鋼絲彎折成型機的製作方法
2024-03-29 18:19:05
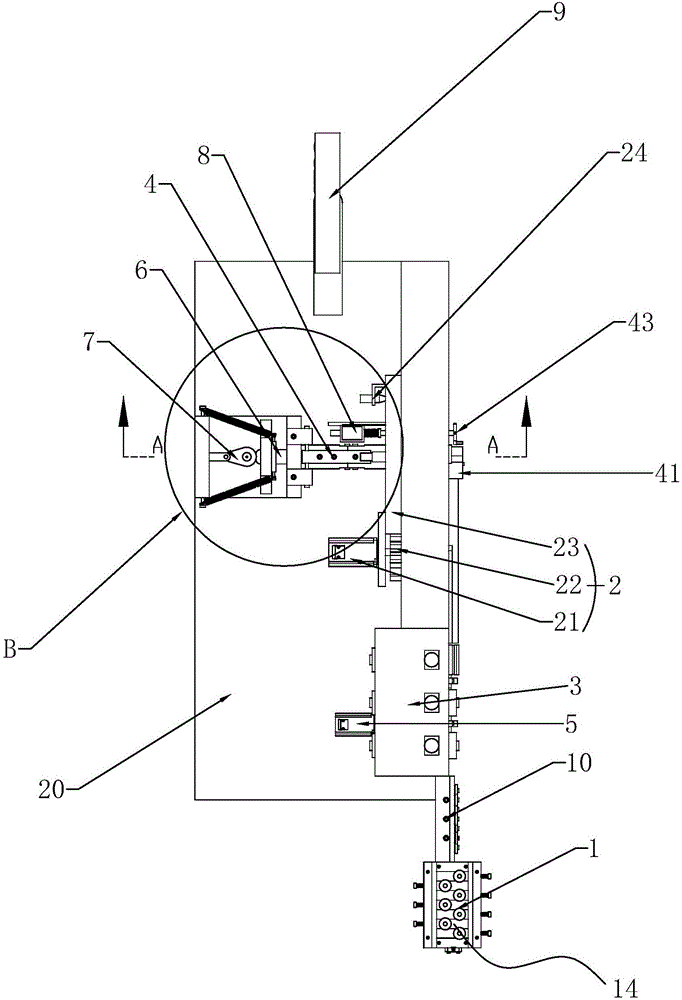
本發明涉及線材彎折加工設備,更具體地說,它涉及一種鋼絲彎折成型機。
背景技術:
鋼絲彎折設備主要用於對如鋼絲、鐵絲等絲狀的線材進行加工或預處理的設備,可將卷繞彎曲的線材進行拉直,同時可將直線狀的線材進行彎折,達到某種預定的彎折效果。
傳統的鋼絲彎折機是將工件模具分成上下兩半,其下半模具固定在工作檯檯面上,上半模具設置在下半模具正上方,進行鋼絲折彎作業時,將待彎折工件放置在下半模具上,然後利用油缸帶動上半模具下降至與下半模具對合,即可將工件彎折成型;公開號為CN202207759U的中國專利公開了一種鋼絲彎折裝置,包括安裝架、與安裝架相轉動設置的轉動軸、固定設置於轉動軸一端部的彎折部、固定設置於轉動軸另一端部的操作裝置、與安裝架相滑動設置的L型牴觸架、將牴觸架與所述的安裝架兩者相鎖定的鎖定機構,牴觸架包括水平設置的壓板、與壓板相固定連接的且垂直設置的牴觸板,壓板位於所述的轉動軸的下方。
在對鋼絲進行彎折時,通過將鋼絲的一端部牴觸在牴觸板上,而後直接轉動操作裝置,且牴觸架與安裝架相滑動地設置,即可完成彎折動作;但是在對鋼絲輸送的過程中不能很好的使鋼絲處於直線的狀態進行輸送,加上相應的設備簡單,無法對鋼絲進行連續的彎折作用,導致無法對鋼絲進行連續的彎折工序,從而影響鋼絲連續彎折的工序,導致生效效率降低。
技術實現要素:
針對現有技術存在的不足,本發明的目的在於提供一種自動進絲、對鋼絲進行連續彎折的鋼絲彎折成型機。
為實現上述目的,本發明提供了如下技術方案:
一種鋼絲彎折成型機,包括設置於機架上鋼絲依次經過的水平預壓裝置、垂直預壓裝置、導絲裝置以及彎折成型裝置,所述導絲裝置連接有用於驅動導絲裝置運轉的驅動組件,所述彎折成型裝置包括與導絲裝置連接的出絲導槽、設置於機架上的工作轉臺、與工作轉臺連接用於將出絲導槽上的鋼絲進行彎折的折彎刀件以及與用於控制折彎刀件朝工作轉臺方向往復運動的電磁組件,所述工作轉臺連接有用於驅動工作轉臺處於機架上往復轉動的動力傳動組件,在所述出絲導槽上連接有用於裁斷鋼絲的剪切裝置,所述剪切裝置連接有用於驅動剪切裝置往復運動的凸輪組件。
如此設置,鋼絲先通過水平預壓裝置對鋼絲水平面上進行預壓處理,使彎曲的狀態的鋼絲處於同一平面上;再通過垂直預壓裝置,對同一面上的鋼絲進行預壓,使鋼絲預壓成直線形式,再通過驅動組件驅動導絲裝置,使導絲裝置對鋼絲進行輸送連續、定向進行傳送的作用;當直線狀態的鋼絲從導絲裝置輸送至折彎成型裝置處進行折彎處理時,通過動力傳動組件使工作轉臺處於機架上轉動,進而使折彎組件相對於出絲導槽發生轉動,從而使出絲導槽出絲口上的鋼絲進行折彎處理,隨後通過電磁組件通電將折彎刀件朝工作轉臺方向運動,即折彎刀件脫離出絲導槽的出絲口,而出絲導槽繼續輸送鋼絲,當鋼絲在出絲導槽的出絲口出絲長度一定時,電磁組件斷電使折彎刀件恢復原狀,再通過動力傳動組件驅動工作轉臺,使折彎刀件相對於出絲導槽轉動,對出絲導槽上的鋼絲進行再次彎折處理,如此轉動,使彎折刀件對鋼絲進行多次,且不同方向上的折彎處理;根據鋼絲所需要彎折的方向,使動力傳動組件驅動工作轉臺轉動的方向,達到對鋼絲不同方向上的彎折;當鋼絲折彎成型後,通過凸輪組件驅動剪切裝置對鋼絲進行裁斷處理,完成鋼絲折彎成型後裁斷的工序;而前部各個裝置繼續配合傳送,對鋼絲進行連續折彎成型處理工序,根據鋼絲所要折彎的角度及不同方向的折彎處理,通過動力傳送組件驅動工作轉臺處於機架上轉動的弧度,即可自動生成不同形狀及角度的產品;使鋼絲在輸送能較好的使鋼絲處於直線的狀態進行連續輸送,可對鋼絲進行連續且不同角度上的彎折加工處理,進而鋼絲連續彎折的工序,極大的提高產品成型的生效效率。
進一步設置:所述電磁組件包括設置於工作轉臺一端面上的安裝殼體、與安裝殼體連接的電磁鐵一、一端與電磁鐵一相配合且與安裝殼體滑動連接的電磁鐵二以及套接於電磁鐵二上的回位彈簧,所述回位彈簧兩端分別與電磁鐵二和安裝殼體牴觸連接,所述電磁鐵二的另一端通過設置於折彎刀件上的折彎軸與工作轉臺另一端面上的折彎刀件連接,所述折彎軸貫穿工作轉臺且通過回位彈簧的壓縮回位處於工作轉臺上與工作轉臺往復滑動連接。
如此設置,當對固定安裝殼體上的電磁鐵一進行通電時,使與安裝殼體滑動連接的電磁鐵二朝電磁鐵一方向運動,進而帶動折彎刀件處於工作轉臺上運動,使折彎刀件脫離出絲導槽的出絲口,便於出絲導槽對鋼絲進行連續輸送;此時,回位彈簧處於壓縮狀態,當電磁鐵一斷電時,電磁鐵一對於電磁鐵而的磁性消失,在回位彈簧的作用下,使電磁鐵二自動回位,折彎刀件繼續對出絲導槽上的鋼絲進行折彎處理。
進一步設置:所述剪切裝置包括設置於機架上的安裝座、與安裝座固定連接且穿設工作轉臺的軸芯以及設置於軸芯內與軸芯滑動的切刀軸,所述切刀軸貫穿軸芯且通過凸輪組件連接,所述軸芯與出絲導槽連接,且在所述出絲導槽的出絲口上設置有用於切刀軸進行切割的凹槽口。
如此設置,安裝座對軸芯起到一個支撐固定的作用,再通過凸輪組件驅動切刀軸,使切刀軸處於軸芯內與軸芯滑動,通過將軸芯與出絲導槽連接,可對鋼絲起到一個固定出絲的埠,再通過將切刀軸處於出絲導槽上的凹槽口上進行滑動裁斷鋼絲的作用,可提高裁斷時切刀軸的穩定性能。
進一步設置:所述凸輪組件包括與安裝座連接的轉動電機、與轉動電機連接的凸輪、與安裝座固定連接用於導向切刀軸運動的固定座以及設置於切刀軸與安裝座之間的回位元件,所述凸輪的凸起部與切刀軸牴觸連接。
如此設置,傳動電機通過驅動凸輪轉動,當凸輪的凸起與切刀軸牴觸時,切刀軸處於出絲導槽的凹槽口上滑動,對鋼絲進行裁斷處理,此時回位元件處於拉伸狀態,當裁斷後,凸輪的凸起慢慢脫離切刀軸,回位元件回位收縮,進而帶動切刀軸回位,完成一次切割工序。
進一步設置:所述動力傳動組件包括與機架固定連接的伺服電機、與伺服電機連接且與機架轉動連接的主齒輪以及與工作轉臺連接的副齒輪,在所述機架上設置有用於感應副齒輪轉動弧度的感應組件,所述感應組件與伺服電機連接。
如此設置,通過伺服電機可將感應組件傳遞過來的信號轉化為驅動信號,使主齒輪達到正反轉的作用,進而使副齒輪連接的工作轉盤達到正反轉的目的,使出絲導槽上的鋼絲通過折彎刀件實現不同角度的折彎效果。
進一步設置:所述感應組件包括設置於副齒輪上的感應塊、設置於機架上用於感應感應塊的光電感應器一和光電感應器三、以及設置於光電感應器一和光電感應器三之間用於控制副齒輪復位的光電傳感器二,所述光電傳感器二與機架連接,所述光電感應器一、光電感應器二以及光電傳感器三均與伺服電機電信號連接。
如此設置,通過各個光電傳感器,使伺服電機帶動主齒輪使副齒輪連接的工作轉臺進行轉動,光電感應器一和光電感應器三主要起限位作用,即控制副齒輪轉動的弧度範圍,使鋼絲達到的折彎角度,而光電傳感器二主要起到復位作用,使伺服電機結束運轉時,通過主齒輪將副齒輪連接的工作轉臺處於初始位置,起到撫慰的作用,方便計量下次轉彎時的折彎效果。
進一步設置:所述導絲裝置包括與機架連接的主動輥輪和從動輥輪、與機架固定連接的導絲槽座、設置於導絲槽座上用於導絲的進線軸,在所述主動輥輪和從動輥輪上均設置有輪軌,在所述輪軌上均設置有環形槽,兩所述輪軌平行布置且兩所述環形槽形成供鋼絲傳送的通槽,所述通槽與進線軸上的軸孔處於同一直線布置,所述出絲導槽與導絲槽座連接,且導絲槽座的出絲口與通槽相通連接,所述主動輪與驅動組件連接。
如此設置,通過驅動組件驅動主動棍輪轉動,使從動棍輪進行轉動,同時在主動輥輪和從動輥輪上均設置有輪軌,以及在輪軌上均設置有環形槽,使兩輪軌上的環形槽形成供鋼絲傳送的通槽,將通槽與進線軸上的軸孔處於同一直線布置,使鋼絲處於直線狀態進行導向傳送的作用,使鋼絲從出絲導槽的出口端出來時,均處於直線狀態,再通過折彎刀件進行折彎工序,提高導絲裝置對鋼絲的輸送以及預壓性能。
進一步設置:所述驅動組件包括與機架連接的驅動電機、與驅動電機連接的主動齒輪、與主動輥輪連接且與主動齒輪相嚙合的第一從動齒輪以及與從動輥輪連接與第一從動齒輪相嚙合的第二從動齒輪。
如此設置,通過驅動電機帶動主動齒輪轉動,使第一從動齒輪轉動,即主動輥輪發生運轉,同時第一從動齒輪與第二齒輪嚙合,使第二從動齒輪發生運動,且第一從動齒輪與第二齒輪嚙合轉動方向相反,使鋼絲從第一從動齒輪與第二齒輪之間輸送的作用。
進一步設置:所述垂直預壓裝置包括與機架連接的水平安裝板、成排狀設置的預壓輥輪一和成排狀設置的預壓輥輪二,所述預壓輥輪一和預壓輥輪二上下平行設置於水平安裝板上且均與水平安裝板轉動連接,所述預壓輥輪一和預壓輥輪二的滾動面之間形成用於對鋼絲預壓的預壓通道,所述預壓通道與通槽處於同一直線布置。
如此設置,通過在水平安裝板上設置排狀且與相對轉動的預壓輥輪一和預壓輥輪二,且兩者之間形成供鋼絲預壓以及輸送的預壓通槽,通過預壓輥輪一和預壓輥輪二使鋼絲在垂直的方向是鋼絲處於同一平面上,再通過水平預壓裝置對鋼絲進行預壓,使鋼絲形成直線狀態,且進行連續預壓輸送的效果,使鋼絲在折彎之前姓黃岑更良好的形態,提高鋼絲折彎的產品質量。
進一步設置:在所述水平安裝板上設置有與水平安裝板滑動連接的滑塊,在所述滑塊的一末端與水平安裝板之間均設置有壓縮彈簧,所述壓縮彈簧兩端分別與滑塊和水平安裝板的內壁牴觸連接,在所述水平安裝板上設置有與水平安裝板螺紋轉動連接的牴觸螺栓,所述牴觸螺栓穿設水平安裝板的內壁與滑塊的另一末端牴觸連接,若干所述滑塊成排狀設置於水平安裝板上,所述預壓輥輪一和預壓輥輪二均獨立與單個滑塊轉動連接,且預壓輥輪一和預壓輥輪二處於排狀的滑塊上間隔布置。
如此設置,滑塊的一端與牴觸螺栓相牴觸,通過轉動水平安裝板一端上的牴觸螺栓,使滑塊處於水平安裝板內滑動,另一端上壓縮彈簧由於滑塊的擠壓再次被壓縮,使滑塊上的預壓輥輪一和預壓輥輪二相對於水平安裝板上的相對位置關係改變,使預壓輥輪一和預壓輥輪二形成的預壓通道的徑口大小改變,以適用不同直徑的鋼絲;通過對每個預壓輥與單個滑動連接,使預壓輥能單獨進行調節,通過上下兩排預壓輥可先對鋼絲進行預壓成一個平面,再預壓成同一直線上的目的。
通過採用上述技術方案,本發明相對現有技術相比:通過鋼絲先輸送至水平預壓裝置對鋼絲水平面上進行預壓處理,使彎曲的狀態的鋼絲處於同一平面上;再通過垂直預壓裝置,對同一面上的鋼絲進行預壓,使鋼絲預壓成直線形式,再通過驅動組件驅動導絲裝置,使導絲裝置對鋼絲進行連續輸送、定向進行傳送的作用;當直線狀態的鋼絲從導絲裝置輸送至折彎成型裝置處進行折彎處理時,通過動力傳動組件使工作轉臺處於機架上轉動,進而使折彎組件相對於出絲導槽發生轉動,從而使出絲導槽出絲口上的鋼絲進行折彎處理,隨後通過電磁組件通電將折彎刀件朝工作轉臺方向運動,即折彎刀件脫離出絲導槽的出絲口,而出絲導槽繼續輸送鋼絲,當鋼絲在出絲導槽的出絲口出絲長度一定時,電磁組件斷電使折彎刀件恢復原狀,再通過動力傳動組件驅動工作轉臺,使折彎刀件相對於出絲導槽轉動,對出絲導槽上的鋼絲進行再次彎折處理,如此轉動,使彎折刀件對鋼絲進行多次,且不同方向上的折彎處理;根據鋼絲所需要彎折的方向,使動力傳動組件驅動工作轉臺轉動的方向,達到對鋼絲不同方向上的彎折;當鋼絲折彎成型後,通過凸輪組件驅動剪切裝置對鋼絲進行裁斷處理,完成鋼絲折彎成型後裁斷的工序;而前部各個裝置繼續配合傳送,對鋼絲進行連續折彎成型處理工序,當彎折成型工序完畢後,感應組件促使動力傳動組件復位,工作轉臺恢復原始位置,凸輪同時處於原始位置,便於下次折彎成型工序;根據鋼絲所要折彎的角度及不同方向的折彎處理,通過動力傳送組件驅動工作轉臺處於機架上轉動的弧度,即可自動生成不同形狀及角度的產品;使鋼絲在輸送能較好的使鋼絲處於直線的狀態進行連續輸送,可對鋼絲進行連續且不同角度上的彎折加工處理,進而鋼絲連續彎折的工序,極大的提高產品成型的生效效率。
附圖說明
圖1為鋼絲彎折成型機的俯視圖;
圖2為圖1中B處的放大圖;
圖3為圖1中A-A出的剖視圖;
圖4為鋼絲彎折成型機中安裝座方向上的結構示意圖;
圖5為鋼絲彎折成型機中工作轉臺方向上的結構示意圖;
圖6為圖5中C處的放大圖;
圖7為鋼絲彎折成型機的導絲裝置處的局部剖視圖;
圖8為圖7中D處的放大圖;
圖9為電氣控制裝置與感應組件之間的電路控制圖。
圖中:1、水平預壓裝置;11、水平安裝板;12、預壓輥輪一;121、環形凹陷;13、預壓輥輪二;14、預壓通道;15、滑塊;16、壓縮彈簧;17、牴觸螺栓;18、入絲板;181、入絲孔;2、動力傳動組件;21、伺服電機;22、主齒輪;23、副齒輪;24、感應組件;241、感應塊;242、光電感應器一;243、光電感應器二;244、光電傳感器三;3、導絲裝置;31、主動輥輪;32、從動輥輪;33、導絲槽座;34、進線軸;341、軸孔;35、輪軌;36、環形槽;37、通槽;4、彎折成型裝置;41、出絲導槽;411、凹槽口;42、工作轉臺;43、折彎刀件;431、圓弧;44、折彎軸;5、驅動組件;51、驅動電機;52、主動齒輪;53、第一從動齒輪;54、第二從動齒輪;6、剪切裝置;61、安裝座;62、軸芯;63、切刀軸;7、凸輪組件;71、轉動電機;72、凸輪;73、固定座;74、回位元件;75、第一限位塊;76、第二限位塊;77、感應器;78、彈簧銷軸;8、電磁組件;81、安裝殼體;82、電磁鐵一;83、電磁鐵二;84、回位彈簧;85、絕緣套;9、電氣控制裝置;10、垂直預壓裝置;20、機架。
具體實施方式
參照圖1至圖9對鋼絲彎折成型機做進一步說明。
一種鋼絲彎折成型機,如圖1所示,包括設置於機架20上鋼絲依次經過用於對鋼絲左右水平平面上進行預處理壓直的水平預壓裝置1、用於對鋼絲上下垂直平面上進行預處理壓直的垂直預壓裝置10、用於將預壓在處理的鋼絲進行直線輸送的導絲裝置3、用於對鋼絲進行彎折加工處理的彎折成型裝置4,用於驅動導絲裝置3運轉的驅動組件5、用於裁斷鋼絲的剪切裝置6以及用於驅動剪切裝置6往復運動的凸輪組件7;在機架20上還設置有用於控制驅動組件5、動力傳動組件2以及凸輪組件7運轉的電氣控制裝置9。
其中,如圖7和圖8所示,水平預壓裝置1包括與機架20連接且呈凹形設置的水平安裝板11、設置於水平安裝板11的凹槽內與水平安裝板11連接的滑塊15、成排狀設置的預壓輥輪一12和成排狀設置的預壓輥輪二13;若干滑塊15成排狀設置於水平安裝板11上,且首位兩末端的滑塊15與水平安裝板11固定連接;預壓輥輪一12和預壓輥輪二13均獨立與單個滑塊15轉動連接,預壓輥輪二13設置於相鄰兩預壓輥輪一12中點的軸向上;同理,預壓輥輪一12設置於相鄰兩預壓輥輪二13中點的軸向上,且預壓輥輪一12和預壓輥輪二13處於排狀的滑塊15上間隔布置,即預壓輥輪一12和預壓輥輪二13呈M形布置於水平安裝板11上。
如圖7和圖8所示,在預壓輥輪一12和預壓輥輪二13的圓周滾動面上均設置有環形凹陷121,使預壓輥輪一12和預壓輥輪二13的環形凹陷121之間形成用於對鋼絲預壓的預壓通道14,在水平安裝板11上設置有入絲板18,入絲板18上設置有與預壓通道14處於同一直線上的入絲孔181,使鋼絲處於該預壓通道14上進行鋼絲水平面上的預壓及傳送的作用。
如圖7和圖8所示,滑塊15處於水平安裝板11的凹槽內沿鋼絲輸送的垂直方向上與水平安裝板11滑動連接;在滑塊15的一末端與水平安裝板11之間均設置有壓縮彈簧16,壓縮彈簧16兩端分別與滑塊15和水平安裝板11上凹槽的其中一內壁牴觸連接,同時在水平安裝板11上設置有與水平安裝板11螺紋轉動連接的牴觸螺栓17,牴觸螺栓17穿設水平安裝板11上凹槽的另一內壁且與滑塊15的另一末端牴觸連接;通過轉動水平安裝板11上的牴觸螺栓17,使另一端壓縮彈簧16壓縮或回位,促使滑動處於水平安裝板11內滑動,達到調節預壓輥輪一12和預壓輥輪二13之間形成的預壓通道14的徑口大小的目的。
如圖7所示,垂直預壓裝置10與水平預壓裝置1採用相同的配置,垂直預壓裝置10與水平預壓裝置1垂直布置,即兩裝置中的安裝板垂直設置;同時垂直預壓裝置10上的兩排預壓輥輪之間形成的垂直預壓通道14與預壓通道14處於同一直線上,達到對鋼絲預壓處理以及直線輸送的作用;垂直預壓裝置10與水平預壓裝置1可連續設置多組。
如圖7所示,導絲裝置3包括均與機架20轉動連接的主動輥輪31和從動輥輪32、與機架20固定連接的導絲槽座33、設置於導絲槽座33上用於導絲的進線軸34;在主動輥輪31和從動輥輪32上均設置有輪軌35,在輪軌35上均設置有環形槽36,兩輪軌35處於同一平面上平行布置且兩環形槽36形成供鋼絲傳送的通槽37,通槽37與進線軸34上的軸孔341處於同一直線布置;主動輥輪31和從動輥輪32可設置多組,且多個主動輥輪31處於同一直線上設置。
如圖8所示,驅動組件5包括與機架20連接的驅動電機51、與驅動電機51連接的主動齒輪52、與主動輥輪31連接且與主動齒輪52相嚙合的第一從動齒輪53以及與從動輥輪32連接與第一從動齒輪53相嚙合的第二從動齒輪54;通過主動齒輪52帶動第一從動齒輪53以及第二從動齒輪54轉動,使主動輥輪31與從動輥輪32的轉動方向相反,達到輸送鋼絲的作用。
如圖6所示,彎折成型裝置4包括與導絲裝置3連接的出絲導槽41、設置於機架20上的工作轉臺42、與工作轉臺42連接用於將出絲導槽41上的鋼絲進行彎折的折彎刀件43以及與用於控制折彎刀件43朝工作轉臺42方向往復運動的電磁組件8;出絲導槽41的出絲口與折彎刀件43均成圓弧431設置,出絲導槽41與導絲槽座33的末端連接,且導絲槽座33的出絲口與進線軸34相通連接,即預壓通道14、通槽37以及進線軸34上的軸孔341處於同一直線上。
如圖4和圖5所示,工作轉臺42連接有用於驅動工作轉臺42處於機架20上往復轉動的動力傳動組件2;動力傳動組件2包括與機架20固定連接的伺服電機21、與伺服電機21連接且相對於機架20轉動連接的主齒輪22以及與工作轉臺42固定連接的副齒輪23;通過主動齒輪52進而帶動與副齒輪23固定連接的工作轉臺42處於機架20上轉動。
如圖1和圖4所示,在機架20上設置有用於感應副齒輪23轉動弧度的感應組件24;感應組件24包括設置於副齒輪23上的感應塊241、設置於機架20上用於感應感應塊241的光電感應器一242和光電感應器二243、以及設置於光電感應器一242和光電感應器二243之間用於控制副齒輪23復位的光電傳感器三244;光電傳感器三244與機架20連接,光電感應器一242、光電感應器二243以及光電傳感器三244均與伺服電機21電信號連接;感應塊241初始狀態處於光電傳感器三244位置,副齒輪23開始轉動,當感應塊241與光電感應器一242相對應時,副齒輪23反向轉動,當光電感應器與光電感應器二243相對應時,副齒輪23再次反轉,使副齒輪23如此往復運轉,即副齒輪23轉動的圓弧距離為工作轉臺42處於機架20上轉動的弧度範圍。
如圖2和圖3所示,剪切裝置6包括設置於機架20上的安裝座61、與安裝座61固定連接且穿設工作轉臺42的軸芯62以及設置於軸芯62內與軸芯62滑動的切刀軸63;軸芯62設置於工作轉臺42的軸心線上且相對於工作轉臺42轉動連接,切刀軸63貫穿軸芯62且與凸輪組件7連接;切刀軸63的一端與出絲導槽41通過螺栓固定連接,且在出絲導槽41的出絲口上設置有用於切刀軸63進行切割的凹槽口411,切刀軸63另一端通過與凸輪組件7連接,使切刀軸63處於出絲導槽41的出槽口處與出絲導槽41往復滑動連接。
如圖2所示,凸輪組件7包括與安裝座61連接的轉動電機71、與電機連接的凸輪72、與安裝座61固定連接用於導向切刀軸63運動的固定座73以及設置於切刀軸63與安裝座61之間且初始狀態為拉伸狀態的回位元件74;回位元件74為回位彈簧84,且通過設置於切刀軸63末端的彈簧銷軸78與切刀軸63連接,另一端通過螺栓與安裝座61固定連接;切刀軸63通過回位元件74的回位作用使切刀軸63的末端與凸輪72牴觸連接,且通過與凸輪72的凸起部牴觸與脫離,促使切刀軸63處於軸芯62內與軸芯62往復滑動連接,實現折彎刀件43相對於工作轉臺42的朝工作轉臺42方向往復運動。
如圖2所示,在軸芯62上設置有用於限位軸芯62處於工作轉臺42上發生相對轉動的第一限位塊75,第一限位塊75通過螺栓與軸心固定連接;兩第一限位塊75對稱設置於軸芯62的圓周面上,且在安裝座61上設置有與第一限位塊75相卡接的第二限位塊76,兩第二限位塊76平行布置且與第一限位塊75垂直布置,使軸芯62通過第一限位塊75處於兩第二限位塊76之間做固定的往復運動。
如圖2所示,同時在安裝座61上設置有用於檢測凸輪72是否處於初始狀態的感應器77,感應器77可為光電傳感器,促使凸輪72停止轉動後處於初始狀態且在回位元件74的作用下與切刀軸63牴觸連接。
如圖2和圖3所示,電磁組件8包括設置於副齒輪23上的安裝殼體81、與安裝殼體81連接的電磁鐵一82、一端與電磁鐵一82相配合且與安裝殼體81滑動連接的電磁鐵二83以及套接於電磁鐵二83上初始狀態為自然狀態的回位彈簧84;回位彈簧84兩端分別與電磁鐵二83和安裝殼體81牴觸連接,電磁鐵二83的另一端通過設置於折彎刀件43上的折彎軸44貫穿工作轉臺42與工作轉臺42另一端面上折彎刀件43連接;通過對電磁鐵一82通電,使電磁鐵二83往電磁鐵一82方向滑動,回位彈簧84壓縮,即折彎刀件43朝工作轉臺42方向運動,使折彎刀件43脫離出絲導槽41的出口端,當電磁鐵一82斷電後,通過回位彈簧84的自動回位,使折彎軸44處於工作轉臺42上與工作轉臺滑動,折彎刀件43自動回位;同時在電磁鐵一82和電磁鐵二83上套設有絕緣套85,便於使電磁鐵一82和電磁鐵二83更好的進行切換作用。
工作原理:如圖1、圖4和圖9所示,鋼絲先輸送至水平預壓裝置1上對鋼絲水平面上進行預壓處理,通過相應的預壓輥使彎曲的狀態的鋼絲處於同一平面上;再通過垂直預壓裝置10,對同一面上的鋼絲進行預壓,使鋼絲預壓成直線形式,再通過驅動組件5驅動導絲裝置3,使導絲裝置3對鋼絲進行連續輸送、定向進行傳送的作用;當直線狀態的鋼絲從導絲裝置3輸送至折彎成型裝置處進行折彎處理時,電氣控制裝置9通過光電感應器二243初始位置的感應的延遲信號控制動力傳動組件2正轉,使工作轉臺42處於機架20上轉動,折彎刀件43相對於出絲導槽41發生轉動,從而對出絲導槽41出絲口上的鋼絲進行折彎處理;感應塊241與光電感應器三242對應時,單次彎折後電氣控制裝置9通過控制電磁組件8通電將折彎刀件43朝工作轉臺42方向運動,即折彎刀件43脫離出絲導槽41的出絲口,出絲導槽41繼續輸送鋼絲,當鋼絲在出絲導槽41的出絲口出絲長度一定時,電磁組件8斷電使折彎刀件43恢復原狀,電氣控制裝置9通過光電感應器三244感應的延遲信號控制動力傳動組件2驅動工作轉臺42反轉,使折彎刀件43相對於出絲導槽41轉動,對出絲導槽41上的鋼絲進行再次彎折處理,感應塊241與光電感應器一242對應時,電氣控制裝置9通過光電感應器一242感應的延遲信號控制動力傳動組件2停止對工作轉臺42反轉,鋼絲反向單次彎折結束,同時電氣控制裝置9通過控制電磁組件8通電將折彎刀件43朝工作轉臺42方向運動,即折彎刀件43脫離出絲導槽41的出絲口,出絲導槽41繼續輸送鋼絲,當鋼絲在出絲導槽41的出絲口出絲長度一定時,電磁組件8斷電使折彎刀件43恢復原狀,電氣控制裝置9通過光電感應器一242感應的延遲信號控制動力傳動組件2驅動工作轉臺42正轉,進行再次彎折處理;如此轉動,使彎折刀件對鋼絲進行多次,且不同方向上的折彎處理;根據鋼絲所需要彎折的方向,通過電氣控制裝置9相應的控制程序控制電磁裝置以及動力傳動組件2的運轉,使動力傳動組件2驅動工作轉臺42轉動的方向,達到對鋼絲不同方向上的彎折;當鋼絲折彎成型後,電氣控制裝置9通過控制凸輪組件7驅動剪切裝置6對鋼絲進行裁斷處理,完成鋼絲折彎成型後裁斷的工序;而前部各個裝置繼續對鋼絲進行預處理以及傳送,通過電氣控制裝置9控制各個部件對鋼絲進行連續折彎成型以及裁斷處理工序,達到自動生產的目的;當彎折成型工序完畢後,感應組件24將信號傳遞給電氣控制裝置9,再通過控制動力傳動組件2使相應的齒輪復位,工作轉臺42恢復原始位置,同時凸輪72也同時處於原始位置,便於下次折彎成型工序;根據鋼絲所要折彎的角度及不同方向的折彎處理,通過電氣控制裝置9設置相應的控制程序,通過控制動力傳送組件驅動工作轉臺42處於機架20上轉動的弧度,即可自動生成不同形狀及角度的產品;使鋼絲在輸送能較好的使鋼絲處於直線的狀態進行連續輸送,可對鋼絲進行連續且不同角度上的自動彎折加工處理,進而達到鋼絲連續彎折的工序,極大的提高產品成型的生效效率。
以上所述僅是本發明的優選實施方式,本發明的保護範圍並不僅局限於上述實施例,凡屬於本發明思路下的技術方案均屬於本發明的保護範圍。應當指出,對於本技術領域的普通技術人員來說,在不脫離本發明原理前提下的若干改進和潤飾,這些改進和潤飾也應視為本發明的保護範圍。