觸頭座擠壓模具及其擠壓成型方法與流程
2024-02-19 00:43:15 1
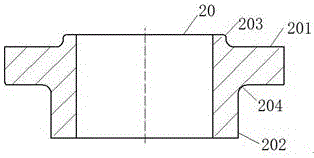
本發明涉及一種觸頭座擠壓模具及其擠壓成型方法。
背景技術:
高質量低成本的開關零部件對提高產品競爭力有著非常重要的意義,純銅因其良好的導電性而被廣泛應用於高壓開關零件的製造。純銅的價格很高,因此很有必要對這些零部件的生產工藝進行研究,以提高材料的利用率。對於如圖1所示的形狀為帶凸緣的管狀結構的純銅觸頭座,這類工件可通過原有的如圖2所述的管狀坯料加工成型,觸頭座20具有直筒部和設置在直筒部外周的凸緣部201,直筒部包括位於凸緣部上方的上端部203和下端部202,該觸頭座的凸緣的端部與側壁的結合處及觸頭座的上端部的外周均設置有外圓角204,且直筒部和凸緣部的徑向尺寸差別較大,目前此類零部件多採用多次熱擠壓-機加工成型的方法或者直接對管料採用機加工的方法製造,在這些加工方法中,通過採用機加工將管狀坯料成型為觸頭座,其機加工量比較大,且材料利用率較低,同時成型的觸頭座的力學性能比較低。多道次熱擠壓加工時,通常是選用棒狀材料,先通過一次擠壓將棒狀材料變形成帶有部分凸緣的管狀結構,其中管狀結構的徑向尺寸與觸頭座的直筒部的徑向尺寸一致;然後再對部分凸緣進行一次、兩次等多次擠壓,使部分凸緣可以墩粗成最終的凸緣部,進而形成最終的觸頭座,但是使用這種多道次擠壓方法成型的觸頭座,但是使用這種多道次擠壓方法成型的觸頭座,所佔工時較長,生產效率較低;多次擠壓也需要設計多套模具,製造成本增加。因此,設計一種能夠實現將觸頭座一次擠壓成型的擠壓模具很有必要。
技術實現要素:
本發明的目的在於提供一種觸頭座擠壓模具,以解決現有技術中觸頭座無法通過一次擠壓成型的問題;本發明的目的還在於提供一種實施該觸頭座擠壓模具的擠壓成型方法。
為實現上述目的,本發明觸頭座擠壓模具的技術方案是:
觸頭座擠壓模具,包括可相對移動的上模體和下模體,上模體和下模體的其中一個包括凹模,另一個包括凸模,凹模上設置有孔口朝向凸模的成型孔,凹模或凸模上設置有用於插裝於坯料的內孔中的定位型芯,所述定位型芯的外徑與所述坯料的內徑尺寸一致,所述成型孔包括大孔段和小孔段,所述大孔段的孔徑大於坯料的外徑,所述小孔段的孔徑小於坯料的外徑。
凹模設置在下模體上,所述定位型芯固定穿裝於凹模內。
凸模上設置有供定位型芯導向插入的容納孔,所述容納孔包括與定位型芯外徑一致的小徑段和設置在小徑段上方的大徑段,所述大徑段內設置有與外界相通的第一通氣孔,所述定位型芯上設置有用於將凹模的小孔段的底部孔腔與容納孔的孔腔連通的通氣孔。
觸頭座擠壓模具還包括設置在下模體上的頂料機構,所述頂料機構包括可沿定位型芯軸線方向導向移動的套設在定位型芯外周並延伸至成型孔內的頂料環,所述頂料環的外徑與小孔段孔徑一致,頂料環的內徑與定位型芯的外徑一致。
下模體還包括設置在凹模下側的凹模支撐座,凹模支撐座上設置有供定位型芯穿過的穿裝孔,所述頂料環可在穿裝孔內上下移動,頂料環的外周設置有凸緣,所述穿裝孔具有在頂料環移動的過程中與凸緣擋止配合的限位部。
頂料機構還包括導向設置在頂料環下側的用於頂推頂料環以將觸頭座推出成型孔的頂杆,所述頂杆不少於兩個,沿頂料環的軸向間隔布置,所述頂杆的下端連接有用於將頂杆固定為一體的頂板。
凹模的大孔段與凹模的小孔段的連接處設置有倒圓角。
凹模的徑向外側套設有與凹模錐面配合的預應力圈,所述下模體還包括固設於凹模支撐座上的壓套,壓套具有用於將預應力圈固定在凹模上的內翻沿。
本發明使用的觸頭座擠壓模具的擠壓成型方法的技術方案是:
使用觸頭座擠壓模具的擠壓成型方法,將管狀坯料套設在定位型芯上,通過凹模和凸模的相對導向移動擠壓坯料;坯料的內徑與定位型芯的外徑尺寸一致,坯料的外徑大於凹模的小孔段孔徑,坯料的外徑小於凹模的大孔段的孔徑。
本發明的有益效果是:相比於現有技術,本發明所涉及的觸頭座擠壓模具,包括可相對導向移動的上模體和下模體,上模體和下模體的其中一個包括凹模,另一個包括凸模,凹模上設置有孔口朝向凸模的成型孔,凹模或凸模上設置有用於插裝於坯料的內孔中的定位型芯,所述定位型芯的外徑與所述坯料的內徑尺寸一致,所述成型孔包括大孔段和小孔段,所述大孔段的孔徑大於坯料的外徑,所述小孔段的孔徑小於坯料的外徑,通過定位型芯保證坯料的內徑尺寸及其在模具中的位置,通過在凹模上設置大孔段和小孔段,且大孔段的孔徑大於坯料的外徑,所述小孔段的孔徑小於坯料的外徑,由此可實現在擠壓成型過程中,坯料成型為凸緣部的部分變形量較小,且在小孔段中形成觸頭座的直筒部,實現一次擠壓成型,結構比較簡單,且加工效率較高,成本較低。
附圖說明
圖1為本發明所要加工的觸頭座結構示意圖;
圖2為本發明所採用的坯料結構示意圖;
圖3為本發明觸頭座擠壓模具的具體實施例裝配結構示意圖;
圖4為圖3中定位型芯的固定結構示意圖;
圖5為圖3中的坯料的定位結構示意圖;
圖6為圖3中的擠壓過程使用狀態圖。
具體實施方式
下面結合附圖對本發明的實施方式作進一步說明。
本發明的觸頭座擠壓模具的具體實施例,如圖1至圖6所示,該觸頭座擠壓模具包括可相對導向移動的上模體和下模體,其中上模體包括上模座17、凸模14、凸模固定板15、凸模墊板16,在凸模14和上模座17之間設置凸模墊板16,並將凸模14頂壓在凸模墊板16上,凸模14的上端具有可卡設在凸模固定板15上的外翻沿,上述的凸模墊板16、上模板和凸模固定板15通過沿周面間隔設置的緊鎖螺釘24和銷軸23實現固定。
下模體包括有凹模9、凹模支撐座、預應力圈10、壓套11、定位型芯19和頂料機構,其中凹模9上設置有孔口朝向凸模14的成型孔,該成型孔包括與工件20的凸緣部201徑向尺寸一致的大孔段91及與工件20的直筒部下端部202徑向尺寸一致的小孔段92,且大孔段91和小孔段92的結合處設置有與觸頭座20的外圓角204對應的內圓角,凹模9沿軸線延伸方向插裝有用於定位坯料的定位型芯19,並伸出至凹模9的上端部。坯料的內徑與定位型芯的外徑尺寸一致,坯料的外徑大於小孔段92的孔徑,小於大孔段91的孔徑。
凹模支撐座包括設置在凹模9下側的凹模支撐板7,及設置在凹模支撐板7下側的型芯固定板5和型芯墊板2,定位型芯19固定在凹模固定板內,通過螺釘鎖緊在型芯墊板2上,型芯墊板2和型芯固定板5固定於下模座1上,定位型芯19沿上下方向導向裝配於凹模支撐板7上與凹模9的通孔同軸的導向孔中。
在定位型芯19和凹模支撐板7之間設置有套設於定位型芯19上並延伸至凹模9的成型孔內的頂料環8,該頂料環8的上端面、大孔段91的孔底面、凸模的成型面、大孔段91和小孔段92的孔壁共同構成用於成型所述工件20的型腔。頂料環8與定位型芯19和凹模9均導向移動配合,以此來保證其同軸度,頂料環8的外徑與凹模9的小孔段92內徑尺寸一致,頂料環8的內徑與定位型芯19的外徑尺寸一致。頂料環8的下端部設置有外翻沿,且在凹模支撐板7上設置有供頂料環8導向上下移動的導向孔,且凹模支撐板7的上端設置有用於與頂料環8的外翻沿擋止配合以限制頂料環8的位移尺寸的內翻沿,外翻沿和內翻沿均具有一定的錐度。貫穿於型芯固定板5和型芯墊板2的上下板面設置有用於頂推頂料環8下端面以使頂料環8向上移動的頂杆3,頂杆3有三個,沿圓周方向均勻設置在頂料環8的軸線的外側,且三個頂杆3的下端部設置有用於保證三個頂杆3同步移動的頂板4。
凹模支撐板7座裝於下模座1上,在凹模支撐板7的外側還套設有凹模固定套6,限制凹模在下模座1上的左右移動,在凹模的外周套設有預應力圈10,以減少坯料18擠壓過程中凹模所受的橫向切應力,凹模的外周和預應力圈10的內壁設置有相應的錐度實現凹模與預應力圈的錐面配合,在預應力圈10上壓設有壓套11,該壓套11固定於凹模固定套6上,且能夠將預應力圈10壓在凹模上。
凸模14的下端部開設有供定位型芯19插入的容納孔,該容納孔的孔口外圍形成用於與觸頭座20的上端部203的端面結構一致的成型面,且凸模14的外徑尺寸與凹模的成型孔的尺寸一致,可導向伸入至成型孔內以擠壓坯料18。
在上模座17和下模座1之間設置有可使二者導向上下移動的導向結構,其包括設置在上模座17軸向兩側的的導套13和設置在下模座1軸向兩側的導杆12。
凸模14的容納孔24包括與定位型芯的外徑尺寸一致的小徑段241和設置在小徑段上側大徑段242,大徑段242的側壁上沿徑向開設有與外界相通的第一通氣孔21,第一通氣孔21在定位型芯19插入時可保證容納孔內部的氣壓與外界氣壓一致。
在定位型芯19上設置有第二通氣孔22,第二通氣孔22由定位型芯19的上端面向下延伸至小孔段的底部孔腔位置,而後沿定位型芯19的徑向左右貫通而成T型結構。
使用時,選取套管狀坯料,坯料的外徑小於凹模的大孔段尺寸,坯料的外徑大於凹模的小孔段尺寸,採用溫擠壓工藝,先對擠壓模具進行預熱,預熱後在凸模14、凹模、型芯上均勻塗抹潤滑劑,然後將坯料18加熱至再結晶溫度以下、回復溫度以上,將加熱後的坯料18套設在定位型芯19上,其下端部放置在大孔段91的孔底面上,在液壓機的作用下,導杆12和導套13相對移動,使凸模14向下擠壓坯料18,在擠壓的過程中,坯料受擠壓變形向小孔段92和大孔段91延伸,最後形成觸頭座20,由此完成觸頭座20的一次擠壓成型。
在其他實施例中,凹模可設置在上模體上,此時定位型芯設置在凸模上,並在凹模上開設供定位型芯導向插入的容納孔;凹模的小孔段的孔徑可以設置為與觸頭座的直筒部的上端部的徑向尺寸一致;可將定位型芯設置為具有凸緣結構,且凸緣結構的上端面構成小孔段的孔底面,通過頂杆頂推定位型芯將成型的觸頭座移出模具;頂杆可以為多個,根據實際的需要增加設置;導向孔可不設置限位部,直接將頂料環和頂杆粘接在一起限制頂料環的移動;可直接通過預應力圈固定在凹模支撐板上,不設置凹模固定套和壓套,並將凹模支撐板固定在下模座上;第二通氣孔可設置為L型,保證在擠壓過程中,小孔段內的壓縮空氣能夠排出外部即可。
本發明的擠壓成型方法的具體實施例,與上述觸頭座擠壓模具的使用實施例一致,不再詳細說明。