一種氣體絕緣式衝擊電壓發生裝置的製作方法
2024-03-07 09:02:15
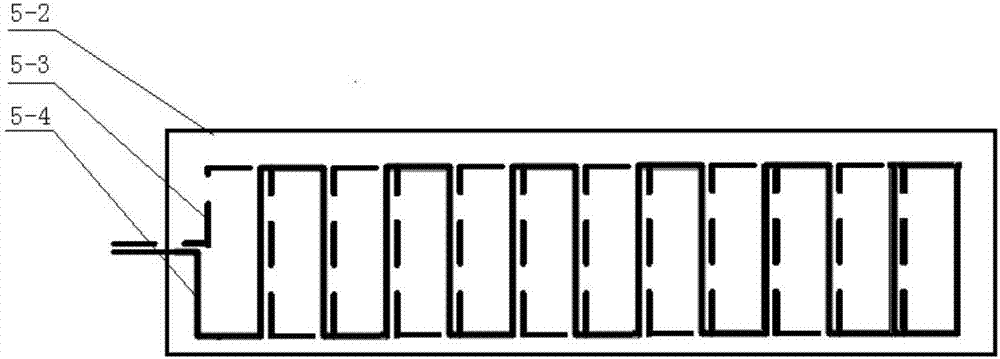
本發明屬於高壓發生裝置技術領域,具體涉及一種氣體絕緣式衝擊電壓發生裝置。
背景技術:
氣體絕緣全封閉組合電器(gas-insulatedmetal-enclosedswitchgear,gis)設備由於結構緊湊、安全性高,在電網的應用日趨廣泛,特別是自2009年1000千伏「晉東南-南陽-荊門」特高壓交流試驗示範工程一期工程的投運後,特高壓gis在我國電力系統的裝用量也穩步增長。
國際大電網組織(cigre)的研究及統計結果表明,雷電衝擊電壓對固定在高壓導體上突出物、絕緣子上微粒類缺陷的反映比交流電壓更為靈敏,因為交流電壓對於某些裝配缺陷、電極表面劃傷類缺陷的檢驗效果不佳,而雷電衝擊和操作衝擊電壓對於上述缺陷有更好的檢驗效果。
然而,由於傳統衝擊電壓發生裝置固有電感量大,從而無法滿足大容量特高壓gis設備衝擊試驗所需的波前時間要求,且傳統衝擊電壓發生裝置具有體積龐大、安裝複雜、試驗中無法移動等不足。因此特高壓gis現場交接試驗階段一般不開展衝擊耐受試驗,進而導致設備運輸、安裝階段產生的部分缺陷無法及時發現,易引起特高壓gis投運後發生絕緣擊穿故障。
技術實現要素:
針對上述問題,本發明提出一種氣體絕緣式衝擊電壓發生裝置,將傳統衝擊電壓發生器集體封裝於sf6氣體中,並在結構優化、部件選型方面進行了革新,具有結構緊湊、自感量低、可移動等特點,可實現在變電站現場開展大容量gis設備標準雷電衝擊耐壓試驗,並可在不同試驗場地間實現自移動。
實現上述技術目的,達到上述技術效果,本發明通過以下技術方案實現:
一種氣體絕緣式衝擊電壓發生裝置,包括衝擊電壓發生器本體、電容分壓器、波尾電阻、波前電阻、充電變壓器;所述衝擊電壓發生器本體與波尾電阻相連;所述波前電阻的一端與衝擊電壓發生器本體相連,另一端與電容分壓器相連;所述充電變壓器與衝擊電壓發生器本體相連,所述衝擊電壓發生器本體包括絕緣外殼和衝擊電壓發生器,所述絕緣外殼內充有設定壓力的絕緣氣體,所述衝擊電壓發生器本體設於絕緣外殼內,其包括多個放電單元,各放電單元沿著絕緣外殼的長度方向順次排列,相鄰放電單元之間通過放電間隙連接。
進一步地,所述放電間隙為氣體火花開關,且相鄰放電單元之間通過絕緣隔板分隔。
進一步地,所述波前電阻包括絕緣基板,所述絕緣基板的正面和反面均設有電阻絲,位於絕緣基板正面和反面的電阻絲互為反向繞制,以使得二者電感方向相反。
進一步地,所述絕緣基板由軟質絕緣材料製成,所述絕緣基板正面和反面的電阻絲均採用軟質材料固定在絕緣基板上。
進一步地,所述絕緣基板正面和/或反面的電阻絲上均設有若干個抽頭。
進一步地,所述衝擊電壓發生器本體、電容分壓器、波尾電阻均為模塊式結構,其中,衝擊電壓發生器本體的絕緣外殼分為上、下兩部分,所述電容分壓器包括1個或者多個分立的電容器,當電容分壓器包括多個分立的電容器時,各電容器之間串聯;所述波尾電阻包括1個或者多個分立的電阻器,當波尾電阻包括多個分立的電阻器時,各電阻器之間串聯。
進一步地,所述的一種氣體絕緣式衝擊電壓發生裝置,還包括測控設備,所述測控設備分別與衝擊電壓發生器本體、電容分壓器、波尾電阻、波前電阻、充電變壓器相連。
進一步地,所述電容分壓器、波尾電阻、波前電阻、充電變壓器和測控設備的底部均設有可鎖死的移動滾輪;所述衝擊電壓發生器本體的底部設有行動裝置,以帶動衝擊電壓發生器本體移動。
進一步地,所述充電變壓器的充電電纜連接處設有自動接地裝置,所述自動接地裝置與接地體相連,其為一自動旋轉式的金屬杆,試驗過程中處於平放狀態,試驗結束後,金屬杆自動豎起並觸碰充電變壓器輸出端,以實現高壓放電。
進一步地,所述絕緣氣體為sf6或者氮氣。
本發明的有益效果:
(1)本發明的衝擊電壓發生器本體的絕緣外殼內充設絕緣氣體的方式來實現絕緣,絕緣外殼內部的衝擊電壓發生器採用垂直緊湊型布置、並使用氣體火花開關作為放電間隙,與傳統技術中採用空氣式絕緣的衝擊壓電發生器單元相比,衝擊電壓發生器本體的整體尺寸大幅降低,從而顯著降低了本發明的氣體絕緣式衝擊電壓發生裝置自身電感量,輸出電壓波前時間計算公式為:其中,tf為波前時間;l為迴路電感;ci為發生器主電容;ct為負載電容,可知,降低電感量能夠顯著降低本發明的氣體絕緣式衝擊電壓發生裝置輸出電壓波前時間。
(2)本發明中的衝擊電壓發生器本體、波尾電阻、電容分壓器均採用模塊式結構,現場安裝時僅需將各分離的器件進行對接,現場安裝工作量大幅降低,且由於衝擊電壓發生器本體的內部結構無需現場組裝,從而能夠顯著提升整體可靠性。
(3)本發明中的衝擊電壓發生器的底部裝設有行動裝置(優選移動履帶車),波尾電阻、電容分壓器、充電變壓器、測控平臺的底部均裝設有帶有制動的移動滑輪,現場試驗中,可在免拆卸情況下實現裝置的移動、轉場,無需重複拆裝,試驗效率大幅提升。
(4)本發明中的波前電阻繞制於軟質絕緣材料上(優選為尼龍布),採用正反兩面交錯繞制,以降低本發明的氣體絕緣式衝擊電壓發生裝置的自感量,縮短輸出電壓波前時間;且電阻絲中間有若干抽頭,能夠便於調節波前電阻阻值,有利於提高試驗中波形調節效率。
附圖說明
圖1為本發明一種實施例的結構示意圖;
圖2為本發明一種實施例的波前電阻的結構示意圖。
具體實施方式
為了使本發明的目的、技術方案及優點更加清楚明白,以下結合實施例,對本發明進行進一步詳細說明。應當理解,此處所描述的具體實施例僅僅用以解釋本發明,並不用於限定本發明。
下面結合附圖對本發明的應用原理作詳細的描述。
實施例1
由於傳統衝擊電壓發生裝置固有電感量大,從而無法滿足大容量特高壓gis設備衝擊試驗所需的波前時間要求,如圖1所示,本發明實施例提供了一種氣體絕緣式衝擊電壓發生裝置,其衝擊電壓發生器本體的絕緣外殼內充設絕緣氣體的方式來實現絕緣,絕緣外殼內部的衝擊電壓發生器採用垂直緊湊型布置、並使用氣體火花開關作為放電間隙,其整體尺寸大幅降低,從而顯著降低了裝置自身電感量,並顯著降低輸出電壓波前時間。
具體地:所述一種氣體絕緣式衝擊電壓發生裝置,包括衝擊電壓發生器本體1、電容分壓器3、波尾電阻4、波前電阻5和充電變壓器6;所述衝擊電壓發生器本體1與波尾電阻4相連;所述波前電阻5的一端與衝擊電壓發生器本體1相連,另一端與電容分壓器3相連;所述充電變壓器6與衝擊電壓發生器本體1相連,用於向衝擊電壓發生器本體1提供正極性或負極性的充電電流;所述衝擊電壓發生器本體1包括絕緣外殼1-2和衝擊電壓發生器1-1,所述絕緣外殼1-2優選為環氧樹脂絕緣筒,其內部充有設定壓力的絕緣氣體,所述絕緣氣體為sf6或者氮氣,優選sf6;所述衝擊電壓發生器1-1設於絕緣外殼1-2內,優選為marx衝擊電壓發生器,其包括多個放電單元1-3,各放電單元1-3沿著絕緣外殼1-2的長度方向順次排列,且相鄰放電單元之間採用絕緣隔板分隔,如圖1中所示,各放電單元1-3為垂直緊湊型布置,即:各放電單元1-3採用堆積木形式一級一級堆疊起來,中間用螺栓固定,相鄰放電單元1-3之間通過放電間隙1-4連接,放電間隙1-4優選為氣體火花開關。
上述方案中,衝擊電壓發生器中的各放電單元1-3採用垂直緊湊型布置,絕緣外殼1-2內充有絕緣氣體,並使用氣體火花開關作為放電間隙1-4,相較於傳統的採用空氣絕緣式的衝擊電壓發生器,絕緣氣體相比於空氣其絕緣性能更好,因此相同電壓下所需的絕緣距離大幅減小,因而可以降低衝擊電壓發生器本體1體積,且傳統的採用空氣絕緣式的衝擊電壓發生器的各級放電單元1-3採用分立元件堆疊放置,放電間隙1-4由兩個半球體組成,因此,其尺寸較本發明中的衝擊電壓發生器本體1可大50%以上。
綜上:本發明的衝擊電壓發生器本體1的尺寸相較於傳統的採用空氣絕緣式的衝擊電壓發生器大幅降低,由於衝擊電壓發生器的自身電感量與其尺寸成正比,因此使得自身電感量顯著降低。
所述充電變壓器6的充電電纜連接處設有自動接地裝置6-1,所述自動接地裝置6-1與接地體相連,其為一自動旋轉式的金屬杆,試驗過程中處於平放狀態,試驗結束後,金屬杆自動豎起並觸碰充電變壓器6輸出端,以實現高壓放電。
所述的一種氣體絕緣式衝擊電壓發生裝置,還包括測控設備,所述測控平臺7優選整體布置於貨櫃內,所述測控設備分別與衝擊電壓發生器本體1、電容分壓器3、波尾電阻4、波前電阻5、充電變壓器6相連。
實施例2
如圖2所示,為了進一步降低本發明的氣體絕緣式衝擊電壓發生裝置輸出電壓波前時間,所述波前電阻5包括絕緣基板5-2,所述絕緣基板的正面和反面均設有電阻絲,且位於絕緣基板正面和反面的電阻絲互為反向繞制,圖2中的虛線為絕緣基板反面的電阻絲5-3,圖2中的實線為絕緣基板正面的電阻絲5-4,以使得二者電感方向相反,達到降低電感量的目的。
優選地,所述絕緣基板5-2由軟質絕緣材料製成,所述絕緣基板5-2正面和反面的電阻絲均採用軟質材料固定在絕緣基板5-2上;傳統衝擊電壓裝置的波前電阻都是硬質、長方體狀的,因而其體積大、重,不便於攜帶,本發明中採用軟質絕緣材料便於摺疊、重量輕、體積小,便於攜帶。
在本發明實施例的一種實施方式中,所述絕緣基板為尼龍布,所述絕緣基板正面和反面的電阻絲均通過尼龍繩縫在尼龍布上;在本發明實施例的其他實施方式中,所述絕緣基板還可以採用其他的軟質絕緣材料,所述絕緣基板正面和反面的電阻絲還可以採用其他的軟質材料固定在絕緣基板上,本發明中不對具體材料進行限定。
進一步地,為了便於調節波前電阻5阻值,提高試驗中波形調節效率,所述絕緣基板正面和/或反面的電阻絲上均設有若干個抽頭5-1,抽頭的數量根據實際需要來確定,如圖1所示,在本發明實施例中,所述絕緣基板正面和反面的電阻絲上均設有三個抽頭。
實施例3
如圖1所示,基於實施例一和實施例二,所述衝擊電壓發生器本體1、電容分壓器3、波尾電阻4均為模塊式結構,其中,衝擊電壓發生器本體1的絕緣外殼1-2分為上下兩部分,所述電容分壓器3包括一個或者多個分立的電容器,各電容器之間串聯,具體數量與本發明的氣體絕緣式衝擊電壓發生裝置的標稱電壓有關,標稱電壓低,用1個就可以了,標稱電壓高就需要用2~4個堆疊串聯而成;所述波尾電阻4包括一個或者多個分立的電阻器,各電阻器之間串聯,具體數量與本發明的氣體絕緣式衝擊電壓發生裝置的標稱電壓有關,標稱電壓低,用1個就可以了,標稱電壓高就需要用2~4個堆疊串聯而成。
由於上述方案中的衝擊電壓發生器本體1、波尾電阻4、電容分壓器3均採用模塊式結構,現場安裝時僅需將各分離的器件進行對接,現場安裝工作量大幅降低,且由於衝擊電壓發生器本體1的內部結構無需現場組裝,從而能夠顯著提升整體可靠性。
實施例4
如圖1所示,基於實施例1-3,所述電容分壓器3、波尾電阻4、波前電阻5、充電變壓器6和測控設備外部的貨櫃的底部均設有可鎖死的移動滾輪;所述衝擊電壓發生器本體1的底部設有行動裝置2,以帶動衝擊電壓發生器本體1移動,所述行動裝置2優選移動履帶車,可以另外配置遙控器,通過人工操作實現自走式移動。
基於上述技術方案,現場試驗中,可在免拆卸情況下實現裝置的移動、轉場,無需重複拆裝,從而大幅提升試驗效率。
實施例5
如圖1所示,為便於開展1100千伏gis現場標準雷電衝擊試驗,根據相關標準,要求在被試品電容量為5nf時,衝擊電壓發生裝置的輸出電壓不低於1920kv,輸出電壓波前時間控制在3μs內,本實施例中的衝擊電壓發生器採用的是marx衝擊電壓發生器。
為此,本實施例中的衝擊電壓發生器本體1中的相關參數為:額定輸出電壓為3000kv,marx衝擊電壓發生器為雙邊充電的衝擊電壓發生器迴路,其包括15級放電單元1-3(每級放電單元1-3均由4個低感脈衝電容和1個氣體火花開關組成),每級放電單元1-3額定電壓為200kv、主電容量為1μf,將15級放電單元1-3採取垂直緊湊型布置,相鄰放電單元1-3之間通過氣體火花開關相連,從而實現將本發明實施例的氣體絕緣式衝擊電壓發生裝置迴路電感量控制在20μh以內。
基於上述參數,可計算出在被試品電容量為5nf時,氣體絕緣式衝擊電壓發生裝置的裝置輸出電壓效率為:
衝擊電壓發生裝置輸出電壓波前時間為:
式(2)和(3)中,l為迴路電感;ci為發生器主電容;ct為負載電容。
衝擊電壓發生器本體1中,marx衝擊電壓發生器中15級放電單元1-3,分為上段7級、下段8級,每級放電單元1-3額定電壓200kv、主電容量1μf,可滿足1100千伏gis現場標準雷電衝擊試驗要求。由於15級全部垂直堆疊的話,裝置的體積較大,不便於運輸,因此本發明實施例中,將裝置分成上下兩段,上段內放入7級放電單元1-3、下段內放入8級放電單元1-3,這樣每段高度均較小(均在4m以下),便於運輸。
為此,經絕緣校核及驗證性試驗,確定衝擊電壓發生器本體1的絕緣外殼1-2內部預充sf6氣體壓力為0.25mpa,高度為7.8m,分為2段,本體重量可控制在4t。所述的0.25mpa是根據電場仿真和驗證試驗確定的,氣壓越高,絕緣性能越好;但是氣壓越高,對絕緣外殼1-2的抗壓能力也越高,因此需要通過仿真計算及驗證試驗,確定所需的氣體壓力。
另外,本實施例中的設於衝擊電壓發生器本體1底部的移動履帶車的具體參數為:採用電動控制、液壓驅動,載重量為8t,移動速度為2m/min,可原地轉向、可倒車、可遙控操作。
電容分壓器3的具體參數為:採用4節分立的電容器串聯,每節電容量1600pf,因此總電容量400pf,低壓臂電容量1μf,分壓比約為1:2500,其底座設有4個可鎖死移動滑輪。
波尾電阻4的具體參數為:採用2節分立式電阻器串聯,電阻器中的電阻絲採用油包線鎳鉻cr20ni80繞制,每節電阻值500ω、總電阻值1000ω,其底座設有4個可鎖死移動滑輪。
波前電阻5的具體參數為:採用尼龍布作為繞制基板,電阻絲採用油包線鎳鉻cr20ni80繞制,電阻絲彎折後通過尼龍繩縫在尼龍布上,基板正反兩面的電阻絲交錯繞制,且基板正反兩面的電阻絲相連,電阻值共200ω,基板正反兩面的電阻絲的中間均設置有3個抽頭,每段50ω。
充電變壓器6的具體參數為:採取雙邊充電方式,充電電壓精度0.1kv,最高充電電壓100kv,充電電纜連接處設有自動接地裝置6-1,其底部設有4個可鎖死移動滑輪。
測控平臺7的具體參數為:包括氣體火花開關氣壓控制、充電電壓控制及測量、輸出電壓測量等功能,整體布置於貨櫃內,其底部設有4個可鎖死移動滑輪。
綜上所述:
(1)本發明的衝擊電壓發生器本體的絕緣外殼內充設絕緣氣體的方式來實現絕緣,絕緣外殼內部的衝擊電壓發生器採用垂直緊湊型布置、並使用氣體火花開關作為放電間隙,與傳統技術中採用空氣式絕緣的衝擊電壓發生器本體相比,其整體尺寸大幅降低,從而顯著降低了裝置自身電感量。
(2)本發明中的衝擊電壓發生器本體、波尾電阻、電容分壓器均採用模塊式結構,現場安裝時僅需將各分離的器件進行對接,現場安裝工作量大幅降低,且由於衝擊電壓發生器本體的內部結構無需現場組裝,從而能夠顯著提升整體可靠性。
(3)本發明中的衝擊電壓發生器的底部裝設有行動裝置(優選移動履帶車),波尾電阻、電容分壓器、充電變壓器、測控平臺的底部均裝設有帶有制動的移動滑輪,現場試驗中,可在免拆卸情況下實現裝置的移動、轉場,無需重複拆裝,試驗效率大幅提升。
(4)本發明中的波前電阻繞制於軟質絕緣材料上(優選為尼龍布),採用正反兩面交錯繞制,以降低裝置的自感量,縮短輸出電壓波前時間;且電阻絲中間有若干抽頭,能夠便於調節波前電阻阻值,有利於提高試驗中波形調節效率。
以上顯示和描述了本發明的基本原理和主要特徵和本發明的優點。本行業的技術人員應該了解,本發明不受上述實施例的限制,上述實施例和說明書中描述的只是說明本發明的原理,在不脫離本發明精神和範圍的前提下,本發明還會有各種變化和改進,這些變化和改進都落入要求保護的本發明範圍內。本發明要求保護範圍由所附的權利要求書及其等效物界定。