量的降低,提升了上錫的效果,保證了焊接質量。也就是說,將所焊接區域的大銅箔面積減小,降低銅箔本身所吸收的熱量,當銅箔面積減少後,其吸收的能力也就減少,同時,連接器焊接的pin腳散熱也就慢了,從而達到滿足上錫要求的效果。
上述實施例僅僅是對本發明的優選實施方式進行的描述,並非對本發明的範圍進行限定,在不脫離本發明設計精神的前提下,本領域相關技術人員對本發明的各種變形和改進,均應擴入本發明權利要求書所確定的保護範圍內。
技術特徵:
技術總結
一種解決焊接不良的電池連接器及製作方法,Pin腳與PCB間設有銅箔,Pin腳插孔外的銅箔為線條狀,線條狀的銅箔一端接觸Pin腳,銅箔的其餘部分貼附固定在PCB上。製作步驟:S1:對PCB鑽通孔/盲孔,部分通孔作為Pin腳插孔;S2:沉銅,形成孔內銅箔;S2:沉銅,形成孔外銅箔;S4:將Pin腳插入經過沉銅的Pin腳插孔內。在其他部件保持不變的條件下將銅箔面積變小,及有原來的面式銅箔改為線條式銅箔,從而實現了對焊接區域銅箔吸收熱量的降低,提升了上錫的效果,保證了焊接質量。也就是說,將所焊接區域的大銅箔面積減小,降低銅箔本身所吸收的熱量,當銅箔面積減少後,其吸收的能力也就減少,同時,連接器焊接的Pin腳散熱也就慢了,從而達到滿足上錫要求的效果。
技術研發人員:張小行
受保護的技術使用者:鄭州雲海信息技術有限公司
技術研發日:2017.07.20
技術公布日:2017.09.15