一種直升機動力艙後部封嚴結構的製作方法
2023-05-11 15:36:12 1
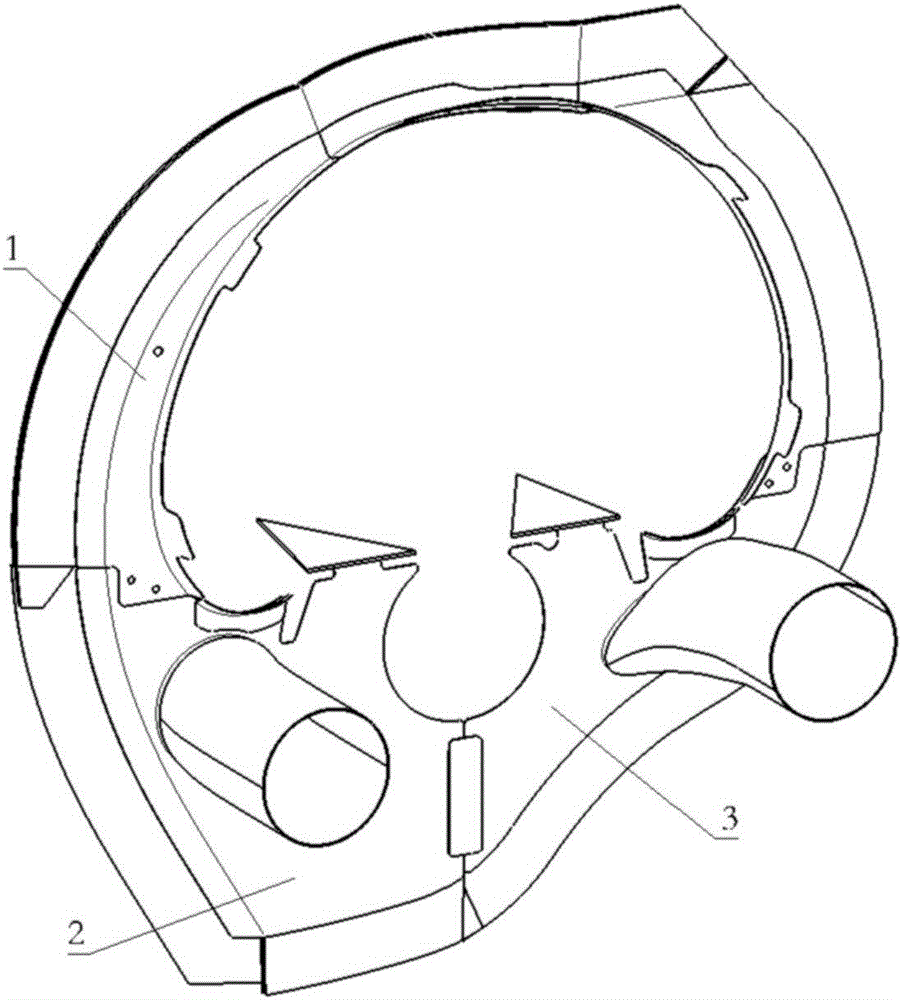
本發明涉及一種直升機的結構設計,特別適用於需要對動力艙進行封嚴的結構設計。
背景技術:
直升機使用的發動機在工作中需要進行散熱以保證發動機的安全工作,多採用將動力艙後部區域開敞進行自然通風的形式散熱。隨著發動機專業的不斷進步及直升機的發展需要,自然通風散熱的形式已經無法滿足當前大功率發動機的使用要求,需要進行強制通風進行散熱,為保證動力艙進氣口和通氣口的壓力差,滿足發動機的散熱要求,需要對動力艙後部開敞區域進行有效封嚴,考慮發動機在動力艙後部區域的複雜形狀、發動機工作時的振動、發動機排氣管的高溫影響等多種因素,需要制定一套新的方案。
技術實現要素:
本發明要解決的技術問題:
本發動的目的是提供一種直升機動力艙後部封嚴方案,保證動力艙後部開敞區域的有效封嚴,並避免由於發動機振動、發動機後部形狀複雜、排氣管高溫等帶來的影響。
本發明的技術方案:
一種直升機動力艙後部封嚴結構,包括上部隔板組件1、下部外隔板組件2和下部內隔板組件3,上部隔板組件1與發動機排氣管、下部外隔板組件2和下部內隔板組件3螺接,下部外隔板組件2和下部內隔板組件3與發動機上法蘭盤螺接,下部外隔板組件2與下部內隔板組件3通過限位片13連接;上部隔板組件1包括上隔板4、密封帶5和U形壓片6,上隔板4與發動機排氣管貼合,密封帶5與上隔板4通過U形壓片6和螺釘7連接。下部外隔板組件2包括U形壓片6、下外隔板8、密封帶9、圓網柵10、鉚釘11、通風管12,下外隔板8與發動機上法蘭盤螺接,密封帶9與下外隔板8通過U形壓片6和螺釘7連接,所述下外隔板8上有通氣圓孔,所述通氣圓孔內側安裝有圓網柵10,圓網柵10與下外隔板8通過鉚釘11連接,所述通氣圓孔外側安裝有通風管12,用於強制引氣;下部內隔板組件3包括U形壓片6、下內隔板15、密封帶16、橢圓網柵17、通風管18,下內隔板15與發動機上法蘭盤螺接,密封帶16與下內隔板15通過U形壓片6和螺釘7連接,下內隔板15上有通氣橢圓孔,所述通氣橢圓孔內側安裝有橢圓網柵17,橢圓網柵17與下內隔板15通過鉚釘11連接;所述通氣橢圓孔外側安裝有通風管18,用於強制引氣。
所述的一種直升機動力艙後部封嚴結構,其特徵在於,所述上隔板4為耐高溫不鏽鋼材料。
所述的一種直升機動力艙後部封嚴結構,其特徵在於,所述下外隔板8和下內隔板15為鋁合金材料。
所述的一種直升機動力艙後部封嚴結構,其特徵在於,所述下部外隔板組件2和下部內隔板組件3還包括三角密封帶14,用於對發動機排氣管下部複雜區域進行封嚴。
所述的一種直升機動力艙後部封嚴結構,其特徵在於,所述密封帶5、密封帶9、密封帶16、三角密封帶14為耐高溫的橡膠帶。
本發明的有益效果:
技術解決方案能夠對動力艙後部開敞區域進行封嚴,避免了發動機振動、發動機形狀複雜、排氣管高溫等對封嚴結構的影響,並為通風冷卻提供足夠面積的通氣接口。
附圖說明
圖1為本發明後部封嚴結構正視圖;
圖2為本發明後部封嚴結構外側軸測圖;
圖3為本發明後部封嚴結構內側軸測圖;
圖4為本發明上部隔板組件正視圖;
圖5為本發明上部隔板組件外側軸測圖;
圖6為本發明上部隔板組件內側軸測圖;
圖7為本發明下部外隔板組件正視圖;
圖8為本發明下部外隔板組件內側軸測圖;
圖9為本發明下部外隔板組件外側軸測圖;
圖10為本發明下部內隔板組件正視圖;
圖11為本發明下部內隔板組件內側軸測圖;
圖12為本發明下部內隔板組件外側軸測圖。
具體實施方式
本發明的技術解決方案是由上部隔板組件(1)、下部外隔板組件(2)、下部內隔板組件(3)組成,三者通過螺接與發動機上相應接口連接固定。
上部隔板組件1由上隔板4、密封帶5和U形壓片6組成。上隔板4選用δ0.4mm的不鏽鋼材料,鈑金工藝分段焊接成形,U形壓片6選用δ0.6mm的鋁合金材料鈑金工藝成形,使用螺釘7將密封帶5夾持固定在上隔板4和U形壓片6之間。
下部外隔板組件2由U形壓片6、下外隔板8、密封帶9、圓網柵10、通風管12、限位片13和三角密封帶14組成。下外隔板8選用δ0.6mm的鋁合金材料,鈑金工藝成形,圓網柵10選用不鏽鋼材料,採用鈑金結合焊接工藝成形,網框厚度0.6mm,網絲直徑0.8mm,與下外隔板8通過鉚釘11連接固定,通風管12選用δ0.8mm的鋁合金材料鈑金工藝成形,限位片13選用δ0.6mm的鋁合金材料鈑金工藝成形,下外隔板8、通風管12和限位片13通過焊接工藝連接,三角密封帶14與下外隔板8鉚接連接固定。
下部內隔板組件3由U形壓片6、下內隔板15、密封帶16、橢圓網柵17、通風管18和三角密封帶14組成。下內隔板15選用δ0.6mm的鋁合金材料,鈑金工藝成形,橢圓網柵17選用不鏽鋼材料,採用鈑金結合焊接工藝成形,網框厚度0.6mm,網絲直徑0.8mm,與下內隔板15通過鉚釘11連接固定,通風管18選用δ0.8mm的鋁合金材料鈑金工藝成形,下外隔板8和通風管12通過焊接工藝連接,三角密封帶14與下內隔板15鉚接連接固定。
密封帶5、密封帶9、密封帶16和三角密封帶14均選用耐高溫的塗有聚氯丁橡膠的玻璃纖維,其中密封帶5、密封帶9和密封帶16為雙層布局,每隔100mm布置有剪口,層間剪口交錯,伸出隔板部分寬35mm,通過與周圈機體結構的擠壓對隔板與機體結構的間隙進行封嚴。
此技術方案能夠有效的對動力艙後部進行封嚴,保證進氣口和通氣口的壓力差,並為強制通風冷卻提供通氣接口,為發動機冷卻系統的實施提供了有效的結構基礎。