電解用陰極和電解用陰極的製造方法與流程
2024-02-12 04:39:15 1
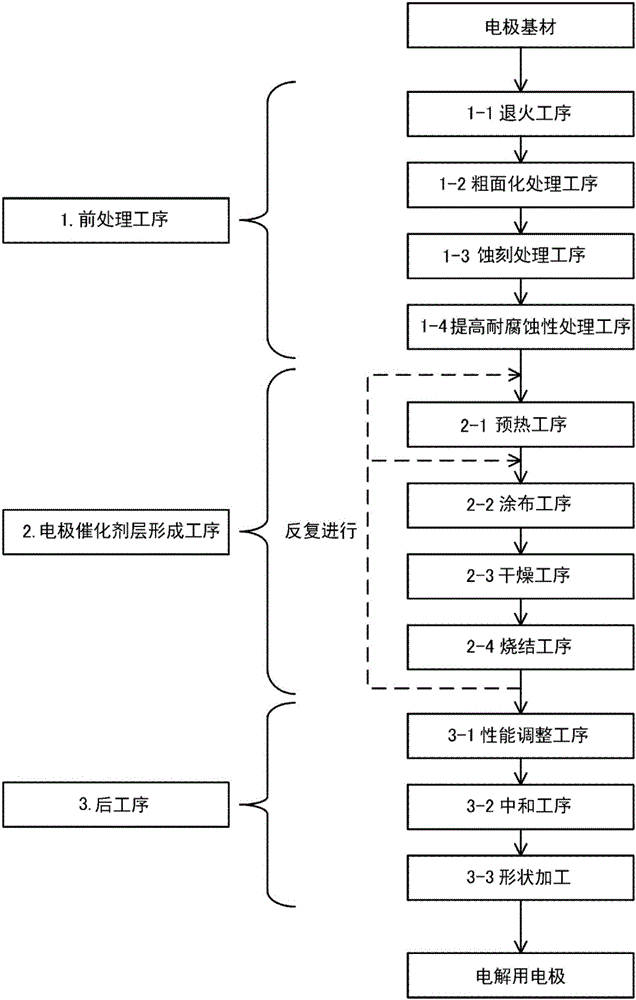
本發明涉及作為鹼電解、水電解、伴有氧產生或者伴有氯產生的各種工業電解的電解槽的陰極使用的,在金屬絲網、金屬拉伸網(expanded metal)、金屬衝孔網(perforated metal)或者類似形狀的具有構件彼此交叉而成的許多交叉部的形態的導電性陰極基材上形成有陰極催化劑層的電解用陰極及電解用陰極的製造方法。
背景技術:
例如,在鹼電解中,以往,多使用為了以高電流效率、低電壓來生產高純度的鹼金屬氫氧化物用的離子交換膜法鹼金屬氯化物電解槽,尤其是,電解用陽極和電解用陰極隔著離子交換膜相接觸的形式的壓濾機型零極距電解槽或者有限間隙電解槽(日文:ファイナイト電解セル)。
在將電解用陰極用作所述離子交換膜法電解、尤其是有限間隙電解槽或者零極距電解槽用的陰極的情況下,其導電性陰極基材使用了金屬絲網、金屬拉伸網、金屬衝孔網或者類似形狀的具有構件彼此交叉而成的許多交叉部的形態的導電性陰極基材(以下,也簡稱為「具有許多交叉部的導電性陰極基材」或者「金屬絲網狀陰極基材」)。並且,通常,在該具有許多交叉部的導電性陰極基材的一面利用塗布法積極形成陰極催化劑層,製造陰極,使形成有陰極催化劑層的一側(陰極催化劑層側)與離子交換膜的一側相接觸或者隔開微小空間地設置,在這樣的狀態下進行使用。其中,離子交換膜的相反一側的面與電解用陽極相接觸或者隔開微小空間地設置。
並且,在這種電解槽中,通常,陰極的基材使用鎳或者鎳合金,陰極的基材使用所述具有許多交叉部的導電性陰極基材,並進行了在這些基材的至少一面形成陰極催化劑層的處理,陰極催化劑層含有昂貴的鉑等稀有金屬即陰極催化劑成分。
關於陽極和陰極隔著離子交換膜相接觸的形式的零極距電解槽中使用的電解用陰極的製造方法,例如,在專利文獻1中有如下記載:用於陽極及陰極時的具有許多交叉部的導電性基材的板厚、開口率、陰極催化劑層的厚度、陰極表面的凹凸的厚度、以及退火、形狀加工、通過軋制進行的平面化處理,通過噴砂進行的粗面化處理、利用酸進行的清洗、蝕刻處理、提高耐腐蝕性處理等前處理。
如專利文獻1也有記載的那樣,以往,通常對具有許多交叉部的導電性基材實施退火、形狀加工、通過軋制進行的平面化處理、通過噴砂進行的粗面化處理、利用酸進行的清洗、蝕刻處理、提高耐腐蝕性處理等前處理,之後,進行了在一面上形成陰極催化劑層的處理,陰極催化劑層含有包括鉑族金屬和/或其氧化物的陰極催化劑成分。
該陰極催化劑層的形成工序被稱作活性化處理工序,通常該工序是通過以下工序來進行的,即:將含有能夠成為陰極催化劑成分的起始原料(以下,也簡稱為起始原料)的塗布液塗布於基材,之後,對塗布於基材的塗布液進行乾燥、燒結。更具體而言,在活性化處理工序中,通常,首先,製作將起始原料溶解而成的塗布液,將該塗布液塗布於實施了所述那樣的前處理的、具有許多孔的導電性基材的一面,之後,對其進行乾燥,然後進行燒結,形成了陰極催化劑層。此時,為了形成目標陰極催化劑層,反覆進行多次塗布塗布液並對塗布於基材的塗布液進行乾燥、燒結的工序,直到附著於導電性陰極基材的表側的陰極催化劑成分成為期望的量為止,經所述塗布、乾燥、燒結工序,來實施形成含有昂貴的鉑等稀有金屬即陰極催化劑成分(催化劑層形成物質)的陰極催化劑層的處理。其中,向基材塗布塗布液的塗布工序通常利用輥塗、噴塗、刷塗、靜電塗裝及其他方法來進行。另外,燒結工序中的加熱通常利用電爐等來進行。
現有技術文獻
專利文獻
專利文獻1:日本特許第4453973號公報
技術實現要素:
發明要解決的問題
針對所述現有技術,本發明人鑑於陰極催化劑成分是鉑等極其昂貴的稀有金屬,研究了在不損害陰極性能的前提下消減或者節省基材上的催化劑層的手段。於是,基於這樣的觀點,尤其是,針對利用嚮導電性陰極基材的表側塗布含有陰極催化劑成分的起始原料在內的塗布液之後對塗布好的塗布液進行乾燥、燒結的塗布法,在基材的表側和背側形成含有陰極催化劑成分的陰極催化劑層的形成過程,進行了詳細的研究。結果,得到以下見解。
(1)發現:在所述導電性陰極基材為具有構件彼此交叉而成的許多交叉部的形態的情況下,在塗布的階段,在該許多交叉部匯集有必要以上的量的塗布液,形成所謂的積液。並且還發現:該積液在之後進行乾燥、燒結工序時會固化,結果,成為在導電性基材的交叉部過剩地固定有陰極催化劑成分的狀態,因該積液產生的過剩地固定在交叉部的陰極催化劑成分不能有效地幫助電解,至少是多餘的,也就是沒用的部分。本發明人基於這些見解認識到:在使塗布液附著於金屬絲網這樣的具有構件彼此交叉而成的許多交叉部的形態的導電性陰極基材時,若能夠防止或者抑制在其許多銳角或者直角交叉部產生積液,則能夠使昂貴的陰極催化劑成分的使用量減少,其經濟效果極大。
(2)另外,發現如下事實:對於所述陰極催化劑層,作為所述導電性陰極基材使用的鎳或者鎳合金的鎳成分容易變成「鎳層」析出到陰極催化劑層中。並且還發現:在作為電極使用時,析出到該催化劑層中的「鎳層」導致催化劑層自身容易剝離,結果,形成所述陰極催化劑層的昂貴的陰極催化劑的消耗量變多,成為有損電極的耐久性的原因之一。所述事實可以認為是:在所述塗布液為酸性的情況下,作為電極基材使用的鎳或者鎳合金被該塗布液腐蝕溶解,該現象特別顯著而被發現。若能夠解決該問題,不僅能夠提高電極的耐久性,還能夠提高陰極催化劑層塗布液的通用性,在工業上,極其有效。
在所述這樣的電解槽中,作為電解用陰極的陰極催化劑成分,使用鉑、銥、釕、鈀、鋨等貴金屬,並且還使用鑭、鈰、釔以及鐠等稀土類元素,無論哪一成分都是被稱作稀有金屬、貴金屬的稀有的極其昂貴的材料,其價格逐年上漲。並且,所述電解槽在臨海地域的大規模化學工廠的電解設備中使用等用於大型設備中,陰極催化劑成分的使用量也極大,電解槽的製造成本中陰極催化劑成分所佔的成本比例變得極大。因此,對於降低陰極催化劑層的形成材料即所述昂貴的陰極催化劑成分的費用,說是利用電解槽的產業界的夙願也不為過。具體而言,能夠以儘可能少量的陰極催化劑成分形成催化劑層,並且形成的催化劑層能夠在更長期間內使用,這在工業上具有極大的意義。
對此,在現有技術中,完全沒有本發明人的下述認識,即:在利用塗布法在具有許多交叉部的金屬絲網、金屬拉伸網、金屬衝孔網等導電性基材上形成陰極催化劑層的情況下,在許多交叉部產生積液、因該積液在許多交叉部產生過剩地固定有對提高陰極催化劑層的性能沒有幫助的陰極催化劑成分的部分,針對該點的節省資源化的認識;以及,作為另一問題,由於析出到催化劑層中的「鎳層」使催化劑層自身變得容易剝離,導致陰極催化劑的消耗量變多,成為有損耐久性的原因,關於該點的認識。另外,自然也完全沒有進行基於這些認識的研究。即,關於使陰極催化劑成分嚮導電性陰極基材的附著量(固定量)、陰極催化劑的消耗量更經濟且使還包括耐久性的提高在內的性能最優化所需要的方法、手段、對策的研究,在現有技術中,不僅作為本發明的對象的陰極的領域,即使對其他技術領域進行調查,包括專利文獻1在內,都沒有公開也沒有給出技術啟示。
因而,本發明的目的在於,向具有許多交叉部的導電性陰極基材的表面利用所述塗布法在所述導電性陰極基材的表側和背側塗布包含陰極催化劑成分的塗布液的情況下,有效防止或者抑制在其許多銳角或者直角交叉部產生積液,降低昂貴的陰極催化劑成分的使用量。同時,其目的還在於,防止所述陰極催化劑層在使用時發生的剝離,謀求降低所述陰極催化劑的消耗量,由此提高電解用陰極的耐久性。更具體而言,本發明的目的在於提供一種在形成所述陰極催化劑層時,在不使陰極性能降低的前提下降低包括貴金屬等稀有金屬的陰極催化劑成分的使用量,而且還解決了催化劑層在使用時的剝離問題的電解用陰極及電解用陰極的製造方法。
用於解決問題的方案
所述目的通過下述的本發明達成。在本發明中,作為第1問題解決手段,提供一種電解用陰極,其特徵在於,具有:導電性陰極基材,其包括具有以線狀或者帶狀的構件彼此交叉的部分為交叉部的許多交叉部的金屬絲網、具有以其孔隙的直角或者銳角部分為交叉部的許多交叉部的金屬拉伸網或者金屬衝孔網中的任一者;陰極催化劑層,其是利用向該導電性陰極基材的表側塗布包含陰極催化劑成分的起始原料在內的塗布液、之後對塗布的塗布液進行乾燥、燒結的塗布法,在所述導電性陰極基材的表側和背側形成的,所述陰極催化劑層含有所述陰極催化劑成分,所述陰極催化劑成分含有從鉑、銥、釕、鈀、鋨、鎳及它們的氧化物中選出的至少一種,所述導電性陰極基材是鎳或者鎳合金,在所述導電性陰極基材的交叉部沒有確認到積液的固化部分,或者,在能確認到積液的固化部分的情況下,該固化部分的截面的形態具有網眼狀的細孔,所述固化部分的平均孔隙率為15%以上。
在所述第1問題解決手段中成為必要的「在導電性陰極基材的交叉部沒有確認到積液的固化部分,或者,在能確認到積液的固化部分的情況下,該固化部分的截面的形態具有網眼狀的細孔,所述固化部分的平均孔隙率為15%以上」這一點是通過將即將塗布所述塗布液時的所述導電性陰極基材預熱為43℃~120℃的溫度來形成所述陰極催化劑層而達成的,同時,還能夠獲得防止由來自基材的鎳向陰極催化劑層中溶出而成為「鎳層」析出導致的、可能產生的所述陰極催化劑層的剝離的問題這樣的效果。
作為本發明的電解用陰極的優選形態,能夠列舉出所述平均孔隙率為44%以上。其中,本申請中規定的所述平均孔隙率是利用後述的方法測量出的孔隙率的算術平均值。
在本發明中,作為方案不同的第2問題解決手段,提供一種電解用陰極的製造方法,其是製造所述任一電解用陰極的方法,其特徵在於,該方法具有陰極催化劑層形成工序,在陰極催化劑層形成工序中,將嚮導電性陰極基材的至少一面塗布含有陰極催化劑成分的起始原料在內的塗布液、之後對塗布於所述基材的塗布液進行乾燥、燒結的工序執行一次或者多次,來在所述導電性陰極基材的表側和背側形成含有所述陰極催化劑成分的陰極催化劑層,所述導電性陰極基材包括具有以線狀或者帶狀的構件彼此交叉的部分為交叉部的許多交叉部的金屬絲網、具有以其孔隙的直角或者銳角部分為交叉部的許多交叉部的金屬拉伸網或者金屬衝孔網中的任一者,所述陰極催化劑成分含有從鉑、銥、釕、鈀、鋨、鎳及它們的氧化物選出的至少一種,所述導電性陰極基材是鎳或者鎳合金,在所述陰極催化劑層形成工序,以使即將塗布所述塗布液時的導電性陰極基材的溫度在43℃~120℃的範圍內的方式加熱一次以上。
作為本發明的電解用陰極的製造方法的優選形態,能夠列舉出:在所述陰極催化劑層形成工序中,在塗布所述塗布液的工序的上遊側設有對所述導電性陰極基材進行預熱的部件,將塗布所述塗布液、之後對塗布於所述基材的塗布液進行乾燥、燒結的工序反覆進行多次,進行反覆的總次數中的每次都使用所述進行預熱的部件以使即將塗布所述塗布液時的導電性陰極基材的溫度在43℃~120℃的範圍內的方式進行加熱;以使即將塗布所述塗布液時的所述導電性陰極基材在43℃~63℃的溫度範圍內的方式進行加熱;所述塗布液為酸性。
關於在前面規定的即將進行塗布時的導電性陰極基材的溫度,如後述那樣,43℃是在驗證試驗中明顯確認到本發明的效果時的實測的下限值,例如,63℃是指以±1℃的誤差實測出的溫度。關於這些見後述。
發明的效果
採用本發明,在陰極催化劑層的形成工序中,在塗布包含陰極催化劑成分的常溫的塗布液時,以即將塗布塗布液時的導電性陰極基材的溫度成為43℃~120℃、優選在43℃~63℃的範圍內的方式加熱一次以上,優選是反覆進行塗布時的總次數,以這樣的極其簡便的手段,能夠在不使電解用陰極的性能降低的前提下,降低用於形成陰極催化劑層的昂貴的陰極催化劑成分的使用量。更具體而言,採用本發明,利用塗布法在金屬絲網等具有許多交叉部的導電性陰極基材的表面塗布包含陰極催化劑成分的塗布液而在導電性陰極基材的表側和背側形成了陰極催化劑層時,在許多交叉部不生成由塗布液的積液導致的過剩地包含陰極催化劑成分的固化部分(多餘且沒用的部分),或者即使產生這樣的由塗布液的積液導致的固化部分,該部分的截面的形態成為具有許多能夠確認到空洞的網眼狀的細孔的形態,也就是說消減了多餘且沒用的固化部分,因而,形成的陰極催化劑層所用的昂貴的陰極催化劑成分的量與以往的陰極催化劑層相比,被有效地消減,結果,能夠提供經濟性優良的電解用陰極。除所述效果之外,採用本發明,以使即將塗布塗布液時的導電性陰極基材的溫度處於特定範圍內的方式進行加熱,利用這樣的極其簡便的手段,還能夠解決形成好的陰極催化劑層自身在使用時容易剝離這樣的問題,結果,能夠謀求降低因使用而產生的陰極催化劑的消耗量,這樣,還能夠提高電解用陰極的耐久性。如所述那樣,採用本發明,能夠提供一種電解用陰極及電解用陰極的製造方法,能夠在不使電解用陰極的性能降低的前提下,降低用於形成陰極催化劑層的昂貴的陰極催化劑成分的使用量,因此,經濟性優良,並且,還能夠期待提高催化劑層的耐久性。
附圖說明
圖1是表示本發明的電解用陰極的製造方法的實施方式的一例的概略工序圖。
圖2-1是本發明的實施例的電解用陰極的形成有陰極催化劑層的金屬絲網基材的交叉部的截面形態的SEM照片的圖。
圖2-2是以往的電解用陰極的形成有陰極催化劑層的金屬絲網基材的交叉部的截面形態的SEM照片的圖。
圖3是表示實施例和比較例中使用的陰極催化劑層的形成工序和孔隙率的測量用試樣的製作工序的圖。
圖4-1是表示利用低濃度塗布液並使即將塗布該塗布液時的金屬絲網基材的溫度為63℃的實施例3-1和實施例3-2中的形成有陰極催化劑層的金屬絲網基材的交叉部的、過剩地固定有陰極催化劑成分的部分(以下,也稱作「積液的固化部分」)的截面的形態和利用圖像二值化處理用軟體測量孔隙率時的狀態的圖。
圖4-2是表示利用低濃度塗布液並使即將塗布該塗布液時的金屬絲網狀基材的溫度為63℃的實施例3-3和實施例3-4中的「積液的固化部分」的截面的形態和利用圖像二值化處理用軟體測量「積液的固化部分」的孔隙率時的狀態的圖。
圖5是表示利用高濃度塗布液並使即將塗布該塗布液時的金屬絲網狀基材的溫度為63℃的實施例4-2和實施例4-4中的「積液的固化部分」的截面的形態和利用圖像二值化處理用軟體測量「積液的固化部分」的孔隙率時的狀態的圖。
圖6-1是表示利用低濃度塗布液並使要塗布該塗布液的金屬絲網狀基材保持為周圍溫度的比較例1-1和比較例1-2中的「積液的固化部分」的截面的形態和利用圖像二值化處理用軟體測量「積液的固化部分」的孔隙率時的狀態的圖。
圖6-2是表示利用低濃度塗布液並使要塗布該塗布液的金屬絲網狀基材保持為周圍溫度的比較例1-3和比較例1-4中的「積液的固化部分」的截面的形態和利用圖像二值化處理用軟體測量「積液的固化部分」的孔隙率時的狀態的圖。
圖7是對在塗布工序中,在使用了100g/L的低濃度塗布液的條件下,使即將塗布該塗布液時的金屬絲網狀基材的溫度在周圍溫度與63℃之間變化的、由實施例1、3及比較例1得到的各8個的孔隙率的數據進行統計解析而得到的表示基材溫度和孔隙率的相關關係的圖表。
圖8是對在塗布工序中,在使用了200g/L的高濃度塗布液的條件下,使即將塗布該塗布液時的金屬絲網狀基材的溫度在周圍溫度與63℃之間變化的、由實施例2、4及比較例2得到的各8個的孔隙率的數據進行統計解析而得到的表示基材溫度與孔隙率的相關關係的圖表。
圖9-1是應用了本發明方法的,以使即將塗布塗布液時的導電性陰極基材的溫度成為43℃的方式進行對導電性陰極基材的加熱而製造出的本發明的一例的電解用陰極的、電解前的陰極催化劑層的剖切面的SEM照片的圖。
圖9-2是沒有應用本發明方法的,在即將塗布塗布液時的導電性陰極基材的溫度仍為常溫(周圍溫度)的狀態下製造的比較用的電解用陰極的、電解前的陰極催化劑層的截面的剖切面的SEM照片的圖。
圖9-3是沒有應用本發明方法的,在即將塗布塗布液時的導電性陰極基材的溫度仍為常溫(周圍溫度)的狀態下製造的比較用的電解用陰極的、表5所示的電解後的陰極催化劑層的剖切面的SEM照片的圖。
具體實施方式
以下,針對本發明的電解用陰極和該電解用陰極的製造方法,列舉優選的實施方式,詳細地說明本發明。
(1)首先,對本發明的電解用陰極的製造方法進行說明,本發明的電解用陰極的製造方法能夠簡便得到本發明的電解用陰極,本發明的電解用陰極具有陰極催化劑層,該陰極催化劑層是通過在含有鎳或鎳合金的導電性陰極基材上塗布含有陰極催化劑成分的原料在內的塗布液並使其乾燥、固化而形成的,在該陰極催化劑層,在陰極基材的構件彼此交叉的交叉部沒有生成多餘且沒用的陰極催化劑層(「積液的固化部分」),或者與以往的電解用陰極相比能夠減少過剩地固定的陰極催化劑成分的量,實現昂貴的陰極催化劑成分的使用量的減少。如所述那樣,本發明的目的在於解決本發明人新發現的、利用塗布法在具有許多交叉部的形態的導電性陰極基材的至少一面形成陰極催化劑層時產生的技術問題。並且,在本發明中,利用新特徵解決所述技術問題,實現所述的顯著效果,該新特徵為:在嚮導電性陰極基材形成陰極催化劑層的工序中,以使即將塗布含有陰極催化劑成分的原料在內的塗布液時的導電性陰極基材的溫度在43℃~120℃的範圍內的方式加熱一次以上、優選是反覆進行塗布液的塗布時的總次數。因而,在本發明的製造方法中,除所述特徵以外,基本上與以往的電解用陰極的製造方法同樣。
(2)而且,採用所述本發明的製造方法,還能解決以往忽視的在電解用陰極產生的下述技術問題。如之前所述那樣,本發明人發現了如下這樣的事實:向鎳或者鎳合金的陰極基材的表面塗布含有貴金屬、其氧化物、鎳氧化物等起始原料的塗布液並使其乾燥、固化而形成了陰極催化劑層時,尤其是,當塗布液為酸性時,鎳成分容易變成「鎳層」析出到陰極催化劑層中。即,利用構成本發明的塗布塗布液並使其乾燥、固化的「塗布熱分解法」來形成陰極催化劑層時,有時陰極基材中的鎳成分會溶出,作為鎳析出部析出到陰極催化劑層中,該鎳析出部經燒結工序變成鎳層。並且,當陰極的陰極催化劑層中存在該鎳層時,由於長期間的電解或者短時間的反向電解會產生下述情況:鎳層加速溶出到電解液中,使陰極催化劑層剝離。本發明人發現利用本發明的製造方法能夠抑制所述「鎳層」的出現。本發明人認為其原因在於,在即將塗布塗布液時以特定的溫度範圍加熱基材,從而促進了塗布液的蒸發,結果,陰極基材上的塗布液的乾燥加快,這樣,能夠縮短酸性的塗布液與基材之間的接觸時間,結果,能夠有效抑制陰極基材的鎳成分變成「鎳層」析出到陰極催化劑層中。基於該點,作為促進塗布液的乾燥的手段,塗布液使用混合有揮發性高的乙醇或者其他有機溶劑而成的塗布液,能夠進一步加快陰極基材上的塗布液的乾燥,結果,能夠形成可以解決所述問題的陰極催化劑層。
在本發明中作為問題的利用塗布法形成陰極催化劑層的情況下,需要使用將貴金屬或者貴金屬氧化物、鎳氧化物等催化劑成分的原料物質均勻地溶解而成的塗布液,這些原料物質如後述那樣使用氯化物、硫酸鹽、硝酸鹽,其溶劑也大多使用鹽酸、硫酸、硝酸等酸性溶劑,塗布液也多為酸性。如所述那樣,採用本發明的製造方法,能夠解決以下這樣的問題:在鎳或者鎳合金的陰極基材的表面使用含有貴金屬、貴金屬的氧化物、鎳氧化物等起始原料的塗布液來形成陰極催化劑層時,在使用了酸性的塗布液的情況下尤其明顯的、由因長期間的電解或者短時間的反向電解而在陰極催化劑層中容易析出鎳層導致陰極催化劑層剝離,由此導致陰極催化劑的消耗量變多。
以下,對具有成為產生本發明的技術問題的對象的形態的導電性陰極基材進行說明。
(導電性陰極基材)
在本發明中,導電性陰極基材使用鎳或者鎳合金。並且,該導電性陰極基材(以下,也稱為「導電性基材」)是金屬絲網、金屬拉伸網、金屬衝孔網或者類似形狀的具有構件彼此交叉而成的許多交叉部的形態。這是因為在本發明中以下述的點為要解決的技術問題。即,在將包含陰極催化劑成分的塗布液塗布於導電性陰極基材時,例如,在構成金屬絲網的線狀的金屬等的構件彼此交叉而成的交叉部生成積液,由該積液引起了在交叉部過剩地固定有陰極催化劑成分。但是,該「積液的固化部分」對提高陰極性能沒有幫助,也就是說成為昂貴的材料被浪費使用的部位,得到了這樣的見解,在本發明中,以儘可能減少該「積液的固化部分」為目標。
本發明中所謂的交叉部是指,例如,構成金屬絲網的線狀、帶狀的金屬制等的構件彼此交叉的部分、金屬拉伸網、金屬衝孔網等的孔隙的直角或者銳角部分,其交叉的角度並不特別限定,但是鑑於所述問題,需要是在將包含陰極催化劑成分的塗布液以通常的狀態塗布於基材時容易產生積液的程度的角度。例如,能夠列舉出:作為金屬制的構件的金屬線彼此縱橫交叉的、所成的角都為90度的、網眼部分的網眼形狀都為正方形或者長方形的金屬絲網;金屬線彼此所成的角的一部分為小於90度的交叉部分的、網眼部分的至少一部分具有三角形、菱形,梯形等網眼形狀的金屬絲網等。
在所述內容中,例示了作為金屬制的構件的金屬線彼此交叉的情況,所述的金屬線不限於鐵絲那樣的截面為圓形的情況,也可以是橢圓、多邊形、偏平的情況,還可以是帶狀的金屬板交叉的情況。另外,不限於直線狀的情況,也可以是具有凹凸的形狀或者鋸齒狀。金屬線等構件的粗細也不特別限定,只要為以往使用的金屬絲網或者類似形態的導電性基材,則均符合。另外,導電性基材的整體形狀並不特別限定,雖然以往通常使用平紋的板狀基材,但是並非一定要是平坦面,根據用途也可以是有適當的曲面的情況。不言而喻,即使是被限定為平紋的結構,也不限定其網眼的大小。在本發明中重要之處在於,符合作為對象的導電性基材具有在其至少一面上塗布了含有陰極催化劑成分的起始原料在內的塗布液的情況下能夠在構件彼此的交叉部產生積液的形態。換言之,本發明的技術不限於向本發明中規定的導電性基材塗布含有陰極催化劑成分的塗布液來形成陰極催化劑層的情況,能夠成為在需要向金屬絲網狀基材的至少一面塗布包含昂貴的稀有金屬成分的塗布液來形成層的其他情況也能夠利用的、能夠實現減少昂貴的成分的浪費使用的、基於節省資源的觀點在哪個領域都有用的技術。另外,採用本發明,還能夠避免在構件彼此的交叉部生成由積液引起的固化部分,因此,根據情況,還能夠提高外觀設計效果,在這方面也是有用的。
所述那樣的具有許多交叉部的導電性基材的材質是鎳或者鎳合金。另外,導電性基材適合使用比表面積1.1m2~2.4m2(每1m2投影面積的實際表面積)、厚度0.1mm~0.8mm左右的材料。以下,說明電解用陰極的製造方法的概略情況,進而,對本發明的電解用陰極的特徵的陰極催化劑層及該陰極催化劑層的形成工序進行說明。
(電解用陰極的製造方法)
1.前處理工序
在圖1中示出了本發明的電解用陰極的製造方法的製造工序的一例。如圖1所示,也可以在陰極催化劑層的形成工序之前對導電性基材實施前處理工序。作為前處理工序,例如實施圖1中1所示那樣的在以往的製造工序中執行的各工序即可。當然,前處理工序並不限定於圖1中示出的前處理。
2.陰極催化劑層形成工序
作為本發明的電解用陰極的製造方法的特徵的工序存在於圖1中2所示的陰極催化劑層形成工序。在該工序中,在所述的具有許多交叉部的形態的導電性基材的至少一面塗布含有陰極催化劑成分(以下,也簡稱為「催化劑成分」)的起始原料在內的塗布液,之後對塗布於所述基材的塗布液進行乾燥、燒結,將這樣的塗布、乾燥、燒結的工序進行一次或反覆進行多次,從而形成陰極催化劑層(以下,也簡稱為「催化劑層」)。根據本發明人的研究,在以往的方法中,要塗布塗布液的對象的導電性基材如之前所述那樣是表面積較大的金屬絲網狀基材,因此在燒結後會迅速地自然冷卻,所以,即使在反覆進行多次所述一連串工序的情況下,再次塗布塗布液時,即將塗布塗布液時的導電性基材的溫度也變成接近周圍溫度(常溫),至少沒有成為43℃以上這樣的高溫。相對於此,在本發明的製造方法中,在該陰極催化劑層形成工序中,以使即將塗布塗布液時的導電性基材的溫度在43℃~120℃的範圍內的方式加熱一次以上、優選是塗布塗布液的次數的總數,進而,從兼顧得到的效果和升溫所需要的成本的角度出發,優選加熱為在43℃~63℃的範圍內,採用該特徵,能夠得到以往沒有的經濟的電解用陰極。如所述那樣,在以往的方法中,不對即將塗布塗布液時的導電性基材的溫度進行控制,在仍為周圍溫度(常溫)的狀態下的導電性基材上塗布塗布液,至少沒有成為43℃以上的高溫。如後述那樣,本發明人基於如下這樣的新見解完成了本發明,即:通過使即將塗布塗布液時的金屬絲網狀等的導電性基材的溫度比以往高,能夠減少形成陰極催化劑層所使用的昂貴的陰極催化劑成分的使用量。
為了在陰極催化劑層的形成工序更有效且可靠地獲得本發明的效果,採用這樣的特徵:在塗布所述塗布液的工序的上遊側設有具有對導電性基材進行預熱的手段的預熱工序。另外,為了形成期望厚度的催化劑層,將塗布所述塗布液之後進行乾燥、燒結的一連串工序反覆進行多次,在該情況下,優選構成為:在每次塗布塗布液時,都使用預熱手段可靠地使即將塗布所述塗布液時的導電性基材的溫度在43℃~120℃的範圍內,優選在43℃~63℃的範圍內。以下,參照圖1例示的工序的概略圖,說明如所述那樣構成的情況下的本發明的電解用陰極的製造方法的步驟。另外,只要使即將塗布塗布液時的導電性基材的溫度在43℃~120℃的範圍內就能夠容易地獲得本發明的顯著效果,因此只要是能夠實現該點的實施方式即可,不限於下面所述的利用預熱手段進行的預熱工序。
圖1中例示的方法構成為:在嚮導電性基材塗布包含催化劑成分的塗布液的塗布工序(2-2)的前段,設有以往的方法中不存在的具有對基材進行預熱的手段的預熱工序(2-1),使用該預熱手段使即將塗布塗布液時的導電性基材的溫度在43℃~120℃的範圍內。如圖1所示,在實施了向經這樣加熱為特定的溫度的導電性基材塗布塗布液的塗布工序(2-2)之後,經乾燥工序(2-3)、燒結工序(2-3),從而在導電性基材上形成催化劑層。
在導電性基材上形成催化劑層的情況下,為了使催化劑層的厚度為期望的厚度,通常,反覆執行所述工序來形成期望的厚度的催化劑層,本發明的製造方法更優選構成為:該情況下,在每次塗布塗布液時,在塗布工序(2-2)之前先進行預熱工序(2-1)。即,若這樣構成,則在塗布塗布液時,導電性基材的溫度始終在43℃~120℃的範圍內,優選在43℃~63℃的範圍內,因此,在每次塗布塗布液時,都能夠避免生成在導電性基材的交叉部形成的積液的固化部分,或者,能夠降低過剩地固定在該部分的昂貴的催化劑成分的使用量,所以能夠獲得更高的效果。當然,在反覆執行所述工序的情況下,只要至少一次對導電性基材進行加熱,則在該次,催化劑成分的浪費與以往的情況相比也能夠減少,因此也能夠獲得本發明的效果。但是,為了獲得更高的效果,優選構成為在每次進行塗布工序(2-2)時都使即將塗布塗布液時的導電性基材的溫度在43℃~120℃的範圍內。若這樣構成,則在任一次都能夠減少用於形成陰極催化劑層的陰極催化劑成分的浪費。
在本發明中,通過適當決定進行預熱的時機和次數,也能夠在基材的表側和背側分別形成具有期望的量的催化劑成分的催化劑層。即,本發明人發現:在嚮導電性基材的表側塗布塗布液的情況下,若通過預熱對基材預加熱,則塗布的塗布液的乾燥加快,該液中的催化劑層形成物質固定於基材表側所需時間縮短。結果,能夠減少塗布液經由孔隙等向金屬絲網狀基材的背側移動的量,能夠有效地控制移動、固定到背側的催化劑層形成物質的量。因此,與不進行預熱就嚮導電性基材塗布塗布液之後進行乾燥、燒結的情況相比較,形成於表側的陰極催化劑層的催化劑成分量明顯多於經由基材的孔隙等而形成到基材的背側的陰極催化劑層的催化劑成分量。
在本發明的方法中,預熱工序在塗布塗布液的工序之前執行至少一次即可,預熱工序的次數也可以是多次或者在所有的塗布工序之前都執行預熱工序。預熱工序的時機,並非一定要在第一次的工序就進行預熱,例如,也可以是,在第一次的工序不進行預熱,首先,進行塗布、乾燥、燒結的一連串工序,之後進行預熱。另外,也可以是,在塗布、乾燥、燒結的一連串工序進行了多次之後,進行預熱,之後,再進行塗布、乾燥、燒結的一連串工序。此外,預熱的次數也是一次以上即可,也可以是針對每次塗布工序,在塗布之前一定進行預熱。根據本發明人的研究,還能夠通過調整預熱的次數和進行預熱的時機,來調整導電性基材的、經由孔隙或者上下左右各端附著於導電性基材背側的含有電極催化劑成分的起始原料在內的塗布液的附著量。作為結果,預熱的次數越多,則相對於形成在導電性基材的表側的陰極催化劑層的催化劑成分量而言形成在該導電性電極基材的背側的陰極催化劑層的催化劑成分量越少。即,能夠使附著於導電性基材的表側的催化劑成分量的、相對於形成在導電性基材的背側的陰極催化劑層的催化劑成分量的比例增大,並且,還能夠適當控制增大的程度。
如所述那樣,能夠降低用於形成陰極催化劑層的催化劑成分的使用量的本發明的經濟的電解用陰極能夠通過本發明的電解用陰極的製造方法極其容易且可靠地得到,本發明的電解用陰極的製造方法為:在陰極催化劑層形成工序中新設了具有預熱手段的預熱工序(2-1),對成為周圍溫度以下的溫度的導電性基材進行一次以上的預熱,優選每次塗布塗布液都進行預熱,加熱為即將塗布包含催化劑成分的塗布液時的導電性基材的溫度在43℃~120℃的範圍內。另外,根據本發明人的研究,在所述內容中,在考慮到能獲得的效果和加熱所要的成本等的情況下,進一步優選使即將進行塗布工序時的導電性基材的溫度為43℃~63℃,通過這樣構成,能夠更經濟地形成良好的陰極催化劑層。以下,對在本發明的特徵的陰極催化劑層的形成工序中為了使即將塗布塗布液時的導電性基材的溫度在43℃~120℃的範圍內而設置的預熱工序(2-1)的一例進行說明,並對通過使即將塗布塗布液時的導電性基材的溫度處於本發明規定的範圍所實現的效果詳細進行說明。
[2-1:預熱工序]
如所述那樣,本發明的電解用陰極的製造方法的特徵在於,在導電性基材的至少一面上形成陰極催化劑層的催化劑層形成工序中,使即將塗布所述塗布液時的導電性基材的溫度在特定的溫度範圍內一次以上,其他工序與以往的電解用陰極的製造方法中的陰極催化劑層的形成方法同樣即可。具體而言,以往,在具有許多交叉部的導電性基材(金屬絲網狀基材)的表面上形成陰極催化劑層的情況下,向該基材的成為表側的一面上塗布含有催化劑成分的起始原料在內的塗布液,之後進行乾燥、燒結,將該塗布、乾燥、燒結的一連串工序反覆執行多次,從而在基材表面形成具有期望的量的陰極催化劑成分的、期望厚度的陰極催化劑層,本發明的方法基本上也是一樣的。本發明的製造方法的特徵在於構成為:在將塗布、乾燥、燒結的一連串工序反覆執行多次的情況下,以使即將塗布塗布液時的導電性基材的溫度在43℃~120℃的範圍內的方式加熱一次以上,向基材塗布塗布液。
根據本發明人的研究,通過使即將塗布所述塗布液時的金屬絲網狀基材的溫度為43℃~120℃的範圍內的溫度,能加快塗布於基材的表面的含有起始原料的塗布液的乾燥,抑制基材表面的塗布液的濡溼擴散,由此在交叉部難以生成積液,並且,即使生成積液,與不進行預熱工序的情況相比較,也能夠明顯減少在金屬絲網狀基材的交叉部積留的催化劑成分的量。結果,當在塗布塗布液後進行乾燥、燒結而形成催化劑層時,在導電性基材所具有的許多交叉部,沒有生成由塗布了所述塗布液時產生的積液引起的過剩的「積液的固化部分」,或者,即使存在因積液而固化的過剩的「積液的固化部分」,該部分的截面的形態也為具有連內部都有許多空洞的網眼狀的細孔的、能夠減少催化劑成分的使用量的狀態。
圖2示出了表示「積液的固化部分」的樣子的SEM照片。圖2-1是設有預熱工序而以使即將塗布塗布液時的金屬絲網狀基材的溫度為實測63℃左右的方式加熱,之後進行乾燥、燒結而形成了催化劑層的情況下的交叉部的截面形態的SEM照片的圖。都是使用催化劑成分為100g/L的同樣濃度的塗布液,且導電性基材使用包括同樣的材質及形態的鎳制的平紋金屬絲網(φ0.15×40網眼)進行了試驗的結果。上層和下層的數據的試驗的日子不同,並且,圖2-1的上層和下層各自的左右的數據是在同一天進行的試驗中改變了觀察部位的情況下的鎳線的交叉部的截面形態的SEM照片的圖。另外,圖2-2是除了未設預熱工序以外以與圖2-1進行的試驗同樣的條件形成了催化劑層的情況下的SEM照片的圖。上層和下層的數據的試驗的日子不同。另外,圖2所示的SEM照片用的試樣的調製通過如下方式進行,即:在形成陰極催化劑層後,從電解用陰極切取包含導電性基材的交叉部的部分,將其沿鉛垂方向埋入透明樹脂中並使之固化,在交叉部進行切斷、研磨,對基材的剖切面進行觀察。關於其詳細情況將在後面進行說明。
從兩者的比較可以確認出:有預熱工序還是沒有預熱工序,尤其是,形成在構成金屬絲網的鎳線的交叉部的催化劑層的狀態明顯發生變化。具體而言,對於本發明的實施品,在從外部進行觀察的情況下,與以往品相比,鎳線交叉的交叉部處的由塗布液的積液導致的固化部分明顯變少,或者有時幾乎確認不到積液的固化部分。更具體而言,從圖2-1所示的交叉部的截面形態的SEM照片的圖來看,本發明的電解用陰極的催化劑層在交叉部具有積液的固化部分的情況下,其截面的形態為連內部都有空洞,成為呈網眼狀存在許多細孔的狀態,與圖2-2所示的以往的電解用陰極的積液的固化部分明顯不同。以往的電解用陰極的積液的固化部分有時也能確認到孔,但是,如圖2-2所示,與本發明的電解用陰極的情況不同,沒有成為連內部都有空洞的網眼狀的細孔。因此,通過與所述同樣地觀察形成有催化劑層的導電性基材的構件彼此的交叉部的截面形態,能夠簡單地判定是本發明的電解用陰極還是以往的電解用陰極。
關於對即將塗布塗布液時的包括金屬絲網的導電性基材(金屬絲網狀基材)實施所述預熱工序所能夠得到的效果,本發明人進行了更詳細的研究。具體而言,通過預熱,使即將塗布塗布液時的金屬絲網狀基材的溫度進行各種變化,詳細研究了形成在金屬絲網的交叉部的催化劑層的狀態的不同。結果,確認出:通過使塗布了塗布液的金屬絲網狀基材的溫度為某溫度以上,能夠加快剛塗布後的塗布液的乾燥,之後進行燒結使其固定,從而能夠抑制塗布好的塗布液的濡溼擴散,尤其是針對會在金屬絲網的交叉部生成的積液的固化部分,與以往的情況相比較,能夠明顯將催化劑成分的使用量抑制為較少。並且,如下述那樣,還了解到:根據即將塗布塗布液時的金屬絲網狀基材的溫度的不同,減少催化劑成分的使用量的效果不同。
根據本發明人的詳細研究,通過使即將塗布塗布液時的金屬絲網狀基材的溫度在43℃~120℃的範圍內,從而使形成在構件彼此的交叉部分的催化劑層的、過剩地固定有陰極催化劑成分的「積液的固化部分」的截面的狀態確實成為圖2-1所示那樣的、具有連內部都有許多空洞的網眼狀的細孔的形態。結果,能夠可靠地減少要使用的陰極催化劑成分量。本發明人為了能夠對能夠達到本發明的效果的條件進行更客觀的判斷,利用後述的方法來求出該「積液的固化部分」的截面的孔隙率,確定了所述溫度範圍。對於該點,利用實施例來詳細說明。
得知:通過實施在以往的製造方法中不進行的對金屬絲網狀基材的預熱工序,對於本發明的電解用陰極,會在金屬絲網狀基材的交叉部生成的、多餘地固定有催化劑成分的「積液的固化部分」的截面形態中的平均孔隙率為15%以上。進而還得知:根據條件,能夠為100%,即能夠消除在本發明中作為問題的交叉部處的「積液的固化部分」的存在。因此,本發明的電解用陰極有效降低了用於形成催化劑層的昂貴的陰極催化劑成分的塗敷量,經濟性良好。即,該平均孔隙率越高,意味著越能降低塗敷的貴金屬等陰極催化劑成分的使用量,因此,為了獲得本發明的更高的效果,期望決定預熱工序的條件,以使該「積液的固化部分」的截面形態中的平均孔隙率更高。通過這樣,能夠進一步有效地降低用於形成催化劑層的昂貴的陰極催化劑成分的使用量,實現電解用陰極的經濟性的提高。
如所述那樣,本發明在陰極催化劑層的形成工序中,在塗布包含陰極催化劑成分的常溫的塗布液時,以使即將塗布塗布液時的導電性陰極基材的溫度在43℃~120℃的範圍內的方式加熱一次以上、優選是在反覆塗布時的總次數。於是,採用該特徵,在所述導電性陰極基材的交叉部沒有確認到積液的固化部分,或者,在確認到的情況下,該固化部分的截面的形態也為具有網眼狀的細孔的平均孔隙率15%以上的形態,並且,導電性陰極基材的鎳成分不會溶出到陰極催化劑層中,在陰極催化劑層中沒有形成鎳析出部。結果,能夠防止由鎳析出部或者鎳層引起的陰極催化劑層的剝離。
本發明中使用的陰極催化劑成分含有從鉑、銥、釕、鈀、鋨、鎳或者它們的氧化物選出的至少一種,並且,還含有鑭、鈰、釔等稀土類元素,鈦、鉭等閥金屬或者它們的氧化物。這些成分都是昂貴的稀有金屬材料,而本發明的電解用陰極能有效地降低形成催化劑層所需的陰極催化劑成分的使用量。因此,本發明的電解用陰極與以往的產品相比較,可靠地降低了昂貴的稀有金屬材料的費用,經濟性良好。
以下,對預熱工序的詳細情況進行說明。
(溫度範圍)
對於所述經濟性良好的本發明的電解用陰極,能夠通過在塗布工序的前段對金屬絲網狀基材進行的預熱工序中,以即將塗布塗布液時的金屬絲網狀基材的溫度在43℃~120℃的範圍內的方式加熱而容易地獲得。在所述溫度為低於43℃的溫度的情況下,沒有顯著效果,另一方面,在所述溫度成為超過120℃的溫度、例如接近塗布液的沸點溫度時,塗布液會蒸發,需要加熱為大幅度地低於塗布液的沸點的溫度以下。本發明中規定的臨界的溫度範圍是經實驗驗證了的。根據本發明人的詳細研究,能夠獲得本發明的顯著效果的下限值是43℃,另一方面,具有隨著溫度升高而能夠減少本發明中作為問題的「積液的固化部分」的趨勢,120℃也能夠獲得顯著效果。但是,如實施例所示那樣,在63℃左右,對於陰極催化劑成分的減少實現了較高的效果,在考慮了加熱所需的成本的情況下,更優選使即將塗布塗布液時的金屬絲網狀基材的溫度為63℃左右。
在預熱工序,即將塗布塗布液時的金屬絲網狀基材的溫度小於43℃的情況下,會產生以下問題。
(1)在所述導電性陰極基材為具有構件彼此交叉而成的許多交叉部的形態的情況下,在進行了塗布的階段,在該許多交叉部聚集有必要以上的量的塗布液,形成所謂的積液。於是,在之後,進行乾燥、燒結工序時,該積液固化,結果,成為在導電性基材的交叉部過剩地固定有陰極催化劑成分的狀態,並且確認出:因該積液產生的過剩地固定在交叉部的陰極催化劑成分不能有效地幫助電解,至少是多餘,也就是沒用的部分。
(2)在向鎳基材塗布了塗布液的情況下,通常,鎳基材與塗布液直接接觸或者浸透陰極催化劑層而相接觸的現象持續到作為下一工序的乾燥工序為止。因此,尤其是塗布液為酸性的情況下,鎳基材溶出到下層的塗布液的膜中或者半乾燥狀態的塗布液中,在之後的燒結工序,在陰極催化劑層中形成鎳層。該層因長期電解或者短時間的反向電解而加速溶出,引起以該空隙為起點的陰極催化劑層的剝離。結果,陰極催化劑的消耗量變多。
針對該情況,在預熱工序,使即將塗布塗布液時的金屬絲網狀基材的溫度為43℃以上的情況下,能夠獲得下述顯著效果。
(1)在利用塗布法向金屬絲網等具有許多交叉部的導電性陰極基材的表面塗布包含陰極催化劑成分的塗布液而在所述導電性基材的表側和背側形成了陰極催化劑層時,在許多交叉部不會生成由塗布液的積液引起的過剩地包含陰極催化劑成分的固化部分(多餘且沒用的部分),或者,即使產生了這樣的由塗布液的積液引起的固化部分,該部分的截面的形態也會成為具有能夠確認到許多空洞的網眼狀的細孔形態。結果,能夠減少多餘且沒用的固化部分,因此,與以往的陰極催化劑層相比,能夠有效地降低形成的陰極催化劑層所用的昂貴的陰極催化劑成分的量,結果,能夠提供經濟性良好的電解用陰極。
(2)由於能夠促進將塗布液塗布於基材後塗布液自身的乾燥,因此,酸性的塗布液與鎳基材接觸的時間縮短,能夠抑制鎳向陰極催化劑層的溶出。結果,陰極催化劑層中不會形成鎳層。即,在形成陰極催化劑層時以高溫進行了燒結的情況下,不存在鎳作為鎳析出部析出到陰極催化劑層中的情況,能夠防止由鎳析出部導致的陰極催化劑層的剝離,結果,能夠降低使用時的陰極催化劑的消耗量,提高電解用陰極的耐久性。
另外,當所述溫度超過120℃時,即使與塗布液的沸點相比是相當低的溫度,含有水分等的塗布液溶劑也會開始急劇蒸發,在引起熱分解反應的溫度以前在塗布液的內部發生崩沸等相變,因陰極催化劑層的多孔化等而變得無法得到均勻的催化劑層。因此,所述溫度需要為120℃以下。考慮到其經濟性,如前面所述那樣,優選為63℃以下。
根據本發明人的研究,通過實施所述簡便的預熱工序,在金屬絲網狀基材的金屬線的交叉部不會產生塗布液過剩地積留而成的積液,或者,即使產生積液,在對塗布於金屬絲網狀基材的塗布液進行乾燥、燒結而形成了陰極催化劑層的情況下,「積液的固化部分」的截面的形態也會成為以連內部都有許多空洞的狀態固化的、截面的形態具有網眼狀的細孔的形態。本發明人認為能夠降低該催化劑成分的使用量的機理為:通過使塗布常溫(周圍溫度)的塗布液時的金屬絲網狀基材的溫度高於常溫(周圍溫度),並處於本發明所規定的特定的溫度範圍內,從而能夠加快剛塗布於基材後的塗布液的乾燥,在塗布工序後進行的乾燥工序中,加速了塗布好的塗布液中的溶劑的蒸發,能抑制塗布液的濡溼擴散,使塗布液迅速固化,結果,在交叉部難以產生積液,或者,即使產生積液,「積液的固化部分」的截面的形態也會成為如圖2-1所示那樣的具有連內部都能確認到許多空洞的網眼狀的細孔的形態。
如後述那樣,例如,若通過實施預熱工序,加熱為塗布常溫(周圍溫度)的塗布液時的金屬絲網狀基材的溫度成為43℃~120℃、優選在43℃~63℃的範圍內,形成陰極催化劑層,則在金屬絲網狀基材所具有的許多交叉部會生成的「積液的固化部分」的截面形態的平均孔隙率為15%以上。進而,通過實施預熱工序,使塗布常溫(周圍溫度)的塗布液時的金屬絲網狀基材的溫度升高到63℃左右,從而能夠使在金屬絲網狀基材的交叉部生成的「積液的固化部分」的截面形態的平均孔隙率為44%以上。
(預熱手段)
作為本發明中使用的預熱工序中的對金屬絲網狀基材進行預熱的手段,出於發熱效率高、升溫響應快這樣的理由,優選例如使用感應加熱裝置,當然,也能夠使用其他加熱手段。作為其他加熱手段,能夠列舉出使用了由紅外線、輻射管等產生的輻射熱的加熱方法,使暖風吹到導電性基材的加熱等,能夠根據狀況適當利用這些方法。
感應加熱(Induction Heating:以下,簡稱為IH)是利用電磁感應的原理,使電流在加熱線圈中流動,使作為加熱對象的金屬等導電體自身發熱的方法。其加熱原理為,當在加熱線圈中有交流電流流動時,會朝向其周圍產生強度變化的磁力線。當在其附近放置通電的金屬等物質時,會受該變化的磁力線的影響,在金屬中流動有渦電流。由於金屬自身的電阻而產生(電流)2×電阻的量的焦耳熱,金屬自己發熱。該現象稱為感應加熱IH。IH的最大優點為,能夠在加熱開始後數秒內使導電性基材升溫至規定溫度。因而,若利用IH,則能夠將預熱和塗布的各設備相鄰設置。
[2-2:塗布工序]
接著,對將本發明的製造方法所規定的含有陰極催化劑成分的起始原料在內的塗布液如前面所說明的那樣塗布於成為43℃~120℃的溫度範圍內的金屬絲網狀基材的至少一面的塗布工序進行說明。此時進行的塗布塗布液的方法並不特別限定,例如,利用輥塗或者噴塗等方法向處於所述的溫度範圍內的金屬絲網狀基材的至少一面塗布塗布液,之後,進行乾燥、燒結而形成催化劑層,從而得到了前面所述的本發明的顯著效果。塗布方法也可以利用所述輥塗或者噴塗以外的方法、例如刷塗、靜電塗裝及其它方法來進行。
作為在所述內容中使用的塗布液,能夠列舉出包括將前面列舉的那樣的催化劑成分的起始原料溶解於無機溶劑或者有機溶劑等的溶液的塗布液,具體而言,如下述那樣調製出來。例如,作為用於製造不溶性金屬陽極的陰極催化劑成分的起始原料,能夠使用從鉑、銥、釕、鈀、鋨中選出的至少一種金屬的無機或者有機化合物。例如,作為起始原料,有所述金屬的氯化物、硫酸鹽、硝酸鹽等。作為含有這些起始原料的塗布液,能夠使用將前面列舉的起始原料溶解於溶劑而成的溶液。本發明中所使用的塗布液也能夠使用進一步向前面列舉的催化劑成分的起始原料中加入了將鈦、鉭、鈮、鋯、鉿等閥金屬的無機或者有機化合物溶解於無機溶劑或者有機溶劑而得到的溶液的、無機溶液或者有機溶液。
另外,作為用於製造電解用陰極的陰極催化劑成分的起始原料,優選一併使用前面列舉的起始原料、和鎳化合物、鑭、鈰、釔等稀土類元素的化合物以及草酸的水和物等。
作為陰極催化劑成分的起始原料使用的具體的化合物能夠列舉出例如以下這樣的化合物,當然,不限於這些。
鉑:氯鉑酸或者硝酸鉑化合物:
銥:氯化銥
釕:氯化釕
鈀:氯化鈀
鈦:氯化鈦
鉭:五氯化鉭
鈰:氯化鈰
鎳:硝酸鎳
本發明中使用的塗布液也能夠使用酸性溶劑。具體而言,能夠列舉出鹽酸、硫酸、硝酸等無機系的酸性溶劑。進而,本發明中使用的塗布液的溶劑也可以是所述酸性溶劑和揮發性高的乙醇等有機溶劑混合而成的混合溶液。具體而言,能夠列舉出例如將四氯化銥、五氯化鉭溶解於35%鹽酸的無機溶液。作為其他的塗布液的例子,也能夠使用將氯化釕、氯化銥、氯化鈦溶液溶解於鹽酸和IPA(異丙醇)而成的無機、有機混合溶液,將二亞硝基二氨鉑、硝酸鈰溶解於硝酸而成的無機溶液等酸性的塗布液。
下面,列舉本發明中進行的、將所述那樣的塗布液塗布於所述那樣的形態的金屬絲網狀基材的至少一面時的塗布條件的一例,當然,本發明不限於此。若在製造食鹽電解用陽極的情況下,也取決於塗布液中的、催化劑成分的起始原料的濃度,例如,能夠列舉出以平均每次的塗布量為0.36g~0.66g、塗布次數為6~12次、整體的塗布量為2.16g~5.28g的方式進行塗布。在本發明中重要的是,以這樣的條件塗布周圍溫度(常溫)的塗布液時,使即將進行塗布時的金屬絲網狀基材的溫度在43℃~120℃的範圍內、優選在43℃~63℃的範圍內一次以上。除此之外,並不特別限定,在如所述這樣反覆進行塗布的情況下,優選進行周圍溫度(常溫)的塗布液的塗布的總次數中的每次,都使即將進行塗布時的金屬絲網狀基材的溫度在所述的溫度範圍內。通過這樣構成,能夠使會在金屬絲網狀基材的許多交叉部生成的「積液的固化部分」的截面形態的平均孔隙率進一步提高。結果,能夠降低形成的陰極催化劑層中的昂貴的陰極催化劑成分的使用量,因此本發明的電解用陰極更經濟。
另外,根據本發明人的研究,得知:在調製本發明的電解用陰極時,若包含所述那樣的陰極催化劑成分的起始原料在內的塗布液使用高濃度的溶液,則具有「積液的固化部分」的截面形態的孔隙率提高的趨勢。提高塗布液的濃度能夠獲得本發明的更顯著效果的理由在於:含有的化合物為高濃度意味著塗布液中的溶劑量變少,由此,發揮了與通過實施預熱工序將即將進行塗布時的金屬絲網狀基材的溫度提高為43℃~120℃的範圍內而加快塗布之後的乾燥的疊加效果。對於本發明中使用的塗布液中的陰極催化劑成分的濃度,雖然也有因催化劑成分的起始原料的種類、溶劑的種類而使塗敷性不同的情況,但是,例如,可以為20g/L~500g/L左右、更優選為50g/L~250g/L左右。
[2-3:乾燥工序]
在所述塗布工序形成的塗布層在之後進行乾燥、燒結,形成催化劑層。乾燥工序並不特別限定,例如,經與塗敷間連續的連續爐的乾燥區,進行了均化(日文:レベリング)後,以乾燥時間5~10分鐘、設定溫度30℃~80℃的溫度進行乾燥。另外,該乾燥工序是在塗布塗布液後,作為燒結的前階段進行的,與本發明的特徵的塗布塗布液之前對金屬絲網狀基材進行加熱、使供塗布液的塗布的基材溫度在特定的範圍內的預熱工序能明確區分開。
[2-4:燒結工序]
所述2-3的乾燥工序後的塗布液的塗布層經燒結工序進行燒結,成為含有催化劑成分(催化劑層形成物質)的陰極催化劑層。在反覆進行塗布、乾燥、燒結的情況下,成為催化劑層的一部分。燒結工序的燒結方法並不特別限定,例如,使用與進行乾燥工序的乾燥區連續的連續爐的燒結區來進行。燒結條件也並不特別限定,不同的陰極催化劑成分,燒結條件也不同,例如,在大氣氣氛下,以燒結時間10~15分鐘、燒結溫度大約350~600℃這樣的條件來進行燒結。
通過以所述那樣的條件來進行燒結,從而所述塗布液中的起始原料被熱分解,在陽極用的情況下,例如,形成含有陰極催化劑成分的催化劑層,陰極催化劑成分包括從鉑、銥、釕、鈀、鋨及它們的氧化物中選出的至少一種的鉑族金屬和/或它們的合金。另外,根據塗布液中含有的起始原料的成分的不同,還能形成含有包括在所述鉑族金屬和/或其氧化物中加入了鈦、鉭、鈮、鋯、鉿等閥金屬的氧化物的複合氧化物或者固溶體的陰極催化劑成分的催化劑層。另外,在陰極用的情況下,能形成含有所述鉑族金屬、鎳和/或其氧化物與鈰、鑭等稀土類元素的氧化物的混合氧化物的陰極催化劑層。
(3.後工序)
在本發明的電解用陰極的製造方法中,在所述那樣的催化劑層形成工序之後,如圖1所示那樣,根據需要,進行性能調整工序、中和處理工序、形狀加工等後處理,製造電解用陰極。這些後處理工序在本發明中也是與以往的方法同樣地進行即可,與以往的方法沒有不同。
另外,如圖1中虛線所示那樣,在2-4的燒結工序後,進入接下來的3.的後工序之前,再次進行2-2的塗布工序,之後,進行乾燥、燒結工序,反覆這樣進行,以形成期望厚度的陰極催化劑層,在該情況下,因為本發明中作為對象的基材是表面積較大的金屬絲網狀等,所以,燒結後的導電性基材的溫度會迅速自然冷卻。根據本發明人的研究,在以通常的反覆步驟進行了一連串工序的情況下,再次塗布塗布液時的、即將塗布塗布液時的導電性基材的溫度下降至接近周圍溫度,至少不會成為本發明的製造方法中規定的43℃以上的溫度。
實施例
接著,列舉實施例和比較例詳細地說明本發明,但本發明並不限定於此。
<實施例1~4和比較例1、2>
<陰極催化劑層的形成>
按照圖3所示的工序圖,利用含有金屬絲網的導電性基材,在該金屬絲網狀基材上利用塗布法形成含有陰極催化劑成分的催化劑層。如圖3所示,導電性基材利用經1.的前處理工序前處理後的金屬絲網狀基材,在該金屬絲網狀基材上按照2.的陰極催化劑層形成工序的步驟形成陰極催化劑層。此時,不實施2-1的預熱工序,或者,實施預熱工序而使即將塗布塗布液時的金屬絲網狀基材的溫度進行各種變化。除此以外的2-2~2-4的工序利用後述的方法同樣地進行。並且,為了比較得到的形成有陰極催化劑層的金屬絲網狀基材的交叉部的部分的性狀,按圖3所示的4.的步驟,製作「積液的固化部分」的截面形態的孔隙率的測量用試樣,利用後述的方法測量孔隙率。並且,利用測量到的孔隙率,評價通過實施作為本發明的特徵的預熱工序而得到的昂貴的陰極催化劑成分的減少效果。以下,對各工序的步驟等進行說明。
(導電性陰極基材)
在所述試驗中,作為導電性基材,使用了鎳制的平紋金屬絲網基材(φ0.15×40網眼)。進行了條件各不相同的試驗,針對各條件的試驗,分別準備了四張100mm見方(日文:角サイズ)的所述金屬絲網。這些金屬絲網狀基材都使用進行了下述的前處理的基材。
〔1.前處理工序〕
[1-1:粗面化處理工序]
利用氧化鋁研磨劑(#320尺寸)對金屬絲網狀基材的兩面實施乾式噴砂處理而進行粗面化處理。
[1-2:蝕刻處理工序]
將金屬絲網狀基材浸漬在20%鹽酸水溶液中(大約25℃)大約3分鐘,進行蝕刻處理,同時進行基材的水洗處理。
[1-3:提高耐腐蝕性處理]
在大氣中,以大約500℃的溫度,對金屬絲網狀基材進行30分鐘以內的加熱處理。
(塗布液)
作為陰極催化劑成分的起始原料,使用氯化釕(RuCl3)溶液、氯化鈰粉末和草酸粉末,準備在氯化釕溶液中混合溶解氯化鈰粉末和草酸粉末而得到的無機、有機混合溶液並將其作為酸性的塗布液。此時,製作出將配合濃度調整為以Ru濃度計為100g/L和200g/L的低濃度和高濃度兩種濃度不同的塗布液。
〔2.陰極催化劑層形成工序〕
利用所述金屬絲網狀基材和塗布液,按照圖3所示的2.陰極催化劑層形成工序,在金屬絲網狀基材上形成催化劑層。
[2-1:預熱工序]
準備爐內尺寸為200mm(W)×200mm(H)×200mm(L)的電爐,利用該電爐進行塗布前的試樣加熱。
並且,對於作為加熱對象的金屬絲網狀基材的加熱條件,以即將塗布塗布液時的金屬絲網狀基材的溫度成為以下列舉的3種的方式設定電爐溫度。將預熱的保持時間設為5分鐘,使金屬絲網狀基材的溫度均勻地成為期望的溫度。之後,基於後述的形成於金屬絲網狀基材的陰極催化劑層的交叉部的「積液的固化部分」的截面形態的不同,如下述那樣,根據即將塗布常溫(周圍溫度)的塗布液時的金屬絲網狀基材的溫度的不同,劃分為實施例和比較例。
(1)不加熱(周圍溫度25℃,比較例1、2)。
(2)將加熱的設定溫度設為60℃進行預熱,使即將塗布塗布液時的金屬絲網狀基材的溫度上升。並且,針對各金屬絲網狀基材,測量此時的基材溫度,能夠確認的是,對於基材溫度,全部的基材均穩定在43℃~46℃的範圍內(實施例1、2)。以下,該條件採用通過所述試驗驗證了效果的下限值43℃,記作43℃。另外,在整個本說明書中,記作43℃的情況具有同樣的意思。
(3)將加熱的設定溫度設為90℃進行預熱,使即將塗布塗布液時的金屬絲網狀基材的溫度上升。並且,針對各金屬絲網狀基材,測量此時的基材溫度,能夠確認的是,對於基材溫度,全部的基材均穩定在62℃~64℃的範圍內(實施例3、4)。以下,將該條件記作中央值63℃。即,63℃是以±1℃的誤差實際測量到的溫度。另外,在整個本說明書中,記作63℃的情況具有同樣的意思。
[2-2:塗布工序、2-3:乾燥工序、2-4:燒結工序]
分別利用之前準備好的低濃度塗布液(100g/L濃度塗布液)和高濃度塗布液(200g/L濃度塗布液),在從電爐取出通過所述預熱工序分別調整為各溫度的金屬絲網狀基材之後,緊接著在塗敷間內通過輥塗將所述塗布液塗布於所述金屬絲網狀基材的一面。以下,對塗布工序的詳細情況進行說明。
在預熱和塗布工序中,除所述塗布液和金屬絲網狀基材以外,還準備並使用了下述材料。為了避免被預熱後的金屬絲網狀基材的溫度在塗布常溫(周圍溫度)的塗布液的工序中在塗敷間內的氣氛下驟冷,而使用了金屬絲網狀基材的保持用墊板(厚度為3mm的Ti薄板)。並且,還準備了用於塗布塗布液的塗布用輥和塗布用臺,並如後述那樣進行了塗布。塗布用臺使用能夠直接插入Ti網眼制的乾燥、燒結爐內的臺。
並且,塗布工序、乾燥工序、燒結工序的步驟、要領如以下那樣。
在塗布工序中,以對所述塗布液的種類和即將塗布塗布液時的金屬絲網狀基材的溫度進行改變而得到的組合,向各金屬絲網狀基材塗布塗布液,之後,利用乾燥工序、燒結工序,對塗布液進行乾燥、燒結,從而形成陰極催化劑層。此時,具體而言,如以下那樣實施。
(a)事先通過刻印在各金屬絲網狀基材刻上識別標記。此時,在各條件下,各使用4張金屬絲網狀基材,確認偏差。
(b)為了使金屬絲網狀基材的溫度不發生變化,而利用基材的保持用墊板,並快速地塗布塗布液。
(c)將規定量的塗布液注入容器,使適量的塗布液滲入輥,將輥輕輕地按壓於基材進行轉印,進而,將規定量的塗布液全部轉印、塗布於基材。
(d)在塗布後,利用乾燥工序,在60℃的溫度下乾燥5分鐘。
(e)在乾燥後,利用燒結工序,在550℃的溫度下燒結10分鐘。
(f)針對各金屬絲網狀基材,反覆進行規定次數(12次)所述(c)~(e),形成陰極催化劑層。
進而,如後述那樣,觀察金屬絲網狀基材的交叉部的「積液的固化部分」,利用後述的方法測量該部分的截面形態的孔隙率,評價陰極催化劑成分的減少程度。根據歸納於表1的即將塗布塗布液時的金屬絲網狀基材的溫度的不同,能夠確認形成的催化劑層的「積液的固化部分」的明確的形態的不同,這是由於即將塗布塗布液時的金屬絲網狀基材的溫度的不同引起的,根據該情況,如表1所示那樣將它們分別作為實施例1~4、比較例1、2。在表1中連同即將塗布塗布液時的金屬絲網狀基材的溫度一起一併示出了塗布液的塗布量、塗布次數。如表1所述那樣,使用形成有陰極催化劑層的實施例1~4、比較例1、2的金屬絲網狀基材,利用後述的方法分別製成試樣1~6的6種評價用試樣。另外,表1中的基材溫度是即將塗布塗布液時的金屬絲網狀基材的溫度,塗布量是根據塗布液的濃度以材料利用率為100%的方式算出的值。
表1:實施例1~4、比較例1、2的試樣的塗布條件
對於表1所示的實施例1~4(試樣3~6)和比較例1、2(試樣1、2)的各試樣,為了觀察金屬絲網狀基材的交叉部的「積液的固化部分」的截面形態以及測量孔隙率,而按照圖3所示的4.孔隙率測量用試樣製作的步驟分別調製測量用試樣。之後,使用經調製好的試樣,利用下述的方法,測量「積液的固化部分」的截面形態的孔隙率。
[4:「積液的固化部分」的截面的孔隙率測量方法]
(4-1)採集測量用試樣
從之前製作出的試樣1~6的形成有催化劑層的實施例1~4、比較例1、2的金屬絲網狀基材的中央部分別切下大約20mm見方的部分。
(4-2)金屬絲網狀基材的樹脂埋入及研磨
將所述切下的金屬絲網狀基材沿著鉛垂方向埋入透明樹脂,進行研磨等,調製使交叉部的基材的截面暴露的測量用試樣。
(4-3)利用電子顯微鏡觀察
利用電子顯微鏡觀察交叉部的「積液的固化部分」的截面,提取用於孔隙率測量的圖像。
(4-4)孔隙率測量
利用電子顯微鏡進行觀察,針對提取的各圖像的「積液的固化部分」,利用圖像二值化處理用軟體測量孔隙率。在圖4~圖6中示出了其中一例。具體而言,如圖4所示,首先,針對提取的圖像的「積液的固化部分」的截面形態,進行確定、識別由積液導致的固化部分的範圍的操作,求出該部分的面積。與此同時,進行分別確定、識別所述的確定的範圍內的許多孔隙部分的操作,針對各孔隙,求出面積,並求出孔隙的總面積。之後,算出孔隙的總面積相對於在上述求出的由積液導致的固化部分的範圍的面積的比例,將該比例作為「積液的固化部分」的截面形態的孔隙率。
圖4表示實施例3的即將塗布濃度為100g/L的低濃度塗布液時的金屬絲網狀基材的溫度為63℃的4個試樣5的測量狀態。對於孔隙率的測量,如圖4所示,針對4張金屬絲網狀基材中的各金屬絲網狀基材,分別測量構成金屬絲網的構件的交叉部的截面形態的圖像中的、位於構件兩側的「積液的固化部分」。因而,孔隙率的測量值的數量為每個條件8個。圖5表示實施例4(試樣6)的即將塗布濃度為200g/L的高濃度塗布液時的金屬絲網狀基材的溫度為63℃的情況下的、與所述同樣的孔隙率的測量狀態,為了與實施例3(試樣5)進行比較,將其一部分結果作為一例示出。根據兩者的比較可知,使用高濃度塗布液的實施例4(試樣6)的情況相比塗布低濃度塗布液的實施例3(試樣5)而言孔隙率也較高。並且,能夠確認的是,在實施例4(試樣6)的條件下,如圖5所示,存在完全不產生「積液的固化部分」的情況。
圖6表示在沒有進行預熱的處於周圍溫度下的金屬絲網狀基材上塗布濃度為100g/L的低濃度塗布液的比較例1(試樣1)的情況下的交叉部的「積液的固化部分」的截面形態的、孔隙率的測量狀態。圖6所示的交叉部與圖4、圖5所示的「積液的固化部分」的截面形態明顯不同,不是本發明的實施例的情況那樣的具有能確認到許多空洞的網眼狀的細孔的形態。因此,能夠確認的是,與本發明的實施例相比,孔隙率也明顯較小。
將如所述那樣得到的比較例1、2(試樣1、2)、實施例1~4(試樣3~6)各例的金屬絲網狀基材的交叉部的「積液的固化部分」的截面形態的孔隙率的測量結果一併表示在表2及表3中。表2是使用濃度為100g/L的低濃度塗布液的情況下的測量結果,表3是使用濃度為200g/L的高濃度塗布液的情況下的測量結果。
表2:塗布低濃度塗布液的情況下的因基材溫度的不同而產生的孔隙率比較結果
圖7是針對表2所示的使用低濃度塗布液的情況下的孔隙率的測量結果,相對於即將塗布塗布液時的金屬絲網狀基材的溫度示出如所述那樣測量而得到的每個條件各得到8個的孔隙率的數據的圖。並且,圖7中的直線是利用所述測量值統計處理得到的,表示非常好的相關關係。對於統計處理的結果,作為其近似式,算出下述式(1)的一次函數,在圖7中也有所示。
y=0.9369x-19.495 (1)
R2=0.7127
這表示,通過提高即將塗布常溫(周圍溫度)的塗布液時的金屬絲網狀基材的溫度,能夠可靠地提高金屬絲網狀基材的交叉部的「積液的固化部分」的截面形態的孔隙率。「積液的固化部分」的截面形態的孔隙率提高意味著形成的催化劑層中的昂貴的陰極催化劑成分的使用量減少。
表3:塗布高濃度塗布液的情況下的因基材溫度的不同而產生的孔隙率比較結果
圖8是針對表3所示的使用高濃度塗布液的情況下的孔隙率的測量結果,相對於即將塗布常溫(周圍溫度)的塗布液時的金屬絲網狀基材的溫度示出如所述那樣測量而得到的每個條件各得到8個的孔隙率的數據的圖。並且,圖8中的直線是利用所述測量值統計處理得到的,與圖7同樣,表示非常好的相關關係。對於統計處理的結果,作為其近似式,算出下述式(2)的一次函數,在圖8中也有所示。
y=1.2261x-27.692 (2)
R2=0.5409
另外,根據與圖7的比較可知,在使用高濃度塗布液的圖8的情況下,在提高了即將塗布塗布液時的金屬絲網狀基材的溫度時,能夠更加穩定、可靠地提高金屬絲網狀基材的交叉部的「積液的固化部分」的截面形態的孔隙率。
表4將使塗布液的濃度和即將塗布該塗布液時的金屬絲網狀基材的溫度變化的、實施例和比較例的各試樣1~6的表2、3所示的測量結果按各條件以孔隙率的測量值的幅度(偏差)、最大值、平均孔隙率的觀點整理出來。由表4也可知:通過提高即將塗布塗布液時的金屬絲網狀基材的溫度而得到的孔隙率的提高效果、通過提高塗布液的濃度而得到的孔隙率有提高的傾向。
表4:「積液的固化部分」的截面形態的孔隙率的傾向
根據以上的結果,判明了以下情況。
(1)比較例1和比較例2的結果
在完全沒有實施作為本發明的特徵的預熱,在金屬絲網狀基材的溫度為周圍溫度(25℃)的狀態下塗布塗布液的情況下,由表示比較例1的試樣1的結果的圖6可知,金屬絲網狀基材的交叉部的「積液的固化部分」的截面的形態與實施例的情況明顯不同,不是具有連內部都能確認到空洞的網眼狀的細孔的形態。雖然未圖示,使用的塗布液的濃度提高了的比較例2的試樣2也是同樣的。並且,能夠確認的是,如表2~4所示,比較例1的試樣1和比較例2的試樣2的孔隙率與塗布液的濃度無關,最大也就18%左右,平均值較小,為小於8%的值,在金屬絲網狀基材的溫度為周圍溫度(25℃)的狀態下塗布塗布液的情況下,「積液的固化部分」成為催化劑成分過剩地存在的堆滿狀態,在無助於提高陰極性能的部分,陰極催化劑成分被浪費使用。
(2)實施例1和實施例2的結果-基材溫度43℃
在實施例1的試樣3和實施例2的試樣4的情況下,將電爐的設定溫度設為60℃對金屬絲網狀基材加熱,使即將塗布常溫(周圍溫度)的塗布液時的金屬絲網狀基材的溫度為43℃左右,形成催化劑層。雖然未圖示,但在這些實施例的情況下,與比較例的圖6不同,金屬絲網狀基材的交叉部的「積液的固化部分」的截面的形態為具有連內部都能確認到空洞的網眼狀的細孔的形態。並且,能夠確認的是,如表2~4和圖7所示,在實施例1的試樣3和實施例2的試樣4的情況下,金屬絲網狀基材的交叉部的「積液的固化部分」的截面形態的孔隙率最大為29%左右,平均值為15%~17%,與在金屬絲網狀基材的溫度為周圍溫度的狀態下塗布塗布液的比較例的情況相比,孔隙率明顯提高。由此可知,若將即將塗布塗布液時的金屬絲網狀基材的溫度提高到43℃左右,則能夠可靠地消除在「積液的固化部分」陰極催化劑成分過剩地被浪費使用的狀態,能夠減少用於形成催化劑層的陰極催化劑成分的量。
(3)實施例3和實施例4的結果-基材溫度63℃
在實施例3的試樣5和實施例4的試樣6的情況下,將電爐的設定溫度設為90℃對金屬絲網狀基材加熱,使即將塗布常溫(周圍溫度)的塗布液時的金屬絲網狀基材的溫度為63℃左右,形成催化劑層。如圖4所示,在實施例3的試樣5的情況下,與比較例的圖6不同,金屬絲網狀基材的交叉部的「積液的固化部分」的截面的形態為具有連內部都能確認到空洞的網眼狀的細孔的形態。並且,能夠確認的是,如圖5所示,在與實施例3的情況相比塗布液的濃度提高了的實施例4的試樣6的情況下,根據情況的不同,能夠實現不存在金屬絲網狀基材的交叉部的「積液的固化部分」的狀態。如表2~4和圖8所示,在使基材溫度為63℃的實施例3的試樣5和實施例4的試樣6的情況下,金屬絲網狀基材的交叉部的「積液的固化部分」的截面形態的孔隙率最大為100%,在存在固化部分的情況下也非常高,為67%左右,平均值也較高,為43%~55%。由此,能夠確認的是,通過使基材溫度進一步提高為63℃,別說與在金屬絲網狀基材的溫度為周圍溫度的狀態下塗布塗布液的比較例的情況相比,就連與即將塗布塗布液時的金屬絲網狀基材的溫度為43℃左右的實施例1的試樣3和實施例2的試樣4相比,孔隙率也明顯提高,陰極催化劑成分的使用量的減少更加明顯。
並且,根據實施例1的試樣3與實施例2的試樣4之間的比較、實施例3的試樣5與實施例4的試樣6之間的比較,能夠確認的是,在使用濃度為100g/L的低濃度塗布液作為塗布液的情況和使用濃度為200g/L的高濃度塗布液作為塗布液的情況下,如表4所示,與即將塗布塗布液時的金屬絲網狀基材的溫度無關,金屬絲網狀基材的交叉部的「積液的固化部分」的截面形態的孔隙率具有在使用高濃度的塗布液的情況下較大的傾向。其理由被認為是如下這樣的結果:若塗布液為高濃度,則該塗布液的溶劑量較少,因此產生與提高金屬絲網狀基材的溫度而得到的效果相疊加的效果。
<實施例5、6及比較例3>
接著,分別使用實施例5、6的電解用陰極和比較例3的電解用陰極進行了電解試驗,其中,實施例5、6的電解用陰極是這樣得到的:在塗布工序的前段進行的預熱工序中,以使即將塗布塗布液時的金屬絲網狀基材的溫度為43℃(實施例5)及63℃(實施例6)的方式進行加熱後,利用對塗布於基材的塗布液進行乾燥、燒結的塗布法,在導電性基材的表側和背側形成含有陰極催化劑成分的陰極催化劑層;比較例3的電解用陰極是這樣形成的:在不進行所述預熱工序而在仍為常溫的狀態下,利用將塗布於金屬絲網狀基材的塗布液進行乾燥、燒結的塗布法,與所述實施例同樣地形成了陰極催化劑層。然後,針對電解前後的電極,利用下述的實驗確認了陰極催化劑層中的鎳析出部、以及由此產生的剝離狀態。
[評價]
(試驗試樣的製造方法)
對於供本試驗的實施例的試樣的製造方法,將基材在塗布塗布液之前以規定溫度加熱保持於電氣加熱式乾燥爐,在即將塗布塗布液時從乾燥爐取出,趁基材還沒有冷卻,塗布塗布液,之後進行乾燥和燒結,將這樣的一連串的塗布工序反覆執行規定的次數,製作出了試驗用的試樣。對於比較例的試樣的調製,除了不進行對基材的加熱保持以外,與所述同樣。
在實施例的試樣的製作時,事先測量即將塗布塗布液時的基材溫度,作為即將進行塗布時的基材溫度進行規定。另外,在進行評價試驗之前測量了試樣的初始重量,以能夠算出由評價試驗導致的催化劑層的消耗量。
(試驗條件)
按表5所示的順序,對如所述那樣得到的各評價用的電極試樣進行了包括反向電解在內的電解。進行了反向電解的情況下,若在催化劑層中存在「鎳層」的析出,則會產生剝離。電解試驗後,對試樣進行水洗,經乾燥後,稱重,使用預先測量的初始重量,算出了消耗量。
1)評價試樣
基材:使用了φ0.15mm的鎳線的平紋金屬絲網
塗布液:與實施例1~4所示的塗布液一樣
2)電解條件(根據表5所記載的電解順序)
表5:試驗中使用的電解條件
(試驗結果)
表6示出了基材溫度和催化劑層的消耗量。
表6:評價結果
如表6的結果明確所示那樣,從實施例5、實施例6及比較例3的催化劑層的消耗量的比較能夠確認出:通過進行了預熱,與比較例3相比能夠大幅度地減少消耗量。其原因在於,通過對基材進行加熱,能夠促進塗布液的塗布後的液乾燥,結果,能夠抑制鎳從導電性基材向陰極催化劑層中的溶出。相對於此,不對即將塗布塗布液時的金屬絲網狀基材加熱,仍為常溫狀態的比較例3的電極的情況下,消耗量為0.706mg/cm2,與實施例5、6相比較,消耗量極大。
圖9-1是實施例5的電解試驗前的電解用陰極的截面的SEM照片的圖。陰極基材的鎳沒有溶出到陰極催化劑層中,陰極催化劑層保持為僅由催化劑成分或者其氧化物構成的穩定狀態。使用該電解用陰極以表5所示的條件進行了電解及反向電解,沒有確認到陰極催化劑層的剝離。該點也能夠從所述消耗量的少量確認出。
圖9-2是比較例3的電解用陰極的電解試驗前的電極的截面的SEM照片的圖。能確認出:陰極基材的鎳析出到陰極催化劑層中,形成了層。
圖9-3是進行了表5所示的電解及反向電解之後的比較例3的電極的剖視圖。陰極基材的鎳析出到陰極催化劑層中而成的鎳層會因電解及反向電解而溶出,因而會在陰極催化劑層中生成空隙,以此為起點,陰極催化劑層剝離。
產業上的可利用性
採用本發明,在向金屬絲網狀基材的表面利用塗布法在導電性陰極基材的表側和背側形成含有陰極催化劑成分的陰極催化劑層的情況下,能夠在不損害陰極性能的前提下,利用將即將塗布常溫(周圍溫度)的塗布液時的金屬絲網狀基材的溫度加熱為規定溫度這樣的極其簡單的手段,能夠降低用於形成陰極催化劑層的貴金屬等昂貴的陰極催化劑成分的使用量。結果,能夠在不損害作為陰極的功能的前提下,獲得經濟的電解用陰極。進而,由本發明提供的經濟的電解用陰極能夠防止因長期電解產生的陰極催化劑層的剝離,減少陰極催化劑層的消耗量,成為與以往的電極相比耐久性得到提高的有用的電解用陰極。如所述那樣,本發明的電解用陰極及其製造方法是這樣的技術:能夠利用簡便的方法,且在不降低陰極功能的前提下,降低形成陰極催化劑層時使用的昂貴的陰極催化劑成分的使用量,還能夠獲得抑制該催化劑層的剝離問題的效果,還能夠期待提高其耐久性能,尤其是降低了可以說是電極業界的夙願的原材料的成本,使產品的經濟性得到提高。因此,能夠期待廣泛的利用。